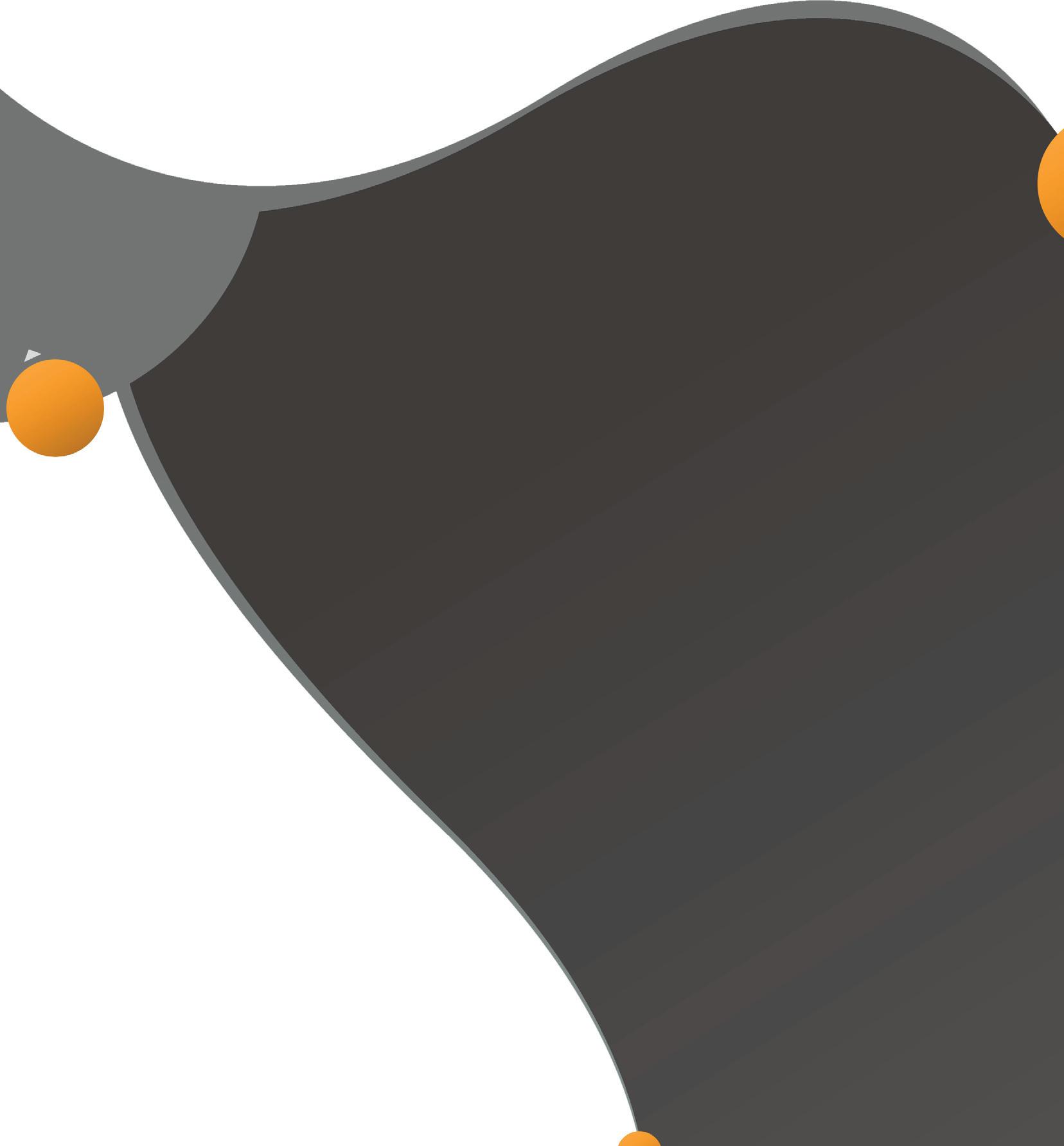
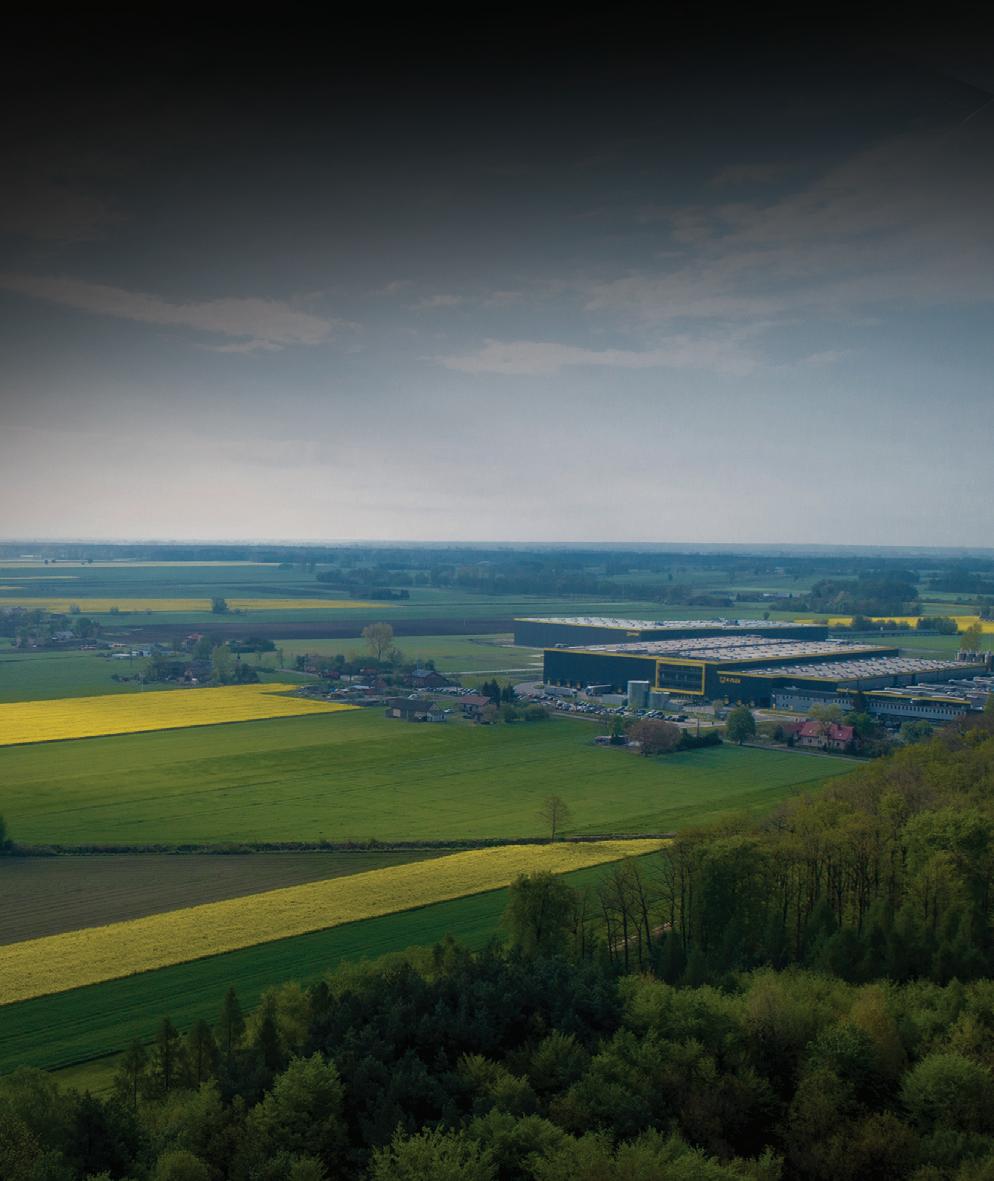
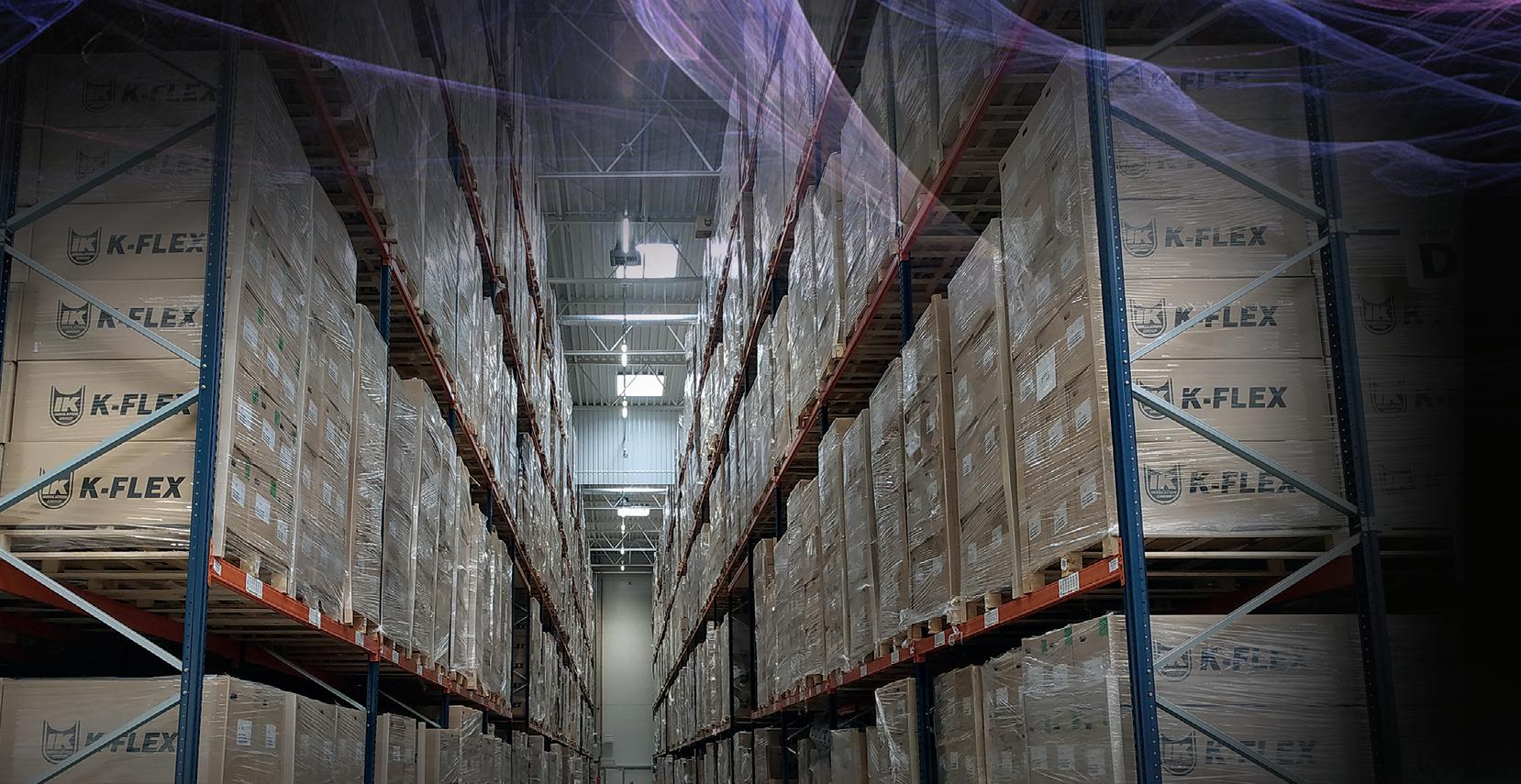

As a world leader in the insulation market, K-FLEX has long been an innovative solution provider in thermal and acoustic flexible elastomeric insulation materials. Bartlomiej Gröbner, Managing Director of its Polish production plant, the biggest of 14 worldwide, told