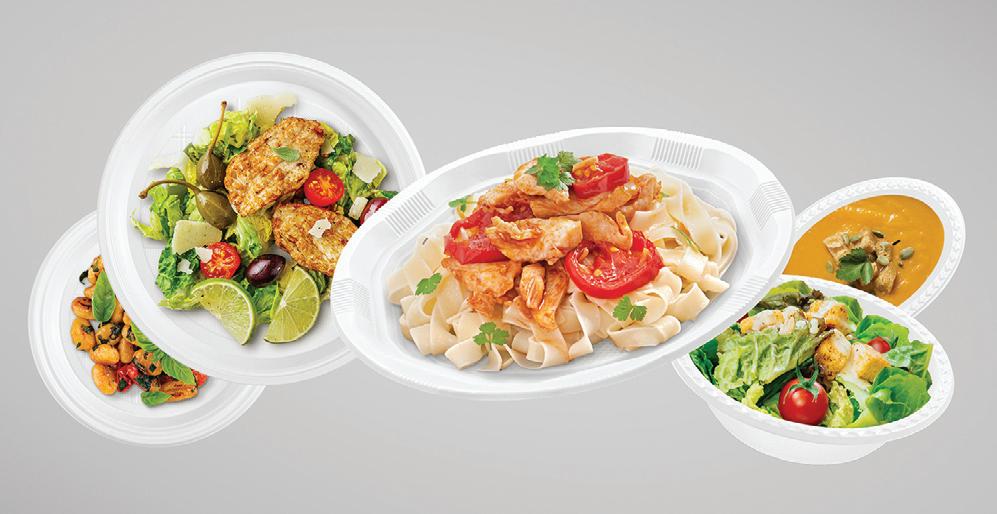
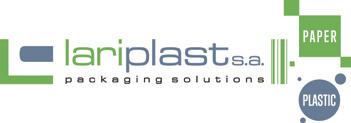

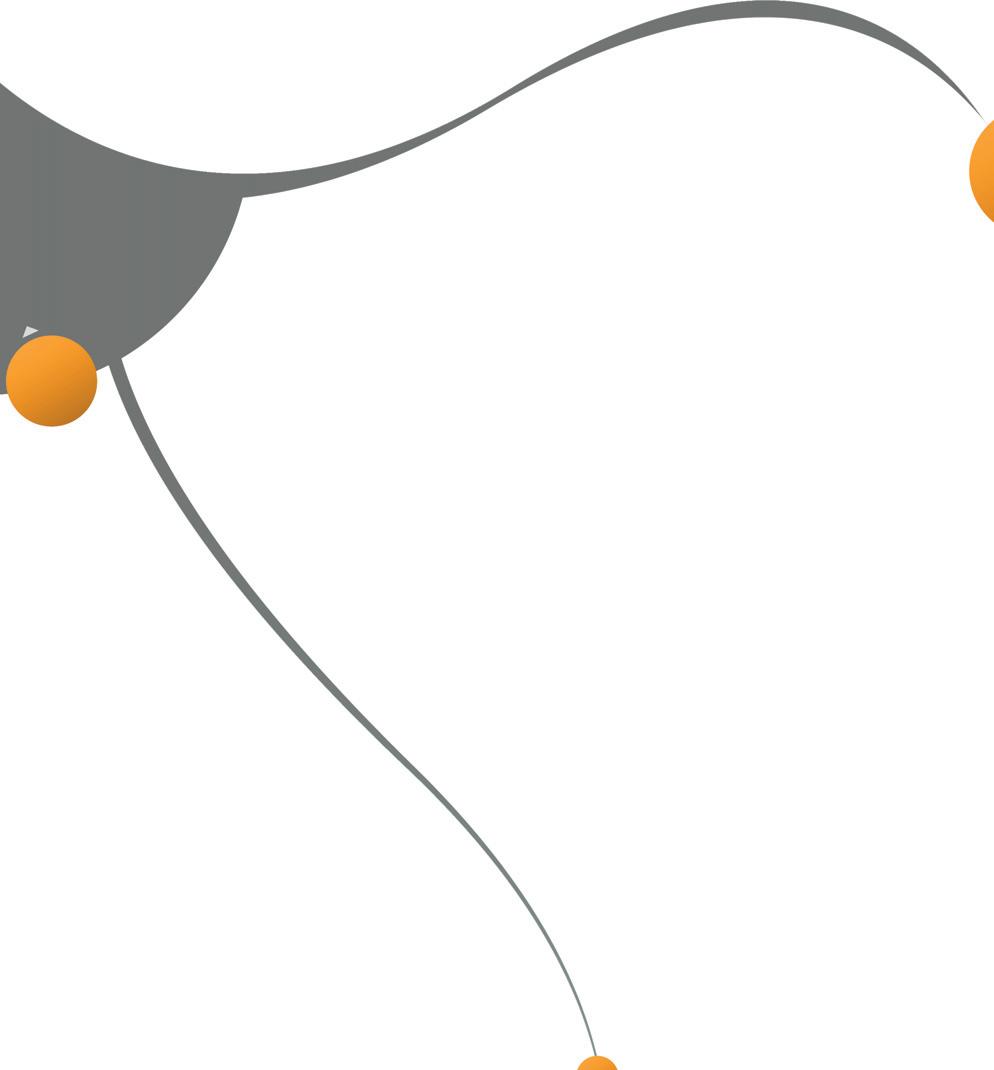
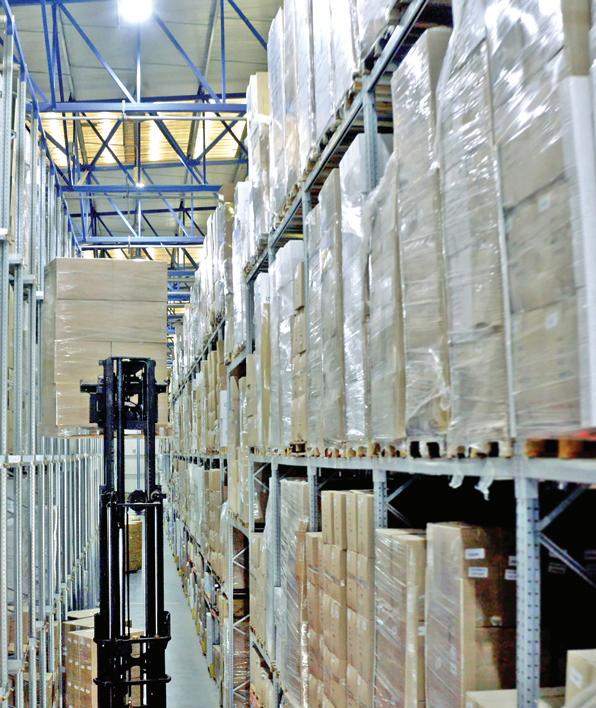
For 55 years, plastics and paper packaging manufacturer Lariplas able resilience in responding to market trends. The Greek family-o continues to expand its operations, develop its product portfolio itself on American soil. Andy Probert spoke to Head of Business D Tserepas to learn more.
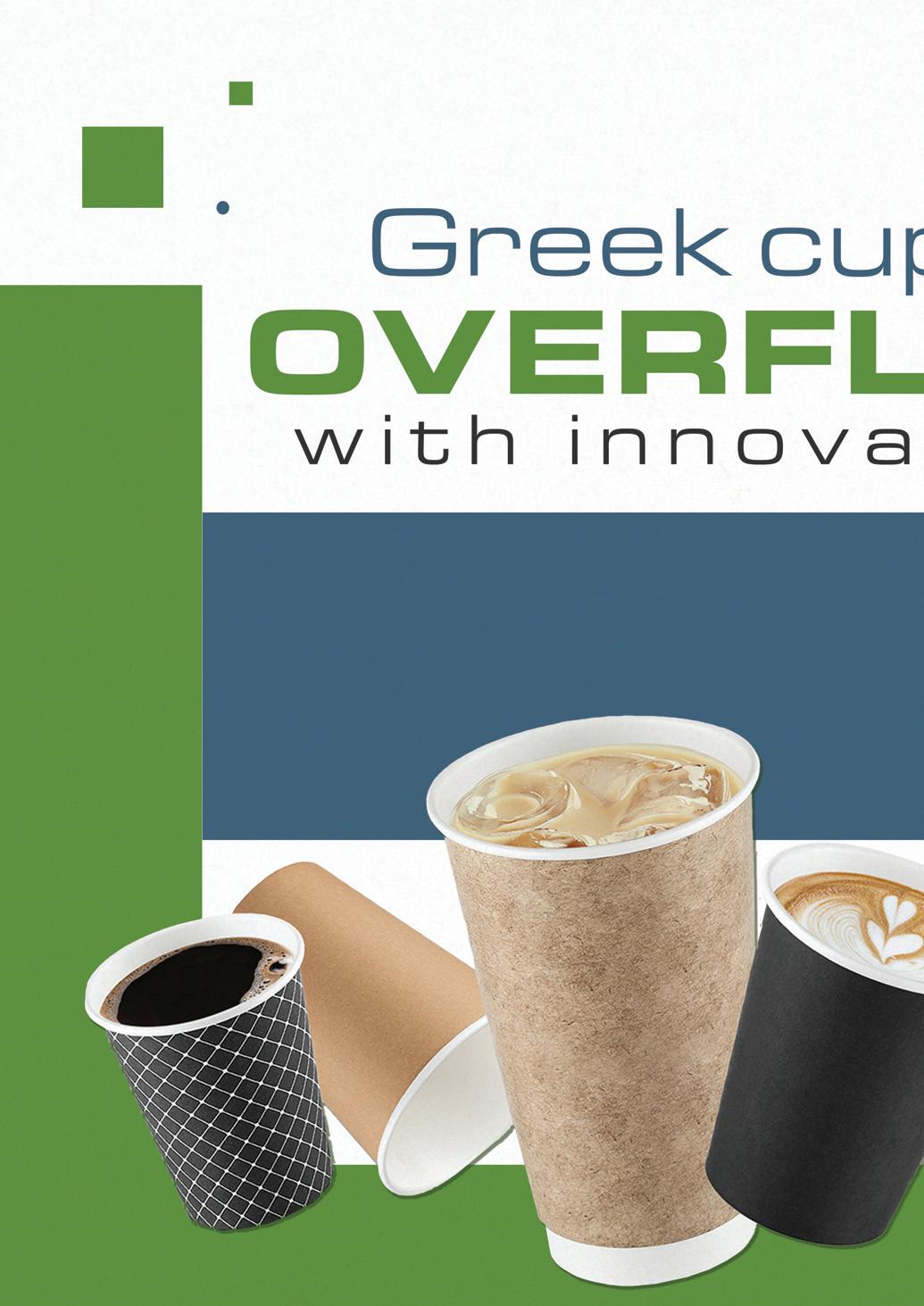
st has shown remarkowned company and firmly establish evelopment Angelos
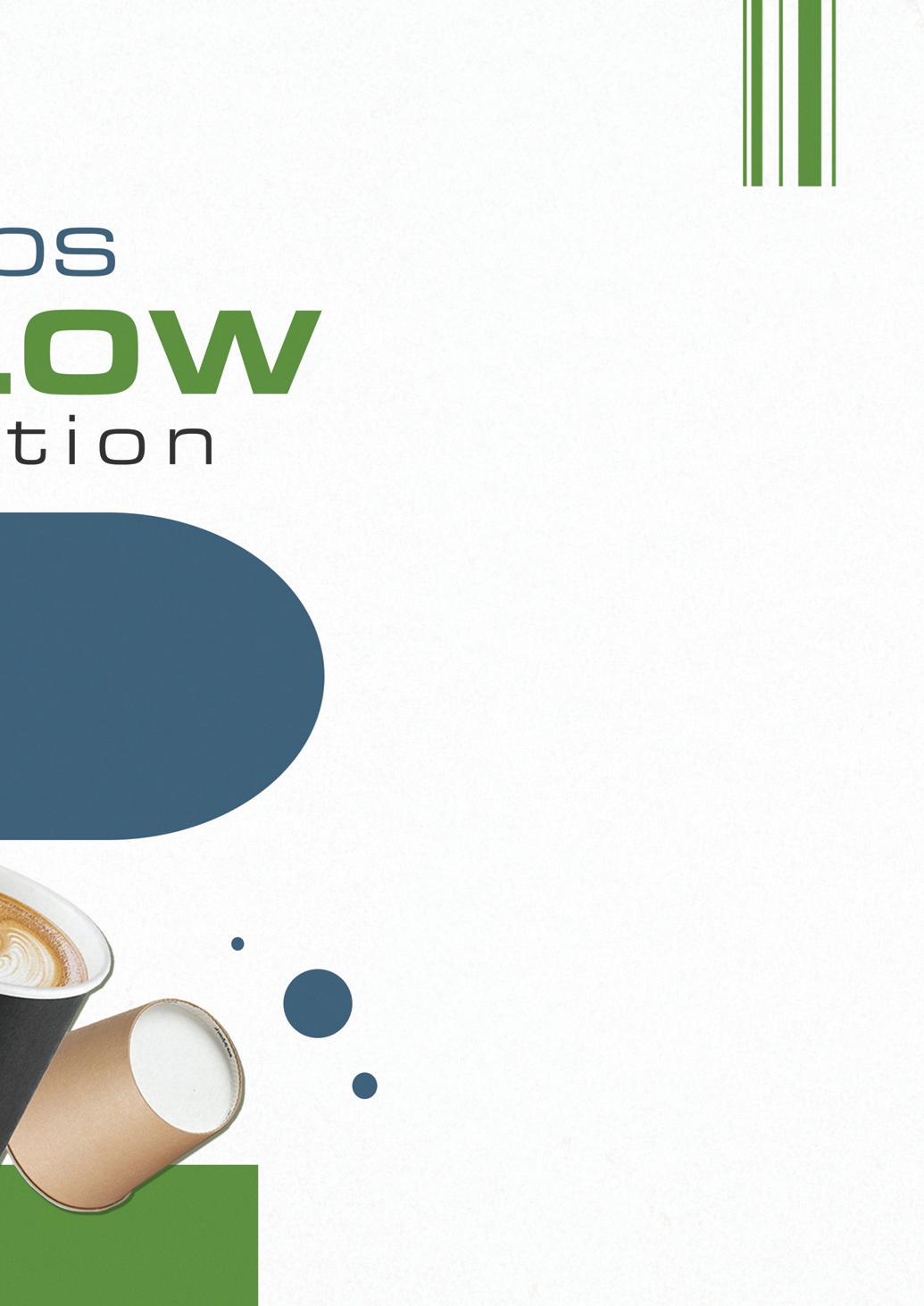
La riplast, a company that specialises in the production of plastic and paper packaging for the food and beverage industry, is eyeing an €80 million turnover by 2027. Having weathered storms brewing over single-use plastics, the company is enormously bullish.
“We are not ones to shy away from business challenges,” said Angelos Tserepas, Business Development Head and third-generational member of the family-owned company. “We are Greek, we are innovators, and we are pragmatic.”
