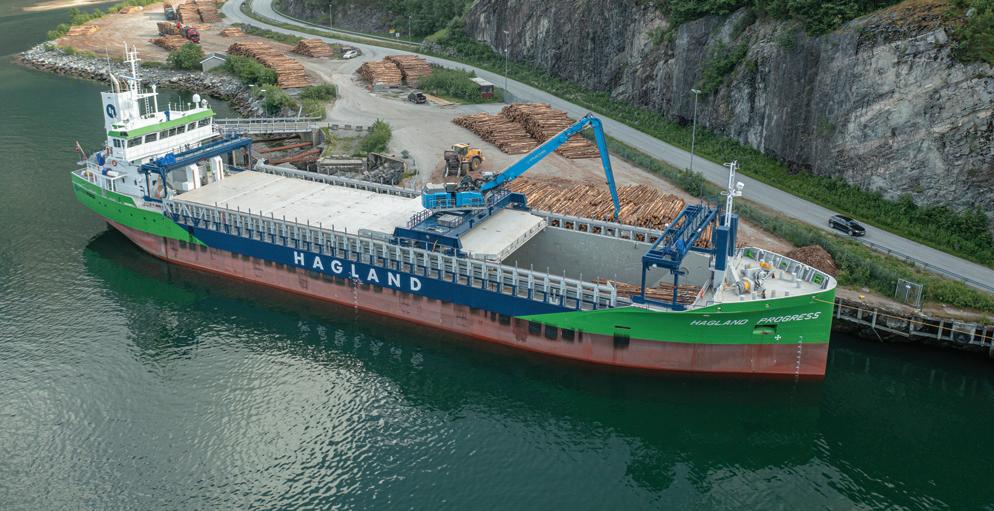

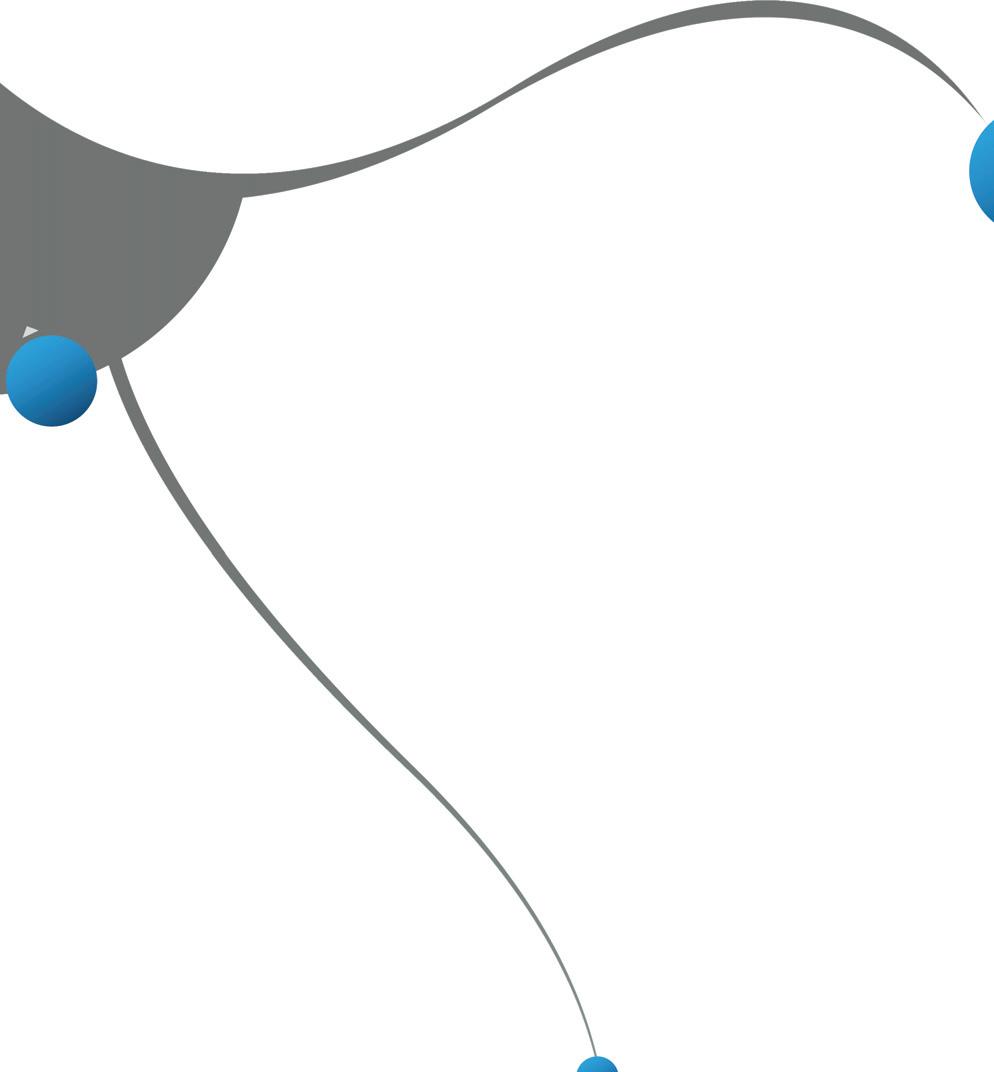
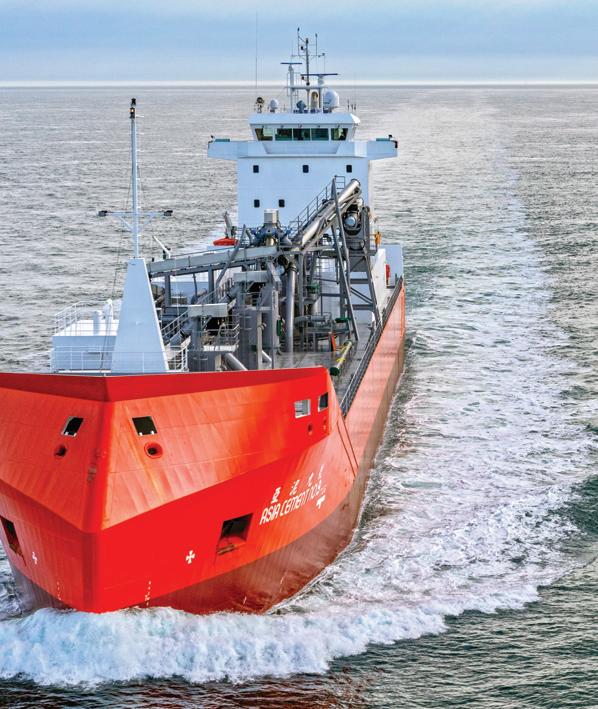
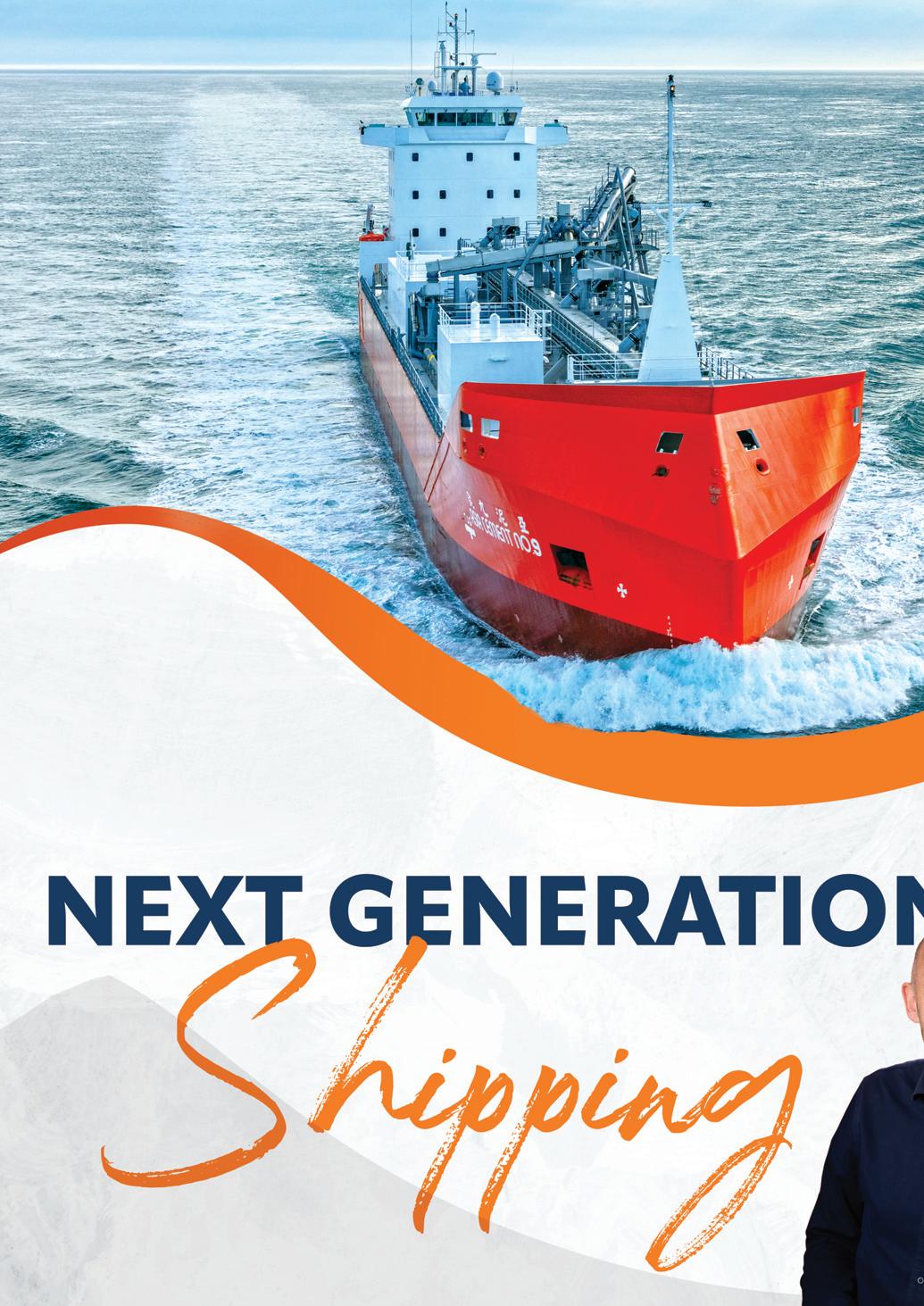
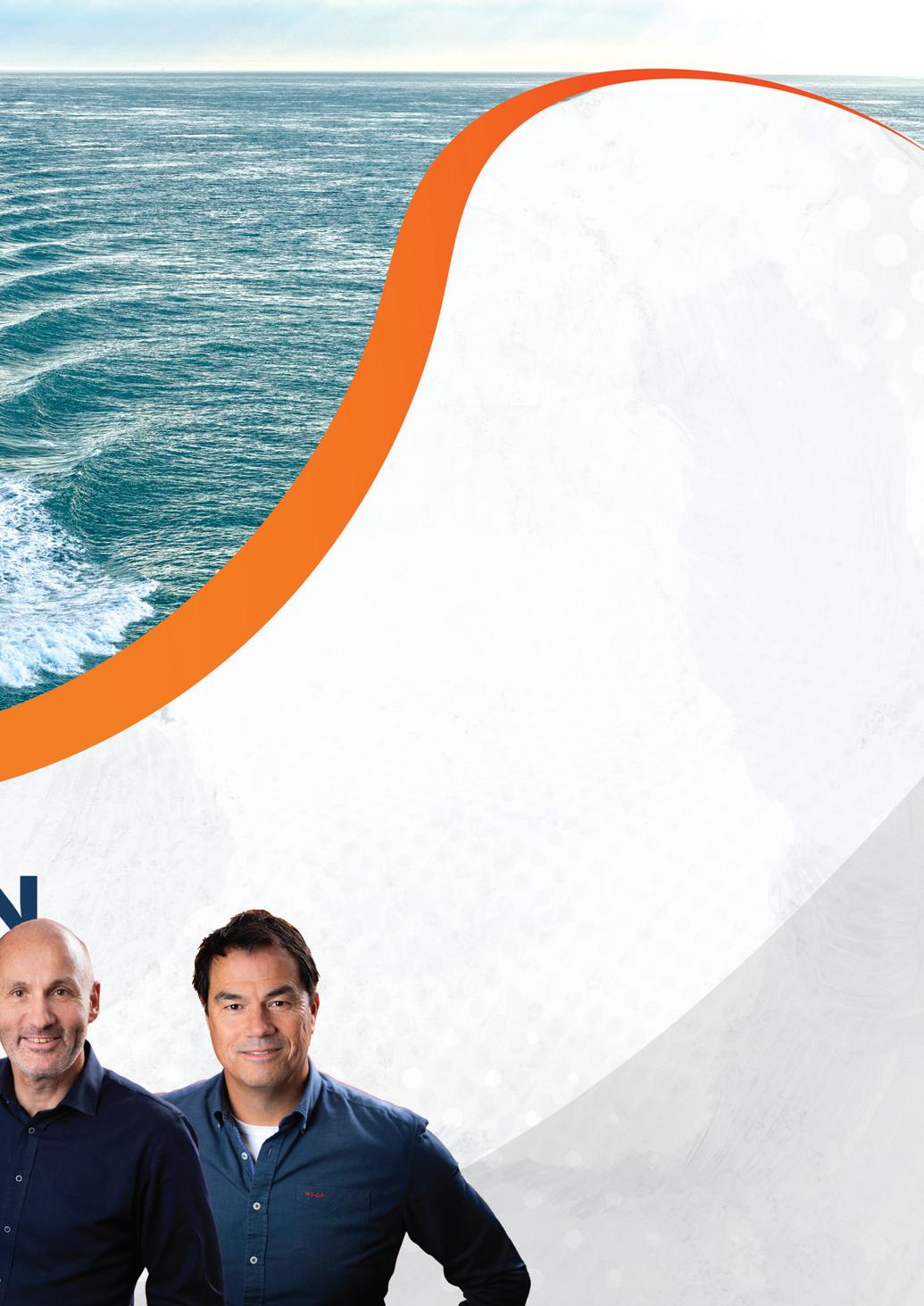
For over 200 years, Royal Bodewes has built vessels that represent innovation and quality, specialising in the design and delivery of general cargo, cement carrier and customised ships. Business Development Managers Martijn Beunk and Gerhard Drenth discussed the company’s sustainable shipbuilding and tailored service. Report by Antonia Cole.
Despite global and industry challenges, Royal Bodewes has continued to grow, Business Development Manager Martijn Beunk said: “We expanded our facilities, renewing building halls and optimising production lines. Now, we own a nearby shipyard with our partners Passer ISDC and also rent another neighbouring yard. With these improvements, we can build nine ships a year.”
