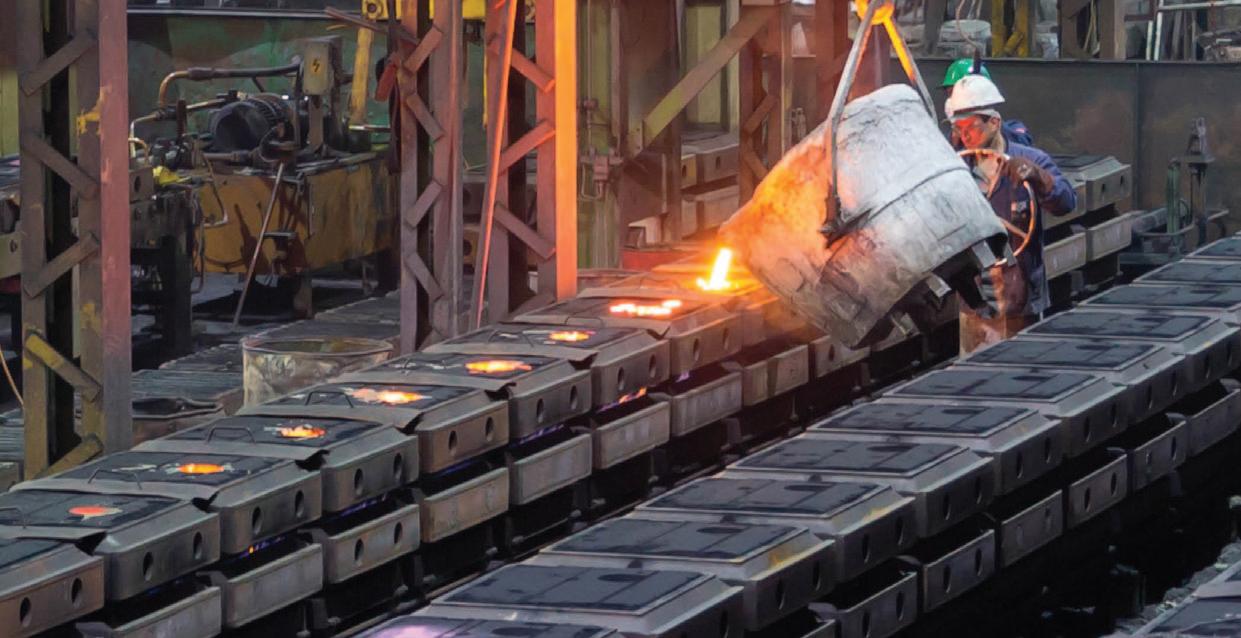

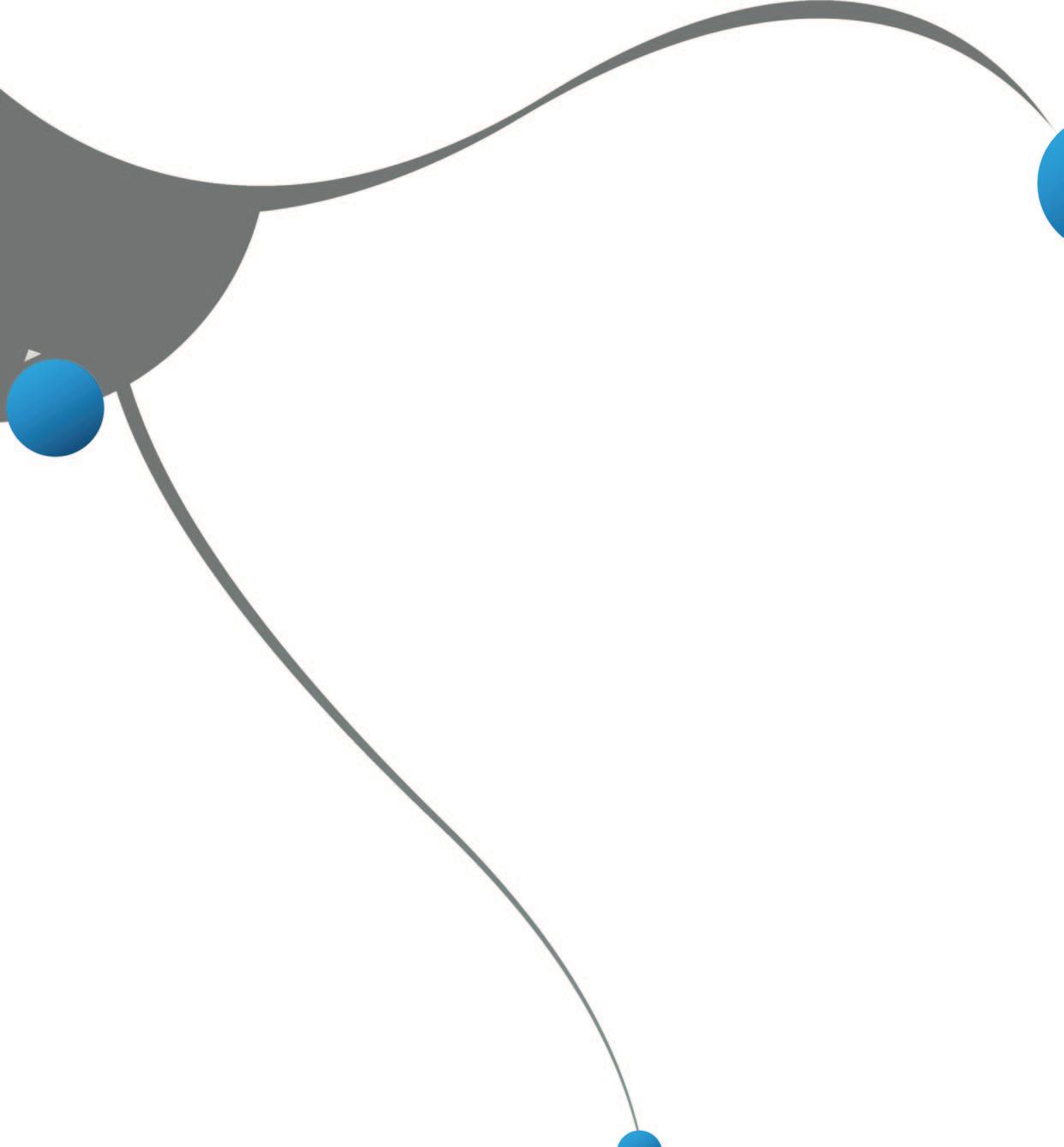
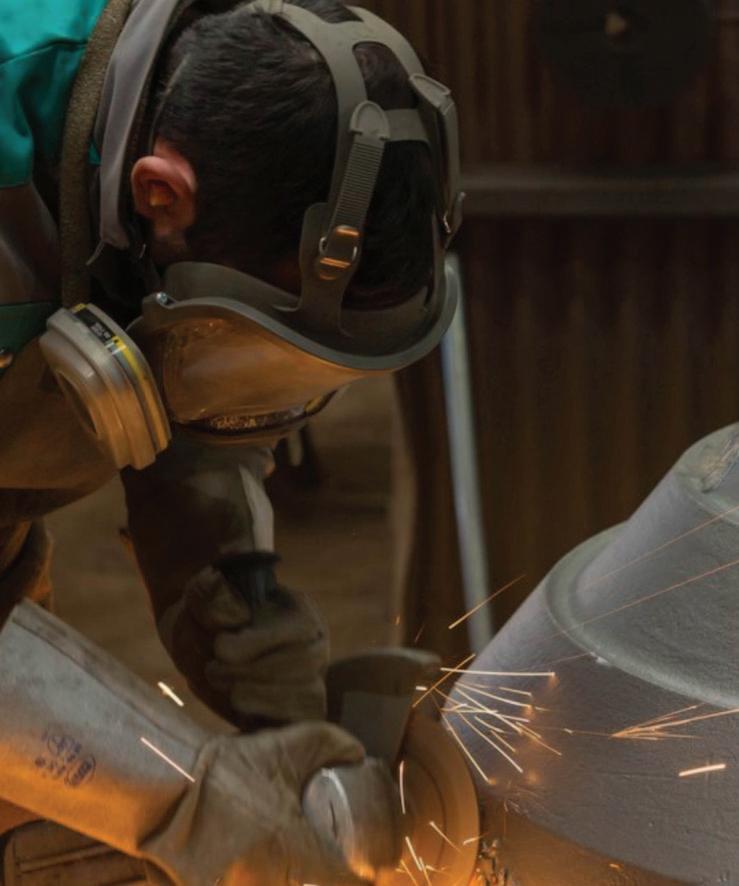
Following years of successful operation led by dedicated management, CMW Foundries has been passed on to the second generation and is eager to grow. Commercial Director Manuel Mendes revealed what this means for the casting specialist, during an in-depth interview with Inside Marine.
Report by Imogen Ward.
Family-run CMW Foundries has undergone a multitude of changes during the last two years, including the transition from first to second generation management.
“The transition has brought some strategic changes and enhancements aimed at modernising the company and ensuring its sustainability and growth,” said Commercial Director Manuel Mendes.
“Although the generational shift has ensured the continuity of the company’s values and vision, it has also led to new ideas and technological investments to address modern challenges.”
CMW Foundries was founded in 1981, in Lousado, Portugal, to meet the demand for wear-resistant technical castings. Today, the company operates from three
foundries producing sand castings in high alloyed cast iron, steel, stainless steel and nickel-based alloys.
Despite the recent transition, CMW has maintained its core expertise in producing wear-resistant materials up to 10 tonnes for applications involving abrasion, impact, corrosion, high temperatures and mechanical stress.
