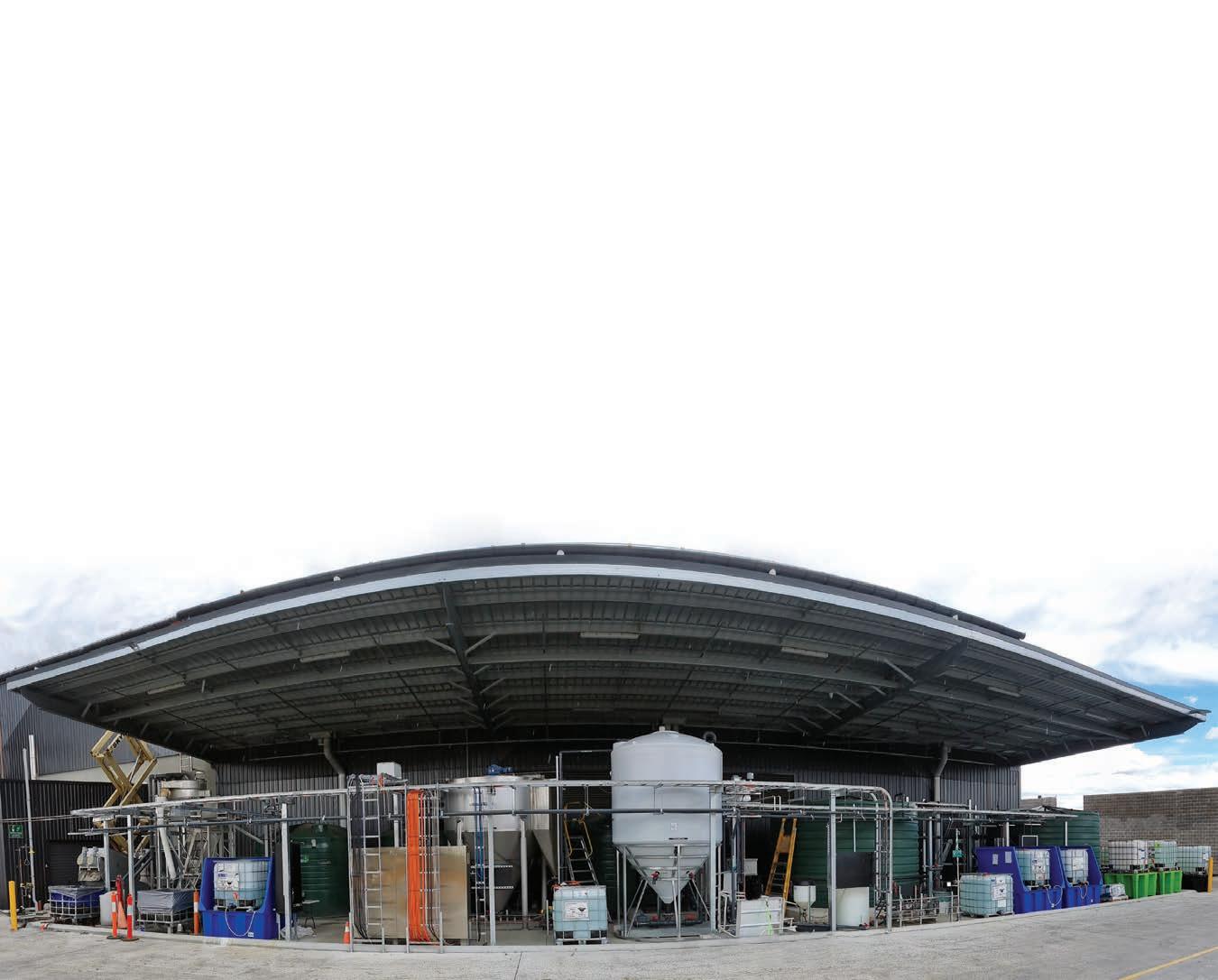
4 minute read
A NEW BENCHMARK
Circular Plastics system raises the bar
The Circular Plastics wastewater treatment plant provides one of the most advanced levels of treatment.
