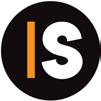
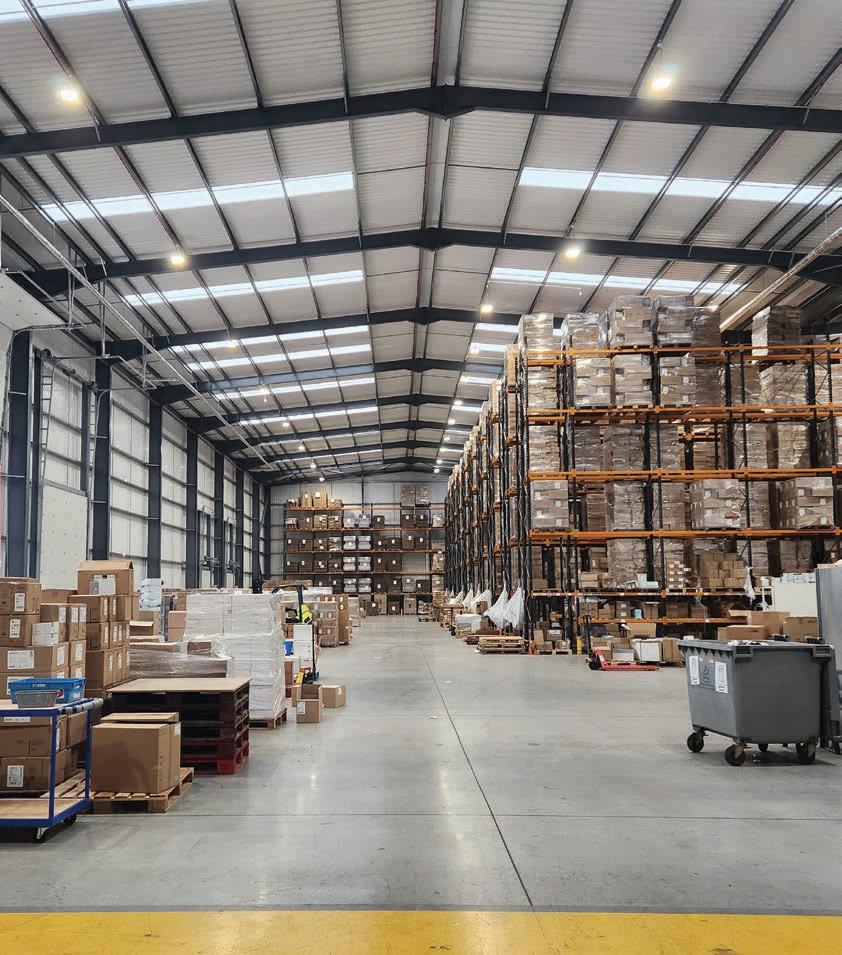
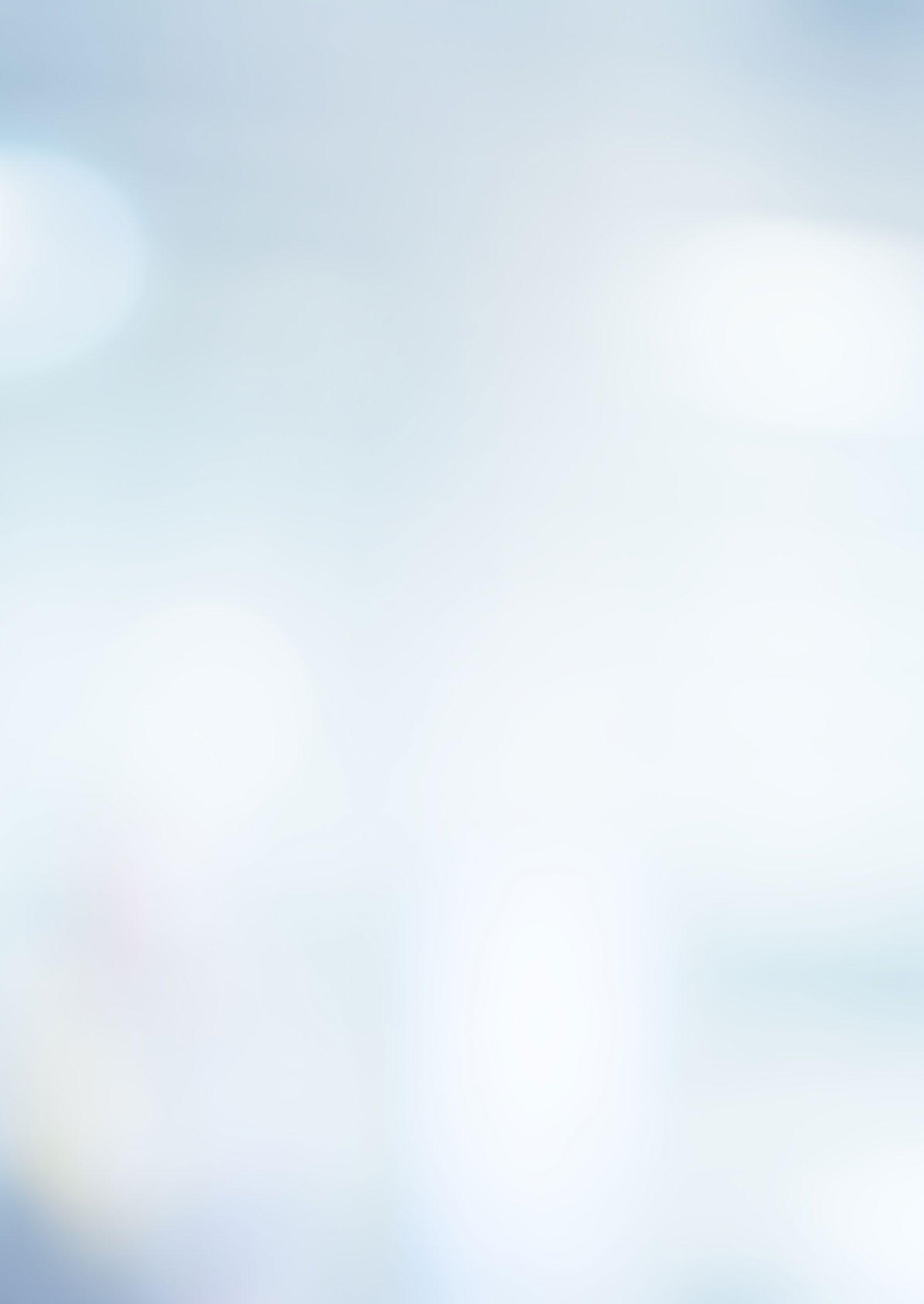
Optimum Medical is a UK-based healthcare manufacturer, specialising in catheterisation, urology and healthcare lubrication. The company has products in an impressive 77 countries, as well as every NHS hospital in the UK. CSR and Sustainability Manager Ian Wheeler explained more to Hannah Barnett.
