
6 minute read
PADDLES AND PACKAGING
WASTECH ENGINEERING’S JEFF GOODWIN EXPLAINS HOW THE ATRITOR TURBO SEPARATOR CAN HELP BUSINESSES ACHIEVE A FOOD WASTE RECOVERY RATE OF 99 PER CENT.
Wastech has been working with UK manufacturer ATRITOR to add food de-packaging to its product roster.
Growing populations and an associated increase in food consumption is accelerating the organic waste problem in Australia and around the world.
As reported by Waste Management Review in June, many Australian businesses are hesitant to engage in the source separation of food waste.
This is due to a limited number of recycling facilities able to process the recovered organics, together with concerns around the ability to recycle packaging.
With the National Packaging Targets are squarely on the waste industry’s agenda, the ability to effectively separate recyclable packaging from its contents is therefore equally important.
Jeff Goodwin, Wastech Engineering’s National Product Manager Projects, says growing issues around food waste generation, paired with rising landfill restrictions and capacity levels, was the driving factor behind a recent addition to Wastech’s product portfolio.
“Working with UK manufacturer ATRITOR, Wastech has added a range of turbo separators for food de-packaging to our product roster,” Jeff says.
“As the exclusive Australian representative for ATRITOR, Wastech can provide customers with a solution offering a typical food waste recovery rate of 99 per cent for both dry and liquid products.”
Jeff says the high recovery rate makes the Turbo Separator ideally suited for use in product destruction units.
The Turbo Separator range comprises four models designed and engineered to efficiently remove a wide range of products from their packaging.
“Wastech’s distribution range includes the TS1260, TS2096, TS3096 and TS42120 models, with a material dependant separation rate ranging from 600 kilograms an hour to 20,000 kilograms an hour,” Jeff says.
According to Jeff, the equipment ideal for separating out-of-date, out-ofspecification or mislabelled products.
“Historically, expired and mislabelled food products were consigned to landfill due to the difficulty of extracting organics from packaging,” Jeff says.
“With the ATRITOR Turbo Separator we can begin shifting that practice.”
Jeff says the Turbo Separator is sufficiently flexible and can depackage a range of products and packaging materials including supermarket waste, tin cans, polymer bottles and soft packaging.
“Additionally, the Turbo Separator is equally at home separating gypsum from the backing paper in plasterboard,” Jeff says.
“The recovered gypsum can be used in agriculture or re-used in plasterboard manufacturing, while the recovered paper can be further recycled.”
Jeff says the Turbo Separator also works for blister packs, sachets, pouches, paper bags, aluminium cans, plastic bottles, plastic drums and TetraPak.
“The only unsuitable application is glass containers or bottles, as the glass shatters and the shards will contaminate the organics,” he explains.
The Turbo Separator combines centrifugal forces, self-generated airflow and mechanical processes to remove organic material from packaging.
Jeff says this allows the recovered materials to be recycled or disposed of correctly.
Packaged materials are fed by an infeed conveyor into the separation chamber, where a number of rotating paddles open up the packaging.
The force of the paddles then creates a squeezing effect, which separates packaging from its contents without destroying the packaging.
