
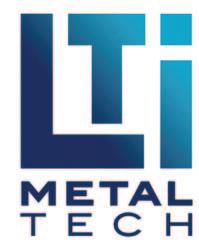


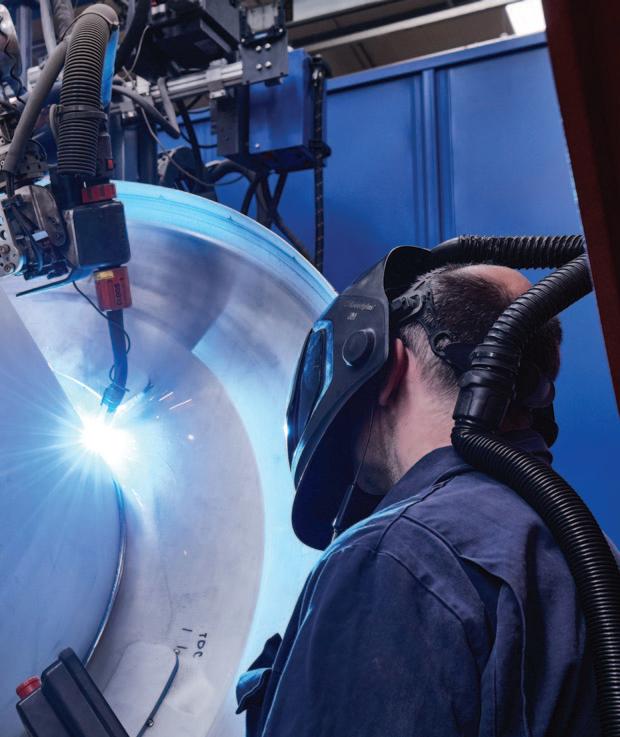
LTi Metaltech manufactures pressure vessels using robotic and semi-automated processes, specialising in the production of cryogenic pressure vessels. Managing Director Edgar Rayner and Business Development & Marketing Executive Nazir Ali discussed sustainable manufacturing and having a positive impact, in conversation with Antonia Cole.
ASa company, LTi Metaltech is not only focused on manufacturing high-quality products, but also on making a difference to the world, Managing Director Edgar Rayner said: “The products we create serve industries that are essential to the wellbeing of people and the planet. We are dedicated to delivering value through our expertise and innovations, contributing to a better society and making stuff that truly matters.”
Offering precision fabrication and welding to highly regulated sectors, including the healthcare, renewable energy and nuclear f usion industries, LTi provides innovative solutions that meet stringent requirements. The company combines over 40 years of experience with a skilled workforce and advanced technology to deliver the most effective products that solve customer challenges.
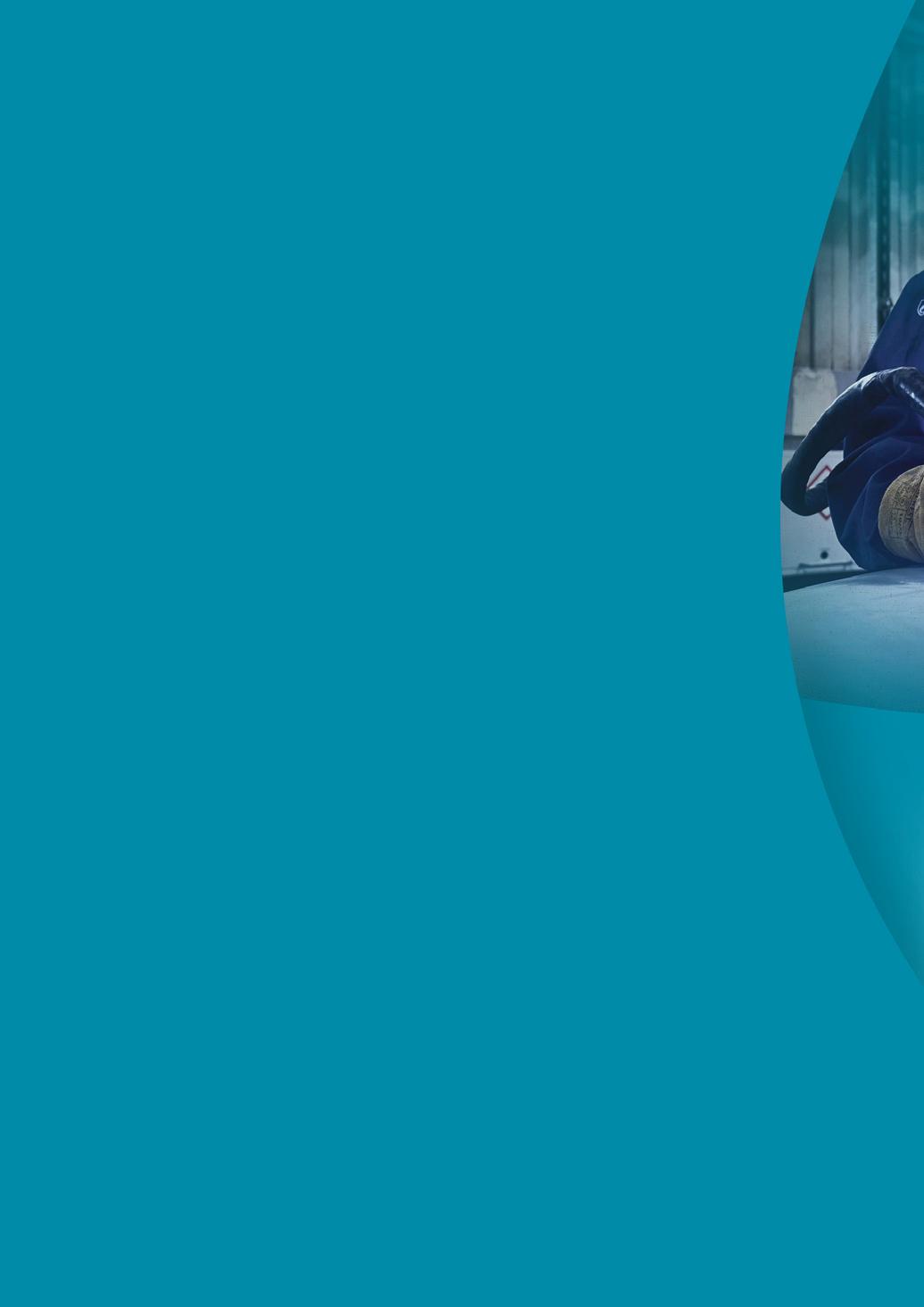