Andy Probert how the company seeks to remain a key supplier to many different sectors.
Over the last 30 years, Italian-based K-FLEX has become recognised as a world-class performer and provider of cutting-edge insulation solu tions for industry, ranging from construction and transportation to petrochemical and renewable energy.
Utilising his experience gained in the rubber processing sector, K-FLEX founder Amedeo Spinelli launched the company in Milan province, in 1989, with just 35 people producing insulation materials from foamed rubber.
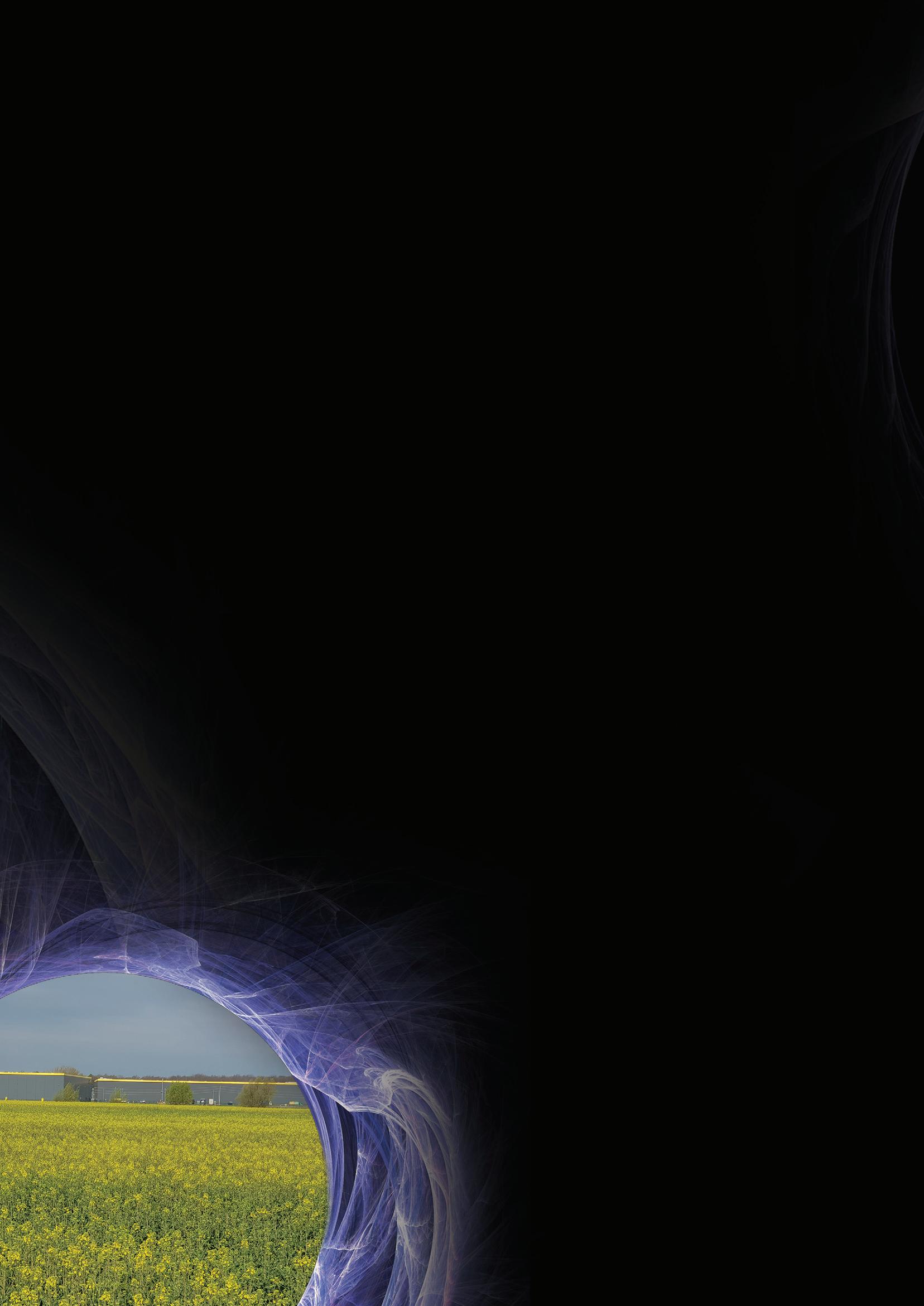
As the complexities of the insulation materials market grew, K-FLEX continued to expand. Today it has 14 production plants globally, employs more than 3,000, and boasts a market presence in 65 countries.
