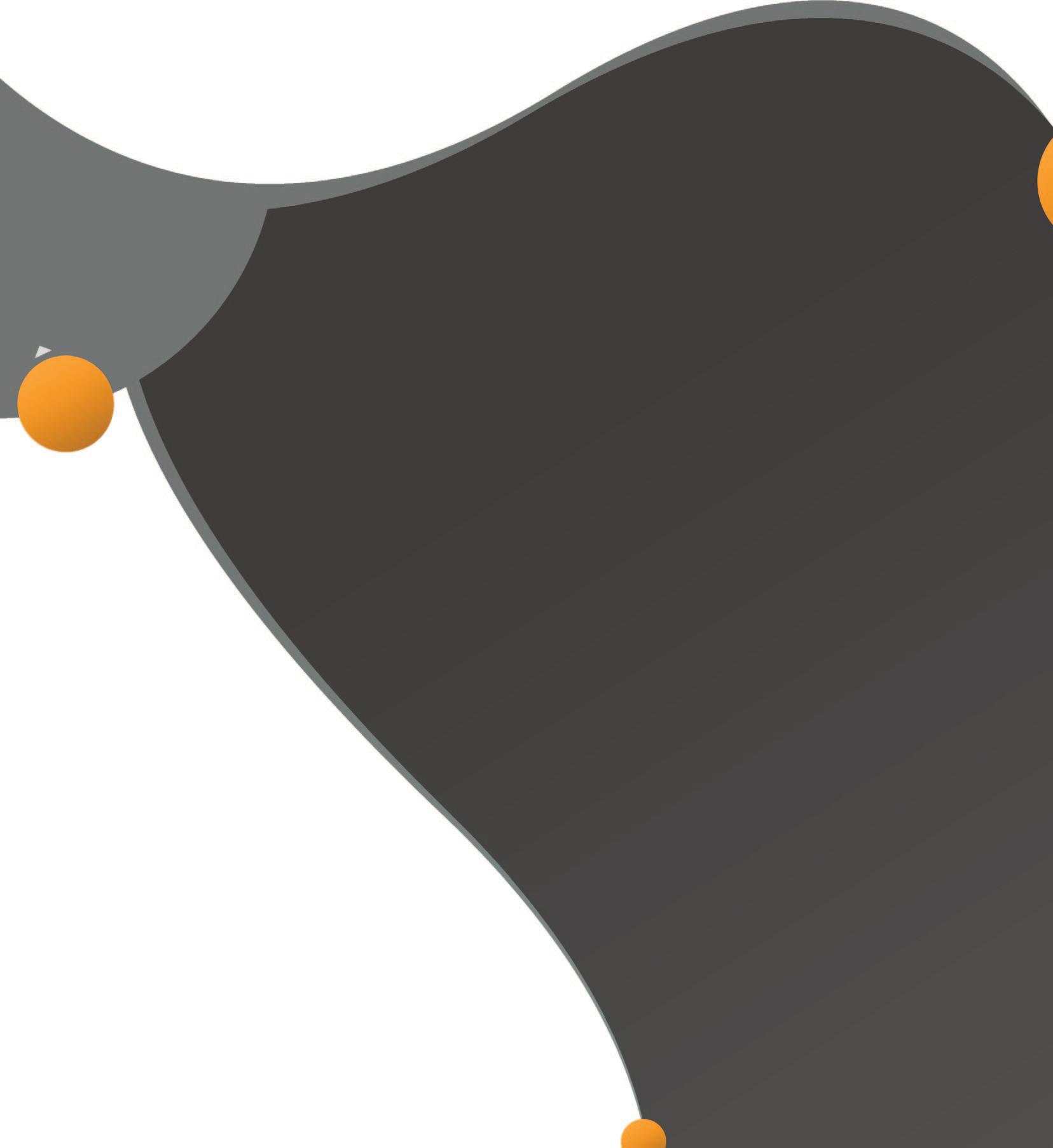




Fabrika Hartije Beograd, a member of the Smurfit Kappa Group, is not only the oldest paper mill in Serbia, celebrating its 100th anniversary in 2021, but also a modern, lean and environ mentally-conscious manufacturing facility restructured to meet the requirements of an increasingly demanding market. Romana Moares reports.
tradition is something to be proud of in today’s fastchanging world, but one Belgrade paper mill stands out for more.
