Erin’s legacy
New waste initiative opens the door for economic opportunity in regional areas.
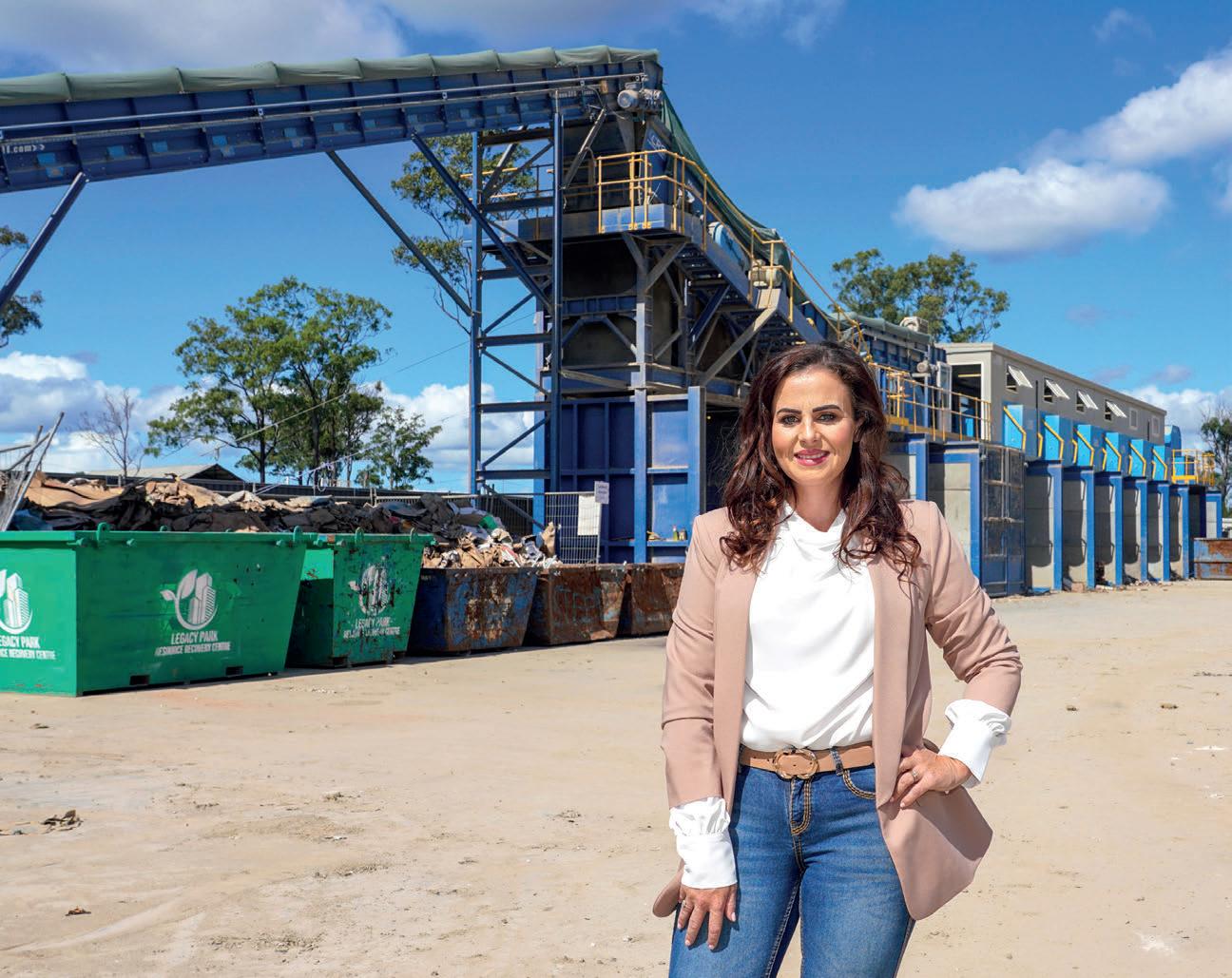
FEATURES Food for thought
A
PROUDLY SUPPORTED BY:


New waste initiative opens the door for economic opportunity in regional areas.
FEATURES Food for thought
A
PROUDLY SUPPORTED BY:
The newly designed WA475-10 features next-generation technology developed with input from customers like you to deliver improved productivity and lower fuel costs. Ideal for waste applications, this gentle giant is a unique solution for tomorrow’s challenges.
Up to 30% more fuel efficient* 8% more breakout force* 20% more boom lift force*
Reducing the waste footprint for future generations by creating a central hub that will be a fully closed circular economy.
Tyrecycle Chief Executive
O cer Jim Fairweather on growing the market for crumb rubber and how to sustain it.
“THIS IS NOT ABOUT DOING THE QUICK, EASY SOLUTION, IT’S ABOUT SUSTAINABLE, LONG-TERM SOLUTIONS THAT HAVE RESULTS.”
- Erin Matthews, General Manager Legacy Park Resource Recovery Centre
Food waste has been described as the sleeping giant of sustainability issues in Australia.
Update from the Victorian Waste Management Association State Conference.
A waste initiative reducing the footprint for future generations.
Wastech has a solid footing in managing demolition and construction waste.
Innovation fuels BINGO Industries’ drive to improve land ll diversion and recovery.
ALLU buckets’ one-step process transforms work sites. 24 CRUSHING WIN
In the rugged world of C&D waste, e ciency and productivity are paramount.
Growing Australia’s crumb rubber market.
SPECIALISED SOLUTIONS
Equipment for any situation, from dust and odour control to heavy lifting.
End-to-end recycling systems to improve material recovery.
Improving waste outcomes and better soil are intertwined for one farmer in the Wide Bay region.
e next generation of aftersales solutions.
37 THIS IS MOTION
Delivering a promise of more choice, more solutions.
40 SWING INTO EFFICIENCY
Short-swing excavators join the eet.
43 MICROMOBILITY REVOLUTION
Bringing global battery safety innovation to Australia.
46 INCREASED EFFICIENCY
Combining power and leading loader technology.
48 ELIMINATING RISK
Asbestos nds highlight the need for consistent policy.
50 AWRE READY
Australasian Waste and Recycling Expo and the circular economy.
53 PRODUCT SPOTLIGHT 57 LAST WORD
How do you create a legacy? Is it what you leave behind, how you make a di erence in the world, or extending positive values to others?
Erin Matthews could claim all the above.
e General Manager of Legacy Park Resource Recovery Centre in Kempsey, New South Wales, is determined to make a di erence for her local community and future generations.
Within a few years she’s transformed a 60-acre site from a discarded rural property to an operational recycling facility that will close the loop on waste and bring economic bene ts to a region hit by high unemployment.
In this edition’s cover story, Erin shares her vision to create a waste free and more sustainable future.
With the help of Waste Initiatives, she’s tackling construction and demolition (C&D) waste. Within ve years she aims to take in all C&D waste from the region’s six councils, diverting it from land ll and manufacturing it into new products. e plan is to replicate the model for all waste streams.
Erin is thinking big, but as she says, it’s not about doing the quick, easy solution. And she’s not alone.
BINGO Industries has made no secret of ambitions to conquer the last mile –nding a solution to divert the last 20 per cent of waste from land ll.
Tara Osborne has led the company’s strategy and innovation for the past ve years, seeking solutions that are commercially bene cial and achieve higher order recovery. We look at some of the initiatives that have BINGO exing its industryleading C&D recovery rates to 90 per cent.
Also in this edition, Ecobatt brings global innovation to Australia to ensure lithium battery safety and sustainability, and Suzanne Toumbourou, Chief Executive O cer of the Australian Council of Recycling, explains how better product stewardship will reward the recycling sector.
Happy reading
CHIEF OPERATING OFFICER
Christine Clancy christine.clancy@primecreative.com.au
PUBLISHER
Sarah Baker sarah.baker@primecreative.com.au
MANAGING EDITOR
Mike Wheeler mike.wheeler@primecreative.com.au
EDITOR
Lisa Korycki lisa.korycki@primecreative.com.au
JOURNALIST
Chris Edwards chris.edwards@primecreative.com.au
DESIGN PRODUCTION MANAGER
Michelle Weston michelle.weston@primecreative.com.au
ART DIRECTOR
Blake Storey blake.storey@primecreative.com.au
DESIGN Laura Drinkwater
BRAND MANAGER
Chelsea Daniel chelsea.daniel@primecreative.com.au p: +61 425 699 878
CLIENT SUCCESS MANAGER
Justine Nardone justine.nardone@primecreative.com.au
HEAD OFFICE
Prime Creative Pty Ltd
379 Docklands Drive Docklands VIC 3008 Australia P: +61 3 9690 8766 enquiries@primecreative.com.au www.wastemanagementreview.com.au
SUBSCRIPTIONS
+61 3 9690 8766 subscriptions@primecreative.com.au
Waste Management Review is available by subscription from the publisher. e rights of refusal are reserved by the publisher
ARTICLES
All articles submitted for publication become the property of the publisher. e Editor reserves the right to adjust any article to conform with the magazine format.
COVER
Cover image: Jeremy Rogers Photography
COPYRIGHT
Waste Management Review is owned by Prime Creative Media and published by John Murphy. All material in Waste Management Review is copyright and no part may be reproduced or copied in any form or by any means (graphic, electronic or mechanical including information and retrieval systems) without written permission of the publisher. e Editor welcomes contributions but reserves the right to accept or reject any material. While every e ort has been made to ensure the accuracy of information, Prime Creative Media will not accept responsibility for errors or omissions or for any consequences arising from reliance on information published. e opinions expressed in Waste Management Review are not necessarily the opinions of, or endorsed by the publisher unless otherwise stated.
Food waste has been described as the sleeping giant of sustainability issues in Australia. Moving the dial will require a multi-pronged approach.
Aland mass bigger than the state of Victoria, 25.73 million hectares, is used every year to grow food that is wasted – enough to ll the Melbourne Cricket Ground 10 times to the brim.
e economic cost is $36.6 billion a year, according to the Food Innovation Australia Annual Report 2020-21. en there’s the environmental impact of the energy, fuel and water used to grow food that may not be consumed, and
the greenhouse gases emitted from food rotting in land ll. At the same time, one in six adults and 1.2 million children regularly goes hungry in Australia.
It doesn’t add up, says Melissa Smith, Horticulture Lead and Technical Account Manager with End Food Waste Australia.
“Everything that goes into creating food is wasted when we waste food,” she says. “We need to stop waste happening in the rst place.”
Melissa is part of a team taking on the challenge of ending food waste and food insecurity in Australia, starting with halving food waste by 2030.
e ght against food waste is a global one. Food loss and waste generates eight to 10 per cent of global greenhouse gas emissions and is widely cited by e United Nations Environment
Programme as almost ve times that of the aviator sector.
Goal 12 of the United Nations Sustainable Development Goals (SDGs), a call to action to end poverty and protect the planet, is to halve global per capita food waste by 2030. Aligning with that goal, in 2017 Australia developed the National Food Waste Strategy to provide a framework to support action toward food waste reduction.
End Food Waste Australia is leading the delivery of the strategy, providing a link between government, businesses, industry bodies retailers and consumers.
Since its inception it has established the Australian Food Pact and sector action plans to guide change. It’s also led Australia’s most
comprehensive research in consumer food waste behaviours.
“Tackling food waste is the single most powerful thing people can do in their everyday lives that will have a positive e ect on climate change,” Melissa says. “We’re about attacking the system at multiple points.”
Early in 2023, End Food Waste Australia, working with the Australian Bananas Growers’ Council, Melons Australia and the horticulture industry, released a rstof-its-kind national plan, pinpointing priority action to reduce fruit and vegetable waste.
Melissa says the horticulture industry has the biggest footprint in food waste in
Australia. It’s important to understand why, where and what can be done.
e Horticulture Sector Action Plan provides a national view of the root cause of horticulture food waste and identi es the most impactful action to reduce it.
Nine key action areas identi ed in the plan aim to reduce fresh produce food waste that occurs at every stage of the food supply chain – on farm, during transportation and manufacturing, and in retail stores.
Interventions include improving food waste data and measurement, exploring whole crop purchasing arrangements, reviewing product speci cations, improving logistics to get fresh produce to food rescue charities, investing in and growing value-add opportunities
and Australia’s upcycled foods market –such as freeze-dried fruits and vegetable powders – along with many more. e objective is to prevent food from becoming waste and keeping it in the human food supply chain. at includes repurposing food, donating it to charity food groups or turning it into stock feed.
“Anything that keeps food waste out of land ll is great, but the most value is keeping it in the human food supply chain,” Melissa says.
“When you’re growing food for humans, the input that goes into that, the care taken, and emissions created are far higher than if you’re creating a compostable product or a fuel source so let’s try and use it for what it was intended.”
