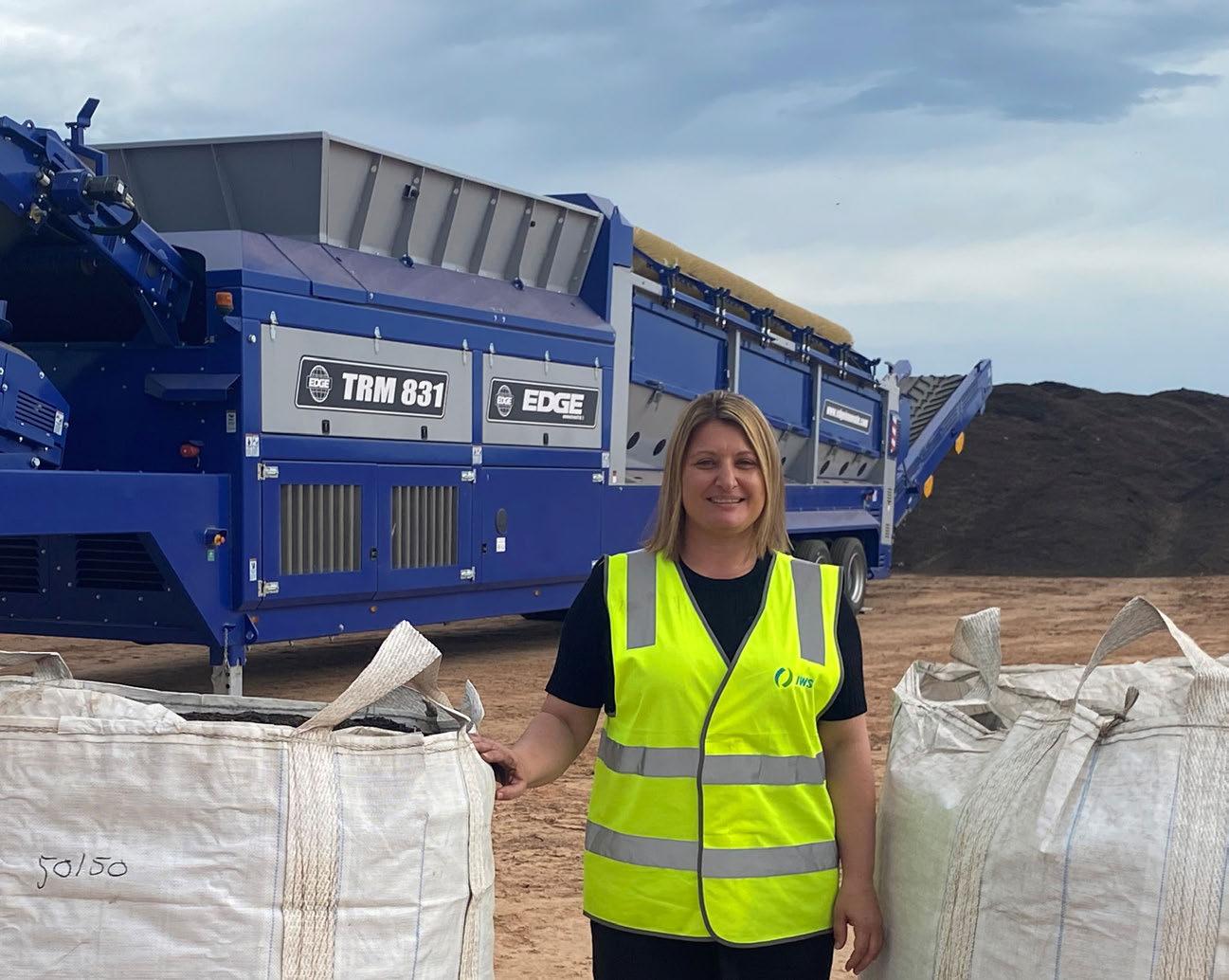

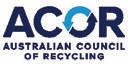
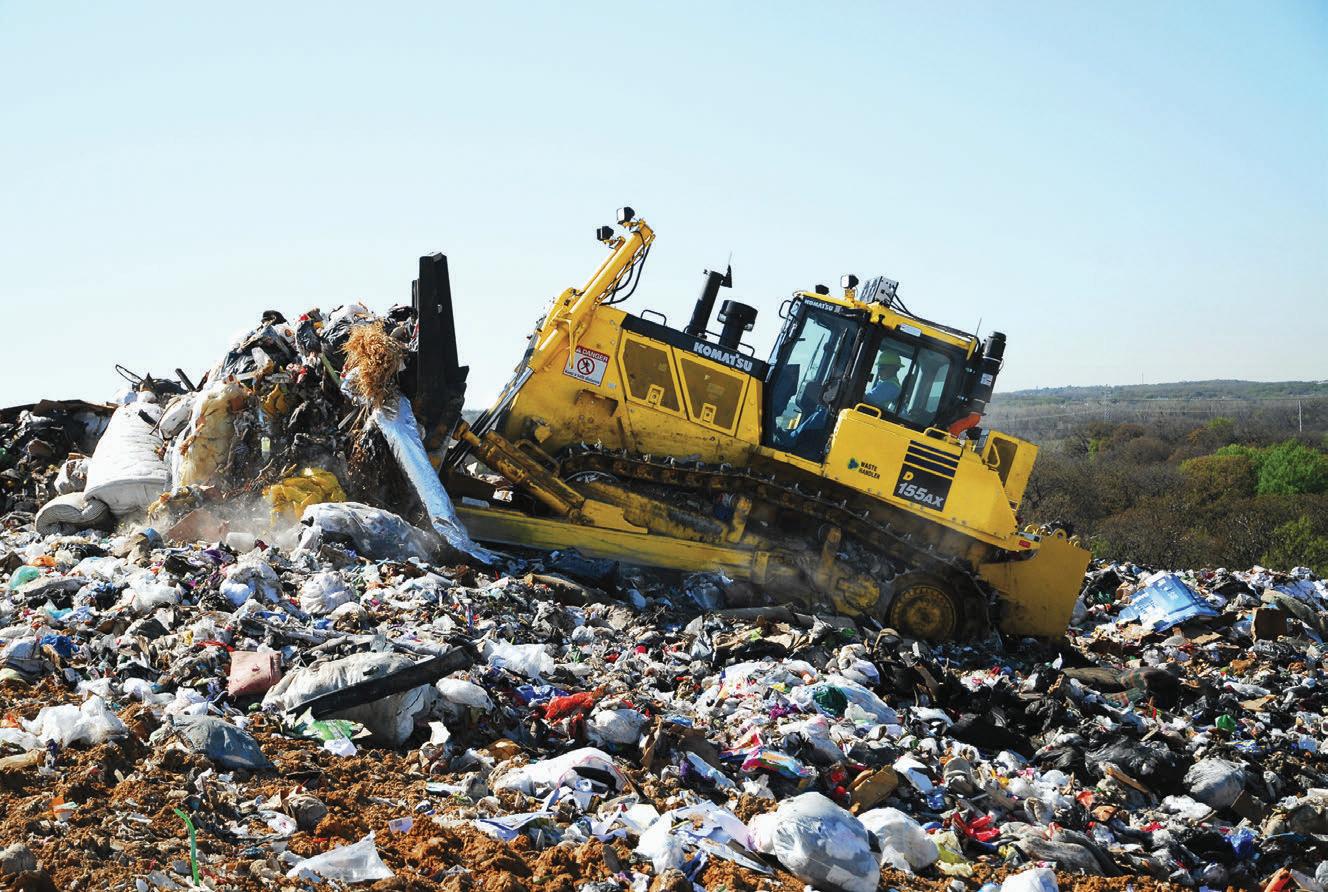
The waste processing industry requires purpose-built equipment for moving highly variable materials. Komatsu creates machines and solutions designed specifically for the difficult terrain and materials involved with handling waste. Our advanced Dozers equipped with smart technology, are engineered for productivity to support your goals of a zero-harm environment.
e Eden Project o ers valuable lessons for rehabilitation projects across Australia.
Bringing Living Earth’s natural soil superfood to Australian markets.
“OUR ULTIMATE AIM IS REJUVENATING SOILS FOR FUTURE GENERATIONS. OUR ETHOS IS ALL ABOUT SUSTAINABLE DEVELOPMENT AND REDUCING WASTE.”
Grace Barila, Environmental Manager Living Earth Australia
Introducing
What
Putting
Constructing a waste management eet from the ground up.
Partnership
on shared outcomes.
Loaders for kerbside and municipal waste collection.
STG Global trucks are cleaning up.
Australia’s favourite garbage truck.
How you can help tomorrow’s waste industry bene t from diversity.
How contamination is a ecting organics recycling processors.
Delivering a bespoke waste management solution for organics.
Pushing for a greener future. 56 GIVING AT THE OFFICE
New recycling for o ces and cafes.
Giving used cooking oil a new life.
Tutt Bryant solutions for C&D waste.
Shaping a sustainable future.
Caterpillar unveils the new MH3050.
Wheel loaders that meet the demands of waste management.
Industrial and production machinery supplier enters recycling realm.
Bringing global tech Down Under.
We’re about to make a big splash in trash, because we’ve just launched a new range of dual control trucks. With lower tare weights than similar models from our competitors, these new trucks can carry bigger payloads. Up to 300kgs per trip! Apply that across a fleet and you’ll see huge boosts in e ciency and reduced operating costs. Visit isuzu.com.au/waste
“Oh, you’re a garbo.”
It’s one of the most common responses people in the waste and recycling industry receive when they tell others what they do. None more so than the frontline workers at land lls around Australia.
But it’s a narrow view of the work carried out at a modern land ll. While they may be the oldest and most common form of waste disposal, land lls today are carefully engineered, managed and regulated to eliminate potential environmental impacts.
ey’ve evolved from being a hole in the ground to resource recovery powerhouses with potential revenue sources and attract some of the brightest minds, determined to change the perception of waste.
In this edition of Waste Management Review, we get an insight into some of the latest advances in land ll management and what it takes to create one of the nation’s most unique land lls.
Environmental scientist Evan Kyriakopoulos has worked in the industry for more than two decades and views land ll as a necessary piece of the puzzle for future waste management. It was eye-opening to chat with him about the advances being made at land lls in Australia and around the world.
We also look at an Australian-developed PFAS treatment technology that is nding success in the United States. e Water and Carbon Group, the company behind the technology, has recently secured a $US10 million investment to expand its reach.
And we lift the lid on more Australian ingenuity that is helping improve operations and safety for waste facilities.
Beyond the technology-based developments, we look at why investing in people is essential for the future of the sector, from training through to encouraging a diverse workforce.
We also explore the adoption of sustainable waste solutions and introduce some new players to the industry.
Happy reading!
Lisa Korycki
CHIEF OPERATING OFFICER
Christine Clancy christine.clancy@primecreative.com.au
PUBLISHER
Sarah Baker sarah.baker@primecreative.com.au
MANAGING EDITOR
Lisa Korycki lisa.korycki@primecreative.com.au
JOURNALIST
Jennifer Pittorino jennifer.pittorino@primecreative.com.au
HEAD OF DESIGN
Blake Storey blake.storey@primecreative.com.au
DESIGN
Laura Drinkwater
BRAND MANAGER
Chelsea Daniel chelsea.daniel@primecreative.com.au p: +61 425 699 878
CLIENT SUCCESS MANAGER
Justine Nardone justine.nardone@primecreative.com.au
HEAD OFFICE
Prime Creative Pty Ltd
379 Docklands Drive Docklands VIC 3008 Australia P: +61 3 9690 8766 enquiries@primecreative.com.au www.wastemanagementreview.com.au
SUBSCRIPTIONS
+61 3 9690 8766 subscriptions@primecreative.com.au
Waste Management Review is available by subscription from the publisher. e rights of refusal are reserved by the publisher
ARTICLES
All articles submitted for publication become the property of the publisher. e Editor reserves the right to adjust any article to conform with the magazine format.
COVER
Cover image: Living Earth Australia
COPYRIGHT
Waste Management Review is owned by Prime Creative Media and published by John Murphy.
All material in Waste Management Review is copyright and no part may be reproduced or copied in any form or by any means (graphic, electronic or mechanical including information and retrieval systems) without written permission of the publisher. e Editor welcomes contributions but reserves the right to accept or reject any material. While every e ort has been made to ensure the accuracy of information, Prime Creative Media will not accept responsibility for errors or omissions or for any consequences arising from reliance on information published. e opinions expressed in Waste Management Review are not necessarily the opinions of, or endorsed by the publisher unless otherwise stated.
With its multi-rotor design the Genox J-series pipe shredder easily shreds HDPE pipes of all sizes.
When combined with a Genox washing plant and Genox pelletising system, you can truly close the loop on HDPE pipes. Pipe to pellets. Pellets to pipe. This is the circular economy in action.
Genox make world-class recycling solutions, for real-world recycling applications.
Living Earth has been rejuvenating soils for future generations across New Zealand for 30 years. A team in South Australia is now bringing the company’s compost and soil enhancers to Australian markets.
To date, Living Earth has composted enough green waste to build a garden the width of a road from New Zealand to Australia.
While the gurative green road, made from more than two million tonnes of organic waste, is paving the way for better soil outcomes in New Zealand, it’s also having tangible results across the ditch.
Living Earth Australia was launched 12 months ago, harnessing the processes, expertise, and products of the New Zealand organics industry.
A subsidiary of the Integrated Waste Services (IWS) Group, Living Earth Australia will bring a range of composts and mulches to the agricultural, landscape and retail industries.
Grace Barila, Environmental Manager, says Living Earth
Australia is an opportunity for IWS Group to consolidate its organics recycling processes.
“We’re con dent we can go out to market in a larger way,” Grace says.
“We’ve been processing organics for several years for councils and wanted to improve those systems. We know we can provide good quality products to help rejuvenate our soils.”
Each year, organic waste in land ll generates about 13 million tonnes of greenhouse gas emissions. e National Waste Plan has set an ambitious target to halve organic waste sent to land lls by 2030 and commits states and territories
to roll out Food Organic Garden Organic (FOGO) collection services. e aim is to convert organic waste into recycled organic products such as compost. rough organics recycling and the return of compost back to soils, greenhouse gas emissions can be reduced. But there are also additional bene ts, such as improved soil health and biodiversity, increased agricultural productivity, enhanced food security, and water quality.
Grace says this is particularly important in South Australia where the local agricultural industry is struggling to work with depleted soils.
IWS Group, supported by environmental management company Ennovo, processes about 50,000 tonnes
annually of FOGO from local councils, producing a range of compost, mulch, and soil enhancements. e products have recently been AS4454 certi ed. Additionally, the South Australian site meets quality assurance and quality control standards set by Living Earth New Zealand.
Grace says an onsite laboratory provides real-time data to ensure products continue to meet strict standards. e site also has a native nursery where compost products are batch tested alongside the grow-out of native plants for large-scale revegetation works.
Living Earth focuses on creating compost that is used as the foundational ingredient in all its mixes, helping to promote long-term soil health.
“Our ultimate aim is rejuvenating soils for future generations,” Grace says. “Our ethos is all about sustainable development and reducing waste.
“Laboratory testing provides evidence that our products are working well according to nutrient level, moisture content and particle size grading. But at ground level, we have farmers who are noticing the di erence in their crop when using our compost.
“Farmers love our products.”
Grace says there has been a marked increase in the amount of FOGO that needs to be processed. Living Earth
Australia has restructured its facility to cater for larger volumes of waste and produce more varied products.
However, contamination continues to be a challenge. While South Australia has led the way in introducing plastic bans, Grace says there’s still confusion about what is compostable and what isn’t. Plastic bags, garden equipment and pots, among other things, continue to be found in FOGO bins.
To that end, Living Earth Australia has invested heavily in machinery to help remove contamination, purchasing an EDGE TRT622 trommel screen and an EDGE TRM831 mobile trommel screen – the rst in Australia – from industrial equipment supplier FOCUS Enviro.
“ e TRM831 is the largest wheel mounted on the market globally. It’s sheer scale provides operators with unrivalled production rates, ideal for operators seeking to boost their production capabilities,” says FOCUS Enviro’s Ryan McParland.
“High-capacity processing equipment, such as the TRM831 will play an important role helping Living Earth Australia meet its plans for expansion.”
He says the EDGE TRM831 portable trommel not only guarantees huge production rates but o ers reliability with minimum upkeep.
“Trommel screens from EDGE Innovate are simple to operate and are designed to require minimal maintenance. Customers know they will start up and consistently process large volumes of material day after day without any of the major upkeep you would associate with other products such as star screens. at’s the biggest selling feature of a machine like this.”
e EDGE trommels supplied by FOCUS Enviro are designed for easy operation. ey are loaded with smart features such as an intelligent load management system that ensures the unit is running at optimum capacity at all times while minimising the risk of blockages occurring.