Established more than 10 years ago, K-FLEX POLSKA is at the beating heart of the operation, spearheading the charge and widely acknowledged as the world’s biggest facility for producing thermal and acoustic flexible elastomeric insula tion materials. These are essential to energy consumption control and greenhouse gas emission reduction.

“Our goal is to offer the largest portfolio of products to our customers,” asserted Bartłomiej Gröbner, K-FLEX POLSKA’s Managing Director. “Which is why we are now increasing production in not only our synthetic rubber insulation, but new and innovative polyethylene, or mineral wool.”
Growing influence and innovations
K-FLEX POLSKA’s influence has grown considerably since 2016. Its factory, in Wielenin-Kolonia near Uniejów, has
expanded by more than eight times from 8,000 sqm to over 60,000 sqm. It began with 10 people, but now employs 900 people.
This has been aided by the parent com pany’s global sales, while profits have grown substantially for ten consecutive years since 2010. In 2021, the company is expected to see 25% growth and pre dicted to register a €500 million turnover, with the Polish operation accounting or more than a fifth.
Expansion of more than 18,000 sqm in October 2020 resulted in the comple tion of two lines exclusively dedicated to producing expanded polyethylene insulating tubes.
A total of seven lines are dedicated to these new products, which are specifi cally developed to meet the needs of the European market. They include inno vative and patented solutions aimed at meeting the most stringent regulations in energy saving.