AEROFLOAT HAS SET A NEW BENCHMARK WITH A WASTEWATER SYSTEM FOR ONE OF AUSTRALIA’S BIGGEST PLASTIC RECYCLING FACILITIES.
Aerofloat’s most advanced wastewater treatment system so far for the plastics industry is in the final stages of commissioning.
The wastewater treatment specialists designed and installed a system for a Circular Plastics Australia PET recycling facility in Albury-Wodonga, New South Wales.
The plant, a joint venture between Cleanaway Waste Management, Pact Group Holdings Group, Asahi Beverages and Coca Cola Europacific Partners is expected to be Australia’s biggest end-to-end recycled polyethylene terephthalate (PET) plant and is expected to recycle up to one billion 600ml PET plastic bottles a year.
It is the third project Aerofloat and Pact Group have worked on together.
Aerofloat has created sustainable wastewater treatment designs for major plastics recycling businesses across Australia and has been awarded for its innovative approach to tackling plastics recycling wastewater issues.
Michael Anderson, Aerofloat General Manager of Engineering, says the Circular Plastics water treatment system pulls together all the elements of previous systems Aerofloat has designed for the plastics industry.
“Stages of the treatment process have all been done at other sites but in the plastics industry, this is the most advanced plant that we’ve done to this level of treatment,” Michael says.
“We’re really happy with what we’ve achieved.”
The Aerofloat design had to ensure a sustainable, long-term solution for Circular Plastics and allow for the expansion of the recycling facility in the future. Clean wastewater from the system is either re-used as wash water within the plastics recycling facility or discharged to sewer, helping to reduce the company’s footprint with savings on water usage.
Aerofloat installed its patented circular dissolved air flotation unit, the AeroCircDAF, to treat higher flow volumes of wash water. It also included its fully automated, intelligent PLC control system to accommodate the integration of additional Aerofloat technology as the business expands.
Michael says Aerofloat worked closely with the local council to ensure strict
policies and guidelines around managing microplastics in inland water were met.
“One of the main considerations for the council and Environment Protection Authority was microplastics,” he says.
“We can remove suspended solids and large plastics and biologically treat soluble contaminants from plastic bottles, such as sugars and soluble proteins, but there’s a concern about microplastics from industries.
“Part of the project brief was to remove a lot of the microplastics down to trace elements. The standards were very tight. Through our treatment process we believe there’s a high degree of microplastics being removed.”
Michael says the scope of the project changed during the contract and a biological treatment and clarification process were added to the original plant to meet stricter trade waste guidelines.
“Every plant we’ve done is different to the next because of the type of plastic, the way they wash the plastic, and council requirements,” he says. “Because this facility was being built in an inland town it meant that the wastewater treatment plant needed to be more advanced than something in a major coastal town. Aerofloat worked with the council, the EPA and the client to define what they wanted to achieve.
“We had to understand the type of plastic they use, the wastewater that comes from the plastic, understand the wash line of the recycling plant and then engineer a solution.
“Everything is on track to achieve what we said we would.”
COVID-19 presented other challenges to the 12-month project. Michael says state border closures, transportation and supply chain issues and quarantine rules affected the build.
“During a major part of the installation we were in a Sydney COVID-19 hot spot,” he says.
“We had to engage local contractors and work remotely for part of the installation.
“But we delivered the installation to the client on time and on budget.”
Michael predicts that as government stimulus continues, the recycling sector will be big business in Australia.
He says locations such as Albury, which is central to other major cities, will play an important role in helping move toward a circular economy.
“As long as this industry keeps growing, there will be more jobs in recycling and manufacturing. We’re seeing a lot of opportunities,” he says.