“All the operator needs to do is to keep loading in the feedstock,” Ryan says.
Full remote functionality over all major functions such a feeder speed and screening angle comes as standard,
allowing the loader operator to stay in complete control from a safe distance, while a 180 degree remote-controlled radial nes conveyor reduces the need to constantly move screened material.
“To further reduce the changes of bridging or drum overload, EDGE Innovate has complemented its intelligent load management system with a larger designed hopper opening and supplied industry-leading belt widths to allow a smooth ow of material through the trommel,” Ryan says.
FOCUS Enviro has established itself as a premier supplier of organic and waste processing solutions, not only in Australia but also in New Zealand. Many leading waste management companies trust the company’s expertise and industry-leading products to enhance their operations.
“Our service goes beyond simply providing equipment,” says Ryan. “We fully invest ourselves in our clients’ businesses, ensuring the solutions we deliver meet their speci c needs.”
In the project with Living Earth Australia, FOCUS Enviro’s engineers thoroughly analysed their feedstocks, making precise adjustments to parameters like drum speed, screening angle, feed rate, and the aggressiveness of the drum lifters. ey also selected the appropriate screen media to ensure the nished product met stringent quality standards – all before the nal handover was completed.
e TRT622 tracked trommel screen, the largest track mounted trommel available in Australia, has proven pedigree among organic waste processors. Its heavy-duty construction design and high manoeuvrability have made it a popular choice.
With a 6.9-metre-long screen drum, it provides advanced screening options and is driven by a direct four-wheel drive system with a variable drum speed of 0-30 revolutions per minute.
Again, Ryan points to its enhanced features such as hydraulic load sensing
and automatic sequential start-up that ensures ease of use and minimal supervision as to why the TRT622 has been so positively received.
“Its customisation has lent itself to being able to ourish in many applications. anks to a wide range of various aperture meshes, drum styles such as punch plate, woven mesh or fully welded punch plate drums with scrolls, all of course interchangeable; has allowed the EDGE TRT622 to excel not only here in Australia but also in North America.”
One of the unique features of the EDGE TRT622 trommel screen is the radial remote-controlled nes conveyor that can place more than 1000 cubic metres of material in a single stockpile – almost 10 times that of traditional trommels.
Paul Bowden, Asset and Carbon Development Manager for Ennovo, says reliable operation for a long time, with consistency, is a critical step in Living Earth Australia’s production process. Machinery that is extremely well built for durability and minimal downtime were key requirements.
Equally as important was after-sales support from a supplier with good
stock on parts and who would support the servicing regimes and preventative maintenance standards.
“FOCUS Enviro had great communication throughout the procurement process and delivered the machine and critical parts on time,” Paul says. “ ey also spent time with our service team and operators throughout the commissioning of the plant and made sure training and operation were set up from the beginning.”
Grace says the new equipment and partnership with Living Earth is already bringing bene ts in the form of increased contracts with local councils.
Living Earth Australia products created from FOGO and green collections will be redirected back to the councils, closing the loop on organics. Bulk products will be delivered to farmers and stocked at IWS Group transfer stations and supply yards. As it continues to look at initiatives to support the community, Living Earth is introducing the Hulka Bag – a delivery service of its mulch and compost products in exible cubic-metre bags.
For more information, visit: www.focusenviro.com.au
Environmental management company Ennovo lives by the motto ‘your gas, your revenue’. Managing Director Dr Ben Dearman explains how waste management companies and local government are reaping the benefits.
here is inherent value within contaminated land and waste materials, says Dr Ben Dearman. e Managing Director of environmental management company Ennovo, Ben is helping land ll operators realise the resource they are sitting on.
He says unlocking land ll gas and generating carbon credits is both an economic and environmental win. A win that Ennovo aims to deliver.
Formed by the merger of DBD Environmental and Biogas Systems Australia in 2023, Ennovo combines the expertise of a range of environmental practitioners in waste management.
Land ll services, technical consulting and recycled organics, coupled with data management and reporting are among its key services.
Ben says a combination of contracting experience and technical consulting means the team can provide pragmatic solutions for clients and the environment, underpinned by a focus on technology.
When it comes to land ll management, technology is being used to better manage two key environmental aspects – land ll gas and leachate.
“If you can measure you can manage, and the way we measure has vastly improved with the use of technology,” Ben says.
“ e computing power of the telemetry systems has increased, the amount of data that can be transmitted has increased and the ease of use of that data allows constant observation.
“We use real time data generated from land ll gas ares, land ll gas
monitoring data and leachate telemetry systems to make sure everything is operating at its optimum. Operators know of any shutdowns in real time or if infrastructure has incurred any damage.”
As waste breaks down it releases methane, a greenhouse gas 28 times more potent than carbon dioxide when it comes to climate change. at same gas can be captured to expedite the transition to renewables and reduce the need for electricity produced by fossil fuels.
Capturing land ll gas and combusting it in a are or engine also generates carbon credits. Each carbon credit represents the avoidance or removal of one metric tonne of greenhouse gas emissions from the atmosphere and can be sold.
Failure to deliver appropriate leachate management, the liquid pollution that seeps through a land ll’s waste pile, can also impact gas collection and control.
Ennovo o ers a full cradle to grave solution incorporating design, construction, operation, and management of gas collection systems. It also manages the carbon credit process on behalf of its clients.
Ben says clients reach out to Ennovo because of regulatory compliance concerns or because they want to realise the revenue available from their resource.
e team will undertake a gas modelling assessment before starting a pilot trial to evaluate the rate and quality of gas.
Based on the pilot trial, the team will design a system to achieve the results sought by the client.
e team has worked on some of the biggest land lls in Australia, as well as some of the oldest, and is
currently present on more than 25 sites nationwide.
Among the projects that stand out is Garden Island, a closed land ll on a 52-hectare site in South Australia that was experiencing lateral migration of gas.
Ennovo designed and constructed a gas collection system, connected to a low calori c are, that enabled the gas to be captured. e system improved the gas collection e ciency of the site bringing it into compliance for surface gas emissions and enabling carbon credit revenue.
Ennovo continues to undertake monthly monitoring and maintenance of the entire system while managing the land ll site.
Another project required investigating possible causes of lower-than-expected land ll gas extraction and how to remedy it. is led to a three-fold increase in gas extraction, and therefore a related three-fold increase in carbon
credit generation. Staged works included reviews of data and associated information, followed by a review of design documentation and previously conducted assessments.
Following these reviews, an on-site inspection was carried out to identify potentially damaged wells, owlines, and lateral lines. Some short-term changes were also made to the gas eld balancing settings.
“For operators already with gas collection systems we can optimise, improve and make sure they’re running as best they possible can,” Ben says.
“Land lls naturally subside, which can have an impact on gas collection infrastructure, and are a relatively harsh environment which required regular monitoring.
“Regulatory compliance must also be met for both land ll gas and leachate.”
Ben says it’s important gas collection systems operate e ectively for the bene t of human and environmental health.
If land ll gas is not well managed it can have compounding e ects such as generating explosions, lateral migration that can kill o surrounding vegetation, not to mention the potency of greenhouse gas itself.
Managing legacy land lls is vital, more so than operational land lls, because there’s more likely to have been a natural urban egress over time, putting neighbourhoods in proximity.
“ ere are potentially relatively high losses of land ll gas. If we can improve the capture of that gas, we not only help improve a client’s revenue stream but mitigate environmental impacts,” Ben says.
“ e team at Ennovo get a lot of satisfaction, knowing we are making a di erence.”
For more information, visit: www.ennovo.com.au
At STG, our primary goal is to provide innovative and dependable products, and our waste truck fleet is no exception. Our state-of-the-art waste trucks feature a patent-pending modular design that excels in efficiency without compromising load capacity.
Advanced technology that enhances performance and efficiency, with a single-screen interface and in-cab controls for easy operation.
Designed for minimal downtime, with accessible components and expert support from STG.
Carry more waste with fewer trips, enhancing your operational efficiency.
Tailor your waste truck with our versatile modules to meet specific requirements.
Reliable and comprehensive support to keep your trucks running smoothly, with dedicated service teams and readily available spare parts. Our remote dial-in feature allows STG engineers to diagnose and resolve issues remotely, minimizing downtime.
Resource Hub boasts an impressive resume delivering training sessions for waste management facilities across Australia. Founder and Director Lacey Webb, and Lead of the compliance, data and training teams, Chloe Rhoades, explain why investing in people is essential for the future of the sector.
There’s a lot of talk in the waste industry about education. Often the focus is the piece of paper at the end of university, but that’s not the only education the industry needs to worry about, says Lacey Webb, Founder and Director of Resource Hub.
Community education is critical, however discussion around community education and behaviour change often doesn’t focus on the people delivering the day-to-day work.
“ ere can be a disconnect between the important strategies of a region or facility and the actual operational knowledge of the people at the facility,” adds Chloe Rhoades the Compliance and Data Lead in charge of the teams delivering Resource Hub’s training.
“ ey are the frontline person you will meet at a weighbridge or gatehouse, they’re often the only people the community will interact with,” she says.
“It’s critical they have the right skills to give the customer a great experience, so they recognise the value the waste industry provides, while also being able to capture great data and compliant outcomes.”
Resource Hub is passionate about helping others navigate the complexity of the waste and resource recovery sector and conducts regular training sessions across every state, aimed at improving facility operations.
Lacey describes it as de ning what best practice looks like for gatehouses, covering everything from waste levies,
the challenges of a transaction system and customer experience, through to the more technical aspects such as how to classify loads, and how to maintain compliance of regulated waste movements. Even how to improve site communications to improve outcomes.
While there is a standard suite of training subjects available, sessions are commonly tailored to each region, state, and customer need. e Resource Hub team will often speak with clients or deliver site audits to identify key challenges and develop their training program to improve outcomes and bottom lines.
e team delivers training sessions to large councils and commercial organisations, smaller rural councils,
regional organisations of councils or regional organisations and even state regulators. When it comes to the land ll and transfer station operators, Lacey says 90 per cent of organisations who take part in training sessions will sign up for annual refreshers.
Isaac Regional Council in Queensland was one of Resource Hub’s rst training clients and one of the growing number of councils Lacey knows who invest in dedicated annual gatehouse and operational team training.
She says, ve years on, the council can benchmark the growth and success of its waste operation because of investment in its people.
“Five years ago, when we asked the council sta what best practice looked like, there were ‘ums’ and ‘ahs’ and talk about things they wish the sites did,” Lacey says.
“ is year, year ve, we went back to that topic. e teams on all training days talked about the great processes they have, the ideas they’ve brought to fruition, the learning and the level of energy around sites . . . and their best practice. It was a total shift from ve years ago, when best practice was perceived to be something that other council facilities delivered, where now they identify themselves as representing the goal!
“It goes to show what investing in sta can achieve. You can see the value you bring to someone when they feel like they’ve been invested in.”
As much as it is an investment in people, training sessions are also an opportunity to nd the gaps in a business and set a new policy or process that is t for purpose.
Councils regularly reach out seeking help to understand how regulation changes can be integrated into their operations. Resource Hub is also in touch with regulators and waste authorities to determine the risk areas where training could help.
“We’re making sure appropriate, t-for-purpose process are embedded using simple language that teams can understand,” Chloe says.
“As regulation changes, we sometimes forget that we may need to change a process at a gatehouse. We’re adapting and developing sessions according to gaps we’re seeing in industry knowledge.”
Resource Hub has been built on an ethos of bringing people and process together to make organisations more e ective. Training is a critical part of its service o ering and within the next six to 12 months the team is investing time and money to expand the opportunities for training.
“It’s all about resourcing up with Resource Hub,” Lacey says. “It’s all about being part of our clients’ team and supporting the team’s growth… while we sit in the background.”
New services will include “lunch and learns” – one-hour sessions every six weeks on a speci c topic. e free sessions are intended for waste
management co-ordinators who are new to a region or role, to give them the basics around a particular topic. ey will be state-based to continue to upskill the industry.
A second new service on its way includes a suite of online and digital training for organisations to use for sta onboarding as well as “refreshers”. It will incorporate speci c video content, competency checklists and a skills matrixes – as well as some fun interactive tools – to determine a team’s understanding of the content.
Lacey says it will make training more accessible for regional and remote councils while also making it more focused on shorter units.
It’s these outcomes that continue to drive Lacey, Chloe and Resource Hub. If the team could teach everyone in the waste industry just one thing, it would be a renewed focus on outcomes.
“It’s about asking why we do what we do,” Lacey says. “Why we press the buttons, record this information and take certain loads.
“Why is often is the piece of the puzzle that’s missing when we nd policies or procedures aren’t being adhered to.
“It is the most common question that we get asked in training workshops and it’s the ultimate question for solving a multitude of process problems and getting our teams to engage in changed outcomes!”
For more information, visit: www.resourcehub.com.au
Daily cover technology set to revolutionise landfill management is being introduced to Australia and New Zealand. Wastech Engineering’s Tim Williams lifts the lid on the company’s new offering.
Australia’s largest land ll will be the rst in the country to deploy the ground-breaking Atmos alternative daily cover system.
Wastech Engineering, the exclusive Australian and New Zealand distributor of the Atmos Daily & Intermediate Cover System, is set to install the rst system in Victoria.
Tim Williams, Wastech Head of Operations, describes it as a game changer for the industry.
“Operational and asset utilisation challenges of land ll operators are both addressed with this one system,” he says.
“ e Atmos Daily & Intermediate Cover System lowers operating costs, improves e ciency, preserves valuable airspace, and protects employees at the land ll.”
e Atmos cover material is a nonhardening, protein-based foam that can be adjusted to last from overnight to multiple days by changing the dilution ratio and the depth of coverage. It’s applied using a custom-designed, single-person-operated Morooka tracked vehicle and a touch-panel storage and dilution centre. e Morooka has the capacity to cover a large working
(tip) face with a single ll in less than an hour.
Tim says the system produces a thick, long-lasting foam barrier for immediate suppression of dust, odours, and volatile organic compounds (VOC), eliminating the need to cover the operating face with cover material at the end of operations.
Land ll licence requirements generally require operators to cover waste daily to reduce the potential for o site impact. Tim says the traditional method of using soil for daily cover comes with its challenges: it takes up valuable airspace (a land ll’s most valuable commodity), as operators can never fully remove all the soil due to the uneven nature of the placed waste and the soil e ectively becoming mixed with the waste.
e Atmos protein-based foam is engineered to do the same job as soil-based products, but because it’s a foam, it doesn’t need to be removed the next day. It can withstand harsh weather conditions, including extreme temperatures, wind, moderate rainfall, and snow.
It can be applied by one person, eliminating the need for multiple units of plant and equipment such as loaders, dump trucks, and bulldozers.
“It provides an immediate nancial bene t to the land ll,” Tim says.
“If a land ll is purchasing soil or using tarps to cover, we believe the Atmos Daily & Intermediate Cover System can reduce running costs on a like-for-like basis. Airspace savings are estimated to be about 20 per cent, which over the life of a land ll is a signi cant cost
saving as well as life extension. Reduced operation, maintenance and labour costs, the speed of application, and no loss of air space are all advantages of the system. But it’s also environmentally friendly; you’ve got one machine driving around the land ll once a day instead of multiple machines, twice a day.”
e Atmos Daily & Intermediate Cover System was developed in the United States and is widely used overseas. Tim says there has been strong interest in Australia, and he expects that to increase once the rst system is installed this year.
e cover system contains no per- and poly uoroalkyl substances (PFAS) or per uorooctane sulfonic (PFOS) and has Victorian Environment Protection Authority approval for use at Australia’s largest land ll.
Foam concentrate, application equipment, bulk storage (a three-metre container), and a mixing centre form
the complete system. Wastech also provides operator training and a full preventative maintenance program as part of the o er.
e system can be scaled up or down as required, and Wastech can provide a six-week turnaround for Australian installations.
Tim, who will oversee Australia’s rst installation, is keen to get on with the job.
“ e impact this one system could make on the environment and operators is potentially huge,” he says. “It’s a great thing to be involved in, and I’m keen to see the rst system operating.
“It will de nitely ll a gap in the market and potentially replace expensive cover systems now in use.”
Wastech Engineering is a well-established player in the waste management and resource recovery sectors, known for its design, engineering, and manufacturing services. It supports
a diverse range of businesses and governments that want technologyenabled solutions to manage waste and resources e ectively and e ciently, whether that be crushers, re suppression systems, transfer stations, or de-packaging systems.
Tim says the company ethos is to treat waste in the best way for the environment. He sees the partnership with Atmos as a perfect t.
“We’re very supportive of sustainable and eco-friendly solutions, and there are some innovative ideas for recycling, land lls, and resource recovery when it comes to technology,” he says.
