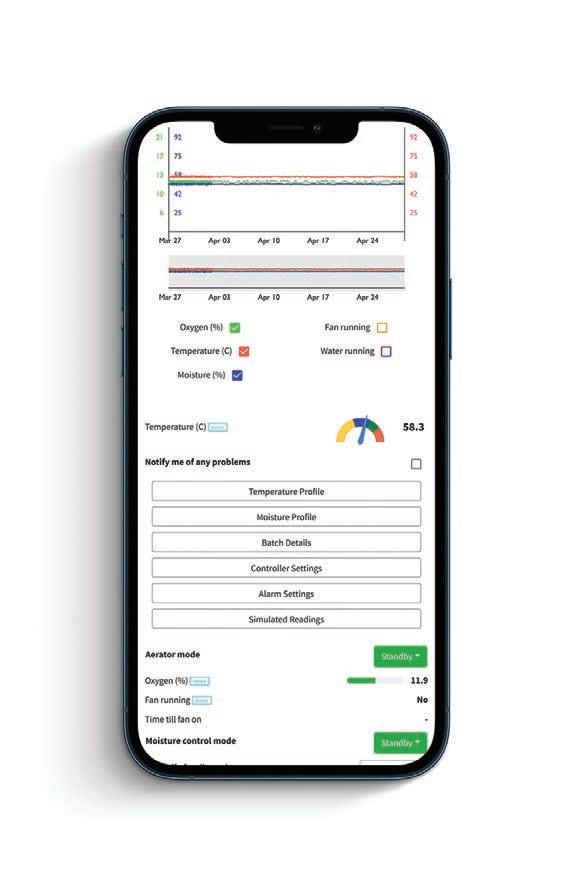
5 minute read
A UNIQUE SOLUTION
RADICLE AGRICULTURE IS TURNING THE TABLE ON TRADITIONAL COMPOSTING, WITH HEAP TECHNOLOGY.
Martin Tower, Managing Director Radicle Agriculture has been involved in the compost industry for more than 20 years. For much of that time he has used traditional compost windrows that are mechanically turned on a scheduled basis to put air into the material.
There’s been an assumption that the aeration is enough to allow the organic material to continue to be broken down. However, research has found the oxygen saturation levels in a windrow can return to their pre-turned levels within two to five hours.
“As a consequence, an efficient composting process can’t be fulfilled,” Martin says. “Even if you have the moisture levels correct when mixing materials, you can’t really get the job done without the oxygen.”
Radicle Agriculture’s HEAP system uses aerated floor technology, a series of pipes running underneath the organics pile, to introduce oxygen on a more frequent basis, optimising conditions for decomposition.
The computer-controlled system is connected to a series of sensors which monitor oxygen levels in the pile and automatically introduce air when levels fall below a set parameter. The same technology can be applied to an irrigation system to monitor and automatically adjust moisture levels.
“Generally, it will blow air on an hourly basis, rather than every two to three days, or weekly for a compost turn,” Martin says.
The system is accessible via a mobile phone-based app and will advise the operator of any issues and when the process is complete. Radicle Agriculture has been developing the HEAP technology for the past two years. Martin says a nine-month trial at a site in Gatton has been “better than we hoped for” and has produced an Australian Standards 4454 compliant finished product.
While composting times depend on the input materials, the process can take between nine and 12 weeks. But the HEAP does have some constraints with input.
“You must use appropriate quantities of carbon to nitrogen,” Martin says. This process won’t operate optimally if you don’t do that. We work with clients to ensure the mix they’re putting into the pile is appropriate to reach the outcome. Fortunately, FOGO is an excellent feedstock.”
Contamination is a key issue with any composting process. Because there is no mechanical action in the HEAP system, any plastic bags, tins or containers that are in the pile are not shredded and can easily be screened out at the end of the process.
Martin says one of the other advantages to HEAP technology is there is no longer a need for someone to operate a compost turner for a significant amount of time.
“You don’t need a turner, maintenance of a turner or the fuel that goes into it,” he says. “The operating costs of this system are fundamentally less. The system itself is less expensive than a compost turner in terms of capital expenditure.”
HEAP also requires a smaller footprint than traditional windrow composting. The system is scalable and can grow over time with demand. The smallest heap would hold about 120 cubic metres (6m x 12m x 2m) and can be increased up to 24m x 24m x 3.5m.
Martin says it’s an ideal solution for smaller councils and remote sites that can’t afford to build an in-vessel composting facility and don’t have the space, time or finances to operate a turned windrow system.
“They can take food organics and garden organics (FOGO) from the local collection, put it on a heap
The HEAP system is accessible via a mobile phone-based app.
