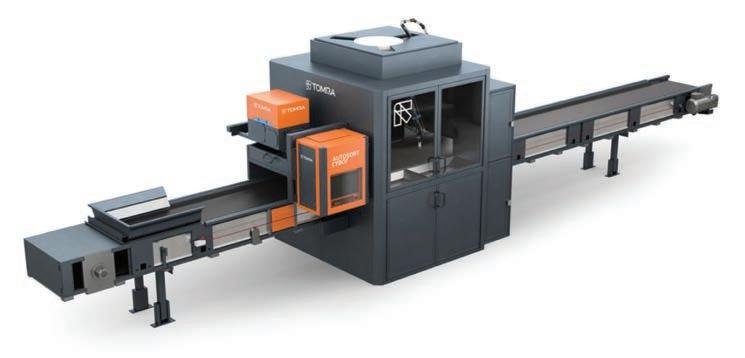
34 minute read
A SYMPHONY OF ALL SORTS
BY UTILISING ADVANCED AUTOMATED SORTING ON THE GROUND FLOOR, SOCIETY CAN KEEP PRECIOUS RESOURCES IN CIRCULATION. CEMAC TECHNOLOGIES’ ERIC PAULSEN EXPLAINS.
Talk of harmonisation is widespread throughout the waste and resource recovery industry. While often applied to discussions of policy and the need for consistent regulatory frameworks, TOMRA Sorting Recycling and CEMAC Technologies are taking the idea to the facility floor.
At Symphony of all Sorts, a digital launch event for TOMRA’s latest iteration of automated sorting technology, Volker Rehrmann, Head of TOMRA’s Recycling/Mining and Circular Economy divisions, highlighted the power of circular composition.
“The bright future we see ahead of us requires the cooperation and smooth interaction of industry and all stakeholders along the value chain,” he said.
“A good example of perfect interaction of all elements is nature. One reaches into the other, nothing is lost. It’s like an endless symphony, where various instruments work together to align and form a beautiful whole.”
One of nature’s best instruments is resources, Rehrmann continued.
“We know resource are finite. We are currently over exploiting mother nature’s resources and we can’t continue like this,” he said.
“Once the resources are gone, they are gone forever. We don’t have a second planet we can rely on – that’s
The AUTOSORT range is designed to meet societal demand for faster, more efficient and smarter recyclable material sorting.
why we need to keep resources in circulation like a musical loop.
“There is simply no alternative – the shift to a circular economy is paramount.”
It’s this line of thinking that inspired TOMRA’s new AUTOSORT range, which works to create a harmonised symphony through the accurate sorting of waste materials.
The idea being that through advanced sorting at the ground level, society can reuse resources currently in circulation, thereby ensuring sustainability for future generations.
The line features three new equipment innovations, a next generation AUTOSORT, AUTOSORT SPEEDAIR and AUTOSORT CYBOT, which incorporates robotic recycling technology.
According to Eric Paulsen, Managing Director of TOMRA’s Australian partner CEMAC Technologies, all three products are designed to meet societal demand for faster, more efficient and smarter recyclable material sorting.
He explains that the next generation AUTOSORT line brings together the latest in technological innovation to deliver advanced accuracy for complex sorting tasks, thereby facilitating higher throughput rates.
“Compact and flexible in construction, AUTOSORT allows for an uncomplicated integration into existing and new facilities,” Paulsen says.
“Utilising TOMRA’s FLYING BEAM technology, homogenous light distribution for better detection and monitoring across the entire belt width is guaranteed, resulting in heightened performance and operational efficiency.”
Additionally, the AUTOSORT’s monitoring system generates more
information from the sorting process than previous models, which can be used to support process and maintenance planning. New sorting software also enables faster processing, Paulsen says, with improved functionalities such as the use of neuronal deep learning networks. “Deep leaning enables sorting processes that cannot be mastered with conventional technology, which extends application possibilities,” he says. “The system also allows for extended detection through THIS YAWEI LASER IS DESIGNED TO CUT ABOVE THE REST. NOW THAT’S APPLIED THINKING. Polystar unwraps the value in film recycling. Now that’s Applied Thinking. R E D U C E S W A S T E S I M P L E T O U S E DEEP LAISER, meaning the AUTOSORT can detect unknown objects in the material stream through intelligent object recognition.” The second component of TOMRA’s new line, the AUTOSORT SPEEDAIR, is designed to stabilise light materials such as plastic films or paper on a high-speed conveyor. This, Paulsen says, allows operators to generate higher throughputs while enhancing sorting quality. The AUTOSORT SPEEDAIR incorporates speedcontrolled, fan-driven air inlets that generate a constant air stream over the conveyor belt to prevent material from moving. “By doubling the speed of the conveyor belts up to six metres per second, customers benefit from a higher return on investment, as well as lower installation and running costs,” Paulsen says. “As the first system on the market with no belt cover,
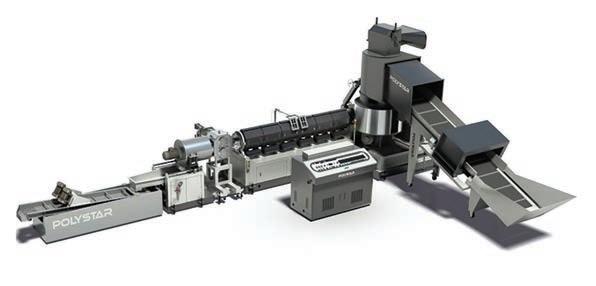
access to the unit for maintenance is enhanced, while material blockage potential is lower when compared to conventional high-speed systems.” With its extreme accuracy, speed and consistency of cut, combined with very low operating Rounding out the new range is the future thinking costs, the new Yawei HLF fiber laser is the perfect way to take your business to the next level. AUTOSORT CYBOT, which according to Paulsen, is the Designed for reprocessing of polyethylene & first waste sorting robot on the market to combine four essential technologies at once. Dollar for dollar, the new HLF is in a league of its own, opening up possibilities for companies all across the laser cutting sector; from start-ups through to full production, 3-shift polypropylene flexible packaging material environments. “The addition of a robot arm to the AUTOSORT Pelletising system with integrated cutter eliminates system opens up a wealth of new opportunities for highly need for pre-cutting automated applications within the sorting process,” he says. With the announcement of the Federal Government’s With a quality German built Precitec auto-focus cutting head, IPG laser source, Siemens 840DSL controller and a fabricated, stress-relieved fully annealed frame it really is a cut above 100% of pellets reusable straight back into your production line new $190 million Recycling Modernisation Fund in early July, Australia’s resource recovery industry is set for a Minimal material degradation without affecting period of unparalleled growth. As such, Paulsen stresses the material properties need to capture the opportunities afforded by automation. “Only through the variation of suitable automated sensor For more information: 03 9706 8066 technologies can true process capacity go beyond manual sales@appliedmachinery.com.au sorting limitations,” he says. www.appliedmachinery.com.au “By achieving improved purity levels through Connect with us socially automation, we can deal with today’s challenges, while also ensuring an economically and environmentally sustainable future.” Fully compatible with FIMIC melt filters
appliedmachinery.com.au
Weathering the storm
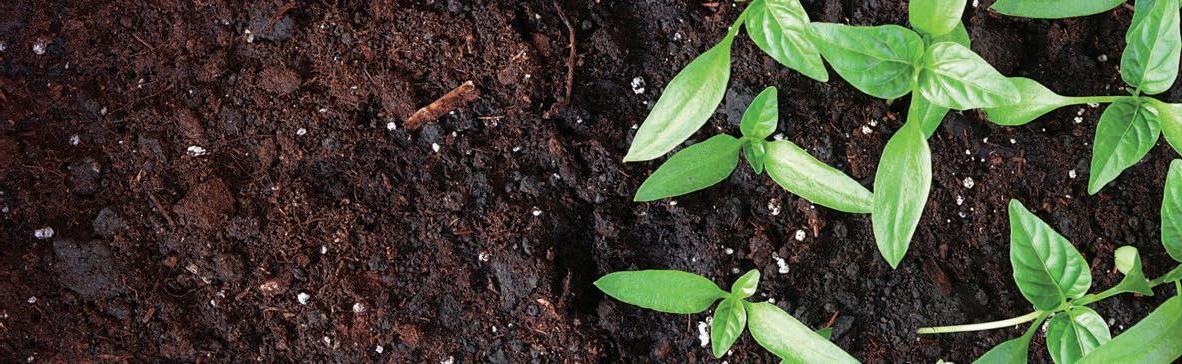
WHILE IT’S A TRYING TIME FOR MANY, AORA MEMBERS HAVE INDICATED THAT THE ORGANICS INDUSTRY IS STANDING STRONG, WRITES NATIONAL EXECUTIVE PETER OLAH.
