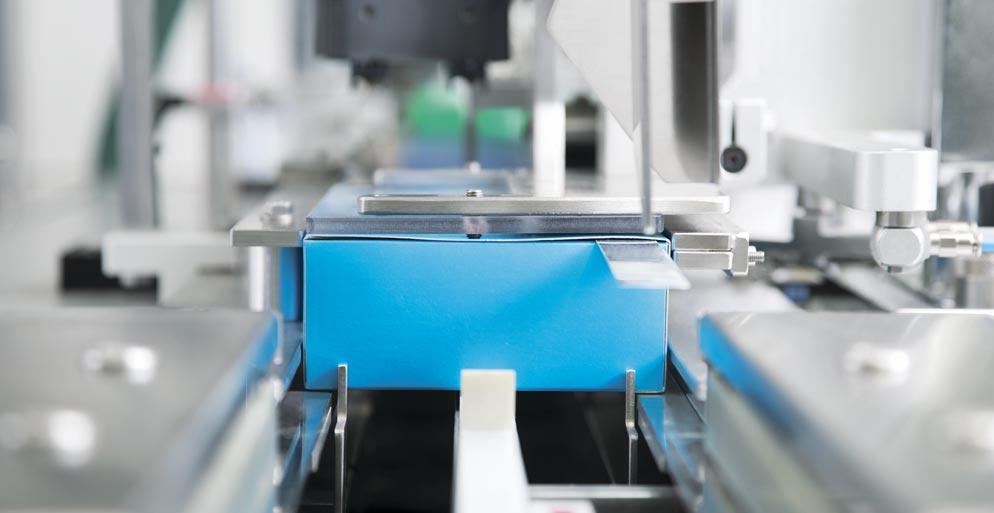


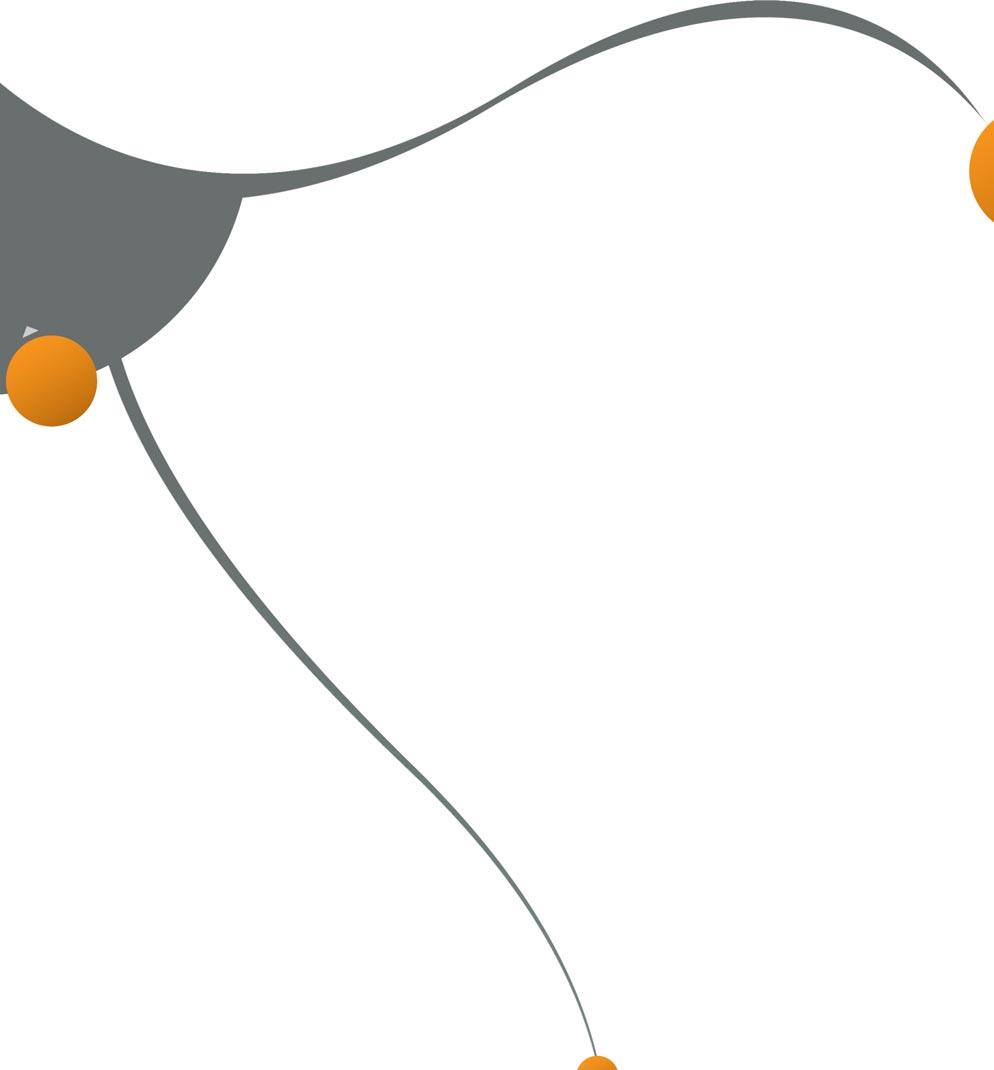
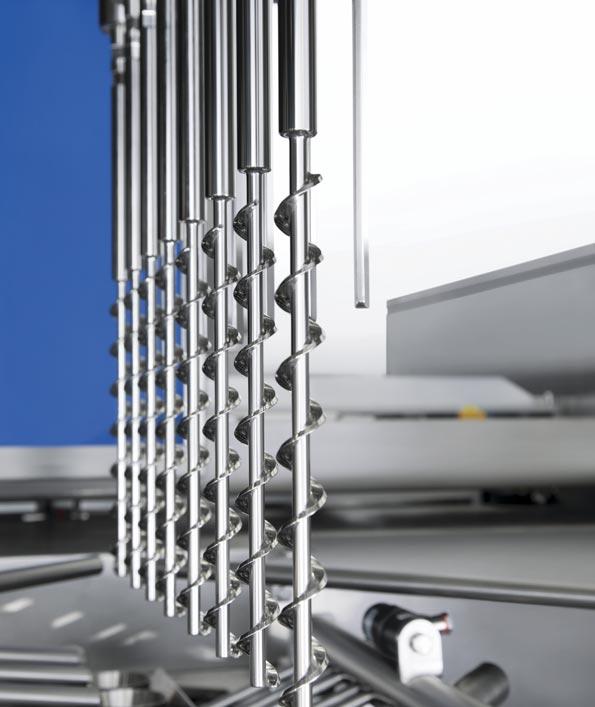

Universal Pack is a maestro of machinery – having dedicated the last 59 years to designing and manufacturing the very best 4-side seal sachet and 3-side seal stick pack packaging machines. Now, as the industry continues to demand increasingly greener, cleaner solutions, Universal Pack is turning its hand to sustainable development. Project & Sales Manager for Pharmaceutical Packaging Federico Fabbri discussed exactly how the company is achieving this, during an in-depth interview with Inside Sustainability. Report by Imogen Ward
Innovation has always been a key element in the decision-making process of Italian packaging machine expert Universal Pack. Now, the company is taking that crucial ingredient and applying it to a more sustainable way of packaging.