“ e Atmos Daily & Intermediate Cover System is a great product to introduce into the Australian market and our customers.
“It could be a game changer for the land ll industry.”
For more information, visit: www.wastech.com.au.
Hanson is pioneering new technology and concepts at its Wollert landfill. We find out what it takes to be a landmark facility.
When Evan Kyriakopoulos tells people what he does for a living, the general response from anyone outside of the industry is “Oh you’re a garbo”.
And in its most basic de nition, that is Evan’s job description. But it’s more complex than people imagine. A lot of science and engineering goes into building, managing, and operating a modern land ll. Particularly one that is among Australia’s most unique.
A quali ed environmental scientist, Evan is Operations Manager for Wollert Land ll in Melbourne’s north. It is one of few, if not the only land ll in Australia, that operates a free draining leachate system. It was also the rst in Australia to power a data centre o land ll gas and the rst to complete a phytocapping study.
“It’s a far cry from what people think is a traditional land ll,” Evan says.
“Land lls have had a bad name and reputation – even today when images of land lls are shown, they are from ird World countries where piles of uncompacted waste are shown. But land lls are a far more controlled environment and are well managed and well-planned facilities.
“I see them as a necessary piece of the puzzle for future waste management.”
Wollert Land ll, operated by Hanson, is an example of how land ll
can play a positive role. Leachate management systems in Australia routinely operate with collection sumps, but not Wollert. It has a free draining system where gravity drains the cells to designated collection points outside of the land ll. Leachate is then treated at an onsite plant and discharged to sewer.
Evan says it’s more e cient and cheaper than having pumps installed within land ll cells or carting leachate o site in trucks. It also helps to maintain environmental compliance. Land lls across Victoria are required to maintain leachate levels to 300 millimetres above the lowest point of the cell – free draining means leachate is constantly extracted.
ere are two treatment ponds, and two discharge ponds at Wollert, treating about 30 megalitres each year. Hanson plans to expand leachate treatment capacity as part of its overall site development.
“We have about 100 years of life left in the land ll,” Evan says.
“As it develops there will be increased volumes of leachate. We’ve planned to have the capacity to treat that future growth.”
It’s also planning ahead when it comes to renewables, with land ll gas extraction systems installed across the site. Evan says this also di ers from other land lls, in that permanent
gas extraction systems are installed early while building land ll cells. It means that when the cells reach a certain level, the permanent system just needs to be switched on.
ere are more than 400 gas wells across the existing 15 cells, collecting gas that powers eight engines producing 8.8 megawatt hours of electricity.
ere is also behind the meter activity powering a data centre on-site.
Evan says that with partners LMS Energy, Hanson hopes to expand opportunities for power generation for behind the meter activities.
Land ll gas management is one of the biggest areas of change he has witnessed in his more than 23 years in the industry.
“Originally land ll gas extraction was seen as an ancillary activity to assist with managing compliance and odour. Now it’s seen as a resource,” he says.
“ ere’s a lot of advancements with land ll gas being made nationally and internationally, such as, making synthetic natural gas to put into town gas systems and hydrogen production, thermal batteries and other behind the meter activities. A lot of things that would never have been looked at in the past are now being considered.”
Site capping at land lls is another area that has evolved over time, and one that has been embraced at Wollert.
Capping involves placing a cover over land ll waste to isolate and keep it in place. Wollert was permitted in the late 1990s for a clay cap – a layer of topsoil that was then grassed. With technology and legislation, capping systems progressed to include synthetic materials such as plastic membranes and liners.
Hanson has since pioneered phytocaps in Australia, using the soils from the local region, and scalps from the quarry with which the land ll shares the site. Native trees, grasses and shrubs are then planted in the cap.
e phytocap is designed to emulate what a synthetic capping system would do – prevent water ingress to land ll, to minimise leachate generation and control fugitive gas emissions.
It took a ve-year study to have the caps approved by the Victorian
Environment Protection Authority. is was later followed up by the Australian Alternative Cover Assessment Program (A-ACAP), to which the Wollert Land ll also contributed to.
e capping system has essentially become a haven for native animals, many of which have lost their natural habitat due to urban encroachment. Kangaroos, wedge-tailed eagles, hawks, echidnas, and blue-tongue lizards call the Wollert site home. e rst goanna in decades has also recently been spotted on site.
Evan describes it as an island refuge. Building on that is just one area Hanson is planning for the site’s future.
Hanson is dedicating more than 20 hectares to the Wollert Resource Park, creating a circular economy within the site. Locating the Resource Park on the same site as the land ll
will take advantage of the existing waste streams. It will divert recyclable materials such as organics, metals, and soils from land lls while creating products that provide increased circularity for the construction materials business.
“Land lls are the most robust of the all the waste management technology – they can take a broad range of wastes at signi cant volumes,” Evan says.
“ ere is always going to be a residual that needs to be managed, for those residuals that can’t be reused or recycled, you need a land ll.
“People who say land ll needs to be abolished, I think they’re being a bit utopian.”
For more information, visit: www.hansonland ll.com.au
An Australian patented invention has got some of landfill management’s most challenging aspects covered.
If Anni Colbran had her way, Land ll Lids would be installed at every land ll site she oversees.
e Waste Manager for Proterra Group, which manages 13 waste facilities throughout regional Queensland, says the patented lids are saving regional councils up to 33 per cent in cover material costs, land ll space and manpower.
“We love them,” Anni says. “ ey’re so quick and easy. We’ve got one land ll site that has been using Land ll Lids for only weeks, and they can see the bene ts already.”
Land ll Lids are an Australian patented invention by Grant Lacey, who has 30 years of land ll and waste experience in the local government and private sectors across Australia and internationally.
He invented the lids to help improve operations and safety for waste facilities. Easy to use and robust, they are exactly what the name suggests – a lid (steel plate) that is placed over land ll cells daily as an alternative to virgin excavated natural material.
e lids have been tried and tested on more than 50 local sites and are in use across the United States and Europe.
Proterra Group rst purchased four Land ll Lids in 2017 for the Goondiwindi Waste Facility. It has now installed them at its Longreach, Charleville and Inglewood facilities and o ers them as an addition to every Proterra contract.
Anni says the advantages of deploying the lids are multifaceted.
One of the biggest issues at any land ll is cover material. Every licensed
land ll in Australia has a requirement for a daily cover. In most instances that is virgin excavated natural material/ soil, which can be both time consuming and costly.
For land lls that buy cover material, it’s not cheap and there are rules and regulations about where it can be sourced and what it contains. Once on the cell, the material must be removed each day; some is lost in the waste pile or contains waste from the previous day.
“But the big thing for us was trying to conserve as much airspace as possible,” Anni says.
“ e saving of land ll space and cover material, particularly in rural areas, is so important. Instead of losing our air space to dirt every day, we cover the rubbish daily with Land ll Lids.”
e second biggest thing is windblown rubbish, especially at rural land lls. Anything that can help alleviate waste escaping from the site is of bene t.
“ ere’s no egress of cover material and the lids keep vermin out. It’s all the things that make managing a land ll site easier,” Anni says.
Land ll Lids are moved to the tip face within minutes using a compactor or loader. Because they don’t have hydraulics or motors that can break down during deployment, no backup stockpiles are required.
ey can be deployed during all weather conditions, can be used day or night and are available in various con gurations to suit the speci c needs of di erent sites.
With the escalating occurrence of res at land lls due to incorrect disposal
of batteries, the lids are adding another layer of safety. e steel plates can be used to help smother and contain any are-ups.
Anni says Land ll Lids are particularly suited to rural land lls that receive mixed waste.
“ ey are very robust, and they don’t rip or tear. We’ve had one that has been run over by a compactor and it’s still good to go,” she says.
It’s not just Anni who is lauding the advantages of Land ll Lids. She says ease of use and time savings are a winning combination for land ll operators.
Grant provides onsite training for operators, so they’re equipped with the knowledge to use and repair the lids. Within hours the lids are operational.
“It’s that easy,” Anni says. “If you spoke to any of our land ll operators,
they all really like them. Some oldschool operators were hesitant, but they were soon won over because it frees them up to do so many other jobs on site.
“I will buy Land ll Lids for every site I manage if I get an opportunity.”
For more information, visit: www.land lllids.com
Tutt Bryant Equipment’s latest BOMAG range of landfill compactors are establishing themselves quickly with multiple orders in hand and interest for many more.
As one of the market leaders in compaction technology, BOMAG strives for optimum sustainability in the development and manufacturing of its refuse compactors. In Australia, it’s been represented by national dealer Tutt Bryant Equipment since 1986.
e latest delivery of the BOMAG Land ll Compactors is designed with additional features to help customers achieve the best results when managing land ll sites. Kempsey Shire Council in New South Wales is one of the rst to put the compactors to the test, recently upgrading with the new BOMAG BC773RB-5.
John Glossat, National Business Development Manager, Tutt Bryant says
there are many unique selling points of the BOMAG BC773RB-5.
However, one of the main features is its four-wheel design is tted with polygon rings and teeth that are used for optimal crushing and kneading performance. Additionally, the teeth are covered with a manufacturers standard of 10,000-hour warranty for Australia.
“All wheels are individually hydraulically driven, with individual hydraulic circuits managed by a four-pump system,” he says. “Adding power to its performance has proven itself repeatedly.
“Each wheel is being tted with scarpers and wire cutters front and rear to prevent wires or ropes from becoming
entangled. More often than not, mattresses and steel cables can become wrapped around the wheel, which can be a real nightmare to remove.”
Other features include the oscillating articulated joint, which John says allows the highest degree of oscillation and articulation from steering to both sides between the front and rear frame.
“Ground contact pressure is even across all tips, bearing the full weight of the machine touching in the most uneven ground situations,” he says. “I usually call it ‘bend it like Beckham’, because you can put the machine into working positions where others could not follow.”
BOMAG engineers focus on safety, functionality, practicality and performance output to deliver a full allround package, with an added touch of luxury for everyday work. A home away from home for the operator, as John describes it.
Having a land ll compactor tted with the newest smart cruise control allows operators to set the blade height and working speed for forward and reverse travel.
“Both of these features can be set with the click of one button, whereas previously you had to adjust both the speed setting and the blade height in order to move forward or backwards,” says John.
e compactor also comes standard with a built-in auto greasing system, eliminating the need for the operator to exit the machine and grease the joints.
Safety is a high priority for BOMAG, which is why an integral preventative system monitors the water and uid levels.
An audible sound and visual display will be activated when levels are low, automatically shutting the compactor o to prevent system damage.
John says the right land ll compactor is a must for Kempsey Shire Council.
“To extend the life of the land ll site the design is critical to achieve higher compaction outputs,” he says.
Jason Magill, Waste Manager for Kempsey Shire Council, says the BOMAG BC773RB-5 compactor was a standout choice.
“We felt it was a good price point and good value for money, it was also in stock and coming to Australia, which was very convenient,” he says.
“Our unit had also been tted with a GPS System which will enable us to locate exactly where densities have been compacted, how much compaction has occurred, whether more compaction is required or if we need to adjust the level in the cell.
“ is is a feature we haven’t had previously. It takes some of the guesswork out of land ll management.”
For more information, visit: www.tuttbryant.com.au
100+ Exhibitors from over 10 Countries 100+ Speakers Delivering over 50 Sessions Across 4 Stages Network with 3,000+ Peers Show Features Government Lounge | VWMA Breakfast Zero Waste Café | Networking Event
Don’t Miss Out Register Now 23-24 October 2024
Australian company Vortair’s patented technology is set to revolutionise waste recycling solutions and address the volumes of municipal solid waste being sent to landfill.
Australia is grappling with a growing waste crisis, marked by escalating waste generation, a shrinking number of land lls, and mounting environmental degradation.
Je Lang, Chief Executive O cer of Vortair, says decisive action is required to reduce waste volumes and enhance recovery rates. Failure to address the challenges will lead to consequences for Australia’s environmental and economic wellbeing.
Vortair technology can provide an on-site waste management solution that reduces the volume of waste as well as maximising value of recovery from waste streams.
Je hopes to introduce the technology to local councils to help meet environmental and business objectives.
According to estimates derived from the 2022 National Waste Report, prepared for the Department of Climate Change, Energy, the Environment and Water, about 75.8 million tonnes (Mt) of waste is generated annually. Of this, 14 Mt is attributed to municipal solid waste (MSW), which forms the cornerstone of council services.
Australian waste management trends reveal disparities in the recycling and recovery of di erent materials. In 2020-21, the largest waste categories were building and demolition materials (33 per cent), organics (19 per cent),
ash (16 per cent), and hazardous waste (10 per cent).
While metals and building materials had high recovery rates of 87 per cent and 81 per cent respectively, plastics lagged with only a 13 per cent recovery rate. Textiles had an even lower rate at ve per cent, excluding charitable donations.
Land lls are a major source of methane, a potent contributor to climate change. About 30 per cent of the nation’s methane emissions are produced by land lls. Additionally, organic waste in land ll generates 13 million tonnes of greenhouse gas emissions annually.
Groundwater contamination necessitates costly remediation e orts by local councils. e situation is exacerbated by the leakage of plastic waste into marine environments,threatening wildlife and ecosystems.
Je says addressing these issues is crucial for mitigating environmental harm and reducing Australia’s overall carbon footprint.
ere are 14 million tonnes of municipal solid waste generated a year in Australia. e average price per tonne to dispose of all kerbside waste for councils is estimated to be $235 per tonne.
“If we assume a similar cost of $235 per tonne to councils nationally, Australian councils will pay about $3.29 billion per year on collecting and processing municipal solid waste,” Je says.
“Councils are facing increasing pressures from state and federal governments and external stakeholders to be more environmentally sustainable. is combines with increasing populations, less availability of land ll sites and extra bureaucratic hurdles.
“Councils also need to navigate the ambitious targets of the National Waste Policy, additional levies and hence additional cost pressures.”
He says Australia’s resource recovery rate for municipal waste rose from 37 per cent in 2007 to 42 per cent in 2021, but still far short of the 80 per cent target set by the National Waste Policy. It’s a similar story for organic waste levels which remain high despite a national target of 50 per cent reduction of organic waste to land ll by 2030.
“ ese goals are far from being realised,” Je says. “ e current trajectory indicates that without the introduction of revolutionary technology and innovative solutions, these critical targets will be missed, leaving councils struggling to manage the growing waste crisis.”
Vortair o ers autogenous grinding systems to process waste materials
into value-add materials. Je says the turnkey systems can mill waste materials into a ne powder to reduce waste volume by up to 90 per cent.
e patented technology, designed and manufactured in Australia, uses air vortex frequency pulverising technology that releases stored kinetic energy within materials, enabling waste materials to be processed and re ned into dry powder or liquid paste.
e technology is applicable across multiple industries, milling materials such as plastic, glass and cardboard, thus reducing the volume of waste, minimising disposal costs and in many cases turning the waste into a saleable commodity.
Je says the technology is applicable for more than just waste processing
as it can also micronise various foods, metal powders for 3D printing, pharmaceuticals, minerals and agriculture biomass.
He says Vortair’s business model of minimising waste and maximising the recovery of value from waste streams, aligns closely with the environmental policies and business objectives of local councils.
Vortair is interested in discussing potential strategic partnerships with councils to implement Vortair technology. is would involve a work plan that includes exploration of capital expenditures (CAPEX), operational expenditures (OPEX), and revenue and pro t generation.
For more information, visit: www.vortair.com.au
An Australian-developed PFAS treatment technology is finding success in the United States. We find out how a $US10 million investment is helping the company expand its reach.
Brisbane-based e Water and Carbon Group has raised $US10 million in capital to accelerate the deployment of its patented perand poly uoroalkyl substances (PFAS) treatment technology globally.
e environmental engineering company has made inroads into the United States market in 2024, launching its rst operational xed plant at Bethlehem Land ll Company in Pennsylvania in July 2024.
Jim Hunter, e Water and Carbon Group’s Chief Executive O cer, says “the funds will enable the company to fast-track its USA expansion, focused on PFAS treatment in complex wastewaters.”
PFAS have been used in products such as re ghting foam, and everyday household and consumer products including food packaging, clothing, cookware and water-repellent fabrics. ese compounds are very resistant to natural degradation and will remain in the environment for long periods of time. As a result, they tend to bioaccumulate and pose serious health risks.
Land lls produce considerable volumes of heavily contaminated wastewater from rainfall and degrading waste. is wastewater, known as leachate, is extracted from land lls and can contain signi cant levels of PFAS.
e LEEF (Low Energy Evaporative
Fractionation) System is designed to intercept and remove PFAS from this leachate.
Dave Leinster, e Water and Carbon Group Technology and Partnership Manager, says “historical consumer waste such as carpet, non-stick cookware and products with protective coatings are major sources of PFAS in leachate.”
