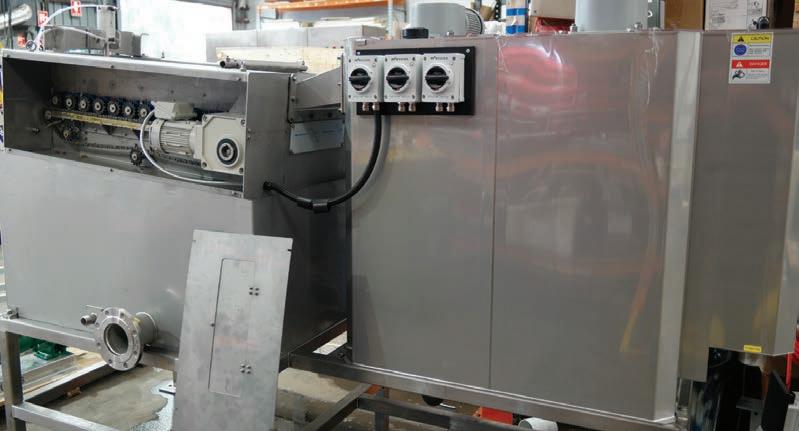
4 minute read
THE NEW WAVE OF TECHNOLOGY
AEROFLOAT’S AEROWAVE WASTEWATER TREATMENT SYSTEM IS REDUCING OPERATING COSTS AND WATER USAGE IN THE PLASTICS RECYCLING INDUSTRY.
National targets to have 70 per cent of plastic packaging recycled or composted and 50 per cent recycled content in packaging by 2025 has driven growth in Australia’s plastics recycling industry.
Advanced recycling technology is being fast-tracked and millions of dollars poured into infrastructure to help increase recycling rates.
In February, wastewater treatment specialist Aerofloat set a new benchmark with a system for one of the nation’s biggest plastic recycling facilities, a PET plant for Circular Plastics Australia in New South Wales.
At the time, the water treatment system brought together all the elements of previous systems that Aerofloat has designed for the industry.
On the back of that project, the company has upgraded PACT Group’s plastics plant in Cheltenham, Victoria with new AeroWAVE technology that allows washwater reuse.
Michael Anderson, Aerofloat General Manager Engineering, says it’s the first time AeroWAVE has been installed at a plastics recycling plant.
The initial cleaning and separating process in plastics recycling requires large volumes of recirculating washwater. This water becomes contaminated and requires regular replacement to avoid odours and contamination of the final recycled product.
Michael says the Cheltenham site had some rudimentary treatment processes in place, including settling tanks and screens which were labour intensive and did not produce high-quality water.
Aerofloat’s system treats washwater to a standard suitable for reuse in the wash system, saving significant water usage and costs. It also means a higher quality and more saleable finished resin.
The PACT system processes up to one tonne of plastic per hour. Some fresh water is added to the wash line to lubricate mechanical equipment and any net excess water that forms part of a trade waste agreement with the local council is discharged into the sewer.
“We create a water recycling loop off their wash line so they can wash the plastic continuously with cleaner water,” Michael says.
Previously, Aerofloat has used the AeroDAF (Dissolved Air Flotation) system that requires a sludge tank and bagging disposal system. Michael says the AeroWAVE eliminates one step in the handling of solids removed from the wastewater.
“This product takes out the need for a sludge tank and puts the solids straight to the bagging disposal system. Depending on the industry and the
Aerofloat’s system for the PACT Group facility treats washwater to a standard suitable for reuse in the wash system.
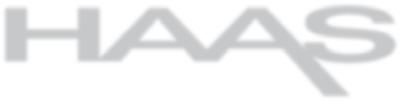
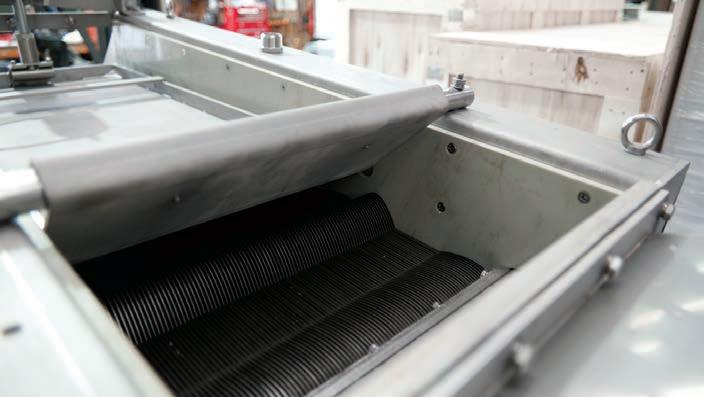
application, DAF still has its place, but for this site we could see the AeroWAVE could bring some improvements and we wanted to try it out.
“So far, all things are going well.”
Aerofloat systems are custom designed to suit individual projects.
For the PACT Group project, the engineering team worked within the constraints of available space in an existing facility, and interstate travel restrictions due to COVID-19.
Michael says PACT Group identified a space for the new treatment system and sent dimensions and photos of the area to Aerofloat engineers, who then created a 3D design of the plant.
“We knew exactly what they needed so put the equipment in that available space and showed them what it would look like in a 3D world.
“The Sydney team designed and built the plant, three staff travelled to Victoria to install it and it was commissioned inside one week.
The wastewater project was supported by the Federal Government’s stimulus package to boost Australia’s plastic recycling capacity as it aims to phase out problematic plastic materials and stop the export of unprocessed plastic waste.
Introducing the AeroWAVE is a first for plastic recycling facilities.
For more information, visit: www.aerofloat.com.au
The strong Viking!
Intelligent 2-shaft shredding
§ Powerful and aggressive § Dynamic shredding programs § Self-cleaning, no wrappage/blockages § Shaft speed infi nitely variable § Rotating direction and reversing
times variable
§ Reliable, minimised downtimes,
highest up-time
§ Solid construction for longer life § Highly effective sound insulation § Maintenance-friendly access § Uniquely low operating cost
The mobile, electric pre-shredder
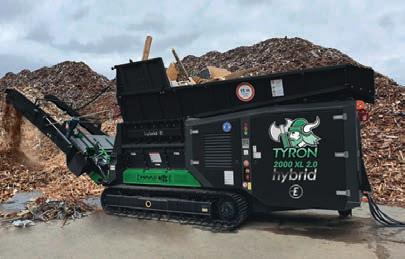
Powerful & effi cient:
§ No exhaust emissions during operation § Minimal maintenance § Signifi cant CO2 reduction § Low energy costs § High energy efficiency
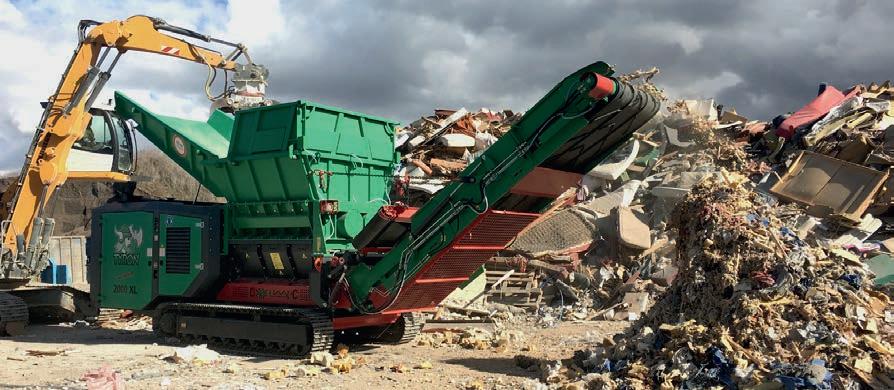