“Universal Pack was founded in 1965 by Gino Donati with the intention of revolutionising the packaging industry,” said Project & Sales Manager for Pharmaceutical Packaging Federico Fabbri. “That’s why innovation has always been at the forefront of our company. And from the very begin-
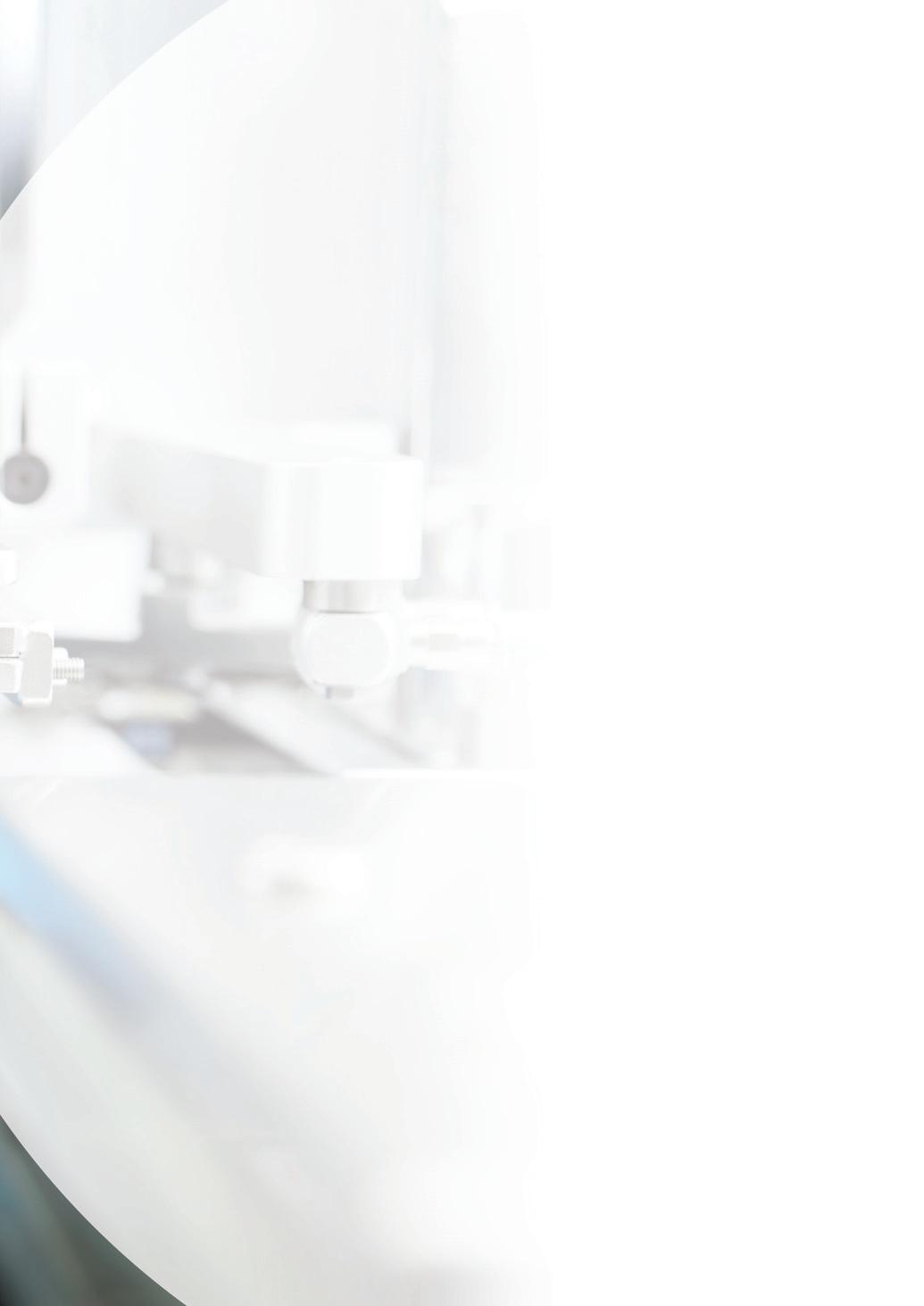
ning, Mr Donati has adopted sustainability into the very biology of the company, so a transition to greener methods made sense.”
Over the years, Universal Pack has established itself as a global leader in packaging machinery. Having developed a reputation for products that are precise, efficient, reliable and mechanically durable, the company has now focused its efforts on the global transition to a greener way of thinking.