It has been a challenging few months for each of us personally and often professionally. Feedback from many of our AORA Members has indicated that, while there have been some struggles, our industry seems to be weathering the COVID-19 crisis better than many others.
Despite this, I know that some of our members have needed to utilise the available government assistance to “tide them over” and keep their people employed. Others who have not yet used the government assistance may need to do so in the near future. That’s why I’d like to give this quick update on the future of these programs.
Recently, the Federal Government confirmed the extension of the JobKeeper payment by six months to March 2021, providing businesses with some certainty during this challenging time. From 28 September 2020 to 3 January 2021, full time employees will receive $1200 per fortnight, while part-time and casual employees working less than 20 hours per week will receive $750 per fortnight.
From 4 January 2021 to 28 March 2021, full time employees will receive $1000 per fortnight, while part-time and casual employees working less than 20 hours per week will receive $650 per fortnight. Businesses will still need to show a reduced turnover of 30 per cent (or 50 per cent if the businesses turnover is more than $1 billion), but reporting requirements have changed.
Businesses will now need to show that they have met the relevant decline in turnover test in both the June and September 2020 quarters to be eligible for the JobKeeper subsidy in the December quarter. Businesses will then need to demonstrate that they have met the decline in turnover test again in the December 2020 quarter to be eligible to receive the payment in 2021.
The Taxation Commissioner will have discretion to set out alternative tests that would establish eligibility in specific circumstances, where it is not appropriate to compare actual turnover in a quarter in 2020 with actual turnover in a quarter in 2019.
We are thinking of all of our members in Victoria and hope that your staff and their families are all safe and well.
I would also like to note that following the recent spikes in COVID-19 cases in Victoria and NSW, the AORA Board and Conference Committee have made the decision to move the rescheduled November Conference to 15-17 June 2021.
The health and safety of our members
Peter Olah says AORA is thinking of its Victorian members and hopes their staff and families are safe and well.
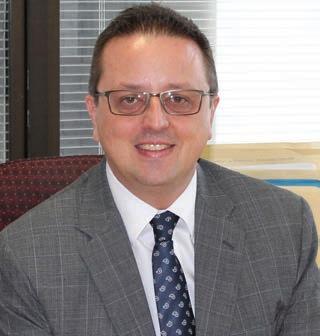
and attendees is our top priority, and after speaking to many of our partners, exhibitors, speakers and attendees, the overwhelming consensus is that postponing the event is the preferred outcome. The Adelaide Conference that was scheduled to be held in June 2021 will now take place in 2022.
If you have booked a ticket to the November Conference this will be rolled over to the 2021 conference. If you are unable to attend, please let us know by August 31 and we can arrange a refund.
We will be contacting speakers and exhibitors in the coming weeks to confirm availability, opportunities and attendance for 2021.
Thank you for your understanding. We can’t wait to see you in 2022.
APPLIED MACHINERY’S GENOX TWIN SHAFT HEAVY DUTY INDUSTRIAL SHREDDERS
Applied Machinery offers a diverse range of Genox shredders to process an array of waste streams down to specific sizes.
The company’s Genox X/M/W Twin Shaft series are designed for challenging materials such as tyres, car shells, barrels, cables, electronics and disc drives.
The M Series, a low speed, high-torque shredder, minimises noise and power consumption while achieving high throughput rates. These machines are particularly suited to size reduction of bulky and voluminous materials, which could include contamination such as metals or stones.
The shredder features a circular rotary screen to effectively control the output product size.
Segmented blade design also greatly reduces blade changing time and cost. The blade comprises of a blade holder and two types of blade segments, with or without hooks.
Both the M and X Series shredders are available with a hydraulic crammer to actively press the input material down into the cutting zone between the two shearing shafts.
The W Series twin shaft shredder is widely used in medium/low speed, high torque crushing applications.
These Genox high performance shredders are available in Australia exclusively through Applied Machinery.
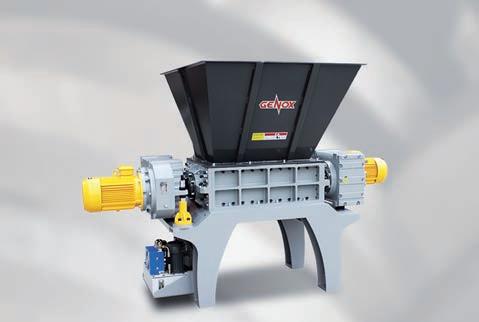
With the uniquely designed rotors and cutting chamber, the rotor knives and counter knives cut materials evenly, while also reducing the dust of raw materials. These heavy duty, high performance shredders are available in Australia exclusively from Applied Machinery.
Contact – Applied Machinery
P 03 9706 8066 E sales@appliedmachinery.com.au W www.appliedmachinery.com.au or www.genoxmachinery.com.au
Did you know that VENTING Refrigerant to the Atmosphere or simply burying/scrapping your whitegoods & aircon units with the refrigerant left in, is ILLEGAL
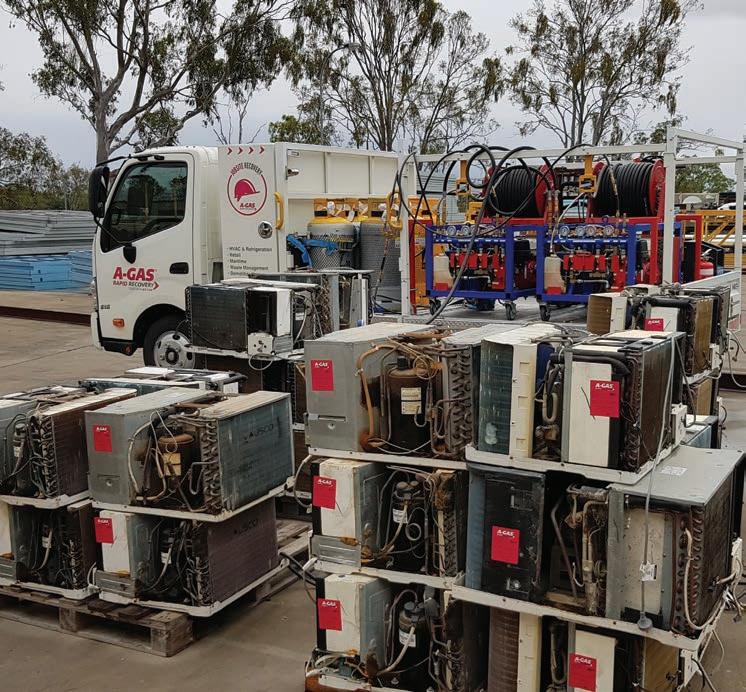
in Australia?
Don’t risk a fine, get the Arctick ✓
Call A-Gas Rapid Recovery 1800 002 427, Your Refrigerant Recovery Experts.
Bark King’s New Mid-Speed Shredder
BARK KING’S ASHLEY JOHNSTON DETAILS THE BENEFITS OF MID-SPEED SHREDDING AND PROACTIVE AFTERSALES SUPPORT, AS ORGANICS PROCESSORS ACROSS VICTORIA GET READY FOR SECTOR EXPANSION.
With the Victorian Government’s Recycling Victoria strategy set to reshape the organics sector, operators across the state are poised for a period of growth.
The strategy seeks to cut the volume of organic material sent to landfill by 50 per cent between 2020 and 2030, with an interim target of 20 per cent reduction by 2025.
Additionally, the strategy’s Infrastructure Fund seeks to encourage investment in organic waste sorting and processing infrastructure, while the Recycling Markets Acceleration package aims to build strong markets for products made from recovered organic waste such as compost.