Based in Abingdon, Oxfordshire, LTi generates an annual turnover of £30 million and manufactures approximately 1,350 vessel sets per annum. The company also owns Vessco Engineering, which contributes an additional £6 million annually. With over 150 employees, 90,000ft2 of factory space and an additional 8,000ft2 facility, LTi is well equipped to supply a range of products that adhere to AD Merkblatt 2000 and PD 5500 pressure containment standards.
“Something that we pride ourselves in, is that our average length of employee service is eight years,” commented Mr Rayner. “We have a really talented mix of people that push boundaries and strive to exceed customer expectations. This, along with the latest technology,

support of a global supply chain and an in-house testing facility, guarantees that we are consistently providing the best products and services.”
Sustainable improvements
LTi’s environmental focus has grown substantially in recent years. With the establishment of a sustainability team, the company is now able to identify ways in which it can make a positive impact throughout operations.
Currently, LTi is making a £300,000 investment into the installation of solar panels across the factory. Upon completion, this will reduce the company’s reliance on the main grid by 45% and minimise carbon emissions by up to 70 tonnes. LTi is located in Milton Park, Oxford’s leading international business and science park, and it will be the first company in the estate to install solar panels.
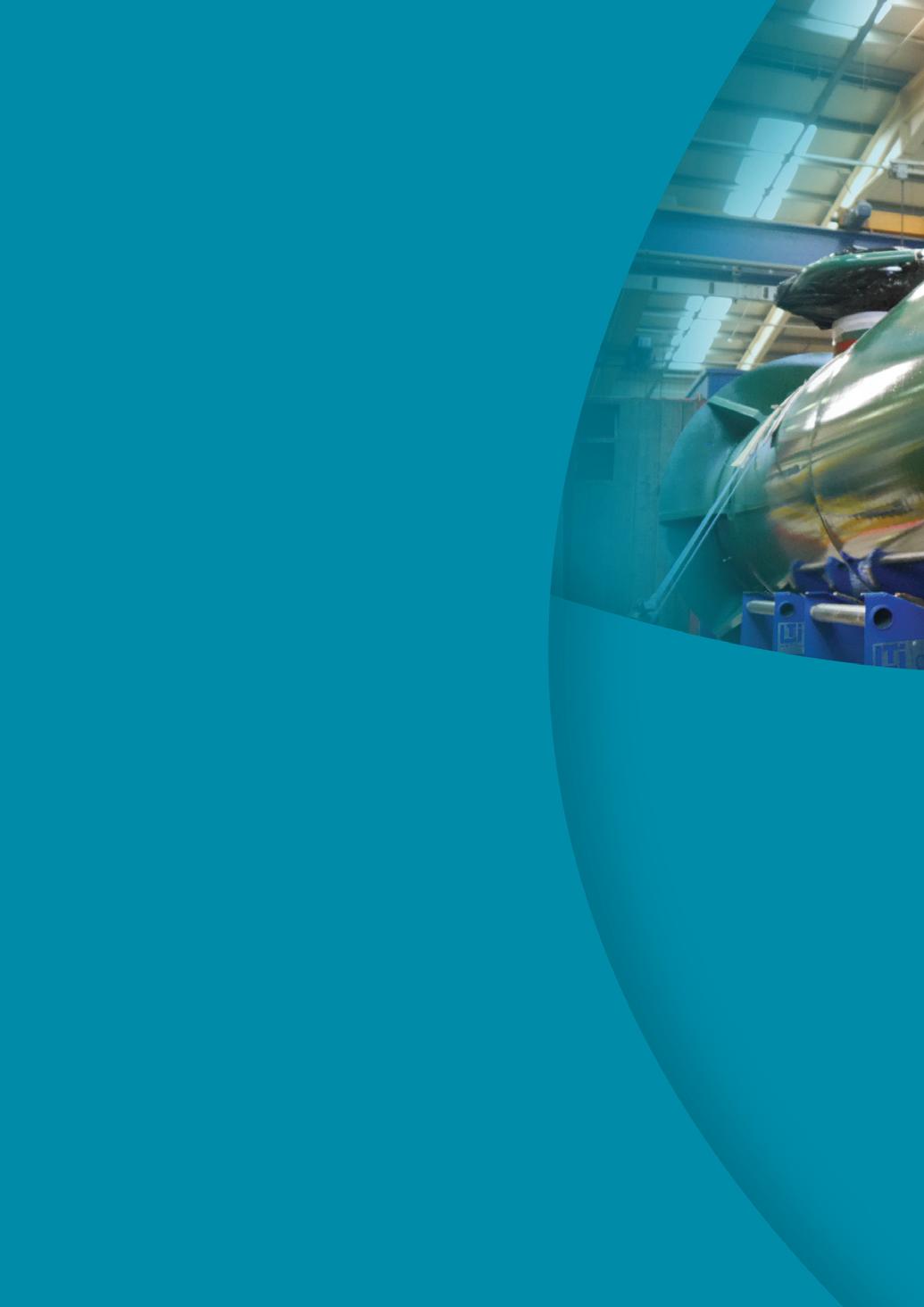
“Our solar panel investment is a big achievement for us,” explained Mr Rayner. “It’s the hard work of our sustainability team, owners and entire workforce that has resulted in this progress. This is a great start to our environmental journey, but we are always looking to the future and investigating ways in which we can limit our impact further.”
The company has also implemented other environmental measures including a Switch It Off internal campaign, which encourages employees to turn off any equipment or lighting that is not currently in use. To support this, automatic lighting has been installed, reducing energy consumption across the site.
Furthermore, LTi is limiting paper usage, as well as material waste in operations. By implementing more efficient processes and controlling resource use, the company is able to reduce its impact. LTi’s full-time onsite sustainability advisor constantly develops initiatives to improve environmental standards throughout the facility.
“Not only are we working on larger projects, like our solar panel installation, but we are also implementing a range of smaller initiatives throughout the company to make a real difference in our carbon footprint,” added Business Development & Marketing Executive Nazir Ali. “We are looking in detail at every aspect of LTi, and finding ways in which we can improve . Our sustainability team is driving us forward in this mission, setting targets and preparing us for the future.”