Melissa says food waste can be solved, but it is too big a challenge for any one, or any single sector, to tackle alone.
A substantial amount of food is diverted from land ll through four major food recovery services – Fareshare, Foodbank, OzHarvest and SecondBite, according to a fact sheet by the Department of the Environment and Energy.
Grocery retailers Coles and Woolworths have partnered with food recovery organisations. ese partnerships mean that retailers can meet their food waste reduction goals while the charities are able to alleviate poverty and improve food security.
Industry is also exploring and experimenting with di erent ways to reduce food waste.
Since launching in 2021, 32 businesses have signed on to the Australian Food Pact, a voluntary initiative that focuses on preventing waste, promoting food reuse and donation through tailored action plans and site visits.
“We help them gure out what needs to happen and nd new ways to manage their waste,” Melissa says. “Can we prevent food waste in the rst place? Can we use it in another process? Can we donate it?
“We have signatories who have reduced food waste from 500 kiolgrams per product run to 100 kilograms. Others we have helped build relationships with food charities to divert more than 1000 kilograms of fresh produce in the rst month alone, creating meals for people in need, instead of going to land ll.
“In the rst two years the Pact signatories have donated the quivalent 190 million meals to help feed people in need. at’s exciting.”
Melissa says the Pact is gaining traction and will continue to grow as businesses recognise the importance of their social licence and the need to meet stricter sustainable supply codes.
Food waste, she says, is bad for social licence. Studies have shown that 91 per cent of consumers are willing to buy from brands/retailers that disclose information on their food waste and will spend more with companies that support ending food waste. But it’s not just food businesses and industry End Food Waste Australia is working with. Later in 2024 the group
will release a behaviour change campaign aimed at consumers.
e campaign is designed to help people understand how they can reduce food waste in their own homes.
“ ere’s been some amazing research looking at what goes on in the household,” Melissa says.
“We’ve put a lot of work into understanding what groups of community are most likely to waste, what they waste, when and why. All the knowledge is there to target the right information at the right people.
“ e campaign will raise the pro le of food waste and put more pressure on industry to be acting, and show that they’re acting, on food waste.”
While End Food Waste Australia’s journey is relatively short, it is drawing on the international experience of WRAP ( e Waste and Resources Action Programme), a British registered charity working around the globe to tackle the causes of climate crisis and give the planet a sustainable future.
During the past 15 years, WRAP has seen a 23 per cent reduction of food waste in the UK. Retailers have reached, and increased, their 50 per cent food waste reduction target. at success is one of the areas Melissa will look at more closely when she travels to the UK, Europe and the United States as part of a Churchill Fellowship later this year.
She hopes to gain insights into onfarm food waste production activities such as increasing industry adoption and working with other parts of the supply chain.
“Coming from a farming background, one of the reasons I love working in food waste reduction is because it’s tackling a sustainability issue where there are no negatives if you act.
“It’s proven that when you reduce food waste you improve your pro t.
Reducing food waste is great for people and planet. It’s a pure topic to be working on.”
The Victorian Waste Management Association State Conference addresses industry challenges.
Increased waste per capita and lithium battery res in recycling facilities are driving up property insurance costs for the industry. Alan Brett, Head of Commercial Underwriting at Australasian Underwriters, says insurers in Australia and North America are facing challenges due to natural disaster and reinsurance costs.
“In the waste sector when you have losses, if you have res, they are
hugely signi cant. Some would say catastrophic, in insurance terminology,” he said.
“And the problem is, globally they are increasing in frequency, which means that the market is reducing.”
Brett was one of several speakers at the 2024 Victorian Waste Management Association State Conference in May, addressing regulations, insurance markets and battery res.
VWMA Executive O cer Mark Smith said battery res were an industry-wide issue, not just in Victoria, that needed to be addressed. e conference included discussions on battery re updates and guidance by Suzanne Toumbourou, Chief Executive O cer of the Australian Council of Recycling, who said the exponential growth of batteries in the market needs to be addressed before the waste and resource recovery sector faces a tsunami.
Libby Chaplin, Chief Executive O cer of national battery recycling scheme B-cycle, gave an update on a scheme review, while Mike Wilson, Head of Safety at BINGO Industries, provided an industry perspective on battery res and outlined plans the company has to address them.
Outlining the challenges faced by insurance companies, Brett said that waste had grown by 20 per cent in the past 20 years in North America, Europe and Australasia. Global waste is expected to double by 2050.
While that gives the waste sector more investment it also means there’s more combustible components that end up in waste due to public negligence. at was exacerbated by China’s import ban in 2018, which resulted in large amounts of plastic being stockpiled in waste and recycling facilities which were a “signi cant cause of more res”.
“And now, the problem has been turbocharged by an explosion
of lithium batteries entering the stock feed.”
Brett said data from the US and Canada suggests there were more than 300 signi cant res in 2022 at waste and recycling centres – more than in any other year – and the volume of signi cant res in waste and recycling centres in the UK doubled in the past 10 years. e insurance sector anticipates that the same thing is happening in Australia.
“While the waste sector is managing the re risk, the insurance sector is underwriting it.
“Waste recycling, not surprisingly, is highly volatile,” Brett said.
He said there’s been a trend for insurers to reduce their exposure to high-risk businesses such as waste management or exit the sector entirely. Australasian Underwriters is operating
with global insurer Lloyd’s of London to underwrite property insurance in the sector. e company reduces its risk by spreading investments across multiple sectors and locations.
“We work with a number of risk surveys and re engineers to survey every single one of the locations that we insure because we want to better understand the risk that’s been presented to us,” Brett said.
Marissa Katsis, Manager Preventative Projects at Environment Protection Authority Victoria, continued the theme with tips on controlling re risk. And Caitlin Ible, Special Counsel at Minter Ellison addressed key safety issue for the waste and recycling sector.
e second day of the conference included a special presentation of the Victorian Recycling Infrastructure Plan (VRIP) by Peter Laslett,
Director of Sector Strengthening at Recycling Victoria.
e VRIP, due to be released in 2024, will provide long-term strategic infrastructure planning to guide and inform decision making in relation to waste, recycling and resource recovery infrastructure over the next 30 years.
It replaces Victoria’s seven regional waste and resource recovery implementation plans and the Statewide Waste and Resource Recovery Infrastructure Plan.
Smith said the conference was important for the industry to come together and discuss the challenges.
e 2024 conference covered a lot of territory from infrastructure planning and industrial relations through to what the waste and recycling industry will look like in terms of its environmental social and governance contributions.
An aim to reduce the waste footprint for future generations is opening the door to economic opportunity for regional areas.
Tell Erin Matthews she can’t do something – and watch her do it.
A relative newcomer to the waste and recycling industry, Erin is steering a multi-million development that could rede ne waste management for the mid north coast region of New South Wales.
A new construction and demolition recycling plant at Legacy Park Resource Recovery Centre in Kempsey is phase one of a broader vision to close the loop on waste and bring economic bene ts to the area. Erin hopes the hub will one day be a blueprint for other regions to manage their waste.
“ is is not about doing the quick, easy solution, it’s about sustainable, long-term solutions that have results,”
she says. “Waste in regions works. ese type of projects t and align with what Australia is trying to do in reducing waste and creating a circular economy.”
By her own admission, Erin is driven by making a di erence and challenging the accepted status quo. e more people say she can’t, is a driver in itself. And while determination and belief can go a long way to propel a project, Erin also has the numbers behind her.
One of the rst changes implemented when her family bought a skip bin and recycling business ve years ago was segregating waste at the source and introducing a transparent tracking system.
at gave Erin an insight into what type of waste and how much was being
produced per home which allowed her to compare regions. What she found was construction and demolition waste being produced in the region was either land lled or dumped.
Legacy Park was born to provide a sustainable alternative. e mission is to provide innovative solutions for waste management, with a focus on reducing waste going to land ll and reusing products.
“Waste management in regional areas has a di erent set of problems compared to metropolitan regions,” Erin says. “ e viability of having waste sorting to the degree that is needed to divert from land ll just isn’t there. One council can’t a ord the resources to sort all the di erent waste streams.
“I don’t think doing something halfhearted was ever going to be satisfactory. Let’s do it and make a big difference and turn the industry on its head.”
Erin Matthews, General Manager Legacy Park Resource Recovery Centre
“We’re creating a central hub in the region that will be a fully closed circular economy. All waste coming in will be recycled and remanufactured into new products.”
Erin says the hub creates a new economy for a region with high unemployment and gives councils an equal opportunity to participate in the circular economy.
Legacy Park is strategically located on a 60-acre site half-way between Brisbane and Sydney. It currently services a 700-kilometre radius from Bulahdelah to Lismore. Of the six participating councils, three are shipping waste to other areas because there isn’t a local solution.
Floods, res and other natural disasters have added pressure to near capacity land ll.
“ e councils are realistic in recognising we have a waste crisis in this region,” Erin says. “ ey’ve embraced an unorthodox solution.”
ey’ve embraced it so eagerly; they are asking Legacy Park to take on other waste streams. Right now, Erin says, they’re learning to walk before they can run.
In a relatively short time, Legacy Park has gone from being a discarded rural property to an operational construction and demolition (C&D) recycling facility.
Being a leader in sustainability means staying on the cutting-edge of
technology and nding new ways to re-use waste products.
C&D is one of largest waste streams in the mid coast region, with 150,000 tonne sent to land ll annually. With the new recycling plant commissioned in February 2023, Legacy Park is diverting 87 per cent of all waste received and aims to hit 95 per cent.
Australian-owned and operated, Waste Initiatives has more than 30 years’ experience supplying waste management equipment across Australia and internationally.
It’s built a reputation for installing waste solutions for C&D waste, as well as commercial and industrial, food organics green organics (FOGO) and
high-risk waste and has been behind some of the largest recovery projects within Australia.
Trusted global suppliers and distribution partners gives the company a front-row seat to technological advances, helping create pioneering projects to meet the unique requirements of individual waste plants.
Caleb Grimshaw, Equipment Specialist, was part of the team that designed and installed the Legacy Park plant. He says high recovery of recyclable waste streams and minimising land ll costs were key considerations.
Manufactured by Irish company CRS Complete Recycling Systems, the plant has 12 outputs for di erent waste streams and incorporates state-of-the art FlipFlow screens, magnetic separators and fan and suction systems. A picking cabin has an additional six outputs for manual processing.
e plant needed to t the site’s footprint, withstand sometimes harsh outdoor climate conditions, and allow for future growth. Waste Initiatives worked closely with CRS throughout the process to ensure the best results.
“It’s impressive,” Caleb says. “What stands out is the use of technology and how much can be achieved without human intervention.
“CRS has been manufacturing and supplying these types of plants globally since 2009 and C&D is its specialty.
“For Legacy Park, it’s a signi cant investment that is transforming the way their business operates.”
He says what’s unique about Waste Initiatives is the array of products it has to suit client needs. Specialist engineers work with clients to determine the best solution and regularly incorporate systems from multiple manufacturers.
For Erin, it’s Waste Initiatives’ willingness to work with the team on a personal level and understand their vision that stands out.
“ ey were really involved from a conceptual stage and worked with us
through each step. eir team is really open at all levels of consultation, and they are there on the ground to help,” Erin says.
“ ere were a lot of challenges, particular during COVID, but maintaining an open relationship with Waste Initiatives allowed us to deal with the challenges.
“ is is not a project that’s been done here before. ere are changes as you go that only experience can teach you. Waste Initiatives has been open to feedback and their technical support has been great.”
e plant was built on one half of a 90-metre x 20-metre slab. Within the next two years Erin plans to duplicate the plant in a staged approach to increase capacity to 200,000 tonne annually and is working with Waste Initiatives for the next phase.
“ is is a long-term project with a 20-year vision, and we look forward to partnering with Waste Initiatives through every step of that process,” she says.
Now they’re producing two recycled gypsum products – one super ne and one more coarse, giving the option to supply a high-grade product back to processors for new gyprock board or for agricultural use. e end goal is to make new plasterboard on site.
Starting with gypsum was a strategic move. It’s a heavy product that takes up a lot of land ll space, and there’s a demand for it given the region’s soil type and agricultural industry.
Erin says a similar process will be used for plastics – after primary
separation, the plastics will be fed back through the C&D plant as a single waste stream, shredded and extruded into a food grade product. e same process will be used with each new waste stream.
While they’re still developing processes, Legacy Park is working with Waste Initiatives to nd a solution for other waste streams.
“It’s an industry with a really big future,” Erin says.
“In ve years, I’d love to see us taking in all C&D waste from the six councils in the region, diverting it from land ll, manufacturing it into new products and shipping it out for resale.
