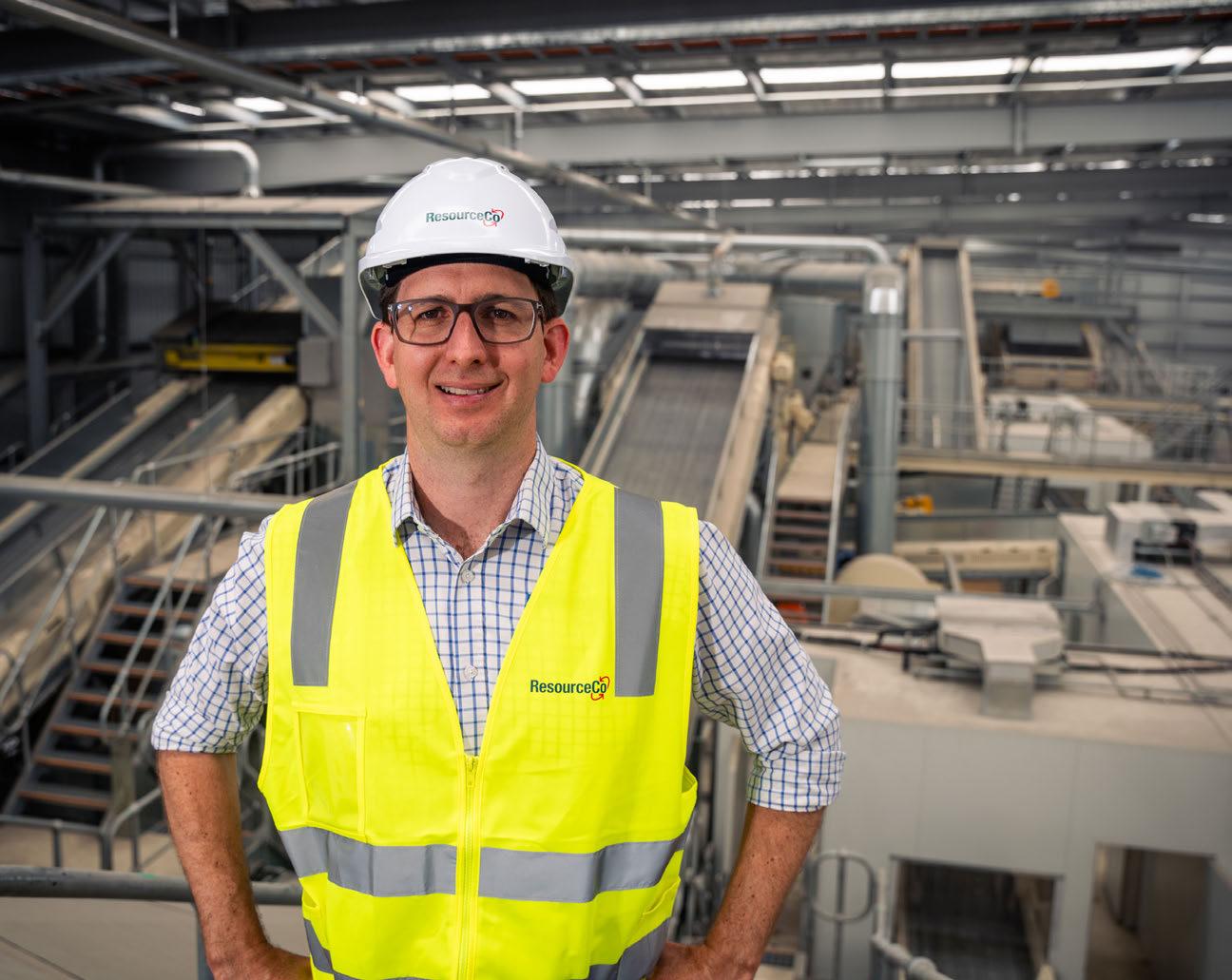

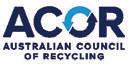
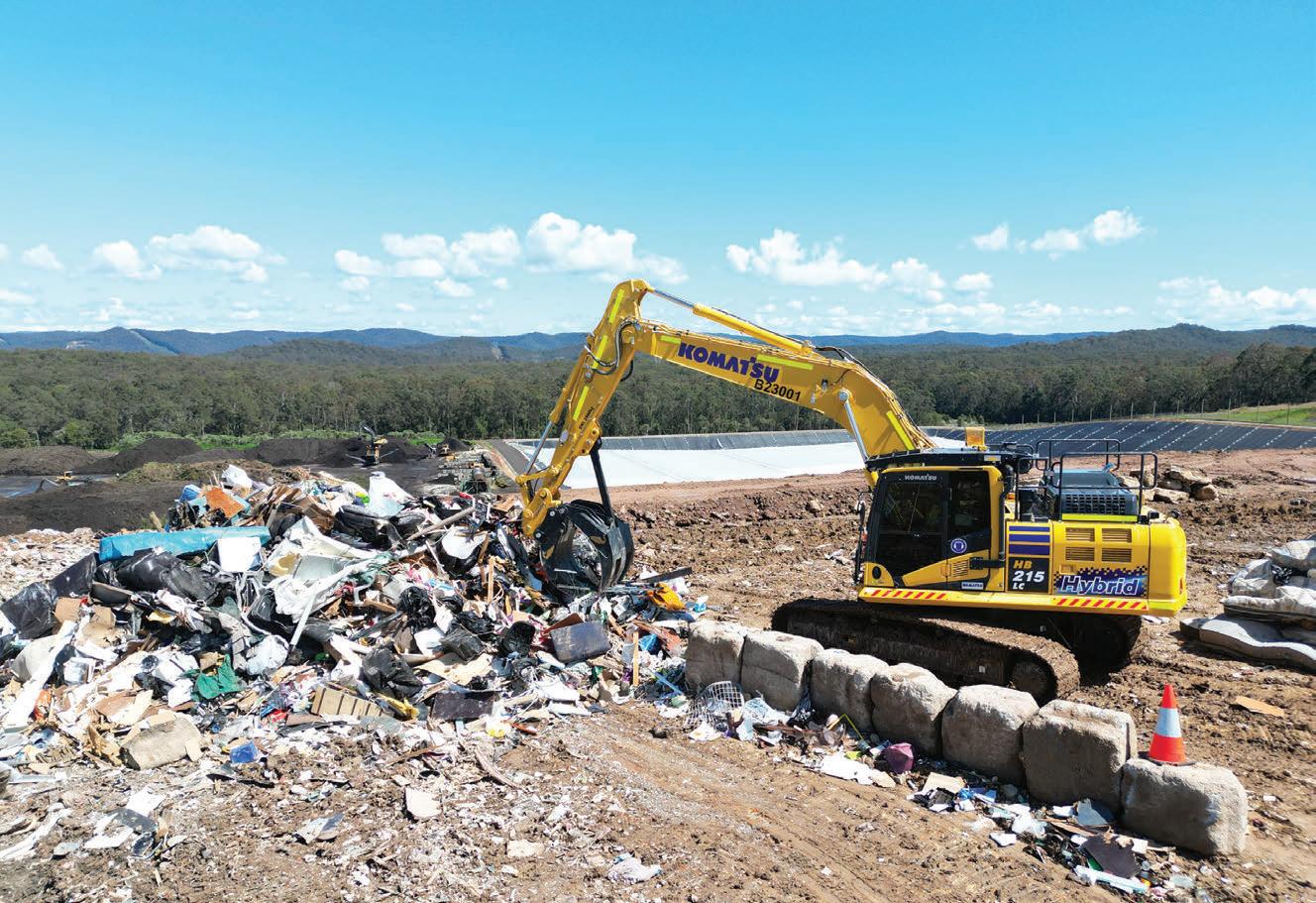
The waste processing industry demands specialised equipment capable of handling a wide range of challenging materials. Komatsu designs excavators and solutions tailored to the tough environments and conditions found in waste management. Our advanced excavators, are engineered to maximise efficiency while supporting your commitment to a zero-harm workplace.
Australia’s rst Incinerator Bottom Ash processing facility is up and running, rewriting the way the nation treats waste.
ResourceCo cements its expansion into Queensland.
Waste
We ask industry leaders for one key takeaway from this year’s Waste Expo.
Helping Australia safely dispose of dangerous
Inside Pure Environmental’s latest acquisition.
New company pools talents of industry experts.
Cleanaway
New
Helping South East Queensland maximise FOGO.
Re ections of AORA’s scholarship recipient.
Windsifting technology in a small, mobile machine.
An engineered solution to keep facilities safe from res.
Australia’s rst Incinerator Bottom Ash plant is up and running.
Why circular precincts have the potential to unlock value for the industry.
New tool revolutionises project planning.
“WE’VE MADE A COMMITMENT TO BE A FIRST MOVER TO HELP DRIVE CHANGE AND THE STATE’S SUSTAINABILITY ASPIRATIONS.”
Henry Anning, Chief Executive Officer, ResourceCo Energy
Bringing the next generation of waste vehicles online.
TAKING IT TO THE J-MAX
Byrne Trailers launches a new walking oor trailer.
WITH FEATURES
Komatsu’s WA475-10 Wheel Loader is a proven fuel-e cient performer.
LiuGong expands into recycling.
Deep dive into Waste Expo Australia.
Inside the Waste Innovation and Recycling Awards.
Time appears to move so quickly, and just like that, another year has passed.
Upon re ection, 2024 has thrown up some challenges – battery res have escalated, we’re no closer to solving diminishing land ll capacity, and a lack of harmonisation on waste collection and processes across the country continues to cause confusion.
But as we close out another year, the waste, recycling and resource recovery industry has much to be proud of.
e industry has shown its willingness to take risks and think outside the box in the hope of delivering better outcomes. Millions of dollars have been poured into new infrastructure across Australia, all aimed at reducing a reliance on nite materials and our carbon footprint.
ResourceCo has long been at the forefront of resource recovery, and it continues to be a rst mover.
In this edition’s cover story, we get a closer look at the company’s newly commissioned alternative fuel plant in Hemmant, Queensland. e solo project is set to play a crucial role in reducing waste and promoting recycling in the region.
Also set to play a crucial role in the way Australia treats its waste is the nation’s rst Incinerator Bottom Ash plant. After many years of tireless work, Ian Lynass has nally seen his vision become a reality, o cially opening the plant in October. We talk with Ian as he absorbs the enormity of what Blue Phoenix Australia has achieved.
As organics recycling targets edge closer, we examine the advancements being made in South East Queensland and New South Wales, review new technology and nd out why introducing the next generation to the industry is so important.
And we salute some of the sector’s brightest minds, bringing you full coverage of the 2024 Waste Innovation and Recycling Awards. e innovations, talent and dedication of all nalists and winners is proof the industry is in good hands and I can’t wait to see what 2025 brings.
On behalf of the Waste Management Review team, we wish you all a happy holiday season.
Happy reading!
Lisa Korycki
CHIEF OPERATING OFFICER
Christine Clancy christine.clancy@primecreative.com.au
PUBLISHER
Sarah Baker sarah.baker@primecreative.com.au
MANAGING EDITOR
Lisa Korycki lisa.korycki@primecreative.com.au
JOURNALIST
Jennifer Pittorino jennifer.pittorino@primecreative.com.au
HEAD OF DESIGN
Blake Storey blake.storey@primecreative.com.au
DESIGN
Laura Drinkwater
BRAND MANAGER
Chelsea Daniel chelsea.daniel@primecreative.com.au p: +61 425 699 878
CLIENT SUCCESS MANAGER
Justine Nardone justine.nardone@primecreative.com.au
HEAD OFFICE
Prime Creative Pty Ltd
379 Docklands Drive Docklands VIC 3008 Australia P: +61 3 9690 8766 enquiries@primecreative.com.au www.wastemanagementreview.com.au
SUBSCRIPTIONS
+61 3 9690 8766 subscriptions@primecreative.com.au
Waste Management Review is available by subscription from the publisher. e rights of refusal are reserved by the publisher
ARTICLES
All articles submitted for publication become the property of the publisher. e Editor reserves the right to adjust any article to conform with the magazine format.
COVER
Cover image: Henry Anning, Chief Executive O cer of ResourceCo’s Energy division. (ResourceCo)
COPYRIGHT
Waste Management Review is owned by Prime Creative Media and published by John Murphy.
All material in Waste Management Review is copyright and no part may be reproduced or copied in any form or by any means (graphic, electronic or mechanical including information and retrieval systems) without written permission of the publisher. e Editor welcomes contributions but reserves the right to accept or reject any material. While every e ort has been made to ensure the accuracy of information, Prime Creative Media will not accept responsibility for errors or omissions or for any consequences arising from reliance on information published. e opinions expressed in Waste Management Review are not necessarily the opinions of, or endorsed by the publisher unless otherwise stated.
With its multi-rotor design the Genox J-series pipe shredder easily shreds HDPE pipes of all sizes.
When combined with a Genox washing plant and Genox pelletising system, you can truly close the loop on HDPE pipes. Pipe to pellets. Pellets to pipe. This is the circular economy in action.
Genox make world-class recycling solutions, for real-world recycling applications.