This is welcome news to family
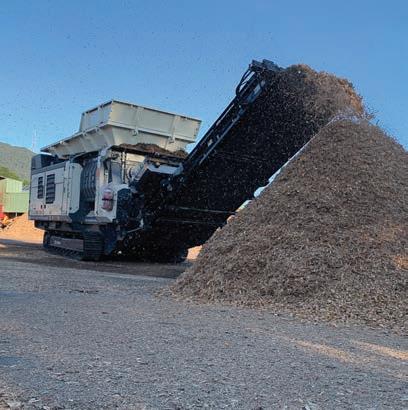
The TDSV20 is able to produce a controlled product size in one pass. owned garden supply distributor Bark King, which has been working to close the state’s organics loop since 1975. According to Business Development Manager Ashley Johnston, Bark King sources by-products from the Victorian, South Australian and NSW forestry industry, processing around 75,000 tonnes per year. As a supplier for government departments, landscape firms and educational institutions, sustainability has formed part of the company’s ethos since its beginnings. As such, Bark King applies strict guidelines on what it receives, processes and sells. To maintain those standards, Bark King operates a range of high-quality equipment, including a Terex Ecotec TDSV20 mid speed shredder – acquired through specialist equipment provider Finlay Waste and Recycling. The Terex TDSV20 features a double shaft shredder chamber, which was developed by Vecoplan specifically for mobile use. The mid-speed shredder also benefits from an independent hydrostatic drive and product sizing screen. This screen system, which is available in different sizes, comes complete with an intelligent protection system, allowing a desired particle size to be produced, while also being able to cope with foreign objects. “We were looking into different methods to improve our processes, predominantly around increasing safety and efficiency,” Johnston says.
“We find that with high-speed shredders, a lot of the product has to be reprocessed. But with the TDSV20 mid-speed shredder, we’re getting more finished product straight away – it’s a one-step shredding process.” Johnston adds that the TDSV20’s ability to produce a controlled product size in one pass is of huge benefit, saving Bark King both time and fuel. “The mid-speed shredder is also a lot quieter and safer for our team to operate,” he says.
The TDSV20 is supported by Terex Ecotec’s TEEvolution program, which incorporates high performance products with reduced noise emissions and lower engine operating speeds.
The TDSV20 features a user-friendly colour display that provides operators with analytical diagnostics to facilitate ongoing efficiency improvements.
Customisable shredding programs are also available, allowing operators to tailor the machine for specific applications.
Furthermore, Finlay’s support program is backed up by highly qualified service personnel to ensure customers are supported throughout the lifecycle of their machines. While the TDSV20 purchase is Bark King’s latest dealing with Finlay, Johnston says the two companies began working together 12 months ago when Bark King acquired a TDS820 slow-speed shredder. “Finlay was great, they took us to
their yard first in Somerton, and then additionally to their headquarters in Queensland and toured us around. That was the starting point of the relationship and we’ve not had any problems since” Johnston says. The TDS820 is purpose-built to process all types of material, whether it is domestic, industrial or bulky solid waste. The industrial shredder features customisable shredding programs that give operators the opportunity to configure the machine to their specific requirements, reducing material wrapping and maximising production. Johnston highlights Finlay’s service team as integral to the ongoing relationship.
“Nothing is too hard, they have an answer to every question,” he says. Johnston adds that Finlay’s service team have been particularly
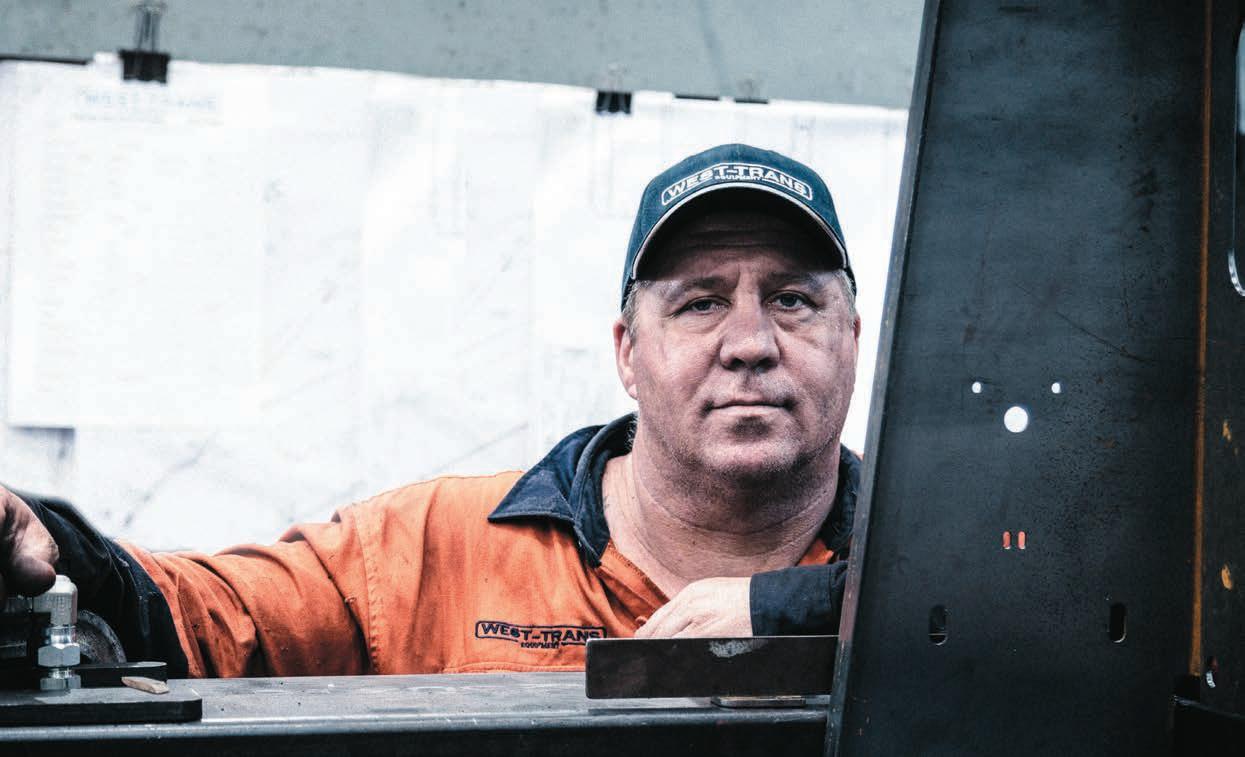
helpful in relation to the TDS820, which Bark King purchased from Finlay second hand.
Finlay supply a large range of used equipment, ranging from ex Terex Ecotec / Terex Finlay hire fleet machines to customer trade-in’s and customer used equipment that is currently for sale.
Johnston explains that while quality equipment is crucial, Finlay’s proactive approach to aftersales and servicing support is “more important than the machines themselves.”
“They’re precious pieces of equipment and downtime can be very detrimental for a company like ours,” Johnston says. “Finlay is always on the other end of the phone and that’s what’s important.
“We need to have confidence on that break down and servicing side, and Finlay understands that.”
Bark King’s Stuart Johnston pictured with Finlay salesrep Liam Maguire in front of the newly purchased TDSV20.
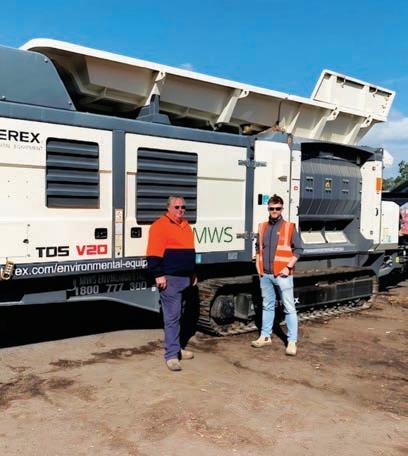
Contact - Finlay
P 1800 777 300 E info@finlay.com.au W www.finlay.com.au/
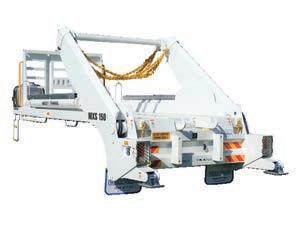
Shredding for soils
WASTE MANAGEMENT REVIEW SPEAKS WITH PHOENIX POWER RECYCLERS’ CHRIS ALEXANDER ABOUT IN-VESSEL COMPOSTING MATERIAL COMPOSITION AND THE ROLE OF EFFICIENT SHREDDING.
The Pronar Shredder’s steel working parts are made of wear-resistant materials, which ensure long and trouble-free operation of the machine.