Founded in 1812, the company began as a manufacturer of wooden barges and coastal sailing vessels. Over the years, Royal Bodewes has developed alongside technological and industry advancements to become a leader of innovation. In 2016, it already built a hybrid multi-purpose vessel sailing on biofuels for Meriaura. Thereafter, in 2017, Royal Bodewes built an LNG Flex bunker tanker. In 2021, the company produced the world's first newbuild hybrid battery powered self-discharger, MV Aasfjell. This demonstrated Royal Bodewes’ ability to turn ideas into high-quality vessels.

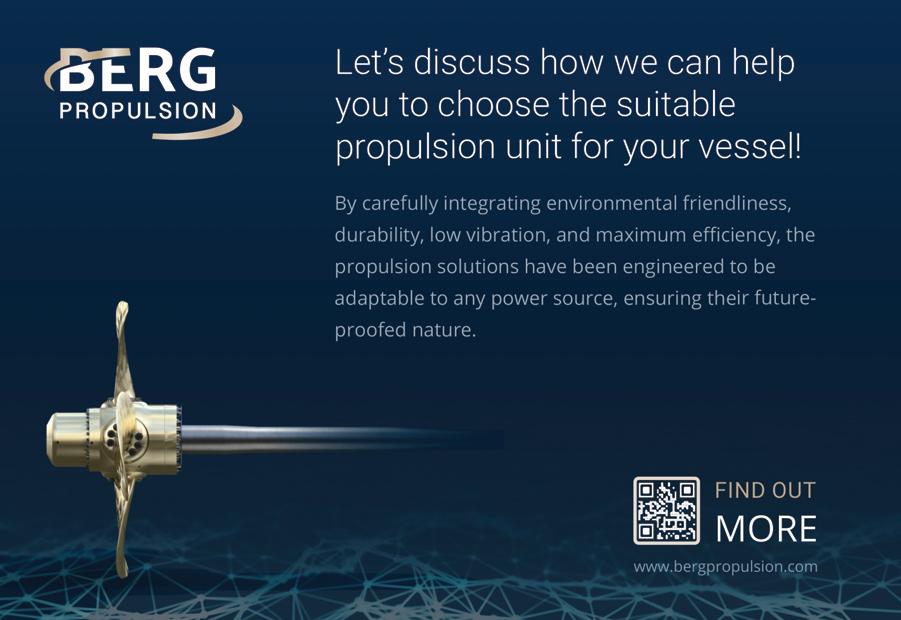
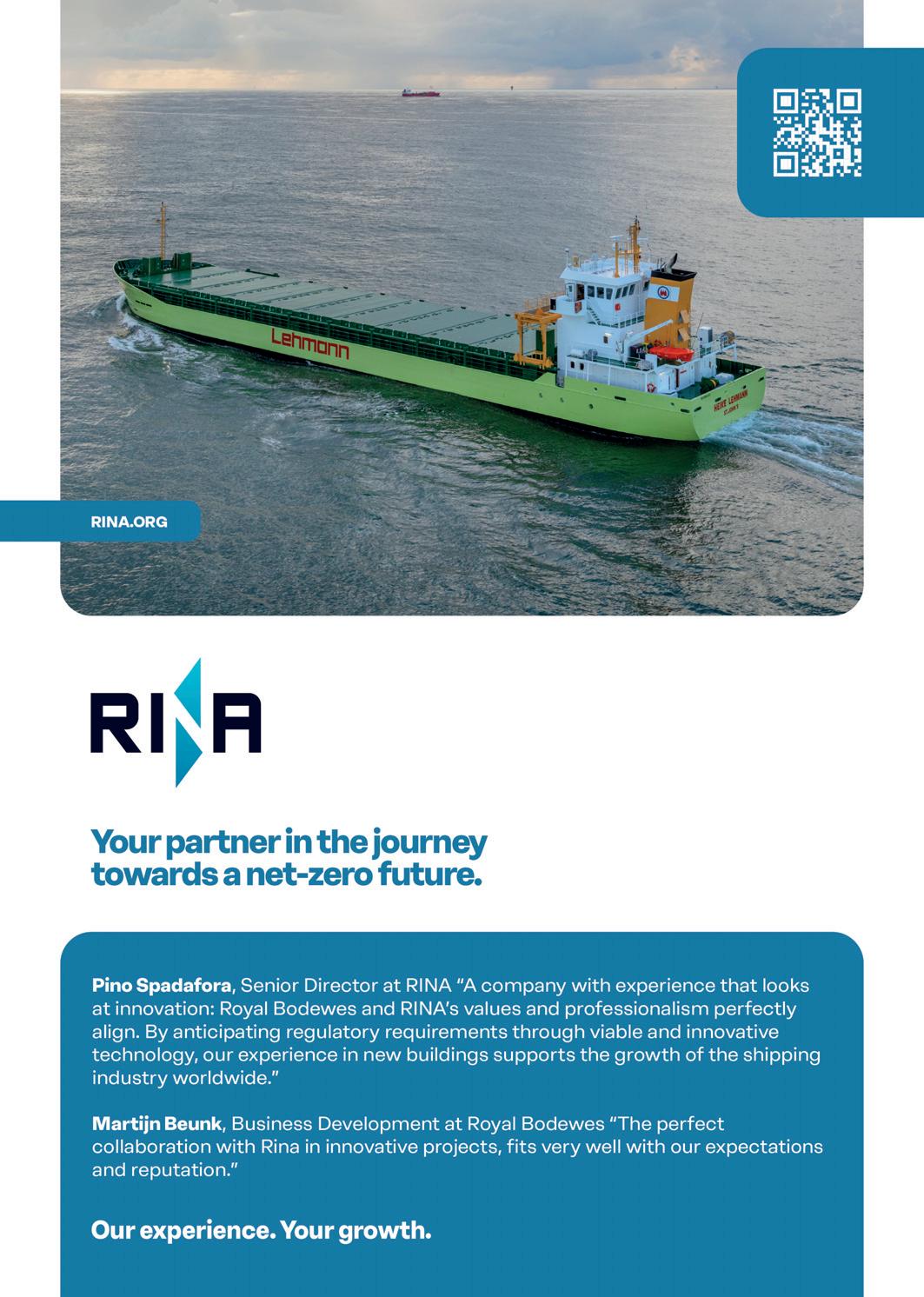
Working in close collaboration with clients, the company builds efficient and economical ships, suited to individual specifications. An in-house design and engineering team firstly creates detailed plans for the vessel with an accompanying 