PFAS behave like surfactants and attract to bubble surfaces. e LEEF System takes advantage of this using a process called foam fractionation. By adding air in a controlled setting, the PFAS compounds will concentrate on the bubbles and rise to the top where they can be skimmed o and separated.
“ e LEEF system is very e ective at removing targeted PFAS compounds down to the limits of detection even in complex wastewaters such as land ll leachate,” Dave says.
PFAS has been getting international attention with increasing levels being detected in water sources across the globe. is includes PFAS detected in Sydney’s drinking water catchment in June 2024. e levels are within Australia’s drinking water guidelines (but above those of the USA). is has further raised awareness about the spread of contamination.
e Water and Carbon Group’s capital raise included $US8 million from global investment rm, Emerald Ventures and US-based Ecolab Inc, with additional investment from Australianowned Dragon y Enviro Capital and some existing shareholders.
Emerald Ventures, which led the round, is known for backing innovative water technology companies.
“ e Water and Carbon Group is bringing a critical solution to the global environmental challenge of PFAS contamination. e company’s success in Australia, and now the US, shows the scalable, global potential of the LEEF System,” Emerald Investment Director Julien Dillon said.
e LEEF System rst proved its e ectiveness in Australia, where it has been operational for nearly two years at the Shoal Bay Leachate Treatment Plant in Darwin, treating about 51 million litres of leachate annually.
e project showed the system’s ability to address PFAS in regions with signi cant rainfall.
e Water and Carbon Group’s Bethlehem Land ll project in the US is built on years of research and development and full-scale operational experience in Australia and is already making an impact. e system can treat 378,000 litres of leachate daily, reducing PFAS to non-detectable levels.
With the US Environmental Protection Agency (EPA) ramping up e orts to combat PFAS through initiatives such as the PFAS Strategic Roadmap and proposed enforceable limits for PFAS compounds in drinking water, the demand for e ective treatment solutions is higher than ever.
e Water and Carbon Group is poised to lead the charge in providing these solutions around the world.
Dave says the US market was always a key component of e Water and Carbon Group’s expansion plans because of its waste volume and number of land ll sites.
However, there is also huge potential for the technology within Australia, particularly for land ll operators who are discharging leachate to sewer or reinjecting it on site.
He says the leachate itself will vary in the type and concentration of PFAS.
e key to developing the solution is understanding what individual land ll operators are targeting to achieve.
“What assists the industry is having a risk-based approach to managing PFAS discharge limits,” he says. “It is challenging to develop solutions without a clear target to manage
the risks of exposure to humans and the environment.”
PFAS is not the only contaminant in leachate that the Water and Carbon Group is tackling. One of the main di culties in treating leachate is its complex chemistry – high salinity, organic carbon, non-biologically degradable compounds, suspended solids, and nitrogen compounds, particularly ammonia, are present.
e Water and Carbon Group can design and operate integrated solutions for clients where the LEEF System is combined with other treatment processes (such as biological or membranes) to address all the contaminants.
Dave says e Water and Carbon Group’s approach is to create leading environmental solutions to complex problems that deliver lasting, positive outcomes.
“We’d like to be recognised as the technology leaders in wastewater treatment where standard commodity approaches are not suitable for complex problems.”
For more information, visit: www.waterandcarbon.com.au
CDE unveils a new generation of filter press, engineered for sustainable water management.
CDE, a leader in the design and engineering of sand and aggregate wet processing solutions for the waste recycling and natural minerals processing sectors, has unveiled its new ProPress high-performance lter press, adding to its state-of-the-art water management and recycling systems.
Developed to meet the evolving needs of construction and demolition (C&D) waste recycling, the ProPress integrates the latest technological advancements to deliver operational e ciency and maximum water recovery.
CDE’s ProPress, which features patentpending technology, bene ts from a exible design and variable throughput that can be scaled to t the processing volume of any operation.
Unlike traditional lter presses, the system is dual feed, meaning sludge is fed from both sides of the ProPress for improved e ciency and faster cycle times.
Optimised sludge feed pressure also allows for faster dewatering to increase overall throughput. is is further supported by an overhead beam design that ensures reliability by reducing stress on the unit and improving its durability.
e ProPress features plates that are 25 per cent larger (2.5 metres x 2 metres) than conventional designs. Greater chamber volume and fewer plates overall provide maximum capacity on a smaller footprint and improved mechanical cycle times.
Safe and e cient maintenance is made possible by integrated plate-shaking technology which addresses lter cake build-up within chambers to help reduce the need for manual intervention.
An access walkway provides unobstructed means to carry out maintenance safely and e ciently, and ush mounted drip trays reduce material entrapment and lock in place to provide a secure maintenance platform for operators.
e smart design is supported by an innovative, multifunctional robot, which serves as the main workhorse for the ProPress, controlling plate opening, plate shaking, cloth washing, plate winch, and the maintenance platform. e CDE ProPress is available in a range of sizes to suit all markets and applications. Available globally, the ProPress is largely pre-assembled to expedite commissioning, allowing operators to get up and running quickly to help achieve a fast return on investment.
As Australia strives towards its recycling and circular economy targets, C&D waste processing facilities continue to be a large part of the investment landscape as more complex and contaminated materials are processed and where output products are bene ciated to high end uses.
Daniel Webber, CDE’s Australasia General Manager, says this typically drives the process plant solution towards wet processing, and that means in a metropolitan setting you need e ective wastewater management. Even for sites with the space and permits to operate ponds, the reasons to look at ltration technology are compelling.
Settling ponds can present operators with signi cant challenges. ey can be hard to maintain, costly, and can impact the e ciency of operations due to both the time needed to clean them, and the material that can often be lost to them. ere are also potential environmental risks in how the operation manages water usage, and in some cases water scarcity, given the volumes of water required for settling ponds.
“Tackling the most challenging of materials is our expertise,” Daniel says. “We’ve poured over 30 years of engineering excellence into the development of the ProPress. We’ve listened to and worked alongside our customers around the globe to design a water management solution that is adaptable to their needs, including considering the speci c requirements of our customers here in Australasia.
“ ose needs were clear: sustainable water management was key to minimise freshwater dependency and maximise water recycling, all while improving processing capacity, reducing operating costs, and minimising maintenance downtime.
“ e ProPress is our response to all of this, and it is already delivering for our customers. By the end of the year, the ProPress will be found on eight plants
across three regions, processing around 1000 tonne per hour of material.”
Daniel says the ProPress is CDE’s most signi cant product launch in recent years and encapsulates the company’s purpose: to create our best world, a ton at a time.
“It represents a constant push for improvement to make our equipment, our customers’ operations, and the sectors we operate in more e cient and less wasteful,” he says.
“We’re very pleased to nally bring this latest innovation to the wider market to help maximise the availability of our natural resources and reduce the industry’s waste burden.”
Once the ProPress is commissioned, every customer is introduced to the CDE CustomCare team which provides aftersales support to help achieve maximum performance from their equipment.
CDE’s new Australian headquarters facilitates responsive on-the-ground support and locally available parts with short lead times.
Based in Stapylton, near Brisbane and Gold Coast, the new site, complete with managed stores, is part of CDE’s commitment to customers in the region.
For more information, visit: www.cdegroup.com
It takes perseverance, drive, and creative ingenuity to find the right solutions for waste and recycling problems. Being able to put them into action also takes the right capital equipment.
Isuzu Australia’s Future of Trucking Report: e Way Forward con rms that a key concern for Australian eet managers and owner-operators is purchasing capital equipment that is well-suited to the industry application and provides ease of use and accessibility for employees. e report also indicates that alongside a strong level of adoption of data-driven safety technology and software, Australian businesses continue to show interest in systems that help support eet business operations and bolster safety outcomes for drivers. Commercial vehicle safety is a top priority for waste and recycling operators, with the increased likelihood that materials being transported are hazardous or require extra care in handling.
For eet managers focused on building a transport eet that can comfortably meet better safety outcomes and sustain high performance under a heavy workload, Isuzu F Series models have proven capability for a range of waste and recycling tasks. Supported with the best in hardware and componentry, Isuzu’s F Series range reliably delivers with a combination of sharp model appointments, industry-ready features, and Isuzu’s intelligent Advanced Driver Assistance Systems (ADAS).
Isuzu’s ADAS includes a network of active safety features linked through a Hitachi Stereo 3D Camera on the dashboard such as Advanced Emergency Braking, Forward Collision Warning, Lane Departure warning, and more. Depending on the truck model, other key safety features such as Electronic Stability Control, Anti-Lock Braking System and an Anti-Skid Regulator assist drivers to maintain optimal control of the vehicle.
THE THREE RS
Recycling, reusing, and resource recovery is an important ethos in sustainable waste management.
With these three ‘Rs’ top of mind, businesses such as Jumbo Skip Bins (based in Brisbane) have stepped up with solutions to tackle the burden of processing Queensland’s unwanted waste.
A particular challenge in Australia is the collection and processing of waste material generated by a booming construction industry.
According to the latest National Waste Report, building and demolition waste is one of the largest sources of recovered materials in the country. However, it’s also the largest source of waste. is is where Jumbo Skip Bins’ Director Rory Crundall sensed an opportunity back in 2016.
O ering residential and domestic skip bin hire but specialising in construction and demolition disposal in the commercial sector, Jumbo Skip Bins covers a service area of Brisbane to the Sunshine Coast.
Commercial skip bin hire makes up to 90 per cent of turnover; it also provides add-on services such as crane bins, forklift bins and the standard wheely bins for high-rise construction.
“Historically, we’ve found that most construction companies haven’t been interested in how much of their waste is being recycled, but that is changing,” Rory says.
“Even though it has taken more time and work to make it happen, I have always had an interest in environmental outcomes and have been willing to make the e ort to deal with waste, separate it and recycle it into di erent streams.”
Rory has made it the team’s mission to improve the way waste disposal is conducted in the local area.
“ e Queensland waste levy has incentivised companies to divert
as much as possible from land ll, especially common materials such as bricks, concrete and soil, so we are moving more and more into this space.”
Jumbo Skip Bins operates a eet of Isuzu trucks ranging from a medium-duty FSR 140-260 chain lift skip loader with Allison automatic transmission, through to heavier chain lift and hook lift trucks. Recent additions of several new Isuzu F Series trucks out tted with West-Trans body equipment are rounding out the service o ering.
e hook lifts in the eet will clock close to 6000 kilometres on the road per month and the skip trucks about 4000 kilometres.
In addition to working a full roster with Jumbo, trucks are often commandeered for double duty, collecting concrete waste for its sister company Moreton Bay Recycling, located near Jumbo’s home base in Narangba.
For Rory, providing a cleaner, greener service has come with challenges in cost and logistics, so eet procurement needed to be approached in a strategic way.
Fleet choice has a knock-on e ect to the business bottom line. Rory notes that he wanted business backed by a truck brand that could provide a product range that was capable of tackling a punishing roster – while staying out of the workshop.
e long-term goal is to present a united front to clients and ensure consistency in performance for the business with an all-Isuzu eet in future.
“I had intentions to grow into a large eet and did a lot of research, asking mechanics and other trucking companies which brand they preferred and the answer I got was Isuzu about 90 per cent of the time,” Rory says.
“I thought it’d be silly if I went any other way; you want to get o on the right foot from the beginning. As a business owner, I wanted that peace of mind and comfort, so Isuzu’s warranty and roadside assistance terms are a massive incentive.
“Brisbane Isuzu in Eagle Farm knew what we were after in the industry and what models were suitable. e type of suspension and engine variations from truck to truck, and they arrange for the bodies to be tted by West-Trans for us.”
With Jumbo Skip Bins and Moreton Bay Recycling sharing resources, Rory has essentially combined two well-matched businesses with a eet that can support both operations.
Once waste has been collected from a site, either a Jumbo truck or one of the Moreton Bay Recycling trucks will deliver it back to the facility, where it is processed into a quality product for use in future construction projects.
Rory says the versatility of the combined eet is leading to e cient service that can save the client money, while also saving him time and delivery costs.
“Our customers at Jumbo often need products that are produced from recycled concrete, so we’re able to ll it up at Moreton Bay facility, then drop it o with their Jumbo skip bin, which saves them the cost of an extra delivery,” he says.
“Our drivers can be trained on skip and tipper trucks as well, which gives us great crossover and means we’re frequently able to utilise our skip trucks to deliver material.
“ e new trucks are a pleasure to drive, and the features Isuzu are including add up to make a big di erence for our drivers.”
For more information, visit: www.isuzu.com.au
REMONDIS and PACCAR continue their respective journeys in sustainability, with the newest delivery of DAF CF340 trucks.
As a local and global leader in resource recovery, REMONDIS strives to protect the environment, prevent climate change and continue recycling raw materials to be recovered and returned to production cycles.
To continue its commitment to sustainability, REMONDIS regularly refreshes its truck eet of more than 560 heavy vehicles, recycling 95,000 bins in rotation at 25 processing facilities, across 40 locations nationally.
In a recent eet renewal program, REMONDIS – the German familyowned business by Rethmann Group – took delivery of a large order of DAF CF340 trucks from long-time supplier PACCAR (DAF).
David Soemali, DAF Brand Manager says; “With a long history of initiatives aimed at improving the environmental footprint of its trucks and operations, PACCAR’s continued investment in research and development and local
manufacturing ensures the best trucks are on the market for our customers.”
In the midst of an aggressive eet rejuvenation, Conor Flynn, Executive General Manager – Technical at REMONDIS, says the CF340 was a standout choice for more than one reason.
“We have an existing legacy DAF eet, but these CF340 trucks are the rst DAF trucks REMONDIS Australia has bought as new,” he says.
Conor says that in addition to comfort, safety, fuel e ciency and power, the CF range is a testament to a commitment to sustainability.
Sustainability is a core objective for REMONDIS, as stated in its 2023 Sustainability Report. e third consecutive report published by the waste management service provider had a strong focus on lowering the company’s carbon dioxide emissions in line with a new Corporate Sustainability Reporting Directive (CSRD) announced in January 2023.
e CSRD, legislated by the European Union (EU), requires all large companies operating in the EU to publish regular reports on their environmental and social impact activities.
Conor says PACCAR is supporting REMONDIS as it aggressively adopts alternative power trucks and avenues to reduce emissions.
Allison fully automatic transmissions are compatible with alternative fuels such as compressed natural gas (CNG), biogas and hydrogen, enabling eets to achieve reduced emissions when compared to internal combustion engines.
“Soon after REMONDIS introduced its rst Fuel Cell Electric Vehicle (FCEV) – the rst operational hydrogen fuel cell waste vehicle in Australia – we had a conversation with PACCAR to see what other technology is coming,” Conor says.
“Our parent company in Europe operates a large eet of FCEV’s so we feel as if we have credibility globally.
“We leveraged that experience and we mobilised a FCEV in 2023. We will continue to push to ensure that we get access to this technology as soon as reasonably possible.”
In addition to acknowledging the commercial reasons for adopting alternative fuel technology, Conor says REMONDIS also chooses to have the greenest engine technology currently available to the Australian market.
All PACCAR’s ADR 80/04 trucks meet Euro 6 emissions standards.
“In 2023, 80 per cent of our new eet was Euro 6 compliant, unfortunately there wasn’t full availability of Euro 6 at the time,” says Conor.
“ e new eet of CF340 trucks now ful lls that objective.”
In continued collaboration, REMONDIS recently mobilised its rst DAF CF 10-wheeler hook lift, also the rst 10-wheeler supported by PACCAR Australia.
Conor says there was much collaboration with DAF’s European arm to build the 10-wheeler on shore.
“ is was a huge engineering project which required very speci c approvals for operation in Australia. Which I think was managed quite well,” Conor says.
“We really wanted to deliver this in Australia, which means we will be the
rst ones operating it for PACCAR in Australia,” he says.
Conor says the REMONDIS team assesses multiple metrics before retiring well-used trucks, including kilometres travelled and hours worked. e company aims to have an average eet age of ve to 10 years.
He says REMONDIS has a history of purchasing DAF product for its European businesses. To maintain an alignment with the European business, local purchases are predominantly focused on trucks with European chassis.
However, many of the European competitors don’t run an Allison transmission, paving the way for DAF.
“ is DAF product is optimal for applications of front lift and nontowing hook lift trucks,” Conor says. “Further to that, from a European chassis perspective, on front lift application it had the best payload, putting the biggest amount of product in the body.”
Conor says CF340 has a simple suspension which is easy to repair and ideal for REMONDIS.
“ e rear end of the truck has locally sourced componentry, which is very simple,” he says. “ e work our trucks do on site can be quite punishing on suspension componentry.
“We believe the CF340 will stand the test of time and we assume that spare parts will be easily available when we do have to repair them.”