That confidence is well-placed, as the company engineered a turnaround of its French factory, which was on the point of closure, and accelerated innovative developments through the introduction of paper-based packaging. Additionally, Lariplast adopted the thermoformingIML process for packaging in its Greek factory, which means less plastic is used in production.
Established in 1969, Lariplast pioneered the production of plastic yoghurt pots for dairy producers, before creating a second production line for plastic cups. The company grew in the 1980s and 1990s, with expor t activity aided by a breakthrough in lowering the weight of a cup – from 4g to 2.4g –without compromising output.
“It wasn't easy to make a cup lighter without lowering production, because that would mean reducing the productivity of the machine, whereas we managed to reduce the weight of the cup without altering our productivity,” explained Mr Tserepas. “But it was 100% functional and a major step for us, which we achieved in a year.”
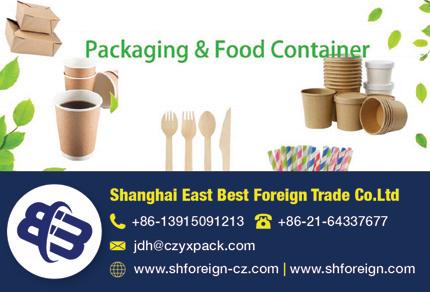

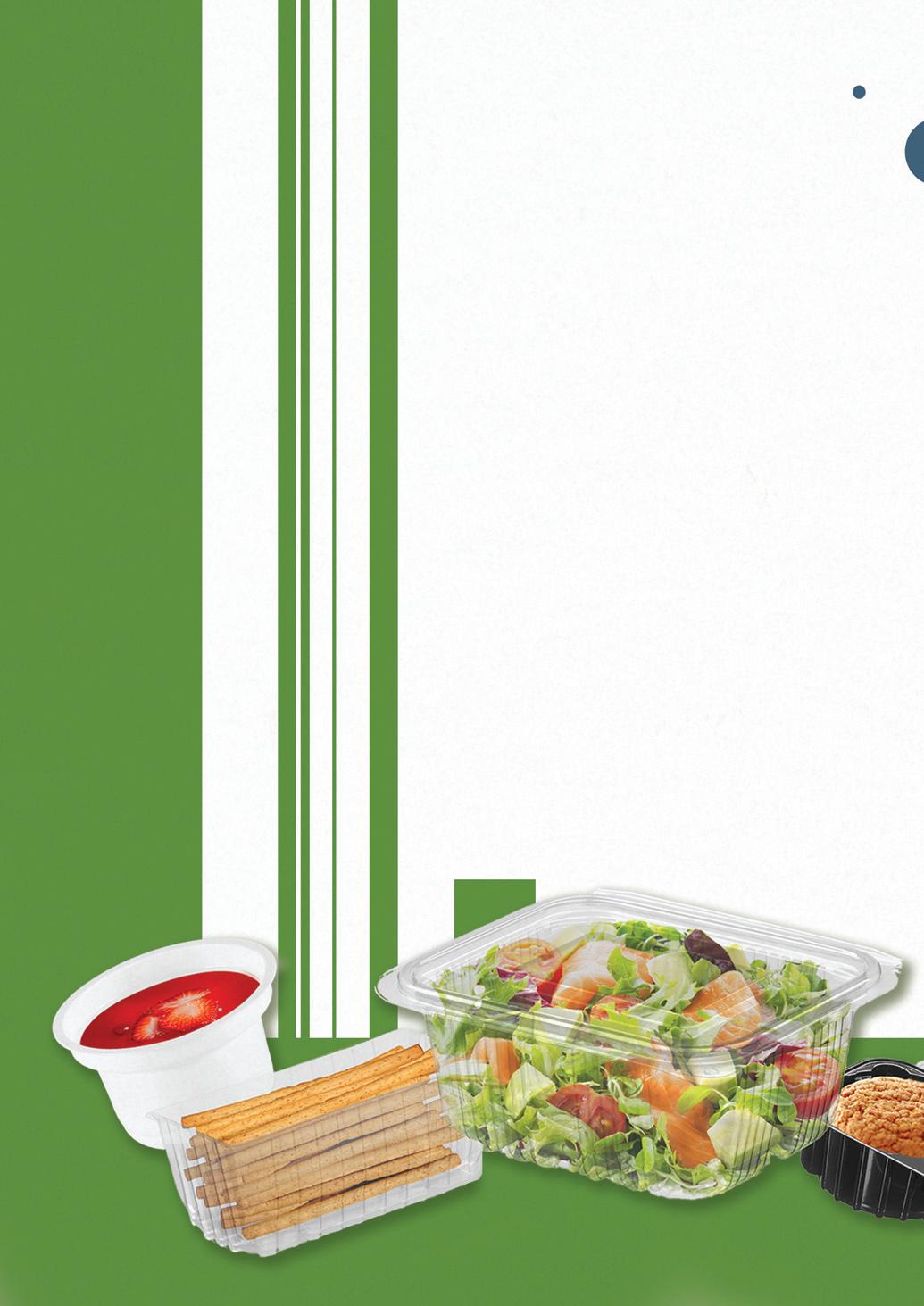
Today, Lariplast has several product lines comprising plastic cups, lids, plates, food trays and industrial packaging, plus paper cups and salad bowls, for clients ranging from industrial conglomerates to supermarkets, restaurant chains and water companies.
Now producing 7.5 billion pieces of plastic, 520 million units of paper products and 9,000 tonnes of tissue paper annually, the company exports 60% of its products to 24 countries on four continents.
French turnaround
In 2010, the company partnered with a French company to manufacture its plastic products portfolio. “We saw an opportunity as there were no big local producers, and we enjoyed enormous success,”
Mr Tserepas said. “However, the French government banned single-use plastics in 2020, adversely impacting companies involved in that sector