While the insulation products market is expected to grow by 40% over the next five years, the need to achieve a sustain able world has also grown. The use of mate rials that provide greater energy efficiency, improve the protection of people against fire, noise and minimise the impact on the environment, has increased in importance.
In 2021, as well as leasing a new 34,500 sqm warehouse in Wielenin, K-FLEX POLSKA’s production facility was extended by another 12,000 sqm in preparation for a new family of materials, K-FLEX K-ROCK, based on natural mineral resources.
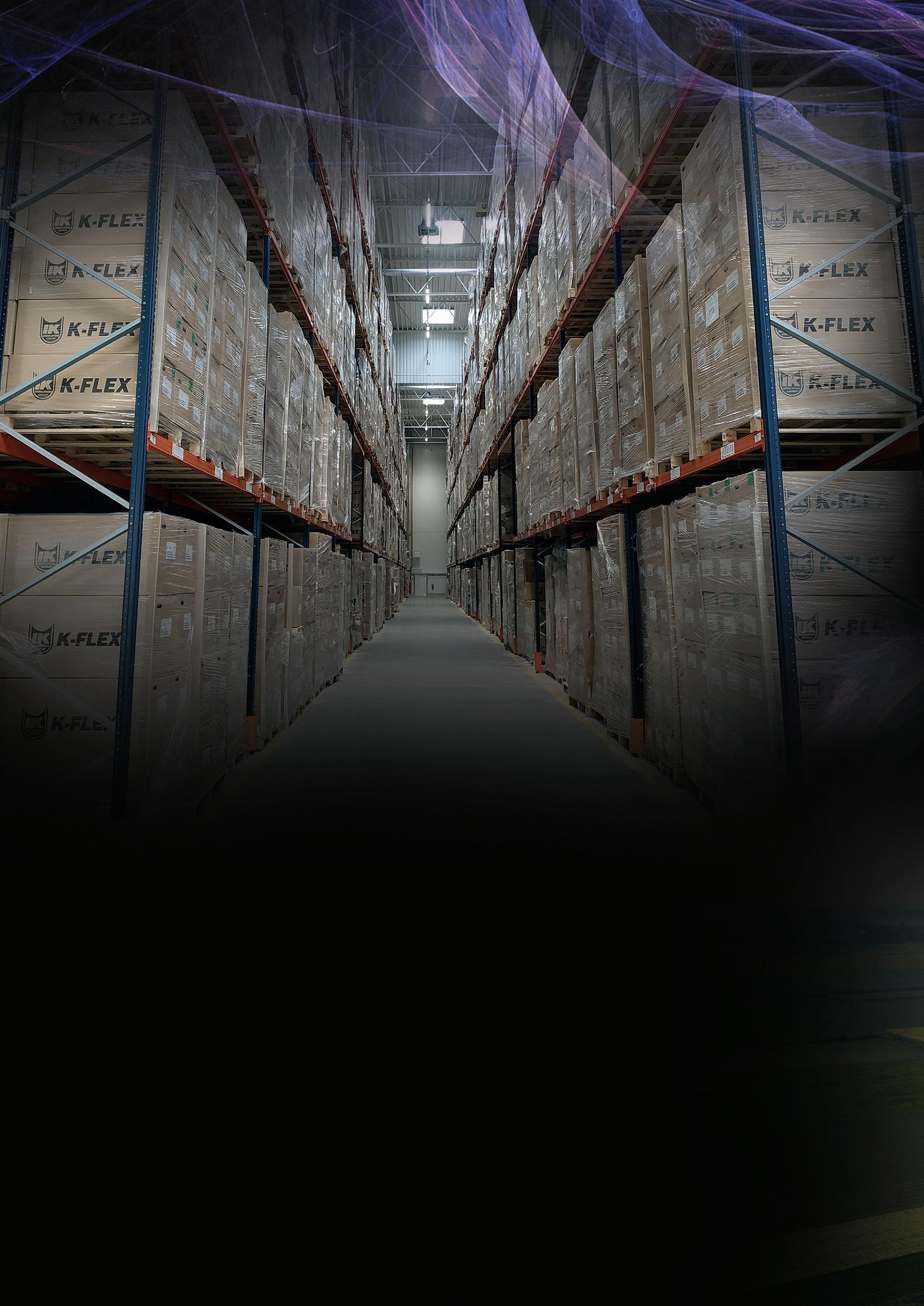
Together with state-of-the-art equipment and aluminium foil covering application lines, seven automatic cutting lines have been installed, guaranteeing production of hundreds of mineral wool sections per hour.
Flexibility allows for the production of an extensive range of dimensions, from small diameter pipes produced in one section to the large industrial sizes where sections are provided in two parts for ease of installation.
These products offer an economical and easy-to-install solution while providing high thermal, acoustic and fire protection perfor mance. Their advantages are thermal insu lation, durability, high resistance to fire, low pollution and sustainability.
They can be used in a wide range of appli cations: HVAC, naval, petrochemical, the offshore industry, and applications where protection from high working temperatures is required.
Complete approach
“We have recently been providing our clients with the pre-insulation service for multilayer and copper pipes,” remarked Mr Gröbner. “We believe future years will bring a large increase in this business.”
He asserted: “Most of our competitors produce one type of insulation material. We strive to provide customers with every thing they need, from the most advanced technical insulation through mounting accessories and ending with finishing materials. This allows K-FLEX and the