“In 10 years, waste to rail. We’re ideally located so we can load waste containers in and out via rail. at would allow us to take waste from problem areas and send it back out as a remanufactured product to deliver to the market.
“From there, it’s self-growing and evolutionary.”
Erin has a clear vision of the big picture, but it’s hasn’t always been smooth sailing. She says being a female in the industry was sometimes a hard sell. Others said she’d never get the construction industry to look at their waste di erently. en there was the legislation, red tape and authorities.
She says it did take some e ort to break through, but there was never a ‘give-up’ point, and she believes she has changed people’s perceptions.
To drive such a large-scale change, it’s vital to have a team that shares the same belief both within the organisation and those that you work with.
Waste Initiatives works with many local change makers like Erin. Caleb says the company recognises that the day-to-day demands of running a facility leave little time for sourcing the best technology available. Partnering with
leading international manufacturers in waste recovery equipment, Waste Initiatives brings that expertise to local projects.
“We know that supporting operations with equipment that will run in the harshest of Australian environments is critical,” he says.
“Waste Initiative supports all of its installations with comprehensive local spare parts and back up.”
Legacy Park is a company of family and employees committed to environmental sustainability. e workforce is about 45 strong, by the end of 2024 that will grow to about 100, and within ve years, with a full remanufacturing facility on site, should be at 350.
“Developing and expanding Legacy Park is about creating a better future for our environment and generations to come,” Erin says.
“I don’t think doing something halfhearted was ever going to be satisfactory. Let’s do it and make a big di erence and turn the industry on its head.”
For more information, visit: www.wasteinitiatives.com.au
Erin Matthews and Paul Mosley, Legacy Park Operations Manager, inspect the new plant.The Australian waste management sector is set to advance with the introduction of the BOMAG BC 1173 RB-5, a robust 58-tonne landfill compactor from Tutt Bryant Equipment. Merging decades of design innovation with cutting-edge technology, this model offers superior compaction efficiency and operational sustainability. Notable features include polygon disc wheels, an articulation joint, and eco-friendly engine options such as the Cummins X15 and Mercedes Benz MTU OM473LA. These attributes ensure optimal performance, reduced fuel consumption, and enhanced operator comfort, positioning the BC 1173 RB-5 as a pivotal tool for efficient landfill operations and increased profitability.
Wastech Engineering has a solid footing in managing demolition and construction waste.
Large volumes of waste are created every time a building is demolished or constructed. at waste is now being recognised as a valuable commodity.
Scott Russ, recently appointed Acting General Manager of Sales and Marketing for Wastech Engineering, says there is huge potential to reuse and regenerate construction and demolition (C&D) waste in Australia.
ere are positive signs, he says, with an increasing number of companies seeking to manage their C&D waste stream to drive better sustainability outcomes and reduce their carbon footprint.
According to the latest data in the National Waste Report 2020, Australia generated 27 million tonnes of waste from the construction and demolition sector in 2018-19. at equates to 44 per cent of all waste.
“C&D recycling and processing is a growing area in Australia,” Scott says.
“A transition to a circular economy and additional levies on waste to land ll has driven a lot of behaviour change. Companies are actively seeking better separation of waste before it goes to land ll and capturing the value of commodities.
“We’re involved in several opportunities, assisting companies to design, develop, install, and
process facilities to manage C&D waste.”
Wastech Engineering was established 30 years ago, pioneering waste management equipment, engineering solutions and sustainable resource recovery facilities.
Scott says the focus has always been building products and solutions for the waste and recycling industry that deliver sustainable outcomes and add e ciency.
Over the years the family-owned business has invested in research and innovation to develop unique products. As a result, it has built relationships with trusted international partners that it represents under agency agreements in Australia and New Zealand.
“We’re proud of the product range we have in regard to supporting the industry with sustainable solutions,” Scott says.
“As an industry leader, we provide the resource recovery sector state-of-the-art equipment and solutions with best-inclass products and services.
“Because we have an in-house design, engineering, and production team, we’re able to o er a service from cradle to grave for projects. We can evaluate existing facilities or green eld
sites and make recommendations on the best solutions for a project and opportunities moving forward.”
A key element to sustainability in waste and recycling, Scott says, is better practices at every stage of the waste life cycle. With C&D waste, sorting and processing recyclable materials is fundamental. Ideally a facility would aim to separate and capture at least six waste streams – anything from concrete, stone, timber, glass and metals.
Scott says that while traditional manual picking stations still have a place, technology is integral to modern separation processes to ensure purity of a waste stream. Wastech incorporates optical sorters, air separation, Arti cial Intelligence technology, eddy currents and magnets into its builds.
e ATRITOR Turbo Separator, manufactured in England, is being used to separate the paper and gypsum in plaster board. e paper can be recycled, and the gypsum repurposed into fertiliser.
“Paper is a commodity that has value. We don’t want to see that go to land ll,” Scott says. “With the Turbo Separator we can o er a sustainable solution in separating those waste streams.
“Australia is encouraging a move away from land lls. e land lls we have are limited by air space. We need to look at solutions that reduce the tonnage of waste going to land ll.
“Separation of waste is cost e ective and e cient.”
Another product o ered by Wastech Engineering is the Presto timber crusher which reduces the volume of wood waste into splinters for transportation, storage and recycling.
“Using the right equipment to process construction waste materials greatly reduces the volume of waste at a facility. is means that construction managers can save money on transport, and waste facilities can process more material more e ciently,” Scott says.
Along with innovative equipment, Wastech has years of knowledge and expertise from international partners and lessons learned from past projects to improve waste solutions.
A big part of the company’s success has been a focus on products and services and building strong, longterm partnerships both with suppliers and customers.
Wastech’s Melbourne-based national service centre and a network of technicians across Australia services and repairs all waste and recycling equipment, 24 hours a day, seven days a week. Scott says a key component to investing in equipment is having a good service agreement and plan in place. Infrastructure and equipment are big investments and need to be maintained.
“When we use the word partnership, we mean it,” Scott says. “Aftermarket services for repairs and parts is important to us. We can o er customers a service plan to look after the equipment we have installed.
“We really do o er a great end-toend solution.”
For more information, visit: www.wastech.com.au
Komptech CEA is a leading supplier of machinery and systems for the treatment of solid waste through mechanical and mechanical biological treatments, as well as the treatment of biomass as a renewable energy source. Komptech CEA is proud to provide innovative solutions for handling waste and biomass.
Komptech CEA’s extensive range of products cover all key processing steps in modern waste handling. At Komptech CEA the focus is always on innovative technology and solutions ensuring maximum benefit to the customer.
Like to know more? why not speak to one of our team today?
Where Function Meets Technology
A slow-running, single-shaft shredder suited to all types of
Screening with a Star
Makes waste wood and biomass processing highly efficient.
Less Fuel, More Power
Ideal for shredding all types of wood and green cuttings.
Robust and Reliable
Combining the practice-proven virtues of its predecessors with new solutions for even greater performance.
The Ideal Combination of Performance and Design
With a sturdy frame, powerful hydraulics and large drum, the Topturn X is ready to handle any work situation.
HURRIKAN S
Enhancing the quality of the recyclable output.
Providing effective removal of plastic film from screen overflow.
Innovation is fuelling BINGO Industries’ drive to improve landfill diversion and waste recovery ambitions.
To achieve a waste-free Australia, we must think outside the box. Conquering the last mile – nding a solution to divert the last ~20 per cent of waste from land ll –requires innovation.
BINGO Industries has grown to be one of Australia’s largest construction and demolition recycling businesses. Its processing ability is industry-leading, pushing up to 80 per cent recovery.
It can ex that to 90 per cent by optimising the use of the residual waste stream in sustainable fuels, says Tara Osborne, General Manager of Strategy and Innovation.
BINGO is producing a range of sustainable biomass-rich fuels, using varying degrees of biomass timber content, as a coal substitute for cement kilns and power stations. About 80,000 tonnes of BINGO’s fuel is being used domestically in heavy industries. Now, it’s targeting export opportunities.
“Sixty to 80 per cent of the residual waste stream which is currently sent to land ll is combustible, eligible for
fuel. at makes it perfect for heavy industry,” Tara says.
“Globally, there’s a lot of appetite for biomass. Considering climate disclosures, carbon emissions pro les, and the impetus for heavy industry to decarbonise their footprint and move away from traditional fossil fuels, an alternative fuel is a great di erence maker.
“And it speaks to the very core of our strategy because of its diversion factor. We can divert that last mile.”
Tara has led strategy and innovation for BINGO for the past ve years. She has been seeking solutions that are both commercially bene cial and achieve higher-order recovery.
An innovation hub within the business pools the talents of employees from various teams, including technology, safety, customer experience, sustainability and environment, ensuring the portfolio gets the attention it deserves.
Key projects to emerge from the hub include using Arti cial Intelligence (AI) to set safety zone parameters across all BINGO sites and detecting waste material.
AI for waste material detection is moving to the next phase, introducing infrared scanning technology and sonars that have a greater capacity to scan larger surface areas – and could be tuned to detect asbestos.
Tara says it’s part of BINGO’s approach to implement small pilot projects, prove them, and then scale them up.
“BINGO is unique in that we are constantly evolving,” she says. “We’re
always thinking what else, how can we improve, what tech is available globally, and what are we lacking?”
While BINGO has made a signi cant contribution to the waste industry and in driving the transition to a circular economy by focusing on higher order recovery of materials to help combat climate change, up until recently, there wasn’t a lot of cause for other companies to kickstart their decarbonisation targets.
Tara says the introduction of mandatory climate disclosures in Australia will fuel an increased appetite for action.
Previously, it was mandatory for large companies that met reporting thresholds to report direct emissionsscope one and two – such as fuel for a eet of vehicles or electricity.
Under new climate disclosures, they will also have to report scope three emissions – all indirect emissions that occur across the value chain and are outside an organisation’s control. ese can include employee travel, the extraction and production of purchased materials, and the transport and disposal of waste.
For example, building projects in Greater Sydney are transporting virgin sand hundreds of miles to construction sites because of a critical sand shortage. Tara says climate disclosure rules could be the catalyst for companies to consider recovered sand and products, which means they’re less likely to transport virgin materials hundreds of kilometres, thus reducing their environmental impact.
“It’s the same for alternative fuels – coal is now relatively cheap, so
the springboard to make a change is driven by climate change targets,” Tara says.
“Many heavy industries now have target thermal substitution rates. ey set an incremental rate over years, start small and grow over time. ey always have that baseload of coal but reduce their reliance on traditional fossil fuels through the transition.
“ e bene t of using BINGO’s alternative fuel is that it is not only an alternative fuel but also a product diverted from land lls.”
Another example of BINGO’s path to a circular economy is a land ll gasto-electricity project at Eastern Creek.
While the path from land ll gas to electricity is well-trodden, there’s an opportunity for hydrogen development and hydrocarbons as a sustainable aviation fuel.
It’s assessing all the options and diversion opportunities that keep Tara and BINGO pressing forward.
“ e waste industry is such an exciting industry to be in,” she says. “You can see it moving and morphing into adjacent industries, and we can work closely together. You’ve got the manufacturing element actively involved in product manufacturing, then you’ve got the heavy industries producing a range of recycled products, such as recycled sand for asphalt, and then a range of sustainable fuels being used to decarbonise.
“It’s quite beautiful to see these three industries colliding and creating what we all want: a waste-free Australia with higher order value.”
For more information, visit: www.bingoindustries.com.au
ALLU bucket’s one-step processes are transforming work sites around Australia.
ALLU buckets are helping to scale up the use of recycled materials on building sites across Australia. e ‘transformer’ buckets are increasingly used on smaller, private projects as environmental awareness, recognition of repurposed materials, and cost pressures change the landscape.
“Tip fees are more expensive, nding clean ll is an issue, and everybody knows money is tight,” says Nathan Pullen, Sales Representative for Queensland Rock Breakers.
“With an ALLU bucket, you can keep a project on budget because you don’t have to spend as much on tip
costs, carting material away and then replacing it with new ll.
“As more people realise there is a place for repurposed material, it’s also promoting sustainable practices.”
ALLU buckets screen and separate a range of materials, including soil, sand, gravel, compost, demolition waste, and biomass. ey classify materials into di erent fractions, allowing for the removal of oversized or undersized particles, all on the job site.
Designed for installation on excavators, wheel loaders, tractors and skid steer, a range of bucket models is available to meet the needs of di erent industries.
Feedlots composting manure, and Gyprock manufacturers, are among the industries that have successfully used the buckets to reduce their waste and repurpose materials, says Craig Einam, Queensland Rock Breakers Sales Representative. ere are also now several local contractors who take an ALLU bucket to all their jobs. e team at Queensland Rock Breakers, distributors of ALLU since 2018, has plenty of case studies to highlight the buckets’ e ciencies.