3D model. Then, through Royal Bodewes’ in-house shipbuilding process, prefabrication, logistics, assembling and painting of the vessel are completed.
Once the ship is launched, outfitting, carpentry and paint works are carried out to finalise the vessel. Sea trials become the final stage of production before the vessel is delivered to the customer, ensuring the ship is fully technically approved.
Endless possibilities
Based in the Netherlands, Royal Bodewes builds all ships locally. This not only reduces the company’s carbon footprint, but also supports the local economy and makes sure operations are carried out to a high standard.
“Not many companies are able to build everything within the Netherlands like we do,” explained Business Development Manager Gerhard Drenth. “It’s a real

suc cess story for us and shows our reputation for efficient and effective services. Many people look to Asia for shipbuilding, but we have people from across the globe looking to us.”
The company has delivered a vessel to Taiwan for shipowner U-Ming Marine Transport Corporation. The 115m long cement carrier was Royal Bodewes’ first order from Asia. Additionally, a new RoRo cargo vessel is under construction for a Polynesian shipping company, expanding Royal Bodewes’ global reach.
Companies look to Royal Bodewes to build their ships due to its high standards of quality and comprehensive service. With every order, the company strives to develop projects that exceed customer expectations.
“When a shipowner comes to us, they have a transportation need that they have to fulfil,” added Mr Drenth. “What we do is communicate with them to fully understand their requirements and then look for a solution. We offer a full turnkey service, meaning we can optimise every aspect of the ship to fit client specifications.”