client to save on costs of transport, logistics and document circulation.”
Mr Gröbner said the company was renowned for approaching all partner relations with honesty and integrity.
“When we know each other, we can assess our strengths and weaknesses and build good relations for the long term. In difficult moments, we can also extend a helping hand to clients.”
He reflected the pandemic had shown how much the world depended on Asian suppliers.
“We are still struggling with problems with the availability of basic raw mate rials for production, and their price has increased significantly.”
To meet this challenge, K-FLEX intends to become independent from external suppliers as much as possible. The group is investing in new lines and locations where the raw materials needed for everyday functioning will be produced.
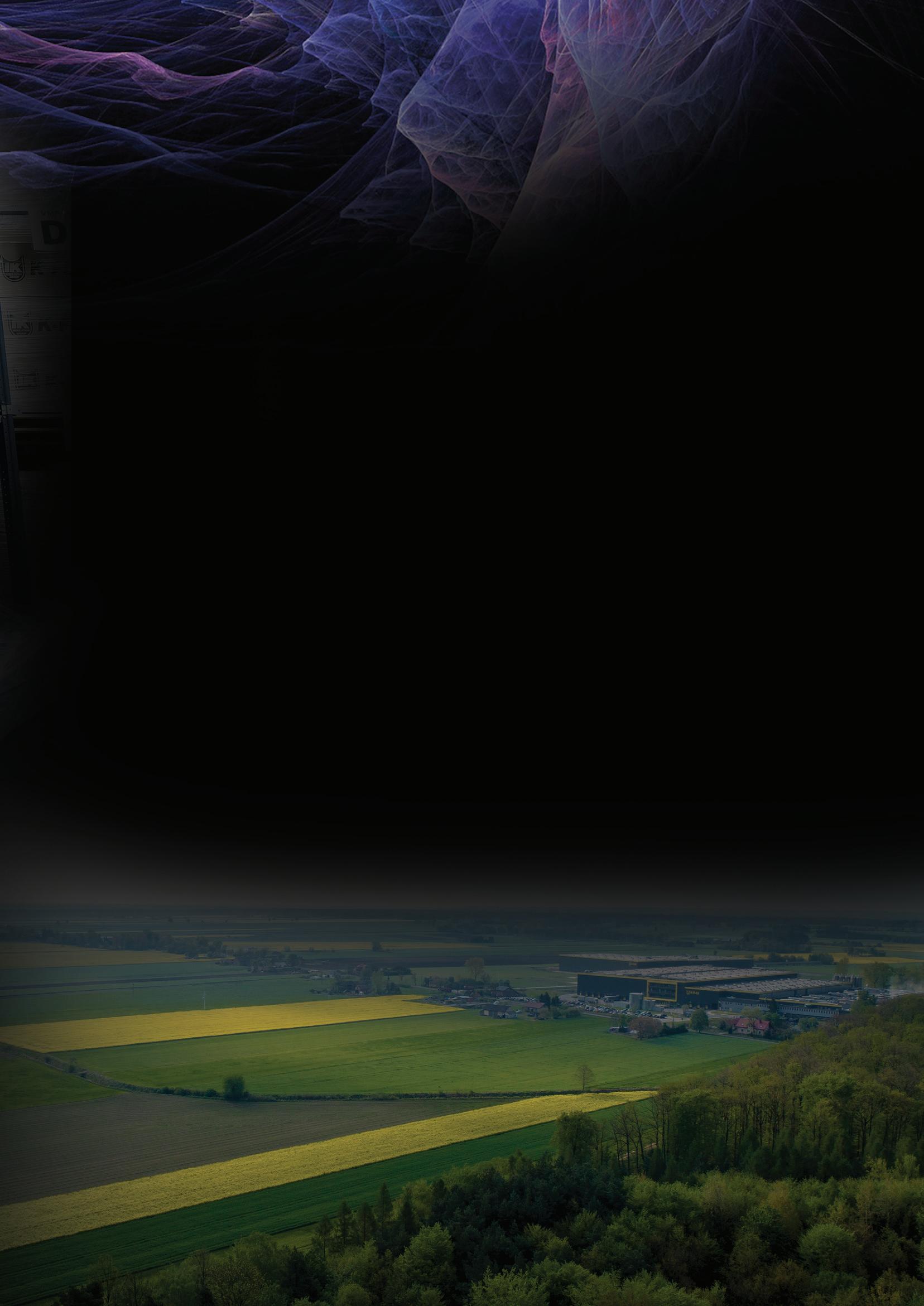
He added: “During the pandemic, our production plant operated practically without any disruptions. We secured the necessary raw materials, which allowed us to safely survive the most difficult period. In order not to dismiss employees, we sen t them on overdue or current holidays, which allowed us to maintain continuity of pro duction and stable working conditions.”
Employees are priority
The Managing Director asserted: “Our employees are the most important to the company. Without them, we would not achieve anything. We constantly invest in their development, giving them the
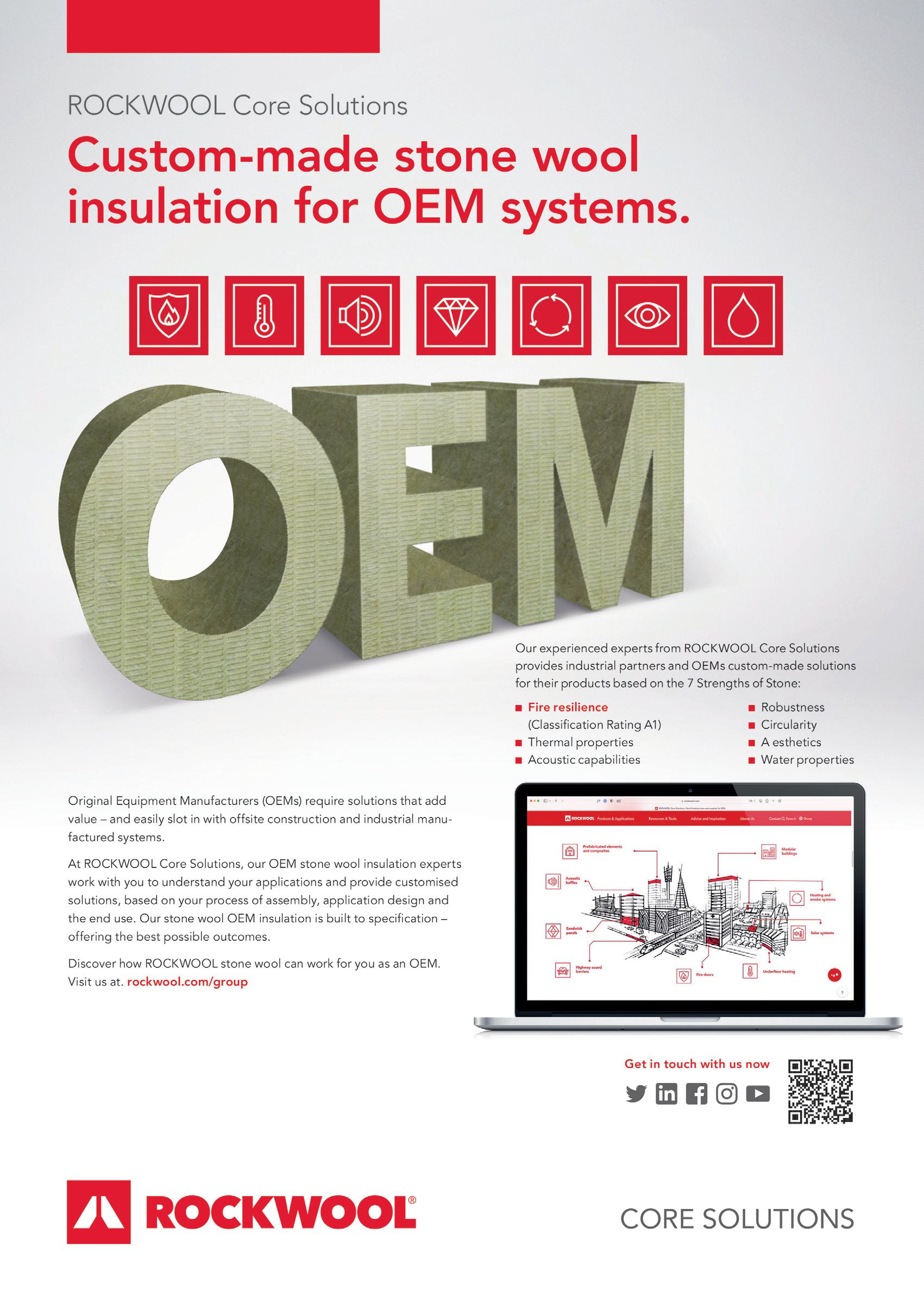
chance to grow. We also try to satisfy customers’ growing demands and adapt our offers to changing market requirements and trends.”
