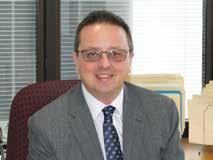
7 minute read
THE NEXT GENERATION
Next generation
AORA’S NEW EXECUTIVE OFFICER PETER OLAH SPEAKS WITH WASTE MANAGEMENT REVIEW ABOUT THE ASSOCIATION’S PLANS TO SUPPORT AND
STRENGTHEN THE AUSTRALIAN ORGANICS INDUSTRY. T he organics industry is in interesting times. While awareness over the importance of sustainable organics management has never been higher, compliance costs, regulatory changes and disrupted end markets are causing problems for small and medium enterprises.
How to effectively manage and process food waste is gaining traction though, with Infrastructure Victoria’s Recycling and Resource Recovery Infrastructure Evidence Base Report suggesting consistent approaches to FOGO are critical to achieving greater overall resource recovery rates.
Though this is likely welcome news to the Victorian arm of the organics sector, across the border in NSW, the situation is murkier.
In October, the NSW EPA reaffirmed its 2018 Mixed Waste Organics Output decision, stating the authority had no intention of amending its revocation of the material’s resource recovery exemption order.
For Peter Olah, the Australian Organics Recycling Association’s (AORA) new Executive Officer, the organics industry’s current challenges present an opportunity for growth.
“While I’m entering my new role at AORA in a challenging time for not just the organics industry, but the recycling industry at large, I’m excited to face those challenges head on and support the organics industry as it advances,” Peter says.
Peter, who currently serves as the Surveying and Spatial Sciences Institute’s Chief Executive Officer, has an extensive background in politics and public administration.
He previously worked on the private staff of a NSW Premier, and served as a Policy Advisor to Ministers for Justice and Police.
Furthermore, Peter served as a Hurstville City Council Councillor in Sydney for 12 years, including three terms as Hurstville Mayor and three as Deputy Mayor.
“I also worked with NSW State Transit for seven years, fulfilling a number of management functions for the organisation’s board and CEO, including projects in government and customer relations, public affairs, industrial advocacy, internal communications and cost efficiency,” he says.
Drawing on this leadership experience, Peter intends to help AORA deliver the objectives laid out in its 2019-2022 National Strategy.
“The strategy’s mission statement is to work with stakeholders to facilitate the conditions through which surplus organic material can be sustainably and cost-effectively recycled.” Peter says.
“Furthermore, we intent to promote the beneficial use of compost and mulches in primary industries.”
In addition to the overall mission, Peter says AORA have three key objectives, including strengthening AORA as the peak body for the organics recycling industry and championing a pathway to optimise closed loop organics recycling. Additionally, he says, AORA intends to establish and participate in knowledge hubs for recycled organics research, development, extension and communication.
“I will use my experience in stakeholder management and knowledge of political processes to ensure our member’s voices are heard and continue the advocacy and industry support role of AORA,” he says.
“As the central body for organics in Australia, I also intend to ensure the sustainable growth of the association.”
To achieve this, Peter says he will take time to speak with members about their concerns and ensure those concerns are further discussed with the AORA board.
One of AORA’s next steps, he says, is collaborating with members to establish standards and best practice certifications programs.
“AORA’s members are leaders in the organics space, and drawing on their expertise, I hope to use my position to identify, communicate and celebrate best practice strategies, technologies, performance and products,” he says.
“By working together, AORA can help create an environment where the work of individuals and organisations in the organics industry leads the way to a more sustainable Australian future.” AORA’s new Executive Officer Peter Olah is ready to work with industry.
1300 048 447 | info@iugis.com
A versatile shred
PETERSON’S 1700D IS PROVING TO OFFER VERSATILE CAPABILITIES FOR ORGANICS AND SCRAP WOOD, AIMING TO PRODUCE A CONSISTENT PRODUCT AT A REDUCED COST.
As with most technological iterations, making products lighter and smaller while still maintaining maximum performance is an advancement that comes with time and continuous refinement.
Wood grinding and chipping original equipment manufacturer (OEM) Peterson has adopted this vision into its ethos as a company, ensuring its new 1700D carries each of these three features.
The machine was released in April to meet the demand of high-value organics from predominate export markets in Europe and Australia and is available through Australian supplier Komatsu Forest Proprietary Limited.