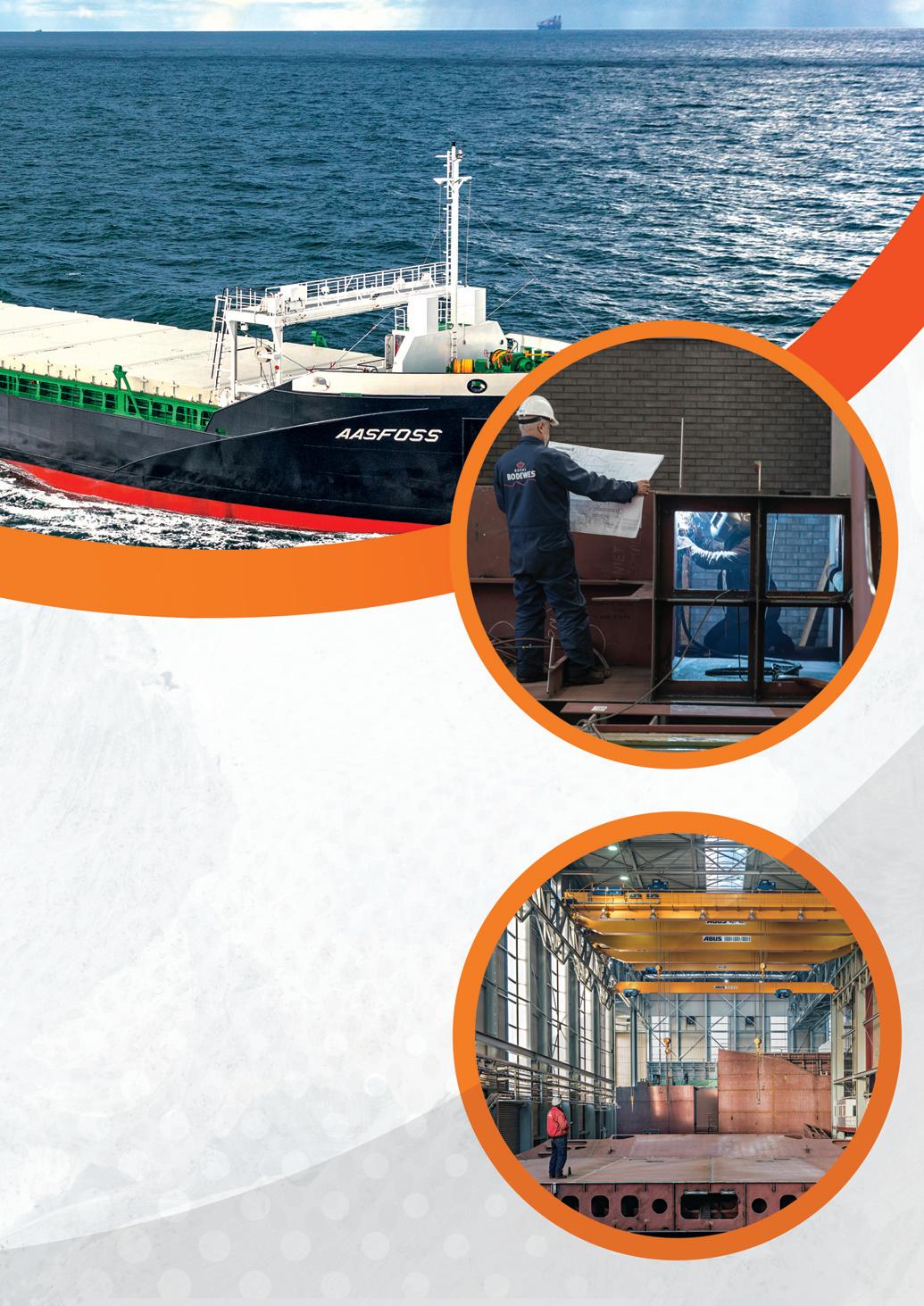
The company’s Arklow Resolve recently won Netherlands Maritime Technology’s ship of the month, attesting to Royal Bodewes’ impressive capabilities. The ship is very efficient due to its innovative design. It is based upon the 5,000 tonne series but is a lengthened version. This means that it can hold 20% more cargo with the same engine, minimising fuel usage and emissions.
Greener and cleaner
Royal Bodewes is focused on integrating sustainability into shipbuilding, promoting a more environmentally friendly industry. The company has already built five ships with a fully battery powered hybrid system and has orders for seven more.
“There’s a lot of technical knowledge that has gone into the designs of these ships,” commented Mr Beunk. “We have put in a lot of work to see these ships become a finished product and the result
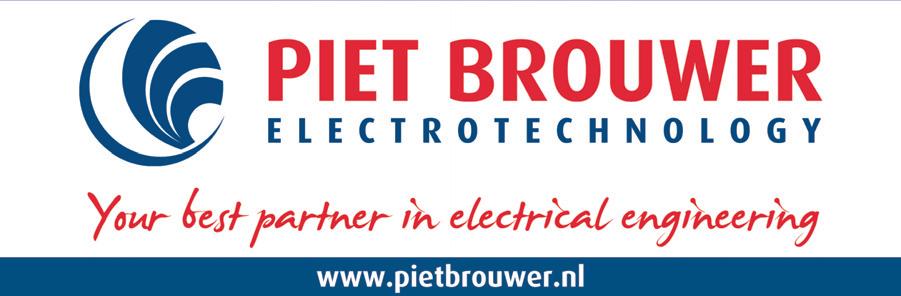