At one project, an ALLU bucket processed more than 18,500 cubic metres of ll material including steel,
rubber, oversized rock, and wood products. About 67 per cent of the material was reclaimed and reused on site.
But perhaps the best case study is from Queensland Rock Breakers itself when the company was building its current Rocklea o ces in 2021.
“We bought out the ALLU,” Nathan says. “We dug out piles and piles of rubbish, screened it, carted away the rubbish and had a whole heap of soil we could put back into the ground.
“ e ALLU saved us thousands of dollars from reduced tip fees, truck movements and purchasing clean ll.”
Aside from the cost savings, the project reinforced the strength of the ALLU bucket. Nathan says decades worth of waste was put through the bucket – including truck rims and engine blocks – and it didn’t skip a beat.
“ e heavy junk stayed on top, we screened the soil and dumped the waste,” Nathan says.
“ ere’s very little you can’t put in the bucket; what you get out the other end is where the value is.”
Craig says there’s not much the team hasn’t tried to process in the past ve years. Some with surprising results – turns out organics matter is one of the highest wearing materials.
It’s the knowledge gained from those trials, such as the best blade combinations and the capabilities of each drum, that the team passes on to customers.
But, Craig says, you still can’t beat an on-the-ground demonstration.
“We know what the buckets can do, let us show you what they can do,” he says.
“One customer wanted to blend two materials together and had never found anything that could do it. We set up a demonstration and the ALLU surpassed what he thought was possible.
“Another customer wrote a cheque on the day of the demonstration once he saw what the bucket was capable of.”
Mobility, Craig says, is another of the bucket’s biggest advantages. You can load the bucket on a truck and easily move it to the next site.
“Recyclers and waste management companies are installing xed plants or large infrastructure to manage waste,”
Craig says. “But with that, where you set up; that’s where you’re stuck.
“For businesses that can’t a ord to build a xed plant, the ALLU bucket is a diverse, mobile processing product.
“It proves you don’t have to be a big player to make a di erence.”
To
In the rugged world of construction and demolition (C&D) waste, efficiency and productivity are paramount. Tutt Bryant has established itself as one of the leading distributors of cutting-edge equipment, including crushers and screeners.
In the evolving construction and demolition (C&D) industry landscape, e ciency and sustainability are not just buzzwords – they’re bottom-line imperatives. is is where C&D waste screeners and crushers come into play. By turning what was once destined for land lls into valuable recycled materials, these machines are revolutionising how the industry handles C&D waste.
Paul Doran is Tutt Bryant’s Business Development Manager. He has been in the C&D industry for 10 years.
“We’ve been the distributor of Metso crushing and screening equipment since 2012,” Paul says. “Metso is a global
leader in high-quality crushers and screeners. We do not just distribute their equipment to the waste industry but also have buyers from the mining and aggregate space.”
According to Paul, the concrete recycling industry has been the biggest growth buyer over the past ve years. As such, Tutt Bryant sells solutions that include support, parts, service, and other essential aspects of after-sales service.
C&D waste is seen as a nuisance stream for many people and companies. However, Tutt Bryant and Metso understand that refreshing
and renewing this into a recyclable, reusable product for road bases and the like is essential.
Paul is convinced that dealing with these waste streams in this manner can help create a circular economy within the waste industry.
“ ere are a lot of large organisations across Australia with very large crushing and screening facilities,” Paul says. “ ey take in C&D waste at their site, and turn it into a road-base or aggregate product to sell to the open market.”
He says Metso machines stand out in several ways, but design is the main di erentiator.
“Metso machines tend to be more robust and have a longer lifespan. We have many Metso crushers and screeners that have tens of thousands of hours of operation so far – some have more than 50,000 hours of operation – and they will continue working for years.”
Tutt Bryant believes each machine is designed and engineered to handle the hard knocks. Metso’s dedicated materials and minerals processing teams have combined more than four decades of experience in engineering and product enhancement across the entire range. Specialists can design a solution to meet any customer’s requirements, resulting in customers achieving optimal performance when it comes to agile, mobile materials and minerals processing.
“We want to ensure that when the customer invests in a machine, it has a long service life,” Paul says. “ is ensures that they get the maximum bene t from their investment.
“Metso has also developed a digital eet management system called Metso Metrics. It allows users to access all the data within their eet of Metso products. It can be used through one portal, enabling operators to plan and record maintenance tasks.”
Metso eet owners can monitor their eet’s performance from anywhere on the planet. e incorporation of an intelligent controller remote (ICR) allows excavator operators to change the crushers and screeners.
“Operators can leave the operators on the machines while making changes on the go. ere is no need to get out of the machine, as the supervisor can pause the feeder, make changes, and then get the operation going again.”
Another bene t is that it caters for the installation of weight scales on di erent belts while monitoring them all from one place.
“Metso is investing heavily in research and development to make the digitisation of the machines easier
for its customers,” says Paul. “It allows users to make informed decisions on what machines to run at speci c times – all designed to help companies become more pro table.”
Paul says the futures of Metso and Tutt Bryant are intertwined, mainly through the expansion of products available to customers. Metso will soon provide a diesel-electric range of crushers and screeners that will increase the exibility of waste management facilities and make companies more e cient, sustainable, and cost-e ective.
“ at will increase revenue for our customers and make them more pro table,” Paul says.
“Our teams are working closely with our customers so we can respond to any issues. Integrating Metso and Tutt Bryant can only be good news for our customer base.”
For more information, visit www.tuttbryant.com.au
Tyrecycle Chief Executive Officer Jim Fairweather on growing the market for crumb rubber and how to sustain it.
A“shakeout” of the Australian crumb rubber industry has driven an increase in demand for quality product.
Jim Fairweather, Tyrecycle Chief Executive O cer, says the market is shifting after an in ux of new players levels out.
Tyrecycle, part of integrated resource recovery group ResourceCo, is well placed to take advantage of the growing market, with the most technologically advanced crumb rubber facilities in the nation operating in Erskine Park, New South Wales, and a larger facility in East Rockingham, Western Australia o cially opened in May 2024.
Frustratingly, for Jim, the market is not growing quickly enough.
He is calling for more investment through government procurement and a collaborative approach to build markets for crumb rubber not just in roads, but in a range of applications, including domestically consumed Tyre Derived Fuel (TDF). Government also must recognise that exports will continue to play a key role in managing Australia’s waste tyres.
“Governments are the biggest procurer of all goods, and they own the road space. It’s important that they show leadership to generate demand for recycled crumb rubber,” Jim says. “ ey will be rewarded for that with investment by industry.
“If the markets are there, industry will respond and build capacity.”
Tyrecycle’s $15 million recycling plant in East Rockingham is a telling example. e plant has capacity to process more than 40,000 tonnes of waste tyres per annum, 7000 tonnes of which will be crumb rubber.
Tyrecycle has invested in the WA market on the back of the Recycling Modernisation Fund and the state government driving procurement – Main Roads Western Australia, the transport agency responsible for the state’s network, has committed to using crumb rubber in its roadworks. e Western Australia plant, combined with facilities in New
South Wales and Melbourne, gives Tyrecycle national coverage. As the market matures, the company is poised to make further investment in the crumb rubber market in Australia.
Jim says commercial viability is also key to building other markets for crumb rubber and industrial applications for tyre-derived products while the market is over capacity.
Industry, government and Tyre Stewardship Australia must work together to target projects that will drive high levels of consumption and have the commercial scale required to process thousands of tonnes of rubber.
With that is a realisation that export markets will continue to be an important o take stream for Australia’s tyre derived products.
e total Australian market is just over 450,000 tonnes annually – 330,000 tonnes of which is end of life truck and passenger tyres, 120,000 tonnes is othe-road (OTR) tyres.
“Tyrecycle alone collects almost 200,000 tonnes. e reality is, Australia’s domestic rubber crumb market is only about 50,000 tonnes per annum, so even if we had all the domestic o take market, we would still have to export,” Jim says. “We need to get governments buying this and specifying the use of crumb rubber in every road project they’re doing. Simultaneously, we need to develop domestic TDF markets.
“Using TDF and crumb rubber more widely in Australia would reduce the reliance on export markets and make our domestic market more robust.”
e bene ts of crumb rubber in roads are well documented. As well as diverting waste from land ll, a road with recycled crumb rubber has proven superior performance when compared to a road without crumb rubber. It reduces re ective cracking; roads are quieter and braking distances are improved.
e carbon bene ts have also now been identi ed in a new report
commissioned by Tyrecycle. Jim says customers across ResourceCo’s portfolio are under increasing pressure to decarbonise. It’s important to understand their drivers and help them reach their goals.
“We’ve commissioned independently veri ed analysis into the very real carbon dioxide equivalent savings of using our crumb rubber and tyre derived fuels. By working with our customers to understand the greenhouse gas emissions savings associated with our products, we’re helping them meet
their technical and sustainability needs,” he says.
“Sustainability requirements on businesses are increasing. It’s well documented that there are strong sustainability reporting obligations on the horizon for all businesses. at’s why we’re prioritising quality and performance, alongside understanding the sustainability bene ts of our products.”
For more information, visit: www.tyrecycle.com.au
Crumb rubber in road surfacing has proven benefits.The Gardner Engineering and Dehaco partnership provides Australia’s waste management and resource recovery industries equipment for any situation.
The urban sprawl is bringing air pollution into the spotlight. Under environmental regulations, waste and recycling facilities across Australia have an obligation to ensure dust from their operations doesn’t harm human health and the environment. Transfer stations, land lls and compost facilities also face strict regulations as authorities try to prevent surrounding communities and the workforce from su ering respiratory problems.
e Dehaco Tera dust control unit is the champion of dust control, says Michael Gardner, Director at Gardner Engineering.
“It’s the new generation of dust control units,” Michael says. “Dehaco has broadened the range of possible applications making the Tera highly e ective for dust and odour control at waste treatment centres.
“With more and more of these facilities closer to neighbourhoods, dust suppression is increasingly important.” e core objective of the Tera is to produce and distribute a ne layer of water droplets that creates a mist of water that captures dust particles.
A recently introduced dosing pump, now allows additives to be combined with the water that can neutralise odours. What sets the Tera apart is a
patented Demto-Rotor. While lime scale and dirt build-up can accumulate on conventional nozzles and require regular maintenance, Michael says the DemtoRotor cannot be blocked.
e droplet size is also adjustable –coarse, medium or ne – saving water and time compared to replacing nozzles.
Available in several models (the largest is 18,000 kilograms with a volume of 6700 litres) to suit industry applications, the Tera’s water spray radius ranges from 25 metres up to 90 metres and can be adjusted to one of three settings: Eco, Eco boost or Power boost. e power consumption in the Eco or Eco boost modes are about 44 to 62.5 per cent lower than in Power boost mode. e savings are increased further when compared with the power consumption to traditional nozzle units.
Michael says the Tera is a mobile unit and can be used in combination with a smaller more e cient generator, adding to their appeal for waste operators.
“ ey’re very e cient and economic,” Michael says. “With operational expenses increasing, costs savings are important.”
What’s also important is trust in a brand. Dehaco’s reputation for quality aligns with Gardner Engineering’s own values.
e Brisbane-based engineering company is known for its specialised manufacturing, rstly in the structural and marine engineering eld and now excavator and earthmoving attachments.
Michael says the company’s knowledge and skills have evolved over the years in line with client demand and the industries in which they work. Change has brought with it the opportunity to partner with Dehaco to bring the European brand to the Australian market.
“Our core priority is to deliver the highest quality product available,” Michael says. “Dehaco has been around for a long time and specialise in the waste, recycling and demolition market. We have con dence in their products.”
Gardner Engineering customers also have con dence in Dehaco products. Michael says Dehaco hydraulic demolition and sorting grabs are soughtafter by waste management and recycling operators. Many are return customers and have multiple units.
“Once a Dehaco hydraulic grab has its claws in something, it is not likely to drop it again,” he says.
“ e weight of the grabs is relatively low, and the volume is large, yet they are powerful, reliable and user friendly. ey are the result of the experience that Dehaco has gained in more than 30 years.”
With models for speci c applications, in dozens of versions from small to large, there is a grab that is suitable for any application.
e smallest model weighs 40 kilograms and has a 30-litre capacity. e largest grab is 13,000-kilograms
with a capacity of no less than 4600 litres. Models with a slewing ring have an unprecedented manoeuvrability, due to a 360-degree hydraulic rotation.
e perforations in the shells provide operators with an optimum view of their work, enabling them to work with the required precision. e dust seal of the hinges provides a lasting, troublefree operation.