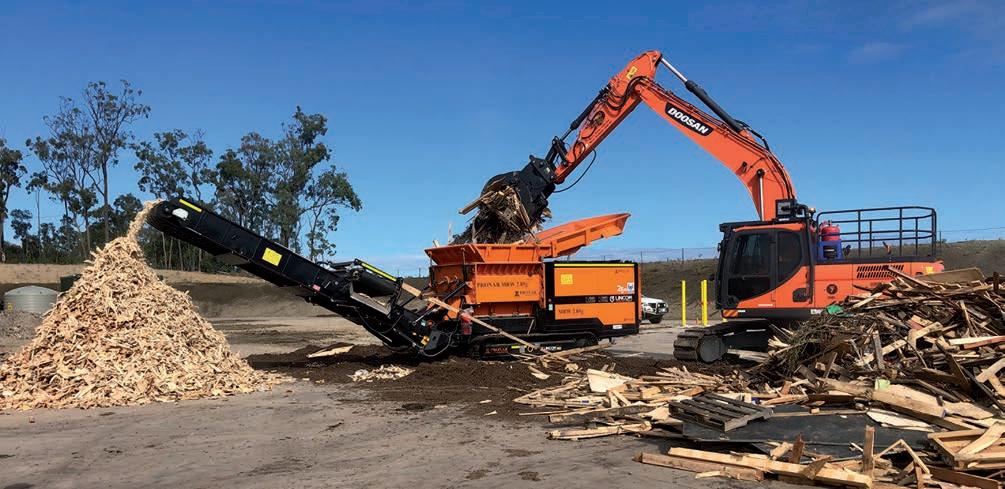
Having operated successfully for many years in the supply of garden soil and compost, Phoenix Power Recyclers is in the process of commissioning a state-ofthe-art in-vessel composting facility with a capacity to process up to 50,00 0 tonnes per annum.
The facility receives and processes waste in a negative pressure environment, meaning deliveries, loading and unloading of the tunnels is all completed in a controlled environment. The tunnels act to optimise the pasteurisation phase of composting through a fully automated control and feedback system.
According to Chris Alexander, Phoenix Power Recyclers General Manager, the company is committed to staying at the forefront of industry and resource recovery technology.
As such, Phoenix relies on high quality processing equipment to maintain consistent input and output material streams.
“With in-vessel composting, the structure of the input material is critical, as success relies on the ability to sparge air through the floor of the tunnel. If air cannot flow through the product, there’s really no point,” Alexander says.
To achieve required airflow and material composition, Phoenix invested in a Pronar slow-speed shredder earlier this year – acquired through waste and recycling equipment specialists Lincom Group.
Pronar slow-speed shredders are designed for pre-processing of all kinds of materials, be it municipal waste, construction and demolition waste, or in the case of Phoenix, organics.
An important advantage of the machine is its mobility, Alexander says, or the ability to quickly transport the shredder across Phoenix’s site. The machine is equipped with a Caterpillar diesel engine with a capacity of 298 kilowatts. Alexander says this creates a high-level of processing efficiency, adding that Caterpillar engines can always be relied on to provide durable service.
Grinding is achieved via two synchronously running shafts grinding in the pressure chamber, while shredding is done by two 1700-millimetre shredding shafts.
The unit is available with a choice of shaft configuration as well as various Breaker Bar types to allow for flexibility depending on the material
being processed, as well as the end product size required.
Operators have the choice of various pre-set or custom operation programs. The working parts are made of quality wear-resistant materials, ensuring long and trouble-free machine operation.
Key benefits of the shredder, Alexander says, are the aforementioned engine quality, less moving parts and overall machine functionality. He adds that the shredder’s ability to protect itself via a durable fencing arrangement is impressive.
In addition to the quality of the shredder, Alexander highlights Lincom’s ability to provide high-level technical support.
“Lincom operate and present very professionally. The way they operate their business offers a level of security, and the aftersales support is consistent – their sales and technical support team are very knowledgeable and communicative,” he says.
Lincom has been distributing Pronar shredders since 2017, and with over 25 years’ experience as a leading provider of material processing equipment, takes pride in building strong relationships with its valued customers.
“Lincom Group takes the time to understand the scope of our customer’s operation and the task at hand,” a Lincom spokesperson says.
“Our sales staff receive continual product support training from the OEM factories on a regular basis to ensure they understand the products and the application to answer any questions, ensuring customers get the most efficient equipment for the right application.”
Lincom’s head office is based in Southern Queensland, with a fully equipped manufacturing facility for custom fit outs, safety guards, machine rebuilds and repairs. The National Spare Parts distribution centre and the operational field service fleet for after-sales support are also based on the same site.
Additionally, Lincom maintain an online parts inventory database for all its locations and can access real-time information and locate parts in every branch in the country.
“Our commitment and long-time association with transport and logistics companies give us flexibility and the ability to deliver parts to you on time,” the spokesperson says.
Contact - Lincom Group
P 1800 182 888 E sales@lincom.com.au W www.lincom.com.au
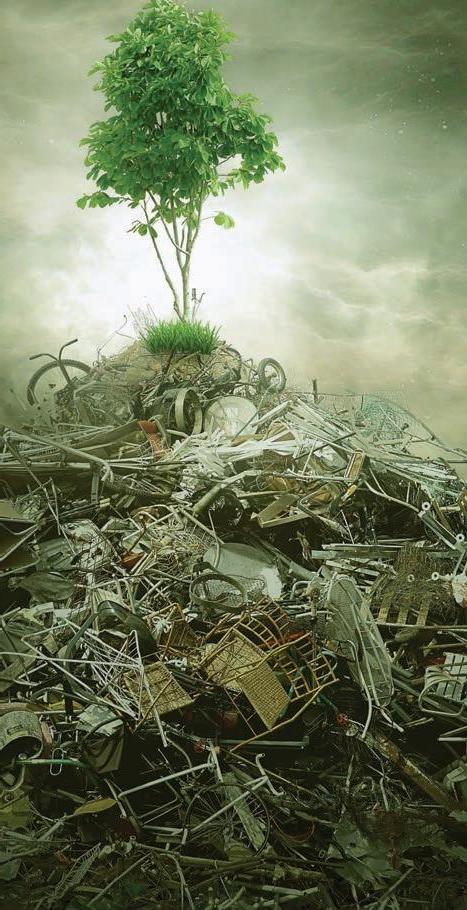
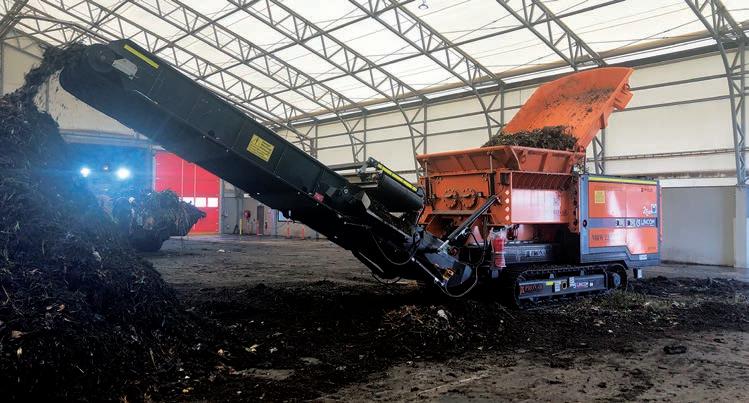
Chris Alexander says key benefits of the Pronar Shredder include engine quality, less moving parts and overall machine functionality.
Pulverising C&D
WASTEDRIVE’S BLAIR VINCENT OUTLINES HOW ROBUST AND DURABLE EQUIPMENT CAN HELP C&D PROCESSORS MEET THEIR ENVIRONMENTAL AND ECONOMIC OBLIGATIONS.
The Australian construction industry has grown significantly in recent decades, with population growth driving an influx of new infrastructure projects, both domestic and civic. As a result, the level of waste produced by construction and demolition (C&D) has grown alongside it. According to the 2018 National Waste Report, C&D waste accounts for almost 40 per cent of total waste produced in Australia by weight. Between 2016-17, more than 6.7 million tonnes of C&D waste was sent to landfill.
While rising landfill disposal costs provide an incentive to recycle, the material makeup of C&D presents a myriad of processing challenges.
Blair Vincent, Director of Australian and New Zealand based equipment distributor Wastedrive, says that to address those challenges, processors need access to robust and durable equipment.
Throughput is key, he adds, highlighting that while a commitment to driving greater C&D recovery is the backbone of the industry, it cannot be achieved without healthy economic viability.