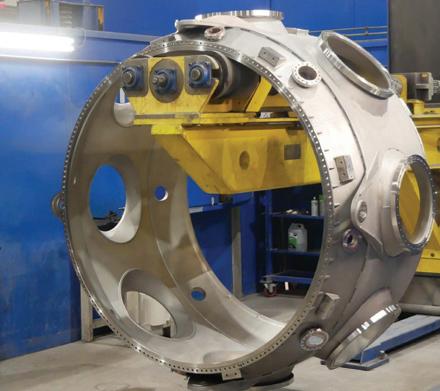
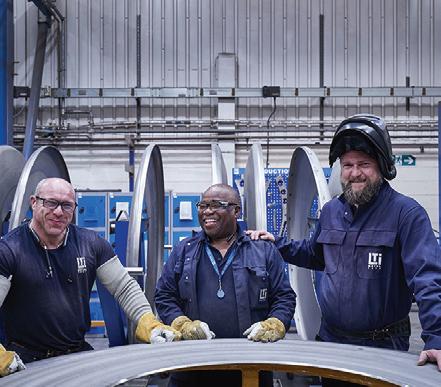
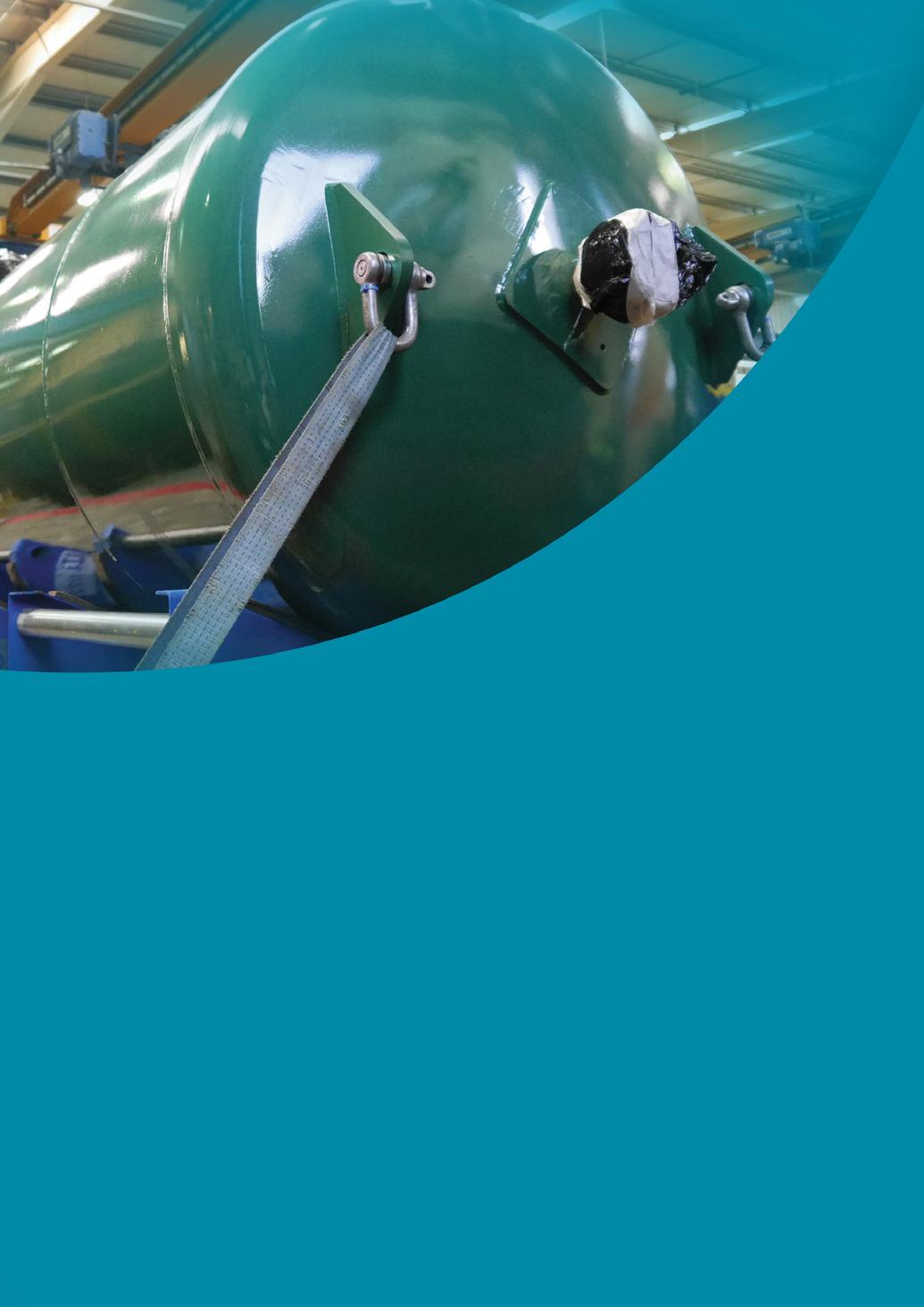
Resolving challenges
In the design stage of production, LTi’s team of engineers work to make products as efficient and effective as possible, whilst adhering to specific industry regulations. The company engages in strong and open lines of communication with customers, ensuring all needs and expectations are met throughout development.
To then manufacture the product, LTi utilises a range of innovative technologies. From cutting and forming to various welding methodologies, the company implements the latest industry advancements and processes into operations. LTi is able to use a range of materials, such as aluminium, stainless steel, carbon steel and more, with thickness capabilities ranging from 0.5mm to 35mm for stainless steel on the laser, and even thicker

materials with the waterjet, ensuring versatility and efficiency.