As a dedicated manufacturer to imple menting and investing in new technologies , K-FLEX has utilised €30 million in European funds to help achieve those goals.
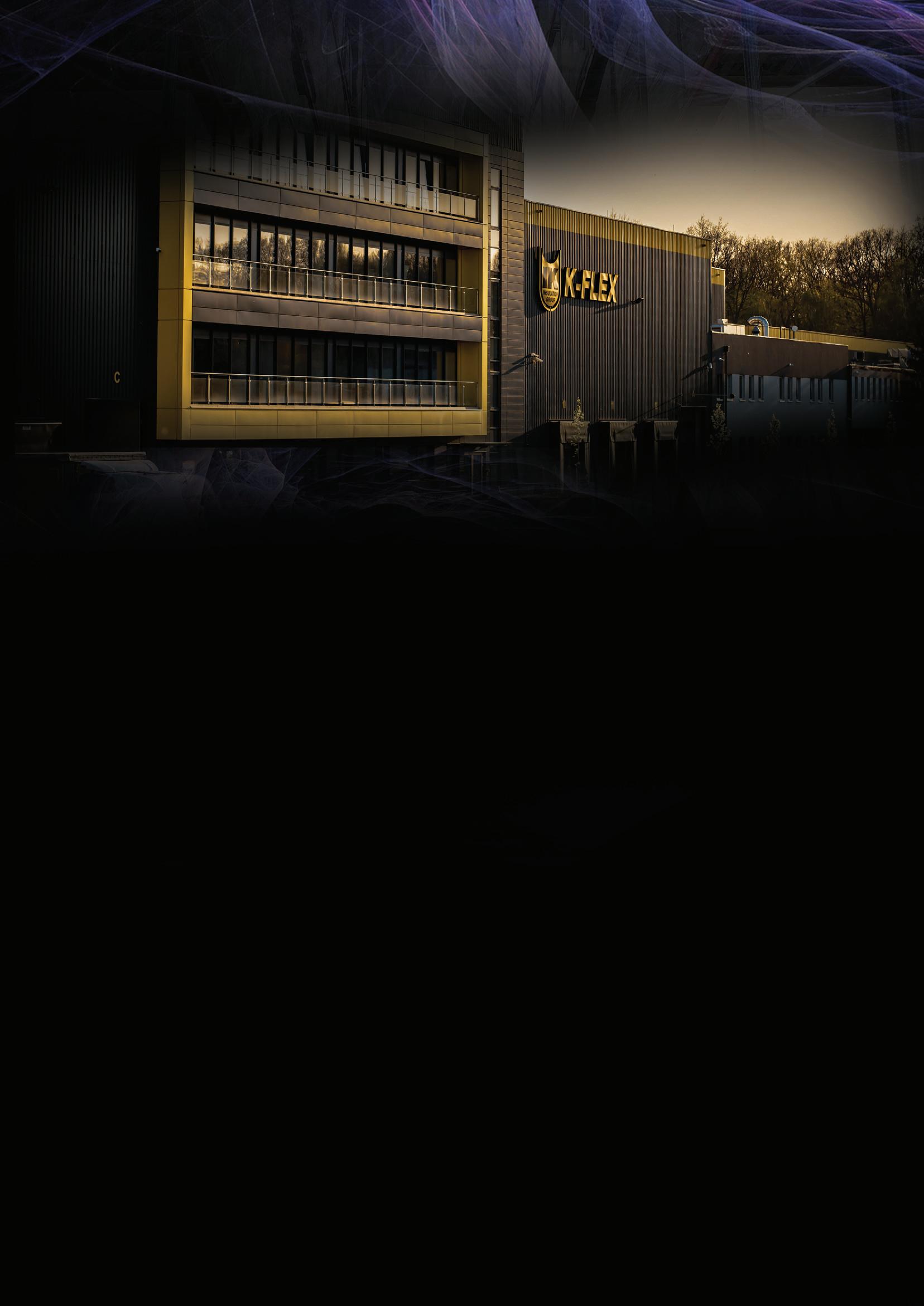
It is also a leader of the FRONTSH1P project, a consortium consisting of over 30 companies and institutions, which aims at ensuring the transition of the Polish Łódzkie Region towards decarbonisation and territorial
regeneration through highly replicable circular systemic models.