From the start, Optimum Medical was driven to do things differently. This has meant using the company’s relatively small size to its advantage.
“We were founded by two guys who wanted to make a difference,” said Ian Wheeler, CSR and Sustainability Manager. “We’ve been very successful, but we’re not as big as a lot of our competitors, and that makes us agile. For example, we collect feedback from multiple avenues, and it’s reviewed weekly. If there’s a common theme, or something we can act on quickly, we might discuss it on the Monday, and often when we meet again on Friday improvements will already be in place.”
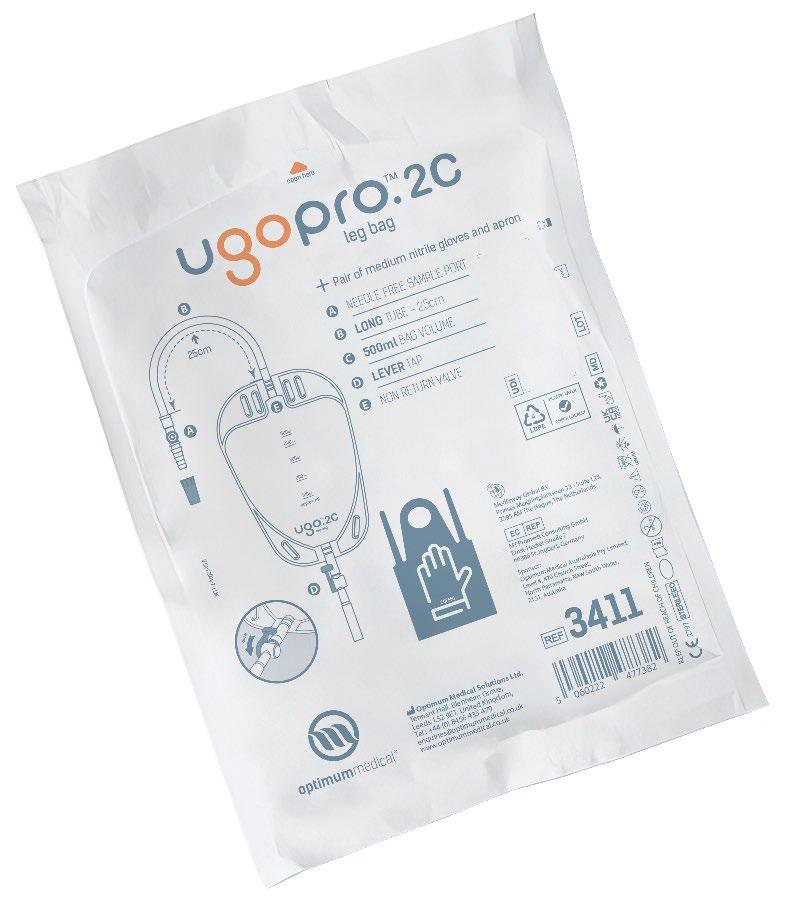
This is testament to Optimum Medical’s dedication to its customers, which has been infused through all it does since the company was founded in in 2008. The business won its first NHS contract in 2009, and its first international contract followed the next year.
A sales office opened in China in 2012 to facilitate international expansion and the company has kept growing ever since, including the acquisition of Hunter Urology.
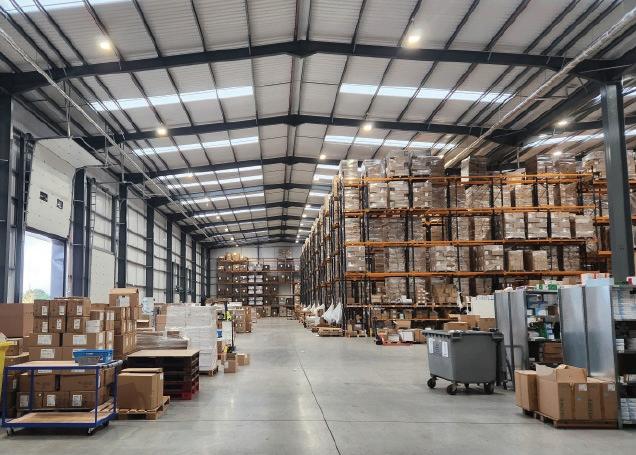
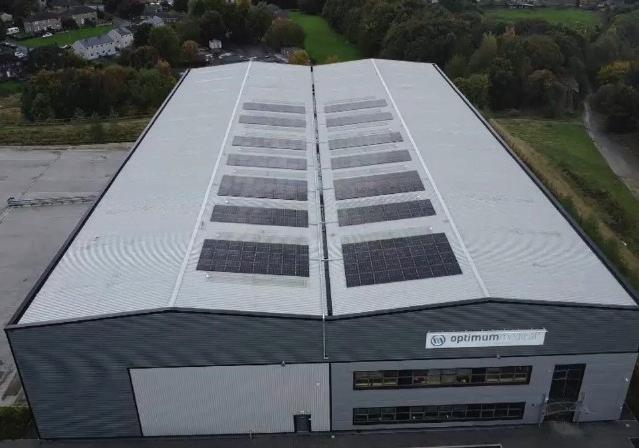
Turnover for 2023 was £18.5 million, with expectations for that to rise to £21.2 million in 2024. The company is supported by 85 UK-based staff over two sites: an HQ in Leeds and a warehouse in Bradford.
Prior to 2021, the company was solely a manufacturer and supplier of medical products, but that year it founded Vyne, a Dispensing Appliance Contractor. The service has been complemented more recently by the launch of an app.
“It’s ultimately a home prescription delivery service,” Mr Wheeler explained. “Rather than
just supply the items, we’re able to carry that service back to the patient and ensure that they get their products in a timely, efficient and caring manner. That is a huge part of the business now.
“We have patients who depend on us to get their products to them in a way that is right for them, with as little hassle as possible. Many are going through the most difficult period in their lives, so it’s important that we’ve got people within the company who can support them, including our team of nurses.”
