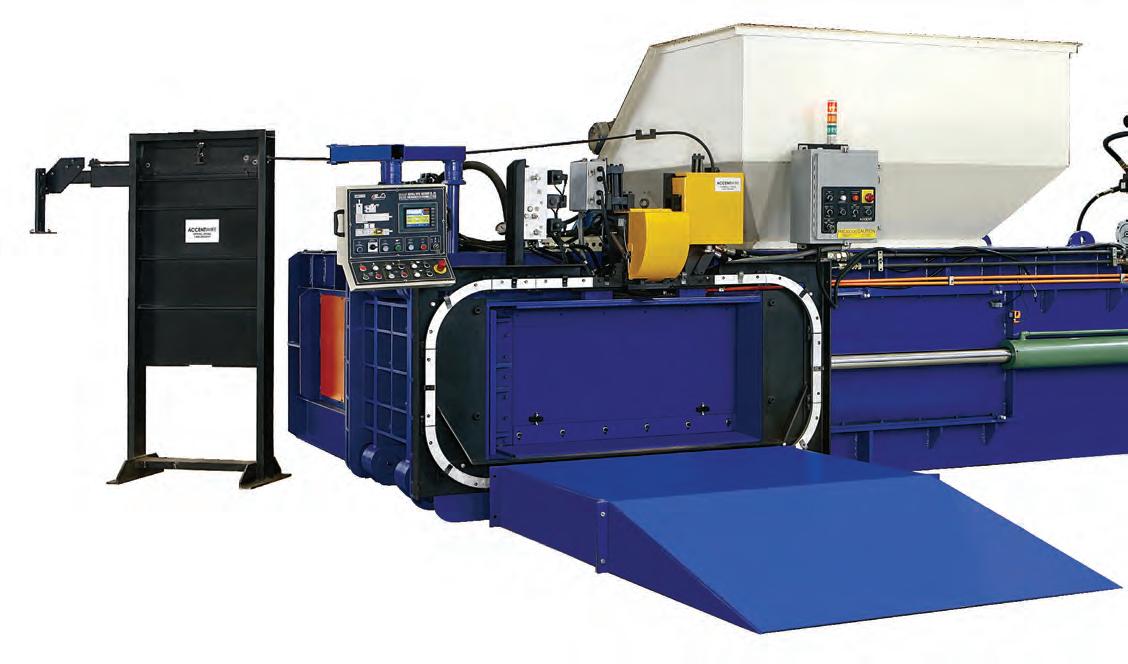
8 minute read
BALED TO PERFECTION
MATERIAL RECOVERY SOLUTIONS EXPLAINS ITS UNIQUE VALUE PROPOSITION AS IT BECOMES THE EXCLUSIVE AGENT FOR GODSWILL BALERS IN AUSTRALIA AND NEW ZEALAND. I nternational original equipment manufacturer (OEM) Godswill Paper
Machinery Company is one of the world’s largest manufacturers of balers.
With nearly 200 balers in operation in Australia and New Zealand, Godswill holds a substantial market share, with many operating in highvolume applications.
Since 1987, Godswill Paper machinery has proven to be an international player with exclusive agents committed to providing front line service and support globally.
To offer the reliable equipment locally, Material Recovery Solutions (MRS) recently became the exclusive agent for Godswill balers in Australia and New Zealand. Its range includes, but is not limited to – channel, two ram, closed door and custom build balers.
Flagship models comprise the GB1111FX channel baler and the GB1175TR two ram baler.
Marcus Corrigan, Managing Director of MRS, says the new agreeement is not a decision Godswill made lightly.
“We believe in putting after-sales support first and supporting our customers. Their confidence in us results in new orders,” Marcus says.
MRS technicians are armed with a suite of OEM spare parts to support Godswill products along with a full-serviced in-house machine shop, allowing items to be manufactured quickly.
Simon Davidson, Project Engineer at
Godswill balers are designed to provide export bale weights at high throughputs.

MRS, says the company aims to offer unrivalled support to the marketplace.
“It’s very significant to be able to offer quality components to a high tolerance,” Simon says.
“OEM parts are trialled and tested over many years to ensure longevity and reduce damage to other aspects of the machinery caused by faulty parts.”
Godswill balers are designed to provide export bale weights at high throughputs across a range of material types.
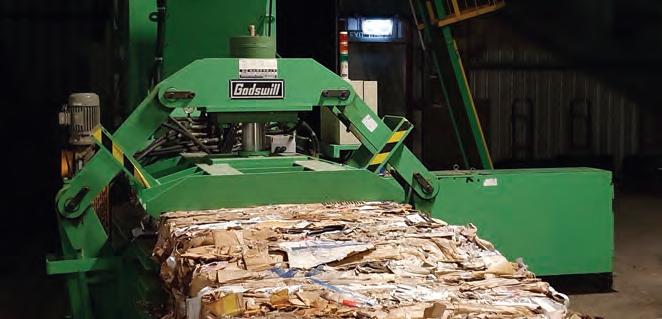
Channel balers support fibrous materials such as paper, cardboard and various waste streams.
