
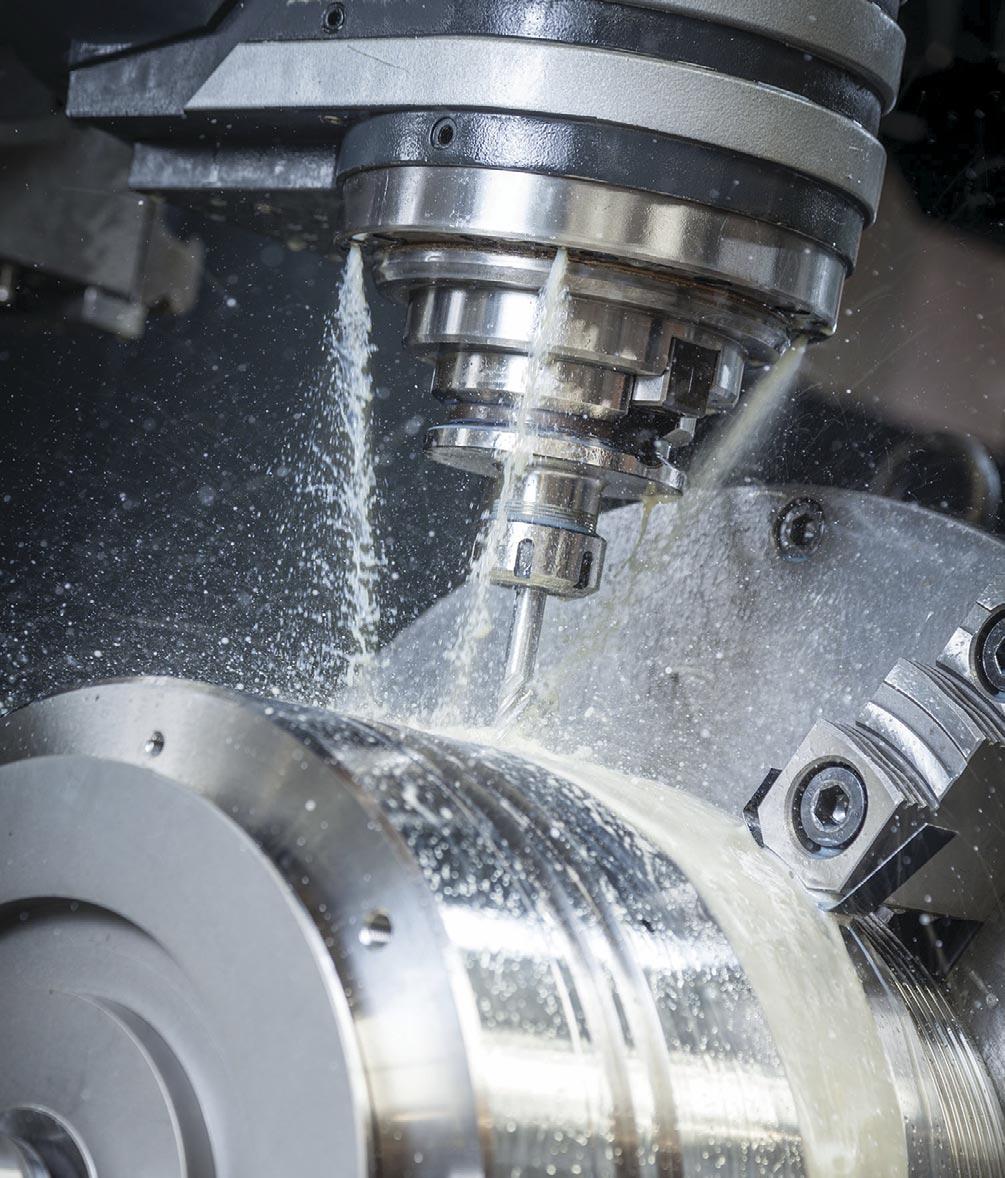
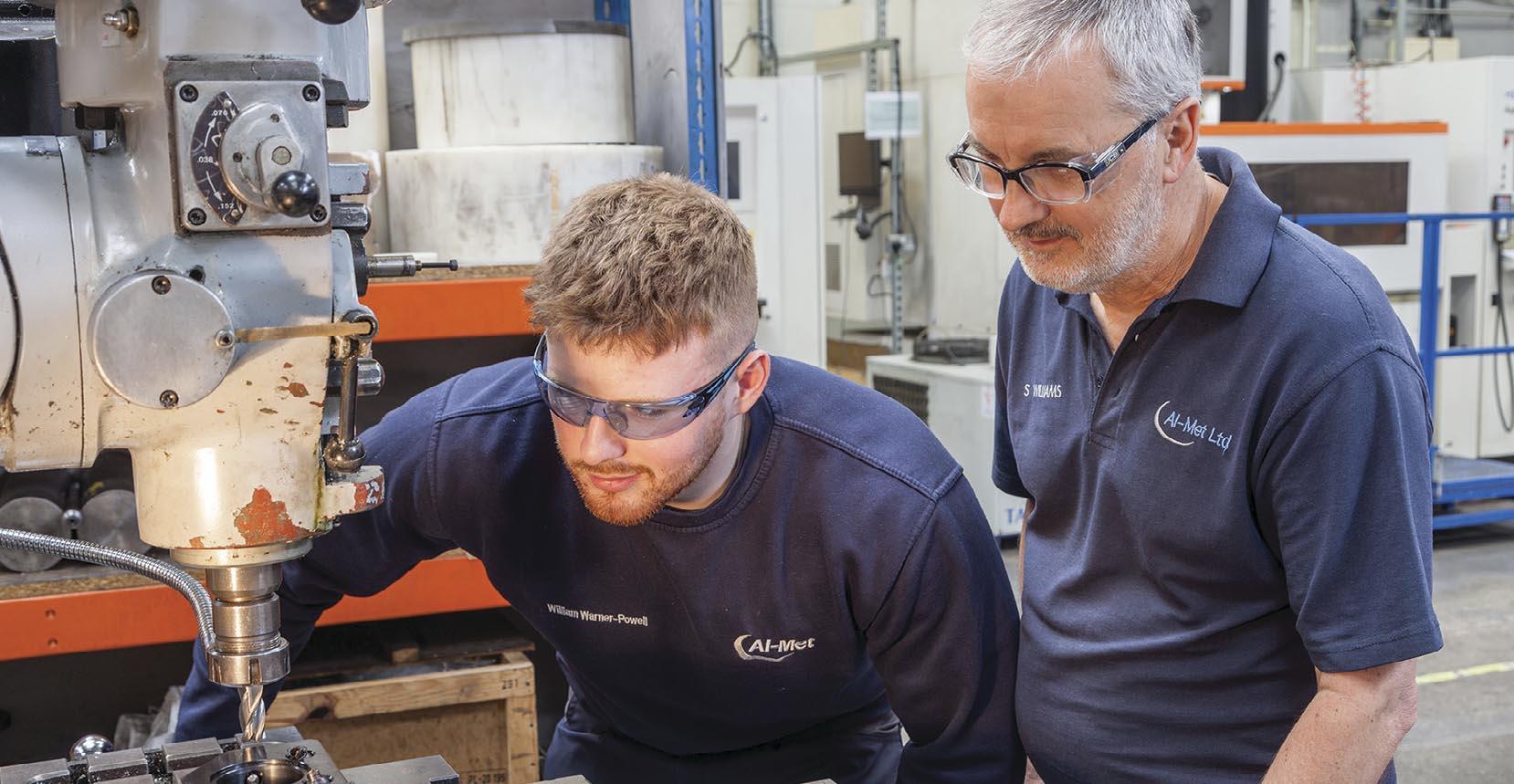

With a dominant presence in high-stakes pressure systems supply and over a century of market leadership, Chesterfield Special Cylinders remains one of only a few such companies worldwide in this challenging field. A leadership team drawn from across its parent company, Pressure Technologies plc, spoke to Richard Hagan about how the group has built on its impressive legacy and continues to remain at the pressurised edge of its end markets.
Chesterfield Special Cylinders, based in Sheffield in the UK, is a world-leading designer and manufacturer of highintegrity, safety-critical components and systems, including both standard and bespoke pressurised gas containment solutions, serving global supply chains in oil and gas, defence, industrial gases and hydrogen energy.
The company’s history spans over 125 years’ worth of develop ments that are not only fascinating but also integral to the company’s presently highly specialised engineering capabilities.
Forged amidst Victorian steam power Chesterfield Special Cylinders can trace its origins back to 1897 when Universal Steel Tubes Ltd was formed, occupying two acres of land in Chesterfield, and having 180 employees at its peak.
In its early years, it manufactured boiler and economiser tubes as well as cylinders for compressed gases and cold-drawn steam pipes for naval construction. Meanwhile, the company also pro duced shell forgings for the ongoing Boer War.
Nearly a decade later, Universal Steel Tubes became the Chesterfield Tube Company Ltd, established in December 1906. Its director at the time, Joe Trevorrow, produced the firm’s first drawings for seamless cylinder manufacture from hot pierced billet. This idea would go on to totally revolutionise the manufac turing process of such cylinders.
