Kadant PAAL’s primary products are horizontal balers and conveyors. These are used to process recyclable materials including paper and plastic, as well as various non-recyclable materials like RDF, waste and agricultural products. Based in Georgsmarienhutte, near Osnabruck in Germany, the company was founded in 1854. President Craig Heley explained more to Hannah Barnett.
The PAAL Group of Companies was formed in 2002 as a combination of Spanish, German, French and British baler manufac turers, establishing a firm European footprint. In 2016, the Group was acquired by Kadant Inc, a NYSE listed company. The Group now employs around 230 personnel and operates across five sites, with the main production facility in Germany, boasting a production capacity of around four balers a week and a smaller manufacturing unit in the UK.
“We have a standard product design with lots of options,” said Craig Heley, President. “Our balers will satisfy 99 per cent of customer applications and from a production point of view, it means we can plan with a much higher degree of certainty. We have a very simple, structured and highly effective production process for customers; we give a delivery date, and we stick to it.”
Kadant PAAL Ltd also designs and manufactures its own range of vertical balers and waste compactors in the UK, as well as distributing the full range of auto-tie balers and conveyors built in Germany.
KADANT PAAL I PROFILE
All of the Kadant PAAL units have mobile engineers strategically located throughout their respective countries, offering comprehensive preventative maintenance cover, as well as a rapid response to any unexpected machine downtime.
Extremely efficient
Kadant PAAL is dedicated to the efficient compacting of a range of materials for recycling, thereby enabling the sustainable benefits of a circular economy.
“Where waste can be reused, it needs to be efficiently handled, stored and transported,” Mr Heley said “Our job is to make the material as dense as possible so that fewer operations per volume of material are needed and transport costs can be minimised. It makes the whole process more efficient, more cost-effective and therefore, more sustainable.”
Baling plastics for recycling tends to be a more challenging process than baling a material like cardboard, because it has an inherently slippery nature, and it retains its material memory so wants to re-expand after being compressed.
“To overcome this, we have increased the power of the pantograph and extended the length of the channel,” explained Mr Heley.
“Also the varying material characteristics when baling need to be considered because there are numerous parameters that are automatically adjusted in the baler to optimise performance for each specific material grade. We refer to these as ‘recipes.’ With plastics, we are trying to get the memory out of the plastic, so the recipe must be a lot more sophisticated than with carboard.”
Bales of recycled material are typically secured in place with wire. Roughly two kilos of steel wire are used per bale, but
with sustainability in mind, the company is striving to reduce that number.
“For an operation producing 50,000 bales a year, customers may consume around 100,000 kilos of wire,” said Mr Heley. “So even a 10 per cent increase in bale density saves 10,000 kilos of steel wire, as well as meaning that more material is sent on a transport load, thereby reducing the number of loads and, as a result, the level of emissions.”
The company has also developed highefficiency motors and axial piston pumps as part of its machinery design. Compared with the previous design, Kadant PAAL now offers the same speed of operation with a 55kW motor that previously needed a 75kW motor, thus saving energy while maintaining the throughput.
Projects and partnerships
Kadant PAAL recently worked on a significant project for a US customer which involved baling pulp for export.
“We’ve developed a baling process that forms a homogenous block of fibre pulp, without the need to tie or secure the bale,”
Mr Heley explained. “It’s been quite a challenging process, but I think the most interesting bit is that it was a very international project for us.
“The customer is in the US, the machines are made in Germany, the tests were run in France, we used Spanish engineers, and the final commissioning process was managed by a UK engineer. It covered all aspects of our Group.”
Mr Heley also explained about a further interesting project involving the automatic
application of bale labels, including RFID chips: “Although designed in Germany, this has been project-managed in France and the system is currently being trialled at a major French customer,” he said. “Such a system could revolutionise the circular processing function because, for the first time, there will be genuine material traceability at the level of each individual bale.”
To accomplish such logistically complex projects and maintain the company’s guarantee of delivery within ten weeks, strong long-term relationships across the supply chain are crucial. Kadant PAAL favours a single source of supply and has frame contracts in place with its core suppliers.
