
11 minute read
WTE AND THE FIGHT AGAINST LANDFILL
Each Moscow plant will feature three lines of HZI grates, as well as the company’s patented flue gas treatment system.
HITACHI ZOSEN INOVA’S MARINA MILLS OUTLINES HOW WASTE-TO-ENERGY TECHNOLOGY IS HELPING SHAPE MOSCOW’S WASTE MANAGEMENT EVOLUTION.
Moscow, a city of 12.5 million people, produces the largest amount of municipal solid waste in Russia. Historically, most of that waste has ended up in large landfills inherited from the Soviet Union, which are often located in highly populated areas.
Based on published statistics, there are circa 400 kilograms of municipal solid waste attributable per person per annum in Russia, or a total of 60 million tonnes each year. That number is forecast to grow to 500 kilograms per person by 2025.
“95 per cent of the waste is not treated but landfilled in Russia,” Hitachi Zosen Inova’s (HZI) Marina Mills says.
“Landfills take up one million hectares of land around Moscow and circa four million hectares across Russia. Most – estimated at 80 per cent – are full and are closing or will be closing soon.”
Environmental awareness has been steadily growing in Russia over the last decade.
In 2017, the country faced large protests organised in 30 regions against illegal waste dumping.
In the summer of 2017, for example, Kuchino landfill, one of the largest serving the Moscow region, was closed due to overcapacity and pollution concerns.
In 2018, the Russian Government approved a national project for ecology.
The project sets a target that 60 per cent of all solid waste will be processed by 2024, with 36 per cent recovered, reused or recycled.
In alignment with the new project for ecology, four waste-to-energy (WtE) facilities are set to be constructed across the Moscow region in coming years, with Russia’s Green Tariff program making these projects more attractive for investors.
The four WtE facilities will be constructed by HZI, in collaboration with consortium partner ZiO-Podolsk.
Through the consortium, HZI acts as combustion and flue gas treatment technology suppliers, while ZiOPodolsk will deliver manufacturing services for power island equipment.
“With more than 600 WtE references worldwide, HZI is one of the world’s leading designers, suppliers and manufacturer of WtE technology,” Mills says.
“We are proud of being able to collaboratively work with our consortium partner, notwithstanding some territorial, cultural and language differences.”
Mills explains that ZiO-Podolsk brings local experience, expertise and the ability to manufacture high quality equipment locally.
“We look forward to growing and strengthening this partnership in the future,” she says.
Each facility will process 700,000 metric tonnes of waste and generate 70 megawatts of electricity for the grid.
Mills explains that this will supply
circa 400,000 residents in the Moscow region.
Construction of the first facility is well underway, she adds, and is progressing reasonably considering the challenges presented by COVID-19.
The second facility also received its Notice to Proceed in June 2020.
Thermal waste treatment will be used to recover energy and material from non-recyclable waste, Mills says.
She adds that the process will convert waste into energy and reduce material volumes by 80 per cent.
“Thanks to continuous optimisation, today’s grate combustion is the most advanced technology for the treatment of non-recyclable waste with regard to environmental friendliness, operating reliability, flexibility and cost effectiveness,” Mills says.
More specifically, each Moscow plant will have three lines with HZI designed reciprocating grates, as well as the company’s patented flue gas treatment system: DyNOR-SNCR for NOx reduction.
“The state-of-the-art grate combustion and dry flue gas technologies developed in-house by HZI are specially designed for the thermal treatment of municipal solid waste,” Mills says.
“It allows HZI plants to process large variations and quantities of waste in compliance with the strictest environmental regulations, such as the European Union’s 2018 Emission Directive, reliably.”
“This is the same standard against which HZI is currently building the East Rockingham WtE project in Perth, Western Australia,” she says.
“Additionally – we have kept in mind the potential for standardisation of multiple WtE plants built in Russia to address waste management issues effectively and efficiently in future, as well as our ability to reliably maintain technology should it be required.”
LESSONS FOR EAST ROCKINGHAM WTE FACILITY
Mills, who lead commercial contracts negotiations on behalf of HZI for the East Rockingham WtE facility, says as Australia’s WtE market expands, the country should look towards international experience and best practise.
“In Russia, for example, the introduction of the Green Tariff applicable to electricity produced by WtE plants has focused the development of the Moscow projects,” she says.
“Governmental support, landfill taxes and WtE grants provide a level of certainty to us, as technology providers, that the market understands modern WtE technology and the need for it.