“We have a quality team that supports and validates the standards of our products too,” said Mr Ali. “Our test house completes both destructive and non-destructive testing to guarantee products meets the necessary levels of quality. Over the last year, we have received an outstanding quality score of 99 percent from our customers. This demonstrates our dedication to exoceptional work.”
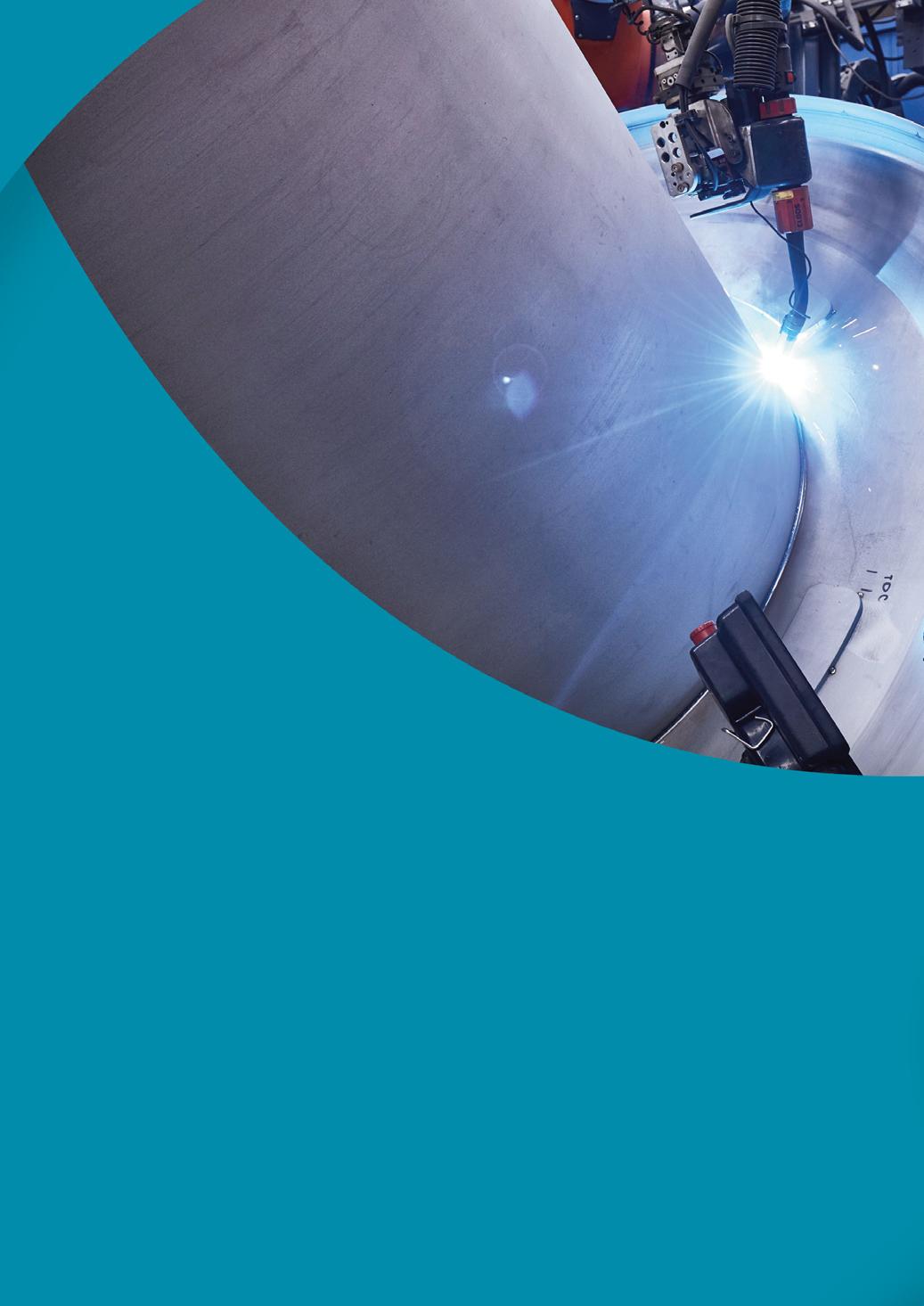
“We’ve also been doing a lot of work with a fusion energy company called Tokamak