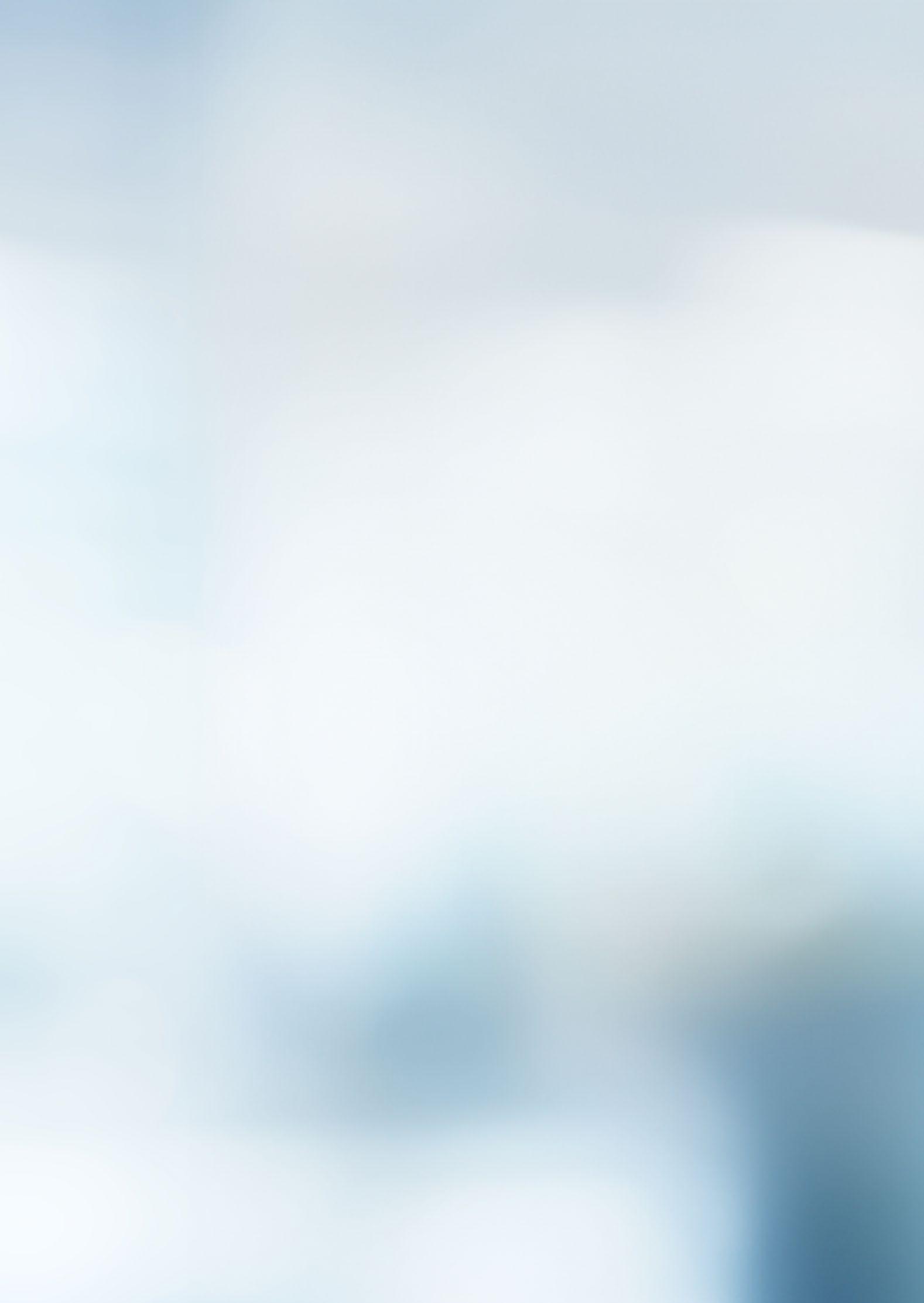

People, planet and community
Several years ago, Optimum Medical purchased its Bradford warehouse to maintain control over operations and run sustainably. The site includes electric forklift trucks with charger timers installed to charge overnight when there is less demand on the grid. The site has LED lighting throughout and seven EV chargers free for staff to use.
“I joined in early 2022 and since then, we’ve made huge strides, starting with carbon auditing and greenhouse gas monitoring,” Mr Wheeler said. “That was a huge achievement for us. In 2023, for the first time, we offset all our Scope 1, 2 and 3 emissions. Again, a huge accomplishment. I’m not sure how many other businesses in our sector are doing that, if any.”
Additionally, the company also recently finished a solar installation on its warehouse, meaning it is now generating its own energy and using it responsibly. This sense of responsibility filters through the workforce.