Vincent notes a partnership with US based equipment manufacturer American Pulverizer as a key component of Wastedrive’s commitment to helping its clients deliver on their
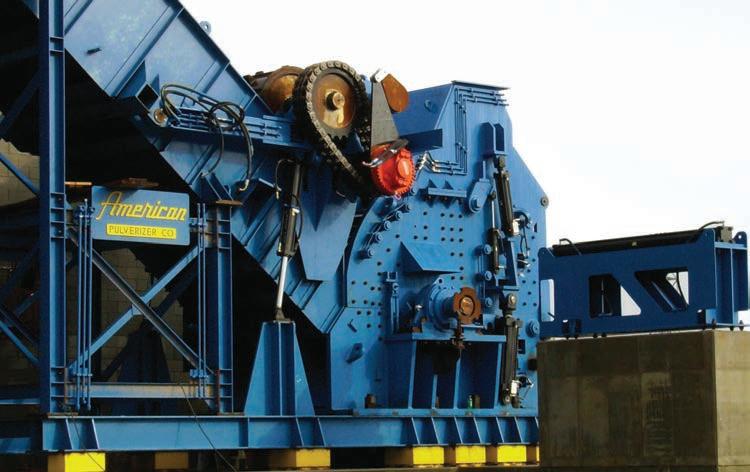
Wastedrive’s heavy-duty scrap shredder features self-supporting grates, with oversized feed roll shafts enclosed in cast steel pillow blocks to facilitate abrasion resistance. environmental and financial obligations.
Since 1908, the American Pulverizer Company of St. Louis, Missouri has been making size-reduction equipment for a range of industrial markets.
With origins in coal pulverising, the company has since widened its focus to address other markets, including the crushing and screening of scrap metal and C&D.
Given American Pulverizer has been operating for over 100 years, Vincent says the company’s shredders are equip with top-level design and manufacturing.
Plus, being American made, there is a high degree of quality assurance, he adds.
“Another benefit, particularly in our turbulent economic and political climate, is that it’s highly unlikely there will be trade disruptions with the US, unlike other parts of the world,” Vincent says.
“This means we will consistently be able to supply our clients with high quality and efficient machinery.”
Wastedrive has been operating in Australia and New Zealand for over 25 years. Vincent explains that Wastedrive’s primary focus is providing a turnkey solution to the recycling industry, primarily incorporating balers, Accent Wire Ties and conveyors.
He adds, however, that interest in the company’s American Pulverizer shredder range is growing.
“One of our standout offerings is the heavy-duty scrap shredder, which features a high-top middle housing design that allows for less horsepower consumption and increased casting wear life,” Vincent says.
The heavy-duty scrap shredder also features self-supporting grates, with oversized feed roll shafts enclosed in cast steel pillow blocks to facilitate abrasion resistance.
American Pulverizer shredders utilise a custom-made gear box, which delivers one of the highest documented torque values in the industry. Wastedrive also offer an American Pulverizer Impactor SRI, which Vincent says suits similar applications to shredders, while employing a slightly different process.
Infeed material enters the impactor through a feed chute and is engaged by rigid rotor hammers before being hurled against impact arms.
Material size reduction is caused by the impact against impact curtains and hammers, and by collision with new infeed material entering the crusher.
As such, the machine principal promotes a uniform cubical product.
“We provided a proposal to a customer for the Impactor recently, and when I told them the machine would give them the ability to process up to 150 tonnes of C&D an hour, they queried me,” Vincent says.
“The throughput seemed too good to be true, but it’s not.”
Wastedrive provides its clients with a fully integrated service, Vincent explains, from foundational drawings to make sure side loads are optimised, through to the logistics of getting equipment onsite.
“We look after every aspect of the
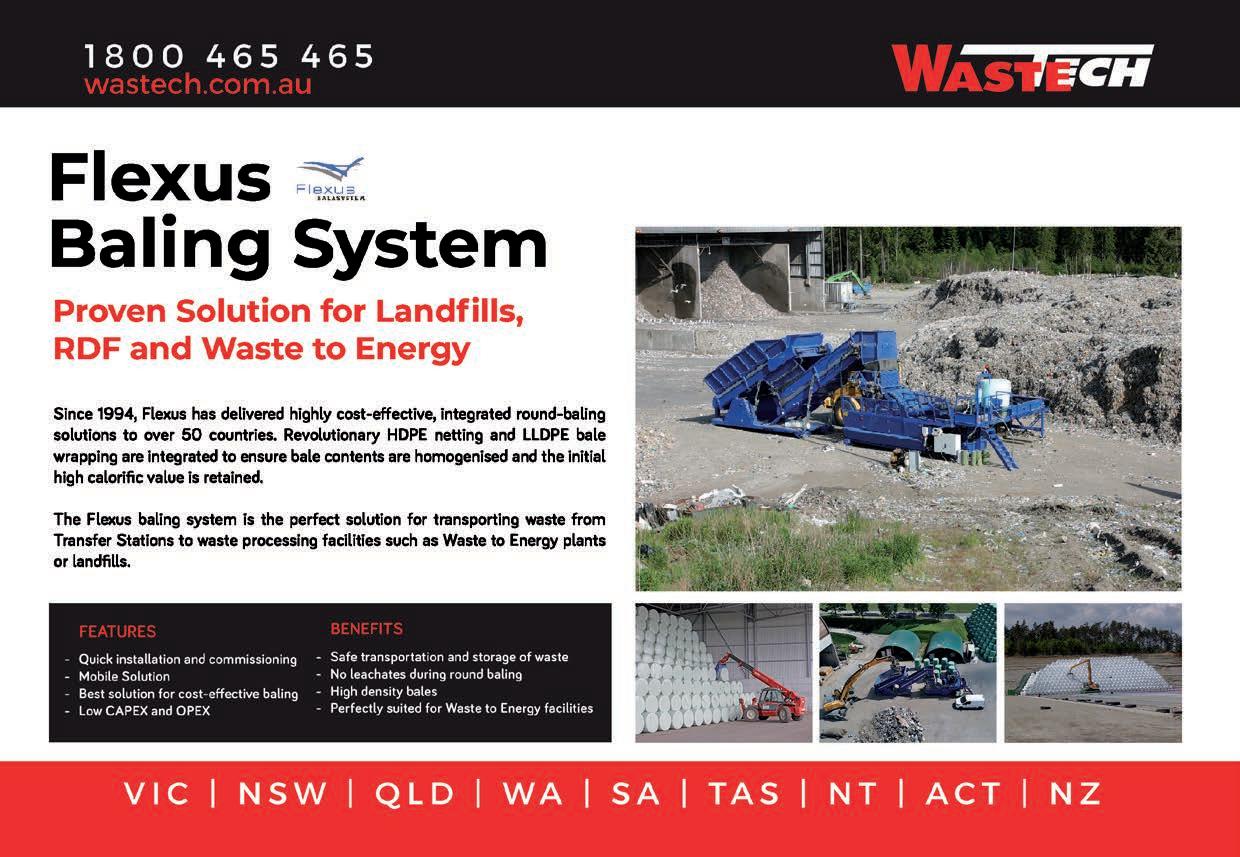
installation and commissioning. We also have an American Pulverizer representative who comes down from the States to help with commissioning,” Vincent says.
“On the aftersales front we provide parts for all of our customer and can ship those directly to them. We can also assist with servicing.”
Vincent adds that Wastedrive’s relationship with its clients doesn’t stop once they’ve bought the product.
“Wastedrive is committed to responding to clients quickly and providing cost effective, competitive pricing, turnkey logistics and schematics,” he says.
“Ultimately, we’re here to assist.”
Contact - Wastedrive
P 0414 071 331 E info@wastedrive.com W https://wastedrive.com.au/
Nextshred
SHRED-TECH’S JUSTIN JOHNS EXPLAINS HOW THE COMPANY’S PLANTBASED SHREDDING SYSTEMS HIGHLIGHT CONTINUOUS IMPROVEMENT, QUALITY AND INNOVATION.
Shred-Tech began in the late 1970s producing stationary two-shaft shredders for a wide range of manufacturing plantbased applications. By the middle of the decade, Shred-Tech had developed one of the world’s first mobile shredding trucks, designed to shred confidential office paper and documents on-site.
The company also offers a range of plant-based shredding and recycling systems, including two-shaft and fourshaft shredders, single-rotor screened shredders and granulators, as well as large primary shredders.