Keen to ensure the foundry is as modern as can be, CMW’s new management has pinpointed several areas of focus. With the rise of Industry 4.0, the company has committed to heavy investment in this area. New technologies with a focus on automation have been installed to better streamline its capabilities, whilst simultaneously enhancing production efficiency and quality control.
Over the last two years alone, the company has successfully increased its investments in machining and automation by 40%.
“Management is also focused on advancing our machining capabilities to provide fully finished and ready-to-install parts to our clients,” explained Mr Mendes. “Enhancements have also been made to working conditions to ensure a safe and productive environment.”
CMW has made significant improvements to its green credentials too, following the completion of a 2.7MW photovoltaic park at its MDF Tramagal industrial unit. This has played an important role in the company’s efforts to reduce its carbon emissions. With all of these investments well underway,
CMW has broken records after a hugely successful 2023 period. The year was groundbreaking for the casting specialist, resulting in a record business volume of €21 million.
“This milestone really underscores the effectiveness of our recent strategic investments and the improvements we have made to our operations,” said Mr Mendes.
Of course, this extraordinary achievement would not have been possible without the dedication of CMW’s staff, clients and its suppliers. According to Mr Mendes, this ecosystem is absolutely crucial. In particular, CMW’s partners are consistent in supplying the highest-quality materials and services, which allow it to maintain excellent production standards.
This is so important, especially at a time when the competition is so imbalanced. CMW has witnessed an increasing number of competitors positioned outside of the EU joining the market.
“Competitors from outside EU with huge subsidies leverages and lower production costs create unfair distortions of the market,” commented Mr Mendes. “This imbalance has put pressure on our pricing and margins: forcing us to focus on high-
value markets and adopt more advanced technologies to remain competitive.
“The lack of robust protection for the European industry has further compelled us to innovate and continuously improve our efficiency.”
Despite this challenge, CMW has maintained its ability to stand out amongst the crowd. Operating witha strong combination of traditional values, expertise and innovation, CMW offers a flexibility second-to-none, providing customised solutions to all who need them.
The group CMW has three foundries, all located in Portugal. Across these sites, CMW has an installed capacity of 12,000 tonnes a year.
“We have an experienced team of met allurgical engineers who enable us to work with complex and rare alloys, such as Inconel, cobalt based, duplex and super duplex, high strength casted steel, stainless steel, heat resistant steel, high chrome cast iron, et cetera.” said Mr Mendes. “We also benefit from high moulding versatility with a green sand automatic moulding line (equipped with moulding boxes measuring 650 by 550mm), phenolic alkaline semi-automatic moulding
lines designed for medium to large castings and three hand-moulding lines perfect for custom and complex castings.”
The foundry also houses both induction and electric arc furnaces, which produce a range of castings from the smaller 3-4kg examples up to much larger products weighing in at 8-10T. Additionally, the site is equipped with state-of-the-art heat treatment processes to guarantee optimised materials.
CMW’s hand-moulding capacity also doubled after the company acquired a 40-tonne mixer – once more, enhancing its production capabilities.
CMW Foundries prides itself on offering comprehensive in-house services, starting
from the project phase. CMW is equipped with the latest CAD/CAM mod elling technologies, solidification and filling simulation software, plus various equipment for rapid prototyping and reverse engineering. The company also boasts its own pattern workshop, featuring two CNC machines, the largest measuring 5,000 x 2,500mm. All metallur gical and foundry activities are conducted on-site. Furthermore, CMW has a dedicated quality control department staffed with Level 2 certified non-destructive testing inspectors and unit equipped with advanced machining capabilities to deliver the castings to our customers ready to assemble.
The company is proud to be working on some amazing projects, utilising its clear expertise in wear-resistant materials, advanced technological capabilities and extreme versatility – all with the help of its hardworking and skilled workforce.
“Currently, we are involved in several key projects, including the production of complex and high-precision components for the offshore, dredging and mining, pump and valve, and shipbuilding industries,” Mr Mendes continued. “Our expertise and investments allow us to meet the stringent demands of these sectors, providing high-quality products with competitive delivery times.
“These products perfectly highlight our capabilities and versatility in delivering finished products that meet the diverse specifications of each industry.”
As CMW continues its quest for forwardthinking innovation, the company has outlined several overarching objectives it is working towards.
“Foundry is a capital-intensive industry, so we need to be continually investing
and upgrading our equipment and training,” said Mr Mendes. “Our future plans include continuous investment in automation and machining technology, expansion of our production capacity, and the strengthening of our commitment to sustainability through green initiatives and energy-efficient practices.
“We are also exploring new markets and growth opportunities to maintain our focus on quality and innovation. Increasing our international presence and continuing to lead in environmental practices are also among our primary objectives.”
According to Mr Mendes, the company remains optimistic, despite the current global challenges and geopolitical tension: “The hardships that come with high interest rates, war and tension across the globe have been difficult. However, we are extremely optimistic about the future.
“We are determined to continue offering high-quality products, whilst meeting the needs of our customers with excellence, and we are so grateful for the continued trust and support of all our partners and customers.”
n