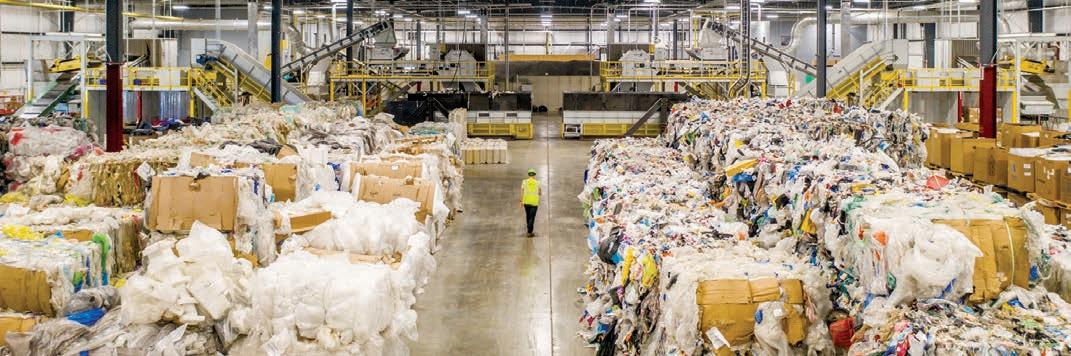
4 minute read
PLASTIC WASTE MEETS ITS (RE)MAKER
“EARTH’S CLEAN-UP CREW” IS BRINGING A CIRCULAR SOLUTION TO PLASTIC POLLUTION DOWN UNDER.
Global waste solutions, Brightmark is unlocking the building blocks of waste and turning it into something reusable.
Brightmark’s first-of-its kind plastics renewal facility in Ashley, Indiana is coming to Parkes, New South Wales.
The plastics renewal facility will be the first new circular economy business in the Parkes Special Activation Precinct and the largest of its type outside of America.
Constructed in partnership with the New South Wales Government, the $260 million facility is tipped to create more than 100 new full-time jobs.
It will re-purpose all types of plastics (1-7) to be ultra-low sulphur diesel, wax and naphtha to produce other plastics and will be capable of processing up to 200,000 tonnes of waste plastics annually, predominantly from NSW.
Announcing the project in March, Paul Toole, Deputy Premier and Minister for Regional NSW said the project was a huge opportunity for Parkes and regional NSW to “get a slice of the $66 billion global plastics recycling industry” and bring strong economic growth and jobs.
The 4800-hectare Parkes Special Activation Precinct is Australia’s first UNIDO Eco-Industrial Park, where business will work together to achieve cost savings and to solve problems including waste and water reuse and energy use and generation.
Located at the only junction of the Inland Rail and the Trans-Australian Railway, the precinct will give suppliers access to 80 per cent of Australia’s population within 12 hours by road or rail.
Bob Powell, Brightmark Founder and Chief Executive Officer, says
Brightmark’s Parkes facility will re-purpose plastics (1-7). The Parkes facility will be capable of processing up to 200,000 tonnes of waste plastics annually.
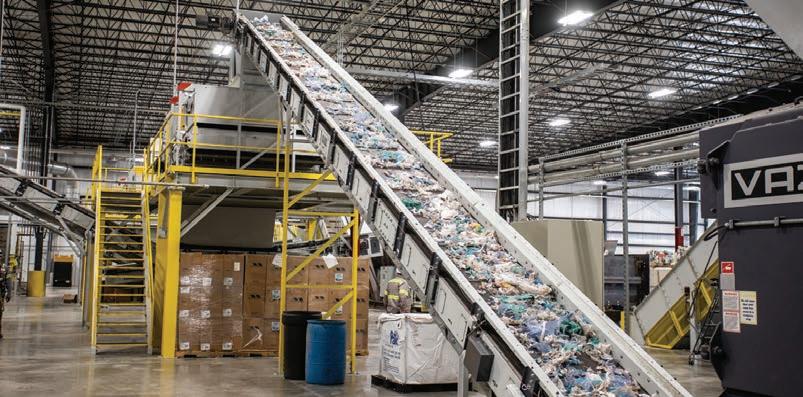
Bob Powell, Brightmark Founder and Chief Executive Officer
the Brightmark team is excited about the Parkes project.