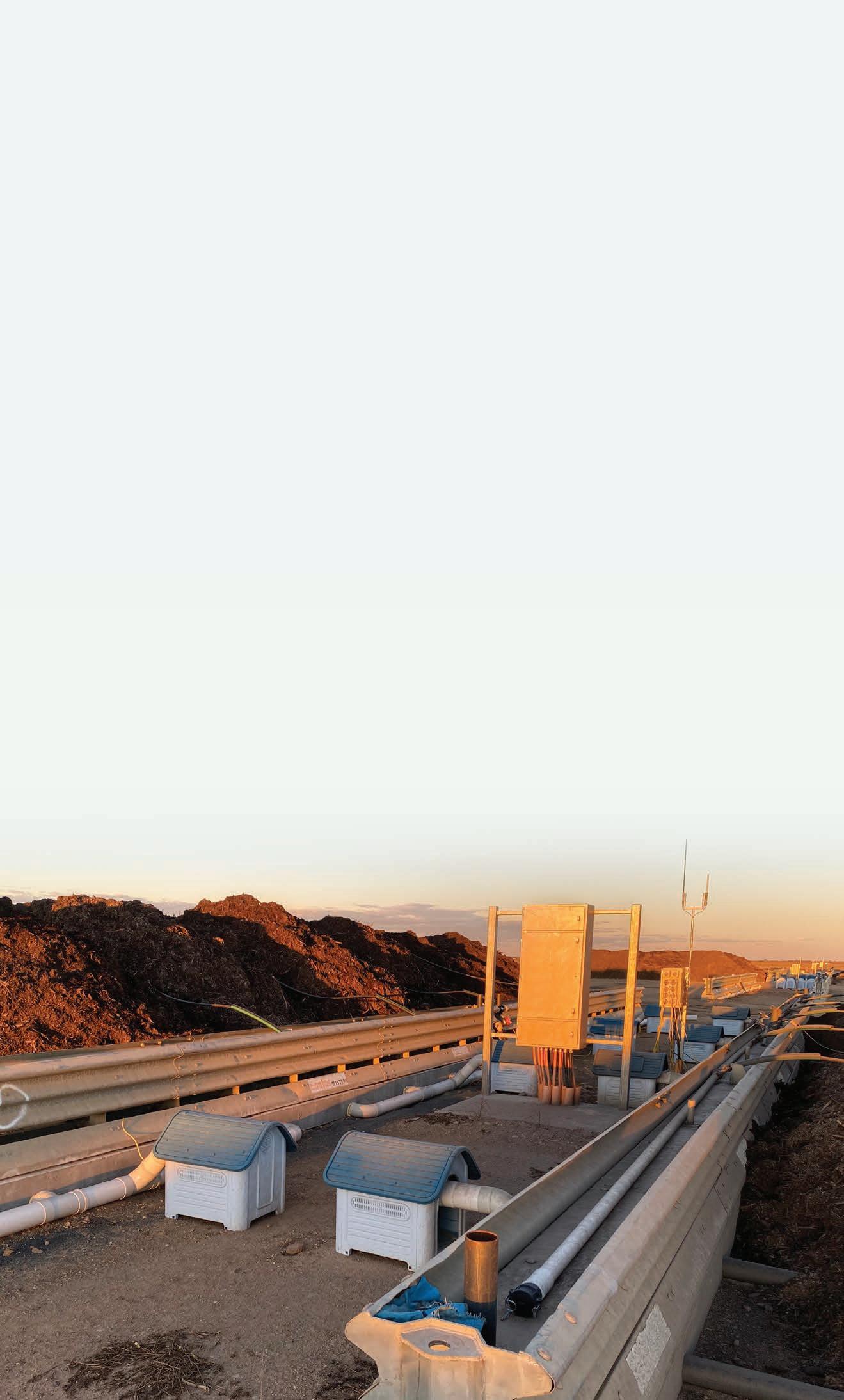
Martin Tower, Managing Director Radicle Agriculture
and the computer will do the job for them. In the meantime, they can be building the next heap.
“Councils can manage their FOGO themselves and reuse the finished product for their own purpose within their municipality, rather than take it to a FOGO facility. The cost savings in transport alone can be very substantial.”
Councillor Jason Cook, Lockyer Valley Regional Council Community Facilities and Waste Portfolio says demonstrating the ‘FOGO bin to garden’ story has played a big part in the success of the Food Organics Garden Organics trial at Lockyer Valley Regional Council.
“The static aerated floor has been instrumental in taking our community on the circular economy journey by enabling us the ability to create an end user product on a system that takes up minimal space, is easy to use and has amazing results,” he says.
“The HEAP system will provide LGAs the opportunity to take ownership over their waste by turning it into a product that can be used locally, instead of making it someone else’s problem.”
HEAP can be retrofitted into existing sites and Martin believes would be suitable as a secondary use for capped landfill which has rainwater management in place to avoid leachate.
Several agricultural facilities are looking at HEAP technology and an Australian mining company is keen to use the system to compost its packaging.
The system can also be deployed quickly to help clean up organic waste in emergency situations. Martin points to recent floods that destroyed produce at the Brisbane markets, cyclones that wiped out banana plantations in northern Queensland and the needle contamination of strawberries in Queensland and Western Australia several years ago.
“It’s entirely possible we could have one of these systems packaged in shipping containers ready to go,” he says. “We could deal with the organic waste and get some value product out of it for the communities rather than letting it rot or go to landfill.”
For more information, visit: www.radicleag.com.au
The HEAP system requires a smaller footprint than traditional windrow composting and can be scaled up as required.