Conor says spare part accessibility was a huge deciding factor when choosing the CF340 with Allison transmission due to the di culty experienced post COVID.
“Post COVID, spare parts were di cult to acquire in Australia,” he says.
“We’ve focused on what would be assembled in Australia, with the potential availability of spare parts, to keep the asset running through its 10-year life. DAF fell into that category very well.”
For more information, visit: www.daf.com.au
Waste equipment manufacturer Garwood International has targeted its range of rear, side and front loaders toward kerbside and municipal waste collection.
Since its establishment more than 40 years ago, Garwood International has continued to design and manufacture elite refuse compactors, expanding and adapting to the industry, particularly the move towards sustainability.
e Garwood International product range is one of the largest of any waste equipment manufacturer in Australia and caters to large-scale commercial collections through to rural communities and everything in between.
It has been recognised for its excellence time and time again, nominated for the Premier’s New South Wales Export Awards six times and named the LGP (local government procurement) Approved Contractor of the Year in 2020 – beating out 900 registered businesses for the award.
Garwood was also presented with an innovation award from the Australasian Waste and Recycling Expo (AWRE)
following the success of its Miner rear loader unit.
e award-winning Garwood Miner known as the “world’s smallest rear load truck” is the smallest rear load compactor body available in Australia, and is used for residential and commercial waste and recycling collections from laneways and basement car parks as low as 2.1 metres.
It has a maximum cab plus body height of only 2080 millimetres, catering for a range of bin capacities, from 120 litres up to 1100 litres, while also having a fast compaction cycle.
Kerbside segregation has become an important aspect to garbage collection, which is why Garwood developed its DualPact unit.
e DualPact rear-loader unit features two chambers, allowing for the simultaneous collection of two di erent waste streams. Available in 50/50, 60/40 or 70/30 capacity splits, it provides operators with a range of bene ts, including reduced operating costs and time required for a collection by o ering one solution for waste which would usually require two separate trucks.
e Bantam series full width rear loading refuse compactor body is available in four, ve or six cubic metre body sizes and is suitable for councils and contractors, parks and gardens and street litter clean-ups, while the compact eight cubic metre body is suitable for collection runs in urban centres or public places. It is designed for payloads of three to four tonnes
(dependent on cab chassis and options).
e Powapact comes with body sizes from 10 to 16 cubic metres and payloads from four to six tonnes (dependent on cab chassis and options). Its powerful compaction force is suitable for larger volume general and commercial waste runs.
For biggest runs, the Maxipact comes into its own – capable of payloads of up to 10 tonnes. Maxipact body sizes range from 16 to 28 cubic metres and are best suited to 6x4 chassis con gurations.
Common applications for the large Maxipact include hard waste collections and commercial waste runs.
Garwood side loaders take on all the needs of waste collection that rear loaders cannot. Both compactors are designed for domestic waste collection where space is minimal, and hazards are in abundance. Side-loaders reduce the possibility of near misses, where operators could encounter any number of hazards including pedestrians, cyclists, push bikes, and parked cars.
e LitterPact is suited to smaller spaces such as parks and gardens, or smaller communities including remote or regional areas. e light body means it can access all roads a conventional 4WD can.
Rounding out the range, Garwood’s Razorbak Front Loader, built in multiple sizes from 28 to 34 cubic metres, can t on all 6x4 or 8x4 cab chassis and is suitable for single person operation on commercial collections.
For more information, visit: www.garwoodinternational.com.au
Pure Environmental is a wholly Australian-owned company founded with the mission to transform the circular economy through advanced resource recovery. We believe in pushing boundaries and challenging norms in waste management, providing exceptional, innovative, and sustainable solutions. Scan Code
STG Global is cleaning up across Australia. We find out why the waste and recycling industry is developing a penchant for the front loader waste truck.
Providing customers with solutions is the most rewarding aspect of Shane Sinclair’s job.
e National Fleet Manager International Sales for STG Global grew up around the heavy truck industry. He’s built his career around “anything to do with trucks” – from selling them to xing them and recommending speci cations – and brings decades of experience to the role.
However, he says it’s the customers who use the equipment in the eld every day who have the greatest in-depth knowledge of the requirements and how products stack up.
It’s this recognition, and ability to pivot to meet client requests, that has put STG Global at the forefront of the waste and recycling industry.
“We don’t just sell trucks,” Shane says. “We customise for our clients to meet speci c needs and ensure we’re giving them operational value and driver-satisfaction.
“STG is big enough and has been around long enough to have the experience and great products, but it’s still a family business that can pivot and quickly re-engineer to meet customer needs.
“If it’s going to be good for the industry, we’ll bring in our engineers, draft it and build it. We’re providing solutions for our customers pinch points.”
Mitchell Farmer, Operations and Contract Manager at Tropical Waste Townsville can attest to STG Global’s adaptability.
Tropical Waste is a family business with more than 20 years’ experience o ering liquid and dry waste management services. e mum and dad operation has grown to a team of more than 20, and a eet of vehicles.
Mitchell says when it came time to buy a new truck, safety and operator functionality were foremost requirements. A remote function to help prevent occupational health and safety issues for truck drivers was a necessity.
“We need to lift multiple bins at one site, and we wanted to prevent the driver having to hop in and out of the truck as much as we could,” Mitchell says.
“A remote function wasn’t something that STG o ered but when we explained what we needed they came back with a cost-e ective option.
“Now all our bins can be lifted with a remote outside of the cab or when sitting inside the cab.”
Mitchell says the 33.5-cubic metre front lift compactor is operator-friendly and incorporates improved safety features including a function that prevents a bin from being tipped when the compactor doors are closed, or the hopper isn’t in place.
“Comparing new to old technology –this new truck is a lot more advanced,” he says.
“An operator Ipad provides a lot of functionality and a lot of instant information. You don’t realise how handy a diagram of a truck in operation is until you get in there and use it.”
He says just as impressive as the truck itself, is the lead time – from the original quote to truck delivery was just 12 weeks.
STG Global has factories in Perth, Melbourne, Sydney and Brisbane, and carries a large stock of critical spare parts.
“No matter where you are, there is support for the product,” Shane says. is presence streamlines processes and is one of the reasons the front loader is gaining traction across Australia.
It also doesn’t hurt that STG Global has built a reputation for building trucks that can navigate Australia’s versatile and sometimes tough conditions. e company mission is to deliver e ciency and expertise worldwide, ensuring every truck, part, and service serves a purpose.
Josh Hirst, Managing Director of Logistick in Western Australia, took delivery of an STG front loader about 10 months ago and is already looking to bring another three into the eet for his residential bulk waste business.
It might have been STG Global’s price and availability that got him over the line for his rst purchase, but the research and development and after sales service is why he’s a return customer.
“ e service has been amazing,” Josh says. “STG’s depot here in Western Australia is relatively new, but they have the right people in it with the right attitude. If it’s not right, they make it right. If it’s broken, they x it.
“We’ve not had any real downtime with the truck in 10 months, due in part to the support in general. at’s been very helpful and it’s a fantastic representation of their brand.”
Vince Barilla, Director of Operations for Victorian environmental services company Speedie Waste & Recycle, put out the call for trucks “straight away”.
In a strategic move facilitated by Shane, Speedie Waste has elevated its
waste management capabilities, trading in two of its old trucks for STG front loaders. A third is on the way.
Vince says the comprehensive training provided by the STG team ensures that Speedie Waste’s sta can pro ciently use their new truck, maximising its e ciency and e ectiveness.
“So far, it’s been good,” he says. “Everyone’s happy.”
Shane says the expansion of Speedie Waste’s eet is a testament to the company’s dedication to staying at the forefront of industry standards and embracing cutting-edge solutions.
Alex Soukie, General Manager of Purple Cow Industries in New South Wales, is not only embracing cutting-edge solutions, but a new enterprise.
e waste solutions company has been servicing the construction and demolition industry from its Sydney base with a eet of 32 trucks.
With a strategic move into the commercial and industrial waste space, Alex has purchased two STG front lift trucks. While the trucks are leadingedge, he says it was STG’s service that sealed the deal.
“We buy o people,” he says. “ e service provided by STG is second to none, then there’s the speed and e ciency that they can get a truck on the road.
“STG can deliver a truck in a fourto-eight-week turnaround compared to four to six months.”
Just weeks away from taking delivery of the two new trucks, Alex said he was eager to put them through their paces as Purple Cow diversi ed its revenue streams.
e commercial service will involve a eet of three to start with (including a truck already in the Purple Cow eet), with an eye to grow within the next 24 months.
For more information, visit: www.stgglobal.net
The journey of Australia’s favourite garbage truck.
IVECO’s popular ACCO model is a familiar sight on Australian roads, normally engaged in demanding refuse collection work, where its tough design and durable construction has meant that many older trucks are still in service.
e ACCO’s history is a long one with roots to 1961. Back then it was known as the ‘AACO’ (Australian A-line Cab Over), and was developed from the International Mark 3, a vehicle with military origins.
In 1966, a manufacturing line change from A to C line resulted in a change of nomenclature to ‘ACCO’, as the vehicle is still known by today.
In 1972 ACCO had its original cabin shape (known as the Butterbox) updated, along with many other major changes. is cabin design continued for more than 40 years, with more than 4000 revisions applied to the model over this time. e last iteration was in 2014. is familiarity of design had bene ts for bodybuilders and customers and there’s unlikely to be a body type that hasn’t been mounted on an ACCO cab chassis.
To meet increasingly stringent emission requirements, and to o er the latest in active and passive safety features for customers, changes were required to the ACCO that weren’t viable on the long serving platform. In a quest for the latest technology, IVECO looked to Europe, and particularly the X-Way product, as the basis for the next ACCO model.
e X-Way was developed in Europe for a mix of on and o -road applications and was an ideal t given the demanding applications in which the ACCO operated within Australia.
is new generation ACCO continued to be manufactured at IVECO’s Dandenong, Melbourne, facility and combined some of the best features of the previous generation trucks, that made it a favourite for tough vocational applications, while including the latest innovations from Europe such as Euro6 power.
For refuse collection work, the ACCO continued to be available with a
factory dual control system and IVECO consulted extensively with the waste industry to develop a variety of body mounting and chassis layout options. e model was also available with a Parker Chelsea PTO, a favourite for waste collection.
Other bene ts included Adaptive Cruise Control (ACC), Anti-lock Braking System (ABS), Electronic Braking System (EBS), Advanced Emergency Braking System (AEBS), Electronic Stability Program (ESP), axle load indicator, electronic battery cut-out and L.E.D daytime running lamps and rear L.E.D lights.
In 2023, the ACCO was again updated after aligning with IVECO’s multi-award-winning S-Way heavy duty range, bringing greater levels of driver comfort and interior appointments, added safety equipment and even more stringent ‘Step E’ Euro6 emission control.
Now fully imported from Europe following a long Australian testing and development period, the current ACCO is available in both 6x4 and 8x4 con gurations and features IVECO’s 8.7-litre Cursor 9 engine, with buyers able to select from three output ratings spanning from 310hp and 1300Nm to 360hp and 1650Nm. e standard transmission across all models is the proven Allison 3200 6-speed full automatic, a favourite for demanding stop and start applications.
Available exclusively with a day cab, the ACCO’s interior has been further re ned to provide more usable space and accommodate dual control hardware for those relevant models. Driver storage solutions have been ampli ed with additional areas allocated.
Previous generation ACCO models were a favourite for bodybuilders owing to their clean chassis rails and mounting options; this legacy has continued in the latest ACCO, with a chassis layout that’s been honed to closely align with requirements of waste industry bodies in consultation with popular body manufacturers and leading companies within the sector. New systems for improved integration between the cab chassis and bodies are also featured.
Other waste industry-speci c adjustments include redesigned steps for extra ground clearance, an engine hour metre and three-blade windscreen wiper system. e latest ACCO also boasts the advanced safety equipment featured in the S-Way including Advanced Emergency Braking System, Brake Assistance System, Adaptive Cruise Control, Lane Departure Warning System, Electronic Stability Program with ABS disc brakes all round and ASR (Anti-Slip Regulation) and full LED lighting.
To provide owners with lower total cost of ownership, ACCO features IVECO ‘EasyRoad’, which covers maintenance and repair costs for 12 months / 150,000 kilometres or 3000 engine hours, whichever comes rst. Additionally, ‘IVECO ON’ telematics is complementary on the latest ACCO models for ve years.
For more information, visit: www.iveco.com.au
Easy to use, tough and low maintenance. No mechanics!
Fire containment including lithium-ion battery fires. Australian owned and
Diversity brings more breadth and depth of ideas and experience. Veolia is determined that tomorrow’s waste industry will be the beneficiary of diversity.
Getting on with it, stepping up and diversifying are the best three avenues for the waste, recycling, and resource recovery sectors to add value to Australia, according to Richard Kirkman. e Managing Director for Veolia Environmental Services, Richard has an unwavering sense of purpose when it comes to ecological transformation. And he has big ideas to achieve success.
Veolia is setting the benchmark to develop a skilled workforce for tomorrow’s waste industry, with agship programs aimed at women, parents, First Nations People and Torres Strait Islanders. It’s also issuing an industry-wide call to arms to boost the employment pool.
“ e best business outcomes are achieved by having a diverse team. at’s been my experience,” Richard says.
“We are committed to providing a supportive and culturally safe environment and through that, supporting people from all walks of life and backgrounds and providing them opportunities to grow within our business.
“I feel we’re a safer, stronger, betterperforming business because we’ve got that diversity.”
Veolia employs more than 6000 people across Australia – and more than 200,000 globally – in its water, waste, and energy divisions. In 2023, 40 per cent of the company’s executive
committee roles were held by women. Not just to get the numbers right, but because they were the best people for those roles. In early 2025 this will reach a 50-50 gender split with a diverse range of backgrounds and career disciplines.
Richard says when diversity is at the top level, it lters down throughout the organisation and becomes part of the agenda.
“I’m really pleased with our diversity; it provides a great dynamic that is changing the look and feel of the company,” he says.
Veolia’s diversity success can be attributed to its attraction and retention programs.
Internally, all sta have access to NextGen, an early careers program that
provides ongoing development and skills while Veolia Cares guarantees every employee globally with parental leave, health cover and death bene ts.
When it comes to attracting sta , the Women on Wheels program, which provides on-the-job training for women who want to become waste collection drivers, has been so successful that it’s being rolled out nationwide.
‘Veterans at Veolia’ has also supported and provided opportunities for veterans in the transition from service to civilian.
e Future Forward program is another key part of Veolia’s diversity story. A partnership between e King’s Trust Australia, TAFE NSW, community and cultural specialists Bullroarers and AES (Aboriginal
Employment Services), the program o ers a customised career pathways program for First Nations People and Torres Strait Islanders.
Participants bene t from experienced mentors who provide insights, advice, and connections, fostering a community for ongoing growth and success.
Richard says there has been deep collaboration to devise a program that is appropriate and will attract more traditional owners to the industry.
Ten apprenticeships have so far been o ered right across Veolia’s operations, with the aim to welcome 100 First Nations and Torres Strait Islanders into the company through this program. And Richard is not stopping there. He’s calling on other businesses to join the journey, so that between them they can employ 1000 people in total.
“I’m aiming for thousands of job opportunities, not single digits,” Richard says. “We’re making our e ort, but I want to bring enough organisations into this to get that number much higher.
“We will be reaching out to a wide group of organisations, people we work
with, suppliers and partners in other aspects of our business to explain what we’ve done, what it looks like, the commitments required as a business and the outcomes.
“I’m con dent we will nd the organisations to do it, but they must be committed. We’re not doing this just so we can put it in our environment and social governance report, it’s so we can provide real employment opportunities, improve our business and do things better.
“We need a lot more people in the next two to three years, currently we don’t have the workforce.”
Logistics, operations management, technology, customer service, regulatory compliance and environmental science are all areas that will provide pathways for people with career ambition.
But Richard describes the waste industry as needing an image makeover to change people’s perceptions.
Veolia Chief of People, Safety and Environment O cer Kim Hall also emphasised the importance of people recognising the industry as more than just waste during a panel session at the
Contamination is an issue right across the recycling and resource recovery sector. For organics recyclers, coping with contamination can be dangerous and costly, as consultant Michael Wood discovered.
Organics consultant Michael Wood has backed a two per cent contamination threshold in kerbside organics collections to safeguard the recycling industry.
A consultant working in compost market development, Michael says other states could learn a lot from organics processors in New South Wales who have voted for the contamination threshold.
“Under the policy, if contamination of kerbside organics is not two per cent or under it is treated as mixed waste, not food organics garden organics (FOGO),” Michael says.
Two per cent doesn’t sound like much, but it could make or break circular outcomes. Michael should know. Working with a composting facility that processes kerbside FOGO collections across south-east Melbourne, he’s seen rst-hand the damage contamination can cause.