According to Justin Johns, Sales Manager Shred-Tech Asia, ShredTech’s latest product innovation is the CR2A645 plant-based shredder.
He explains that the CR2A645 is ideal for shearing engine blocks, cylinder heads and general mixed metal scrap.
“The shredder features four Linde hydraulic motors powered by two 200-kilowatt power packs,” Johns says.
“Hydraulics allow independent shaft speed and ration direction for
Shred-Tech can configure systems for virtually any shredding application.
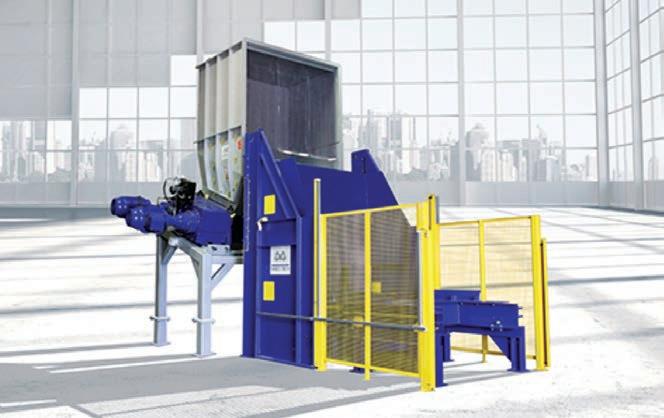
re-orienting materials in the chamber when shredding large or difficult items.”
The CR2A645 has a maximum shaft speed of approximately eight rotations per minute.
“Replaceable segmented tool teel cutters last 1500 to 2000+ hours depending on application, with metal throughput rates between 15 to 20 tonnes per hour,” John says.
He adds that the company’s commitment to building best practise shredders requires a laser focus on continuous improvement, quality and innovation. Headquartered in Cambridge, Canada, Shred-Tech prides itself on a global commitment to engineering innovation and quality. The company also has offices in Thailand, the US, the UK, Japan and Australia.
“More than 6000 shredding and recycling systems have been installed worldwide in locations as diverse as Fortune 500 manufacturers, hospitals, government and military facilities.”
Johns explains that almost every order is customised to a certain extent – with two systems rarely identical.
Shred-Tech’s custom process begins with gathering customer requirements, including the nature of the material, reduction size and required volumes needed to shred. Johns says that the reason for the shredding can even influence the final equipment design.
“With cutting chambers ranging in lengths from 85 to more than 3000 millimetres, and horsepower ranging from five to 1200, Shred-Tech can configure a system for virtually any shredding application,” he says.
The company’s systems are configured with the correct knife design, chamber size, horsepower, feed and discharge rates to suit the application.
“In many cases, customers approach Shred-Tech with a problem that many of their competitors haven’t been able to solve,” Johns says.
“Since Shred-Tech has a broadly skilled in-house engineering team, they are able to work closely with the sales department and the customer to find a viable solution.
“Coupled with a vigorous quality control process, in-house assembly and manufacturing, Shred-Tech builds and manufactures the world’s best shredding and recycling systems.”
Contact - Shred-Tech
P 1 800-730-684 E jjohns@shred-tech.com W https://shred-tech.com/
TEREX ECOTEC TDS 825 SLOW SPEED SHREDDER
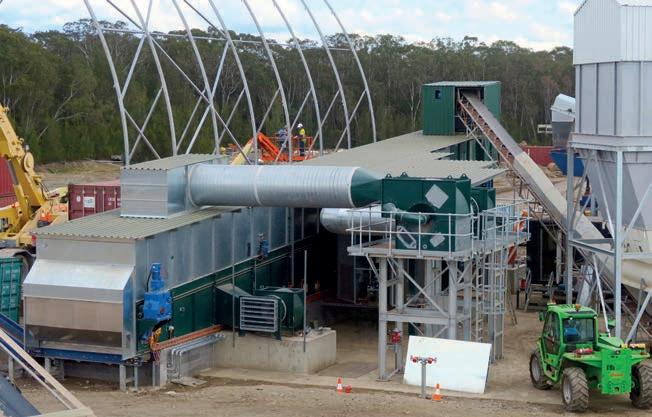
Customisable shredding programs allow operators to configure the machine to their specific requirements.
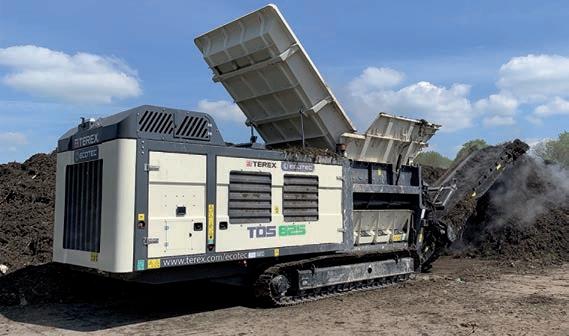
Terex Ecotec’s TDS 825 Slow Speed Shredder is suitable for all material types including household waste, bulky waste, commercial waste, green waste, waste wood, tree stumps and roots.
The TDS 825, which is available in Australia through Finlay Waste and Recycling, is manoeuvred via a robust tracked undercarriage making it an ideal solution for difficult terrain.
Customisable shredding programs allow operators to configure the machine to their specific requirements to maximise production.
The hydrostatic drive offers protection against contamination and allows for bidirectional shredding, while independent gear boxes enable each shaft to run separately, helping reduce warpage and improve shredding.
Should a blockage occur, the shafts can be controlled via the radio remote control, allowing material to be repositioned before attempting to shred again.
The double shaft shredder has 2.5 long shafts made from solid steel, with a fully welded tooth configuration giving an extremely high production rate with excellent size reduction.
Located in the centre of the chamber, directly below the shredding shafts is the replaceable breaker bar, which controls the end product size by retaining material in the chamber to aid reduction and protects the transfer belt from damage caused by large pieces of contaminants.
The high volume, tipping hopper increases the feed area providing optimum material feed and can be activated using the control panel or via the remote control. Tipping cycle times can be configured to suit the application.
Contact - Finlay
P 1800 777 300 E info@finlay.com.au W www.finlay.com.au/
CD28800 Conveyor Drier
WE DRY
Woodchip
Pharmaceutical Waste MSW
RDF Digestate Glass
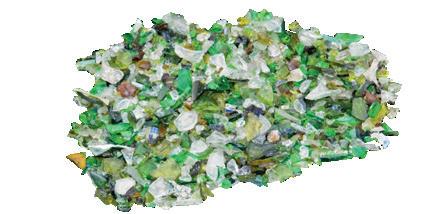
AND MORE
CONVEYOR DRIER TRULY MULTI-PURPOSE!
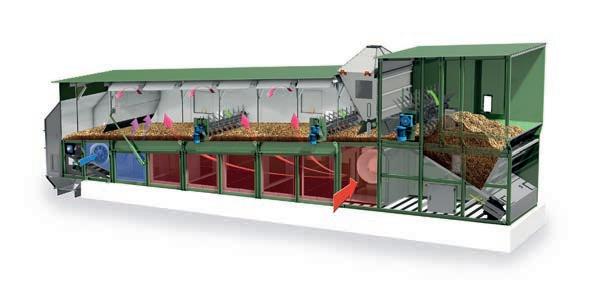
Alvan Blanch APAC Region
T: + 61 435 776 796 E: jim.duncan@alvanblanch.com.au
UK Headquarters: Chelworth, Malmesbury, Wiltshire, SN16 9SG. England T: +44 (0) 1666 577333 F: +44 (0) 1666 577339 E: info@alvanblanch.co.uk
Iconic hazardous waste removal
ASBESTOS REMOVAL REQUIRES SOUND AND FLEXIBLE TRANSPORT SOLUTIONS THAT ARE BOTH EFFICIENT AND RELIABLE.
Despite clocking up 53,000 kilometres in a year and over 1000 kilometres per week, Curtis Lyons has had no issues or unnecessary downtime with his FRR Tipper.