“Nowadays, we all understand the critical role that sustainability plays in everyone’s operations,” Explained Mr Fabbri. “For that

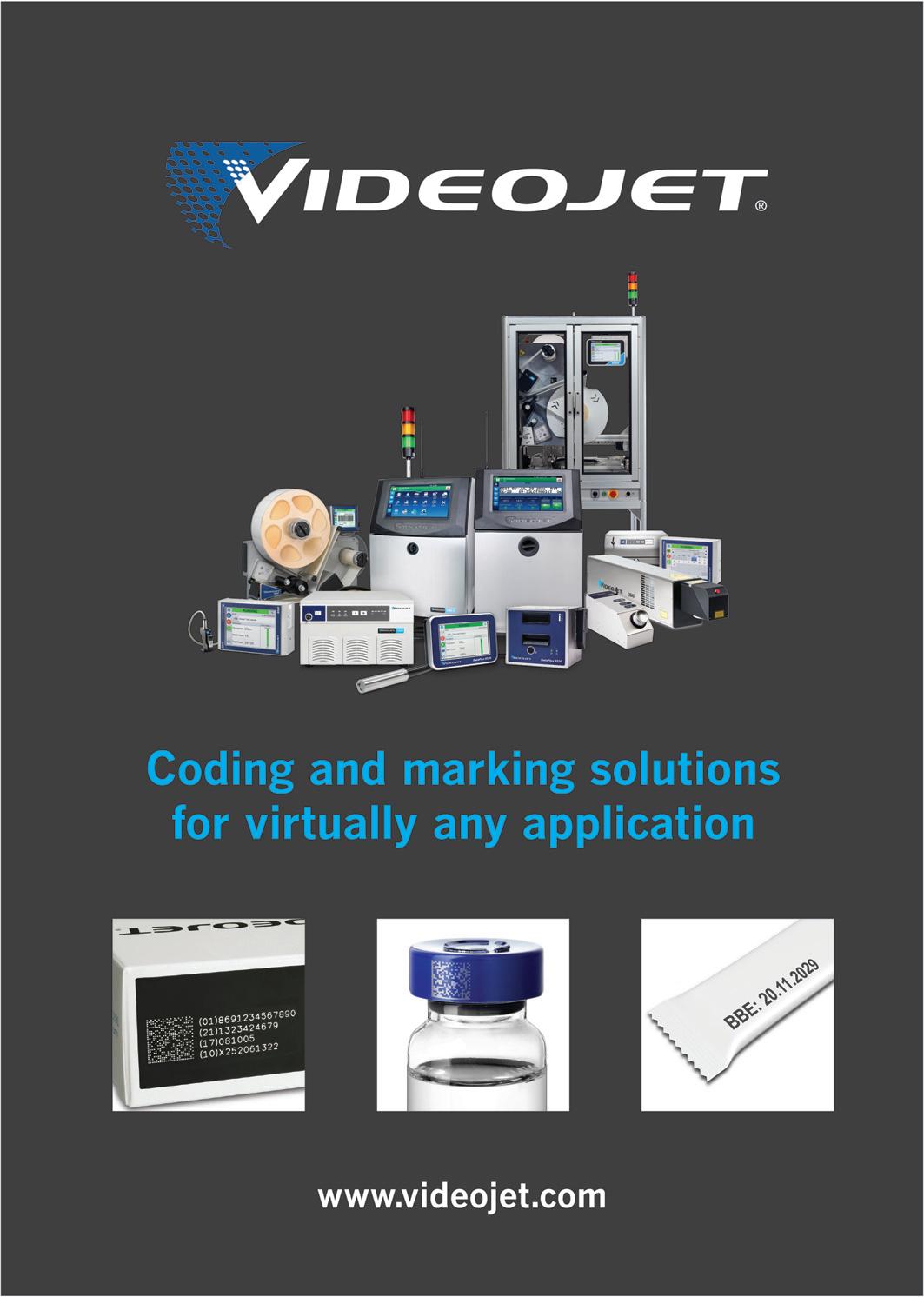
reason, we have dedicated the last few years to improving our sustainable activities. This process was also inspired by the demands of our customers.”
Sustainable development
With research and development in abundance, Universal Pack established its in-house laboratory to support product investments with scientific research and analysis. Most recently, the laboratory has been tasked with a collaborative project that involved major suppliers from the pharmaceutical sector.