The two ram balers, designed to bale high memory materials such as plastic bottles and LDPE film, can also bale an array of other materials. Custom builds are also available for niche applications.
Simon says the Godswill range was designed with usability and ease of maintenance in mind.
“Touchscreen human machine interface (HMI) combined with a push button system offers ease of use.”
Simon adds that customisable material settings with selective switchovers support effortless material changeovers.
“HMI provides intuitive diagnostics. Combined with our 24/7 service and support, we are able to ensure liability and year-long operations.”
“Our direct communication and close relationship with Godswill as a supplier enables us to get a quick response on all issues backed up by our technical knowledge and industry experience.”
“Through default, all Godswill balers have innovative safety functions with dual redundancy systems to operate in the safest possible manner.”
Marcus says the company currently manufacture systems to service the baling, processing, recovery and product destruction industries.
“We are expanding our scope within the industry by providing solutions in the collection sector, currently manufacturing a number of automated document collection vehicles.”
Marcus’ 20 years of experience in the material processing industry, including 15 in the material recovery industry, ensures he can serve customers with an advanced level of industry knowledge.
“While MRS is a young company, the ever-expanding team of engineers, technicians and manufacturers offer a wealth of knowledge adding to our overall diversity. I am proud of our achievements and excited about the future,” Marcus says.
Fast Fact The Godswill balers line-up includes but is not limited to:
• Channel balers designed to bale fibrous materials such as papers/ cardboards and various waste streams. • Two ram baler designed to bale high memory materials such as plastic bottles. LDPE film can also bale an array of other materials making it ideal to bale various material types.
• Closed door balers offer high compaction across all material types at low volume throughput. • Custom builds committed to work closely with end users. Godswill has and will always consider building custom balers for niche applications. Flagship models include the GB1111FX channel baler. Depending on specification it has a real-world throughput of 21 tonnes per hour when baling cardboard and 25 tonnes per hour when baling paper. The GB1175TR two ram baler, depending on specification orders, has a throughput of five tonnes per hour when baling PET bottles (non-pierced) and six tonnes per hour when baling HDPE bottles.
Landfill loading
CATERPILLAR ASIA PACIFIC EXPLAINS HOW DIFFERENTIAL LOCKS AND CAT CONNECT TECHNOLOGY CAN INCREASE LANDFILL OPERATION EFFICIENCY.
Not all landfill sites are the same, with many posing unique and harsh environmental challenges for operators. Land is often unlevel, with small space for movement and barriers to reach cells.
In these environments, managing multiple seemingly competing requirements such as maximising operational efficiency, economic viability and worker safety, can be a challenge.
Ayden Piri, Caterpillar (Cat) Asia Pacific Industry Specialist Account Manager, says landfill operators require reliable and efficient machinery to facilitate safe site management and consistent operations.
He says Cat is uniquely positioned to understand machinery requirements relevant to the waste industry, with over 40 years experience providing for the sector in multiple application modes.
According to Ayden, Cat M Series waste handling wheel loaders are popular with landfill operators due to their heavy-duty handling capacity.
“Cat’s waste handling wheel loaders deliver sustainable productivity, fuel efficiency, ease of serviceability, ergonomics and operator comfort,” Ayden says.
“These environmentally-friendly front end loader machines apply proven technology systematically and strategically, to meet our customer’s high expectations.”
With a global network of 172 dealers, factories in 30 countries and more than 10,000 Cat and dealer employees in Australia and New Zealand, the extensive reach ensures CAT is able to draw on a network of experts to solve its customers’ challenges.
Ayden says M series 950- and 972-metre models have a standard front axle differential lock, which is manually activated by a switch on the cab floor.
The fully automatic front and rear axle differential locks work by measuring differences in axle speeds and require no operator intervention to activate.
“These disc-type differential locks
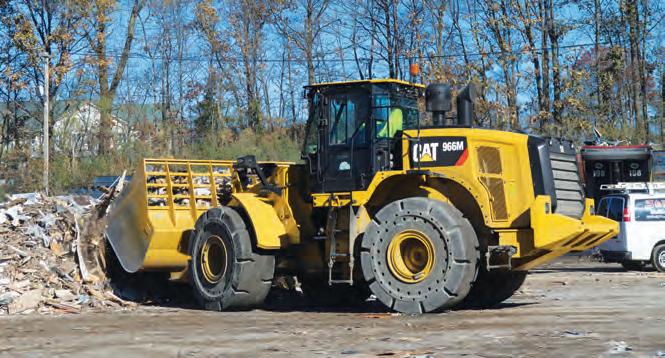
Cat M Series waste handling wheel loaders are popular with landfill operators due to their heavy-duty handling capacity.
will reduce tyre scuffing compared to other traction aids, further reducing operating costs for customers,” Ayden says.