For more information, visit: www.aerofloat.com.au
* enjoy extra support with volvo ce
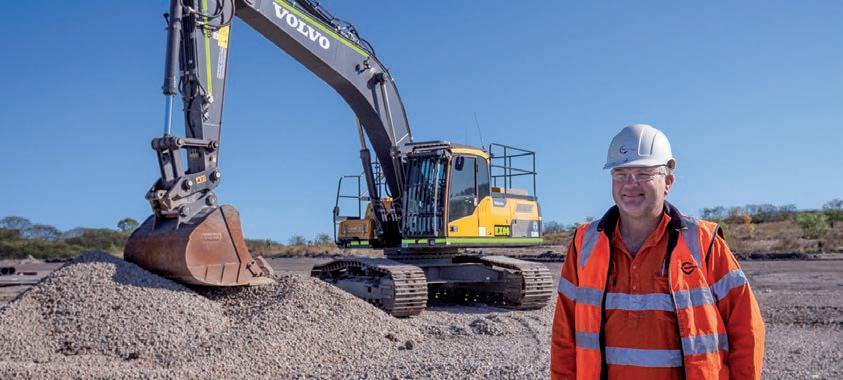
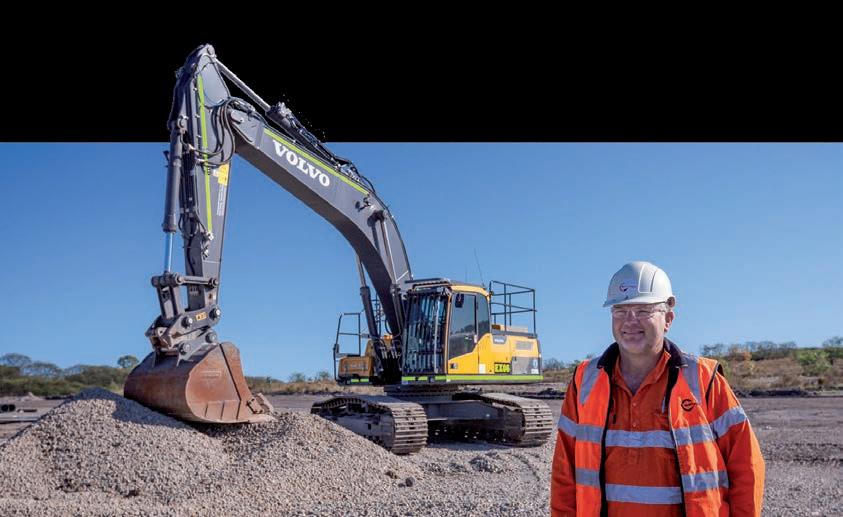
EXTENDED
3-YEAR/6000 HOUR WARRANTY
AVAILABLE NOW
Purchase a new 14 - 30 tonne Volvo excavator between the 1st of March and the 31st of August 2022 and receive extra piece of mind with an extended 3-year/6000 hour warranty.
Visit cjd.com.au for more information or call 1300 139 804
enquiries@cjd.com.au | Find us on Facebook, LinkedIn and Instagram
Bonus upgrade to 3 year/6000 hour warranty offer is valid for every new 14-30 tonne Volvo excavator purchased between 1st March 2022 and 31st August 2022. Offer available on Volvo excavator models EC140D, EC140EL, ECR145EL/ELD, EC200EL, EC200D, EC220D, EC220EL/ELD, ECR235EL/ELD, EC250D, EC250EL/ELD, EC300D, EC300EL/ELD, EWR130E, EWR150E, EW160E, EWR170E, EW180E and EW240EMH. Machine must be delivered by 31st October 2022. Warranty is valid on component only. The warranty is limited to three years or 6000 operating hours, whichever occurs first, commencing from the date of delivery. Normal manufacturer’s warranty terms and conditions apply. Images are for illustration purposes only. CJD Equipment reserves the right to withdraw this offer at any time without notice.