He says that in 2023, contamination rates at the facility were so high, customers were turning their back on the company.
e culprit? Glass.
“We couldn’t cope with the amount of glass in the bins,” Michael says.
“It smashes in trucks when it’s collected, it smashes on the concrete oor when the load is dropped and in the process system. Because the glass was so ne, it was missed at the picking station, and it started turning up in our product.
“ e amount of glass that came in was staggering. We started picking if o the
oor to try and get it out of piles before it smashed, but there was just too much.” e volume of glass in FOGO collections increased at peak occasions such as AFL grand nal weekend, Melbourne Cup Day, Christmas and New Year. However, oss sticks, thumb drives, syringes, razor blades and plastics are also common contaminants. Many of them small enough to slip through compost screening processes and too dangerous for manual picking.
Michael believes one cause of the contamination is a change in waste collection services. He says an increase in contamination correlated with the change to weekly FOGO collections and fortnightly waste collections.
“Once the garbage bin is full, the weekly service (FOGO), becomes the primary garbage disposal service,” he says.
John McKew, National Executive O cer of the Australian Organics Recycling Association has been raising awareness of the challenges and dangers of contamination for the industry.
“ e old saying is that you can’t make a silk purse from a sow’s ear,” says John. “And you cannot make quality compost, mulch, or soil conditioners from badly contaminated feedstock.
“If we cannot sell the end product because of poor feedstock or contamination, we do not have an organics recycling industry.”
Michael holds a Graduate Diploma in Applied Science Horticulture and has worked in organic recycling and nursery production for more than 30 years.
He provides consulting services in the industry through his business Oakwood Consultants. For the past six months he has worked to rebuild the reputation of the industry and introduce new equipment and processes to the Melbourne operation.
He says the industry needs standards and education across the entire supply chain, as well as the ability to contract contamination levels. Achieving a two per cent or less contamination rate is possible. For areas that can’t meet that threshold, he questions whether they should o er a FOGO service at all.
“We’re too focused on diversion and not circularity,” he says.
“Would you rather divert 70 per cent of waste and make a product and be circular or try and get 90 per cent diversion, not make product because it’s too contaminated and have a giant disposal problem?”
For more information, visit: www.aora.org.au
Obtaining the quickest return on your capital investment depends on how quickly operators can be up and running, and the volume of commodities that an operator can recover from their waste stream. EDGE Innovate’s range of mobile solutions are tried and tested, are quick and easy to set up, require no on-site civil works, represent a low capital outlay and are proven to achieve high commodity recovery levels.
Tailored solutions provider Orez is delivering a bespoke waste management solution for Epping facility Repurpose It to help minimise waste going to landfill.
Orez designs, builds and commissions cutting-edge waste management facilities for both kerbside and commercial waste streams.
Its latest project – an organic nishing line for Victorian resource recovery company Repurpose It – is the second time the companies have collaborated to breathe new life into recycled materials.
Repurpose It is a leading resource recovery company in Melbourne’s northern suburbs, recovering Food Organics, Garden Organics (FOGO) and turning it into nutrientrich compost.
e new nishing line will be used to provide a solution that doesn’t just focus on the reduction of waste but turns it into by-products that have both utility and value.
Ollie Brunt, Sales and Partnerships Manager, Orez, says the company specialises in providing holistic solutions for clients trying to overcome challenges in managing their waste streams.
DYNAMIC DUO
Orez and Repurpose It rst began working together two years ago when
Orez delivered its rst project – a FOGO pre-treatment process line.
Sean Galdermans, General Manager, Orez, says that project has given Repurpose It the con dence and trust to work with Orez a second time.
“ ey worked with us initially to provide a solution to decontaminate their incoming feedstocks prior to the composting process,” he says.
“ rough steep growth they are now at the point where they need additional processing capacity, and they’ve come back to us to provide a solution to screen the composted product in a highcapacity nishing line.”
Sean says returning customers are one of the biggest compliments Orez can get as a solution provider.
“ at is why we position ourselves in the market as a company committed to always deliver while not compromising on quality,” he says. “We have an extensive in-house design and delivery team here that’s local and understands the needs of our market.
“ is ensures we not only deliver projects in accordance with Australian standards but go above and beyond to
provide our partners with a solution that’s t for purpose and delivers a quality nish.”
THE PURPOSE OF REPURPOSE IT Sean says Repurpose It will use the nishing line to re ne its organic waste into di erent products for market.
“ e nishing line will take compost, do a nal polish by removing light plastics and metals, and size it into four di erent fractions that can be repurposed into soil blending and other premium products for further use,” he says.
“Repurpose It is on a steep growth trajectory, so this project is also being built to allow for future growth. It will be one of the highest capacity lines in Australia in this industry sector. It is crucial that this line processes material at a very high rate and what is coming out is in line with quality expectations of our customer.”
Sean says the nishing line incorporates two drums connected to form one large drum, adding up to more than 20-metres in length. “Drum screens are capable of sizing
material, we feed material into that drum and whatever is small enough to pass through the holes in each section is then screened out, conveyed and stockpiled,” he says.
“We remove ferrous metals out of the waste streams with magnets which is quite standard in the industry.
“ e design also has allowed for dedicated wind sifters on the mid and oversize fractions that separate light plastics and light materials from heavies. Combined with the very long drum screen these are the highlights of this project.”
Jaimen D’Souza, Head of Continuous Improvement and Capital Projects for Repurpose It says the Epping facility is one of the largest organics processing facilities in Victoria, with the capacity to process more than
200,000 tonnes of organic waste each year.
“Creating premium quality, sustainable products is vital to the transition of Australia to a circular economy,” he says. “ is nishing line complements our existing organics operations; however, the new nishing line will allow the innovation of new products, and an increase in the amount we can process.”
Jaimen says the nishing line will support the National Waste Action Plan to reduce organic waste to land ll by 50 per cent by 2030.
“ rough our best-in-class composting solutions we can divert FOGO from land ll and produce high-quality nished products,” he says.
“While there is existing demand for FOGO-derived compost in
broad acre applications, Repurpose It is dedicated to transforming its FOGO into a premium value product, responding to increased market demand, and expanding into emerging markets for high quality, nished materials”
e nishing line is with Orez’s design team and is expected to arrive in Australia for installation in 2025. is project is supported by the Victorian Circular Economy Recycling Modernisation Fund. e Fund is delivered by Sustainability Victoria under the Australian Government’s Recycling Modernisation Fund and the Victorian Government’s circular economy plan, Recycling Victoria: a new economy
For more information, visit: www.orez.com.au
Mobile phone recycler MobileMuster is seeking a bigger bandwidth, extending its reach to businesses.
MobileMuster is dialling things up.
For the past 25 years the product stewardship program has worked with the telecommunications industry to provide a free nationwide mobile phone recycling network.
e rst voluntary product stewardship scheme in Australia to be accredited by the Federal Government under the Product Stewardship Act 2011, its membership boasts 94 per cent of all telecommunications carriers and 96 per cent of all phone manufacturers.
Since its inception, the scheme has collected and recycled more than 2000 tonnes of e-waste and diverted more than 96 per cent of donated materials from land ll – equivalent to 5000 tonnes of carbon dioxide being removed from the atmosphere or planting more than 80,000 trees.
In the 2024 nancial year alone, 109 tonnes of mobile phone components were recycled by the scheme. But it’s not done yet.
Joel Murray, Australian Mobile Telecommunications Association
(AMTA) Marketing and Communications Manager, says the scheme is extending its reach.
“We’re looking outside the telecommunications industry to see who else we can help,” he says.
MobileMuster’s Insights into mobile phone use, reuse and recycling 2020 report showed a high awareness of mobile phone recycling in the community, with 70 per cent of the population aware of the program.
However, Joel says there is an abundance of untapped recyclability in businesses across Australia. It’s that resource MobileMuster is hoping to dial into.
He says when it comes to upgrading or buying new eets of phones, businesses sometimes are unaware of their options.
“While there are reverse logistics and waste management services who accept mobile phones and accessories, MobileMuster is the more responsible way to deal with mobile waste,” Joel says.
“We’re a free mobile phone recycling service with logistics and transport built in.”
e business-to-business service can take many shapes – from an in-o ce MobileMuster collection point to a designated recycling event.
Depending on the quantity, end-of-life phones and accessories can be mailed to MobileMuster or the scheme can arrange pickup.
e scheme has been extended over the years to include smartphones, landlines, speakers and networking equipment. However, items covered under the National Television and Computer
Recycling Scheme (NTCRS) such as tablets, computers and screens, are not accepted.
Collected items are transported to MobileMuster’s recycling partner where they are dismantled, sorted and broken down into raw materials.
A smartphone contains many materials including cobalt, nickel, and lithium as well as small amounts of gold, silver, palladium, copper, and platinum. When mobile phones are recycled these materials are available for use in new products, reducing the need for virgin materials and resources.
At year’s end, MobileMuster provides a report of the number of phones collected and the environmental impact which can be used in corporate environmental and social governance reporting.
Joel says starting a collection service is as simple as sending an email to MobileMuster or lling in an online form.
He encourages any and every business to get involved. MobileMuster is also looking to work with waste management companies to discuss opportunities for greater collaboration.
“Our goal is to create a circular economy for mobile waste,” Joel says.
“ at’s not easy, but the more resources we can avoid being mined from habitats by recycling devices and putting materials back into the market, the better.
“We’re trying to do our small part for the environment.”
For more information, visit: www.mobilemuster.com.au
For more than 11 years, WestRex has taken dangerous and hazardous waste and made it safe. Now, it’s ready to revolutionise the industry, taking on the name of parent company, Pure Environmental.
David Powell, WestRex General Manager says the time is right to embrace innovative thinking and technology.
“Now is the time to think even bigger and continue to challenge ourselves about how we can take waste management to a whole new level,” he says.
“Collectively, we have a team of over 70, including some of the top minds in the dangerous and hazardous waste space.
“Pure Environmental represents more than just a change in name. It represents a shift in aspirations and renews our commitment to leading the charge towards sustainability.”
Recognising the importance of a shared vision, David says WestRex values align with Pure Environmental.
“We’re actively committed to research and development in processing, treatment and resource recovery,” he says.
“And we know there’s real power in collaboration.”
David says harnessing the collective expertise of the Pure Environmental board provides the team with access to a depth of knowledge and expertise, encompassing all aspects of waste management.
From receival and recycling to waste reduction innovations and sustainable practices, the team can stay at the forefront of new technologies and strategies, ultimately enhancing its ability to manage waste more e ciently and e ectively.
“ e board of Pure Environmental consists of key players and thought
leaders of the waste industry,” David says.
“ ey came together to form a contemporary business to genuinely address sustainability through more agile and innovative practices.”
Across Pure Environmental’s national facilities a technical team of engineers and in-house industrial chemists is developing treatment and recovery technologies to identify and bene cially reuse hazardous waste materials.
is focus on sustainable waste management solutions represents a broader industry shift towards a circular economy and highlights the importance of environmental and social governance (ESG) reporting and compliance for customers in the dangerous and hazardous waste sector.
Beyond compliance, David says a new generation of skilled workers is looking to recycling, re ning and reuse of waste as an exciting career opportunity.
“Pure Environmental’s Graduate Program is evidence of incubating fresh perspectives and cutting-edge creative solutions,” he says. “Historically, it has been a challenge to attract new talent to the industry. Pure’s Graduate Program received more than 100 applicants for 2024, a clear indication that sustainable environmental outcomes are becoming increasingly appealing to the younger generation wanting to make a di erence.
“With a new generation comes a new way of thinking, bene ting the entire team. Enthusiasm and passion, tech-savvy skills, and new perspectives are just some of the bene ts of hiring young talent.”
David says the future is bright for the industry with advancements in technology pushing the boundaries of what’s possible. e enthusiasm in the industry is palpable, driven by passionate individuals and teams who are committed to shaping a better tomorrow.
“Our customers know that with Pure Environmental, they’re partnering with a company committed to providing commercially competitive, compliant solutions for the most challenging waste,” he says.
“We hold a high standard for any recycled products and manufacturing of products as required.”
Launched in 2022, the Pure NV Compost, Leyburn Organics Recycling facility is a hub of innovation that reuses waste in a sustainable way, a prime example of Pure Environmental
standards according to David. “By employing cutting-edge technology, state-of-the-art equipment and best practice, we are now leaders in sustainable and e ective soil solutions,” he says.
“Our commitment to environmental stewardship and soil health ensures our products are e ective and responsible.”
David says it is time for everyone to embrace the evolution of waste management.
“We’re all invested in striving towards a circular economy and a sustainable and greener future,” he says.
“We know Pure Environmental is going to lead the way, because we believe it’s a shared responsibility, owed to ourselves, future generations, and our planet.”
For more information, visit: www.purenv.com.au
• 4 bay sorting - Recovers clean stone, wood, paper, plastics, card or other recyclable materials at the option of the operator
• Combines air separation, magnetic separation, and manual sorting in one compact unit
• Adjustable belt speed - 1200 mm wide picking belt adjustable to suit waste material and desired recovery required
• The hydraulic jack leg support offers rapid set-up and transport
RecycleSmart introduces a new recycling system across offices and cafes in hopes to reduce the number of tricky-to-recycle items landing in landfill.
Only nine per cent of plastic waste generated in o ces is e ectively recycled, with a large portion ending up in land lls, according to notfor-pro t environmental conservation organisation Clean Up Australia.
For this reason, on-demand recycling business RecycleSmart recently introduced a new package to make recycling easier for businesses and cafes.
Dan Crawford, RecycleSmart National Business Development Manager, says the package is a rst for the industry, is scalable and easy to manage. He sees it as only the beginning of the o ce and café recycling journey with RecycleSmart.
“We believe it will be a great way to drive recycling of tricky items for businesses and cafés,” he says. “It provides them with a simple solution.” e solution is a one or two-bin system delivered directly to participating o ces and cafes. Dan describes it as set and forget – customers can forget about their recyclables until RecycleSmart’s fortnightly pickup.
“Having a separate bin drives better recycling rates and increases engagement because sta members and their customers can clearly see a bin that’s just for recyclables,” he says.
“It drives people’s mindsets to be better recyclers, while also being a great branding opportunity for the business or café.”
For the past ve years, RecycleSmart has strived to make recycling easy and accessible for everyone.
It began as a home pick-up service for hard-to-recycle items and has expanded across Sydney, Melbourne, Brisbane, Adelaide, Perth and beyond.
Dan believes the expansion into o ces and cafes will continue to foster a growing and engaged community that embraces sustainable behaviour.
RecycleSmart o ers two recycling packages for o ces.
e essentials o ce package comprises one 60-litre bin for ‘tricky recyclables’, one year of fortnightly collections (26 pickups) and a customisable internal communication pack.
Accepted items range from soft plastics to e-waste, co ee capsules, co ee cups, batteries, pen and markers, textile, etc.
For larger o ces, RecycleSmart o ers one premium-sized bin in addition to the items in the essentials pack. Both packages are delivered and set up by RecycleSmart.
e premium package is an example of a circular economy in action – its clear decorative labels are made from recycled materials.
Both packages include the educational signage.
Understanding that a café di ers from an o ce, RecycleSmart’s caféspeci c package includes two 60-litre bins with educational signage. One bin collects soft plastics, 10-cent refundable containers and other tricky-to-recycle items, while the second collects single-use co ee cups.
e package also includes one window decal which says, ‘saving resources with RecycleSmart’, and one co ee cup stamp.
“Cafés can press that onto the cups to communicate to their customers about their recycling project,” Dan says.
“It also helps drive business. If the customer has recyclables and we operate in that area, it helps them know they can recycle with us, or they can bring it back to the store for recycling.”
In addition to reducing recyclables reaching land ll, RecycleSmart hopes these packages will increase education on tricky-recyclables.
“People are constantly asking us what can be recycled, and it is always changing,” Dan says. “Only last week we discovered six new items that we could start to recycle because we found a solution.
“For this reason, we also have a QR code which is regularly updated with what items we can recycle.”
Dan says the o ce and café package is a positive step forward for businesses wanting to advance their recycling systems.
“Any business or café that wants to recycle can participate.”
For more information, visit: www.recyclesmart.com
The BOMAG BC773 soil compactor excels on large construction sites and landfills, adept at handling almost any material, from highly cohesive soils to challenging wet conditions. This capability stems from its optimal traction and powerful diesel engines.
Combined with high thrust, the BC773 achieves outstanding gradeability. Its low centre of gravity and wide wheelbase ensure stability, while BOMAG’s specially developed wheel design makes this all-rounder suitable for nearly any application, even under the most demanding conditions. Brisbane
Cookers gives used cooking oil from commercial kitchens across Australia a second life – one that avoids ending up in landfill.