Over the last decade or so, Fabrika Hartije Beograd – the only manufacturer of corrugated paper in Serbia – has been substantially modernised, and an envi ronmental focus embodied in its very products. The company uses wastepaper as the basic material for the production of European quality cardboard, processing some 100,000 tonnes of used paper which would otherwise end up in landfill.
Reflecting on the company’s 100th anniversary, CEO Milan Markovic´ sum marised the company’s development: “Founded in 1921, the factory moved to new premises on the bank of the Danube river in the 1960s where it continues to reside today.”
“In the 1990s, the company changed hands several times, until it was bought in 2008 by the Serbian Kappa Star Group, starting a period of rapid development and major capacity restructuring.
“In 2018, the company achieved record breaking production of over 100,000 tonnes and negotiations with the Smurfit Kappa Group started. These were com pleted a year later, and we became a fully- fledged member of the Smurfit Kappa Group, Europe’s leading corrugated paper manu facturer and one of the largest paper based packaging companies in the world, with operations in over 30 countries.”
Corrugated paper was introduced in 1856, initially for the production of protective boxes for hats. The product was patented in 1871 and was used mostly to protect glass bottles during transport. At the time, only the two-layer paperboard was produced.
Today, corrugated paper is mostly used to make boards (corrugated cardboard and containerboard), but it is also used in the production of the final layers of paper tubes as well as paper bags.
Fabrika Hartije Beograd makes three types of corrugated paper, all based on 100% recycled used paper: ‘Testliner’,
FABRIKAor simply liner, represents a type of corrugated paper used to make the outer layers of boxes or tubes; ‘Fluting’ is used to make the wavy sheet inside the cardboard and the third type is ‘Schrenz’ , another liner, used mostly for the inner layer of a triple-layered box or a five-layer box for the middle and inner layers. The papers range from 90 to 230 grams per square metre and are made on a 5-metre wide machine.
“We do not plan to expand the portfolio but are seeking to optimise the product range in order to satisfy the needs of our clients,” said Mr Markovic´ , noting that most of the output is sold in the Serbian market, but with exports to neighbouring countries increasing every year. The objec tive is to position the company as a leading supplier in the region.
“We are witnessing changing cus tomer requirements with demand sharply increasing,” remarked the CEO, admitting that the factory has now reached full capacity utilisation.
“This is partly due to increased aware ness of the importance of recycling and a preference for sustainable products, and also due to the sharp rise in online shopping during the pandemic, resulting in a dramatic increase in demand for this type of paper.”
The company is ISO 14001:2004 certified and also holds the FSC Chain of Custody certification, providing credible confirma tion for products with environmentally
and socially responsible sources to access the market.
Applying the basic principles of sustain able development and prudent business operations, Fabrika Hartije continuously invests in environmental measures. In terms of waste management, the focus is on waste sorting at the point of origin and on reduced use of materials and energy consumption as well as replacing traditional materials with more environ mentally-friendly ones where possibl e.
Today, Fabrika Hartije Beograd is a certified materials recycling facility for wastepaper and cardboard and the entire amount of waste packaging paper and cardboard being recycled in Fabrika Hartije’s plant is counted as a contribution to realising national goals.
Industrial water treatment has been an area that has undergone significant mod ernisation over the years. During the first phase of facility reconstruction in 2010,
a high six figure sum was invested in tech nology enabling fresh water usage reduc tion and better waste water purification.
Right now, the factory is completing its investment in next-stage water treat ment, which will make it the first com pany in Belgrade to employ the latest , state-of-the-art technology, revealed Mr Markovic´ .
Speaking about the company’s out standing performance over the last few years,
Mr Markovic´ acknowledged that credit must go to the people, the company’s core asset, who also represent its key competitive advantage.
“We are proud to have enthusiastic people, who are ready to learn and exchange knowledge and thoughts within the group, and are open to new ideas. People and technology will remain
FABRIKA HARTIJE BEOGRAD I PROFILEthe key focuses of our investment, as the two go together to promote further growth and success.”
And suppliers are part of this develop ment, he confirmed: “We foster long-term relationships with our suppliers, both local and global, in which trust is one of the key values. All of our suppliers have been working with us for many years.”
Mr Markovic´ concluded: “Being a member of a strong group gives us the opportunity to learn from others and to grow. Clear goals were defined when Smurfit Kappa acquired the company two years ago, together with the way to achieve them, setting a clear path forward.
“Within our five-year plan, we are set to double production capacity, to reach an output of 200,000 tonnes per annum – a respectable objective to ensure the continuation of the century-long tradition of the paper mill.”