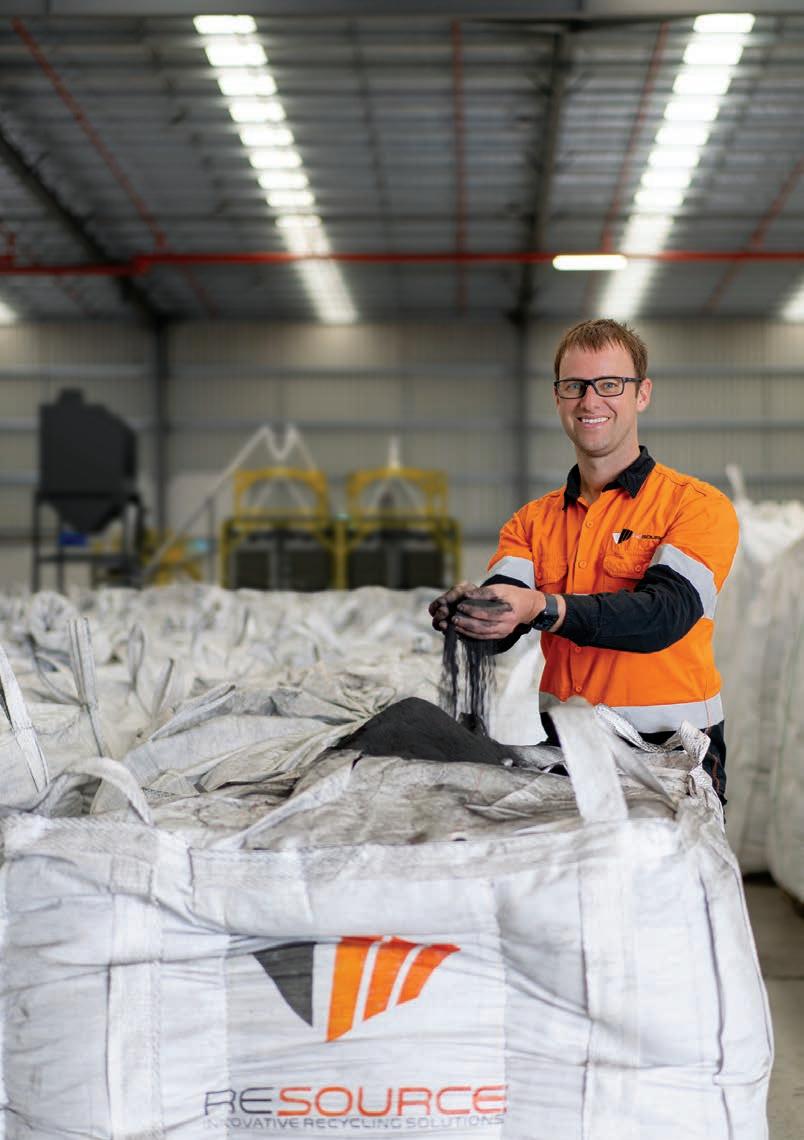
4 minute read
POSITIVE THINKING
TROY ROWE, THE FOUNDER OF BATTERY RECYCLING COMPANY RESOURCE, IS PROOF THAT PERSISTENCE PAYS OFF.
Less than five years after starting his recycling business with a small plant and big ideas, Troy Rowe is standing tall.
ReSource, believed to be the first and only alkaline and zinc carbon battery recycling company in Australia capable of producing a fertiliser-grade black mass output, is installing a third-generation plant at a purposebuilt facility in Victoria. It will be home to the Southern Hemisphere’s first installation of an X-ray sorter for batteries.
The X-ray Battery Sorter is capable of sorting 8-10 batteries per second, just over 1000 kilograms per hour, with a guaranteed 99.8 per cent accuracy.
Built by a Belarus company that specialises in X-ray for security and hospitals, the X-ray Battery Sorter looks through the skin of a battery to determine its chemical composition, ensuring there no risk of contamination from other battery chemistries.