Waste Expo Australia brought together industry leaders ready to discuss all things waste, including one panel on plastics and policy.
Iwas told 12 years ago that the Container Deposit Scheme (CDS) would never happen, that it was too expensive, and people wouldn’t use it,” said Toby Hutcheon, Campaign Manager at Boomerang Alliance.
“Witnessing its success now convinces us that’s exactly the right process that we need to apply to plastics and packaging going forward.”
Hutcheon was one of four industry leaders who provided insight into the country’s plastic problem, including policy, reuse and recycling, during a panel session at Waste Expo Australia.
He was joined by Peter Kinrade, Associate Director at Marsden Jacob Associates, Chris Smith, Territory Manager Victoria at Replas, and Steve Morriss, Head of Circularity at Close e Loop.
When talking policy, Hutcheon said unity across the country is needed.
“We need the Commonwealth Government, with the public support of every single state and territory government, to say we want products and materials managed to their highest resource value,” he said.
“It means that every single problematic product is subjected to a circular economy approach, whereby it is managed through its entire life cycle according to the highest resource value.
“Recycling is part of that, but it’s only one of the options that we will see in the future.”
e panel dove into the shift from single-use plastics towards reusable alternatives, discussing the necessary government policies and business practices to support this change.
Morriss said product stewardship in the packaging space needs to become mandated to encourage all brands to be a part of it.
“It’s the most important thing we can do,” he said. “All the brands will be a part of it as long as everyone’s involved.”
Kinrade addressed the development of markets for recycled soft plastics and the importance of circular contracts in ensuring that what is recycled is also purchased and reused.
“We are currently a long way from eliminating single use plastics, despite the ministers agreeing last year on a nationally consistent approach,” he said.
“ ere is currently a lot of inconsistency across Australia and across jurisdictions when it comes to single use plastic.”
He said these inconsistencies vary from dealing with co ee cups through to heavyweight plastic bags.
“When it comes to working out what we can do about eliminating those, I believe there needs to be a strong focus on harmonisation and consistency,” he said. “At the moment, there are some great programs happening at a local level, but we need to look at a nationally coordinated approach.”
Smith discussed the overall challenges of plastic recycling. He said
contamination was a major problem.
“At Replas we have had experience with mixed soft plastics and contamination,” he said. “ e more layers and more lms in the packaging, the harder it is for places like Replas and manufacturers to utilise that e ectively.
“In the past three to ve years I have noticed a policy shift towards procurement policies, and I think that’s where we need to continue to head.”
e panel also spoke about following in the footsteps of European countries to expel single use plastics.
“ e recent Paris Olympics gifted every spectator with a reusable cup and a reusable container,” Hutcheon said.
“Germans have brought in a rule where every takeaway food outlet also must provide a reusable cup to their customers if they want it. is has shown people they have a choice.
“We need to start to put those things in place so that we start to change our behaviour.”
The Breakdown is a monthly column giving industry leaders and decision makers a chance to share their views on topics central to the sector.
This month we asked: “How important are events like Waste Expo Australia and what is one key takeaway you have from this year’s event?”
Lacey Webb Founder and Director, Resource Hub
This year there is a real focus on embracing new technologies and diving into change.
We’re seeing the same faces that we often see at expos around Australia but we’re also seeing them delivering new technology outcomes, really embracing artificial intelligence (AI) and starting to move into a world where they are talking about how we can integrate with each other. It’s almost like our technology is supporting collaboration.
Matt Genever Chief Executive Officer, Sustainability Victoria
These events are incredibly important.
We know we’ve got a diverse industry and people are bringing lots of different angles to it, so it’s great when we can come together and have active discussions about the opportunities that are ahead in the circular economy.
The key takeaway for me is that right now is the time to start the conversation about consumption.
We’re putting so much energy and investment into our recycling sector, and we are hearing a lot today about the innovations and investment, but looking at the trajectory – which suggests 33 million tonnes of waste in Victoria by 2050 – that’s completely unacceptable.
We have to start a conversation about consumption. The time is now to start thinking beyond recycling.
Sales, Focus Enviro
These events are vital to catching up with new and existing customers so we can bring them together.
We should never underestimate the value of discussion and face-to-face meetings.
If you or someone at your organisation is an industry leader and would like to be a part of this monthly column in 2025, please get in touch with Editor, Lisa Korycki lisa.korycki@primecreative.com.au
ResourceCo is set to make a positive impact on Queensland’s resource recovery industry.
ResourceCo has cemented its expansion into Queensland with its latest resource recovery facility capable of saving more than 250,000 tonnes of residual material from being sent to land ll every year.
e $70 million alternative fuel plant in Hemmant, an eastern industrial suburb of Brisbane, is the rst facility of its type in Queensland, and builds on ResourceCo’s growing national footprint of resource recovery operations.
e plant provides a signi cant opportunity for land ll diversion and emissions reduction as part of its production of Process Engineered Fuel
(PEF), which is used to replace coal in high energy industrial applications, such as cement kilns, both in Australia and globally.
In addition to extracting materials such as metals, heavy recyclables including rock, brick and concrete, the facility has capacity to manufacture about 150,000 tonnes of PEF each year, with an overall land ll diversion rate of 95 per cent.
Henry Anning, Chief Executive O cer of ResourceCo’s Energy division, says the plant will play a crucial role in reducing waste sent to land ll and promoting recycling in the region.
“Queensland is a market with a lot of opportunity in terms of its recycling rate, which means there’s opportunity to capture tonnes of materials and divert them from land ll,” he says.
“Waste policy in Queensland has also evolved signi cantly in the past ve years following the introduction of a waste levy and the State Government’s Waste Strategy 2050.
“We’ve made a commitment to be a rst mover to help drive change and the state’s sustainability aspirations.”
e Queensland Waste Management and Resource Recovery Strategy sets ambitious targets to increase
diversion of waste from land ll and increase recycling.
A 10-year roadmap and action plan provide a framework to accelerate this transition. is is also set to be an important contributor to the national waste diversion target of 80 per cent by 2030.
To achieve this, the State Government has committed to supporting capital investment that increases the region’s recycling rates.
ResourceCo has invested more than $70 million, including a government grant under the state’s Resource Recovery Industry Development Program, to develop the resource recovery plant to service South East Queensland.
All incoming materials will be dry, non-putrescible material from waste businesses or generators, council sites, and commercial waste facilities.
“We recognise the embodied energy in all materials, recovering that energy wherever possible is our priority. Now, for the rst time, Queensland has a facility that can provide a higher order solution in terms of the waste hierarchy,” Henry says.
“PEF’s ability to harness the energy value of material currently being wasted in land ll sites is unrivalled.
“Aside from the obvious environmental bene ts of less material being sent to land ll, less methane and less fossil fuels consumed by our o take partners, we’re also helping to extend the life of existing land lls, reserving that important airspace for the critical materials that genuinely have no other reuse or recycling solution.
“ e outputs of this facility deliver signi cant reductions in carbon emissions – every tonne of waste diverted from land ll saves about one tonne of carbon and every tonne of PEF consumed instead of fossil fuels saves about one tonne of carbon as well – two bangs for your buck.”
PEF is a ready-to-use alternative fuel source, generated from select dry commercial, industrial, mixed construction and demolition materials.
e right mix possesses signi cant calori c value and can be used as a fuel substitute for coal and gas in high combustion facilities.
e ResourceCo Group believes alternative sources of energy to fossil fuels are integral to maintaining a sustainable environment.
e company’s renewable energy biomass fuel sources are used across Asia and Australia, helping to conserve natural resources, reduce
land ll and reduce greenhouse gas emissions.
e company is an international leader in resource recovery and alternative fuels, manufacturing PEF from various sites.
In South Australia, the current Veolia – ResourceCo partnership enables the production of PEF to supply alternative fuels to AdBri.
is plant, the rst of its type in Australia when it was opened in 2006, sorts the entire raw material stream into its various components, with more than 90 per cent of the material recovered.
With similar operations with another joint venture partner in New South Wales, ResourceCo’s new Queensland facility is the rst of this type fully owned by ResourceCo.
“It’s a major step in our market and a major step for ResourceCo,” Henry says. ResourceCo worked with Australianbased manufacturer and integrator Ogtec to design and deliver the Queensland plant.
It includes a range of screens, shredders, optical sorters and ballastic separators designed to separate material for recycling and produce a fuel to speci cations.
e facility was commissioned in October and Henry says the response has been positive.
“ResourceCo has national waste clients who have been crying out for a land ll diversion solution like this in South East Queensland,” he says.
“We’ve also had good support and momentum from the State Government which is very proactive in getting things done to deliver opportunities like this in Queensland.
“From an employment perspective, the facility will bring additional job opportunities to the region, so it’s not just the environment that bene ts from recycling, the economy does too. It’s widely reported that for every 10,000 tonnes of material diverted from land ll into the resource
recovery sector, there’s a three-fold employment bene t.”
More than seven years in development, the facility is a substantial investment in the state. Henry says ResourceCo takes a long-term view of the sector and is excited about the future of operations in Queensland.
“South East Queensland is forecast for major population growth over the next 10 years,” Henry says. “With an already lower recycling rate compared to other states, population growth and the 2032 Olympics adding a little bit of extra boost, there are a lot of opportunities.
“ResourceCo had the vision and commitment to make a call and follow it through.
“By leveraging our expertise in commercial and industrial, as well as construction and demolition waste recycling, we are poised to make a substantial impact on Queensland’s environmental sustainability.”
ResourceCo has operations in every Australian state and aims to deliver multiple resource recovery facilities
around east coast capital cities. Henry describes it as building an ecosystem of sustainability and believes ResourceCo has the experience, scale and strong relationships with o take partners to have con dence in investing in the sector.
“We could build many more of this type of facility around Australia if the economics and policy settings are right,” he says. “ ere is 15 million tonnes of construction and demolition and commercial and industrial waste still going to land ll. Even if half or a third of this still went to land ll we could divert millions of tonnes of this waste and save millions of tonnes of emissions from the land lls and energy users.
“It would also drive hundreds, if not thousands of jobs, just with this type of plant. at’s something that often gets lost in conversation, this type of investment is an economic and social opportunity.”
For more information, visit: www.resourceco.com.au
The IFE AEROSELECTOR is a turnkey solution for removing contaminants from matured compost. Trusted by leading European compost processors, it excels in removal of ferrous metals, plastic foils, stones, and structural materials, ensuring a superior composting process.
Key Benefits
• Innovative Technology: Combines Wind Sifting, Ballistic Separation, and Screening
• High Throughput Capacity: Compact design for enhanced performance
• Unmatched Efficiency: Reduces operational costs while increasing productivity
• Top-Quality Output: Produces fine compost that surpasses industry standards
Transform your composting process with the IFE AEROSELECTOR. Get cleaner, higher quality compost which exceeds industry standards.
Perth chemical engineer Reece Russell is in his element helping Australia safely dispose of dangerous goods.
Radiation, explosives, sulphur hexa uoride – they can send tremors through organisations that don’t have an appetite for risk.
But risk is Reece Russell’s bread and butter. e Director of Perth Chemical Specialists gets a sense of accomplishment from identifying everything from chemicals dumped in the bush to a blue liquid found in a discarded soft drink bottle.
Reece has assembled a team of experienced chemists, environmental and waste experts to handle “all the unusual situations” that arise in the waste industry.
“You’d be amazed at what people put in containers,” Reece says. “Every week we come across every combination of container with every combination of chemical.
“It’s scary. If you put a bright coloured liquid in a soft drink bottle a child will think it’s a drink. We are set up to identify that liquid so it can be labelled, packaged and transported properly so no one is put in danger.”
A chemical engineer, Reece has always enjoyed nding solutions. He founded Perth Chemical Specialists two years ago as a service-based business for waste
companies after identifying a gap in the market.
Perth Chemical Specialists has a mobile laboratory, which Reece says is the only one in Western Australia, speci cally designed for unknown chemical identi cation, chemical response, explosives, radiation and sulphur hexa uoride management, as well as hazardous and dangerous goods disposal.
It means the team can respond rapidly to waste incidents, big or small. It currently handles all unknown waste for the Western Australian Local Government Association and was recently awarded a ve-year contract by Western Australia Health Support Services, part of the state’s health department, to dispose of expired medical equipment and COVID test kits.
e company’s niche o erings have also been engaged nationwide, including a pesticide cleanup in Dubbo New South Wales, training waste chemists in Brisbane, and a sulphuric acid cleanup in Darwin in October 2024.
“We o er customised solutions to niche waste problems,” Reece says.
“If someone needs a chemist sent onsite, we have one available. If they need help to manage a bigger job, we can help.
“We really have a lot of technical capability that other companies may not have.”
at technical capability has been highlighted by the development of Blast Breaker – a chemical solution for treating ammonium nitrate emulsion (ANE) waste. (ANE is an oxidising
“Every time we do a job successfully, we’ve helped to achieve a better environmental outcome.”
Reece Russell Director, Perth Chemical Specialists
agent used to manufacture a range of bulk blasting agents).