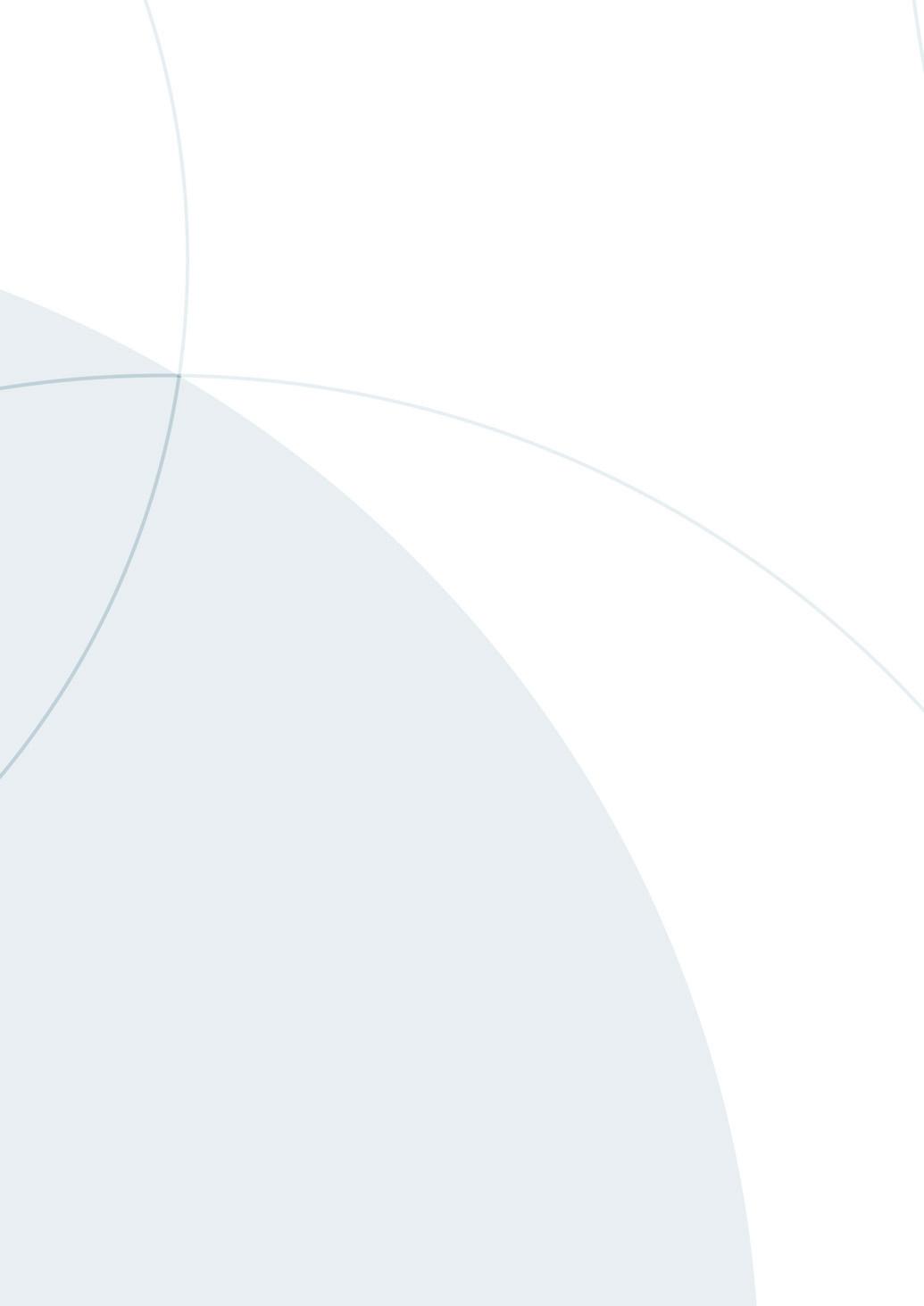
“We give them a commitment in terms of what we will use over the course of the year and the maximum that we will demand weekly for each specification, so they’re able to plan,” said Mr Heley. “This means they supply us in a very timely way f or things like cylinders, motors, panels and so on. We have a very structured approach to the whole procurement and production planning process. When we get a customer order for a baler, we place the order on our suppliers and know that they will be able to deliver to us within a four-week period, because we have a long-term historical working relationship with them, and they have the security of the frame contract. Our suppliers’ performance enables us, in turn, to be a reliable, market-leading supplier to our customers.”
Future focus
Having already established a strong presence across Europe, where Kadant PAAL is known for its outstanding
localised service, the Group’s next steps are set to continue on the path of international expansion.
“The US market is still relatively untapped,” said Mr Heley. “We’ve had some success but there are still significant challenges to overcome, and we need to provide our potential customers with new ideas because we are confident we can provide them with more efficient ways of doing what they’re currently doing.”
Kadant PAAL is ultimately a business dedicated to helping processes run more efficiently and sustainably. It is also, according to Mr Heley, a highly meritocratic organisation.
“Working here is all about dealing with smart and committed people,” he
concluded. “Personally, I have a great sense of the talent at all levels within the company. So, I love seeing a person taking on responsibility and developing as an employee. There are lots of examples of people who have moved up significantly within the organisation. We are small enough to be able to enable people to push themselves forward and to give them opportunities. This also benefits our customers because these employees have a depth of knowledge and experience that is impossible to match.” n