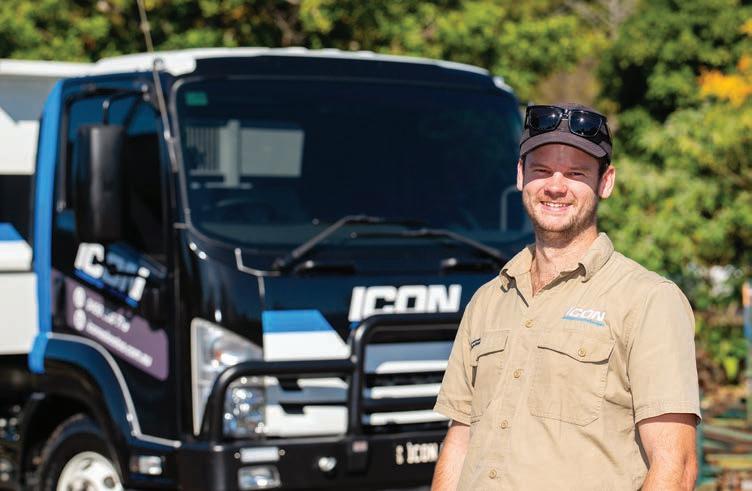
Roof shingles, water supply lines, wall insulation, carpet underlay—these are just a handful of possible areas where asbestos might be found, especially if the building was constructed before 1990.
A naturally occurring mineral, asbestos was once widely used in building construction due to its affordability, flexibility, strength and heat and electricity insulating properties.
However, exposure to asbestos fibres carries health hazards, such as cancers like mesothelioma. As such, the use of asbestos has been banned in Australia since 2003.
Due to its once-pervasive use in the construction industry, asbestos is still frequently encountered, especially when working on older buildings such as residential homes.
Its removal is not lightly regarded, and is best handled by hazardous waste removal professionals such as Icon Asbestos Removal.
ICON does everything from residential to commercial asbestos removal, which includes Class A asbestos removal. This includes a higher risk, such as in removing friable asbestos – which is in a powder form and therefo re more likely to release fibres into the air – and removing asbestos in locations such as government buildings, factories, schools and hospitals.
For business owner, Curtis Lyons, the safety of his employees is paramount in this line of business. On any job, the ICON crew is suited up with respirators and other necessary personal protective equipment. Decontamination showers are al so available for an extra layer of safety. But safety precautions in ICON’s operations doesn’t stop there.
For Lyons, he understands that any professional waste removalist operation requires a sound and flexible transport solution that’s both efficient and reliable, which in turn enhances safety and productivity when removing and transporting hazardous waste.
Supported by his FRR 107-210 Tipper from Isuzu’s Ready-to-Work range, Lyons trusts that operations will run smoothly from start to end.
Once the asbestos is carefully removed, it is loaded onto the back of the FRR 107-210 Tipper, which is double-lined with plastic to seal up the removed material. The waste is then transported to licensed dumps.
With a GVM of 10,700 kg and GCM of 16,000 kg, the FRR 107-210 Tipper is well specified for this task. Equipped with Isuzu’s four-cylinder 4HK1 engine, the FRR Tipper’s power and torque sit at 154 kW at 2400 rpm and 726 Nm at 1600 rpm, respectively.
“It probably shocks a few other people in traffic when they see the size of the truck and the heavy
The ride height of the FRR Tipper cabin means operators can see everything on the road ahead.
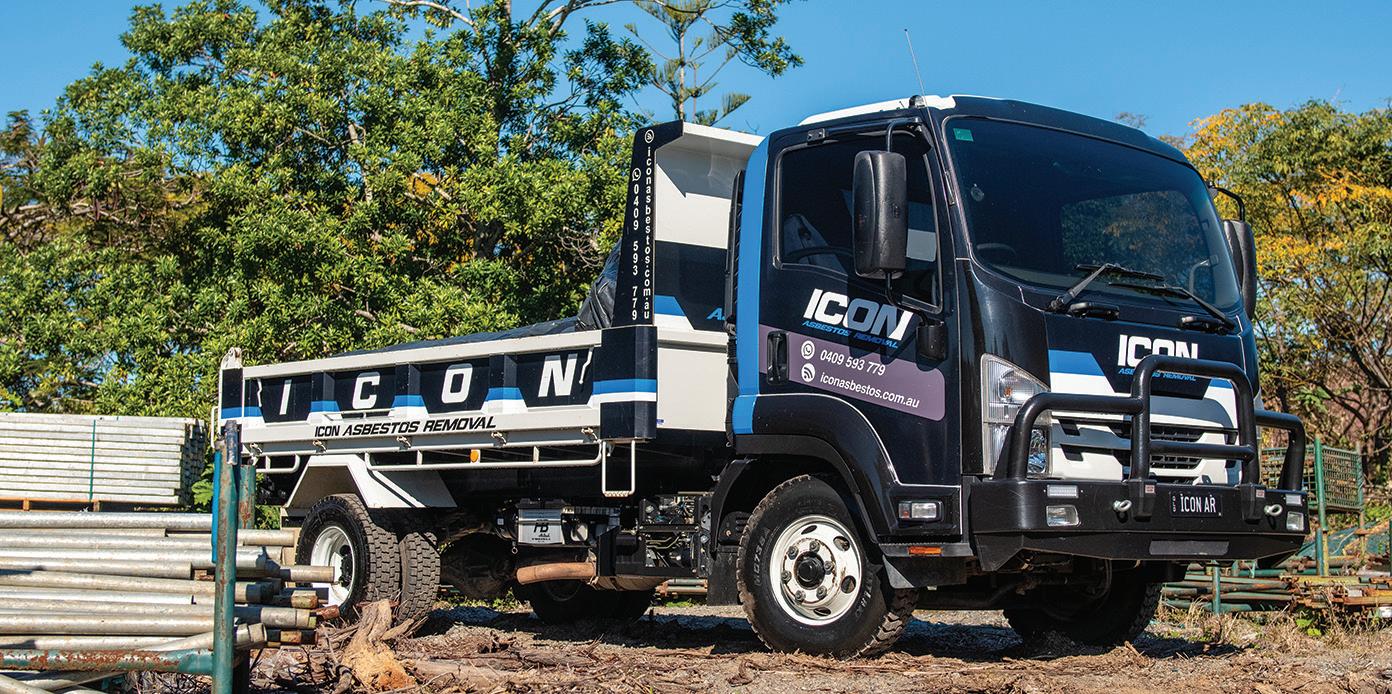
load, tackling inclines without a problem,” Lyons says.
“The most impressive thing is that I’ve got a heavy load with over five tonnes in it and the truck is still driveable through congested Brisbane traffic.”
The ride height of the FRR Tipper cabin means Lyons can see everything on the road ahead, and large passenger windows mean peripheral vision is uninhibited too.
“The vision is great because we can see what’s coming up ahead and stop earlier if we have to,” Lyons says.
Besides power and payload capacity, the truck is a neat balance between being compact enough to access tight, hard-to-reach spaces and having enough load space for its unique application.
“With residential work, we can easily get the FRR Tipper down a side access or through gated driveways. And with the truck bed size – you can get two
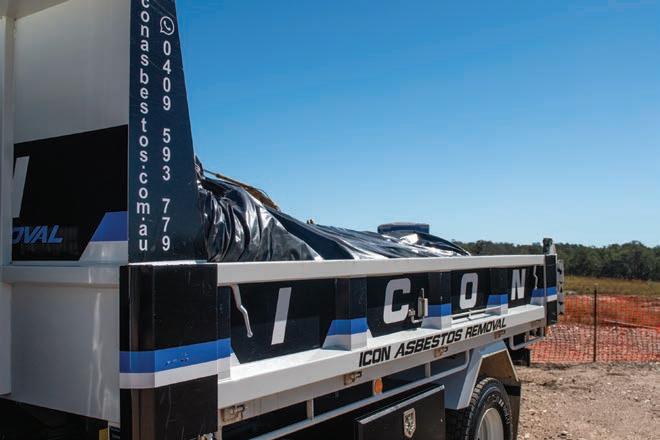
Once asbestos is carefully removed, ICON loads it onto the back of the Tipper, which is double-lined with plastic to seal up the removed material. asbestos sheets laid flat next to each other, side by side. That’s a big win,” Lyons says.
“This means we can keep the load weight down nice and low, and get two or three jobs in each truck load without having to do multiple trips to the tip.”
For Lyons, driving the FRR Tipper five to six days a week has been a pleasure. More importantly, it is also reliable – a must-have in the hazardous waste business, where smooth and hassle-free transport is paramount.