While there are other solutions available, Blast Breaker is believed to be the rst retail option for ANE waste treatment. It separates a clear and recyclable hydrocarbon layer from the emulsion, leaving a single watery layer of ammonium nitrate that can be recycled into composting operations or other pathways.
It took 18 months to develop but in the past 12 months, more than 60,000 litres of Blast Breaker have been sold.
“Back in the day, you would put ANE in a hole, or a mine site would burn it or blast it,” Reece says. “You can’t detonate waste anymore, so a lot of ANE was going into land ll.
“Just this year, Blast Breaker has avoided more than one million litres of ANE going to land ll or other unsavoury disposal options.”
e solution has earned Perth Chemical Specialists a Western Australian Waste Sorted Award in the small business category. e company has also been shortlisted for an Australian Institute of Management, Small Business Award.
Based in Waikiki, an outer southern suburb of Perth, the company is punching above its weight and the success has spurred Reece on to continue to develop more chemical solutions for waste treatment.
“ ere are a lot of elegant chemical and technical solutions for current waste issues,” he says.
“ ere’s still massive potential and gaps in the waste industry that need to be lled. We’re working on a couple that, if successful, will be industry changing.”
Reece is keen to employ more chemical engineers, believing they have a valuable skillset for managing niche and hazardous waste problems.
He says chemical engineers are taught to look at the whole picture. Something might work in a laboratory beaker, but what happens when you scale it up? What happens if something goes wrong?
“ e engineering skillset is very holistic when solving problems and that’s what we need because for a lot of what we’re doing, there is no playbook.”
But that is also part of the attraction.
“Every time we do a job successfully, we’ve helped to achieve a better environmental outcome,” Reece says.
“We’ve stopped someone getting rid of a something toxic down the drain or into land ll.”
For more information, visit: www.perthchemical.com.au
The acquisition of a key liquid processing facility will expand Pure Environmental’s reach across Australia, growing its efforts to revolutionise how waste is managed and perceived.
Pure Environmental is implementing its brand promise to focus on the sustainable management and disposal of regulated wastes, with the addition of another liquid waste facility to its portfolio in Pilbara, Western Australia. With a strong focus on maximising resource recovery and reducing waste to land ll, Pure Environmental has built a reputation as one of Australia’s leading environmental service providers.
Brad Gornall, General Manager Western Australia, Pure Environmental says the Pilbara facility is a signi cant piece of infrastructure which is required to support the growing need for sustainable disposal solutions for varying industries in the region.
Liquid wastes can include anything from waste oil and industrial wash waters to organic liquids, sludges and contaminated drilling muds.
Brad says the facility will receive and sustainably treat a range of liquid and solid wastes, arising from the resources, mining and export sectors in the Pilbara. e six waste codes include grease traps which cover food waste and water from restaurant drainage systems, septage and human waste, industrial wash waters, heavy saline water and industrial waste residues.
“We provide customised services for materials requiring unique methods to ensure their compliant disposal, and to minimise environmental impact,” Brad says.
“ is facility is capable of processing up to 120,000 tonnes a year of liquid waste.”
Brad says Pure is looking forward to adding the facility to its growing portfolio.
“We purchased the facility from Corps Group who will continue to run the operations for the next six months under our ownership,” he says.
“We will then transition the facility to Pure’s control, allowing us to expand both geographically and through our existing and new customer base.
“Part of Pure Environmental’s focus is to innovate and do things di erently which is why we have invested heavily in
building our technical expertise across the country.”
Pure Environmental has eight existing liquid processing facilities across Perth and Queensland. e Pilbara facility will allow the company to service additional customers in Western Australia.
Brad says improving its customer facing business is also a strong focal point.
“Our existing facilities have been in operation for a number years and our customers have always provided very positive feedback,” he says.
“ ey are all easy access sites, which provide a quick turnaround time for trucks that enter and exit the facilities.”
Brad says Pure Environmental has a reputation for building and maintaining facilities at a high standard and the additional facility will be consistent with what it has achieved across the business.
“We will ensure a good experience for all our customers including safe and e cient turnarounds, utilising high quality infrastructure and facilities that our customers can enjoy,” he says.
“We are really pleased to be able to service the Pilbara region. is facility is another critical asset to let us better service our customers and support Australia’s critical resource sector.”
For more information, visit: www.purenv.com.au
e process 100% of IBA from our partner, Acciona, losing the loop on the Energy-from-Waste sector nd accelerating the circular economy in Australia.
ith our state-of-the-art technology, we prevent he negative impacts of extracting raw materials by ecovering metals from IBA and producing a econdary aggregate for civil construction wor
Blue Phoenix Australia
Mr Ian Lynass, Managing Director
nvironmental protection is at the forefront of our ay-to-day operations. We assure the proper use of ggregates, limiting the impact on the environment.
New hazardous waste services company Evoro pools the talents of industry experts motivated to make a difference.
Evoro’s name might be new in the hazardous and liquid waste space, but the company has more than 20 years industry experience behind it, led by new Chief Executive O cer Susie McBurney.
A stalwart of the industry, with notable stints at both Cleanaway and REMONDIS Australia, Susie has taken on the role at Evoro, intent on driving the company forward.
Announcing her move, Susie says she is keen to bring all her experience into a uniquely strategic role.
“I thrive on creating structure and can see the big picture but understand the details,” she says.
“I uncover new opportunities and have the grit and resilience to capitalise on them.
“After 25 years in waste management, I couldn’t be more excited to be taking on this new role.”
e amalgamation of waste management companies Cleanway, EnviroChoice and Lee’s Environmental, Evoro has a complete eastern seaboard presence with operations in Queensland, New South Wales and Victoria.
Susie describes it as creating a “powerhouse in total waste solutions” covering everything from bin hire to industrial services. For clients, it means safe, e cient and environmentally responsible disposal solutions for hazardous and non-hazardous waste, and cutting-edge sustainability practices.
“We take our environmental responsibilities very seriously,” Susie says.
“We are committed to nding solutions that return and reuse materials.”
Evoro operates across a range of industries throughout Australia, including municipal councils, manufacturing, transport and logistics, oil and gas and infrastructure and construction.
A suite of services is tailored towards hazardous waste such as collection and disposal, emergency and spill response, grease trap and septic tank cleans and hazardous waste treatment.
Susie says the team of chemists, engineers and operational specialists is committed to innovation and excellence and can provide tailored solutions for even the most challenging waste streams.
Case in point – the company’s treatment plant in Victoria specialises in neutralising and recycling hazardous chemicals and can recover reusable product from waste glycol, an organic compound commonly referred to as antifreeze.
e facility has capability to process about 400,000 litres of glycol each month, achieving purity levels of 90 per cent for reuse.
Susie says building a greener future includes adopting eco-friendly waste streams.
“Evoro works to be at the forefront of technical waste treatment solutions, with the aim to provide input into the circular economy,” she says.
“Our team pursues strategies in house and through our partners, including resource recovery, recycling, composting and waste-to-energy, to rede ne the waste cycle by rst approaching waste as a potential source of reusable product.”
Evoro’s chemical neutralisation process safely balances PH levels in acidic and alkaline wastes through a controlled chemical reaction, turning them into a non-hazardous chemical such as water or insoluble salts.
Wastewater treatment includes ensuring industrial wastewater meets regulatory standards before discharge, advanced technology to treat waters with high levels of PFAS (Per- and poly uoroalkyl substances) and a safe and e ective technique to treat and dispose of hydrogen uoride (HF) chemicals.
Using advanced solidi cation techniques, the team also stabilises sludges and powders, making them safe for sustainable disposal. Recycling oil helps to ensure that less is wasted, and more is reused, reducing the strain on nite resources.
Facility upgrades in Laverton, Victoria, New South Wales and Stapylton, Queensland are set to strengthen the line-up.
e Laverton project, ve years in the making, was set to commence construction in November 2024 and will modernise the facility, improve access and increase processing capacity.
For Stapylton, Evoro has approvals to expand onsite treatment capabilities, with the project set to start in 2025.
All Evoro facilities and operations comply with environmental regulations and are Environment Protection Authority certi ed. e team also conducts waste audits to help customers better understand their waste streams and provide them with an e cient and eco-friendly solution.
Susie says the company strives to minimise the amount of waste going to land ll.
e team has a commitment to sustainable waste management practices and clients can be assured that their waste is managed in line with professional and legal standards.
“Implementing the highest safety standards when dealing with waste also helps to ensure our clients, employees and the wider public do not come into necessary harm,” Susie says.
“By setting ambitious goals, embracing technological innovation, and collaborating with stakeholders, we ensure our waste management practices evolve in sync with the latest advancements.
“ is commitment drives positive results for us and our customers.”
For more information, visit: www.evoro.com.au
Waste solutions provider Cleanaway is primed to deliver a circular solution for Food Organics Garden Organics (FOGO) in New South Wales.
Organics is one of the fastestevolving segments of the waste industry as councils adopt kerbside collections in line with State and Federal government mandates to keep food waste out of land ll. is will be the biggest change in the waste industry for the past 20 years.
For Ash Turner, State Manager for Resource Recovery at Cleanaway’s organics facility in Eastern Creek, it’s an opportunity to play an important role in enabling Australia’s transition to a circular economy.
Ash is leading the shift of Cleanaway’s Eastern Creek facility from red-bin waste treatment to processing Food Organics Garden Organics (FOGO) into compost for the agricultural sector.
Facility upgrades occurring as part of the transition will increase Cleanaway’s processing capacity at the Western Sydney facility by 35 per cent.
“Cleanaway believes in circularity and the environmental bene ts of removing organics from land ll,” Ash says.
“Our process is true circularity. We take food and garden waste, process it into compost and return it to agriculture to improve the soils and yield.
“Additionally, diverting food waste from land ll and processing into compost is a great way to reduce greenhouse gases.”
Organic waste in Australian land lls generates about 13 million tonnes of greenhouse gas emissions (carbon dioxide equivalent) annually – about 2.5 per cent of Australia’s total annual emissions – according to the Department of Climate Change, Energy, the Environment and Water.
In 2021, the New South Wales Government introduced e NSW Waste and Sustainable Materials Strategy 2041, which aims to recover
more FOGO to reduce land ll waste. Under the strategy, all councils must roll out a FOGO collection service by 2030.
Ash says the upgrade of the Eastern Creek facility to include FOGO processing is crucial to supporting the state’s transition to FOGO, accounting for almost 30 per cent of the infrastructure required to meet forecasted capacities.
“Cleanaway has invested about $200 million into the FOGO transition in New South Wales,” he says.
“ ere has been a commitment and an understanding within Cleanaway that this is the right thing to do for the environment and our communities.”
Cleanaway has a history of delivering at-scale waste solutions that provide environmental bene ts. Its Blueprint 2030 strategy sets out a goal to be the
most sustainable waste management provider in Australia, using innovation to see all waste as a resource and asking, ‘what can it be next?’
To reach that goal it has invested in recycling and land ll diversion infrastructure and the rollout of new waste stream services. In August 2022, Cleanaway acquired Global Renewables Limited (GRL) and has rebranded it to Cleanaway.
Ash says the Eastern Creek facility had a proven track record of removing contamination from waste materials and was well placed to make the change to FOGO with minimal disruption.
During the past two years, the facility has been upgraded to increase processing capacity. is will output larger volumes of compost to a higher standard, in anticipation of growing customer demand.
In October 2024, the facility started processing FOGO from a number of Sydney metropolitan councils, with more expected to sign on before the end of the year.
Up to 220,000 tonnes of organics can be processed annually, with capacity to expand on application approval.
“Cleanaway saw the need and value for a facility like this and has committed to organics processing in a signi cant way,” Ash says.
“ e move to FOGO alleviates some of the stress on the diminishing land ll space in New South Wales, providing a way to remove organic material from land ll, which has a signi cant impact on carbon emission equivalents.
“ at’s underscored by the fact it is absolute circularity. Food and garden material is processed into compliant compost that goes to agriculture and comes back as quality food products. ere are very few steps from kitchen table through to farmland and the bene ts are signi cant.”
ose bene ts are being backed up by science. Various trial plots around
the state are visibly demonstrating improved soil quality when the compost from Cleanaway’s Eastern Creek facility is applied.
Ash says farm trials with oats indicate a 100 per cent increase in yield when compared to standard fertiliser. A Brassica trial indicates a 240 per cent increase in yield when compared to no compost.
“We’ve adjusted the process to produce a higher bulk density compost,” he says. “It spreads beautifully.
“Farmers have a real earthy connection with it. ey say it feels and smells earthy and natural, not like a chemical.”
e secret to a high-quality product, Ash says, is a wellmaintained composting process and early decontamination.
At Cleanaway’s Eastern Creek organics facility, quality, compliant product can be produced in four weeks – two weeks in a compost hall and two weeks maturation.
It is monitored for moisture and undergoes a thorough screening process. Feedstock also undergoes various levels of decontamination prior to composting.
e rate of contamination has been raised as an ongoing concern for the Australian Organics Recycling
Association because it is di cult and costly for organics processors to remove.
Ash says as the former GRL site, the facility was already well equipped to sort through general waste, remove recyclables and isolate contaminated material. ese capabilities have been carried over to the organics processes, giving Cleanaway the ability to reduce contamination and produce a cleaner compost product.
