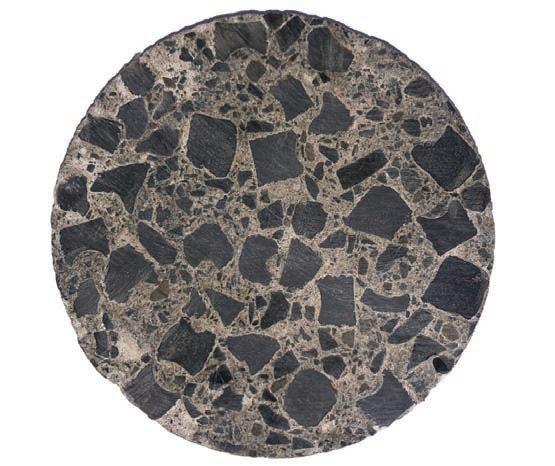
3 minute read
AN ECO-FRIENDLY ALTERNATIVE
URBAN RECYCLING SOLUTIONS HAS TEAMED UP WITH ENVIROPLAZ INTERNATIONAL TO MAKE A PRODUCT THAT PARTIALLY SUBSTITUTES ROCK AGGREGATE AND SAND IN CONCRETE WITH CO-MINGLED WASTE PLASTICS.
According to World Wildlife Fund Australia, 130 kilograms of plastic is used per person each year. Less than 12 per cent of that is recycled.
Additionally, up to 130,000 tonnes of plastic will find its way into waterways and the ocean annually.
With waste plastics becoming a national and global issue, many companies are looking to close the loop on plastic products.
Urban Recycling Solutions is one of them. Gavin Grace, Co-Director says the issue needs rectifying.
“Plastic is polluting the world at alarming rates. A lot of people don’t fully understand the impact that waste plastics are having on the environment, whether it be in the soil, water or air,” he says.
After seeing the large volume of medical waste which was being produced during the beginning of the COVID-19 pandemic, Gavin started doing his own research on how it could be dealt with.
He came across a product known as Plazrok, a concrete aggregate additive that enhances the properties of concrete and is made from all seven types of plastics that occur in co-mingled waste plastic.
Dean Payne, Urban Recycling Solutions Co-Director says the process of making Plazrok does not require burning, instead it uses a thermomechanical process. The product can include co-mingled plastics from classes one to seven, meaning that virtually every plastic product can be used, including contaminated materials such as discoloured plastic and residues. No sorting or washing is required. Labels and caps need not be removed.
“We can take the full spectrum. This plastic waste can be anything, from your kids’ toys to e-waste or nylon from tyres,” Gavin says.
“It creates a commercial market for waste management companies, while also reducing plastic pollution.”
Plazrok is compatible with existing concrete batching plants. Plazrok has already proven itself in practical environments, with the additive being used to make concrete panels and in other applications such as pavement, facades, road barriers and railway sleepers to name a few.
The products attributes such as size and dimensional ratios can be altered to specific project requirements.
AN INTERNATIONAL ORIGIN
Plazrok is a product invented by the founder of the New Zealand technology company Enviroplaz International Ltd, Peter Barrow, and developed in conjunction with an American partner
Gavin and Dean have secured the Master License to manufacture the product in Australia, with the view of commercialising the product for use in various other countries.
Dean says that initial testing, conducted in New
Plazrok can be included in a range of applications, such as pavement, road barriers or even railway sleepers.
Zealand, has shown it’s more than just a viable alternative to conventional concrete.
“Plazrok is about 20 per cent of the weight of standard aggregate. It improves the tensile strength, without changing the compressive properties,” he says.
“The reduced weight means moving the product takes less trucks, saving time and costs. It also performs to a better when undergoing fi re-proofi ng tests, compared to standard concrete. It can last up to an hour longer,” Dean says.
Testing has found that the product is expected to have superior thermal and acoustic performance, when compared to conventional aggregates. Concrete produced using Plazrok has high impact and shatter resistance.
Plazrok is also recyclable, once the concrete has reached its end-of-life.
THE NEXT STEP
Urban Recycling Solutions will look to manufacture the product on a greater scale early in 2023 following the completion of testing.
A major Australian concrete company has shown interest, as well as state government. Gavin expects this interest to “go crazy” once prospective customers understand the product’s potential.
“Because it is a new technology, some people are hesitant as they don’t believe that it can accept all types of plastic, when it actually can,” he says.
“At the moment we are talking to overseas government offi cials and ministries. We are hoping by the end of next year to have 20 production plants globally.”
For more information, visit: https://plazrok.com/
The size of the Plazrok ‘nugget’ can be altered, depending on what is required for any given project.
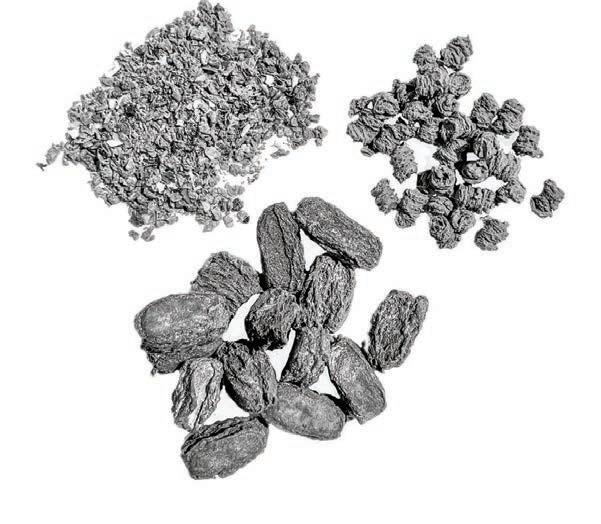
vertical shredders. shredders. Built tough for the most demanding of shredding applications.
HEAVY DUTY VALUEFOR MONEY CIRCULAR ECONOMY
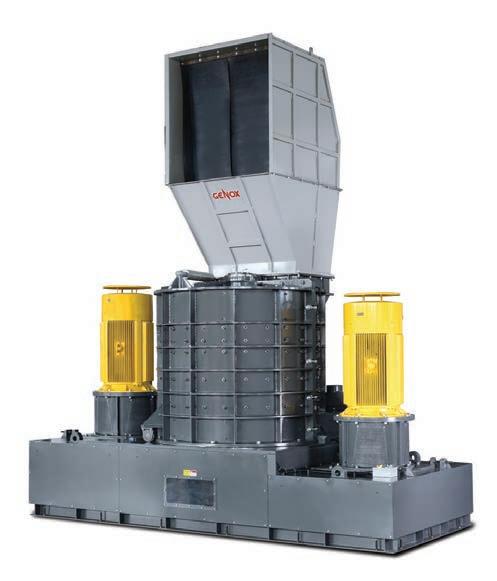
• Aggressive size reduction and densification of preshredded materials • Clean, high bulk density output for easy sorting and transportation • C&D waste, scrap metal and other heavy duty applications • Available with up to 440kW of power • Industry-proven and built tough for Australian conditions