“Long story short, Lariplast France faced shutting down because that was our obligation under French law.”
The company sold off its machinery, but rather than close, it transitioned to produce tissue paper and toilet paper. This sparked an amazing recovery for Lariplast France. Before the legislation, it generated €12 million in revenue, slipping to €3 million within two years. After adopting paper production, Lariplast France bounced back to €12 million in 2023 and will top €17 million in 2024. The factory now supplies its paper products portfolio to clients across the Benelux region and is expanding into the UK.
New investments
At its Larissa HQ, Lariplast has invested €10 million building an autonomous paper-converting production plant next

to its existing operation. This involves the production of paper cups and salad bowls, plus the capability to produce any paper packaging required by a client.
“We have also earmarked an additional €2 million for new paper product solutions within two years,” said Mr Tserepas, whose father Ioannis is CEO.
Lariplast has also invested in innovative thermoforming-IML technology for its yoghurt cups. “We are going back to our roots and reinventing ourselves,” Mr Tserepas continued. “It means less plasti c per cup, but all the premium marketing labels are in the process.”
Thermoforming is a technique for producing rigid plastic packaging by adding the IML label during the process. The end result is a decorated packaging part produced in one step. “IML technology in thermoforming is still relatively new,” he added. Only 14 machines have been sold globally, and Lariplast has one.
Mr Tserepas outlined how Lariplast’s first thermoforming-IML products entered the market in January 2024 and were enthusiastically embraced by dairy industry clients: “There are many other

opportunities in the food industry that could benefit from this solution. Our strategy is to focus more on the industrial packaging side.”