However, education is a crucial way to drive engagement and encourage the right recycling behaviour.
A contamination feedback loop provides reporting on the rate and types of contamination. Cleanaway’s in-house team of educators work closely with a variety of stakeholders such as schools, councils and businesses to build con dence around waste disposal and resource recovery.
Additionally, there is a suite of education resources available to assist the community in reducing FOGO contamination and improving overall recycling rates across Australia.
Ash says this is just another way Cleanaway is working together with local communities, to make a sustainable future possible.
For more information, visit: www.cleanaway.com.au
A new compost processing solution promises quality and quantity.
Contamination remains an ongoing concern in organic waste processing, but European manufacturer IFE Material Handling has developed technology that will not only screen contaminants but turn any over ow into usable fractions.
e Aeroselector combines wind sifting, ballistic separation and screening in one machine and has been proven to separate plastic foils, stone, and structural material from the screen over ow in several European composting plants.
Simon Sherwood, Managing Director of Material Processing Solutions, an exclusive distributor of IFE equipment in Australia and New Zealand,
says the Aeroselector is speci cally designed to simplify the organics re nement process.
“Using one-of-a-kind technology, the Aeroselector can increase compost quantity, purity and quality,” he says.
“Its throughput, compact design and e ciency will make it popular in Australia’s organics and recycling sector.”
At the core of the Aeroselector is a magnet, ip- op screen and air separation system which allows the puri cation of compost in one simultaneous process. Ferrous metals, stones, plastic foils and lms are removed from the stream while making a high-quality nal product.
As the nal component, a star screen removes any remaining elongated, structured material which can be placed directly back into windrows to allow additional aeration and decomposition, saving costs of re-grinding a percentage of the oversize material.
e compact, stationary system is ready for use in any weather, even with moist raw compost.
Each machine is also exibly integrated into existing recycling processes and can be expanded as required.
Optional features include a modular feed hopper, various size ip- op screens and magnetic pulley, all speci cally sized to the processor’s requirements.
Simon says due to easy handling and low energy consumption, the operating costs for compost processing can be signi cantly reduced by using an Aeroselector.
Optimal selection and co-ordination of components also means the machine is easy to maintain and clean.
For more information, email: sales@mpsbulk.com.au
SOILCO is leveraging 50 years of operational experience to support South East Queensland’s infrastructure requirements for source-separated organics.
About 300,000 Queensland households have an organic waste bin, mostly used for garden waste. By 2030 the State Government wants more than 1.6 million households collecting both food and garden waste to assist in meeting national and state waste reduction targets.
e state’s Organics Action Plan 2022-32 sets out a roadmap to transition to a circular economy and build economic and market opportunity for the organics recycling industry.
With a proven track record of transforming organic resources into quality-assured, life-giving soil products, SOILCO is an early mover
in the South East Queensland market, investing in strategic locations that will deliver key infrastructure and technology to bring its source-separated organics processing services to councils, commercial waste generators and local communities.
In 2022-23 the company secured three green eld sites – Badgerys Creek in Western Sydney, Pinkenba in Brisbane, and Bromelton, in the Scenic Rim – that are now well on their way to being developed into large-scale organics recovery facilities.
Roslyn Florie-George, Executive General Manager – Strategic Growth & Infrastructure, says each site has been carefully chosen to meet
the infrastructure needs of the surrounding region.
e combined capacity of these new facilities will exceed 900,000 tonnes per annum and will bolster SOILCO’s existing networks that span New South Wales, Victoria and the Australian Capital Territory. Importantly, they will deliver proven results in helping communities increase the diversion of Food Organics and Garden Organics (FOGO) from land ll.
“We successfully transitioned from public drop-o /self haul feedstocks to kerbside garden organics (GO) 25 years ago, and more recently, we’ve assisted our council partners to navigate the transition from GO to FOGO,” Roslyn
says. “We’ve needed to overcome challenges and collaborate closely with our council partners. We feel that all of our learnings as a business will be bene cial to Queensland, and we’ve invested signi cant capital in the region.”
e designs for a new intersection and road extension have been accepted and procurement for the initial infrastructure works is progressing for the 161-hectare Bromelton Compost Manufacturing Facility (CMF) site.
e Development Application for the CMF was submitted in October 2024. Designs include a 400,000-tonne capacity facility comprising 250,000 tonnes of organics processing and 150,000 tonnes of additional valueadd products, such as sand and soil, to blend with composted products.
SOILCO’s Bromelton CMF will use aerated static pile technology, which, Roslyn says, has proven to work e ectively for feedstocks containing food in more regional locations.
“It’s a technology we are familiar with and we have successfully used since 2018 at our Wogamia facility, near Nowra in New South Wales,” she says.
“It’s the sweet spot between open windrow composting and in vessel systems. It provides the required environmental and process controls, without the need for capital investment in enclosed tunnels.”
e facility will ll a gap in South East Queensland and northern New South Wales which, Roslyn says, are currently lacking organics facilities.
SOILCO’s Tweed Heads Organics Processing Facility (located at Stotts Creek Resource Recovery Centre) is nearing its licensed capacity. SOILCO is regularly approached by councils on both sides of the border seeking a solution for organic waste in the region.
She says the biggest challenge in Queensland is that land ll levies
do not yet provide an economic incentive for local government to transition to FOGO. At the same time, strict legislative frameworks are being introduced, resulting in less appetite for organics processors to invest in expensive enclosed technologies alongside pre- and post-sort decontamination processing equipment.
However, if the industry is to meet legislative requirements and resource recovery targets, additional capital expenditure is needed.
“Self-haul GO is a relatively clean waste stream that can continue to be managed by existing infrastructure, however, we anticipate that councils will see a change in feedstock quality when kerbside GO services are introduced more broadly. With the move to FOGO, there will likely be another shift in the feedstock characteristics, which will require further investment in the industry,” Roslyn says. “SOILCO is a legitimate player. We have half a century of experience, and we are developing
facilities locally to get the most out of this valuable resource.”
While the kerbside organics recycling landscape continues to evolve, SOILCO is broadening its service o ering and is nalising the Material Change in Use application for its Pinkenba facility, which will allow it to receive and aggregate a range of waste streams, in addition to organics.
It plays to a broader objective for the company to become a national resource recovery platform.
“SOILCO has an excellent reputation for recycling domestic and commercial organic feedstocks in southern New South Wales, and more recently the Northern Rivers and Canberra,” Roslyn says. “In the past three years we’ve broadened our footprint and crossed state borders. We’re working hard to establish a largescale strategic network and are on the cusp of achieving so much more. 2025 will be our biggest year yet.”
For more information, visit: www.soilco.com.au
The recipient of the Australian Organics Recycling Association (AORA) scholarship discusses her motives for applying and reflects on her time at the AORA Conference.
Each year the Australian Organics Recycling Association (AORA) holds the AORA Annual Conference, a forum for education, discussion and networking related to organics recycling.
Now regarded as the principal conference in Australia for the organics recycling industry, it is also an opportunity to celebrate outstanding achievements in the industry.
To encourage growth for the next generation of waste leaders, AORA o ers a $3000 scholarship to help a young professional attend the conference which features workshops, presentations, social functions and an equipment demonstration day.
emed Collaboration for Success – Securing our industry’s future, the 2024 conference was held across three days from June 5-7 at the Seaworld Conference Centre, Gold Coast, Queensland.
Violet Edwards, a 26-year-old agronomist, who was working at Verterra Ecological Engineering at the time, was this year’s Komptech CEA Young Professionals Scholarship recipient. She says it was a privilege to be awarded the scholarship and attend the conference.
During her time at Verterra Ecological Engineering, Violet worked as an agronomist, focusing on recycled organics and the bene cial reuse of biosolids via direct land application in agriculture.
It was here she discovered the AORA scholarship.
“I wanted to apply for the scholarship for several reasons, one was primarily due to working in the space of biosolids and the bene cial reuse of what most people consider a waste product,” says Violet.
“ e stigma around recycled products can be somewhat in uenced by negative public perception. Being able to highlight the bene ts of recycled organics and learn more about their valuable contribution to the circular economy was extremely important.”
Violet says the scholarship also provided a unique opportunity.
“ ere is a lot of talk around composting FOGO (Food Organics Garden Organics) and recycled green waste, but not a lot of information on biosolids and the bene ts it has to an agricultural production system,” she says. “We are actively trying to break down the community perception of it being waste and trying to highlight the bene ts.”
As a young professional in the industry, Violet says she couldn’t pass up the opportunity to network with other industry professionals.
“It can be di cult to network and leverage in smaller industries, so I was glad to have the opportunity to attend the AORA conference where there was a concentration of industry people who are willing to pass on knowledge and have valuable discussions,” she says.
“It is very important to make those connections and speak with people in the space to leverage and learn. Particularly for young professionals.”
Violet describes the conference as an in-depth display of topics and discussions pertinent to the industry.
“A demonstration day sponsored by Focus Enviro kicked o the event and o ered a fantastic display of technological innovation. I think it covered all bases and was quite in depth.”
More than 20 machines were on site for the demonstration, including shredders, compost screens, loaders, and excavators.
“ e rst day of the actual conference focused primarily on regulations and legislations, as well as the application of recycled organics,” Violet says.
e presentations began with a keynote presentation by Professor Sally Brown on the versatility of compost, which turned out to be one of Violet’s favourite presentations.
“Presentations and sessions on this day centred around shaping the industry’s
future while analysing its current standings,” she says.
“Janine Price from Scolexia was another speaker who broke down and reviewed current state regulations on soil amendments and speci c feedstock from each state’s EPA’s (environment protection authorities).”
Violet says this presentation was a standout for her as it shed critical light on discrepancies between each state’s regulations.
“Janine discussed many areas for improvement and standardisation within those regulations,” she says.
To nish o the conference, day three centred around primary producers, highlighting the application and signi cance of compost products in agricultural production systems.
Violet says as an agronomist, she enjoyed the presentations throughout
the third day as they focused primarily on agronomic topics, diagnostics and the research that’s going on within recycled organics.
“Learning of the positive advancements that recycled organics are having on Australia’s agricultural, horticultural, and viticultural industries was eye-opening and rounded out the conference perfectly,” she says.
With time to re ect on her experience, Violet says she is looking forward to the growth of the industry.
“In the grand scheme of things, the industry is still small, so I am looking forward to seeing positive growth within the recycled organics industry in the coming years,” she says.
“For an industry that is still evolving, it is poised for substantial
growth. I enjoyed learning about the quantity of research going into the recycling industry.”
For those looking ahead to next year’s scholarship and conference, Violet couldn’t recommend the experience enough.
“ e opportunity to speak with like-minded people within the industry is enough of a reason to apply for the scholarship,” she says.
“On top of that, all the information and knowledge that you take in from the conference itself is a once-in-a-lifetime opportunity.
“I would de nitely recommend it to young people in the recycled organics space.”
For more information, visit: www.aora.org.au and www.aoraconference.com.au
WESTERIA brings the advantages of windsifting technology to a small, mobile machine.
Recycling and resource recovery engineering experts CEMAC technologies are always looking to advance technology to boost Australia’s circular economy.
Its newest o ering from German expert in windsifting and materials handling, WESTERIA, is the AirBasic windsifter system.
e Airbasic is an ideal plug-andplay solution for sifting applications, and is also used to clean up compost to a high quality product that meets customer need.
By bringing the advantages of well proven windsifting technologies to a small, mobile machine, the AirBasic is able to clean all forms of wastes including organics,
construction, household, slag and even scrap metal.
Organics processor SOILCO has 40 years’ experience in designing, building and operating organics recycling facilities, recovering and transforming organic waste into products to regenerate and give life to soil. To continue its goal to diversify its operations and meet the challenges of Australia’s dynamic waste and resource recovery sector, SOILCO partnered with CEMAC technologies to install an AirBasic system.
Eric Paulsen, Managing Director, CEMAC technologies says SOILCO installed the AirBasic system to
address contaminants across its di erent sites.
“ is machine is a portable, plugand-play solution for windsifting materials,” says Paulsen.
“SOILCO’s byproducts from composting Food Organics and Garden Organics (FOGO) is oversize material, including a range of physical non compostable contaminants such as di erent forms of plastic, that have been thrown into household green bins.
“Materials such as plastic and FOGO must be reliably separated.
e AirBasic achieves the highest possible removal of lm and other light contamination, allowing a larger quantity of marketable size fractions then what has been achieved to date.”
e AirBasic is available on a hook lift skid or tracks, and features a patented adjustable and precise nozzle system to ensure optimum separation results. It is a two-way separation system, with the option to integrate conveyors or other modules, such as the AirLift or DiscSpreader, to accommodate operator needs.
e AirLift vacuum system creates a third fraction by separating ultra-light impurities from the light fraction.
At speeds of up to three metres per second, material is propelled over a bend in the conveyor belt as the AirLift, positioned above, vacuums up any lightweight items, while heavier biowaste stays on the sloped belt.
e DiscSpreader material distribution system ensures uniform ow and distribution, independent of the feed type and direction.