“I have a meeting with every new member of staff,” Mr Wheeler explained. “And recently, when talking about the sustainability objectives of the company, a significant number of people have said that’s one of the reasons they joined. They saw what we were doing, and it resonated.”
A sensible supply chain
When analysed, the biggest impact to Optimum Medical’s carbon footprint was found to come from shipping and freight.
“We have suppliers all over the world,” Mr Wheeler explained. “Clearly, if we’ve got products coming
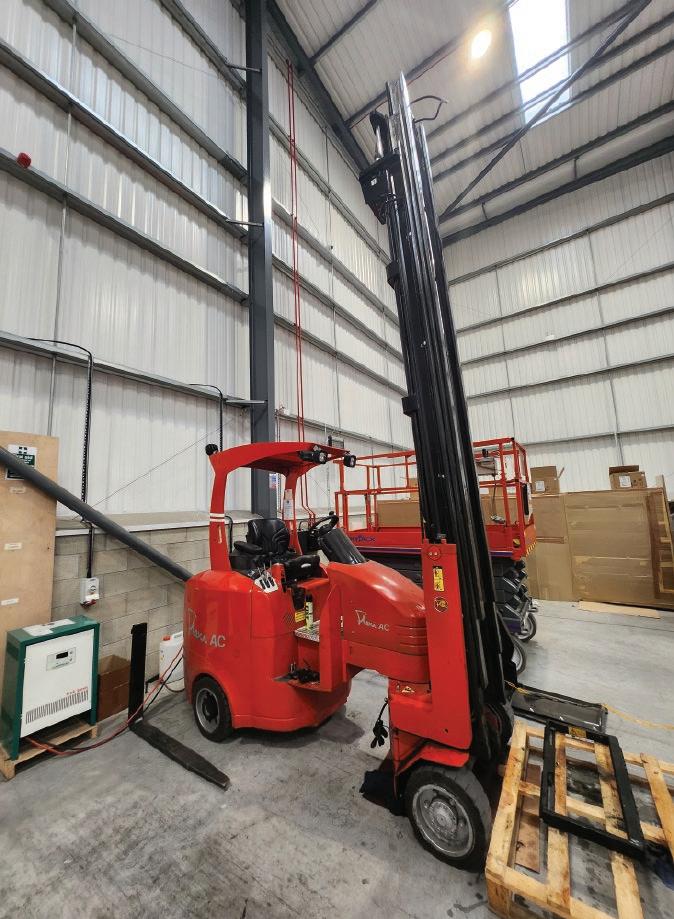
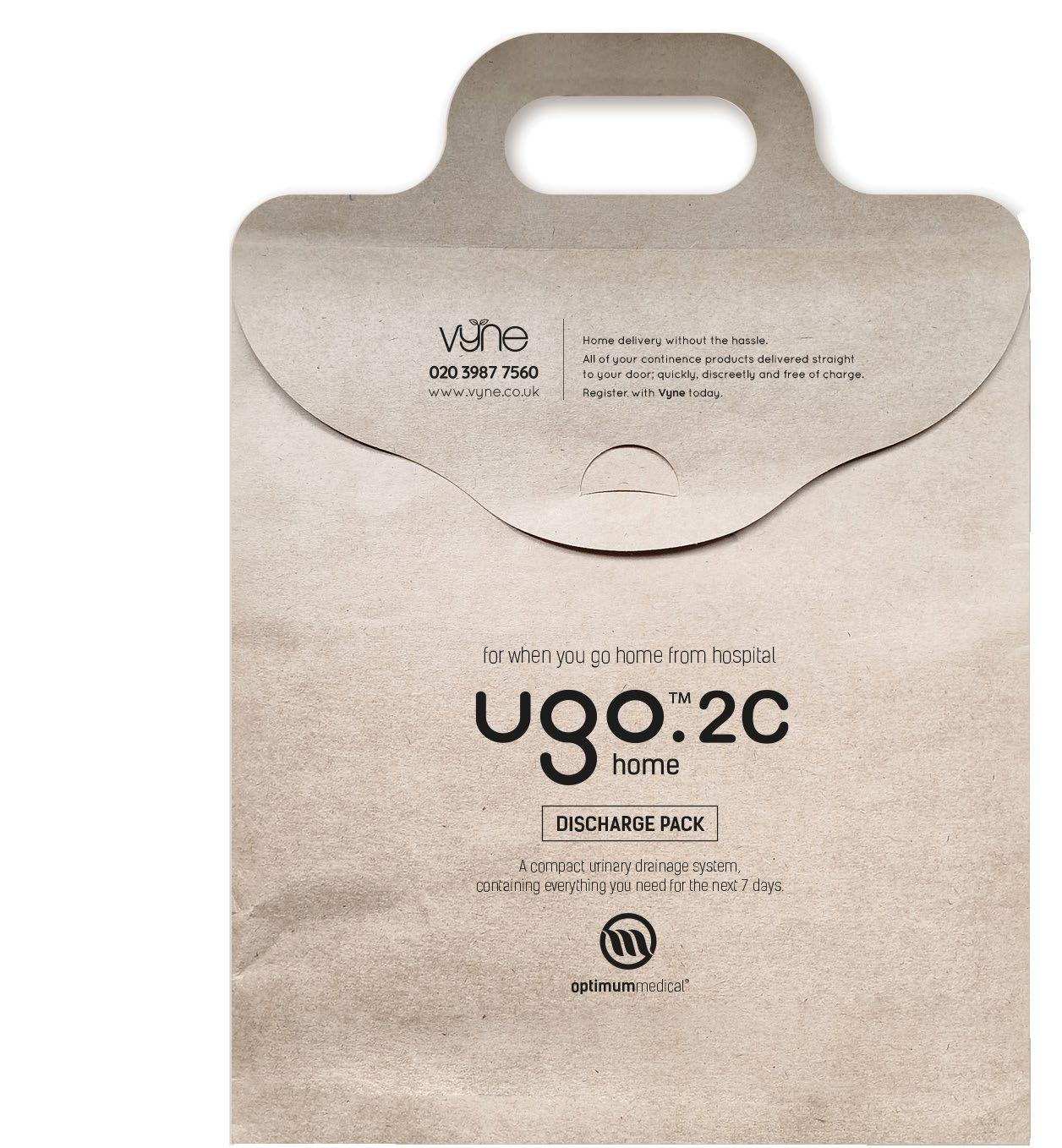

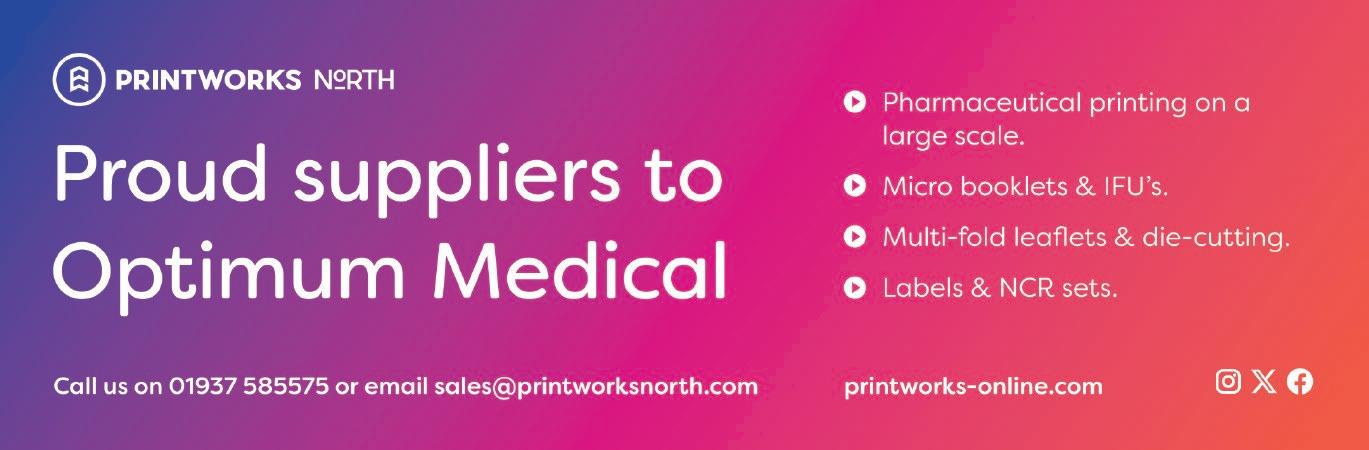
from China, there’s going to be significant emissions associated with the shipping. It’s a difficult area because there’s only so much that is under our control – we’re largely waiting on advances in technology and industry improvements.”
However, Optimum Medical has also made changes to its freight policy. This includes the consolidation of containers and packing products in the most efficient way possible. The company has also started working more closely with a particular handler with strong sustainability qualifications and recognition in the industry.