Energy,” continued Mr Rayner. “One of our projects involved developing a vacuum vessel, which had some really challenging requirements. In projects like these, it’s about demonstrating
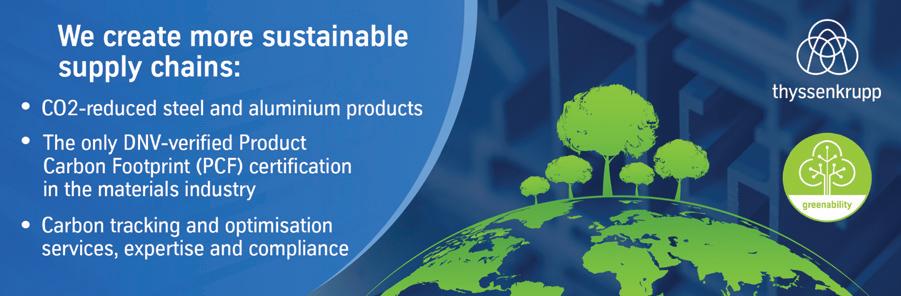
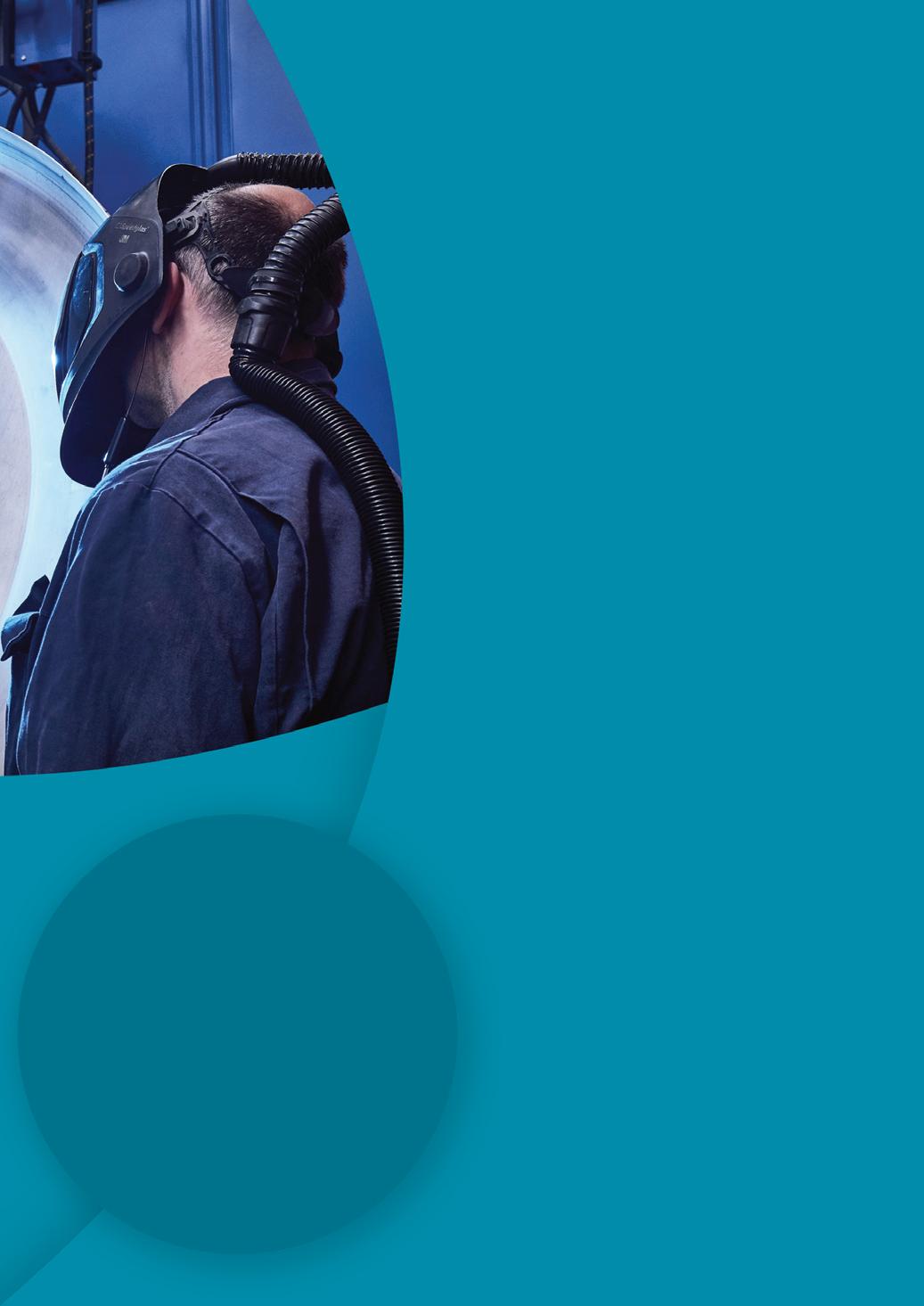
the ability to meet specifications, whilst also adhering to regulatory requirements, which are key. The expertise of our staff and the capabilities of our technology however, enabled us to use unique material grades and techniques successfully.”