In the main part of the machine, an acceleration conveyor belt brings the material up to three metres per second, while the Air jet system ensures high purity of the output fractions through the smallest deviation of the blowing speed.
e SOILCO project was customised to meet the company’s needs and included a DiscSpreader, Airlift and the heaviest power conveyor.
Eric says one of the attractions of the AirBasic is its portability.
“Having a mobile machine like the AirBasic is an optimal choice for companies like SOILCO,” he says. “ e machine arrived on a skid lift for easy transportation, and it can be positioned directly behind a screening trommel, which allows the operator to clean up oversized material very easily.
“ e lightweight components and compactness of the machine means the AirBasic can be moved from site to site, with the option to be integrated into a processing plant at a later stage.”
Eric says the AirBasic brings new technology to Australia and is an exciting step forward in the windsifting space.
AirStar Evolution is the stationary version of the AirBasic, also known as the big brother of the AirBasic. is year, the entire machine was redeveloped to allow better access to all components.
e AirStar features an adjustable fan that allows precise control of air speed and is equipped with an extra-wide nozzle opening for a broader and more even air ow, contributing to improved separation. e AirStar is also tted
with an optimised air guidance system to direct air ow into the lightweight chamber. Parameters are automatically adjusted by the PLC control, allowing simple program changes by central plant control or touch screen operation.
Eric says one key aspect of the AirStar is the ability to adjust the nozzle angle and pressure controls for separation of di erent materials.
“All materials recycled on the machine can be saved for the ideal processing settings on the machine. Once in the system, these settings can be chosen at any point in time.”
CEMAC welcomes the opportunity to demonstrate the AirBasic.
For more information, visit: www.cemactech.com
As the risk of battery-related fires increases in waste and resource recovery facilities, an engineered solution is helping to keep them safe.
Three key phrases are often repeated by Fire Rover customers – risk reduction, peace of mind and asset protection.
“ e waste and recycling industry is facing a surge in res caused by batteries,” says Scott Russ, National Business Development Manager for Wastech Engineering. “ e Fire Rover detects a heat source and stops it before it turns into something dangerous.
“Within seconds, it will pick up variations of heat in waste material and send an alarm to the control centre, which then immediately looks at the cameras to determine what’s going on.
“Customers are paying for a 24/7 monitoring service for Fire Rover to make the determination of the next steps. You could potentially have an incident that is over and done with before you even know about it.”
ere are between 10,000 and 12,000 battery-related res a year across waste
and recycling facilities in Australia, according to an industry survey.
e survey, released in June 2024 by the Australian Council of Recycling (ACOR) and the Waste Contractors and Recyclers Association (WCRA), estimates costs of more than $400,000 for facilities that experienced battery-related re and heat events in the past 12 months.
Aside from the nancial impact –including facility damage, rebuilding and clean-up costs – these events interrupt business and cause a loss of revenue.
Scott says the Fire Rover Fire Suppression System is a key piece of the puzzle to reducing major res and a game changer for the industry.
Wastech Engineering, exclusive distributors of the Fire Rover in Australia and New Zealand, recently installed Fire Rover’s re suppression system at Re.Group’s facility in Dandenong, Victoria, a busy waste management site handling 65 trucks of waste daily.
e system, featuring three 20-foot containers with multiple cameras and nozzles, has been well-received, leading to commitments for additional installations in Sydney and other Australian sites.
Scott says what’s unique about the Fire Rover is the environmentally friendly F5 100 re suppression agent. With a density of nearly 100 times more than water, the agent acts as a foam blanket, neutralising the threat of re within seconds.
“Fire Rover is setting a new benchmark in safety at Re.Group, a critical recycling site,” he says.
“With Fire Rover, the Dandenong recycling facility has improved safety for site teams and rst responders, protected valuable equipment and infrastructure, minimised re-related disruptions and has 24/7 protection.
“Re.Group can rest assured that the facility is secure, even in highrisk environments.”
e Fire Rover is an engineered solution for speci c facilities. Scott says the Re.Group project had particular challenges, including limited space and installation at a site that operated 24 hours a day, six days a week.
“Working around existing infrastructure like a material recovery facility (MRF) is not easy,” he says.
“We designed a number of versions to get the ultimate setup for Re.Group. As you can imagine, a 20-foot container within a MRF does take up space, so we had to put it in the right location.
“And we could only install the system on a weekend when the facility was a lot quieter.”
Following installation, Wastech works with facility sta to ensure they understand the system and can work in tandem with it.
One unique aspect of the Fire Rover is the installation of emergency buttons in key locations throughout facilities so if sta do notice something unusual, they can quickly alert Fire Rover.
“We work closely with the on-ground sta , so they’re aware how the system works and how they can use it to help their facility,” Scott says.
“Each customer has their own emergency protocols for sta to follow. Fire Rover can be considered the rst line of defence prior to the re department attending.
“If you’re talking about a potential window of ve to 30 minutes for a re department to turn out, a re can get out of control a lot quicker than that. Fire Rover will engage instantly.”
e Fire Rover system has a built-in battery pack as redundancy for a power outage and 4G backup for internet outages. If either are activated, it is
included in a quarterly customer report that outlines all alarm activations and callouts.
Wastech Engineering has o ered the Fire Rover since 2022. Scott says momentum is building as recycling and resource recovery operations look to protect their infrastructure from rising contamination of waste streams.
“People are just not educated enough in Australia about how to handle batteries,” he says. “ at’s one of the big issues.”
Re.Group Chief Development O cer Garth Lamb says the main game is getting hazardous items and batteries out of household bins, but in the meantime the company continues to do all it can to manage risks at its sites.
“ e ability to retro t this rapid- re suppression system at an operating site with minimal service disruption is a key bene t to helping us address this huge problem,” he says.
Wastech Engineering has installed a Fire Rover system at a transfer station in North Sydney, a transfer station in Western Australia, an e-waste recycler in Sydney and is about to install a rst system in New Zealand.
e system has also proved successful in rural and remote areas where hardwired internet connectivity is an issue.
e Fire Rover can work via Starlink – a satellite network developed by private space ight company SpaceX to provide low-cost internet to remote locations.
e Fire Rover is currently geared toward material recovery facilities, transfer stations, waste stockpiles, construction and demolition waste, waste-to-energy, electronic scrap and more.
A land ll-speci c version called the OnWatch has been launched in America to early detect and verify res on the working face of a land ll, outdoor stockpiles and windrows.
Scott is now keen to lobby Australian re regulators and insurance companies to recognise that the Fire Rover containerised solution is a compliant system, with the hope it could eventually help reduce insurance premiums.
“If we can get it compliant, it would be a massive game changer.”
For more information, visit: www.wastech.com.au
Australia’s first incinerator bottom ash processing facility is up and running, rewriting the way the nation treats waste.
Ian Lynass has nally seen his vision become reality.
In October, the Managing Director of Blue Phoenix Australia icked the switch on an Australian- rst facility that has been ve years in the making and is set to change the nation’s waste landscape.
Ian has been the driving force behind the Incinerator Bottom Ash (IBA) treatment facility in Kwinana, Western Australia and has been patiently waiting to be able to showcase a proven, sustainable and responsible way to recover and reuse materials otherwise lost to land ll.
He got that chance when the $11.3 million IBA project at Hope Valley in Kwinana, Western Australia powered up.
“I am extremely proud to bring Australia’s rst incinerator bottom ash treatment facility to life in support of our partnering customer Acciona, owners of the Kwinana Energy Recovery Project,” Ian says.
“ is new patented and proven technology will bring about a truly circular economic outcome for our customers and the community.”
e opening was attended by Ardi Stoios-Braken, ambassador of the Kingdom of the Netherlands to Australia, and Elizabeth Carr, Chair of Western Australia’s Waste Authority, along with local and interstate industry leaders. Ian says it’s a major step for Blue Phoenix and Australia’s waste management landscape.
“We are excited to bring our global expertise in IBA processing to Australia, where we see tremendous potential for reducing environmental impact and promoting sustainability,” he says.
“ is facility will also be available to help educate local communities about the recycling of waste and the responsible recovery of construction materials that, until now, simply ended up increasing the land ll debt for future generations.”
e state-of-the-art plant will process 100 per cent of the IBA – about 80,000 tonnes per annum – from its EfW partner, Acciona, transforming it into valuable secondary materials, such as aggregates for use in the civil construction industry.
For the past 20 years, Blue Phoenix Group in Europe has recovered and safely reintroduced 15-million tonnes of aggregate, predominantly into road base, with no detrimental environmental e ects.
“Blue Phoenix Group focus on responsible and sustainable solutions. We liberate the resident metals in the ash and deliver a high-quality aggregate into the civil construction industry,” Ian says.
“For 25 years we have proven the bene ts of this material both mechanically and environmentally.”
As well as spearheading the IBA plant construction, Ian established the Manufacturers of Incinerator Bottom
Ash Aggregate of Australia (MIBAAA) Association, to bring together industry players to ensure sustainable and responsible pathways for the reuse of incinerator bottom ash.
e association is supported by Manufacturers of IBA Aggregates Association in the United Kingdom, which has worked with regulators and industry to set standards for the reuse of more than 2.5 million tonnes of ash each year.
“IBAA is a resource that has not previously been recovered in Australia. is is an exciting time to really tap into recycled materials that we didn’t even know were there,” Ian says.
e rst ash was received at the Western Australian plant on 13 September 2024, and the o cial commissioning started on
1 October 2024. It was a proud moment for Ian, and his family, who have shared his vision. Daughter Stephanie is taking on the role of operations supervisor at the plant.
“My most sincere thanks go to my wife Fiona and my family who have all been very actively involved in bringing this dream to reality,” he says.
“I could not have done it without their support.”
Perth councillors and businesses have previously toured the site.
Blue Phoenix welcomes other state’s representatives to tour the plant to gain an appreciation of the opportunity to divert material from land ll through IBA processing.
For more information, visit: www.bluephoenix-group.com
Circular precincts have the potential to unlock significant value for the waste and resource recovery industry. Amal Jugdeo, Business Development Manager for Kanadevia INOVA, explains.
It is an exciting time for the wasteto-energy (WtE) sector. Western Australian projects in East Rockingham and Kwinana lead the way. From 2025 onwards, these facilities will jointly treat more than 760,000 tonnes of residual waste per annum (tpa) that would otherwise go to land lls.
Victoria is not far behind. e Maryvale WtE facility is licensed to process 650,000 tpa of residual waste, and a few more projects are in the permitting phase.
Plans are also afoot for WtE facilities in New South Wales and South Australia.
e standout is Queensland’s City of Gold Coast, which has bold ambitions to reduce its reliance on the Stapylton and Reedy Creek land lls and aspires to achieve 97 per cent land ll diversion. It proposes an Advanced Resource Recovery Centre (ARRC) circular precinct with recycling, composting/anaerobic digestion, hydrogen production, and a WtE plant of more than 500,000 tpa residual waste.
It’s all well that project developers are pursuing WtE projects across Australia as a more sustainable waste
management solution than land lls. However, some harsh realities must be considered when exploring the viability of such large and advanced WtE facilities, says Amal Jugdeo, Business Development Manager at the Sydney o ce of Kanadevia INOVA.
Amal says it is all too easy for project developers to jump into costly design and engineering studies only to realise at the end of the exercise that the business case is challenged.
He says land ll levies in Australia are simply too low to justify investment in a conventional stand-alone WtE
solution – we therefore must think bigger and smarter!
“Circular precincts make for a bigger resource recovery party,” he says. “Colocating a WtE facility with other waste processing facilities, such as a material recovery facility (MRF), an organics processing facility, and other industrial facilities requiring steam or heat, has the potential to unlock signi cant value.
“In this way, waste receival can be centralised to take advantage of shared infrastructure such as weighbridges and workshops; non-recyclables and reject waste streams can be processed at the WtE facility while the WtE facility can provide ‘behind-the-grid’ electricity to the nearby facilities.
“ e centralised processing of various waste streams will positively impact the business case.”
He says when it comes to ‘bigger’, look no further than the world’s largest WtE facility in Dubai. Kanadevia Inova (KVI) designed the ve-line 126MWth boiler facility that will process 1.9 million tpa of residual waste.
KVI has hundreds of WtE references, a strong balance sheet from Japanese parent Kanadevia Corporation, and invests signi cantly in research and development. It is no surprise that WtE plants have increased considerably
in throughput per line over the years – from 300,000 tpy/line in the early 2000s (Greatmoor, United Kingdom), to 325,000 tpy/y (FMI1 and FM2, UK) to 360,000 tpy/y (Dubai) to now 450,000 tpy/line for the two-line 140MWth Abu-Dhabi plant currently in construction.
ese ultra-large combustion boilers yield the lowest capex per ton of waste processed.
Amal says increases in construction costs are a signi cant challenge for the industry. In Victoria, for example, the largest construction union negotiated a 21.5 per cent pay rise for workers over ve years, and similar arrangements have been reached by unions in New South Wales and Queensland.