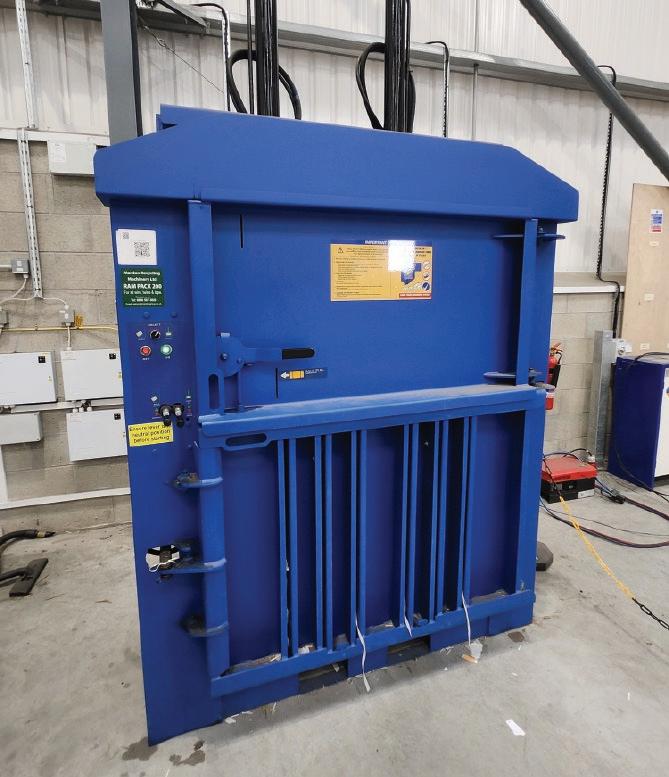
Removing and reducing plastic has also been particularly challenging for a company operating in the medical industry, with products intended to go inside the human body. Many products must be sterile, made using virgin plastics and packaged in a way that prevents damage.
“We’ve worked hard at this and in some products, we’ve managed to reduce the plastic by 85 per cent – or completely eliminate it,” said Mr Wheeler. “Also, where before we offered five different sizes of catheter straps, but only one size of box, we have made changes. We couldn’t have different sized boxes for each of them, but we’re now
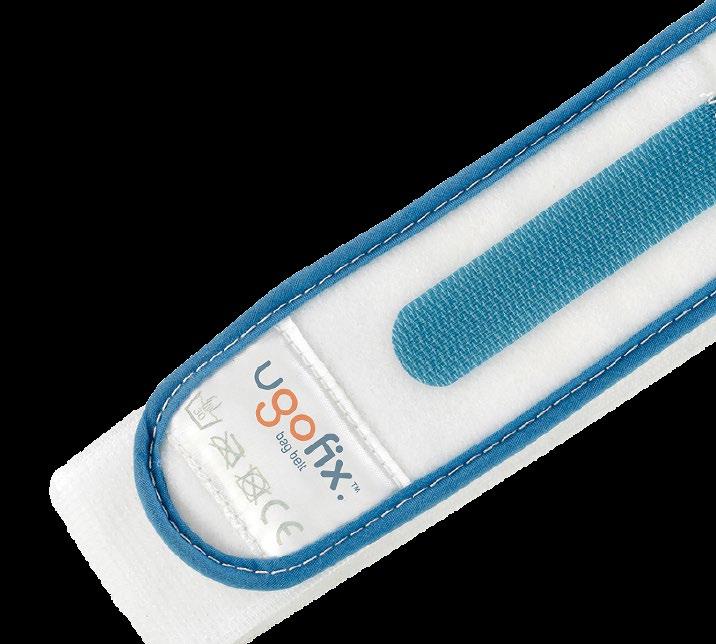
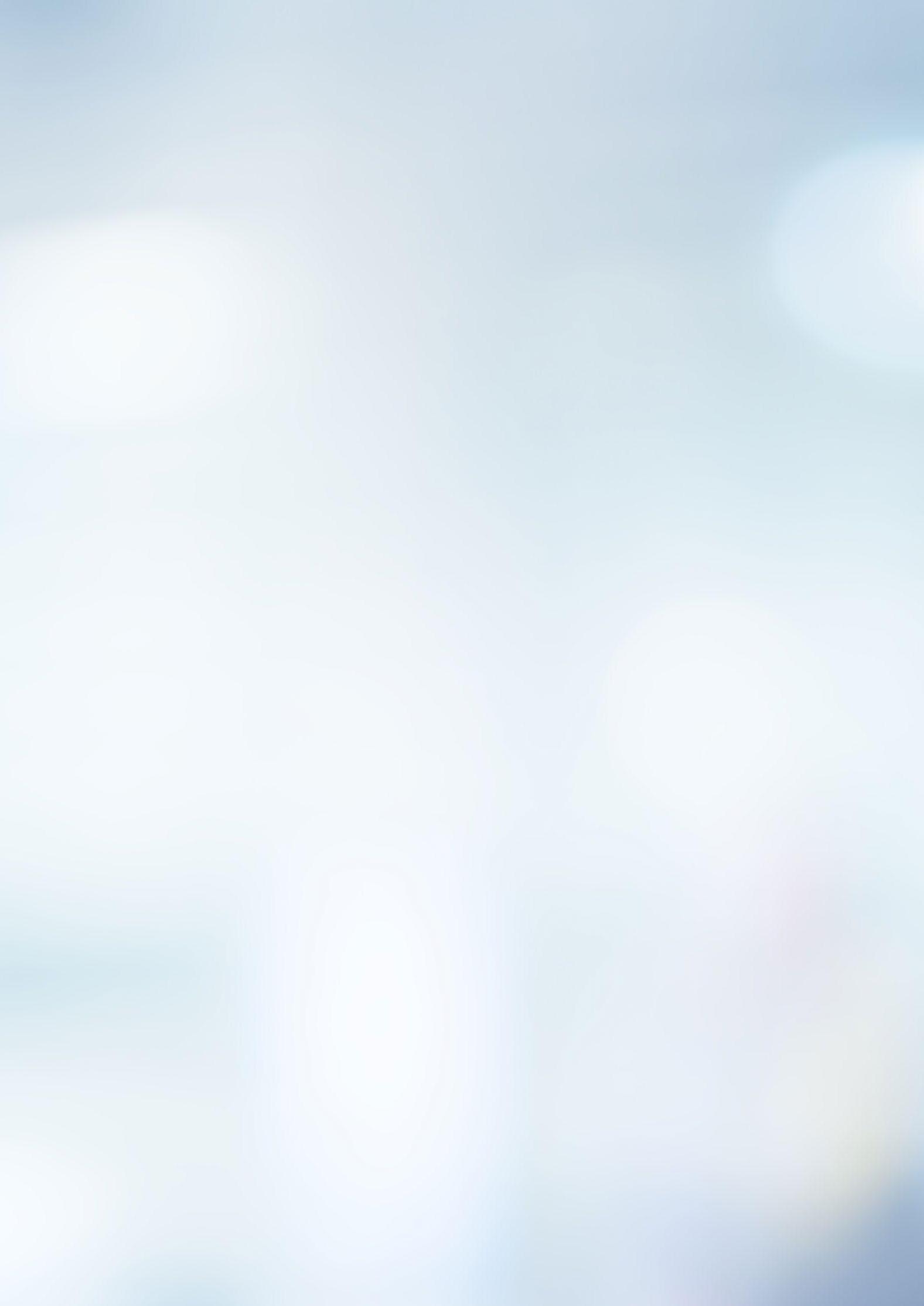
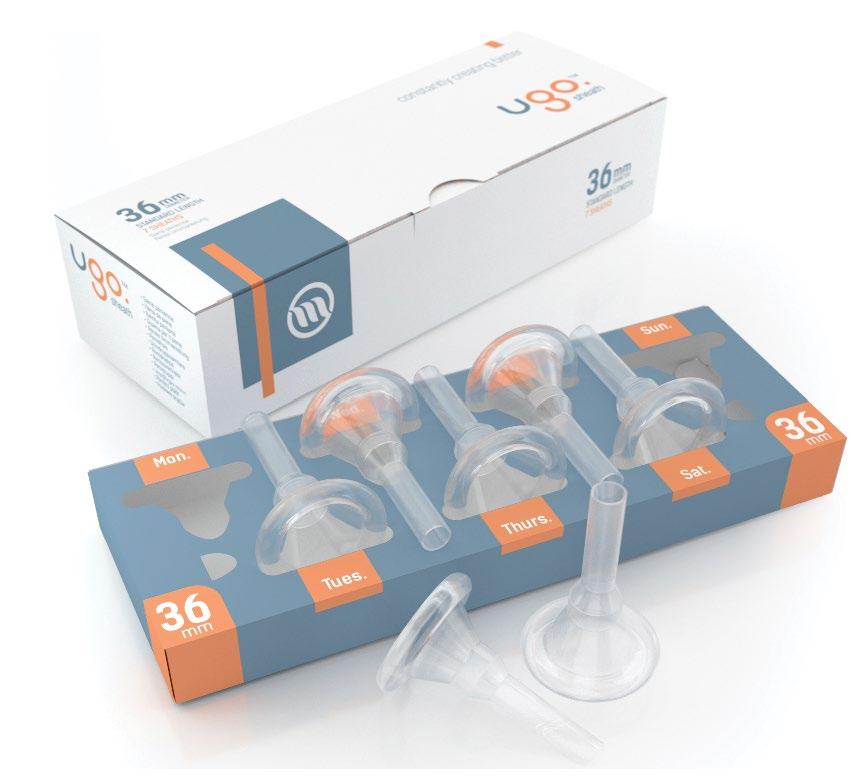