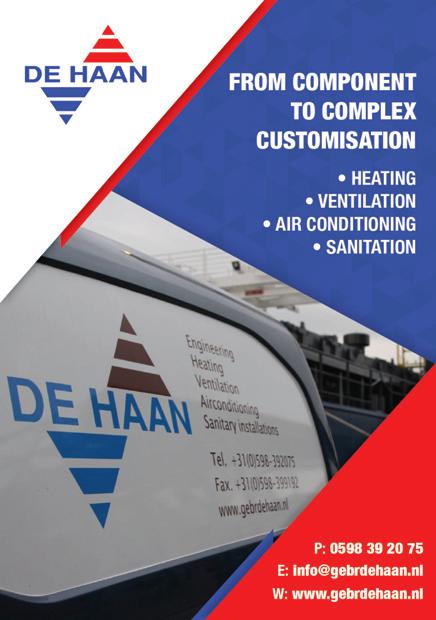
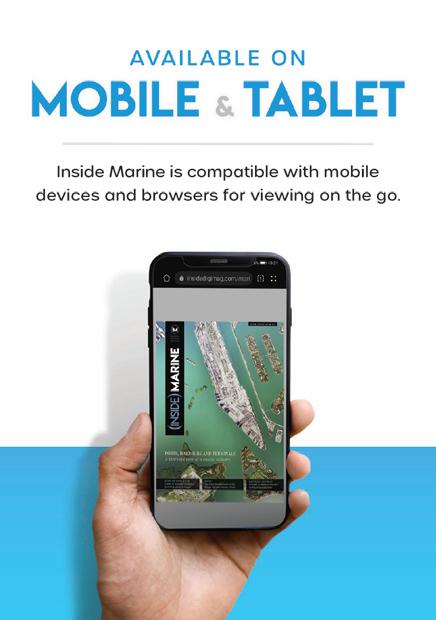
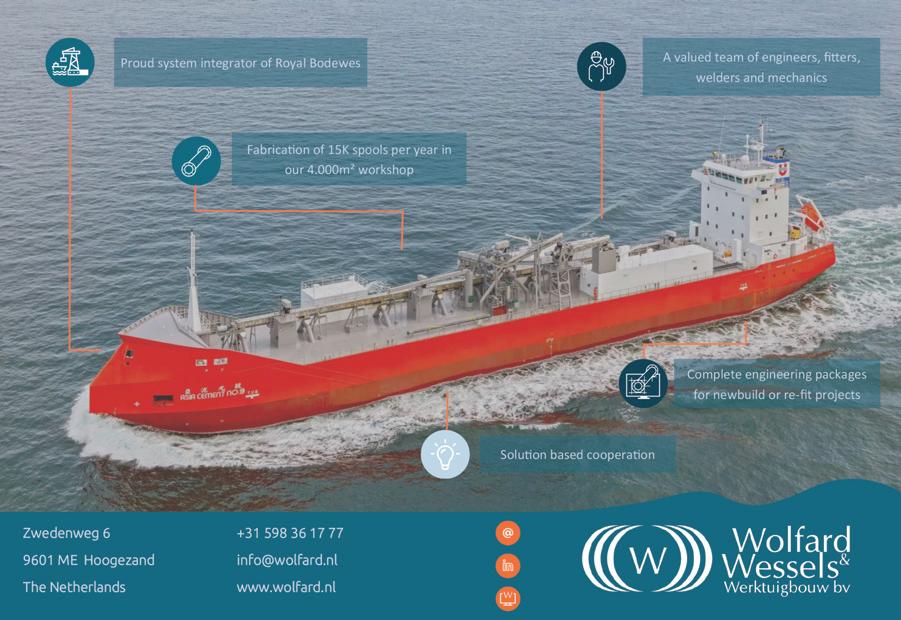
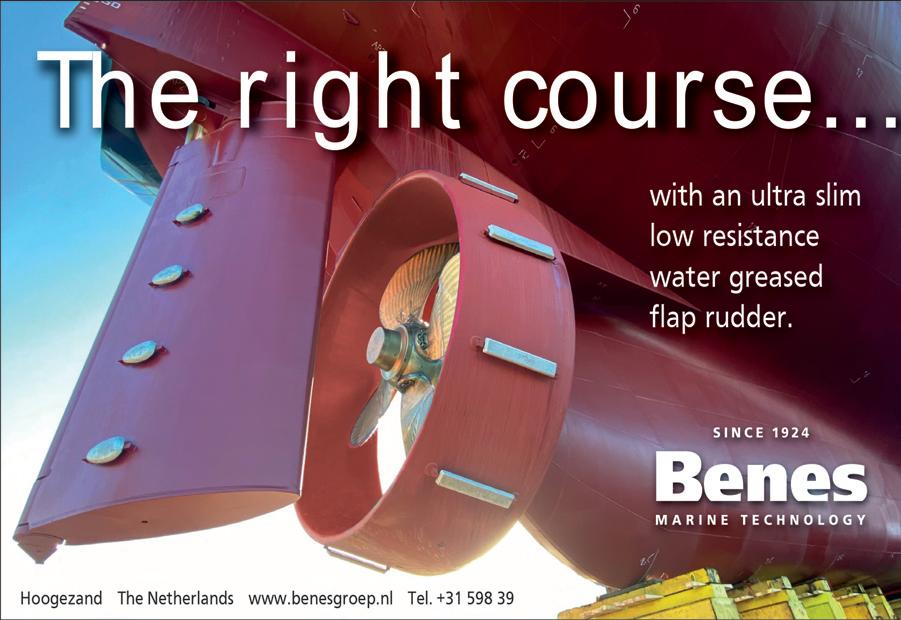
is very special. Our hybrid ships are exceptionally efficient and are created with the future in mind.”
The Hagland, RB 5,000 series are hybrid cargo vessels equipped with a battery package and an excavator on top for self-loading and discharging. This creates a process that emits zero emissions in port operations, as well as using less fuel during journeys.
Hagland Shipping has recently ordered four more of these vessels. The bulk carriers will have the same sustainable design, but will include additional features that further reduce emissions. Royal Bodewes is creating ships that optimise fuel-use and preserve the environment, preparing ship owners for evolving sustainability regulations into the future.