“ is alone places signi cant cost pressure on labour-intensive projects such as WtE plants. Add to these, uctuations in the international steel and process equipment market, and it becomes clear that it is no easy task to peg construction costs for a WtE plant that has a large mechanical, electrical and piping component with a high degree of certainty as one would a commercial o ce building or bridge for example.
“Project nanciers need price certainty; without this, projects are simply not bankable. It is imperative that credible players conduct
comprehensive engineering and project management studies to quantify construction costs with a high degree of certainty and derisk the project before proceeding with project execution.”
Approximately 20 per cent by mass of the waste treated at the WtE facility will result in Incinerator Bottom Ash (IBA). Once metals are recovered from the IBA for recycling, the resulting IBA is processed into aggregate suitable for use in the road and construction industry. is is also well established in the UK and provides a precedent in a similar jurisdiction when seeking regulatory approval in Australia. Victoria and Western Australia have made progress in this regard. Without regulatory approval for the reuse, the IBA aggregate must be disposed of in a land ll, weakening the business case, Amal says.
Again, bigger is better. A centralised large IBA treatment plant processing IBA from multiple WtE plants further reduces the unit cost of IBA disposal. is approach is common in Europe.
“It is clear that a bigger party is better when it comes to WtE in Australia,” Amal says. “WtE should be seen as central to the success of circular resource recovery precincts. We must push the technology boundaries and increase the scale of WtE and IBA treatment facilities.
“IBA must be seen as a resource for the construction industry, and there should be a clear regulatory pathway to enable this. We should partner with credible players and only after su cient design work is done to quantify construction costs adequately.
“It is the only credible pathway to an environmentally and nancially sustainable alternative to land ll for our ever-increasing residual waste.”
For more information, visit: www.kanadevia-inova.com
Volvo introduces a new tool to easily calculate charging and battery runtime for compact electric construction equipment.
CJD Equipment continues to revolutionise project planning in the construction industry with the Volvo Electric Machines Charging and Runtime Calculator. is handy tool allows operators to estimate battery runtime and charging time for electric machines, helping optimise operations and reduce environmental impact.
With the growing demand for electric construction equipment in Australia and worldwide, understanding how to use this calculator e ectively is crucial for project success, says Reid Gibson, Product Manager, Electric and Sustainable Technologies CJD. at’s where CJD product managers come in. Reid says CJD product managers will guide operators through key components of the calculator and how to customise calculations for speci c project needs.
“Whether corporations are considering an electric mini excavator or planning large-scale sustainable
construction projects, this calculator will help operators harness the power of electric excavators to boost productivity and achieve zero emissions on the worksite,” he says.
e Volvo calculator is a user-friendly tool designed to help operators plan their workday e ciently. It consists of three main steps, each allowing for customisable calculations based on individual needs.
Step one involves selecting the Volvo electric machine and preferred charging option.
“ is step is crucial as it sets the foundation for accurate runtime and charging estimates,” says Reid.
In step two the operator will provide details on the intended use of the machine. is includes daily operating hours, idling percentage, and workload intensity.
Reid says the calculator considers that a machine can be idling for up to 70 per cent of its operating time, helping operators estimate actual usage.
“Step three allows operators to switch between charging and runtime results, giving instant insights into how to plan a workday e ectively,” he says.
“ is feature helps ensure a machine is fully charged and ready to go when needed.”
Reid says operators need to input accurate data about the project to tailor the Volvo Electric Machine Calculator to speci c worksites.
“Start by estimating your daily operating hours and idling time, remembering that machines often idle up to 70 per cent of their operating time,” he says.
“ e calculator adjusts active operating hours to the nearest half hour, providing a realistic view of usage. e calculator estimates a machine’s usage, energy consumption, and available charging power.”
Alternating current (AC) charging assumes a maximum rated power of
11 kilowatts, however Reid says it’s crucial to factor in any on-site power limitations, and the capacity of a machine’s onboard charger.
“To optimise an electric excavator’s performance, it is recommended storing it indoors overnight, to help maintain battery temperature, improving e ciency in cold or hot conditions,” he says. “If outdoor storage is unavoidable, rest assured light elements won’t damage the batteries.”
Integrating renewable energy sources, such as solar and wind power, can also reduce costs – achieving a high level of cost reduction compared to scenarios without renewable energy, Reid says.
“By leveraging the calculator’s data, you can develop a charging strategy
that aligns with your project’s needs, ensuring your electric machine is always ready when needed.
“ e Volvo Electric Excavator Charging and Run Time Calculator signi cantly impacts project planning and execution in the construction industry.”
Reid says this tool is particularly valuable as the industry shifts towards more sustainable practices, allowing companies to harness the power of electric excavators to boost productivity and achieve zero emissions on worksites.
“As the demand for electric construction equipment grows, understanding how to use this calculator e ectively becomes crucial to project success,” he says.
“It empowers construction professionals to make informed decisions about machine usage, charging
strategies, and project timelines. By embracing this technology, construction companies can stay ahead of the curve and contribute to a more sustainable future in the industry.”
For more information, visit: www.cjd.com.au
As Australia seeks to minimise its carbon footprint, Garwood International is helping to bring the next generation of waste vehicles online.
Garwood International has tailormade waste compactors for customer needs for the past 40 years. Its latest project answers the call for lower emissions, fuel security and reduced tra c noise.
e team developed and delivered an electric garbage truck for a Victorian council. e truck, the rst of its kind produced by Garwood, features an electric motor coupled with a hydraulic pump instead of the usual diesel engine and transmission.
Ian Pinney, Garwood Sales Manager for Victoria, Tasmania and South Australia, says the call for electric trucks is growing, mostly driven by local councils seeking a greener footprint.
“ is is a progressive council,” Ian says. “ ey want to do the right thing by the environment and be the driver of change so have chosen to go electric for all their transport operations.”
e compactors are the same, but the way it operates is di erent. Ian says the compactor drive would normally pick up o a diesel engine with a power take-o (PTO), a device that transfers the engine’s mechanical power to the transmission. e electric truck – a Hino – has an electric power cell instead of a transmission.
“It’s a lot more complicated,” Ian says. “ ere had to be a little bit of innovation and adaptation from our behalf.
“Our compactor body system is the same as what we build for every
customer, electric or diesel, but the way it’s powered is di erent.
“It’s been challenging, and we’ve learned a lot along the way. But there was always going to be development on the run with the rst one.”
e council took delivery of the rst truck in October, a six cubic metre Bantam rear loader. A second, larger truck (an eight cubic metre compact rear loader) is expected to arrive within months. e council will monitor the performance of both with the potential to order more.
Ian says with the rst one under their belt, the engineering team is well versed with what is required for future eets. He praises Garwood’s engineering team for delivering on the
council’s requirements. “Personally, I think the council is going to be very happy. It will serve them well and delivers what they want as far as a green footprint and zero emissions,” Ian says.
“ ey’ll also be saving money because there is no need to ll the tanks with diesel every day – it’s just a matter of charging the battery. You’ve literally just got to plug it in and charge it.”
As for the truck itself, the body’s still the same size as Garwood’s traditional builds, so there’s no loss of volume for rubbish collected.
Moving forward, Ian’s keen for similar projects, given the opportunity. But that will be driven by the customer.
“We’re not selling the electric product. We’re building the body to suit customer needs. at’s what we’re all about, a customer-driven service operation that is providing solutions,” he says.
“Sometimes they’re easy and straightforward, sometimes they’re challenging, but the challenging ones are rewarding.
“Garwood is known for giving customers what they need, especially
those one-o inquiries. We’d like to think that’s a good point of di erence.”
While the council project was a rst for Garwood’s engineering team, it’s not the company’s rst foray into electric vehicles.
Earlier this year Garwood launched the newest sweeper to its range, a 100 per cent electric compact sweeper.
e Boschung Urban Sweeper
S2.0 sets new standards in the twocubic metre class and is distributed exclusively by Garwood. It is the rst Boschung-engineered sweeper fully powered by onboard batteries and has an ten-hour operating time, producing zero emissions.
“ e innovatively engineered battery de nes a whole new intelligence management system, making the boundaries between work and charging times hard to discern,” Ian says.
e unit has articulated steering with oscillating suspension between front and rear frame for safe ascending and descending sidewalks.
Additionally, two 20-kilowatt wheel motors can reach top speeds of 45 kilometres per hour. e sweeper has
a maximum payload weight of 1200 kilograms, an 800-millimetre suction mouth and sweeping width between 1150 and 2300 millimetres.
A walk-through cab for entering on both sides o ers maximum operator comfort and security, while the central sweeping control console is easily operated with a single hand. Reverse and suction mouth cameras aid in safe and e cient operation.
Electrically driven wheel motors, broom motors and a turbine motor require no active cooling, smaller construction and have the ability to provide dynamic charging while in free spin.
With the ability to recharge on car charging stations, and with the Supercharger option, the unit has a charging time of two hours for 10 hours work.
Ian says the sweeper is revolutionising the industry and interest has been high as the sector searches for greener outcomes.
For more information, visit: www.garwoodinternational.com.au
Byrne Trailers launches a new walking floor trailer designed for maximum performance, versatility, and diversity.
You can’t have all your eggs in one basket,” says Mick Bray, National Sales Manager for Byrne Trailers.
“You have to diversify.”
It was for this reason the New South Wales-based trailer manufacturer turned its attention to the waste industry, introducing walking oor trailer technology – a hydraulically powered oor composed of moving slats. It was a fortuitous move. Now, 20 years after the company’s rst major waste project in Tasmania, Byrne Trailers is pushing to be one of the big players in the sector, launching a new trailer at this year’s Waste Expo Australia.
Mick says the drop deck trailer, with Keith J-MAX steel ooring, has been in development for about 12 months and will set Byrne Trailers apart.
“In today’s world, it’s all about compliance and better utilisation of equipment,” he says. “We’re building better units with bigger capacity that can carry more weight and give customers more pro tability.
“In transport, that’s what it’s all about these days.”
From small beginnings in Peak Hill, New South Wales almost 50 years ago, Byrne Trailers has a national footprint with manufacturing facilities in Wagga Wagga, New South Wales,
and Toowoomba in Queensland. It has a solid reputation for building revolutionary trailers for the agricultural industry and has made inroads into the waste sector as a leading supplier of leak-proof trailers that minimise leachate from municipal waste contaminating roads and waterways during transit. e introduction of the walking oor brought increased safety and ease of waste disposal.
“Times were changing,” Mick says. “Councils were more focused on operator safety and liked that the trailers didn’t have to be tipped to move contents out.
“You just walk the waste out.”
Byrne Trailers are built around a walking oor and drive unit from Keith Manufacturing Co, an American company that introduced the rst commercially viable moving oor unloading system under the Walking Floor brand name in 1973.
Byrne o ers two walking oor variations, the heavy-duty sheet and post trailer – suitable for heavier products such as construction and demolition waste – and the Euro trailer, another Byrne innovation, for carting lighter products such as recycling and mulch.
Both trailers can vary in size and capacity, ranging from smallest length to longer Performance Based Standards (PBS) dimensions. e company’s standard 45-foot trailer can take on 94 cubic metres, while the 48-foot trailer
can take up to 104 cubic metres and the new drop deck up to 134 cubic metres under PBS. Custom designs are also available.
e new drop deck trailer is a combination of the Euro trailer and a heavy-duty walking oor. A lower pro le and suspension allow for maximum capacity inside the trailer, while the Keith J-Max steel ooring is designed for longer wear when unloading abrasive material.
Mick says the Keith system is one of the fastest and strongest for unloading. But you don’t just have to take his word for it. If you’re not able to take a J-Max for a test drive, promotional videos of the new walking oor in action are the next best thing.
e videos clearly show the walking oor in action, pushing out sand, gravel, wood waste, glass, construction debris and “sticky” material
with ease. About 35 tonnes of municipal solid waste is cleaned out in under ve minutes; 48 tonnes of bauxite, with four to six per cent moisture, is unloaded in little more than four minutes from a 38 cubic metre box; and 31 tonnes of y ash unloaded in three minutes.
“We believe Keith are the superior brand for walking oors,” Mick says. “ e new J-Max is built for performance, versatility, and diversity.
“We’ve already had strong interest from across Australia.”
e Byrne Trailers team has a wealth of experience in new builds, servicing and restoring trailers with representation in New South Wales and Queensland. Keith also has a representative based in Melbourne to help with inquiries.
For more information, visit: www.byrnetrailers.com.au
Big Enough to Trust, Small Enough to Care
Komatsu’s WA475-10 Wheel Loader is a proven fuel-efficient performer.
Komatsu’s WA475-10, a 26-tonne wheel loader, has made a strong impact on Australian worksites since its release, quickly establishing itself as a versatile machine that blends power with advanced technology to o er e ciency and productivity for waste and quarry operations.
O ering an impressive 30 per cent improvement in fuel e ciency compared to its predecessor, the WA475-10 has become a preferred choice for hauling and loading tasks. It delivers an ideal combination of fuel economy, productivity, and operational ease, making it a valuable addition to any eet.
Nick Vrontas, Komatsu Australia’s National Business Manager, highlights the notable upgrades, including
Komatsu’s Hydraulic Mechanical Transmission (KHMT) that make the WA475-10 a standout model.