According to Peterson, operators
The 1700D is ideal for operators both small and large and able to process a range of materials.

have traditionally focused on being the most powerful in their class, but OEMs needed to differentiate and eventually moved into offering better maintenance and versatility.
Taking versatility to new heights, the 1700D is ideal for operators both small and large, processing materials ranging from small mulch, compost or even pallet grinding. Trials earlier this year showed the machine could process more than 100 cubic metres per hour in green waste and 140 cubic metres an hour in scrap wood.
Jody Volner, President of Peterson Pacific Corp says the company is impressed by the capabilities of the remarkable grinder and have loaded it with features Peterson customers have come to expect.
One of these key features is a powerful up-turn and three stage grinding process that works to provide a better fracturing of material and a more consistent product.
Once the feed material has been fractured, Peterson horizontal grinders have a range of tooling options from grates in hex, round, square and rectangle openings. The four-piece grate system allows users to mix and match to achieve a desired product in the pre-grind and grind stage.
The Adaptive Feed System helps with consistent productivity by maintaining near constant material flow to the grind chamber.
The machine’s large feed opening allows it to measure by 54 to 27 inches. When boosted by machine’s
high-lift feed roll, the feed opening’s maximum lift of 41.5 inches can tackle large feedstock and allows accessibility to the rotor for maintenance.
The 1700D horizontal grinder is equipped with a Caterpillar Tier IV C9.3 455 horsepower engine or an optional export-only C9 Tier III, 350 horsepower engine. It is the lightest of Peterson’s grinder series and is easily transportable.
Added to the machine’s versatility is a quick-change multiple grate system which streamlines customised grate configurations. Grates are removed through an easy-access door on the side wall.
Peterson’s Adaptive Control System also features a fully adjustable feed system. It includes a large display that provides the operator with full engine and system parameters to offer a simple set-up and efficient operations.
To protect against deleterious materials, Peterson also features a patented Impact Release System. Likewise, additional protection of the machine itself is offered through a patented up-turn rotor, heavy duty parts and a robust anvil for long wear life and product sizing.
As a secondary line of defence, the OEM offers an Impact Cushion System that utilises urethrane cushions while shear pins help protect the mill from damage from contaminants in the feedstock.
In keeping with the fast pace of technological evolution, Peterson offers a remote monitoring solution to provide machine operators access to real-time and historical data of their machine’s performance and location.
Michael Spreadbury, Peterson Marketing Manager, says Peterson+ is a unique communication network and information system connecting Peterson machines, customers and dealers with cloud-based machine monitoring, diagnostics and information systems.
“The system will help improve customer profitability through higher machine utilisation, productivity and increased uptime,” Michael says.
Peterson+ equipped machines such as its 3310 drum chipper and 4710D horizontal grinder provide streamlined data, including a GPS locator. Users can gain live access to the machine’s on-board display and operating information on their office computer, laptop or mobile phone.
Statistical data can be used to track key information such as fuel consumption, engine revolutions per minute and oil temperatures, providing operators with better efficiencies and therefore cost savings.
The wireless display feature uses a local area network to allow machine operators to use their smartphone as a wireless display mounted in an excavator, loader or control booth. According to the company, Peterson+ is akin to having a technician on-site working through a potential problem.
The Peterson portal also allows machine documentation, parts information and supports services to be easily accessible through its website.
Peterson’s versatile nature is supported by a full line of horizontal grinders from 580 to 1200 horsepower in diesel and electric applications to suit varied grinding needs.
Its grinders are available in wheeled, tracked or fixed stationary applications, depending on the needs of the site.
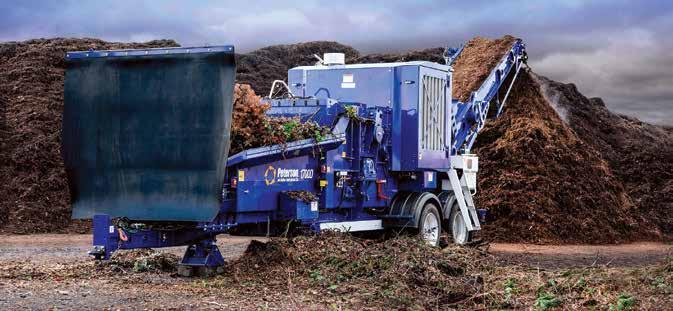