“One of our biggest challenges has been accuracy of sorting,” Troy says. “Because we’re pursuing a fertiliser path as an end-product, the tolerance for contaminants, which are extensive in other battery types, is very limited. Our minimum is 99.5 per cent accuracy.
“This X-ray plant is key to our process. It’s absolutely the most important thing. We can’t afford mistakes. We’re talking product that goes into our food source. Mistakes are not viable.”
“Not viable” is something Troy has heard often over the past five years. The third-generation recycler says
Troy Rowe is recycling alkaline and zinc carbon batteries into a fertiliser-grade black mass output.
Troy Rowe, Founder of the battery recycling company ReSource
finding his own path and pursuing a solution not yet adopted in Australia “has been a journey”.
What sparked that journey was a documentary on micronutrients.
Troy began looking into the commodities of different batteries and found that alkaline batteries contained zinc and manganese dioxide, two micronutrients used in fertiliser production.
He says while most recycled alkaline and zinc carbon batteries are smeltered, a North American company had begun converting the batteries into micronutrient fertiliser and he began to question why it wasn’t being done in Australia. After researching processes in Europe and North America, Troy found that melting alkaline and zinc carbon batteries has questionable recovery outcomes, uses 15-25 times the energy and produces more greenhouse gases in comparison to the process ReSource has developed.
Despite his research, Troy says he was told on numerous occasions that what he was trying to do “wasn’t possible”.
In late 2016 he brought his first piece of machinery “based on an idea that theoretically, this is how it can work”.
By his own admission it was a “slow operation”. But the 200kg/hr plant allowed Troy to learn and improve as he worked with customers to produce a product that could be used in fertiliser. He later updated to a 400kg/hr plant and shipped his first product out in late 2018.
In February 2022, ReSource moved into a 15,000 square metre site equipped with a third-generation plant with a processing capacity of up to 2000 kilograms an hour – believed to be the highest capacity processing plant in Australia. In time, it will also house and process e-waste.
With assistance from a Sustainability Victoria grant, the factory is being built using best practices from Europe, including multiple automated thermal fire cannons and more than a dozen thermal cameras.
“It was not as simple as I thought it would be,” Troy says. “There’s been a lot of very long days and nights. I was driving Uber to keep the doors open and for more than a year took care of dogs, just trying to make enough money to keep investing in the equipment.
“We kept trying to progress the equipment to a point that the end users of the product were happy. It’s been the hardest five years of my life but it’s really, really rewarding to get to this point.
“We’ve actually figured out how to do this now.”
Troy is targeting the hundreds of tonnes of stockpiled batteries across Sydney and Melbourne and says ReSource will have capacity to process at least 60 per cent of the nation’s single-use batteries should collections reach that level.
“We know there are 400 tonnes of batteries in Sydney, along with a number of large stockpiles in Melbourne,” he says. “Stockpiles are not being dealt with in an environmentally friendly way because nobody is capable of truly recycling them due to the degradation of the casings, making it impossible to sort optically or by hand. It’s a really big deal to give Australia the capacity and capability to sort these stockpiles with X-ray technology.
ReSource is a member of the Australian Battery Recycling Initiative (ABRI), a not-for-profit association established in 2008 to promote responsible environmental management of batteries at end-of-life. Troy is on the Executive Committee. ReSource is also an accredited sorter and recycler with B-cycle, Australia’s official battery recycling scheme run by the Battery Stewardship Council.
He says battery recycling is another area where Australia is “a long way behind” compared with European countries. However, he believes B-cycle will play a key role in educating the next generation.
“It’s important we’re starting to get collection points out there and get batteries out of rubbish bins and garbage trucks,” he says.
“The education is there but it’s not enough. It seems almost once a week there’s a fire in a garbage truck and many of these fires are lithium batteries. We have to get through to people this can’t happen.”
For more information, visit: www.re-source.net.au