“The proven Z-bar linkage combines efficiency with great visibility to the tool, resulting in excellent penetration into the pile, high breakout forces and superior production capabilities.”
M Series’ next generation ride control works as a shock absorber, which Ayden says improves ride quality and smoothness over the rough surfaces often found in transfer stations.
“When paired with the Fusion coupler, from a loaded high-dump bucket to a fork to move material, the ride control system provides reduced cycle times, better productivity and a smoother, more comfortable ride for the operator,” he adds.
M Series wheel loaders are equipped with Cat Connect technology, which allows operators to monitor, manage and enhance job site operations.
“Cat Connect facilitates easier service access, with the legacy one-piece hood, centralised service centre’s, windshield cleaning platform and harness tie-off,” Ayden explains.
“Optional purpose-built guarding is also available to help protect your machine from the harsh environments common in waste applications.”
The wheel loader’s machine guarding protects the unit’s major components and systems, facilitating reliable durability.
“Wear in waste handling applications is severe and can drastically cut down a machine’s life,” Ayden says.
“All Cat waste handling machines are protected in key impact areas, including undercarriages, radiators, axles and cabs.”
According to Ayden, the M Series medium wheel loader is 10 per cent more fuel efficient than the industryleading K Series, and up to 25 per cent more fuel efficient than the H Series.
The updated Caterpillar powershift transmission, with a lock-up clutch torque converter, is standard on all M Series wheel loaders.
“The new torque converters have been matched with engine power and hydraulics to improve performance and fuel efficiency, while also managing the pile or loading trucks,” he says.
“The rugged transmission also has a new split-flow oil system, which uses multi-viscosity oil to reduce parasitics and improve fuel economy.”
Ayden says the M Series hydraulic
The M Series wheel loader is 10 per cent more fuel efficient than the K Series.
system has recently undergone significant design changes.
“The main hydraulic valve is now a mono-block with an integrated ride control section,” Ayden says.
“The mono-block design also reduces weight, has forty per cent fewer leak points and is common
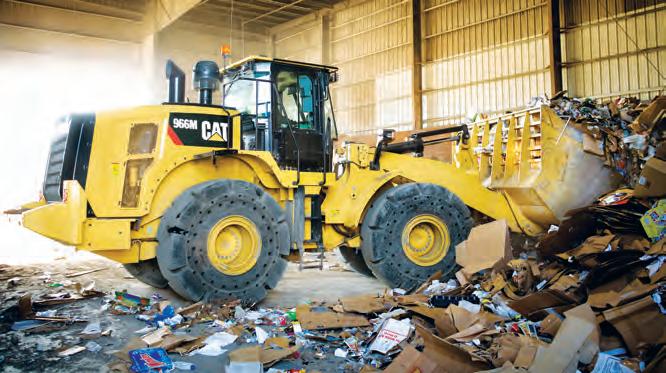
across all M Series models.”
On 950- and 972-metre models, auxiliary hydraulic functions can be added at the factory or in the field, with the addition of a second remote valve.
“A new thermal bypass valve has also been added to improve hydraulic system warm-up,” Ayden says.
Reduce Downtime with Advanced Motor Control Technology
NHP is proud to bring to the local Australian and New Zealand markets the newly released Allen-Bradley® SMC-50 soft starter with internal bypass incorporating advanced motor control and protection functions. Designed for customer flexibility, this product features advanced monitoring, greater protection, superior communication and network integration capabilities to increase efficiency and reduce costly downtime. Available in nominal ratings of 108 through to 480A at 415V AC and 690V AC, this device ensures greater functionality and effectiveness for controlled motor starting, whilst also providing flexibility to meet ever-changing requirements.

To increase your performance, visit nhp.com.au/more/smc50
NHP ELECTRICAL ENGINEERING PRODUCTS 1300 NHP NHP | nhp.com.au |
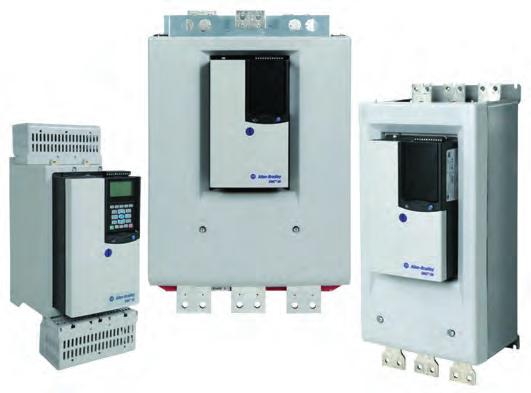