From the DSG603 up, all models are provided with two rotation motors, ensuring a much better distribution of forces on the slewing ring. e models upwards from DSG803 are made with two cylinders for an optimum power distribution, allowing the shells to close simultaneously.
Gardner Engineering carries a large range of spare parts for emergency breakdowns, including hydraulic cylinders, rotating motors, cutting edges and pin and bush kits. Grapples to t from ve tonne up to 50-tonne excavators are also in stock.
“We supply some of the larger
waste management companies across Australia. If they have a breakdown that’s time and money they’re losing,” Michael says.
“Because we have full workshop facilities and spare parts, it minimises their downtime.”
Gardner Engineering has been part of Dehaco’s dealer network since 2017 and has quickly made a mark in the Australian market.
In 2022, Gardner Engineering was named the number one dealer, selling the most Dehaco products outside of Europe.
“It’s been a busy couple of years and it’s great to have that recognition,” Michael says.
“We run an engineering company ourselves and are renowned for quality products. It’s good to be associated with another quality brand. We wouldn’t sell an inferior product.”
For more information, visit: www.gardnerengineering.com.au
MECBIO’s waste recycling system offers an end-to-end solution to improve material recovery and reduce environmental impact.
As global populations swell and consumerism reaches new heights, the byproduct is an ever-increasing stream of waste.
e challenge is monumental. e solution – e ective and e cient waste recycling systems – is within grasp, says Dean Dowie, Mecbio Managing Director and Chief Executive O cer.
“In an era where sustainability is not just a choice but a necessity, waste recycling systems stand at the forefront of environmental innovation,” Dean says.
“Waste recycling systems are not just mechanisms; they are a movement towards a greener, more sustainable future.
“When companies invest in such systems, they also increase their environmental stewardship, regulatory compliance, cost savings, and enhance their reputation among consumers and investors.”
Incorporating waste recycling processes allows companies to manage waste more e ectively, recover valuable
materials, and reduce environmental impact. Mecbio designs, builds and services mechanical and biological waste recovery facilities for construction and demolition, plastics and organics waste. It also provides a range of world-class sorting and processing lines, as well as specialist recycling equipment.
It is the exclusive Australasian distributor of RENTEC, a manufacturer of high-duty, robust machines for waste processing and rendering applications.
MECBIO’s recycling systems encompass the entire process from sorting through to screening and shredding. RENTEC supports MECBIO with screening and shredding.
Sorting is the rst step to recycling and is critical in determining the quality of the recyclable material. Automated sorting systems have revolutionised this stage, bringing e ciency and precision. ey can separate materials by type and composition, ensuring that each item is directed towards its appropriate recycling path.
Dean says the RENTEC BagRipper is a new approach to the classic bag ripper or bag shredder. e machine provides constant output with higher separation e ciency and sorting quality, reduced share of residual material, and no damage to the recyclables.
When sorting separately collected lightweight household packaging with a density of 80 cubic kilograms, the
BagRipper can process more than 25 tonnes per hour.
“ e machine is also able to treat the more elaborate plastics such as lms, tapes and ribbons,” Dean says.
Screening lters out contaminants and non-recyclable components and is vital for maintaining the integrity of the recycling stream.
Advanced screening technologies can now di erentiate materials with remarkable accuracy, a testament to the technological strides the industry has made.
e RENTEC Scalpel grader is a unique roller grader. With a 1.6 metre wide x 9.0 metre long grader bed, the scalpel can sort fractions from 0-300 millimetres, without any overlength, from a mixed waste stream. Each roller can be set for height, speed and mutual shaft distance as the application
dictates. If the waste contains little recyclable matter, for example, coarse waste fractions, a driver is con gured to produce as many fractions smaller than 300 millimetres as possible.
Shredding is the transformative process that breaks down bulky items into manageable sizes. is not only facilitates easier handling and
transportation but also prepares materials for the next stage of recycling.
Dean describes shredders as the unsung heroes, tirelessly working to ensure that every piece of waste is given a new lease on life.
e RENTEC Dinosaurus is a stationary, slow-speed, double-rotor shredder with hydraulic drive. It is suitable for the shredding and conditioning of all kinds of solid waste: industrial waste, bulky household waste, construction and demolition waste, green or organic waste, wood, etc.
e processing capacity varies from 15 to 100 tonnes per hour, depending on the input material and the con guration of the rotors and knives.
e Dinosaurus system is equipped with a shredder table that converts the waste into coarse or ne material depending on the selected
program. In addition, the variable speed control allows for production capacity adjustment depending on the downstream processes.
e Dinosaurus is suited to waste-to-energy plants, to sort and recover recyclables and in biogas and composting installations.
“Governments, businesses, and individuals alike must come together to champion the cause of recycling,” Dean says.
“It is a collective e ort that demands innovation, investment, and most importantly, a change in mindset.
“Investing in waste recycling systems is not just as a matter of compliance but is a core strategy for sustainable growth.”
For more information, visit: www.mecbio.com.au
Soil is not always what people think about when it comes to improving waste outcomes. For one farmer in the Wide Bay region, it’s vital to everything he does.
Sustainability and the circular economy are central to many agricultural businesses worldwide.
Australia is no stranger to this. Greensill Farming is one such organisation that believes in sustainable agriculture practices, prioritising the planet’s health and its people.
Based in the rich red soil of the Bundaberg region, Greensill Farming is a leader in environmental and sustainable farming practices. It’s one of the largest growers of sugarcane and sweet potatoes, and has been diversifying in recent years into peanuts and lucerne.
e family-owned business has built a legacy across three generations and nearly 100 years. It continues to develop, research, and invest in agriculture.
“For generations, Greensill Farming has been deeply rooted in the Australian agricultural industry,” says Peter Greensill, Managing Director. “It started with a humble sugarcane farm in Bundaberg, Queensland, and over time, through dedication, innovation, and a commitment to quality, we have grown into one of the leading agricultural enterprises in the region.”
Greensill Farming strives to be a professional, strategic partner focused on quality and continuity of supply for its clients. It also aims to drive the Bundaberg region’s ongoing economic growth and development.
“Our unique approach lies in our unwavering commitment to sustainability and environmental stewardship,” Peter
says. “We prioritise responsible farming practices and embrace cutting-edge technologies to ensure the long-term health of our land and the communities we serve. By combining our agricultural expertise with innovation, we strive to be leaders in sustainable food production.”
Komptech CEA is a leading technology supplier of machinery and systems for the mechanical and mechanicalbiological treatment of solid waste and the treatment of biomass as a renewable energy source. With a product range that includes more than 30 di erent types
of machines, Komptech CEA’s focus is always on innovative technology and solutions that ensure maximum bene t to the end user.
“Komptech CEA has worked with Greensill Farming, speci cally when it comes to Green Solutions Wide Bay,” says Peter. “It is a division of the business dedicated to recycling green waste into nutrient-rich compost. e process uses cutting-edge technology supplied by Komptech CEA including a turner, grinder, and screens.”
ese Komptech CEA machines support the e cient transformation of green waste into high-value compost,
which is then returned to the soil. at contributes to the overall sustainability of Greensill Farming’s agricultural practices.
“Compost improves soil health while also enhancing crop productivity and resilience,” Peter says.
Green Solutions Wide Bay is an open windrow composting facility. It provides Wide Bay residents a free and convenient green waste drop-o and disposal site that turns green waste into compost. e Green Solutions and Greensill Farming team is committed to nding sustainable ways to use and bene t from the region’s natural resources.
“We are proud to play a part in closing the loop of waste management,” Peter says. “As an organisation, we want to ensure a more sustainable future for our farming operations, the local community, and the environment through regenerative agricultural practices.
“By using the facility, Greensill Farming can act to reduce our planet’s carbon footprint, combat pollution, and enrich the soil by giving green waste a new life.”
At the heart of Greensill Farming’s soil restoration and fertilisation
e orts is its innovative green waste composting facility, Green Solutions Wide Bay. is unique and awardwinning facility helps Greensill Farming keep the rich, fertile red earth in peak condition.
“Komptech machines have been instrumental in driving the success of Green Solutions Wide Bay,” Peter says. “ e advanced equipment enables us to streamline and enhance the composting operations, increasing productivity and e ciency.
“Our Komptech eet o ers greater control over temperature, air circulation, and moisture content, facilitating a quicker and more e ective decomposition process. is allows us to produce a superior quality compost product that enriches the soil and promotes healthy crop results on the farm.”
It’s not just about creating better compost. It’s also about improving sustainability outcomes through technology. e Komptech CEA machines have provided a signi cant impetus to better soil health and carbon levels.
“ ese machines contribute to developing high-quality compost,” says Peter. “It is a valuable source of
organic matter and nutrients for the soil. Incorporating the compost from green waste recycling into our farming practices enhances soil structure, water retention, and nutrient availability. Adding organic matter to the soil through composting also facilitates carbon sequestration, aiding our e orts to reduce greenhouse gas emissions and combat climate change.”
Greensill Farming is not resting on its laurels. It plans to further integrate advanced technologies and sustainable practices into its farming operations. New possibilities for precision agriculture and resource e ciency could bene t Greensill Farming and the Bundaberg region.
Peter says that by leveraging the expertise of the Komptech CEA team and their knowledge of equipment and machinery, Greensill Farming is focused on continuing to lead the way in sustainable food production and creating a brighter future for generations to come.
For more information, visit: www.komptechcea.com.au
Turmec launches new Aftersales CRM system, the next generation of rapid solutions providing customers with one central place to order spare parts and services and achieve a faster response time.
Turmec has lead the way in recycling innovations with turnkey solutions for waste management, exempli ed by a worldrst project in Brisbane.
With more than 50 years’ experience in the engineering and recycling industries, it’s now setting new benchmarks in aftersales solutions, with what’s been described as the fastest response time in the marketplace.
All future Turmec projects will have the aftersales CRM system as standard, with QR codes tted, meaning there will no longer be delays in ordering, training or tting spare parts.
Robert ornton, Turmec’s Supply Chain and Aftersales Director, says the new Turmec aftersales CRM system will provide clients with a quicker response time and access to search, nd and order parts 24/7, providing next generation service.
Key features include: easier ordering parts veri ed to t customers’ assets; scanning QR code to instantly access veri ed-to- t parts; 24/7 access to parts ordering and service request; and general support resources, including manuals and PPM’s.
“In our commitment to enhance our customer experience, we are thrilled to announce the implementation of the cutting-edge Turmec CRM system,” Robert says.
“With this innovative system, each plant will now feature a distinctive QR code, making part identi cation e ortless and re-ordering a breeze.
“By simply scanning a QR code, clients now access detailed information
about the machine, including its documents and the various parts.”
Turmec o ers planning, design, manufacturing, installation and support to waste and recycling management companies globally.
From a base in Gaeltacht at Rathcairn, Co. Meath, an in-house team of engineers and designers o er a complete turnkey process, from conceptual drawings to a fully operational plant, for bespoke plants through to solutions for
new or existing plants, and general engineering projects.
In 2018, 2019, 2023 and 2024, Turmec won various awards for its work, most notably Irish Exporters Awards (medium-sized business),
Manufacturing Company of the year from Chambers Business and Irish Steel Association.
Geo Bailey, Turmec Chief Executive O cer, says the team is proud to announce the launch of the aftersales CRM system, leading the way in the aftersales market within the industry.
He says team Turmec is dedicated to nding the best recycling engineering solutions for client requirements, with tried and tested approaches, combined with design expertise, to address speci c requirements.
e goal is to create systems that minimise labour input while consistently extracting high-quality recyclables, achieving maximum throughput with minimal maintenance.
One of Turmec’s key projects is the Turmec/Rino project, the world’s largest state-of-the-art construction waste processing facility in Brisbane.
Geo says this project is a testament to Turmec’s commitment to sustainable waste management and its ability to deliver large-scale, complex projects.
e €30m project began in March 2022 with a timeline for completion by November 2023. e facility processes construction and demolition (C&D) and commercial and industrial (C&I) waste, with a processing capacity of 475,000 tonnes per hour. It’s a world- rst, able to sort through wet and dry waste under one roof.
Upon completion of the plant, Dan Blaser, Rino Recycling General Manager, said the company had scoured the globe and “brought together the best engineers in the world to successfully deliver a leading plant that underpins a strong sustainable recycling industry for Australia”.
Geo says the project is Turmec’s largest, by scale, in its long history in the supply and installation of mechanical treatment plants worldwide.
“Our expertise and knowledge made us the ideal candidate for this project, which is the biggest mixed construction and demolition plant in the world by volume,” he says. “ e solution Turmec created and installed, in collaboration with wet plant specialists CDE, means that varied waste types can be integrated into an automated production line which e ectively separates out the materials allowing for the production of a number of high-quality products such as aggregates and road base. e residual waste can be used as fuel for industrial boilers.”