Despite clocking up 53,000 kilometres in a year and over 1000 kilometres per week, Lyons has had no issues or unnecessary downtime with his FRR Tipper. For Lyons, this and the accessibility of the many Isuzu Trucks authorised dealerships and service centres means he and his team can deliver this unique service to their customers quickly and efficiently.
“If I had an Isuzu truck and another truck side by side to choose from, I’d go with the Isuzu every time,” Lyons says.
Contact - Isuzu
P 1800 035 640 W www.isuzu.com.au
Maximising landfill life
JOHN GLOSSAT, NATIONAL BUSINESS DEVELOPMENT MANAGER AT TUTT BRYANT EQUIPMENT, EXPLAINS HOW ONE MACHINE HAS HELPED LANDFILL OPERATORS TRANSFORM THEIR COMPACTING ABILITIES.
According to a recent industry segment survey, the major driving factor of the global waste compactor truck market is growing waste due to urbanisation and rising population. However, following COVID-19 lockdown restrictions this year, operators have seen growing waste due to a huge increase in volumes of household rubbish and dumping of waste triggered by a combination of more online shopping, home improvements and clearing out of unwanted possessions during stay at home orders.
Compacting landfill waste has never been more highly sought after. Rising domestic waste that can’t be disposed of at recycling centres is a concern to regional and metro areas across the nation. In fact, according to the Global Garbage Compactor Truck Market industry survey released this year, the need for landfill compactors will boom over the 2018- 2025 forecast period. The Asia-Pacific region is also anticipated to exhibit a higher growth rate across the global market.
John Glossat, National Business Development Manager at Tutt Bryant Equipment says versatile compactors are an essential tool for councils and contractors across Australia, especially during this current climate. He credits the latest BOMAG landfill compactor as a game-changer for Australian operators.
According to John, BOMAG has been a market leader in compaction technology since 1957 and provides a range of quality machines and solutions to support the waste sector. He says a recent highlight has been the introduction of BOMAG BC473RS-3 to landfill sites that have transformed operations due to the multi-function applications.
Last year Tutt Bryant was approached by a landfill operator in Tasmania. The operator wanted a streamlined machine that was also cost effective.
“We were so excited to show them a multi-functional compactor with high lift applications that they’d never seen before,” Glossat says.
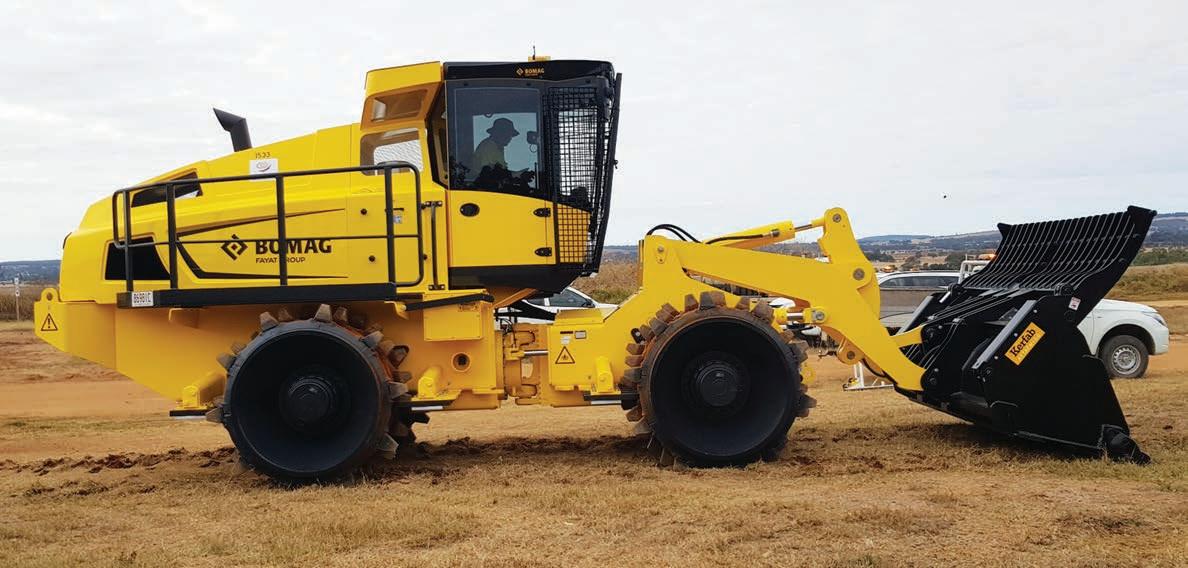
“The operator in Tasmania had a smaller landfill to compact and sort materials including loading applications and they were using various machines including excavators, loaders to compact, dig, load material and compact.
“You could only imagine how thrilled they were to hear the news that we could provide them with one machine that can meet the needs of all their required tasks.”
Since installation last year, Glossat has since visited the site in Tasmania and says the operator was proud to show the machine in action and demonstrate the ongoing efficiencies at the site since the Landfill Compactor arrived.
Glossat talks with pride explaining the endless benefits of the BOGMAG BC473RS-3.
“There are many various designs available however the unique set up here is a versatile Compactor like no other which can be used for many applications,” he explains.
“ If you want to load, to compact, to grab, to dean or more - it can all be done with this one machine.”
Tutt Bryant believes this revised concept sets new standards and the versatility has proven to be a hit with end-users especially smaller council owned landfills. Following the success in Tasmania, Tutt Bryant recently delivered another BOMAG BC473RS-3 into a facility in Western Queensland in July this year.
“The operator in Queensland was considering the use of excavators, dozers and loaders for its operations just like we saw in Tassie, after seeing the multi-functional capabilities of one machine the choice of purchasing this landfill compactor was a no brainer,” he says.
Glossat says the features of the machine stand out immediately fitted with a 4in1 multi-purpose bucket locally manufactured through Kerfab in VIC.
“Spreading, loading, sorting or compacting - the high versatility of this model produced a clear vote of acceptance and recommendation. It handles sensitively with a fast response time and the operator vision over the large hood is extremely clear not to mention also hydraulically operated,” he says.
Glossat highlights that one of the most impressive features is its practical 4 X polygon wheel design with scraper bars fitted to the front and rear of each wheel including wire cutters to keep the tools extremely clean for maximum compaction efforts.
“Fitted as standard is a reverse camera with optional reverse sensors available to meet operator’s most demanding safety requirements, an auto greasing system for constant maintenance of pins and bushes and the popular Telematics system to remotely manage your machine, check its position, engine hours, machine performance and more with a click of a mouse from nearly any device,” he says.
Extending the life of landfills in Australia requires a multi-functional compactor.
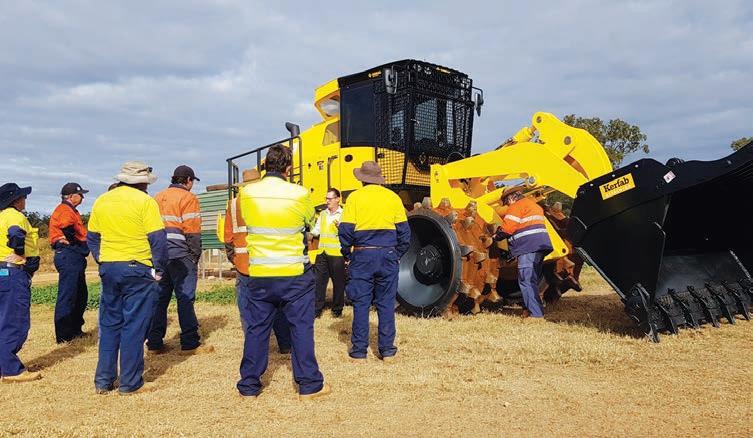
Other notable features include automatic reports which can be set as required that provide full transparency on fuel consumption, idle times, and the potential for fleet optimisation. “The underside is completely sealed and closed off to prevent debris entering the engine compartment. Clean, safe and no external loss of fluids. This will also contribute to minimising the risk of fires under the hood caused by waste entering nasty little openings,” Glossat says.
Landfill operators from small councils to larger waste contractors have a duty during this time to provide essential waste management services to Australian communities.
Tutt Bryant provides a range of Landfill Compactors from 24T to 58T with various models and configurations.
“We are helping streamline waste management through highly versatile machines that are important tools used in maintaining an efficient operation and extending the life of landfills Australia wide,” Glossat says.
Contact - Tutt Bryant Equipment
P 1300 658 888 E John.Glossat@tuttbryant.com.au W tuttbryant.com.au