

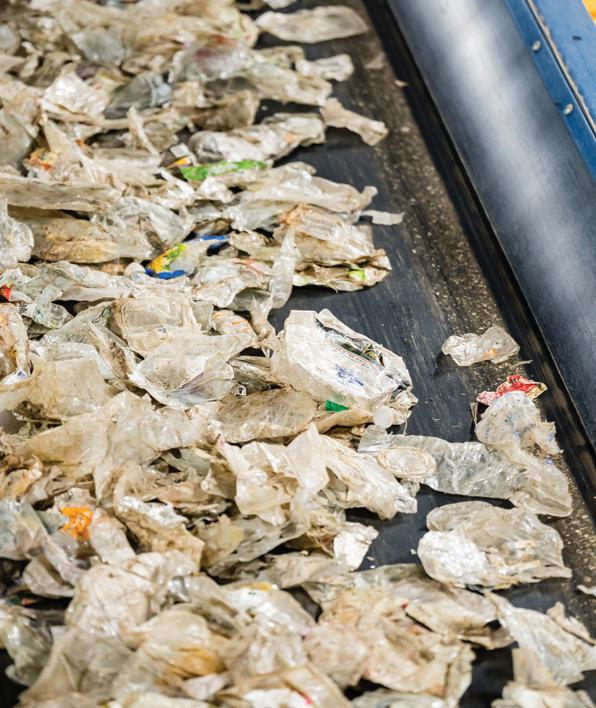
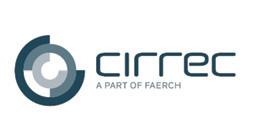
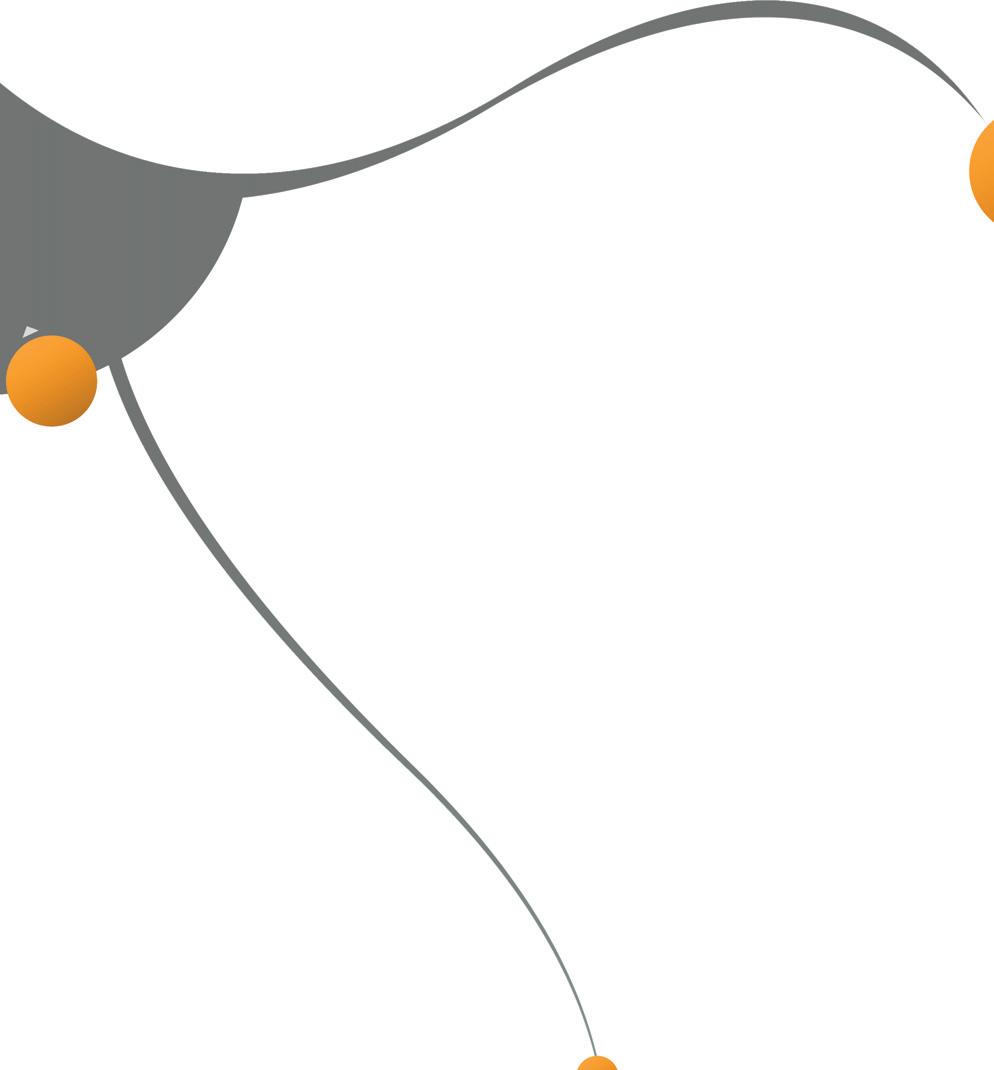
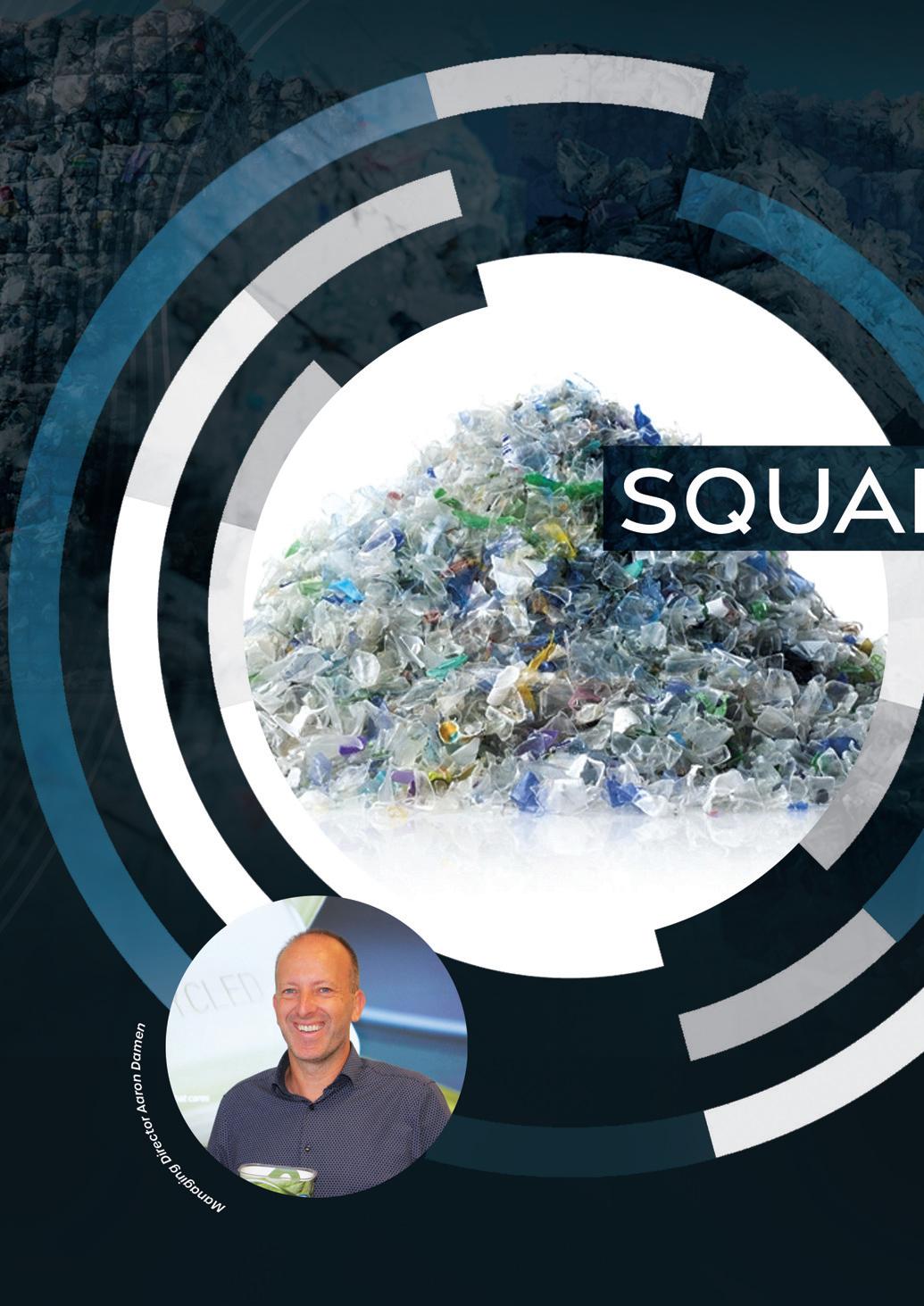
Cirrec is a front-runner in European PET recycling. The company uses its technology to regenerate household waste and produce raw materials for food-grade packaging, thereby closing the loop on PET packaging. Hannah Barnett spoke to Director of Recycling Aron Damen to learn more about this innovative and important process.
Where others see waste, Cirrec sees a valuable resource.
The Dutch company takes back waste material and revitalises it, ensuring that energy is saved and valuable materials are kept in the economy and out of the environment. Rigid food packaging products that contain up to 100% post-consumer recycled PET reduce their CO2 footprint by more than 50% with this process.
“This technology does not exist in the UK yet, but we want to expand it all over

Europe,” said Aron Damen, Director of Recycling. “Food packaging products are used, on average, for eight days. That means producing something that’s only valuable to society for eight days. It’s such a short lifespan and most people use two or three of these things per day. So, it is important that it’s sorted and recycled properly.”