For more information visit: www.turmec.com
Machine to Material - ALLU Transformer buckets offer the most portable processing solution available by allowing the machine to go to material pile instead of hauling the pile to the machine.
One ALLU can produce multiple fragment sizes with various blade and drum configurations.
For excavators and loaders from 8t to 160t.
Scan for ALLU dealer locations in Australia or visit attachmentspecialists.com.au/allu
Location, runtime, operating angle and more can be viewed and analysed via ALLU app• 360° hydraulic rotation
• Dual rotation motors, from 10 ton weight class
• Interchangeable & reversible cutting edges
• Equipped for the heaviest applications
• Optimum power distribution
• Dual cylinders, from 12 ton weight class
• Adjustable droplet size
• Adjustable maximum throw
• Maintenance free
• Energy efficient
• Adjustable water consumption
• Electrical tilt and rotation functions
• Mobile and fixed installation configurations
With an unparalleled selection of products, expertise and branches nationwide, Motion is living out its promise to provide Australia’s waste and recycling industries with ‘more choices, more solutions’.
“If it moves, we can add value to it,” says Ryan Kendrigan, Executive General Manager of Engineering Services at Motion Australia.
It’s this brand promise that has kept the wheels turning in waste and recycling facilities across Australia in the face of some of the toughest conditions.
As well as often harsh outdoor environments – think land lls and concrete crushing plants – recycling facilities and machinery are vulnerable to contaminants that can wreak havoc on conveyors and bearings. Lubricants in shredding and material handling equipment are an important part of preventative maintenance.
Motion’s lubricants, motors and gears have provided viable solutions that improve the reliability of machinery across a range of applications from metal recycling to construction and demolition waste and organics.
e story of Motion Australia is one that begins more than a century ago, spanning the supply of bearings, industrial drives, motors, lifting, sealing and uid power solutions, as well as engineering services.
“Each business within the Motion family comes with its own speciality. What’s advantageous is that with all these businesses and their specialties consolidated, our customers have an incomparable breadth of o er.”
e Motion family includes longestablished businesses BSC and CBC – which have traditionally supplied bearing and power transmission products to industry – as well as businesses that specialise in uid power such as AIP, Hardy Spicer and Powell, and the hydraulic engineering business, CRAM.
Under each of these businesses is a vast inventory of branded products –totalling more than 600,000 individual items – supported by a network of more than 1600 employees, 180 branches, 30 repair and service facilities and eight dedicated distribution centres.
“Over the past few decades Motion has shifted its focus from being a supplier of componentry to being a full solutions provider,” Ryan says. “We came to the decision through our relationships with customers, and learning what their needs are.”
While some legacy customers may still not be familiar with the ‘Motion’ name, the businesses and brands
within the business are well-regarded. Stephen Forbes, Executive General Manager of Fluid Power Solutions at Motion Australia, says that Motion’s approach is still fundamentally a familybusiness – which is essential to the company’s evolution.
“For most of our history, we’ve operated as a group of family-owned companies and this heritage is re ected in the approach we take today, which is relationship focused,” Stephen says.
“And our customers are looking to us to make it easier for them. ey trust us, the brands that we supply, and the expertise we have to now provide fullservice solutions.”
Broadly, Motion’s businesses can be grouped into three key areas – industrial solutions, uid power and engineering services. As Executive General Manager for Industrial Solutions, Nick Kerwin says the consolidation of the company’s core businesses has had positive implications for customers.
“We’ve worked with many of our bearing and power transmission suppliers for decades and have built on a wealth of expertise both in partnership with suppliers and in our own team,” he says.
“Being able to go to industrial businesses with a holistic o ering – that incorporates everything from traditional rotating componentry to hydraulics, hoses and ttings to bespoke engineering services, training, and even energy e ciency reviews – is hugely bene cial.”
When Ryan Kendrigan began his career with Motion it was with the bearing company, BSC. He has since been part of an evolution that has seen the engineering division grow from being one or two people in each business arm, to some 350 specialised engineers.
“We started out as a bearing company that provided engineering support for traditional rotating equipment,” he says. “Now we can look at anything that’s operating in rotary motion, linear motion or hydraulic motion and provide a turnkey solution that will maximise the e ciency and output of that equipment.”
Ryan provides an example of a solution that was delivered to a steel manufacturer to illustrate how the consolidation of the company and its collective of skilled engineers can bene t customers.
“ e customer needed a custom-built acid tank and one of the key constraints was the space in their facility. We came up with a solution where we half-built the tank in our workshop, then we dropped through the roof, coming through a whole bunch of di erent pipework at the sides, slotted it in position, and then built the top part of the tank once it was in-situ,” he says.
“Once upon a time this would have required six or seven di erent
companies to make that happen. Instead, we created the process and saw the solution executed from concept to delivery – ensuring it was working e ectively afterwards.”
Importantly, the journey is ongoing. While engineering services comprise 14 per cent of Motion’s current revenue, Ryan projects that this will climb to about 30 per cent within the next decade.
Stephen began his Motion career at Hardy Spicer, more than 20 years ago, in hoses and ttings. Today, he heads up the Motion Fluid Power Solutions, which encompasses hydraulic hoses, industrial hoses, mobile service units, and general uid power componentry, such as cylinders, valves, and ltration products.
“It’s quite a large market, and one that has been fragmented with lots of smaller, specialised businesses,” he says.
“A key advantage of us having these specialised businesses under the one umbrella is it makes it a lot easier for customers. We only provide products that meet strict Australian standards and can provide technically precise solutions.”
Importantly, Stephen stresses that the consolidation of brands under the Motion banner will not come at the
expense of the small business mindset that has served many of the company’s customers well for years.
“It’s still vital that we have regional sales reps with strong local connections and knowledge,” he says. “But as part of Motion, they also have access to our extensive network of expertise, which will help them deliver the right solutions and advice to their customers.”
While the general industrial supply side of Motion’s business is its most established, Nick Kerwin is enthusiastic about the opportunities that are unfolding in the industrial solutions space.
“We’ve got a solid foundation in the bearing, power transmission and mechanical drive solutions space, largely due to the relationships forged over the years with our legacy companies BSC and CBC,” says Nick.
“What’s exciting is being able to customise solutions so that businesses don’t have to consult with various suppliers to get what they need.”
Crucially, Nick says, being a customer of any one of Motion’s divisions means customers can bene t from the resources and experience shared between them.
“Our purpose is to keep the world moving,” he says. “ at is what our
customers want. ey want to keep producing and maintaining their equipment to keep them moving, productive, and pro table.”
What does the future hold for Motion?
Stephen says there’s plenty of room for the Motion business to grow both in its geographical coverage and range of solutions.
“We’re always looking for opportunities to extend our capabilities to cover any gaps in our o ering,” he says. “We’re also very conscious of exploring emerging technologies such as renewable energy. Plus, we’re looking to invest further into our e-commerce capability to better enable customers to access the whole Motion o ering.”
For more information, visit: www.motion.com.au
ERIEZ_AU_CPTPAd_WMR_5_24.qxp_Layout 1 5/7/24 4:40
can extract ferrous from virtually any shredded material. High strength suspended magnets provide continuous and uniform magnetic field across the feed belt. We offer a wide range of strengths and sizes to fit every need.
Solutions for:
• Tyre Shredding
• General Recycling
• Ferrous Separation & Recovery
CJD Equipment’s latest offering features the Volvo E-Series short-swing excavators, which are suitable for waste management applications.
The popularity of zero-tail swing excavator models is increasing because of their ease of manoeuvering in congested environments where space is at a premium.
e Volvo E-Series short swing excavators, available in 14-tonne (ECR145E), 23-tonne (ECR235E), and 35-tonne (ECR355E) models, are designed for applications where the excavator needs to operate in tight spaces or near obstacles. ese models
feature a narrow body design with a centrally positioned boom, allowing the excavator to get close to objects and help reduce risk of rear damage as it swings.
Hayden Grant, Product Manager for Volvo at CJD Equipment, emphasises the transformative impact of short-swing radius excavators on safety, highlighting that the Volvo zero-swing design enables operators to manoeuvre with precision, even in con ned spaces where conventional excavators face challenges. By minimising the counterweight
radius, these excavators reduce the risk of causing damage to nearby structures when operating near buildings and other obstacles.
“Reduced and zero tail swing machines address the challenge of limited space by redistributing weight towards the rear, maintaining lifting capacity comparable to standard size excavators while o ering even greater versatility, particularly in Australia’s increasingly constrained work environments,” Hayden says.
With its Stage V engine, Volvo’s short-swing excavators combine robust performance with eco-friendly operation. Hayden says Volvo CE is already ahead of the game for these engines since the company introduced Stage V engines across 56-130kW powerband ranges in early 2019.
“ e E-Series comes with Stage V emission control engines and are classed as one of the most fuel-e cient and cleanest engines currently in use in Australia,” he says.
“ e Volvo Stage V engine, crafted with precision and foresight, has been built to meet stringent requirements and provides several bene ts for original equipment manufacturers and operators.
“For instance, it is dedicated to enhancing productivity by optimising power output, maximising operational e ciency, and ensuring a favourable return on investment. Furthermore, its focus on uptime underscores its robustness, reliability, and maintenance ease, guaranteeing uninterrupted work ow.”
e ECR145E, ECR235E and ECR355E also deliver good fuel e ciency and environmental compliance, reducing operating costs and carbon footprint. e Stage V emission control engine aids with fuel e ciency and compliance with environmental regulations, ensuring economic and ecological sustainability.
e ECR145E has a maximum digging depth of more than six metres and a breakout force exceeding 80 kiloNewton (kN), ensuring superior productivity and performance in waste management tasks such as excavation, loading, and material handling.
Similarly, the ECR235E, weighing about 23 tonne, o ers a balance of strength and agility, enabling it to tackle demanding tasks easily while manoeuvring through tight spaces.
e biggest model in the short swing lineup is the ECR355E, a robust machine designed to handle demanding tasks with e ciency and precision. With its capacity and advanced features, including a maximum digging depth of more than eight metres, and a breakout force exceeding 150 kN, the ECR355E is a testament to Volvo’s commitment to delivering excellence in construction equipment.
Hayden says what sets the E-Series apart is its integration of advanced technology. Optional Dig Assist technology, part of the Volvo Co-Pilot system, empowers operators to achieve optimal performance with good precision. is intelligent interface provides real-time insights and guidance, ensuring tasks are completed accurately and e ciently. From trenching to site levelling, Dig Assist streamlines operations, minimising errors, and maximising productivity.
“Dig Assist o ers exceptional control, whether you’re digging trenches, levelling sites, or grading slopes, and provides real-time data for a responsive and e cient operating experience,” he says. “Once the pre-set operating limits are met, the Volvo Co-Pilot automatically alerts the operator through audio and visual signals.”
Dig Assist o ers three tiers of techassisted options to cater to various project needs. e standard 2D package simpli es complex digging processes, while the In-Field Design (IFD) and 3D options enhance accuracy for largescale projects. With features such as GPS and RTK navigation technology, operators can achieve precise excavation results without extensive marking or manual intervention.
Moreover, the Volvo Co-Pilot system enhances operator comfort and control with an intuitive touchscreen interface that centralises all excavator functions. From selecting operating modes to managing joystick buttons, operators can focus on the task without distractions, thus optimising work ow and safety.
e Volvo E-Series excavators, backed by CJD Equipment’s national product support network, give customers con dence in their investment. With their expertise and commitment to customer success, CJD Equipment ensures operators reach their full potential, making the Volvo E-Series excavators ideal for any earthmoving or civil construction job.
For more information, visit: www.cjd.com.au
E-Series advanced technology empowers operators to achieve optimal performance with precision.
Ecobatt brings global innovation to Australia to ensure lithium battery safety and sustainability.
Aquiet revolution on wheels is gaining momentum in Australian suburbs. e rise of electric bikes (e-bikes) and electric scooters (e-scooters) is shifting how Australians traverse their cities and towns.
is burgeoning industry not only signals a shift towards more sustainable urban mobility but also introduces new challenges in the realms of safety and waste management, in particular lithium-ion batteries.
Australia’s engagement with micromobility, (a relatively new term, comprising di erent transportation technologies, such as e-scooters and e-bikes) is not just a eeting trend but a robust economic contributor.
A landmark study by We Ride Australia reveals that the e-scooter segment alone contributed $728 million into the economy in 2022, with 3.6 million users taking to the streets. e Australian Capital Territory (ACT) leads the charge with the highest per capita consumption of e-scooters, spotlighting a growing enthusiasm that spans across age groups, particularly among those aged 18-34, who represent 35 per cent of the user base.