“Protecting the environment is a vital part of our daily operations,” continued Mr Beunk. “We are always looking for ways to make ships greener and cleaner. From a shipyard perspective, we are also optimising our energy-use in operations. We have installed solar panels at the
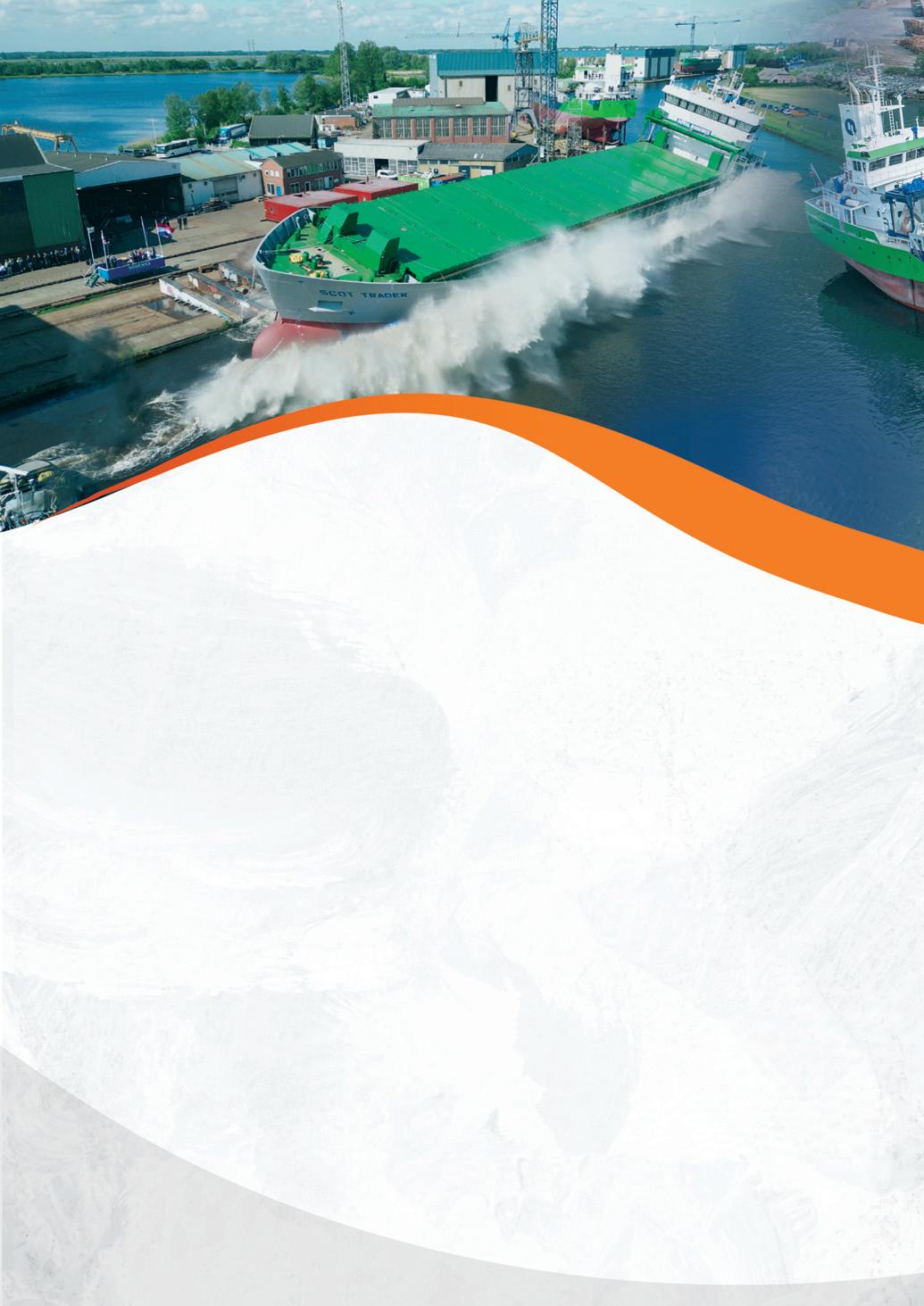
shipyard to generate our own renewable energy and mitigate our impact on the environment.”
Royal Bodewes plans to continue improving the facilities at its site to make them more sustainable. Additionally, the company is investing in people through active engagement within communities.
Later this year, Royal Bodewes will hold an open day to engage and educate the public on the shipbuilding industry.
“It’s important that we get young people involved and excited about the sector,” said Mr Drenth. “We are focused on the future and it’s in their hands. By going to schools and holding events, we hope to get young people enthusiastic about technical jobs like shipbuilding.”
Family values
As a family company in its seventh gener ation, Royal Bodewes has maintained many relationships over 200 years of operations. Around 90% of the company’s customers are also family
companies, aligning their values with that of Royal Bodewes and facilitating healthy working partnerships.
“We always try to establish long-term relationships with our partners and suppliers,” explained Mr Beunk. “By creating a sense of trust and reliability, we can serve our clients more effectively. Through collaboration and the sharing of knowledge, we have been able to develop innovative shipbuilding solutions. There is so much to learn from our partners, and we try to take advantage of this.”
The company has built up strong relationships with many suppliers, including Piet Brouwer Elektrotechniek which is working on several vessels with Royal Bodewes currently. To create high-quality vessels, Royal Bodewes
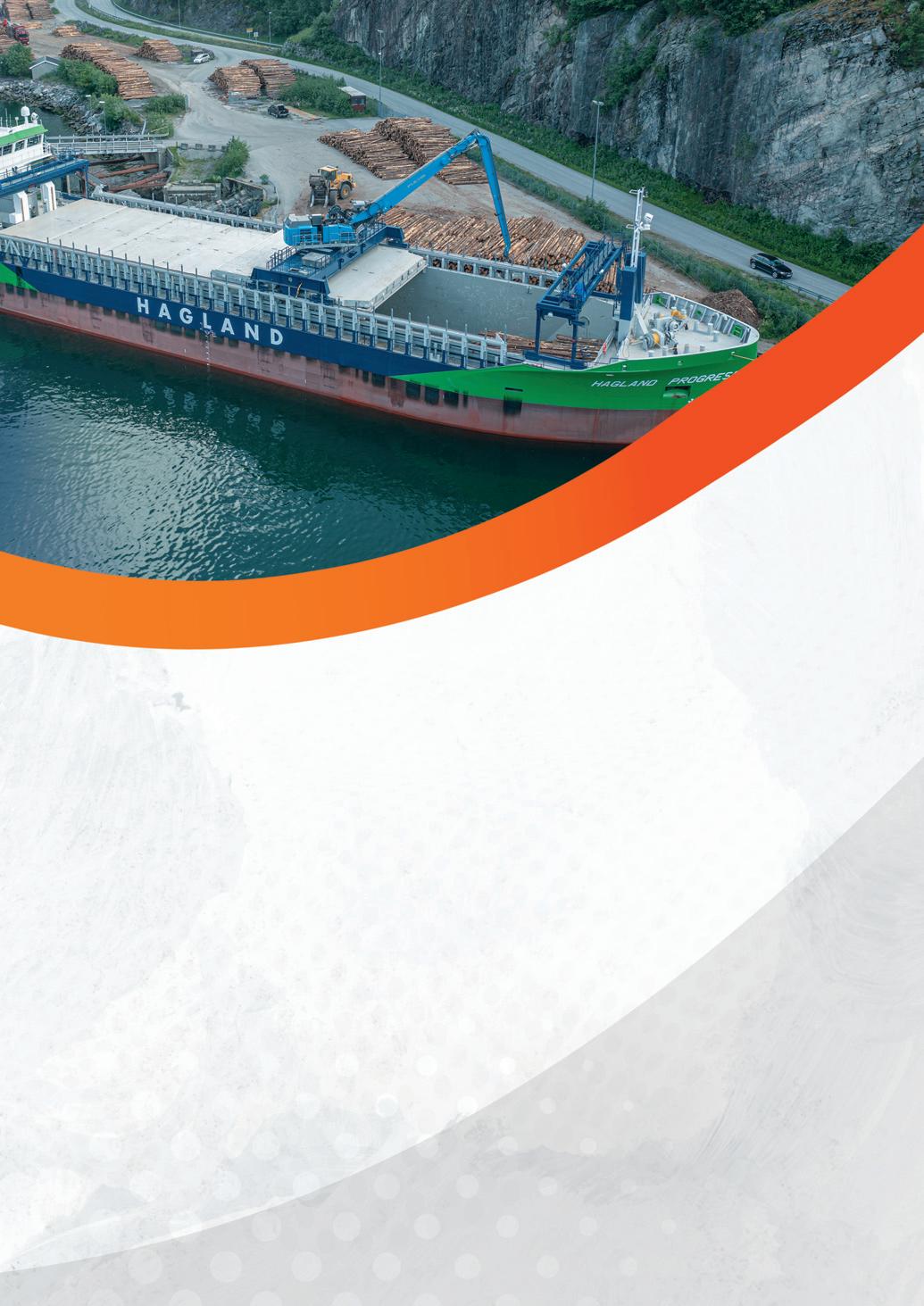
utilises the skills of companies like Wolfard & Wessels and Marine Service Holding, which develop ship engine rooms. ABC Engines, Wärtsilä, MAN and Berg Propulsion are also key suppliers that facilitate the execution of effective shipbuilding.