“We helped them develop some eco-friendly packaging solutions that
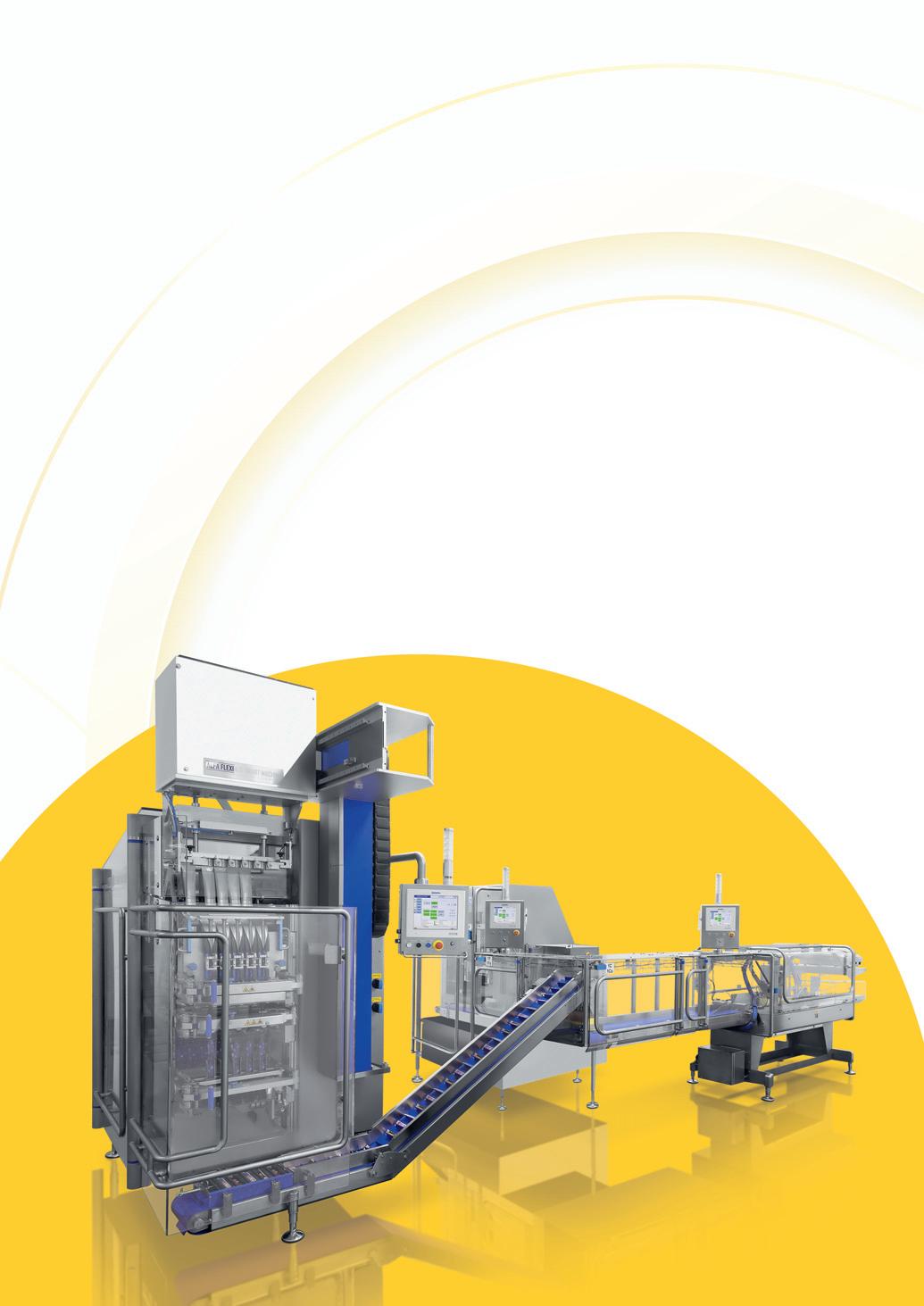
were recycle-ready, compostable and compatible with our machines,” said Mr Fabbri. “This was very challenging because it required us to innovate at every stage, from the design of the machine to the most sophisticated units and controlling systems.”
As a result of the laboratory’s extensive research and analysis, Universal Pack was able to co-develop compostable and recyclable films that retained a strong protection barrier – creating the perfect protection for its customers’ products.