Lithium-ion batteries are proven safe when handled with care and within manufacturer speci cations. In rare circumstances if overcharged, they can overheat resulting in a re. Fire and Rescue NSW reported a startling rise
in res caused by these devices recently, recording an average of six lithiumion battery-related incidences a week in 2023-24. is trend underscores a crucial need for enhanced safety measures at home and at work.
In response to the growing safety concerns associated with micromobility batteries, industry leaders and safety experts are advocating for rigorous industry standards and innovative safety solutions.
David Cooke, from Ecobatt Safety, anticipates that Federal and State Government agencies will soon make recommendations for the safe storage, charging and disposal of electric scooters. e guidelines are expected to address a need for standardised safety protocols to mitigate risks associated with micromobility devices to reduce re incidences.
Building on its safety premise, Ecobatt o ers UN-rated Lithium-ion Safety Drums, available in 53-litre and 62-litre capacities.
“As we observed developments across the globe, it became clear that integrating advanced safety technology with our battery recycling e orts was essential,” David says.
“ ese Lithium-ion Safety Drums represent a signi cant advancement in the safe handling and storage of micromobility batteries.”
e specialist battery drums are designed to contain used, recalled, or potentially damaged batteries that may
Lithium-ion Safety Drums are designed to contain used, recalled, or potentially damaged batteries that may be prone to thermal incidents. Images: Ecobatt.be prone to thermal incidents. ey are suited for secure storage of used and new lithium-ion batteries for businesses specialising in electronic repairs, and any other retailers or commercial entities dealing with lithium-ion batteries and battery powered products.
e Ecobatt Lithium Safety Drums also suit work sites, schools and universities, apartment complexes and residential units, o ering peace of mind when it comes to protecting physical assets and the safekeeping of micromobility lithium-ion batteries.
e drums are constructed from 0.7 millimetre-thick steel and reinforced with structural ribs. ey’re engineered to withstand severe impacts and stress, maintaining integrity under various transport and storage conditions.
David says this durability is vital in preventing physical breaches that could expose the batteries held in rare circumstance to external threats and contribute to internal failure.
Danish company InsPyro, a consultancy company in the eld of high-temperature processes, tested the drums to con rm their e cacy and dependability.
Tests found that the ame-arresting lter incorporated into the drum’s lid con nes a potential lithium-ion battery re to the interior of the drum. is lid is engineered to release pressure from internal gases. e drum’s design and added vent prevents any ames from passing through.
e overpressure system in these drums consists of a pair of metal plates
integrated with a ame-arresting lter. is system acts as a critical safety valve, allowing the safe release of gases that could build up inside of the drum during a thermal event, thus preventing pressure build-up that could lead to a potential uncontrolled and harmful energy release. is feature also blocks any external ignition sources from reaching the drum’s contents, e ectively isolating the lithium-ion batteries in a controlled environment.
e internal non-conductive epoxy coating of the drums adds another layer of safety. e coating protects the drum’s material from corrosive elements that could weaken its structure over time, thereby extending the life of the drum and enhancing the safety of its contents. e drums are also hermetically sealed with a polyurethane (PU) seal and a steel closing ring, ensuring that no hazardous materials escape into the environment and no external contaminants enter the drum.
For those wanting a more compact solution to safely store and charge their micromobility batteries, there are CellBlock Safe Charge Sleeves – the ‘E Series’, designed for protection of highenergy lithium-ion batteries for devices ranging from drones to e-bikes, catering to 800WHr capacities.
Ecobatt Safety is the exclusive Australian and New Zealand distributor of CellBlock Fire Containment Solutions, USA. ese sleeves feature a multi-layered FireShield composite material and have been tested by Aeroblaze, a heavy anti-air unit used by the United States, and aviation service AccuFleet.
David says the sleeves are proven to contain battery res and potential explosions in lithium-ion battery assemblies even at full charge.
For larger scale multi set charging needs, Ecobatt o ers the CellBlock Safe Charge Battery Racks, equipped with re-resistant barriers and CellBlockEX’s
re suppression system to prevent a spread of a battery re between charging bays.
Constructed with durable powdercoated steel and aluminium, and a rechargeable re containment and extinguishing system, the racks are best in industry, equipped with heavyduty locking wheels to ensure safe,
There are growing safety concerns around the fire risk of lithium batteries in electric bikes and scooters. Image: BLACKDAY / shutterstock.com
mobile storage. Complementing the racks is the CellBlock Safe Charge FireShield, a textile cover tested to withstand temperatures of more than 1000 degrees Celsius and safeguarding a thermal runaway event while providing convenient access to the charging interfaces. e shield is included with each rack.
“ e range of CellBlock products Ecobatt o ers, exempli es our commitment to combining the latest technology in materials advancement and high-tech safety products for not only the evolving landscape of micromobility but also other high energy lithium-ion battery equipment applications, such as medical, commercial and construction industries,” David says.
“As Australia continues to navigate its micromobility journey, the focus
must not only remain on promoting these environmentally friendly transport options but also on ensuring safe charging, storage and end-of-life recycling options for all users and the community at large.
“ e integration of innovative safety technologies like those from Ecobatt Safety represents a critical step towards securing a sustainable and safe future for micromobility and all lithium-ion batteries used.”
David says the path forward involves an in-depth collaborative e ort among manufacturers, safety experts and policymakers to guide consumers to foster a culture of safety with the correct equipment tailored to suit most applications.
For more information, visit: www.ecobatt.net
• Tyre Recycling
• Aluminium Recycling
• Cable Recycling
• Electronics Recycling
• MSW Recycling
• Fridge Recycling
• ASR Recycling
• Various Scrap
• Car Battery Recycling
• Conveyor Belt Recycling
• Solar Panel Recycling
• *NEWS* Optical Sorting
SORTING MPS - Multi Purpose Sorter Intelligence & Artificial Vision
SPS - Small Purpose Sorter theSPShere!
• High-resolution camera
• State-of-the-art NIR technology
• E xceptional separation ratios
Komatsu has introduced the WA475-10, 26-tonne wheel loader to Australian shores. This versatile machine combines power with Komatsu’s loader technology to provide an efficient and productive model for waste sites.
The newly designed WA47510 features next-generation technology developed with customer input to improve productivity and lower fuel costs. Ideal for waste management and quarry applications, this gentle giant is a unique solution for tomorrow’s challenges.
e WA475-10 o ers 30 per cent more fuel e ciency than the previous model. It is ideal for hauling or loading jobs with outstanding fuel e ciency, productivity, and ease of operation.
Nick Vrontas, Komatsu Australia’s National Business Manager, says the WA475-10’s upgrades make it an appealing addition to waste eets.
“ e WA475-10 features the newly developed Komatsu Hydraulic
Mechanical Transmission (KHMT), an innovative solution that makes the loader more powerful and fuel-e cient. Variable speed control allows operators to adjust the machine’s top speed to meet speci c site requirements, and the adjustable variable traction control also limits wheel spin on unstable and slippery ground conditions often found on waste sites,” Nick says.
“We’ve also completely innovated the power control on this latest model. It’s never been easier for an operator to nd the right balance between traction and lifting power.
“ e hydraulic speed is independently controlled by the accelerator pedal, and the hydraulic lever controls the boom speed.”
An optimised Z-bar linkage system provides much more lift force and a higher tonnes-per-hour production rate on the WA475-10, and the response time of the hydraulics and the dumping or lifting can be set to speci c waste site requirements.
“ e WA475-10 engine is Tier 4 compliant, and at even low engine speeds, it puts out high power and delivers more engine torque and performance. e engine’s advanced electronic control system manages the air ow rate, fuel injection, combustion parameters, and after-treatment functions. All combined, this control system provides optimised performance, reduced emissions, and advanced diagnostic capabilities, making it a powerful yet environmentally friendly machine,” Nick says.
“ e loader can also be tailored for speci c applications, whether that is the demanding nature of a waste site or the abrasive environments of quarries.
e Komatsu team will work with customers to provide a solution tailored to the loader’s application, from enquiry to post-delivery, maintaining service checks and requirements.
“We’re beyond excited to have the loader on our shores and to introduce it to many waste sites across the country,” Nick says.
For more information, visit: www.komatsu.com.au
“OUR LONG-STANDING PARTNERSHIP WITH WASTE INITIATIVES ENSURES AN EFFICIENT C&D RECOVERY PLANT BACKED UP WITH LOCAL SUPPORT AND PARTS.”
ErinMatthews - CEO of Legacy Solutions Group
We collaborate closely with our clients to help them maximise the efficiency of their waste streams. Our approach involves designing, constructing, and implementing engineered systems tailored to meet each client’s unique requirements. We provide market-leading solutions for recycling plants, including C&D, C&I, Tyre Recycling, Compaction, and Shredding Systems.
Our nationwide support network ensures uninterrupted operation and peak performance from day one, backed by local supply of parts.
View our case study
The peak body for Australia’s organics recycling industry says recent asbestos finds highlight the need for consistent policy.
The discovery of asbestos in mulch across multiple states has highlighted the importance of controls and monitoring in the waste and resource recovery sector.
e Australian Organics Recycling Association (AORA) has long advocated for consistent policy and regulatory settings that promote the delivery of clean, source-separated organic feedstock without plastics, chemicals and other contaminants, to organics recycling facilities.
National Executive O cer, John McKew, says hazardous materials and contaminants from all feedstock streams are one of the most signi cant threats to the future success of recycling and the circular economy.
“We are alarmed with the growing number of sites a ected and the impact this is having on the industry as a whole and con dence in recycled organics products,” John says. “AORA promotes quality assurance as a whole of value chain responsibility – from feedstock receival, processing, transportation though to application of materials for end use. rough this approach, potential risk to human health and the environment is minimised and quality products prevail.
“ ose carrying out resource recovery activities across Australia are particularly concerned about the increased level of risk that they now face in relation to the presence of potentially invisible asbestos in their input materials, which is an issue over which they often have minimal control.”
Traces of asbestos in mulch were found in dozens of sites across New South
Wales healthcare facilities, hospitals, and public spaces in January 2024. e NSW Environment Protection Authority (EPA) has been investigating the discovery with the support of the NSW Asbestos Taskforce.
In Victoria, asbestos was found in mulch at parks and reserves in March and April. After more than 30 inspections, EPA Victoria said that less than half a shopping bag of suspect materials was found, removed and sent for testing.
It was believed some of the asbestos fragments found may have already been present on site or could have been illegally dumped.
In early March, the environmental watchdog carried out proactive inspections at 59 commercial mulch producers that use recycled timbers and found no asbestos contamination in mulch at any of these premises.
John says AORA understands the concerns about the incidents, but it was important to note that the Australian Organics Recycling Industry does not use, or add, asbestos in the mulch production process. And while producers will not knowingly accept asbestoscontaminated feedstock, detection of asbestos within feedstock is di cult.
At a Victorian Waste Management Association seminar in March, environmental lawyer Stefan Fiedler described it as “like looking for a black sock in a tub of black socks”. He said vigilant processes are vital as the nation’s targets to divert organics from land ll, and a transition to a circular economy, results in more construction and demolition waste in organics processing.
John says the Australian Organics Recycling Industry has been manufacturing and supplying quality products in large volumes for decades and remains committed to producing high-quality and high-performing compost and mulch products that are safe for application to land and to human health.
Maintaining product quality and regulatory compliance are key to protecting the livelihood of the recycling organics industry.
“AORA supports all e orts by regulators to eliminate the risk of asbestos within all feedstock streams that are destined for recovery and any compliance action being taken against organisations that are shown to do the wrong thing, across the supply chain,” he says.
Illegally dumping asbestos now carries a multi-million dollar ne under new laws passed by the New South Wales Government in November 2023.
For more information, visit: www.aora.org.au
With discussions of a circular economy becoming more prominent, there is no better time to participate in the Australasian Waste & Recycling Expo (AWRE) this year in Sydney.
The push for a circular economy seeks to eliminate waste and pollution, recirculate products and materials, and regenerate nature. It’s a system with resilience at its core and is good for businesses, people, and the environment.
Australians are looking to the waste and recycling industry to drive positive change.
Australasian Waste & Recycling Expo (AWRE) is the premier business event for the waste, recycling, and resource recovery sector. It is where industry leaders and decision-makers come together to create a world of solutions for a cleaner, more sustainable future.
Presented by Diversi ed Communications, the exhibition and conference bring together policymakers, enterprise leaders,
educators, and professionals to share ideas and solutions.
As AWRE continues to expand, there is a broader focus on recycling and resource recovery, which is at the heart of a sustainable future.