Embracing technology
LTi collaborates with partners and suppliers to deliver products that meet customer expectations. The company focuses on building relationships across the industry to not only deliver high-quality services, but to also improve environmental standards and limit the impact of the supply chain.
“Many of our suppliers have worked with us for a very long time now,” commented Mr Rayner. “We have built up trust and can effectively collaborate for better results. At LTi, we are all about people. We have a great team who are able to connect and effectively communicate with people across the industry. We all work together, striving for continuous improvement.
Looking forward, LTi plans to continue embracing technology in order to progress its capabilities. From incorporating electric cars to utilising AI, the company is investigating a multitude of ways to make operations more efficient and environmentally friendly.
“By looking at the market and identifying sustainability issues, we have been able to make good progress improving our impact,” added Mr Rayner, in conclusion. “What we are doing at LTi is meaningful. The industries we support are essential to society and we are constantly aiming to provide them with the best service possible.”
n OVER THE LAST YEAR, WE HAVE RECEIVED AN OUTSTANDING QUALITY SCORE OF 99 PERCENT FROM OUR CUSTOMERS
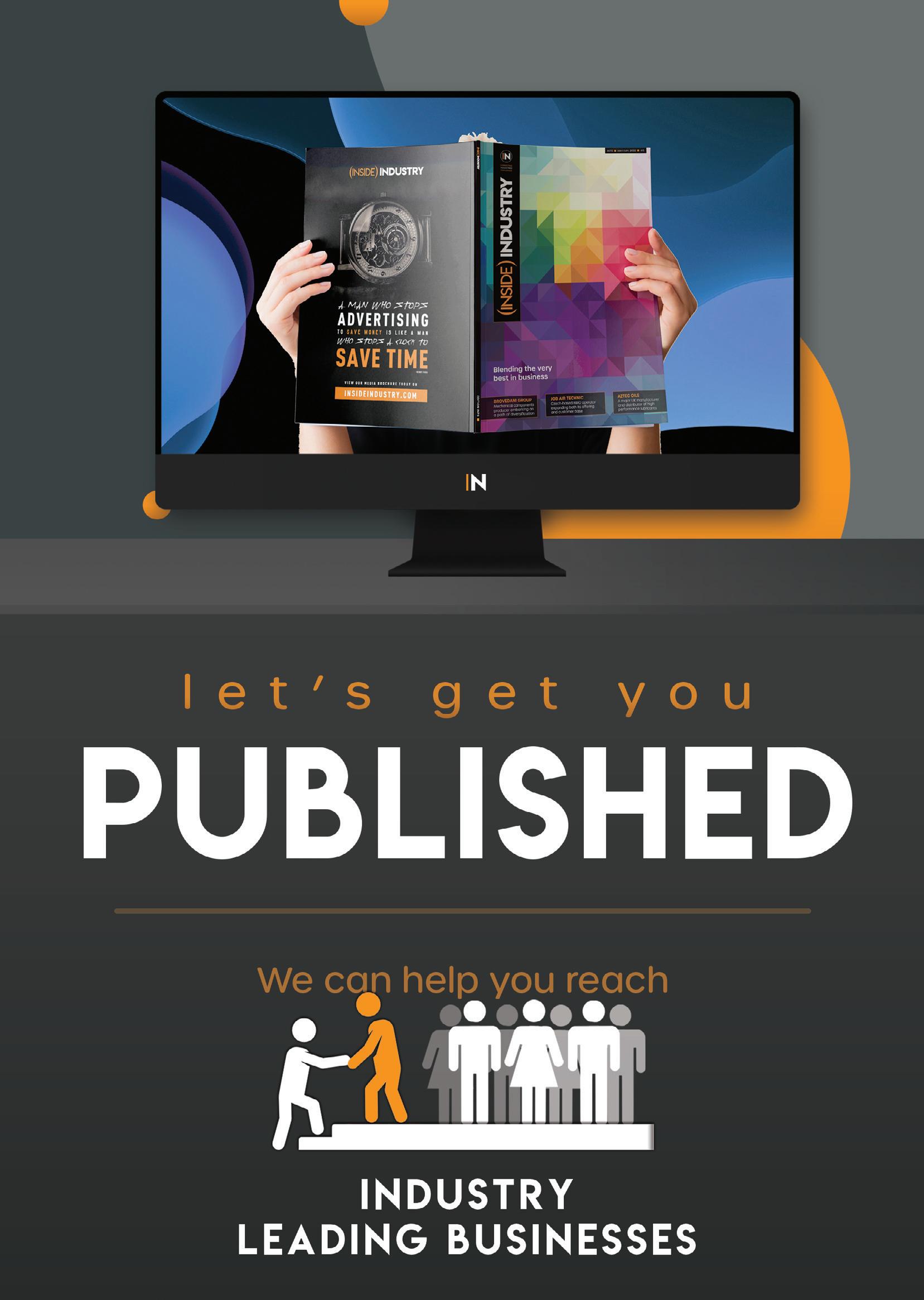
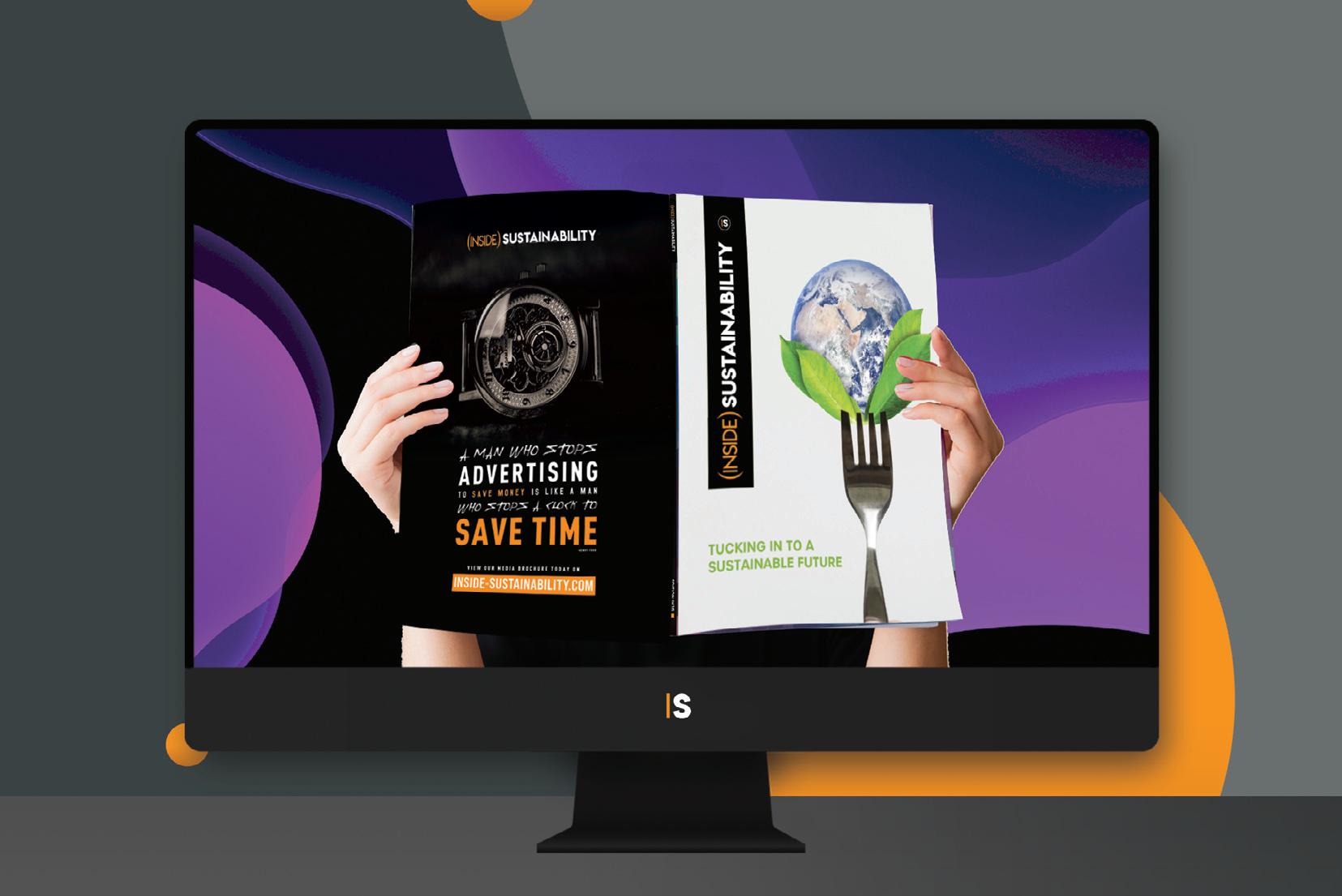