“As the market leader in rubber and polyethylene insulation, continuous invest ments mean we can gain new markets and new sectors, while increasing our production lines and independence from external suppliers,” said Mr Gröbner.

“We hope the recent changes on the market caused by the pandemic will not impact on the sectors in which we operate, and will allow us to maintain harmonious growth.”
He concluded: “At K-FLEX, we are a wellcoordinated team. We listen to the needs of our employees, we meet them, and people are eager to join us because they know working with us means employment stability and development opportunities.
“From the outset, it has remained a family business despite the passage of 30 years and the employment of over 3,000 employees. Everyone feels as if they are in a family – the K-FLEX family.” n
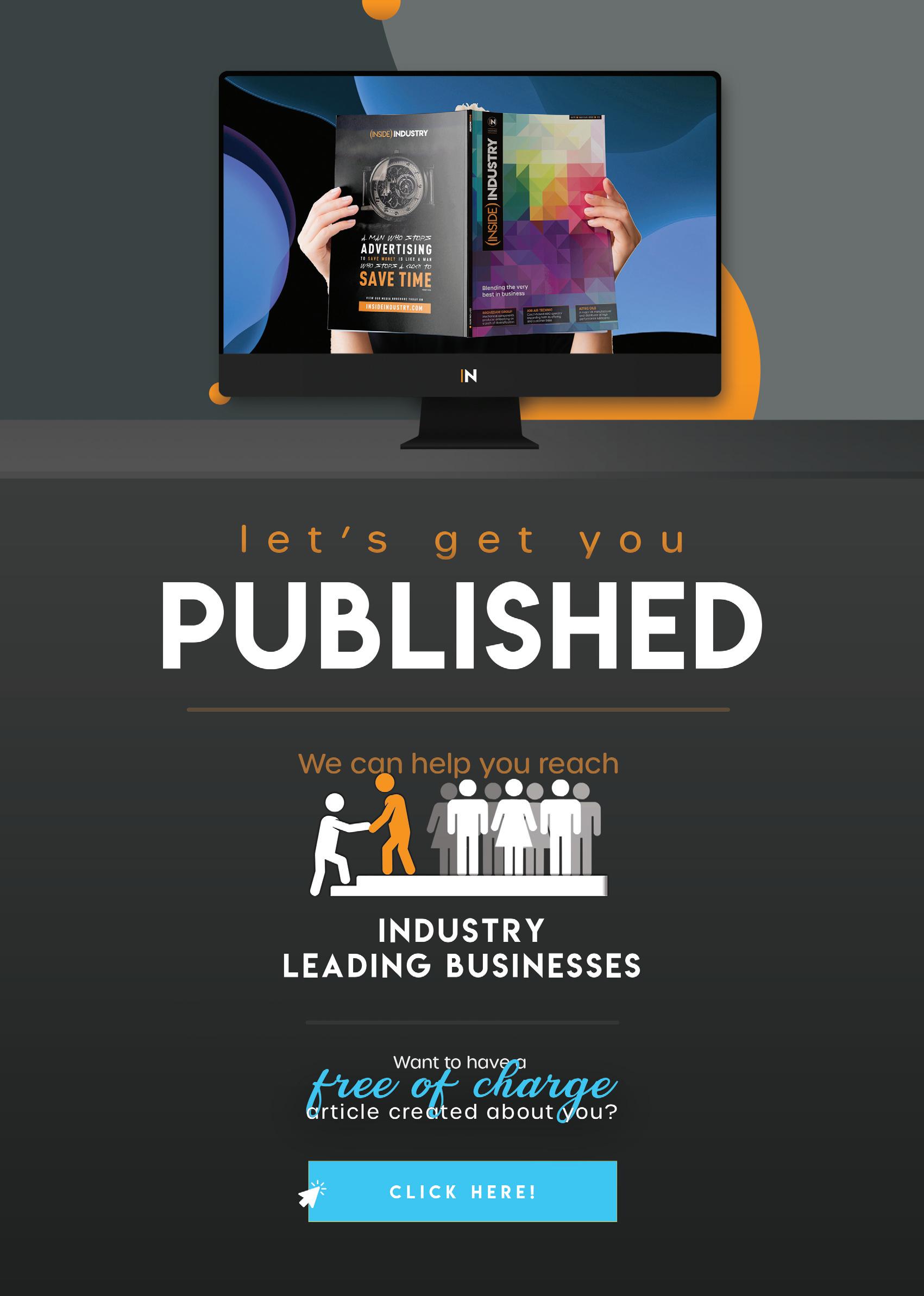