Representatives from food and organic waste solutions, e-waste, software and technologies, and medical waste are among the industry sectors attending AWRE. ey will give attendees new insights into the challenging opportunities to recover, recycle, and reuse the unique materials from these waste streams.
“We’re excited to bring AWRE 2024 to the sustainable waste management and responsible resource recovery industries in July with an
overarching theme of Transitioning to a Circular Economy,” says Ali Lawes, Event Director at Diversi ed Communications. “We will have a bigger and more diverse show oor. We will showcase vital product solutions and the latest cutting-edge technologies for the sector.”
New for 2024 will be a Packaging Pavilion conducted in partnership with the Australian Institute of Packaging (AIP). Ali says the continued collaboration between AWRE and AIP, the peak professional body for packaging education and training in Australasia, is an opportunity to exhibit new outcomes in the packaging industry. She says the seminars AIP will present will be highly educational for multiple stakeholders and attendees.
Over two days, attendees can immerse themselves in live events curated to unveil cutting-edge concepts and limitless possibilities within the industry.
As waste management takes the spotlight in today’s landscape, AWRE is the gateway to connect with forward-thinking pioneers, forging new relationships that propel ecofriendly advancement.
“AWRE o ers a unique platform for our industry to converge, share success stories, and openly discuss the key roadblocks to achieving success in our collective goal of transitioning to a
circular economy,” says Ali.
Visitors attending include small and large businesses, local councils, state governments, industry thought leaders, environment and sustainability leaders, and waste innovators. Ali says waste problems touch all industries in the economy, so the sectors that are attending are diverse.
“ ere are many opportunities for networking and learning,” Ali says.
“ at’s before we look at discussion panels featuring esteemed speakers from, among others, the Australian Council of Recycling, the Australian Packaging Covenant Organisation, and NSW Fire Rescue. at’s just a small sample of the people and organisations speaking and presenting as part of a comprehensive conference program.”
e AWRE 2024 Summit, sponsored by NSW EPA, forms part of the free-
to attend seminar series across the show oor.
e Australian Organics Recycling Association (AORA) is returning with its AORA Organic Zone. e dedicated area will highlight the growing importance of the organics recycling sector and present the latest innovations and technology in organics and food waste management.
More and more waste and recycling professionals want to see the latest solutions servicing the industry, and the AWRE Innovation Zone on the exhibition oor is the place to do so. It will provide a unique opportunity for exhibitors to showcase their groundbreaking products and solutions.
Similarly, the Recycled Zone will
spotlight new and innovative products and materials made entirely from recycled or repurposed materials. It provides a newly imagined opportunity for exhibitors to showcase their business to the growing market.
For more information, visit: www.awre.com.au
AGRICULTURE FARMING EDUCATION WASTE
MANAGEMENT RESOURCE MANAGEMENT
CONSERVATION MANUFACTURING RESOURCES
ENERGY HEALTH & SAFETY INFRASTRUCTURE
ENGINEERING MINING CONSTRUCTION
QUARRYING AGRICULTURE FARMING EDUCATION
WASTE MANAGEMENT RESOURCE MANAGEMENT
CONSERVATION MANUFACTURING RESOURCES
ENERGY HEALTH & SAFETY INFRASTRUCTURE
ENGINEERING MINING CONSTRUCTION
QUARRYING AGRICULTURE FARMING EDUCATION
WASTE MANAGEMENT RESOURCE MANAGEMENT
CONSERVATION MANUFACTURING RESOURCES
ENERGY HEALTH & SAFETY INFRASTRUCTURE
ENGINEERING MINING CONSTRUCTION
QUARRYING AGRICULTURE FARMING EDUCATION
WASTE MANAGEMENT RESOURCE MANAGEMENT
SEARCH FOR TOP INDUSTRY TALENT THROUGH OUR JOBS BOARD.
CONNECT WITH ALIGNED CANDIDATES.
BOOST YOUR CHANCES OF FINDING SKILLED APPLICANTS.
SCAN TO CREATE AN ACCOUNT TODAY AND DISCOVER YOUR PERFECT MATCH!
The ALLU M-Series bucket is a versatile attachment designed for large-scale material processing and screening applications.
Compatible with large excavators and wheel loaders, the M-Series is ideal for screening, crushing, mixing, and loading waste materials, among other tasks.
The use of the M-Series bucket can eliminate the need for material processing equipment and reduces the need for material double handling, increasing efficiency and productivity.
It’s environmentally and economically beneficial –processing materials on site minimises waste, optimises resource use and reduces transportation costs.
The M-bucket is designed to be user-friendly. Attaching it to earthmoving machinery is straightforward, allowing for quick setup and operation. The M-Series bucket is recommended for attachment on excavators at job sites that require speed and reach.
When equipment mobility is a criterion, such as a bulk material storage sites, the M-Series buckets mounted on wheel loaders are well suited, bringing the machine to the material.
Expanding the demolition excavator line offering, the new purpose-built Cat® 330 Straight Boom excavator delivers exceptional performance in low-level demolition applications.
Offering a maximum digging depth of 19.1 ft (5.8 metres), the new straight boom excavator features a vertical reach of 40.9 ft (12.48 metres), which is 8.0 ft (2.45 metres) higher than a standard Cat 330 excavator. The 330 SB is also matched to a wide range of tools, including hammers, multiprocessors, demolition grapples, pulverisers, and quick couplers.
The new 330 comes with a range of standard Cat technologies that enhance machine versatility, precision and efficiency. Powered by the fieldproven 275 hp (205 kW) Cat C7.1 engine, it offers three power modes – Smart, Power and Eco. They intelligently match engine and hydraulic power to the task, reducing fuel consumption. The excavator’s electrohydraulic system handles different types of materials, while the standard quick coupler, medium and high-pressure circuits allow for the use of a variety of Cat demolition attachments.
By using sophisticated design software and unique magnetic circuits, Eriez provides permanent and electromagnetic scrap drums with deeper magnetic fields to reclaim ferrous materials in automotive shredder residue (ASR), materials recovery facilities (MRF), municipal solid waste (MSW), scrap metal yards, wood waste, slag, incinerator bottom ash, foundry sand, and minerals processing applications.
This design uses permanent magnets and bucking poles to project a deep magnetic field capable of removing ferrous from up to 380 millimetres (15 inches). These permanent scrap drums are ideal for applications with limited or unstable electrical power.
The All Electro Agitator type uses a deep field rectangular core pickup magnet to reach out and grasp the ferrous, and a second rectangular-core agitator magnet to flip or agitate the ferrous, cleaning it of contaminants such as loose mud, paper, fluff, and trash.
Eriez also offers a non-agitating transfer design that uses a deep field radial pickup magnet and pole shoes to convey or transfer the ferrous around the drum shell to the discharge area.
The Peterson 2710D is engineered to meet the demands of operations requiring frequent transitions between tasks while maintaining high production standards.
Boasting a robust design and powered by the Caterpillar Tier II C18 765 hp (570 kW) engine for the export version, the 2710D’s mobility, combined with heavy-duty construction, sets a new standard for throughput for machines of its size.
Featuring a generously sized feed opening, 153 x 81-centimetres, and boasting a maximum lift of 112 centimetres when enhanced by Peterson’s high lift feed roll, the 2710D accommodates a variety of feed stock shapes and sizes. This expansive feed opening stands as one of the largest in its class.
The quick-change multiple grate system empowers users to tailor grate configurations, enabling the production of a range of finished materials precisely to desired specifications. Grate adjustments are simplified through an easily accessible side wall door.
Equipped with triple grouser 50-centimetre-wide tracks, the 2710D excels in manoeuvrability even in challenging terrains. The advanced three-stage grinding process, characterised by a powerful up-turn mechanism, ensures superior material fracturing and consistent
product quality. The Patented Impact Release System, featuring air bags, makes certain uniform grinding and protecting against contaminated feedstock – a feature exclusive to Peterson grinders.
As a second line of defence, the Impact Cushion System, comprising urethane cushions and shear pins, shields the mill from potential catastrophic damage resulting from severe impacts caused by contaminants in the feed stock.
Recognising excellence across the waste and resource recovery sector. Sponsorship opportunities are now available for 2024.
www.wasteawards.com.au
Better product stewardship will reward the recycling sector.
Suzanne Toumbourou, Chief Executive Officer of the Australian Council of Recycling, explains.
We all want the recycling sector to grow and prosper. Good recyclers do vital work, and do it to a high standard, addressing environmental and social priorities while advancing economic outcomes.
As the pre-eminent industry forum for recyclers, Australian Council of Recycling (ACOR) is focused on leading the transition to a circular economy through the resource recovery, remanufacturing and recycling supply chain. We spend a lot of time talking to recyclers about what’s needed to support a thriving industry.
A clear message has arisen from recyclers about a key element that can
create more opportunities for the sector: better product stewardship.
ese days, we’re all familiar with one or more product stewardship initiatives. From beverage containers to batteries, these programs make it their missions to take responsibility for the end-of-use management of their products.
And we all know how much the priority of a circular economy has transformed the context of waste. Years ago, materials had a linear ow: ‘take, make, waste, disappear’. ese days, it is an imperative for recovered materials to re-enter the market, in a t-forpurpose-way, through the recycling value chain.
Here’s how high-quality product stewardship schemes can support better circular economy outcomes and greater opportunities for investment in bestpractice recycling.
First, design for recycling and reuse must be prioritised. Building in a priority of recyclability creates more certainty for investment in recycling infrastructure and, of course, less waste.
Next, there must be robust market demand for recycled materials and the products made from them. With a focus on markets for recycled materials, product stewardship initiatives can support more value, scale and ongoing viability of recycling.
Strong signals from government can do a lot to strengthen markets. In the UK, governments set a minimum recycled plastic content for plastic items.
e certainty and clarity of the new rules created a stable, reliable market for recycled polymers, sparking a urry of investment in the sector.
Scale is critical, as is addressing the true cost of recycling processes. In Australia, there is a high cost to labour, energy, transport, infrastructure, and the research and development that keep recyclers growing. Our products also need to compete with the price of new, mostly imported, non-recycled products.
Developing markets, both at home in Australia and overseas, means governments and industry will be more inclined to properly invest in necessary
“Developing markets, both at home in Australia and overseas, means governments and industry will be more inclined to properly invest in necessary infrastructure.”
Suzanne Toumbourou CEO, Australian Council Of Recycling
infrastructure including collection points, storage, logistics and processing. Enhanced collection infrastructure ensures that material can be aggregated at su cient volumes, helping recyclers to grow.
In many cases, consumers will also need incentives, such as deposit schemes, to encourage them to dispose of products correctly, supporting source separation and diverting hazardous items such as batteries from conventional waste and recycling streams.
Another bene t of good product stewardship is the positive perceptions
they can create for the recycling sector. Goodwill can be fostered when people can clearly see that their end-of-use product is genuinely recycled into something useful.
Protecting ourselves from negative perceptions is essential to keep our industry strong – and that means tightening product stewardship scheme governance. From scandals where collected items haven’t been recycled, to a general perception that “they don’t really recycle these things do they?”, negative publicity quickly erodes social licence and drives poor recycling
behaviours. is ultimately results in challenges establishing new projects, along with more contamination in recycling streams – adding expense and ine ciency.
Another part of the mix is compliance and consequences to ensure that product stewardship schemes are held to account. A system of ‘bespoke’ accreditation schemes run by brand owners can lead to self-reporting, skewing the data and potentially creating a system where what’s cheap and easy is prioritised over genuine and high value recycling outcomes. A good way to address this would be an overarching recycler-led accreditation program, ensuring that all schemes align to consistent metrics, and good recyclers can be fairly assessed.
For more detail on the opportunities for the recycling industry created by product stewardship, see our recent report Recyclers in Product Stewardship. Better product stewardship will support a stronger recycling sector, ensure fairness for operators, and help make our economy truly circular, bene tting jobs, businesses and environment – and that’s good for everyone.
We recycle almost 20 million used tyres from across Australia each year. Whether helping industries reduce their reliance on fossil fuels, or creating more sustainable roads and surfaces, our products are having a positive impact on our world daily. 20 million reasons why we’re making a difference
To learn more scan the QR code or visit tyrecycle.com.au
Engineered to redefine efficiency, our Transfer Trailers are built with high tensile steel, offering unparalleled durability to withstand compaction forces in waste transfer stations. With a range of sizes and features like a hydraulic eject blade for efficient waste disposal, it’s the ultimate solution for optimizing your waste management operations.
• 53 – 65m3 Triaxle
• 65 – 75m3 Quad Axle
• 114 – 120m3 A-Double
• 106m3 Pocket Road Train
• 130m3 Road Train
• 70m3 Top Load Moving Floor Trailer