Tray recycling
While Cirrec has been recycling bottles for several years, it is now focused on popularising its innovative tray-to-tray process. This reflects how, over the last
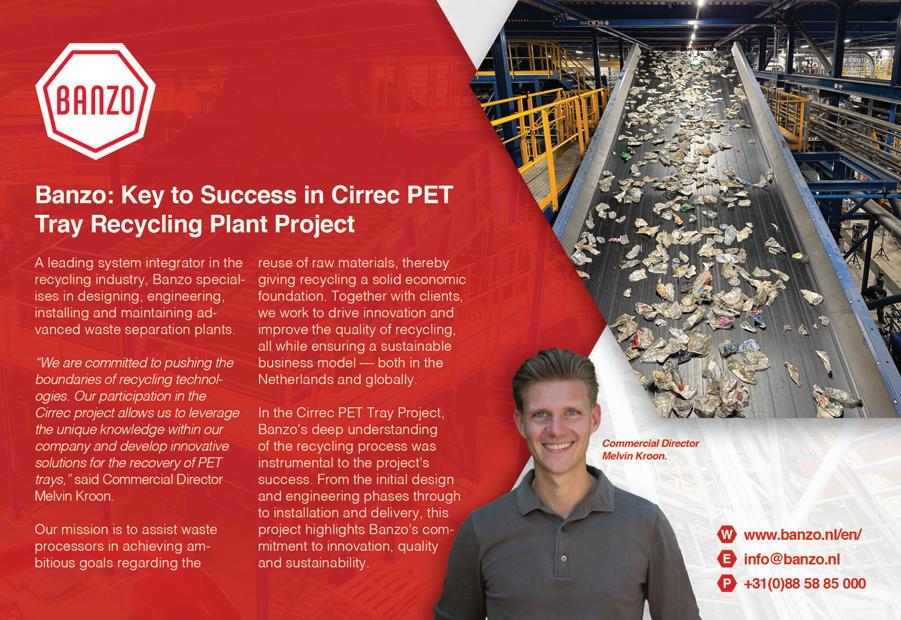

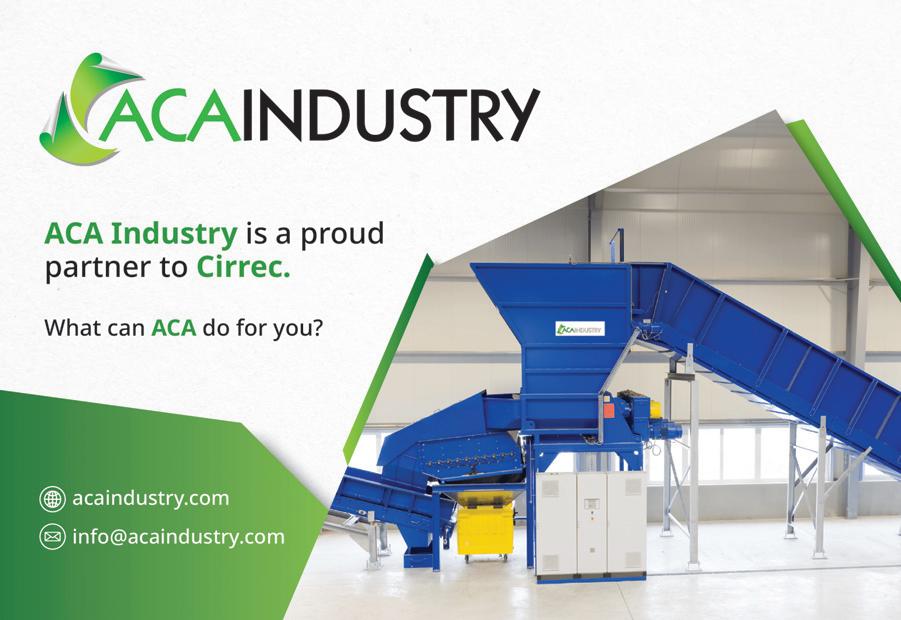
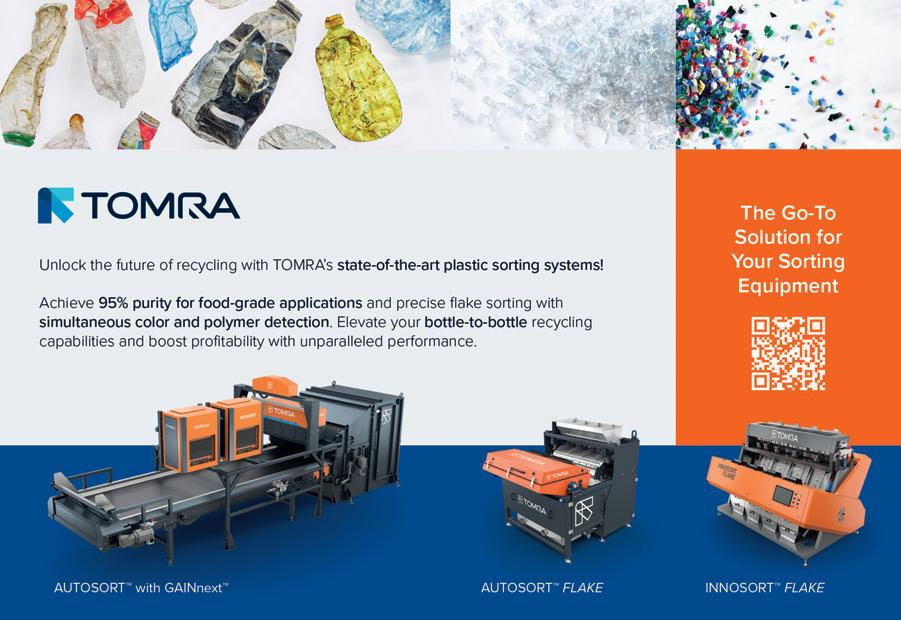
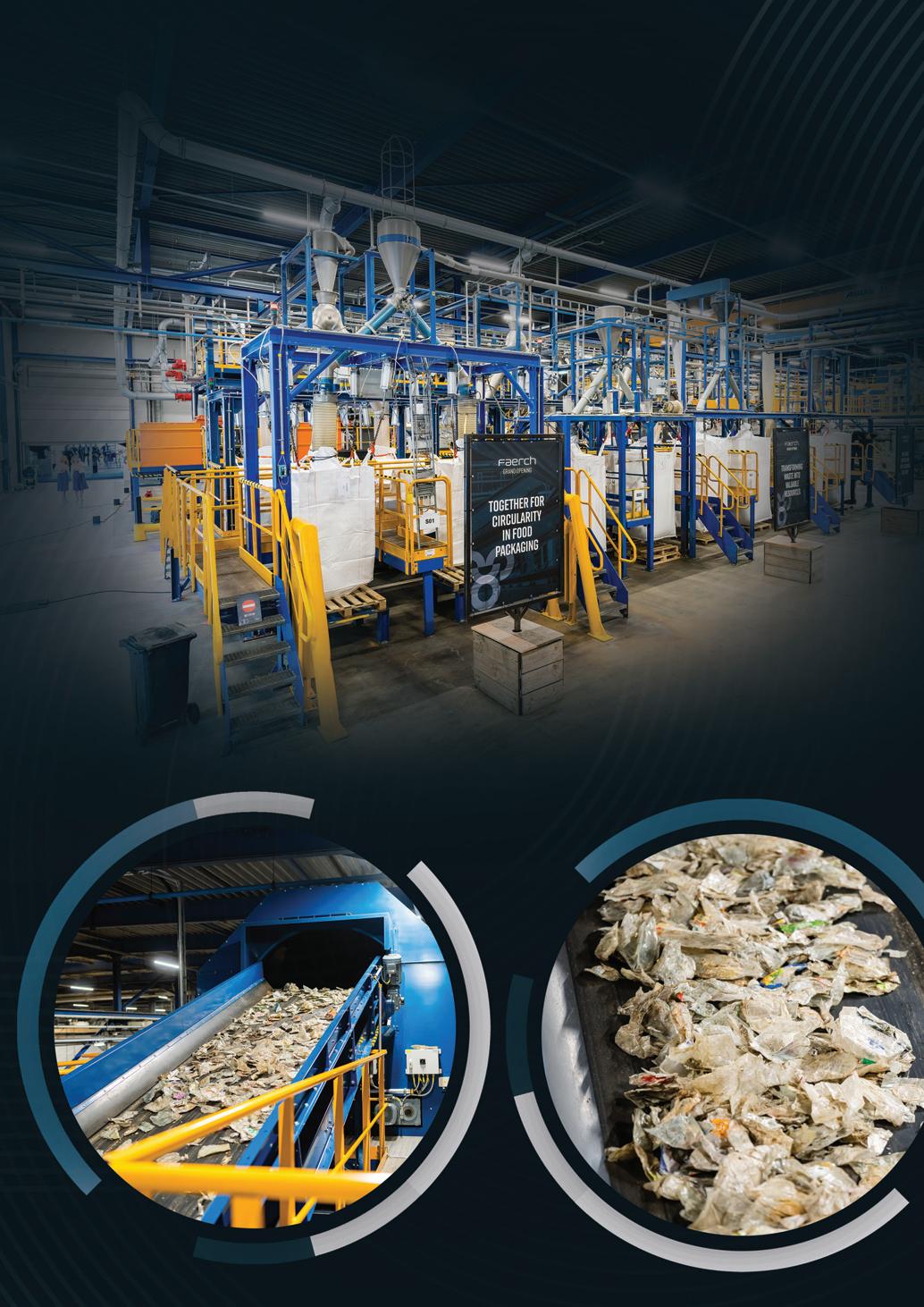
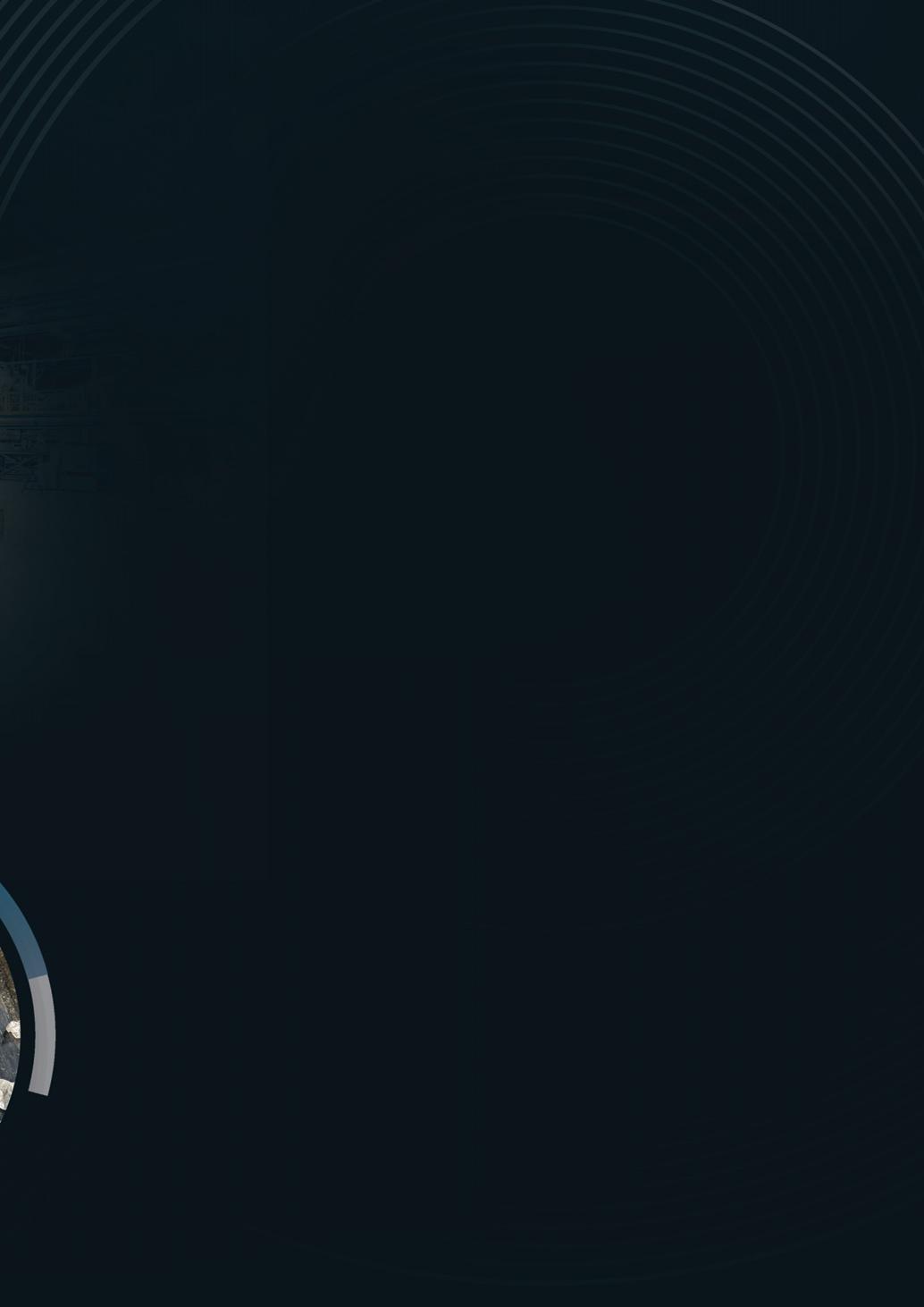
decade, the PET market has evolved significantly from virgin material to post-consumer recycled content.
Due to Extended Producer Responsibility (EPR), the European bottle industry is obliged to implement 25% recycled content by 2025 and 30% by 2030. This will be a game-changer for the European circular economy and will cause a shortfall in supply of recycled PET material from bottles. Tray-to-tray recycling will ensure an additional circular outlet for the valuable material.
Cirrec began operations recycling 24,000 tonnes per year and has recently added a new line allowing up to 60,000 tonnes: the annual equivalent of roughly three billion pieces of packaging. By 2026, the company intends to be recycling 200,000 tonnes every year. “Since we are the only ones doing tray-to-tray on a large scale, we’re saving that amount from incineration or landfill,” said Mr Damen. “And we are expanding.”
Cirrec has been part of Faerch Group since 2018, a global pioneer in rigid PET food packaging. Faerch’s packaging solutions are designed for recycling in a circular economy while meeting the highest food safety standards.
“We have already achieved circularity in the Netherlands and Belgium,” said Mr Damen. “We can recycle a food tray and make a new one out of it. From next year, we will also open plants in several big European countries. Three years ago, this technology didn’t exist. But now, we must make sure we have feedstock for our business.”
The process
In response to this growing need for raw material made from PET, Cirrec has invested tens of millions of Euros into perfecting its tray-to-tray recycling process.