“Ensuring that the film retained its compatibility (whilst also providing a very high barrier for the products inside)
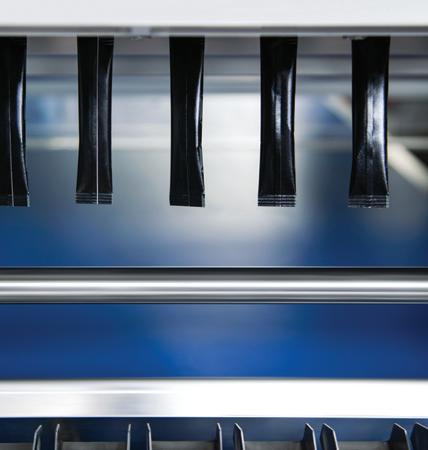
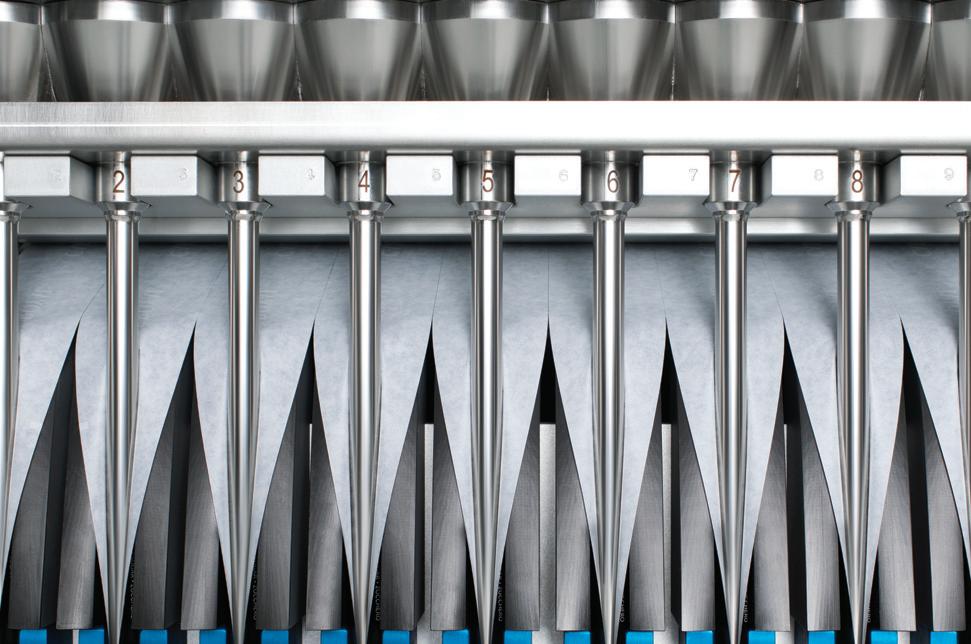
required a lot of forward-thinking,” revealed Mr Fabbri. “We researched alongside our major film suppliers to decipher the right composition that would be compatible with our machines and adapted them accordingly.
“Since then, we have tested these films with our suppliers and customers, and the results have been very satisfactory, especially when it comes to maintaining a product’s shelf-life and protecting it from damage.”
Following the successful development of these films, Universal Pack is interested in exploring this area of the market further.
A company that cares
In line with its green projects, Universal Pack has also committed to a waste recovery goal of 95% by 2025.