For more than 20 years, Cookers Bulk Oil System, or Cookers, has specialised in cooking oil management and handling – from the hazards of handling hot oil through to safely disposing of it once used and giving it a second life.
According to deep frying specialists Frying Nation, just one commercial kitchen can be responsible for 90 kilograms of fryer oil each week, 306 kilograms per month and 4700 kilograms per year, ending its life in land ll.
It’s this practice that Cookers is aiming to eliminate with its Smart Oil Solution.
Peter Fitzgerald, Cookers Managing Director, said the team saw the opportunity to provide a circular system in commercial oil handling.
“We saw a good opportunity for a business that was scalable, sustainable and a better way of doing things,” he says. Typically, oil has been delivered
to restaurants, cafes, hotels, fast food establishments and manufacturers in single use tins or a bag in box. Cookers supplies specialised, food-grade, stainless-steel tanks to its clients on free loan, eliminating the use of single use non-recyclable tins that end up in land ll.
Cookers supply a fresh oil tank with an electric pump to ll the fryers and another stainless-steel tank speci cally for used cooking oil.
Peter says these custom storage units are designed to eliminate the residual oil left in packaging and the subsequent waste of the packaging itself.
“When the outlet needs to dispose of the used oil we collect it in a designated vehicle. e oil will be dewatered through a certi ed line of process in the Cookers’ depot and sent out for recycling, from where it can be reused in other industries,” he says.
“Cookers’ mission to reduce greenhouse gases and lower carbon emissions is achieved through its extensive recycling process into three main uses – biodiesel, animal feedstock, and other oil-based products.
“Cookers understands the value of cooking oil and the need to give it a second life.”
Cookers tracks every drop of cooking oil supplied and used, ensuring no oil gets disposed into drains, waterways and land ll.
Peter says every truckload of fresh oil delivered saves 300 tins going to land ll, making Cookers a positive player in the waste industry.
Biodiesel is the main product produced from the recycled oil. In Cookers’ case, the oil is being repurposed into sustainable aeronautical fuel.
Peter says aeronautical fuel is currently the greatest use of recycled cooking oil internationally. Renewable fuel is one of the most important approaches the aeronautical industry can take to o set the large percentage of greenhouse gases emitted by planes.
“You can’t run planes on electricity, they need that fossil fuel replacement, so the processes have developed signi cantly,” he says. “ ere’s a lot of investment going into sustainable aeronautical fuel because it’s such a big contributor to greenhouse gasses.”
Stock feed is the second use for Cookers recycled oil, primarily for cattle that require a strong nutritional pro le. An animal nutritionist will determine the level of carbohydrates, protein and fat within the cattle’s required diet.
Peter explains how, in many cases, re ned used cooking oil is the fat
portion of the dietary uptake for most feedlots.
“It has to comply with the standard set by the Australian rendering industry,” he says.
A yearly audit ensures Cookers is not providing a contaminated product.
e third use for used cooking oil is chemicals.
ere are varying uses for the chemicals, including agricultural surfactants, dust suppressants, concrete release agents, and bitumen.
“As the economy is becoming more conscious of environmental issues, there’s increasingly interesting outcomes for used cooking oil,” Peter says. “If it’s of a su cient quality we can substitute for that, it’s not uncommon in the chemical industry.”
To further cement its commitment to sustainability, Cookers developed its oil management training. e training is a large part of the service it o ers, overseeing businesses as they are educated by Cookers representatives to make sure they get the most from their oil.
“We go out and evaluate the condition of the oil in the fryer, and we can also check the calibration of the fryer,” Peter says.
“We encourage people to do tests and trials to assist them to get the most bene t out of their oil and to not throw it out early because it is a waste.”
For more information, visit: www.cookers.com.au
Why a leading industry player in construction and demolition resource recovery and recycling continues to partner with Tutt Bryant Equipment.
BMI Resource Recovery has been at the forefront of property development and the provision of waste management solutions for recycling, waste transfer stations and land ll activities in south-east Queensland since 1988.
While the privately-owned business undertakes resource recovery at all sites, two plants in particular focus on the recovery of various materials, including concrete, bricks, masonry, asphalt, green waste, timber, soils, metals, e-waste, and plasterboard from a mixed waste stream.
More than 90 per cent of the waste delivered to BMI’s resource recovery sites is recycled and reused – either separated for further reprocessing or collected by specialist recycling partners.
e company’s concrete crushing plants play a crucial role in producing
a range of recycled road base products used in building, landscaping, and civil construction.
Committed to improve resource recovery conversions, BMI continues to develop its sites and invest in state-of the-art waste sorting technology.
BMI purchased an M&J 4000-8 mobile pre-shredder from Tutt Bryant in 2021. e company was so impressed by the machine’s performance and reliability, that when management was considering further expansion of shredding operations, it turned to Tutt Bryant for a solution.
BMI’s Watson Road facility at Acacia Ridge processes large volumes of construction and demolition (C&D) waste. A xed plant extracts recoverables such as concrete, timber and steel.
e residual waste from this process is normally bulky, light products such as plastic pipe, gyprock, and the like. BMI has placed another M&J 4000-8 into this operation to reduce the volumes of these residual products and maximise transport densities and land ll compaction.
“It’s one hell of a shredder,” Site Manager Ryan Watson says of the M&J shredder. “We have thrown power poles in this thing, and it eats them. It is simple to operate, has great access and is very manoeuvrable around site. It’s a really good machine.”
In parallel, BMI Group’s Operations Manager AJ Ali required another
shredder at the Stapylton Resource Recovery facility to support various shredding applications around the site.
is was AJ’s third M&J shredder purchase and his reason for the repeat purchases was clear.
“We need a machine that is t for purpose and robust enough to handle the volumes and composition of waste streams we receive. e M&J is very reliable and provides great production.”
M&J Waste Recycling shredding technology is based on an aggressive knife design and open cutting table which provides outstanding performance when dealing with mixed and challenging materials.
ese key features make M&J PreShred units resistant to wear caused by materials and waste normally considered as unshreddable, including metal, reinforced concrete and rocks. e combination of aggressive knives cutting in both directions through the cutting table and the shafts running asynchronously means shredding is available in every direction to optimise production.
Tutt Bryant Equipment provides technical support to BMI Group with ongoing equipment, parts, and service needs, as required.
For more information, visit: www.metso@tuttbryant.com.au
Turmec is drawing on decades of global experience to shape a sustainable future, one recycled material at a time.
Construction and demolition (C&D) waste recycling is an Australian success story.
Waste industry operators continue to invest in waste processing and recycling technology, pushing resource recovery to more than 22.4 million tonnes in 2020-21 – more than double the volume recovered 15 years ago – according to the National Waste Report 2022
Better recovery techniques have resulted in reusable/recycled materials including metals, timber, soils and aggregates for use across multiple sectors, reducing reliance on virgin materials.
e imperative to manage and recycle construction waste more e ectively has never been more pronounced, says Geo Bailey, Turmec Chief Executive O cer.
e escalating costs of land ll disposal, driven by regulatory pressures and environmental considerations, necessitate advanced recycling solutions.
Turmec, stands at the forefront of delivering state-of-the-art recycling facilities. Its legacy in the recycling industry is built on a foundation of engineering excellence and innovation.
Geo says Turmec’s approach leverages the latest advancements in proven technology to design and implement bespoke recycling solutions tailored to the needs of each client.
“Our systems are highly automated which reduces the reliance on expensive manual labour and ensures consistent and e cient recovery of valuable recyclables while maintaining high standards of purity,” he says.
A past project for Central Waste, New South Wales. See the full case study at www.turmec. com/case-study/central-waste-station/ Image: Turmec
“Our impact on the recycling industry is profound. Our facilities consistently achieve recovery rates exceeding 90 per cent, setting benchmarks for the industry.”
Each Turmec plant is speci cally designed to meet each customer’s recycling needs.
e factors that in uence each design include available space, current and anticipated future volumes, the composition of the waste to be processed, the materials to be recovered and the purity required, the degree of automation and the available capital budget.
A typical C&D plant would include some or all of the following equipment:
• a shredder (for size reduction ensuring optimal throughput and materials recovery)
• screeners or density separators, ballistic separators, magnets, eddy current and optical sorters.
Geo says the team takes pride in being able to see the bigger picture with innovative, proven solutions.
Turmec helps clients stay abreast of the changing demands of waste management, including waste-toenergy, biomass, rubber, glass and ash.
Looking forward, Turmec envisions a future where land ll usage is minimised, and resource recovery is maximised.
“We aim to expand our footprint globally, bringing our expertise and cutting-edge solutions to markets that are beginning their recycling journeys,” Geo says.
“As market leaders, we are committed to driving the recycling revolution, ensuring that valuable resources are recovered, and environmental impacts minimised.
“ e upward trend in land ll costs underscores the necessity for advanced recycling facilities, and Turmec is poised to meet this demand with best-in-class technology and innovative designs.”
For more information, visit: www.turmec.com
Landfill Services
Gas collection system (GCS) design and construct
Carbon credit reporting and management
Data management and reporting
Monitoring and maintenance
Leachate system installation and servicing
Advisory and strategy
Power generator servicing and maintenance
Landfill Products
Mobile flare hire
Lo-cal flare range
High temperature flare range
Gasflux continuous gas analysers
Leachate telemetry systems
Leachate pumps and controllers
Power and heat generation systems
Caterpillar unveils the new MH3050 material handler.
Incorporating feedback from its global customers, the MH3050 material handler takes innovations from earlier models, and adds a few of its own.
“ e MH3050 is our largest wheeled material handler,” says Bassem Ibrahim, Waste and Recycling Specialist, Caterpillar General Construction and Infrastructure Division.
“It completes our line-up and bridges the gap we had with our series of tracked material handlers – the MH3250 and MH3260.
“I regard it as best-in-class as it bene ts from all the innovations of earlier models. We have leveraged the engineering development, optimised common parts, and used the same general service procedures.”
At 18 metres, the MH3050 has the longest reach of the wheeled material handler line-up. It can be tted with
the Cat® 1.5 metre orange-peel grapple in typical scrap material applications, as well as the Cat clamshell grapples up to 1.7 cubic metres, depending on the material handled.
e electro-hydraulic system is at the heart of the next generation of Cat hydraulic excavators – and now also the material handlers. It takes centre stage within the MH3050.
e pilot system with hydraulic lines and lters going from the elevated cab to the main valve has been removed. In its place, the joystick signal is sent via an electrical connection to the ECM (electronic control module) that controls the main control valves.
Bassem says the update simpli es the whole system with the removal of the pilot lines and allows endless tuning possibilities. e machine can be netuned to individual operator preferences
and those can be saved under the operator ID.
Heat and noise generation in the cab is reduced with the removal of the pilot system. Operator feedback suggests it provides a smoother operation and controllability while using combined functions – boom, stick, grapple open and close, and swing.
e hydraulic cab riser with new dampening system provides additional cushioning from external vibrations.
e MH3050s operator space is based on the new ergonomic cab found on Caterpillar’s earthmoving excavators. It has been validated by many operators and is adapted to the operations of the wheeled material handlers – and speci cally the MH 3050 – with operator safety in mind.
“Steering is by joystick command only,” says Bassem. “ e elimination of the steering column improves forward visibility as well as enhancing legroom and ease of cab entry.
“Navigation of the touchscreen monitor is as easy and intuitive as using a smartphone.”
A large, 10-inch high-resolution touchscreen monitor with jog-dial o ers easy navigation of the intuitive operator controls. e machine automatically recalls joystick settings based on the operator ID.
Large tempered glass windows with smaller pillars on the cab enhance allaround visibility and operating safety. Front and roof windows are made of high impact glass –10-millimetre thick P5A or the 25-millimetre P8B certi ed laminated glass.
Cabs are also optionally tted with the FOPS (falling object protective structure) guard level II and feature a wide seat that is heated, ventilated, and o ers a variety of settings and adjustments.
e MH3050 is also equipped with 1800-lumen LED lights on the chassis, boom and stick, o ering greater safety and full visibility while operating in the dark.
Standard right-side and rear-view cameras, with the option to upgrade to 360-degree vision, display a video feed on the large in-cab touchscreen monitor to further enhance work area visibility.
E-fence, which comes as standard – allows the operator to pre-set the working envelope from the monitor. ey can also activate the Cab Avoidance to ensure the grapple doesn’t meet the cab.
A ground level shut-o switch stops all fuel to the engine and shuts down the machine. Standard boom and stick lowering check valves prevent reverse oil ow in the event of unexpected loss of hydraulic pressure,
always keeping the front linkages securely in place.
e MH3050 is powered by the Cat C9.3B engine, which can operate on up to B20 biodiesel and meets EU Stage V and US EPA Tier 4 Final emissions standards.
Bassem says the engine’s maintenance-free after treatment system lowers operating costs and maximises machine uptime.
“ is six-cylinder engine is the same one found in other mass production excavator models such as the 336 and other Cat product lines (D6, D7 dozers, 966 and 972 medium wheel loaders),” he says.
“ e exact power requirements are ne-tuned to the task at hand with the choice between Power, Smart and Economy modes, lowering fuel consumption without sacri cing machine performance.”
Boom and stick o erings combine to provide up to 18-metres of reach, allowing operators to move more material without repositioning the machine. e MH3050 also o ers high swing torque to quickly move material.
Allowing the boom to freely travel up and down without using pump ow, standard Smart Boom allows the operator to focus on stick and grapple control from a more fuel-e cient cycle.
A range of attachments are available, increasing operating exibility. An optional 25kW generator is available exfactory for magnet applications.
Bassem says it’s the long stretch in the Cat line-up, large grapple size all around, controllability and smooth hydraulic response that combine for the MH3050s superior performance.
“ e electro-hydraulic system allows further development,” he says. “ e MH3050 also o ers reliability
that customers can count on and low operating costs thanks to extended service intervals, a choice of power modes and parts commonality with the rest of Cat excavators.
“ e operator is in a safe and comfortable work environment and can set up the machine for optimum production and e ciency with the latest onboard technology.”
Various cab access options provide easy, safe and quick access to the upper service area.
e Standard Product Link captures critical operating data such as location, hours, fuel usage, productivity, idle time, maintenance alerts and fault codes, which can be remotely accessed and tracked to boost eet management e ciency.
Lasting 50 per cent longer than previous designs, the new hydraulic oil lter improves ltration and increases change intervals to 3000 operating hours, while new anti-drain valves keep the hydraulic oil clean during lter replacement.
Operators can track lter life and maintenance intervals on the in-cab high-resolution monitor. Eliminating the need for operator interaction, the high-e ciency cooling fan features a standard automatic reverse function to keep the cores clean, maximising machine uptime. For
The Eden Project has transformed a disused clay pit into a thriving ecological wonderland, offering valuable lessons for rehabilitation projects across Australia.
The Eden Project’s journey began in the mid-1990s when businessman
Tim Smit saw potential in an exhausted clay pit. e project persevered despite initial challenges, including torrential rains and complex drainage issues.
e project’s success in converting a sterile clay pit into a thriving ecosystem is o ering a powerful model for remediation and revegetation of Australia’s numerous disused mining and quarry sites.
A diversity of plants has been planted in soil made from waste materials, in giant conservatories and buildings that draw inspiration from nature.
e Eden Project’s commitment to sustainability extended to its day-today operations. By partnering with companies such as Volvo Construction Equipment, the project transitioned to electric machinery, a shift that bene ts the environment and improves worker comfort and e ciency.
Using zero-emission electric excavators and wheel loaders also demonstrates the viability of electric heavy equipment on large-scale projects while supporting Eden’s commitment to sustainability, including its ambitious
goal of achieving climate positivity by 2030.
More broadly, it showcases the potential of sustainable technologies in real-world applications.
During a three-month project, the use of Volvo CE’s electric machines saved three tonnes of carbon dioxide emissions, highlighting electromobility’s tangible impact on reducing the carbon footprint of large projects and contributing to improved air quality within the project area in Cornwall.
e electric machines also helped conserve nearly 2000 kilowatts per hour of energy over the same threemonth period.
Electric machinery typically produces less noise than traditional dieselpowered equipment, which contributes to a better environment for employees and visitors to the project.
is reduction in noise levels can greatly enhance operator comfort, reducing fatigue and stress over long working hours.
Electric motors also produce less vibration than internal combustion
engines. is vibration reduction can lead to a smoother operating experience and potentially reduce physical strain on the operator.
With zero direct emissions, electric machines eliminate the exhaust fumes associated with diesel engines. is can result in better air quality around the machine, which is particularly bene cial for operators working in enclosed or poorly ventilated areas.
Electric motors provide instant torque and smoother power delivery, translating to more precise control and potentially a more comfortable operating experience.
