SEAMAR MANAGEMENT MANAGEMENT OF THE HIGH SEAS

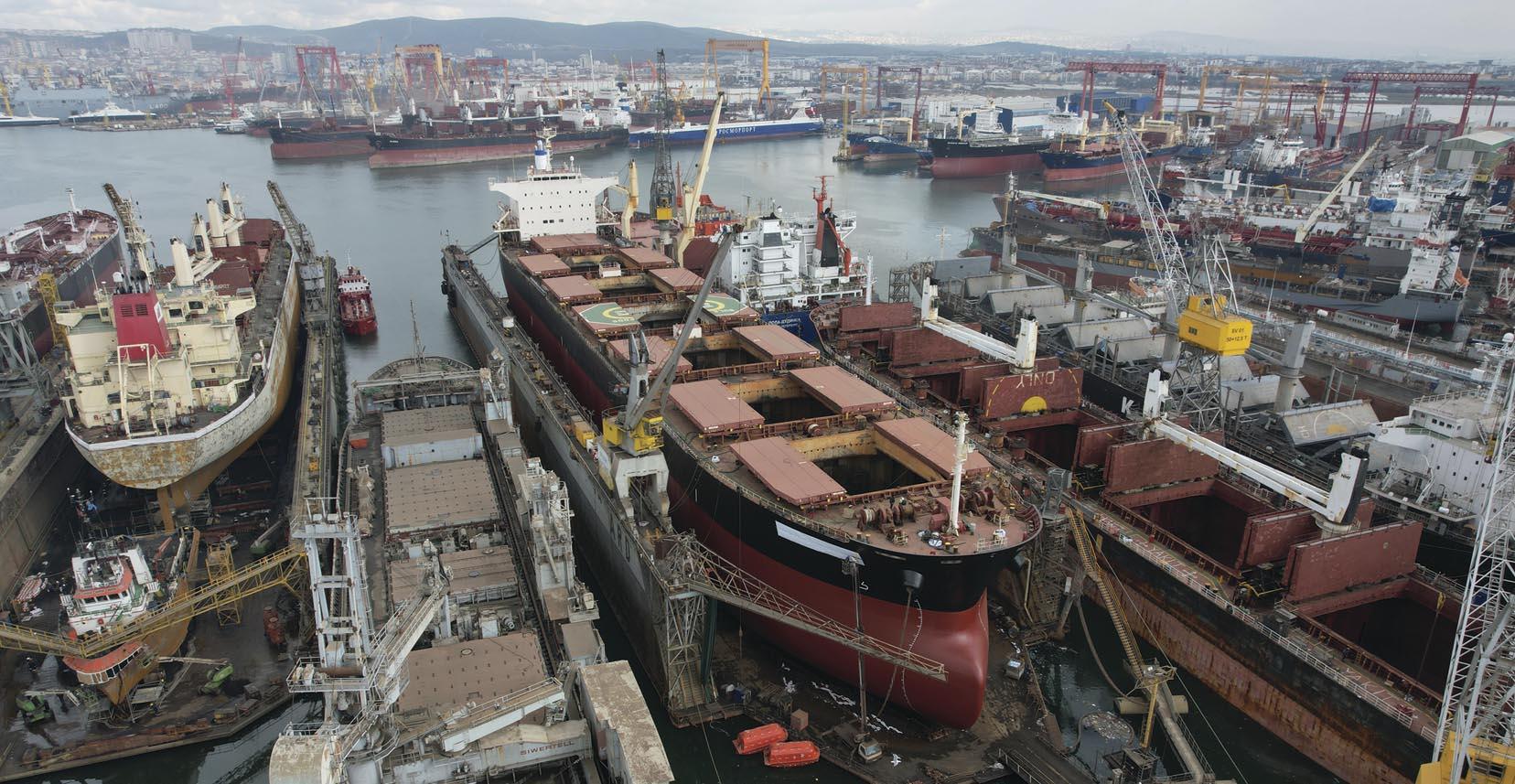
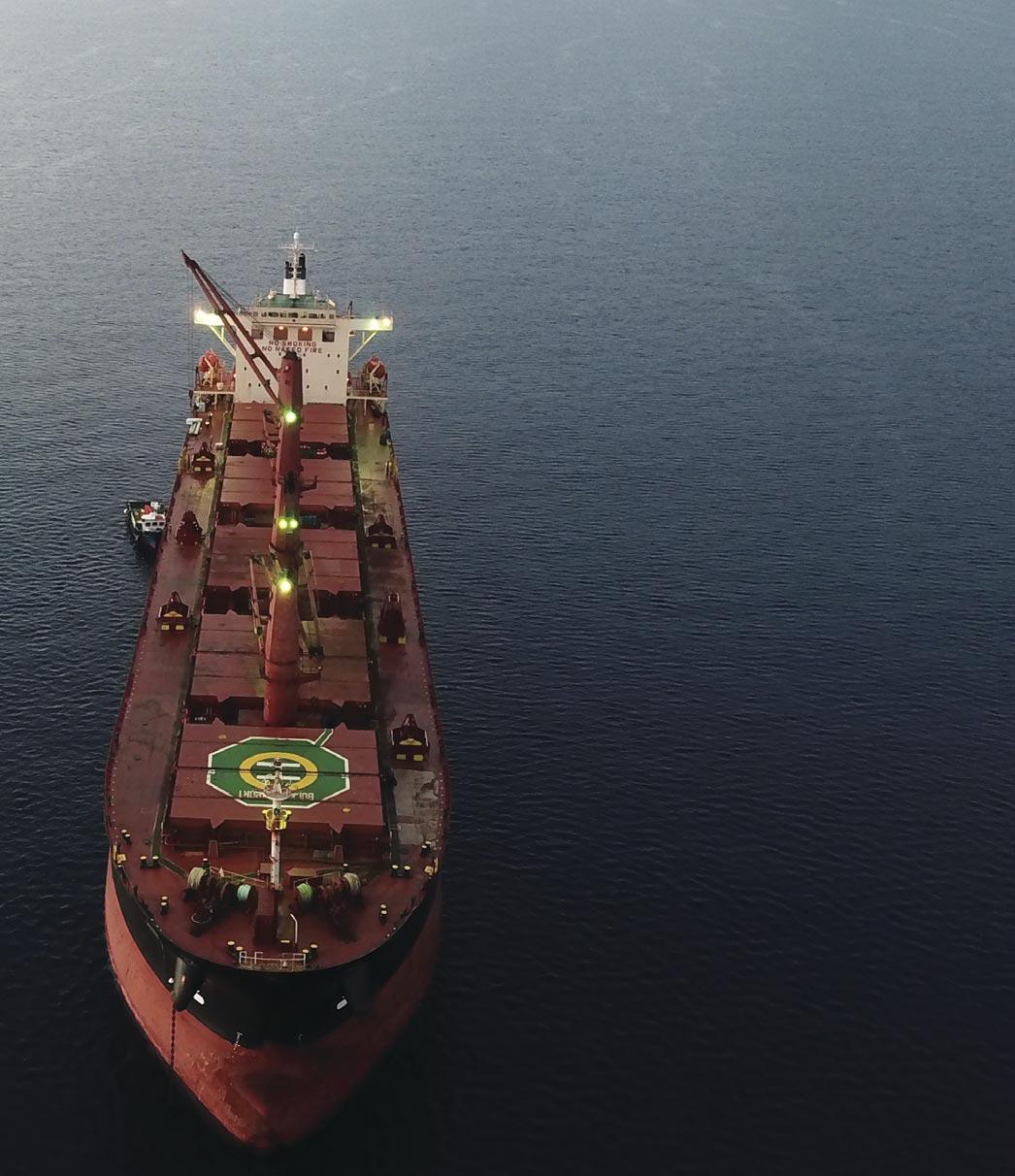


Hailing from Greece, the tight-knit team of highly skilled specialists at Seamar Management offers its clients an extremely efficient, lean and professional technical management service. In addition to its ongoing efforts to perfect its service offering, the company is collaborating on a groundbreaking ocean research project whilst also mastering ice navigation. General Manager Lydia Doussopoulos revealed the company’s strategy for successfully juggling all of these areas of expertise to Richard Hagan.
E stablished as recently as 2007, as part of a successful and strong group of companies, Pangaea Logistics Solutions, Seamar Management has emerged as a technical manage ment powerhouse with a string of impressive accolades to its name, with a particular highlight of those occurring in 2013.
Seamar Management was the first technical management company to have a commercial bulk carrier transit the north west passage, with the commercial management under Nordic Bulk Carriers.
“We took the first commercial bulk carrier through a very challenging route,” General Manager Lydia Doussopoulos revealed. “We developed the knowledge for transiting the Arctic in-house over a period of time. They’re very challenging waters to navigate. It’s extremely remote so you have to be 100% pre pared because you’re really on your own. The crew need to be very experienced – they need to know ice navigation and be able to maintain proper communications with the ice breakers. It also requires lots of preparation from the company in terms of spare parts and supplies.”
Ms Doussopoulos highlighted the company’s highly efficient staffing structure: “We manage 15 bulk carriers and we employ 32 people in our Athens office, so it’s about 2.1 people per vesse l. We believe that’s quite an efficient arrangement.”
This lean staff complement is an important part of the company’s boutique service offering for which it is famous.
“There’s a lot of competition in our niche, especially from the big-name third-party technical management companies that are increasingly entering this market,” she explained. “However, we’re not interested in high-volume activities; rather, our focus is on high-quality service. Every owner is unique in terms of what they require; their trade is special, and they want a very focused level of service. That’s what we provide.”
Seamar Management’s technical management services are specifically tailored to each of its ship owners’ particular needs. It achieves this through the company’s unique, well-oiled mix of personnel across its various departments which include crewing, technical, and purchasing.