Along with ambitions to reach €80 million in revenue by 2027, Lariplast is to build a €7 million “black box” logistics centre between the paper converting plant and the plastics production unit. “The 'black box' will connect the factories and serve as an autonomous warehouse,” Mr Tserepas explained. “The aim is to make production fully automated, from machine feeding to palletising.”
Sustainable aims
The company has adopted a zero-waste strategy in material production at its plastic plant. “When thermoforming, we realise around 36% to 40% as plastic waste,” said Mr Tserepas. “So, we have a closed loop system and transform the waste. It goes back through an extruder for reuse as raw materials. We internally recycle whatever we produce,”
Similarly, any tissue paper waste is recycled into products and resold to clients. Solar panels have been installed at Lariplast’s factories in Greece. Around 90% of electricity is generated for its paper-converting plant and about 20% for its plastic production unit.
“We continue to find ways to make our paper and plastic products lighter and fully functional,” Mr Tserepas continued. “Tha t means fewer raw materials are utilised, and carbon emissions are reduced in our production and transportation phases.
“We are actively analysing our carbon footprint metrics and aim to become more
efficient. Sustainability also means tackling food waste: our products are designed to protect food when transported and thus contribute to extending the expiration dates of food.”
Battling on
When pressed on business challenges, Mr Tserepas touched on finding skilled and motivated people to add to the workforce. “Another challenge is the European Union,” he said, “as it has a unique way of destroying European industries.
“It has this bureasucracy for European business to be cleaner, greener and safer , but then allows in imported goods from China and elsewhere in the world that do not comply with its own guidelines.