“It’s not so different from bottle recycling,” Mr Damen explained. “A post consumer tray bale is firstly divided into its components and anything that shouldn’t be there, like PVC or Polystyrene, is sorted . Then we grind it to flakes about a centimetre thick and wash them to remove all the labels and organic waste.”
The main difficulty with tray-to-tray comes from the multiple layers of material, usually made for easy sealing or for better food preservation, which must als o be separated. This is followed by a final rinsing of the PET flakes.
“The last step is always decontamination and pelletising,” Mr Damen added. “That’s what makes the product foodgrade. It is heated and all the volatile materials are extracted. Then the product is put through a very fine screen to take out anything that shouldn’t be there, like wood and small glass particles. After that, it’s EFSA-approved.
“Bottles are quite tough and flexible, but trays are brittle. If trays go through the bottle line, they will turn to dust, because there’s so much friction.
So, tray-to-tray recycling must be treated gently - but not too gently, because we need to be able to lop off the multilayers. Getting that balance right is the secret.”
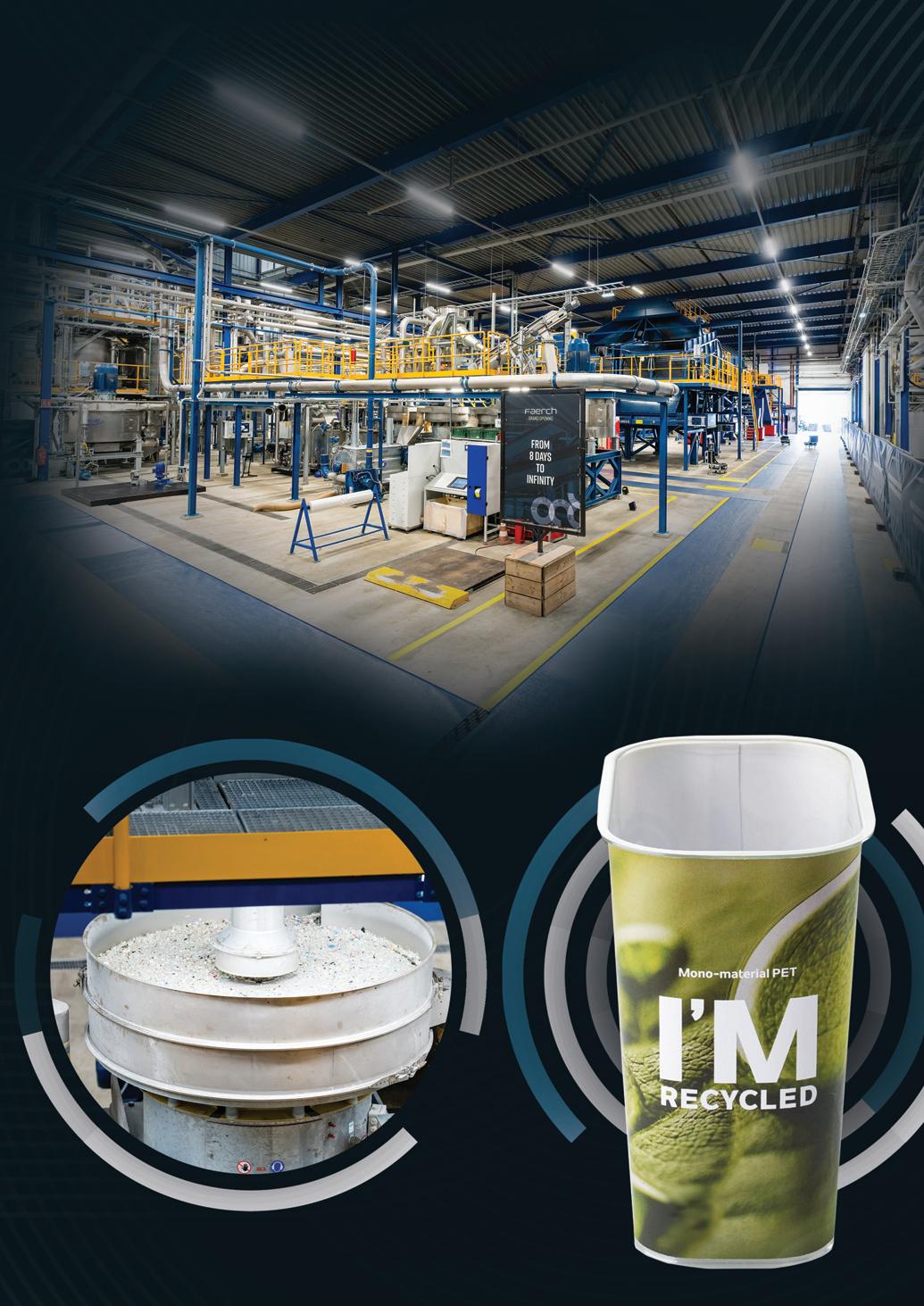
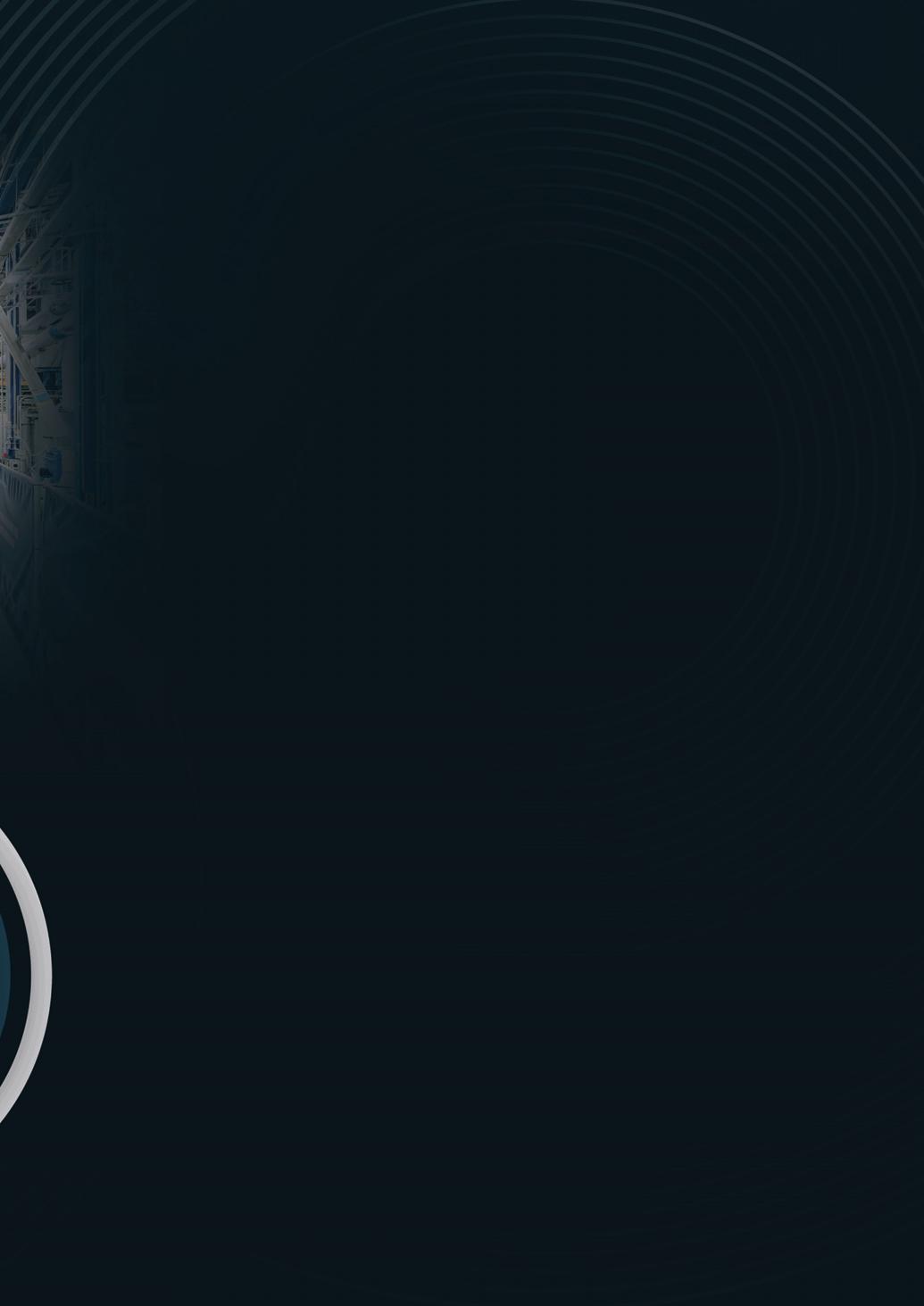
Forming partnerships
Cirrec receives post-consumer food packaging from waste managers across Europe to produce its PET flakes and pellets. Faerch packaging plants then use the food-grade product to produce new packaging.
Being integrated within Faerch has proved an invaluable advantage for Cirrec, as all its supply goes directly to the mother company. But there are still strides that need to be taken to popularise this recycling process more widely.
“Being circular requires post-consumer waste,” said Mr Damen. “We want to ensure that the infrastructure and EPR systems are ready. When we started, we had to throw away 70 per cent of the material and pay for the privilege; there was so little PET, it was not a viable business case.
“In some places, the sorting centres are still not equipped to remove PETtrays, so it is going into incineration. When new sorting facilities are built, they need a PET tray faction, because installing them afterwards is expensive and difficult.”
The company works with major retailers and brand owners across Europe, including Ferrero, Tesco, Aldi and Greggs, to develop a circular stream and convert non-recyclable into recyclable packaging.
“An example is the Sprite bottle that was designed label-free” Mr Damen explained. “The logo and other information were embossed in the material. There’s a big appetite for sustainable packaging in the industry; everybody’s working on it. But cost is still an issue for most companies, except for a few front runners who really want to invest in sustainability.”