“Our teams all have different specialisations,” Ms Doussopoulos confirmed. “But the big thing is how you bring them together to provide the service levels that the owner needs. We’re in a very difficult trade, so it requires focus and great collaboration between the teams.”
Seamar Management forms part of the NASDAQ-listed Pangaea Logistics Solutions, which provides shipping and logistics ser vices to a broad spectrum of mainly industrial clients. For its part, Seamar Management provides the technical management solutions portfolio within the group.
One area in which the company has developed particularly strong expertise is in the management of vessels of diverse ages and resolving all of the challenges inherent to that.
“We’re very knowledgeable in terms of dealing with secondhand vessels that require good programming when purchasing from another owner, in order to bring the vessel up to your com pany’s standards,” Ms Doussopoulos proudly noted. “We have some younger units and some older. We’ve taken on vessels up to 30 years old, with others as old as 25 or 15 years old, all dependent on the owner’s needs.”
While acknowledging the drawback of older vessels requiring greater maintenance efforts, she emphasised the company still relentlessly pursues modernisation efforts across its fleets.
“One of our strategies for staying ahead of the competition is to ensure that we’re constantly modernising our fleet. We’ve been doing that with all of our second-hand vessels in the last few years, replacing older ones with new, more efficient vessels.”
At Seamar Management, sustainability is not just a buzzword that gets tossed around at the office. Instead, it’s a major theme within its operations and a real commitment that the company is working hard on every day.
“We’re constantly looking at ways to improve our operations and better manage the emissions and efficiency of our fleet,” said Ms Doussopoulos. “One example is through the use of biofuel, which we expect might further help us to reduce our carbon emissions and to become more efficient. We’ve already implemented it on one vessel in which everything went very smoothly, and it’s made us optimistic about the future of that technology.”
Carbon capture technology is also firmly in the company’s crosshairs, according to Ms Doussopoulos: “We really believe in it, we think it has great potential for the future,” she noted.
“We believe in advanced technology and software and in how it can improve and optimise our voyages and our operations,” she added. “We’re already using software that is helping us to opti mise our passage plans, our voyages and our operations. We’re able to measure the improvements the new plan offers versus what the normal passage plan would be. That suggested route is submitted to the ship’s master and if he agrees to it, we’ve successfully saved that fuel and those emissions.”
Meanwhile, the company is reviewing the implementation of energy-saving devices across its fleet – even on its older vessels resulting in substantial energy savings. It’s also upgrading the governor software wherever possible in its ships for improved efficiency, and additional energy-savings devices and technologies, beyond what has already been installed, are
being reviewed. This includes super-efficient hull coatings and other measures.
In furtherance of its commitment to the environment, Seamar Management is engaged in a groundbreaking research collabo ration with the US-based Woods Hole Oceanographic Institute in Cape Cod. The company’s ships are engaged in a programme of being fitted with sensors and an acoustic doppler to evaluate data from the regular routes that its ships run. The data gath ered by these sensors have proved especially useful for groundbreaking weather research.
“Our collaboration with Woods Hole is a project that we’re very proud of and will continue with, including in other areas,” Ms Doussopoulos confirmed.
Outside of emissions regulations and efficiency improvement efforts, Seamar Management is using technology in an additional, altogether far more surprising way: to 3D print spare parts.
“We’ve partnered with a company that specialises in industrial 3D printing,” Ms Doussopoulos revealed. “We believe this tech nology is going to be a big game-changer in the future, especially given the difficulties we’re now facing with regards to parts avail ability and unreasonable shipping costs.”
As per most businesses worldwide, the company is confronted with the same post-Covid supply chain chaos. Ms Doussopoulos provided some insight into how her teams are coping:
“The current supply chain environment is our biggest chal lenge right now. We’re adapting our processes to address those issues and we’re ready to change wherever required.
“One area we are working on is to be better prepared in terms of spares because that area is very tough at the moment. For example, if you need a major spare part for your crane, you might be waiting for five to six months depending on your loca tion, and that was never the case in the past. It’s become more difficult for all of us but we’ve tried to be flexible to change and to be as adaptable as possible.”
That flexibility is important in the fast-moving shipping industry. “We always try to stay ahead, and we’re constantly conducting research,” she emphasised. “We like to ensure that we’re jumping into any new initiatives we find that we think can deliver value to our clients. Altogether, it’s kept us open-minded, which is important in our industry.”
In closing, Ms Doussopoulos reaffirmed her trust in her handpicked team of specialists.
“I’m proud of my team. It’s been a truly big effort to build up this team of amazing individuals, who appreciate the values and mission of the company, and who are consistent in supporting it by going above and beyond on a daily basis, carrying out the diffi cult tasks that we’re doing every day. They’re like family; I really enjoy working with them. It makes me eager to come in to work every morning. Their efforts every day separate us from the com petition and ensure that our results speak for themselves.” n