“It’s really clear to us that in Australia, and elsewhere globally, people have woken up to the fact that the things we throw away and dispose of have environmental impacts,” Bob says.
“The last two to three years there has been an emphasis on plastic waste in Australia and we see an acceleration of that. Efforts to ban plastic waste are already in motion.
“At Brightmark, part of our mission is to reimagine waste and create a world without waste. Australia is a very natural fit for us.”
The plastics renewal facility uses a patented pyrolysis technology, decomposition brought about by high temperatures, to turn plastics into liquid that can then create usable products. Brightmark says it is the only company in the world to use this unique type of advanced recycling technology, that is 93 per cent efficient, on all plastic types.
While contracts for the end-product from the Parkes facility are still to be decided, Bob says a “majority” of what is produced will be used in Australia.
He says the wax produced from this recycling process is used every day in products such as food-grade wax and surfboard wax, the ultra-low sulphur diesels produced will be sold locally.
“The largest emphasis for us is to create a fully circular solution,” he says. “We create the building blocks to remake plastics. One of the challenges we have with unrecycled plastics is we have a use and dispose of model. Using Brightmark’s technology we can use and reuse plastics.
“What’s great about this unique process, in addition to being able to take every plastic that is produced, we can do it economically, at scale, for a fully circular plastic that we can continually reuse.
“It should largely eliminate the need for excessive amounts of virgin plastics.”
Bob says waste collectors and potindustrial users who pay a landfill levy to dispose of non-recyclable plastics landfilled will save money whey they bring those plastics to Brightmark.
“We’ve flipped the economic value of nuisance plastics.
“There’s inherent value in the plastics we unlock.
“We are unleashing a value that otherwise was locked and lost.”
Construction at Parkes is expected to start in mid-2023 and the plastics renewal facility to be operational by 2025. Bob says Brightmark has been working with a team in Australia for almost two years, which has played a big role in the project’s success so far.
“Living and working in parts of Asia Pacific previously, we have found that to be successful with projects like these you need to make sure you have local people working as a team.
“One of the most important things when we decide to build one of our facilities is ‘does the community want us there? The reaction from the Parkes community has been overwhelmingly positive. I think because of the awareness of the problem, and now what is a great solution to the problem.
“We’re excited to be in Parkes and New South Wales.”
For all corporate and commercial plastic inquiries, email Australia@ brightmark.com
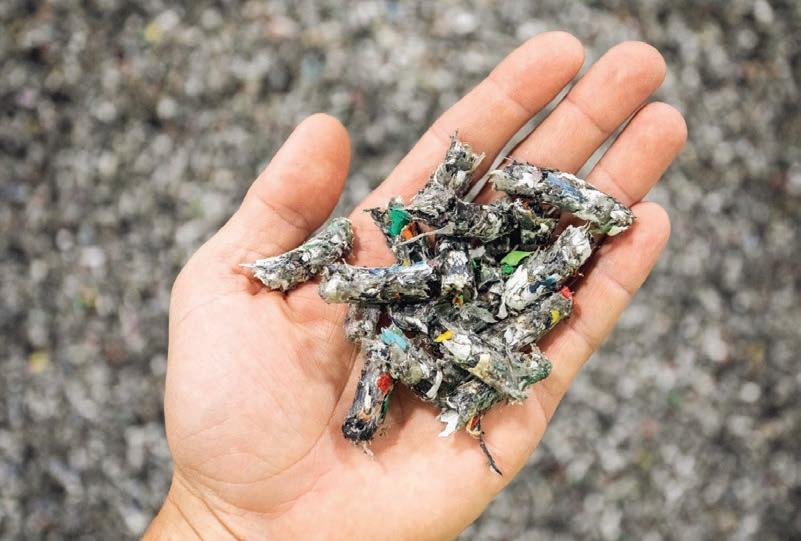
Patented pyrolysis technology turns plastics into liquid that can then create usable products. For more information, visit: www.brightmark.com