“However, continuous raising awareness of it in general public and involving local communities cannot be underestimated.”
The Australian market has particular challenges, Mills says, such as individual state regulations and variance in council waste volume sizes, as well as the
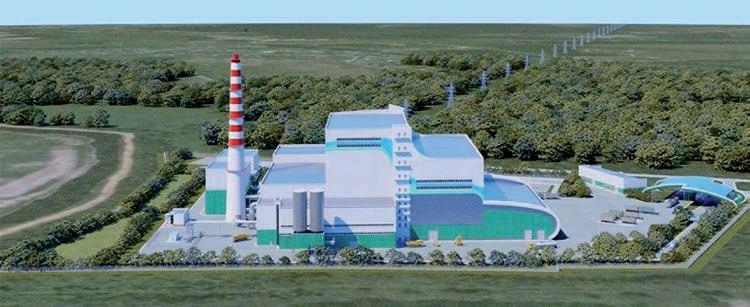
The four Moscow WtE facilities will be constructed by HZI, in collaboration with consortium partner ZiO-Podolsk. location of Australia.
“As a consequence, each project needs local knowledge, stakeholder information and a good understanding of the local waste composition to allow for WtE projects and affordable gatefees,” she says.
Mills adds that HZI’s international experience presents opportunities to evaluate the differences and similarities in standards applicable to construction of WtE facility globally.
Furthermore, she says to grow WtE in Australia, further source separation of organics, recyclables and residual waste is key.
Mills explains that in collaboration with composting facilities, HZI’s Kompogas dry anaerobic digestion systems can produce renewable energy in the form of biogas, which can then be used for natural gas grid injection.
“We aim for as much waste as possible to be recycled, but there will always be a non-recyclable fraction of waste,” Mills says.
“WtE is a clean and safe solution for municipal solid waste that cannot be further recycled.
“In addition, it allows recycling of aggregates and metals which would normally be lost in landfills.”
HZI is also preparing for the renewable future with its power-to-gas solution EtoGas, which transforms surplus electricity from intermittent sources such as wind and solar to hydrogen.
“Together with carbon dioxide, we can synthesize renewable methane. Considering the large Australian footprint available for wind and solar, we can see a future where Australia becomes fully sustainable and a net exporter of renewable energy,” Mills says.
“This aligns with HZI’s vision of the world moving away from landfills, that account for 8 per cent of the total greenhouse emissions, to a circular economy.”
Data as intelligence
MANDALAY TECHNOLOGIES’ FACILITY ANALYTICS PRODUCT IS ALLOWING USERS TO NAVIGATE BETWEEN KPI’S, METRICS AND UNDERLYING DETAIL.
The need to develop more extensive and accurate waste data has been highlighted in both the NSW 20-Year Waste Strategy Issues Paper and Victorian Government’s new Circular Economy policy. Specifically, Victoria’s policy notes that a shift to a circular economy relies on high-quality and transparent data, which at present, is lacking. Add to this the fact that the Federal Government’s 2016 State of the Environment Report – the most recently undertaken – draws on data from 2013, and one notes a widespread issue. While these instances address data from a waste policy and regulatory perspective, Simon Kalinowski, Mandalay Technologies CEO, says comprehensive and accurate data is critical at every level.
“Quality data is the bedrock for good decision making. Operating without it can leave organisations vulnerable to making poor and expensive decisions or lose their competitive edge,” he explains.
“Unfortunately, the waste industry in Australia is severely underutilising data, partly due to lack of quality data, failure in compliance processes, a lack of proper implementation of reporting and analytics strategies, or a combination of these.”
To boost facility manager’s ability to access and leverage data, Mandalay has developed a new Facility Analytics & Reporting product.
Utilising Mandalay’s existing naus Intelligence platform and Microsoft Power BI, the product facilitates a big picture view of facility operations– right down to the minute detail of individual transactions. With real data, analysis and insights, Kalinowski says local government authorities and waste managers can better plan
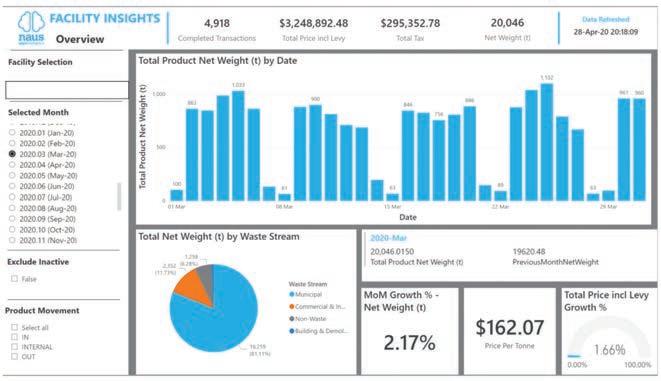
Operational reporting provides users with an intuitive interface to generate and export tabular style reports based on transactional data. and track their strategies for waste diversion, landfill reduction and support planning for new facilities.
