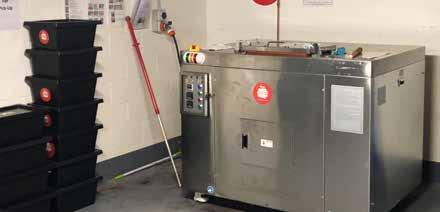
5 minute read
BACK TO THE LAND
Giving back to the land
BRISBANE AIRPORT HAS INSTALLED AN ENRICH360 DEHYDRATOR AT ITS SKYGATE PRECINCT, ENABLING IT TO REACH ITS LANDFILL DIVERSION
TARGETS AND MOVE TOWARDS A CIRCULAR ECONOMY. L ast year’s announcement of the waste levy in Queensland created a new business case for Brisbane Airport.
With the levy stimulating additional demand for resource recovery solutions, Brisbane Airport began to look at diverting some of its most prominent waste streams.
Having previously conducted audits into its incoming tonnages, the airport knew food waste was its second biggest input after glass. Moreover, the airport has a target to divert 80 per cent of its total waste from landfill by 2030, with food waste emerging as the low hanging fruit.
Andrew Masci, Environment & Sustainability Adviser, says the airport decided to investigate and identify a suitable food waste service. He says that this was its first foray into nonstandard commingled recycled, with the airport also participating in the QLD Government Container Refund Scheme.
In a six-month investigation process, enrich360 emerged as the most suitable choice, with its food dehydrator arriving in February this year and timing well with the levy’s 1 July start date.
Launched in late 2017, enrich360’s program uses a dehydrator to condense food waste into recycled water and biomass that can be utilised as fertiliser or as part of compost. The model is established on a closed loop system where restaurants and food service businesses across the country convert their food waste into rich organic fertiliser to give back to farmers and grow better, more nutritious produce.
The benefits lead to more resources being recovered while replenishing globally scarce nutrients and improving Australia’s low food waste recovery rate. The process works to reduce the volume of food waste by up to 93 per cent and create a sterile and pathogenfree material. In a closed loop reverse logistics process, logistics partner In2food picks up the materials during their usual drop-off route and delivers them to farms.
Brisbane Airport’s Skygate Precinct was chosen as the ideal location for a trial of the dehydrator as it was not too busy and included a range of food outlets in the area.
Enrich360’s suitability centred on Brisbane Airport’s desire to ensure its food waste would always find a home, ensuring it did not go to landfill when the airport didn’t have an end-to-end solution.
“Brisbane Airport is transitioning to a circular economy and that is why enrich360 grabbed our attention. There were different dehydrators in the market, but none offered the full service,” Andrew says.
“It took three months to kick off with a few teething issues, but now we are getting amazing results.”
The results speak for themselves, with enrich360 diverting 5500 kilograms of food waste since commencing its trial in February.
Andrew says that around 11 retailers have so far participated in the program. He say the dehydrator is able to detect whether it is overfilled and unfilled. Depending on moisture content, it takes roughly 10 to 12 hours to produce the biomass.
He says that participating retailers Enrich360 is getting buy-in from a range of businesses, including retail, restaurants, food outlets and universities.
will soon be able to take part in a certification scheme that will allow them to showcase their involvement in the program to their customers. The scheme requires partners to demonstrate compliance to the organisation’s program to be granted an enrich360 certification mark.
As an added benefit, Andrew says that Brisbane Airport is also testing whether single-use compostable items could break down in the machine and support the maturation process.
“What I like about the machine is it takes a lot of different varieties of food waste, including chicken bones. There is very little it can’t handle,” Andrew says.
To ensure the system is commercially viable for operators, enrich360 provides purchase, rent and rent-to-own options – enabling businesses to dehydrate food waste on site and have it collected for farms or off-site composting.
The airport is now looking to expand its programs to the main terminals: a challenging, but ambitious next step.
Dean Turner, enrich360 CEO, says with issues of climate change sweeping through the headlines, the system has never been more timely. He says enrich360 is now getting buy-in from a range of businesses, including retail, restaurants, food outlets and universities.
“One of the interesting things in talking to our other global partners who sell this equipment is it was developed eight years ago, and what we’re feeling is it was eight years to early. Now is the time when people are ready for this technology,” Dean says.
“Certainly we found visitors at the Waste Expo were visiting our stand in droves. Almost everyone wanted to talk about their situation, from manufacturing plant operators right through to large-scale primary producers.”
He adds that primary producers, for example, tend to have massive volumes with high water content and the dehydrator can create a water source and dry output slow-release fertiliser.
“When you dehydrate the food waste, you get a green standard recycled water that can be used for all sorts of end uses, including irrigation.”
Dean says the company is now setting its sights on moving into hospitals and the aged care sector.
“An aged care facility can use the water and fertiliser each day across their grounds, creating a circular economy within their own premises,” he says.
In future, he hopes demand for the outputs will be so high that it creates a commodity that end users are prepared to purchase from the generator.
Detect and protect with NHP’s Integrated Condition Monitoring solutions
With a Smart Motor Control system and the help of our condition monitoring products, NHP and Rockwell Automation help you keep your plant floor running by detecting potential mechanical issues before they impact production. A Smart Condition Monitoring solution detects vibrations related to specific motor issues allowing you to schedule proactive maintenance. This involves the capability to not only capture the information but also the expertise to set limits and alarms specific to your machinery.


For more information on our real-time protection modules, sensors, surveillance software and portable instruments call NHP today.
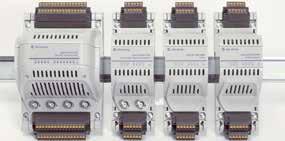