“ e KHMT is cutting-edge technology that enhances both power and fuel e ciency,” Nick says. “With variable speed control, operators can adjust the loader’s top speed based on speci c site needs.
“Additionally, the adjustable variable traction control minimises wheel spin on unstable and slippery ground, which is often encountered in waste and quarry sites.” is model also introduces enhanced power control, simplifying the process for operators to balance traction with lifting power. e loader allows for independent control of hydraulic speed via the hydraulic lever, while
boom speed can be adjusted using the accelerator pedal – creating a more intuitive experience for operators.
e WA475-10 features an optimised Z-bar linkage system, which boosts lift force and enables higher tonnes-per-hour productivity. Its hydraulic response time and the dumping or lifting operations can also be customised to t speci c job requirements.
Built to meet Tier 4 emissions standards, the WA475-10 engine provides high power at low engine speeds, with increased engine torque and overall performance. An advanced electronic control system manages air ow, fuel injection, combustion parameters, and aftertreatment functions. is results in optimised performance, reduced emissions, and enhanced diagnostic capabilities, making it both a powerful and environmentally responsible choice.
Beyond its core capabilities, the WA475-10 can be adapted to suit speci c applications – whether facing the demanding conditions of waste sites or the abrasive environments found in quarries.
Komatsu o ers customised solutions to meet various operational needs, from initial inquiry to post-delivery service, ensuring that maintenance requirements are met e ciently.
e WA475-10 has quickly proven itself across a range of Australian sites, bringing new levels of e ciency and productivity to waste and quarry operations nationwide.
For more information, visit: www.komatsu.com.au
Pure Environmental is a wholly Australian-owned company founded with the mission to transform the circular economy through advanced resource recovery. We believe in pushing boundaries and challenging norms in waste management, providing exceptional, innovative, and sustainable solutions. Scan Code
The versatility and performance of LiuGong wheel loaders is expanding its workplace experience across Australia, including into the yards of scrap metal recyclers.
Immix Integrated Metal Management has built a strong history in the scrap metal sector in Melbourne and regional Victoria, as well as into New South Wales.
In addition to Melbourne, the familyowned business has sites at Shepparton, Wangaratta, Hallam, Wodonga and Wagga Wagga.
e company has contracts with regional councils, helping to reduce scrap metal loads in land ll, has bins placed with numerous building and mining industry organisations, and collects scrap metal from the farming sector.
Most typical scrap metal is processed and exported, while recycled, non-ferrous material is generally sold locally.
At its Wodonga site, Immix recently invested in a LiuGong wheel loader for the rst time as part of its eet renewal.
A high-spec 835H model was selected by the company to join the working rigs at the site, which include excavators and material handlers.
e LiuGong loader works with a mesh screen to sieve dirt out of scrap
metal collections before processing, while a large bucket with grab also assists to push up and tidy the scrap metal piles.
LiuGong wheel loaders are renowned for their build quality, featuring Cummins engines, German-engineered transmissions, simple operation – particularly in relation to their electrical systems – as well as their performance and comfort.
e turbocharged and airto-air intercooled, six-cylinder,
Stage III Cummins engines o er speeds up to 40 kilometres per hour, while the countershaft, power shift transmissions provide four forward speeds and three reverse speeds.
e 160-horsepower 835H model at the Immix site at Wodonga o ers a 7.9-tonne tipping load and has chalked-up about 600 hours.
Comfort, visibility and safety have been other major focus areas for LiuGong with its wheel loaders and this has been recognised by the Immix team.
e 835H model has 360-degree surround handrails and anti-slip steps, leading into an ergonomic, fully pressurised cab with multi-adjustable arm rest, joystick and airsuspension seat. Cabs are similar on all loaders, also featuring curved, panoramic glass windows.
Branch Manager Tim Karpeles, who joined the business about 18 months ago after working in the defence industry, says there was some initial hesitation about jumping in a LiuGong loader from some of the company’s operators, but this was short-lived.
“ ey are certainly happy to get behind the wheel,” Tim says.
e LiuGong wheel loaders also incorporate easy-toaccess service points that allow for fast maintenance checks. Wide-opening engine hoods reveal the easy service points, while hydraulic hoses and air, diesel and oil lters can all be easily reached and quickly changed.
“We had to look into a few things with the setting up of the mesh screen and we re-routed some of the hydraulics to keep them out of the way, but otherwise we have had no issues or complaints,” Tim says.
Immix purchased the wheel loader through Paci c Machinery Group. Tim says the dealer completed the 500-hour service and had provided good support with the machine. All other services are completed by the Immix team.
LiuGong’s high-spec wheel loaders o er a range of extra features in addition to the standard models, including reversing fans, variable hydraulic transmissions, radial tyres, ride control, rear view cameras, larger buckets on some models, air suspension seats and auto lubrication.
Tim says Immix is considering further LiuGong machines to support a system for farm clean-ups it was hoping to progress into 2025.
For more information, visit: www.mcintoshdistribution.com.au
From standing-room-only conference theatres to a sold-out exhibition floor, this year’s Waste Expo Australia attracted more than 3000 attendees through the doors.
Our community needs this industry to be great.”
John Merritt Non-Executive Director of the Victorian Waste Management Association (VWMA), set the scene for two days of thought leadership, professional development, and industry-leading solutions.
John was speaking at the VWMA industry breakfast on day one of Waste Expo Australia, a showcase of everything that is “great” about the sector.
Held at the Melbourne Convention and Exhibition Centre, the 2024 event had a rm focus on resource recovery and the circular economy with 120 exhibitors and more than 100 speakers across 50 conference sessions.
Kicking o a packed plenary session at the Government and Policy eatre, sponsored by Sircel, was an industry leaders’ discussion about progress and future directions in waste management.
Tony Circelli, Chief Executive O cer Recycling Victoria, says the panel discussion and conversations across the conference demonstrated the exciting opportunities for the waste management industry to lead the charge towards a more sustainable future.
“Waste management has become a really important part of sustainability around how we recover material, how we reprocess it and how we turn it back into valuable materials that society needs,” Tony says. “Importantly, in that process, we create hundreds of jobs, as well as investment and growth. Waste Expo Australia is so critical in showcasing the industry’s technology, people, and aspirations, but also coupling that with government policy and programs.”
Tony had earlier told attendees at the sold out VWMA breakfast that two years since its inception, Recycling Victoria still has a clear purpose.
“ e waste sector is an essential service and economic driver. It’s nearly a $4.5 billion sector in Victoria alone,” he says. “We are focused on creating an environment to attract more investment and improve economic opportunity for the sector.”
Government policy and interaction was a particular focus at this year’s event, from the Government and Policy conference stream to the new Government Lounge on the expo oor, incorporating representatives from Environment Protection Authority Victoria, Sustainability Victoria, and Recycling Victoria.
Matt Genever, Chief Executive O cer Sustainability Victoria, says the Government Lounge was an amazing opportunity for attendees to interact directly with government.
“Individual businesses can’t change sectors on their own, so they need to
understand who’s out there and what are the opportunities for collaboration,” he says.
“I think the same goes for government. Myself and my colleagues, as well as local government need to understand the initiatives and innovations within this sector. An event like Waste Expo is so fantastic at bringing all those people together.
“It’s a real melting pot of energy and conversation.”
is year’s conference streams covered circular economy, government policy, waste-to-energy, commercial industrial and construction and demolition waste.
Dr Sarah King, GHD Technical Director, Circular Economy, spoke as part of the day two Circular Economy conference stream.
She says that the industry is in the midst of a paradigm shift from a focus on managing waste to activating the circular economy.
“Waste Expo Australia is well-placed to address the changes in our industry, particularly as we begin to treat waste as a valuable resource,” she says.
“As Australia shifts from a linear to a circular economy, events like this
play a signi cant role in demonstrating the potential for adding value to waste resources through new technologies and highlight the importance of regions and place-based circular economy initiatives.”
e exhibition oor was packed, with exhibitors making valuable industry contacts as well as adding to their professional development.
Brent Murray, Strategic Account Manager at TOMRA, says the exhibition is a key opportunity to connect with government and other interested parties.
“Being able to connect with industry is integral for suppliers so we can learn about what’s happening in the packaging space or the regulatory space,” he says.
“Whether it’s networking on the exhibition oor or being able to attend the conference sessions and hear from industry experts in those subjects, Waste Expo is really important from a professional development perspective for anyone who’s in the waste industry.”
It’s also a chance for attendees to get up close to some key industry equipment available from manufacturers and resellers.
On display this year was Komatsu’s 15-tonne excavator and a Rotar Grab attachment, Paci c Materials Handling’s Sennebogen material handler and the new 355E telehandler and Garwood International’s innovative DualPact split chamber compactor truck, which attracted plenty of attention.
Ian Pinney, from Garwood International, says the opportunity to display a tangible product creates conversations and connections with the right customers.
“We’ve had a lot of interest from people who have the product and people who don’t have the product, and they’re inquiring about its capabilities and how it could help them,” he says.
“For us, Waste Expo has helped to facilitate conversations with relevant waste collection users, contractors and councils, and we have tangible business leads to follow up from here.”
Exhibition Manager Sherri Pearson says that Waste Expo Australia has continued to grow thanks to its relevance, strategic industry partnerships, and ongoing adaptation to industry trends.
“ e event’s success is driven by its ability to bring together the most in uential players in the sector, and future editions will focus on expanding international reach and providing even more value to attendees and exhibitors,” she says.
“Next year’s event will have exciting enhancements, including targeted new content streams and the latest technologies being developed globally.
“As part of an international portfolio of events, Waste Expo Australia will feature an even larger international presence in 2025, making it the industry’s mustattend event.”
Waste Expo Australia will return to the Melbourne Convention and Exhibition Centre on 29-30 October 2025.
Stay up to date at www.wasteexpoaustralia.com.au
Some of the waste and resource recovery sector’s brightest minds were recognised at the 2024 Waste Innovation and Recycling Awards.
From an innovative recycling program using prisoner labour, to a dynamic founder with a visionary approach to resource recovery, and a world- rst recycling facility, this year’s Waste Innovation and Recycling Awards shone a spotlight on people and projects making a di erence.
Industry came together at a packed gala dinner held at e Trust in Melbourne’s CBD, to celebrate excellence across the industry.
More than 30 individuals and projects were shortlisted across eight categories, presented by respected media personality James O’Loghlin.
PROJECT – REGIONAL
Awarded to Queensland Corrective Services for its Environmental Management Recycling Program. Lotus Glen is the northern most correctional facility in Queensland.
In 2022 it commenced the Environmental Management Recycling Program, the largest recycling program in a correctional facility in Queensland.
Using prisoner labour, it diverted about 50 per cent of its waste from land ll. With 74 per cent of the population at Lotus Glen, First Nations, the facility is not only looking to protect the environment, but also provide training and opportunities for people on release.
e end goal is to use all resources available to reduce waste to the lowest possible level, o set carbon and provide opportunity to reduce recidivism.
PROJECT – METRO
Awarded to Waste Circularity Team – Frankston City Council for the implementation of its separate glass service.
Frankston City Council implemented
a separate glass service to all residential households in October 2023. e rollout was seamless due to planning and communication with the community, which included the implementation of a gender impact assessment, allowing for an intersectional approach to communications, and accurate data for service providers.
Accepting the award, a council spokesperson said the glass bin introduction had been a long journey and the project team was critical to its success.
“People at rst thought ‘why do we need a glass bin?’ But the outcome has been huge,” he said. “ e markets that we’ve created and supported by having a very clean product has been fantastic.”
He said the community had embraced the journey – of 50,000 bins distributed, just 20 have been asked to be returned in the rst year.
“Twelve months in, we’ve just recently had a community survey which has basically given us the ‘thumbs up’.”
Awarded to Rino Recycling for its new recycling facility.
Rino Recycling is a state-of-the-art construction and demolition waste recycling facility in Pinkenba, Brisbane, transforming 1.5 million tonnes per year of co-mingled waste into highquality recycled construction materials, including aggregates, road base, ll, and sands.
e facility is the world’s largest under one roof by volume and the rst of its kind globally.
Setting this facility apart is the integration of wet and dry processing technologies and automated processing, sorting, and separating technologies
to process diverse waste streams, enhancing waste recovery rates and e ciency.
It represents a ground-breaking step towards a circular economy by signi cantly reducing land ll and carbon emissions.
Daniel Blaser, MBA Rino General Manager, said there had been a lot of people pulling together to establish a world- rst facility.
“To take the lead in the industry and then be able to make it a success and do it on time and on budget in this current climate has been fantastic,” he said.
“ is award is a really big reward and recognition for our sta .”
COMMUNITY ENGAGEMENT SUCCESS, PROUDLY SPONSORED BY VISY.
Awarded to Bayside City Council for its Bayside Roving Repair Program. Bayside launched an exciting initiative focused on reducing waste by encouraging repair and reuse rather than throwing items away.
e program started a repair culture across Bayside, giving the community opportunities to repair items destined for land ll, while building knowledge and social connections through events.
A council spokesperson said a series of repair workshops, supported by volunteer repairers, taught the community how to repair everything from textiles, to electronics and even bicycles.