“Traditionally, waste facility operators have one transacting system, which multiple stakeholders will then use to extract data from. From there, numerous excel spreadsheets are created for different reporting purposes,” Kalinowski says.
This creates a myriad of issues, namely, that as with any degree of manual reporting, the data’s integrity and history is lost.
“What you’re reporting on changes and evolves. When it’s open to manual adjustment and effort, you inevitability lose some of the integrity of that information, which creates conflicts in reporting,” he says.
“We’ve seen a need from our customers to give them a single point of data truth, which in turn boosts efficiency from a regulatory, financial and mass flow reporting perspective.”
By providing a single point of truth, users can drill in from a high-level report through to the specific data that makes it up – all within two or three clicks. This in turn provides a high level of confidence and trust in the data.
Using a combination of dashboards and detailed reporting capabilities, the Facility Analytics & Reporting product enables flexible access to data across facilities, while maintaining security, such as user permissions, data backup and recovery.
“The product was born over the past 12 months, as we really started to drive our data and analytic
The software also allows users to view information using a mix of the latest visualisation components and navigation controls.

capabilities,” Hendrik Venter, Mandalay’s Data Manager, says.
He explains that the product was developed by researching Mandalay’s first-generation web-based reporting tool. Venter adds that a key element of that was looking at reporting commonalities and outliers.
“The product has only been available for three months and has already been taken up by 20 per cent of our client base, which highlights the value of that research and development,” he says.
By utilising Power BI, Mandalay was able to develop more interactivity and navigation options.
“Facility operators and managers are now able to look at what’s happening right now, but also go back and look at what was happening in the past,” Venter says.
“This allows them to draw from trends and variances, thereby giving the user a functionality and feature set that can assess whether the facility’s efficiency is on track.”
Central to the new system, Venter says, is the presentation of data in a single secure form.
“Operational reporting provides the user with an easy to use interface to generate and export tabular style reports based on the transactional data generated at the facility,” he explains.
Also available is Mass Management Reporting, which Venter says captures overloaded vehicle details and presents it in a detailed report, thereby enabling facility managers or owners to more effectively manage compliance breaches.
Venter explains that with large fines for breaches via the National Heavy Vehicle Regulator, the ability to effectively manage overloaded vehicles is critical.
“The module enables our clients to set vehicle mass configurations, so when a truck comes through the weighbridge, our system can record and present that information.”
The new system also allows users to configure security groups and permissions on a granular level, Venter says. He adds that this gives administrators the power to define which of their users is allowed to see different elements of data reports.
Furthermore, the Facility Insights tool offers facility managers a powerful analytics user experience, enabling the user to navigate seamlessly between KPI’s, metrics and the underlying detail.
“It provides on-tap access to years of historical data, which provides a deeper understanding of facility performance across a variety of metrics, empowering owners and managers to better manage operations from a client, carrier, product and financial perspective,” Venter explains.
The software also allows users to view information using a mix of the latest visualisation components and navigation controls.
According to Mandalay COO Rex Heathwood, this versatility is a core component of the Facility Analytics & Reporting software.
“The data will say different things to different people. Site operators, for instance, can use it to note transactions at odd hours, whereas a council waste manager might use it to extract diversion rates,” he says.
“Given the product presents data visually, anomalies are more likely to stand out. Finding those anomalies is really triggered by visual tools.”
Additionally, Heathwood notes that many of Mandalay’s clients operate multiple facilities, be it transfer stations, landfills and recycling centres, all in one community. Using the Facility Analytics & Reporting tool, data from each site can be merged together, allowing operators to examine all movements within their waste ecosystem.
“Data, in many ways, is alive. One of the challenges when clients export it to excel is that it immediately becomes static, but the source of the data is still changing,” Heathwood says.
“When you take data away from the live system it dies – it doesn’t react, and it doesn’t respond. By using a real-time fully integrated system, operators can trust that they are always reporting on the most accurate and timely data.”