Depending on the material, the recovered organics can then be used for animal feed, nutrient-rich compost
The Turbo Separator can de-package a range of products and packaging materials.

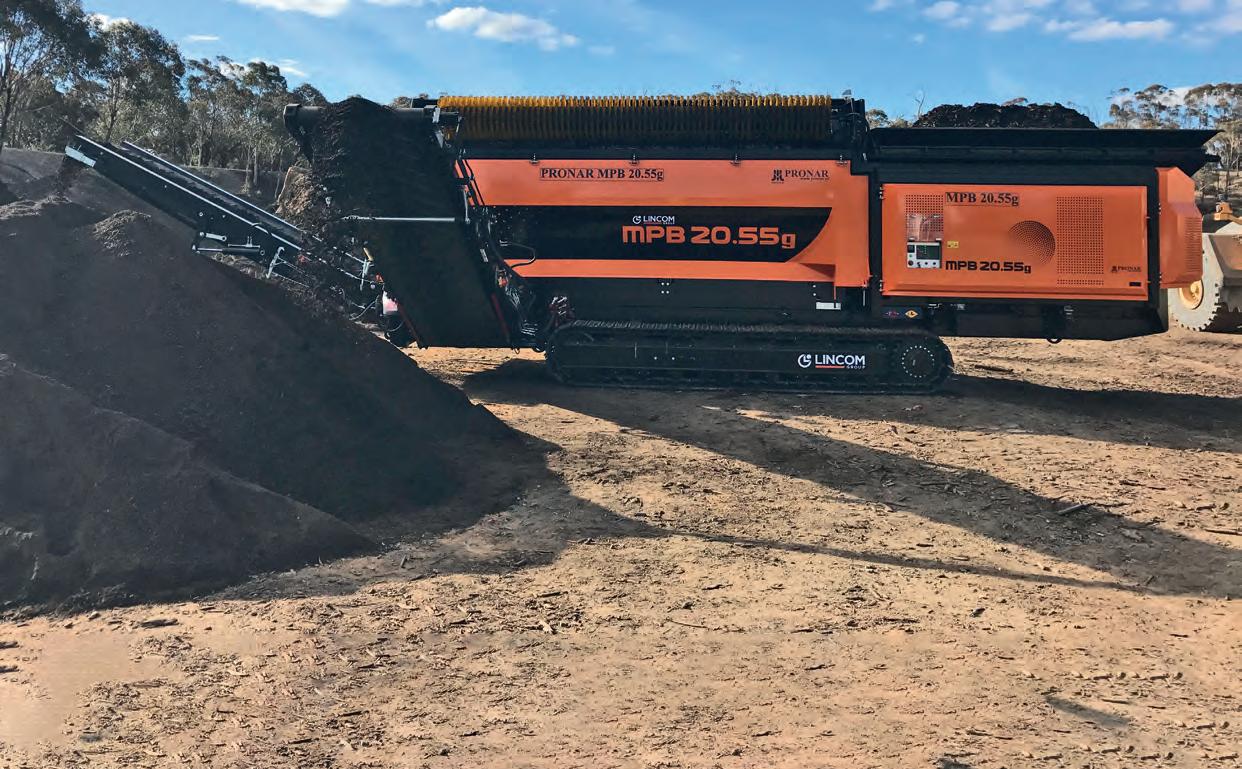
or anaerobic digestion.
Wastech can supply the Turbo Separator as a complete package, with an infeed hopper and conveyor, separation chamber and outfeed conveyors.
The separator is also delivered with a maintenance access platform and control cabinet.
“The Turbo Separator’s rugged and durable construction, coupled with high product separation rates and economy of operation, is an ideal proposition for all de-packaging applications.”
Controlling pumps and scarcity
NHP ELECTRICAL ENGINEERING SMART MOTOR CONTROL SYSTEMS PROVIDE REAL-TIME OPERATIONAL DISRUPTION DATA AND ENERGY EFFICIENT PUMPING TO WASTEWATER FACILITIES.
Australia’s dry and inconsistent climate poses a challenge to water security. As a consequence, increasing the capacity of wastewater recycling facilities is vital to mitigating resource scarcity and increasing climate resistance.
Recycling wastewater can ease pressure on water resources and avoid the need to discharge the material into the environment.
Managing masses of liquid can be challenging, however, given the rheological makeup of the material.
For wastewater facilities to operate effectively, they require centralised pumping systems supported by reliable motor control.
Power distribution, automation and motor control specialists NHP Electrical Engineering Products (NHP) have been operating in the wastewater space for decades.
Michael Liberatore, NHP Automation, Safety and Motor Control Business Manager, says within the digitised modern world, it’s important that NHP can deliver customer-focused Industrial Internet of Things initiatives and tools.
“Water is an essential input that feeds the production cycle of almost all other industries,” Michael says.
“In the contemporary climate, where limited water resources and concerns about the environmental impact of electricity production are real, innovation is central to success.”
According to Michael, Smart Motor Control is one of many innovative solutions supported by the company. He adds that efficient motor control enables application flexibility, as well as higher productivity and workplace safety. “At the core of this are inventive solutions that provide a reliable supply of water to minimise network upgrade disruptions and optimise capital investment.”
Smart Motor Control enables real-time monitoring of wastewater networks.
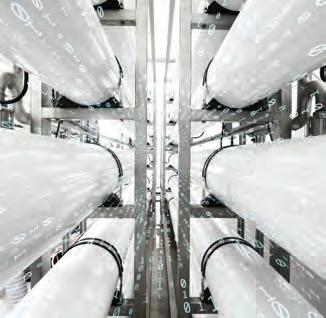
Michael says Smart Motor Control supports secure wastewater networks by enabling real-time monitoring and asset management. Additionally, he says 75 per cent of motor control failures can be prevented by applying appropriate protection measures.
“Efficient motors drive wastewater management performance, and the impact of motor failure can be significant,” he explains.
“With Smart Motor Control devices, clients can improve productivity and help avoid motor failures with an integrated, data-driven approach.”
Michael says the technology diagnoses problems early and identifies where they are, which allows clients to transform data into actionable information to reduce production losses.
Michael says Smart Motor Control systems minimise energy expenditure by reducing overall system power requirements and wear and tear on equipment.