As Australia faces environmental challenges, the Eden Project is an inspiring model for embracing renewable energy and electric machinery to reduce carbon footprint.
e Eden Project’s success demonstrates that with vision, innovation, and commitment to sustainability, even the most challenging sites can be transformed.
For more information, visit: www.cjd.com.au
Komatsu wheel loaders are ideal for any type of loading and handling operation within waste, recycling and resource recovery.
Pioneers in advanced machinery, Komatsu Australia has maintained its position as a leader in the industry for more than 40 years.
Renowned for high quality standards and reliability, Komatsu wheel loaders meet the huge demands placed on machines by the waste management and resource recovery industry with a range of options and modi cations available.
Nick Vrontas, National Business Manager, says this exibility allows the wheel loader range to adapt to speci c requirements of waste handling applications and job site conditions.
Available in both standard and tool carrier variants, the Komatsu wheel loaders range from compact utility machines for local government projects, through to loading, handling and stockpile machines, right up to the largest mechanical and electrical drive mining loaders.
“For decades, owners and operators have appreciated Komatsu wheel loaders’ low fuel consumption and operating costs,” Nick says. “When combined with reliability and ease of operation, they are suitable for any type of loading and handling operation.”
Bucket cylinder guards, cooling screens, underbelly guarding, and front window and OEM light guards are standard inclusions on all Komatsu wheel loaders.
Nick says these are particularly important when working on uneven ground and sites with debris, such as land lls.
Underbelly guarding reduces debris build-up into the rear frame and shields the power train and hydraulic components while protecting the engine oil pan, oil drain and fuel tank drain. e front window guard provides an
additional layer of protection to the window and operator and cooling screens increase e ective air ow while reducing the amount of debris reaching the coolers.
Lift cylinder guards can be included to protect the lifting cylinder hydraulic hoses, as can axle seal guards, to reduce debris build up around shaft and seals.
Solid tyres, another optional inclusion, are designed to perform in tough recycling and waste management applications, reducing downtime and improving productivity.
When it comes to improving productivity, the newly designed WA475-10 features the next generation technology developed with input from customers.
Nick says it saves 30 per cent more on fuel e ciency than the previous
model and is suited for any loading jobs with a combination of fuel e ciency, productivity and ease of operation.
e wheel loader features the newly developed Komatsu’s Hydraulic Mechanical Transmission (KHMT), an innovative solution that makes the loader more powerful and fuel-e cient.
Variable speed control allows operators to adjust the machine’s top speed to meet speci c site requirements, and the adjustable variable traction control also limits wheel spin on unstable and slippery ground conditions often found on many waste sites.
An optimised Z-bar linkage system provides much more lift force and a higher tonnes-per-hour production rate than previous models, and the response time of the hydraulics and the dumping or lifting can be set to speci c site requirements.
e newest Dash 8 wheel loader range, including the WA2708 and WA320-8, is powered by Tier 4-compliant low emission engine technology, delivering improved fuel e ciency, higher productivity, and reduced costs.
“ ere’s been a growing demand for Tier 4-compliant machines in Europe and the United States, and Australia is now following in that respect,” Nick says.
“Because our customers are chasing machines with the Tier 4 tick, the vast majority of the products that we market nationally are now Tier 4.”
Also helping to drive productivity is Komatsu’s innovative SmartLoader Logic technology which regularly evaluates load and working requirements. is engine control system senses the power
Melbourne, 23-24 Oct 2024
www.eldan-recycling.com
requirement of each work phase and automatically changes between ‘economy’ and ‘power’ mode based on the application’s demand, reducing fuel consumption while maintaining the machine’s performance.
Nick says Komatsu designed and manufactured drivetrain and hydraulic components ensure that all elements work together to their optimum capabilities, paving the way for high productivity, ease of operation, reliability and durability, and long service lives.
All Komatsu machines are covered by the Komtrax remote monitoring system which constantly monitors and analyses machine health, production rates, fuel consumption and other operating parameters.
For more information, visit: www.komatsu.com.au
Rimini, Nov 5-8 2024
• Modified for recycling of tough material, e.g. ASCR cables Cu scrap & Al cables and low-grade cables.
• The rotor is manufactured with hard-face welding.
• Screens with different hole sizes are available .
• Exchangeable wear parts makes it a virtually indestructible machine.
• Large fly wheel to minimize current spikes.
Industrial equipment distributor Bliss & Reels is entering the recycling equipment market and aims to take on one of Australia’s largest waste streams.
Bliss & Reels has a wealth of experience in supplying, commissioning, and servicing a variety of production machinery for steel, concrete, asphalt and timber industries.
Now it’s using its expertise to help create a smarter, greener Australian economy. e company is entering a new era, partnering with French recycler and recycling equipment manufacturer MTB.
Martin Kesselring, Managing Director Bliss & Reels, says the strategic move comes on the back of regulatory changes in Australia’s waste and recycling landscape and aligns with the company’s vision for resource recovery.
“We’ve got to stop looking at waste as waste, instead treating it as a valuable resource,” Martin says.
“With other countries no longer accepting our rubbish, and the Australian Government introducing waste export bans, it creates a lot of opportunity here in Australia.”
He sees one of the biggest opportunities in dealing with the nation’s estimated 459,000 tonnes of waste tyres annually.
Stefan Reiling, Business Development for Recycling and Automation, says secondary mining of metal and copper from Australia’s “mountain”
of waste tyres is an ideal introduction into the industry.
Stefan will head Bliss & Reels recycling division, working closely with MTB to bring its containerised solutions for tyre recycling to Australia.
He says one of the attractions of MTB is that it not only manufactures recycling equipment for metal recovery but operates its own nonferrous recycling plants.
“ e idea that MTB carries out practical production is very attractive,” he says. “ ey use the machines they develop.”
MTB’s range of equipment extends from full recycling lines to turnkey and compact lines but it’s the recycling line in a container that Stefan believes will be suited to the Australian market.
“It’s a range of ready-to-use lines made up of a series of MTB machines contained in one or various containers,” he says.
“It’s plug and play. When we talk to customers about their recycling challenges, this seems like a good solution, especially for remote areas.”
MTB continually expands its equipment range to provide a variety of solutions for all types of waste. New equipment is designed to respond to market challenges and to perfect solutions.
“Innovation is really a key factor for us,” explains MTB Sales Manager Romain Doeppen. “We take our role of advising our customers very seriously, so that together we can design the most technically e cient recycling lines, but also the most pro table and energy-e cient.
“ e evolution of our range and the integration of new technologies enable us to meet ever more complex demands.”
While Bliss & Reels is at rst focusing on tyre waste, the company aims to expand its o erings in the recycling sector. It will have a stock of all critical parts available in Australia.
Martin says the company’s 76-years’ experience provides a solid knowledge of engineering, infrastructure and safety requirements.
“ is diversity has been planned for several years, we’ve been waiting for the right time,” Martin says.
“ ere now seems to be government appetite and regulations in place for Australia to become a smarter, greener economy.
“We are looking forward to building it into a substantial division.”
For more information, visit: www.blissandreels.com.au
Metso Lokotrack® LT1213S™
Discover the Lokotrack LT1213S Mobile Horizontal Impact Crusher: Engineered for versatility, high capacity, and seamless mobility. Ideal for diverse applications from limestone processing to recycling materials, this robust machine includes a high-capacity dual-slope screen and a return conveyor that delivers precision-calibrated end-products.
Elevate your waste management capabilities with the LT1213S–where efficiency meets performance.
Brisbane | Sydney | Melbourne
Adelaide | Perth
Material Processing Solutions joins forces with IFE Material Handling, enhancing Australia and New Zealand’s access to global material handling and processing technologies.
Material Processing Solutions
Pty (MPS) is quickly gaining recognition in the recycling and resource recovery industries for its innovative approach to material processing, with a strong focus on the recycling, alternative fuels, and organics sectors.
With more than 50 years’ combined experience in these supporting industries, the company is dedicated to delivering reliable and advanced technological solutions.
Simon Sherwood, MPS Managing Director, says it’s the company’s unwavering commitment to excellence, including its customer service, that makes MPS a standout for businesses seeking cutting-edge solutions in material processing.
European manufacturer IFE Material Handling is a global leader in the manufacture of tailor-made processing equipment.
Its range of waste screens, ip op screens, vibrating feeders and magnetic separations technologies such as eddy currents, drum magnets and electro and permanent magnets, are speci cally designed to meet customer requirements and applications.
IFE already has a strong foothold in Australia and New Zealand with more than 150 machines in operation across the two countries. e collaboration with MPS o ers a unique opportunity to increase its footprint in the AsiaPaci c region.
Helmut Tröbinger, IFE Global Sales Director, says the partnership is set to deliver substantial bene ts to processors across the two countries.
“By combining MPS’s strong local presence and deep understanding of the region’s material processing requirements with IFE’s innovative product range, customers can expect unmatched service and advanced technology,” Helmut says.
“To further enhance support, MPS now holds a local stock of IFE critical spares and o ers comprehensive service from its headquarters in the New South Wales’ Blue Mountains, ensuring timely and e cient assistance for our current and future customers.”
e partnership marks a signi cant milestone for both companies. For MPS it represents a strategic expansion of its product portfolio and a strengthening
of its market position in Australia and New Zealand.
“We are thrilled to partner with IFE Material Handling,” Simon says.
“ is collaboration allows us to enhance our product o ering and deliver even more value to our customers.
“We are eagerly awaiting the chance to discuss requirements and nd tailored solutions that meet the needs of current and prospective IFE customers.”
For more information, email: sales@mpsbulk.com.au
Based on customer demand for high-capacity preshredders, Fornnax has developed the SR-200 HD primary shredder.
More powerful than its predecessor, the standard SR200 model, the SR-200 HD has the highest input capacity model in the SR series.
Primarily designed for tyre shredding, the SR-200 HD can also be used for other applications, including highvolume municipal solid waste, wood pallets, industrial and commercial waste, and more.
The new shredders come with various proven knives developed by Fornnax and a larger shaft centre that provides more discharge space to process bulky and high-thickness materials.
The slow-speed shafts, which produce up to 2,000,00 Nm (newton meter) of torque, allow the SR200HD to work with the most challenging materials. This, along with quick shafts change system, enables the end user to switch from working in one application to another.
There are different variants available for different market standards. The SR-200 HD with a trommel screen provides output sizes of 60-80 millimetres.
Without a screen the SR-200 HD produces single pass rough shreds at 400 millimetres.
The new HD model offers low cost-per-ton with high reliability, ease of operation, and flexibility.
The IFE Eddy Current Separator is the pinnacle of advanced metal separation technology. Designed for efficiency and precision, it is the go-to solution for sorting various metals without the need for manual handling.
The IFE Eddy Current Separator is engineered to separate non-ferrous metals such as aluminium, copper, and brass from other materials with unmatched accuracy.
There is no manual handling required as the system automates the separation process, ensuring a safer and more efficient operation.
Whether recycling, waste management, alternative fuels or material recovery, the IFE Eddy Current Separator adapts to effortlessly handle a wide range of materials.
Capable of processing large volumes at high speeds, it’s suitable for operations requiring both speed and precision and because it is built to last, the IFE Eddy Current Separator requires minimal maintenance, reducing downtime and operating costs.
With a reputation for quality, innovation and reliability, IFE stands at the forefront of separation technology. The IFE Eddy Current Separator embodies a commitment to delivering robust, reliable, and efficient solutions tailored to meet the demands of varied applications.
The TANA Shark is designed for challenging waste streams, making light work of a variety of materials including tyres, commercial and industrial, construction and demolition, solid recovered fuel (SRF), plastics, mattresses and ragger wire.
Just one TANA Shark does the work of three machines, eliminating the need for separate preshredder, primary shredder and screen.
TANA SHARK enables full control over the particle size from 50 to 500 millimetres. Because it performs shredding in just one pass it results in time and cost savings.
Adding or removing screens takes just 10 minutes. Screen sizes are available from 50 millimetres through to 275 millimetres.
The TANA Control System (TCS) monitors and controls the machine functions and comes with 12 preprogrammed operations for varying materials.
Extra customer-specified programs can also be added to achieve optimal operating level and the desired output. For instance, overcharge pressure limits, rotor revs per minute and conveyor speed can be adjusted.
Peterson D-series grinders, designed for recycling waste and green wood material, offer industry-leading features to produce quality product at the lowest cost per ton with a range of five models to meet market demands.
The 5710D horizontal grinder is a tracked horizontal grinder designed for high-volume producers with demanding end-product specification.
Powered by Caterpillar C27 Tier II 772kW engine (with an optional C32 838kW engine), the 5710D provides the highest power to weight ratio of any Peterson grinder. At 43,091 kilograms it’s suited for operations requiring high production and frequent moves between jobs. With a feed opening of 152 centimetres x 102 centimetres, combined with Peterson’s high lift feed roll, it can readily produce a wide range of material.
Unique features include a three-stage grinding process that provides better fracturing of material and a more consistent product.
Peterson’s patented Impact Release System’s air bags provide uniform grinding and protection from contaminated feedstock, a feature unique to Peterson grinders.
The Impact Cushion System Urethane cushions and shear pins help protect the mill from catastrophic damage
in the event of a severe impact from contaminants in the feed stock.
Combined, the features allow the Peterson horizontal grinders to be more productive since less energy is required to reduce the feed material.
The difference in profitability at the end of the year can be dramatic with lower fuel consumption, and higher mulch yield.
Faced with the evolving complexities of modern waste streams, the waste industry is not just addressing challenges, but turning them into opportunities. Brett Lemin, Executive Director Waste Contractors & Recyclers Association NSW, explains.
The waste and recycling sector in New South Wales is on the cusp of transformative change. Environmental and human health concerns are taking centre stage, and the sector is responding with a focus on enhancing resource recovery, fostering collaboration among stakeholders, and mitigating risks.
Here is just a snapshot of some of the issues Waste Contractors and Recyclers Association of NSW is focusing on:
e O ce of the Chief Scientist and Engineer’s (OSCE) research into asbestos risks within the sector and the broader circular economy is a game-changer. is research is not only evaluating the safe management of asbestos contamination, but also setting the stage for establishing new standards and advancing regulatory frameworks.
By exploring the integration of risk-based regulation into the resource recovery processes, we are paving the way for more e ective risk management strategies that will bene t both public health and the circular economy.
WCRA recognises that this is an extraordinary opportunity for industry and has committed to working closely with the OCSE and other stakeholders. WCRA invited OCSE on guided tours of various facilities, showcasing an array of material types and processing facilities. Our e orts extend beyond construction and demolition to include organics and residential waste streams.
ese tours highlighted the practical challenges that our industry faces with contaminants of concern. Despite bans on blue asbestos in 1967, brown asbestos
in 1985, and a complete ban on all forms by 2003, asbestos remains a signi cant contaminant in the industry and broader environment.
OSCE’s research is crucial to providing an independent, risk-based approach to managing this legacy contaminant.
e ndings will undoubtedly set new benchmarks for safety and resource recovery, helping us create a cleaner, safer environment for future generations.
Equally important is the growing challenge of battery res – an increasingly common and dangerous occurrence in the industry. e rise of lithium-ion batteries in consumer electronics, electric vehicles, and renewable energy storage has brought with it an increased risk of res due to improper disposal. With more than 10,000 battery res occurring annually, the urgency to address this issue cannot be overstated.
WCRA has been at the forefront, bringing regulators and industry stakeholders together, calling for swift government intervention and support in developing strategies to prevent and
manage battery res. While some states are moving quickly to forge a path forward, the national approach is crucial. Fire Rescue NSW deserves recognition for leading the charge with its safety of alternative and renewable energy technologies program. Its expertise and proactive stance have been invaluable in raising awareness, working closely with waste management companies, recyclers, and government agencies to protect people and environment.
In an ongoing quest for safety excellence, WCRA’s annual Safety Summit has become a cornerstone event in the sector. Expert-led discussions at the most recent summit in August 2024 covered a range of concerns, from workplace accident prevention, overhead wires right through to arti cial intelligence (AI) integration.
e summit also serves as a crucial networking platform, fostering collaboration and knowledge-sharing that strengthens individual organisations and contributes to the broader goal of creating a safer, more resilient industry.
As New South Wales navigates the contemporary and emerging complexities of waste management, we are poised to make signi cant strides toward a more sustainable future.
e research into asbestos risks, e orts to address battery res, and the empowering initiatives from WCRA’s Safety Summit exemplify our proactive approach to current and emerging challenges. ese initiatives highlight the importance of collaboration, innovation, and resilience in our sector.
• The ATMOS Cover ADC is a non-hardening protein-based foam that adapts to your needs with adjustable dilution ratios and coverage depth.
• Quick and easy to deploy, even in large areas, compared to traditional cover methods.
• Maximises airspace with effective and superior coverage that protects and extends your landfill’s lifespan.