“Everyone is very enthusiastic here and we all work well together,” continued Mr Beunk. “Our market is very demanding, but having a good team eases the challenges.”
Royal Bodewes hosts a great, collaborative environment, Mr Drenth added, in conclusion: “We know that we need each other’s skills and expertise to be successful. I can’t build a ship on my own. All of our individual talents combine to create a successful operation .” n
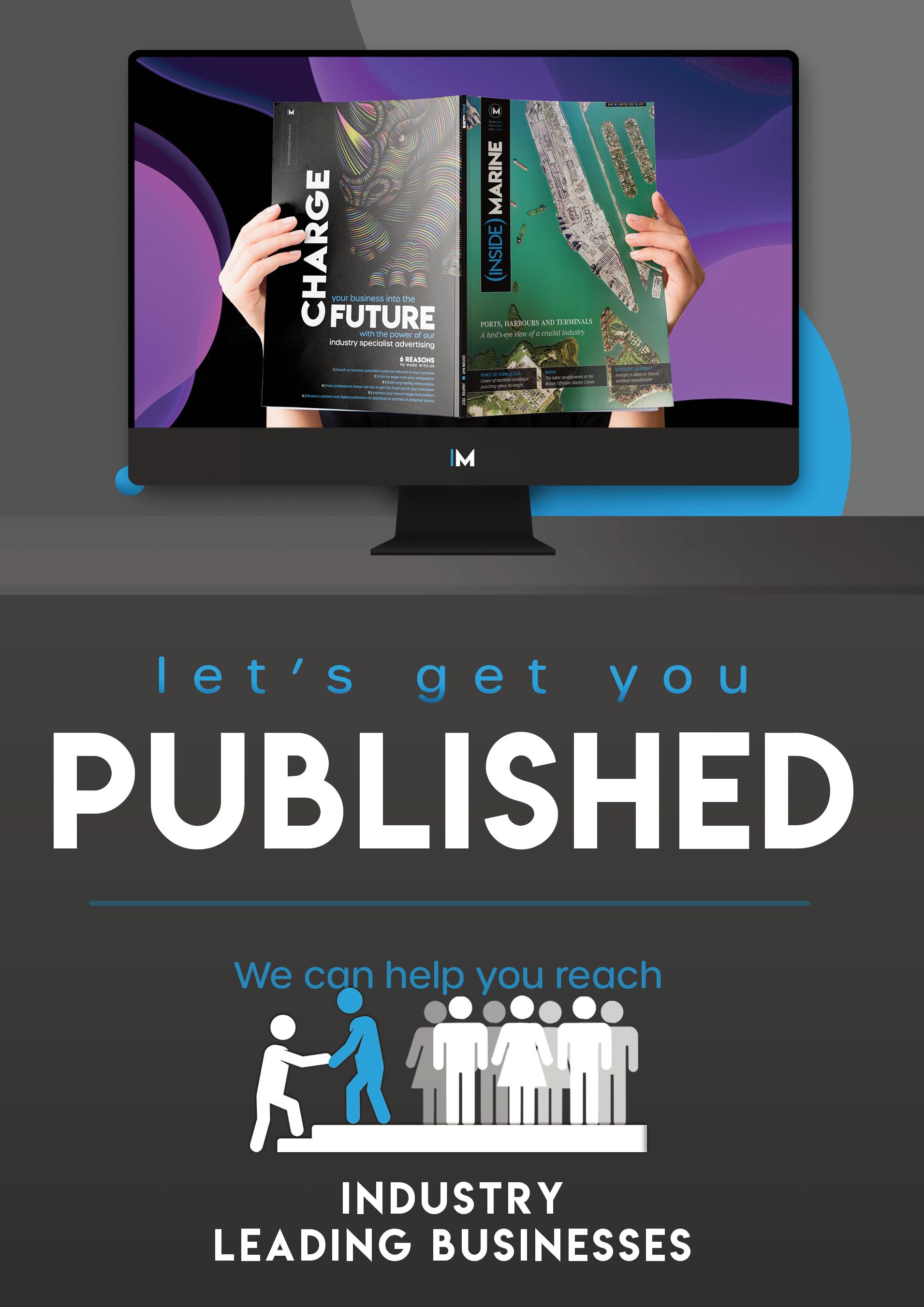