“Smart Motor Control can be easily integrated into clients’ existing motor control systems to offer higher productivity and shorter downtimes,” he explains.
Be it pumping station treatment plants or pipelines, Michael says NHP can provide complete solutions for the most complex water and wastewater applications.
NHP offers a complete portfolio of Smart Motor Control solutions, from simple fixed and variable speed control to precise torque and position control.
“With Smart Motor Control Devices, energy consumption can be monitored on each motor individually at any point,” he explains. “Our Smart Motor Control solution helps customers achieve advanced pressure and flow control, including soft start, stop capabilities and energy savings.”
Let us design a shredding system to meetyour specific needs. Solving problems and creating opportunities processing a wide range of materials is what we do best. Everything from e-waste, metals, tyres, confidential documents, medical waste, plastics, wood and packaged products can be destroyed, size reduced and separated.
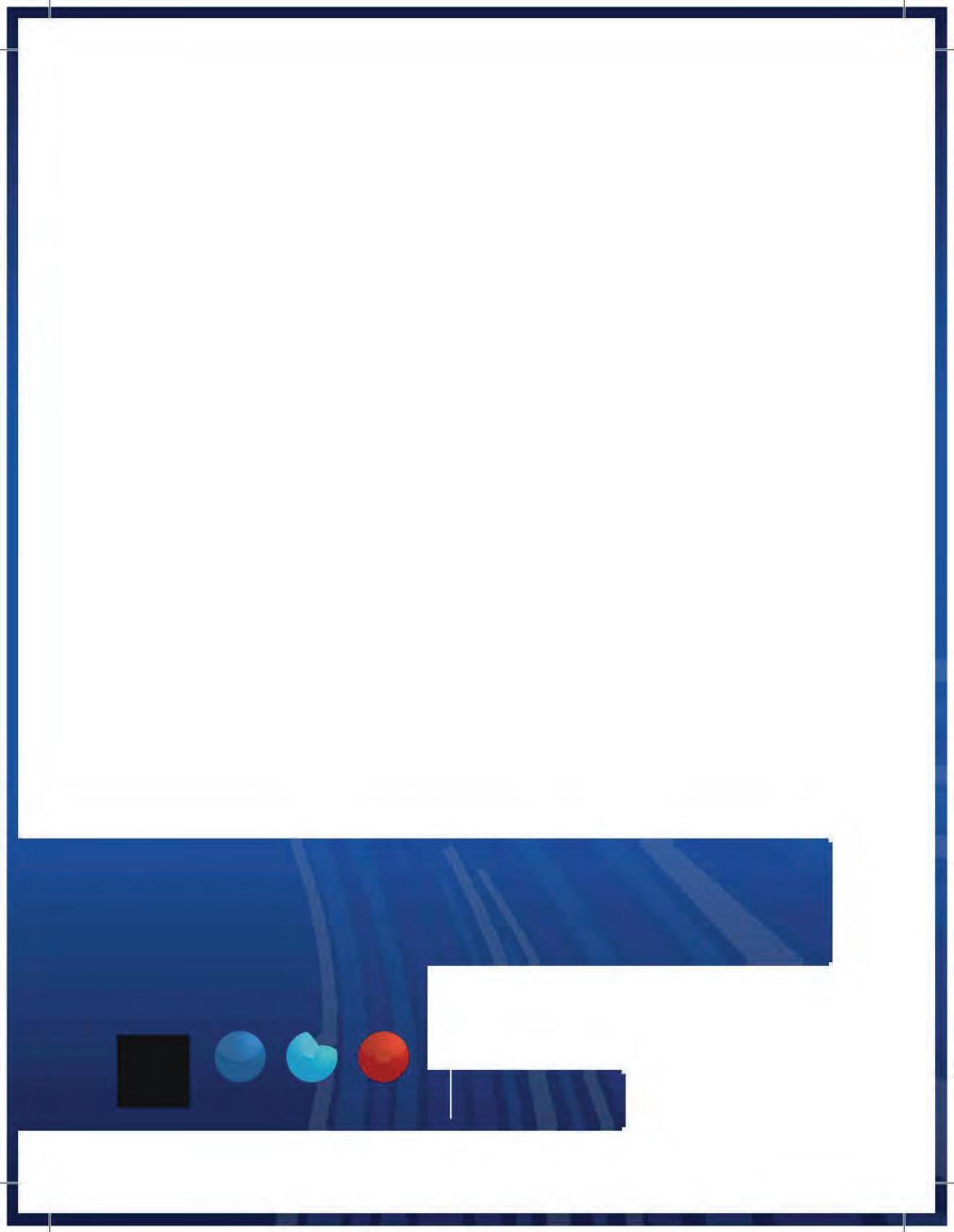