“Secondly, most exporters into Europe receive a premium subsidy from their state every time they export, and the EU doesn't put duty on the products. How many European industries will still be aliv e in ten years?”
Mr Tserepas added that despite these issues, Lariplast maintained key relationships with its supply chain based on quality, consistency, transparency, safety and reliability.
The company remains highly ambitious about innovating in food packaging as fast as the industry needs while realising plans to set up a factory in the USA. “My father says he will not leave the business until we have a plant in the States,” Mr Tserepas said in conclusion. “The US is the epitome of our portfolio. We remain active and hopeful of realising that ambition.” n
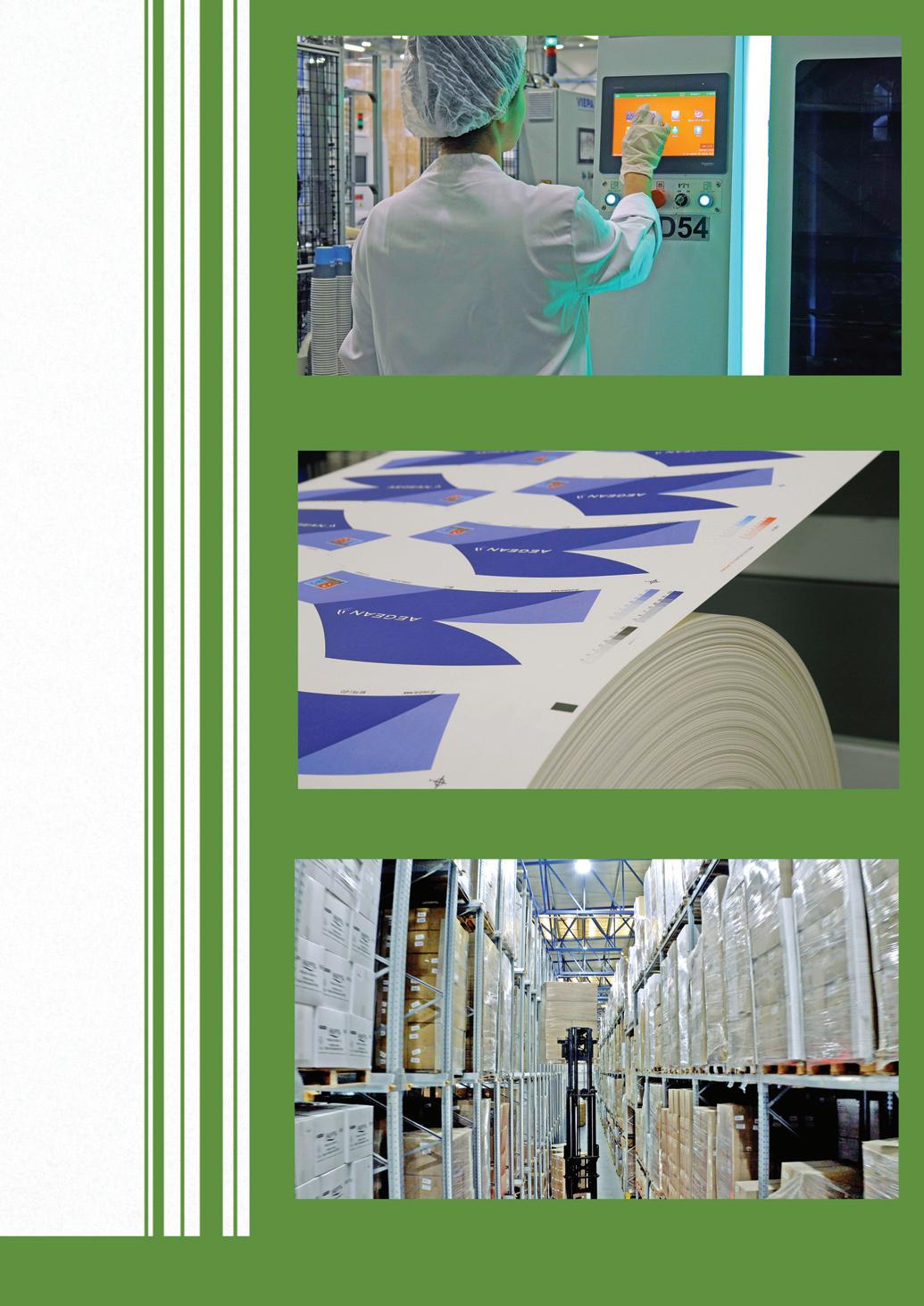
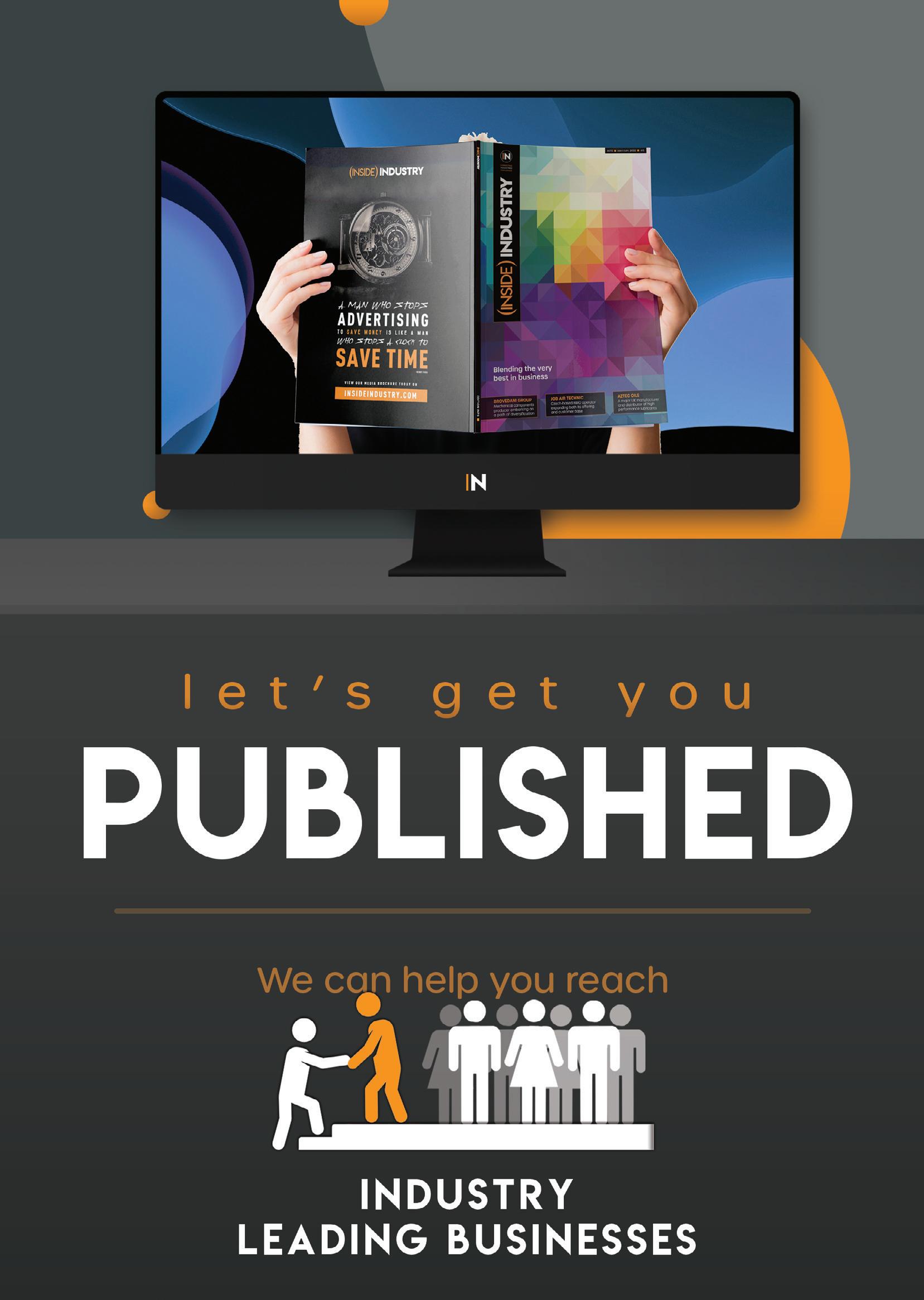
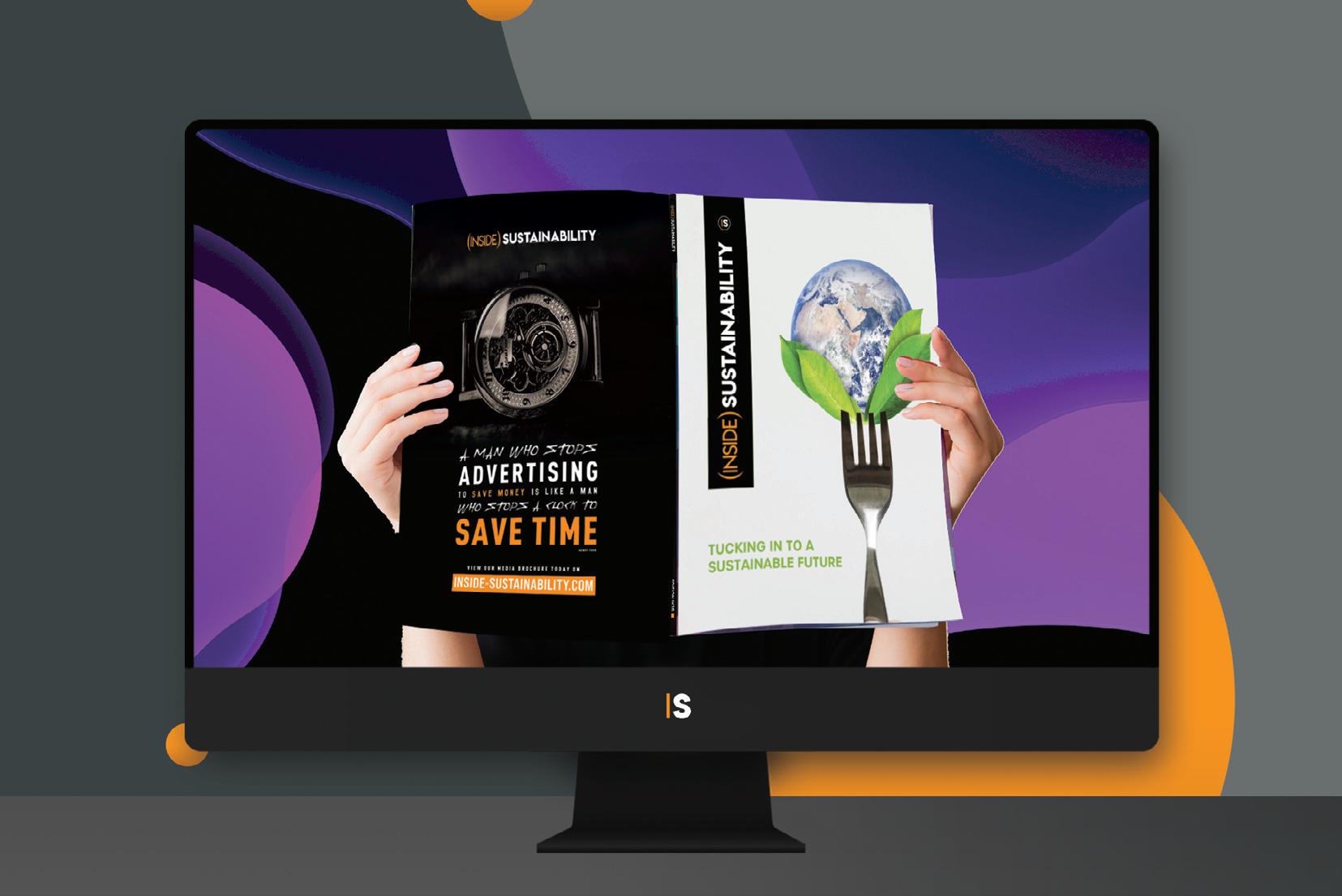