That would prove to be the first of many such innovations developed by the company which by the late 1930s, was enjoying increasing demand for its products. So much so that in 1939 the company celebrated the manufacture of its one-millionth cylinder.
Over the following decades, the organisation went through several name changes and various evolutions in terms of its manufacturing capabilities until 2004 when Chesterfield Special Cylinders, in its present form, emerged.
In 2005, Chesterfield Special Cylinders relocated from its original home in Chesterfield to its present location in Sheffield at a cost of £1.5 million. The move delivered a 100,000 sqft factory situated on 4.4 acres, vastly improving the company’s productivity and production capacity.
Public listing of Pressure Technologies plc on AIM in 2007 sig nalled the beginning of a new era that would see the company grow substantially through strategic acquisitions with the forma tion of its Precision Machined Components division.
The first was a 2010 acquisition of flow control component spe cialist Al-Met, forming the first member within the company’s new Precision Machined Components (PMC) division. Next was the acquisition of specialist machining service provider Roota Engineering in 2014, followed in 2017 by spherical ball valve grinding specialist Martract.
The capabilities of each site within the PMC division are highly specialist, as Shaun Newby, Sales Director for PMC highlighted: “These brands are leaders in their markets, with world-class lead t imes, specialised precision engineering skills and a blue-chip customer base.
“We pride ourselves on evolving alongside our customers’ needs and working closely in partnership with them on the development
of technical solutions for their specific end-product applications,” he continued. “These applications serve primarily the oil and gas market. We supply key components made from super alloys, manu factured to exacting standards and tolerances, and destined for extremely challenging environments like subsea oil exploration and wear parts for offshore and onshore oil production.”
Supporting safety Stephen Butler, Sales Director for Chesterfield Special Cylinders explained: “Our high-pressure cylinders are safety-critical compo nents for a number of applications, from high-pressure systems in n aval submarines and surface ships, to oxygen cylinders in aircraft.”
Of course, that list is far from the only uses for these cylinders, but it illustrates the critical nature of these products. The superior reliability and durability of steel cylinders is ensured through periodic inspection and maintenance.
In addition to the design and manufacturing of safety-critical pressure systems, Chesterfield Special Cylinders delivers highly specialised inspection, reconditioning and recertification services for its global customer base.
Integrity Management services can be deployed in situ for sys tems where cylinders cannot be easily or cost-effectively removed for periodic inspection and testing. These services are based on years of experience and the use of specialised equipment and inspection procedures that help maximise the availability of sys tems and support safe operations to demanding international standards standards that Chesterfield Special Cylinders also helped develop.
Inspection teams work all over the world and in a variety of operational environments to get the job done, according to Dan Nuttall, Inspection and Testing Services Manager for Chesterfield Special Cylinders: “Our Chesterfield team has carried out a number of challenging in situ inspections, including one example in which they conducted a complete inspection and test regime while a ship was crossing the Atlantic.”
The products produced by Chesterfield Special Cylinders are highly recyclable, being primarily made from high grade steel alloys. As Stephen Butler revealed: “Our products can be easily reconditioned, and their lives extended over many years. About 90% of the raw material we use is itself recycled.”
Though its products are highly recyclable, Chesterfield Special Cylinders’ other sustainability win is the ultra-long lifespan of its cylinders, according to Naval Programmes Director, Lee Lawrence: “The lifespan of our cylinders is a definite strength to our customers because with regular inspection and maintenance, the cylinders keep going for decades. Our Integrity Management service ensures through-life support for optimal longevity of the product.”
“We have cylinders that have been in service for 85 years for the storage of hydrogen,” Mr Butler said. “It’s a great testament to the longevity and reliability of our products, and it makes great commercial sense for our customers in terms of their total cost of ownership.”
Hydrogen is, of course, the focus of many energy sustainability efforts globally. Chesterfield Special Cylinders intends to continue innovating to remain at the forefront of providing static and mobile pressurised hydrogen storage long into the future.
“Hydrogen has been an important part of our business for over 85 years,” said Mr Butler, “and we are excited to see the rapidly growing demand for new hydrogen applications that require pres
surised storage. We understand the market and the importance of safe operations which is why we’re seen as the partner of choice by our customers.”
Chesterfield Special Cylinders provides complete ‘plug and go’ sys tems globally, supplying the entire solution including key elements such as cylinders, manifolds, valves, and through-life maintenance.
“This turnkey approach has served the company well because oil and gas majors, in particular, need a trusted partner to deliver a complete solution,” Mr Butler revealed. “A further factor is our strong presence in the global defence industry. Working with the sector’s prime contractors adds further credibility to the standards that we work to.
“We’re looking forward to the next four or five years, which we already know will be full of interesting opportunities,” he concluded. “That’s the excitement that keeps us positive for our future.” n