Unlike a bottle, which is usually relatively light on contamination, only half of an average tray bale has usable PET, making it more difficult to recycle. “The more rubbish in a tray bale, the more expensive it is because that must be removed,” said Mr Damen. “Plus, a recycled tray will not look as clear as one in the supermarket made from virgin material.
“But it’s mindset that needs to change; sorting will never be 100 per cent efficient, but this is the future. There will always be something that causes a small deterioration of quality. It’s the same with bottles, but with trays it’s worse.”
To further promote a shift in outlook, the company also supplies CPET, a crystalline material used as an alternative to aluminium trays. This comes under Cirrec’s coloured division, as it is keen to dispel the myth that clear recycling is the only standard.
For Mr Damen, Cirrec’s operation is simply one that makes sense – for himself, the business and the most importantly, the planet.
“I’m quite sustainable by nature,” he concluded. “I shop in a packaging-free store using my bike and not my car. So, I was hesitant to work in the industry until I read more about what Cirrec was doing, and I realised it was something good for the world. Then I felt like I was contributing to a better future for my children, which continues to motivate me. It’s not about the money. Of course, there is money to be made, and we will not do it for free, but change for the better is my intrinsic motivator.”
n
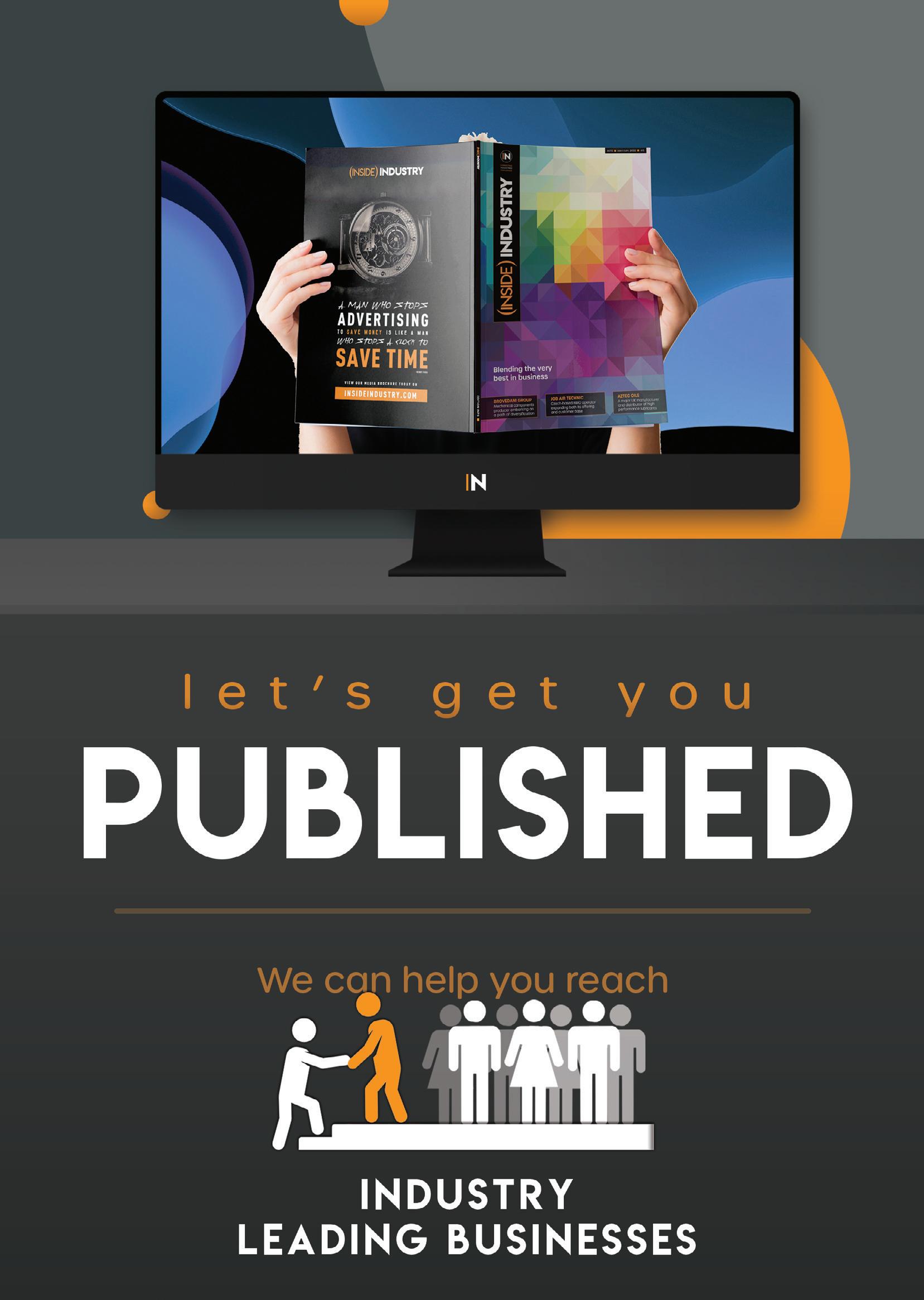