“We encouraged accessibility and throughout the program ran workshops in a variety of locations across the municipality,” the spokesperson said.
“We really wanted to promote a circular economy and it was a raging success. I’m really proud to receive this award.”
YOUNG PROFESSIONAL OF THE YEAR, PROUDLY SPONSORED BY REMONDIS AUSTRALIA.
Awarded to omas Anton, from Repurpose It.
omas, head of customer experience at Repurpose It, is driven by his passion to provide circular outcomes for customers. He manages the entire customer experience, including the front line of communication, ensuring a positive experience, and fostering long-lasting relationships with customers.
With 15 sta in customer-facing roles across the business, setting expectations and building leadership and autonomy has been paramount to omas’ team’s success.
e team works across multiple sites – Epping, Montrose, and Hallam, and omas actively participates in the dayto-day activities of all sites ensuring sta are engaged and supported.
Awarded to ReSource for pioneering ethical and innovative recycling. Recognising that the old way of recycling e-waste isn’t enough to tackle the volume of e-waste and process it as e ciently and sustainably as possible, ReSource has invested in technology to raise the standards.
e e-waste specialist has introduced new technology, including Arti cial Intelligence (AI)-driven battery sorting, recycling of alkaline and zinc carbon batteries, as well as high-e ciency recycling for low-value items.
It has implemented dual-stage activated carbon lters to ensure heavy metal or volatile organic compound (VOC) emissions from its processing don’t enter the atmosphere. It’s also implemented AI-powered thermally activated re cannons to stop any res that might come from e-waste.
ReSource is the rst company in Australia to be energy negative in processing, due to its 860-kilowatt solar system.
Awarded to Vanja Marjanovic from the City of Melville.
Vanja is the Waste Co-ordinator at the City of Melville. Since moving from Croatia to Perth in 2000 to escape con ict, she’s learned English, completed her studies and quickly risen the ranks of the waste industry.
Industry peers know her for her ability to improve operations, align strategy and respect and support her sta .
Vanja is responsible for overseeing a team of 30, more than $10 million in eet, a further $5 million in assets and plays a key role in behaviour change, best practice innovative waste management and expert guidance on waste management plans to internal and external stakeholders.
She also ensures e cient contract management and contributes to the development of annual operational and capital budgets for the department.
Accepting the award, Vanja said each day o ers the opportunity to make small adjustments and help those around you feel valuable, heard, respected and appreciated.
“My intentions are to continue to motivate woman, and those underrepresented groups to chase careers in the industry,” she said.
“ e goal is to build a legacy where success is determined by talent and hard work not by gender or background. My team at Melville allows me to accomplish all these tasks to create a better workplace experience for everyone.”
Awarded to Narelle Anderson from Envirobank
Narelle is the Founder and Managing Director of Envirobank, a company revolutionising recycling in Australia.
Narelle has championed innovative solutions to combat waste, fostering a culture of sustainability. Her leadership has positioned Envirobank as one of the leaders in environmental stewardship, implementing cutting-edge technology and consumer-friendly initiatives to enhance recycling e ciency.
She said that after 16 years at Envirobank and nearly 30 years in the recycling and sustainability industry, the journey had been one of constant learning and growth.
“You can’t be a leader without a fabulous team, and I want to acknowledge all the people that I get to work with at Envirobank,” she said.
“ is award is a re ection of the amazing team and community that have supported and inspired me every step of the way. Together, we’ve been able to drive change, push boundaries and work towards a more sustainable future.”
Fornnax SR-MAX2500 is a tailor-made and multi-purpose machine for the volume reduction of the most rigid materials.
The SR-MAX2500 primary shredder is aimed at largescale municipal waste recyclers, cement plants, waste-toenergy plants, mechanical biological treatment facilities, materials recovery centres, construction and demolition recyclers, aluminium recyclers, and other applications requiring high-capacity machines and robust technology.
It combines ripping and shearing technologies to shred, tear, drill, cut, split, crush, break, and reduce the size of materials.
A high-capacity machine, it boasts advanced engineering and technology, featuring hydraulic motors driving each shaft for optimal power and torque.
Its unique cutter design, replaceable cutting table, and shaft design make it a suitable solution for various applications.
The output size can be controlled by using different knive thicknesses, and there is a wide range of shredding capabilities to handle various materials.
A specific Stop-Auto-Reverse feature controls feeding according to load percentages for high efficiency and protect against damage.
The Wastech Bin Wash unit is a safe, efficient and effective way to clean 120-litre, 240-litre, 660-litre and 1100-litre bins.
The bin lift mechanism lifts and holds bins at an angle to promote efficient washing and water drainage, while two rotating spray heads, mounted on fixed arms, spray high pressured water to wash all interior spaces of the bin.
A hand-held lance, included in the system, can be used to wash off the exterior of the bins and wash down the surrounding area.
The lance connects to a 20-metre retractable hose for manoeuvrability, convenience and flexibility.
Mobile and easily moved, the bin wash unit operates with hot and cold water (detergent can be added if required).
The cycle time of the washing sequence is 20 seconds and it’s capable of washing one 660 or 1100-litre bin or two 120-240-litre bins simultaneously.
All surfaces of the bin wash unit are fully galvanized to avoid rust.
The IFE flip-flop screen is suitable for screening difficult to handle material including construction and demolition waste, sand and gravel, municipal waste, compost, and shredded materials, where conventional screening machines may become blocked or stuck.
The unique three-phase oscillation of the TRISOMAT screen ensures rapid break-up of the material in the feed area, efficient screening in the central area and improved material destratification and ‘near-size’ screening in the discharge area.
High acceleration being generated by stretching of the screen mats and over expansion of the openings result in almost clog-free screening.
The screen mats can be bolted or keyed alternatively and come in a variety of sizes specifically designed to guarantee specification requirements are met while maximising throughput.
The JCB 427 Wheel Loader is a powerful and versatile machine. With its robust construction, and advanced features it’s well placed for handling heavy loads and demanding tasks in waste management facilities.
A powerful engine provides ample power and torque to handle even the heaviest loads, including large piles of waste and recycling material, ensuring that the machine can efficiently move materials around a facility, maximising productivity and minimising downtime.
Its durable components and heavy-duty frame are built to withstand the harsh conditions of the industry, ensure long-lasting performance and reliability.
The JCB 427 also offers a range of advanced features that enhance its performance and operator comfort.
These include a spacious and ergonomic cab with excellent visibility, a powerful hydraulic system for precise control, and a variety of attachment options to suit different waste handling tasks.
2nd
Mike Ritchie, Managing Director, MRA Consulting Group, has the last word for 2024.
There is a lot of news about individual companies innovating, developing and introducing new initiatives and as an industry we should be very proud of that.
But is this innovation making much of a di erence compared to the challenges we face? Not much if truth be told.
At best we are holding our own against a ood of waste, rising industrial emissions and stagnating recycling rates. Why?
Because governments are not innovating at the same rate that private companies are. In fact, governments across Australia are seriously lagging the demands of industry for reform.
How many parliamentary inquiries do we need to have before we will see some serious structural reform in the waste/recycling/circular economy space?
How many government “discussion papers” do we need to read, full of “motherhood and apple pie” statements of intent, but with no substance and no actionable reform.
Here are some basic facts which every minister should be aware of:
1. No government will achieve the National Waste Targets for 2030 based on current policy settings:
a. 80 per cent diversion from land ll.
b. 50 per cent reduction in organics to land ll.
c. 10 per cent reduction in per capita waste generation.
2. South Australia will go the closest with its construction and demolition (C&D) sector and possibly commercial and industrial (C&I) achieving the 80 per cent diversion gure. Western Australia may go
close with municipal solid waste (MSW) as the new incinerators re up. (Yes, that is counted in the 80 per cent).
3. No government will achieve the 50 per cent reduction in organics to land ll.
4. No government will reduce per capita waste generation. In fact, since the 2019 announcement of the National Waste Policy, per capita waste generation has grown by two per cent (rather than falling by 10 per cent).
5. National aggregated recycling rates have stagnated at 60 per cent of waste generation for at least ve years. We are swamped by growth in waste generation.
e challenge is for governments to get back onto the reform bus. ere have been some rays of sunshine, so rather than be too critical, let’s start with some positives: Levy – Queensland, Victoria and Tasmania have announced further increases in the land ll levy in
real terms. at creates the economic environment for investment. ey explain the investment in C&D processing but are not high enough yet for C&I processing or most Commercial Food collection.
Higher levies shift the behaviour of waste generators, although hypothecation increases would be a bonus.
Organics – Many governments have mandated three-bin Food Organics Garden Organics (FOGO) for household waste. at is a good start, but it is not enough.
e recovery rate for MSW food is still about 60 per cent compared to 90 per cent plus for garden waste.
A big acknowledgement to New South Wales, which has mandated commercial food collection to start July 2025. Other states need to follow.
Energy-from-Waste – Western Australia has two shiny new incinerators coming on line. Hopefully they will show the Australian community that
incineration is a viable and responsible alternative for the disposal of truly residual waste. And I mean residual waste after the recyclables have been extracted including all organics.
So, three-bin systems (recycling, FOGO and MSW) plus additional pre-sorting, should be mandatory precursors of incineration. Again, a big acknowledgement to New South Wales.
If we are going to achieve the National Waste Targets, we will need to recover an additional 18 million tonnes (MT) per year, on top of the 40 MT we are recycling now. e gap is already 11 MT on where we need to be. at gap will grow with population growth and per capita consumption growth between now and 2030.
Put simply we are treading water at best and going backwards at worst. e thing that really upsets me about the slowness of reform is the missed opportunities for cheap and easy emissions abatement.
We are sleepwalking towards climate chaos. e waste/recycling/ circular economy sector o ers enormous greenhouse gas abatement opportunities that are largely unrecognised.
Go to most greenhouse reports and you will see that “waste” represents three per cent of Australia’s direct emissions. For that reason, it is largely ignored.
But what those direct emissions don’t tell you is that the waste sector can reduce EVERYBODY else’s emissions.
e embodied energy stored in an aluminium can, a car body, a plastic bottle, cardboard etc all contribute to reducing the emissions in the industrial sector (not the “waste” sector). ese savings go unrecognised re policy reform. It frustrates me senseless.
e sector can easily abate more than 10 per cent of Australia’s total emissions. And yet we ignore it.
What do we need to do?
1. Stop land lling organics (10MT of current emissions).
2. Capture all the gas from land lls (11MT of legacy emissions per year).
3. EfW of residual waste – o setting at least 10 MT of coal emissions.
4. Embodied energy – through better recycling (10 MT at least).
5. Circular economy – savings in manufacture (gazillions of tonnes; currently unmeasured).
6. Sequestration – of compost and biochar in soil (estimated 100 MT/ year or higher).
Our policy makers have not realised the potential or seen the jobs and abatement opportunities.
What do all governments need to do (and this is a minimalist list):
Investment
1. Increase the levy in real terms and forward announce those increases.
2. Take the levy and grants to a level that gets us the infrastructure we need to hit the targets.
3. Release infrastructure plans to guide investment.
Organics
5. Mandate three-bin FOGO.
6. Mandate Commercial Food (COFO) separation.
7. Ban organics to land ll (including cardboard, pallets and wood).
8. Set new minimum standards for FOGO contamination.
Land lls
9. Mandate gas capture and aring at all land lls above say 5kt carbon dioxide equivalent per year (CO2-e/ yr) emissions.
10. Set minimum operating standards for all land lls and apply a levy to all (even if it is a di erential levy)
Markets
11. Amend the export bans to make them export quality standards (we need the overseas markets).
12. Set higher standards for FOGO compost so we don’t wreck the existing markets.
13. Accelerate research and development funding to grow domestic markets. Recycling
14. Kerbside Recycling – standardise yellow bin materials.
15. Packaging – national mandatory EPR scheme, eco-modulated levy, recycled content and bans on nonrecyclable materials.
16. Container Deposit Scheme –increase rebate to at least 20 cents and include wine and spirits.
17. EPR – make all schemes mandatory to eliminate the free-rider problems and expand to a wider range of products.
18. Legislate the “right to repair”.
19. Develop a circular economy plan that has force (not just motherhood statements).
It is not hard to do but it does require government ministers to tell their departments that they want reform. It requires us to tell ministers (loudly) that we demand reform. It will not happen by osmosis or business as usual.
For more information, contact: info@mraconsulting.com.au
We recycle almost 20 million used tyres from across Australia each year. Whether helping industries reduce their reliance on fossil fuels, or creating more sustainable roads and surfaces, our products are having a positive impact on our world daily. 20 million reasons why we’re making a difference
To learn more scan the QR code or visit tyrecycle.com.au
Efficient and quick waste handling
Ideal for large amounts of materials.
Due to the wide Sliding Door of 1.82 metres and deep chamber of 1.1 metres, there is no need to break down boxes before loading.
The compacted bales are optimised for transport because they can be stacked two and two.
Additional Highlights
■ Extra-large chamber
■ 8 wire tying for a more stable bale
■ Compacted bales measure 1825 x 1066 x 1200-1300 mm