at two different sized boxes, both of which are reduced in size. It’s been a real success story.”
Human relationships
The company works closely to maintain a strong and successful supply chain. Some suppliers may be ahead on their sustainability journey, others may have further to go. The idea is that they can learn from each other. And, as Mr Wheeler explained, at Optimum Medical, suppliers are like family.
“We have amazing relationships and still work really closely with our first supplier from 2008,” he explained. “We visited them recently with one of the directors, and I was blown away by how close that relationship is. We even ate with them that evening, not at a restaurant but actually with the family. It was an amazing experience.
“We don’t want to let each other down, so we focus on being open, honest and reasonable with suppliers. If we expect a change in demand for products, we
will involve the supplier in that conversation and give them plenty of notice. We’ve got a really strong procurement team having those conversations.”
It is no surprise that Optimum Medical extends this familial atmosphere to its interactions with end users. Local customers based in the Leeds and Bradford area now receive home deliveries from the company’s own service, run by EV’s and powered by solar. Perhaps even more significantly, this means the company can ensure the personal touch.
“We get excellent feedback about our delivery drivers,” said Mr Wheeler. “They say ‘Steve is brilliant, I really look forward to seeing him, he helps me put my products away and always has a smile on his face.’
“Personally, I’ve never had so much job satisfaction. Every project we work on makes a difference. If it’s putting solar panels on the roof, then it’s making a difference environmentally.
If it’s taking feedback from customers and changing the way we work, then it’s improving someone’s quality of life. Finishing every day knowing that is huge.
“Optimum Medical is such a positive environment. Everyone’s really engaged with the message of doing what is in the customer’s best interests at all times.” n
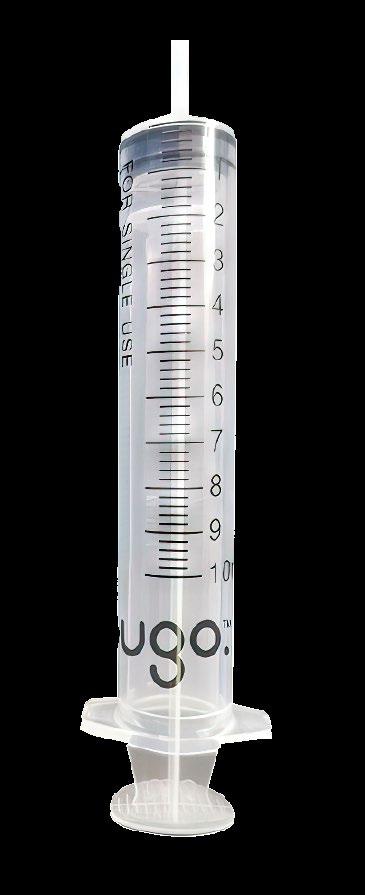
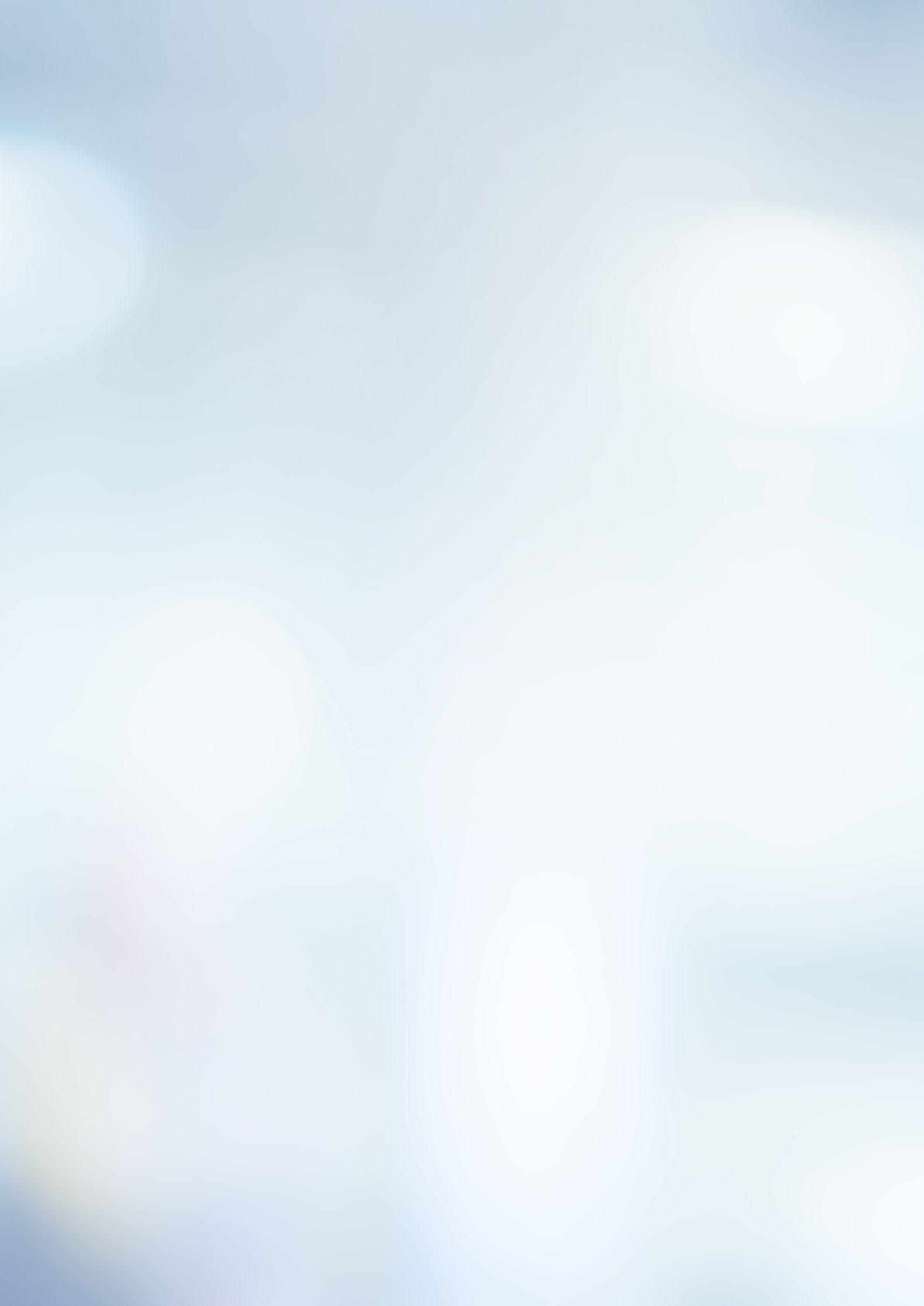


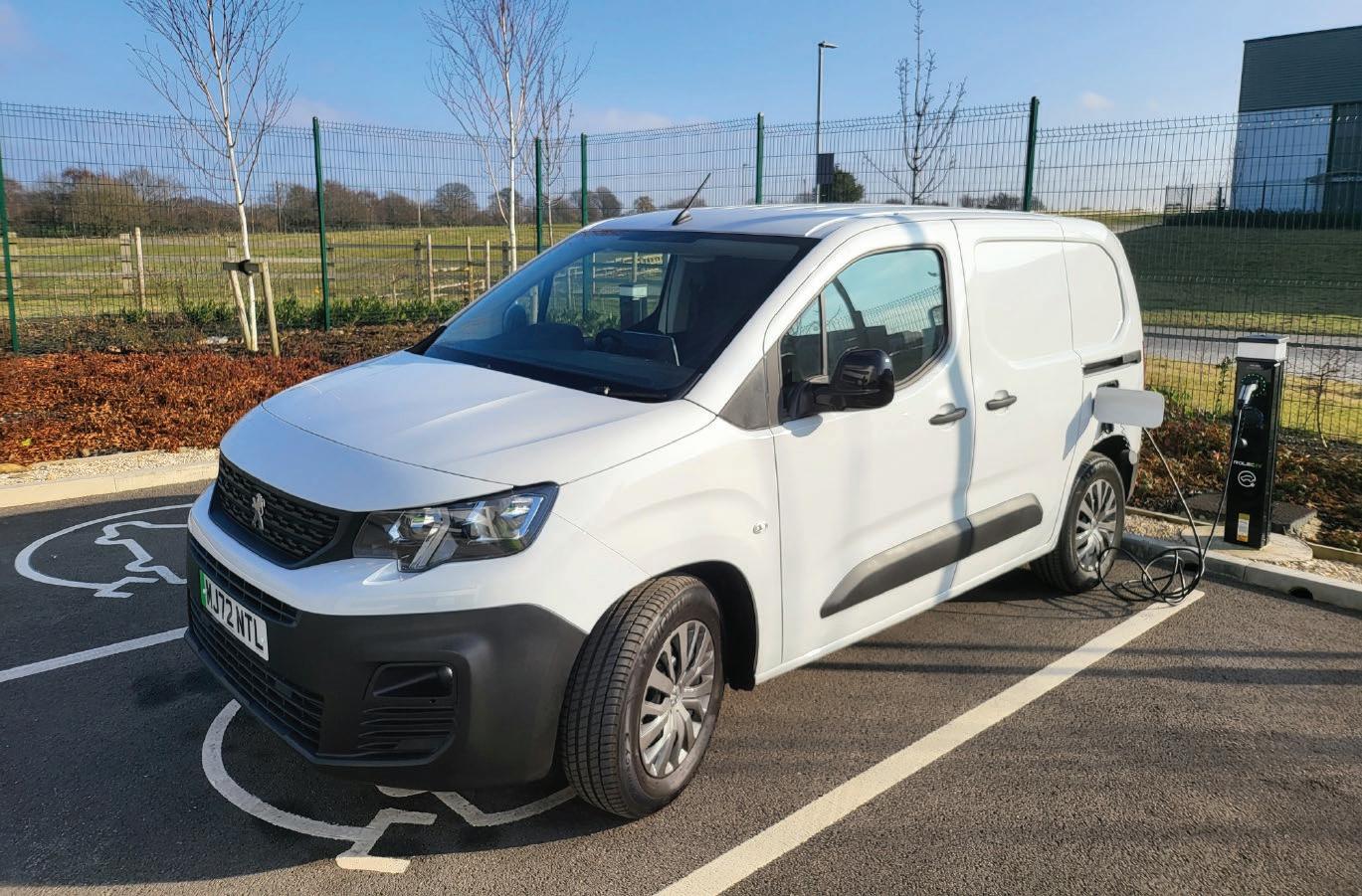
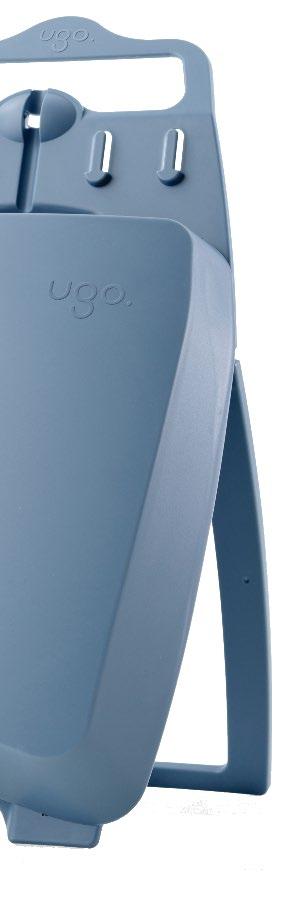
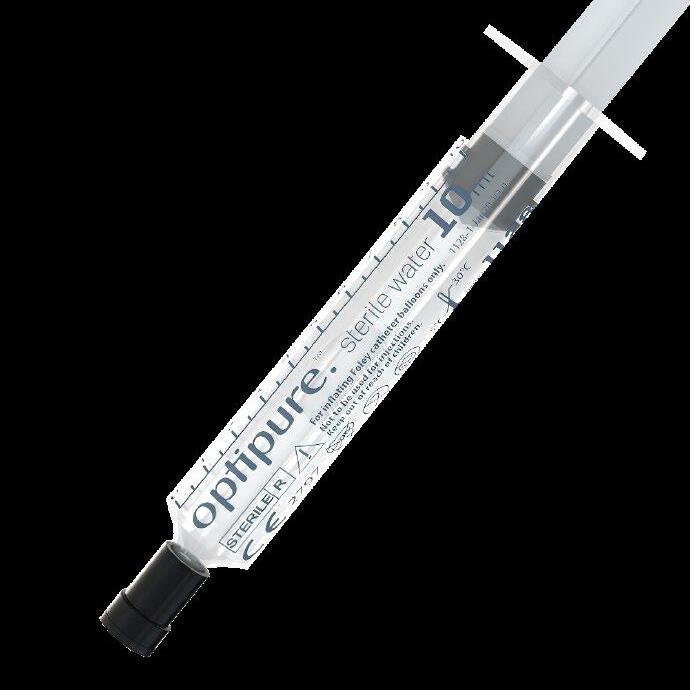
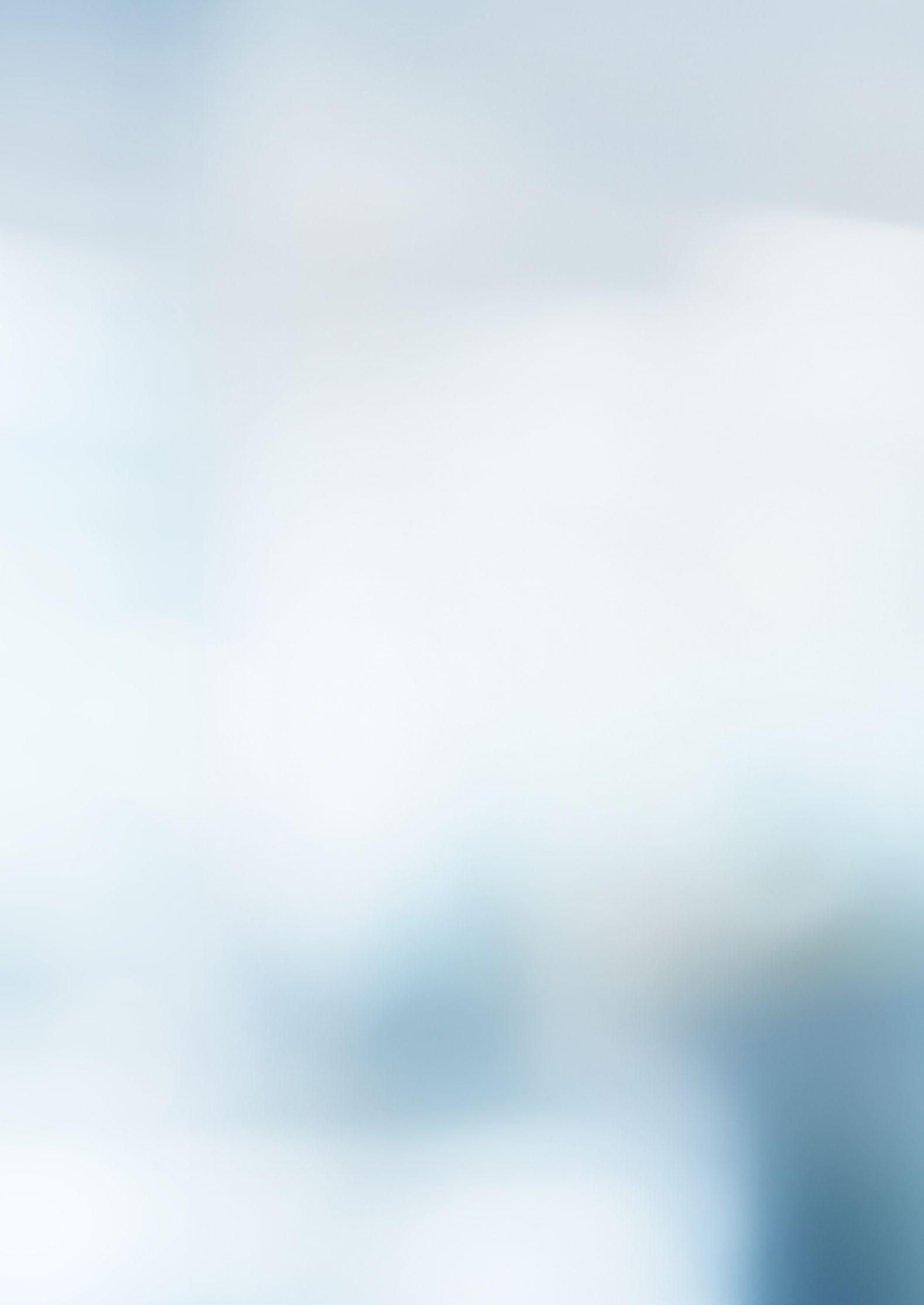