“We are confident that we are on the right track to achieve our 2025 waste recovery goal,” said Mr Fabbri. “In 2022,
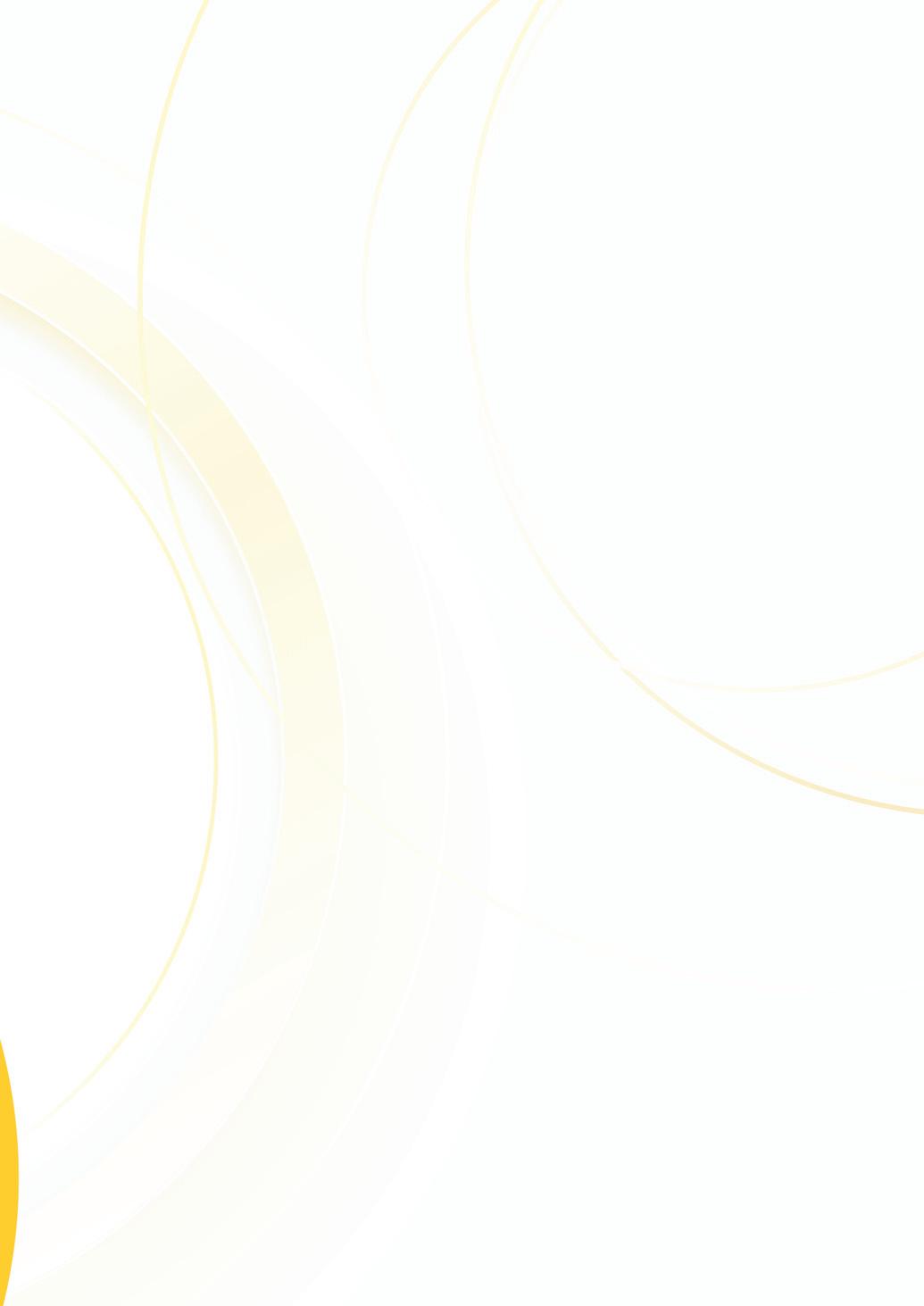
we reached 91.7 per cent, and we are now waiting for the results for last year. In the meantime, we are implementing even more initiatives to minimise this waste, optimising our manufacturing processes and prioritising the use of recoverable materials as well.”
The company has adjusted its manufacturing processes – replacing old machines for new, investing in state-of-the-art preci sion technology, and analysing the market for the latest developments in laminating film.
“We have fine-tuned our components to ensure compatibility with the latest sustainable solutions from the laminating field,” explained Mr Fabbri. “This has helped reduce the carbon footprint and life cycle assessment of our packaging machines.”
During the adaption of its machines, the company had to make sure that the laminates were processed correctly, and that high levels of efficiency and performance
were retained. With an objective in mind, Universal Pack focused on improving the sealing and cutting components of its machines.
“Laminating films are subject to several factors when they are processed, such as heat, pressure and tension,” said Mr Fabbri. “Ensuring the machines are improved and ready to work with these sustainable films is essential, because they are more sensitive than standard films.”
Universal Pack is on a journey of continuous improvement when it comes to its machines – working shoulder-to-shoulder with huge companies to provide the most efficient solutions.
Another recent adaption saw the company improve the energy efficiency of its machines by using energy-saving
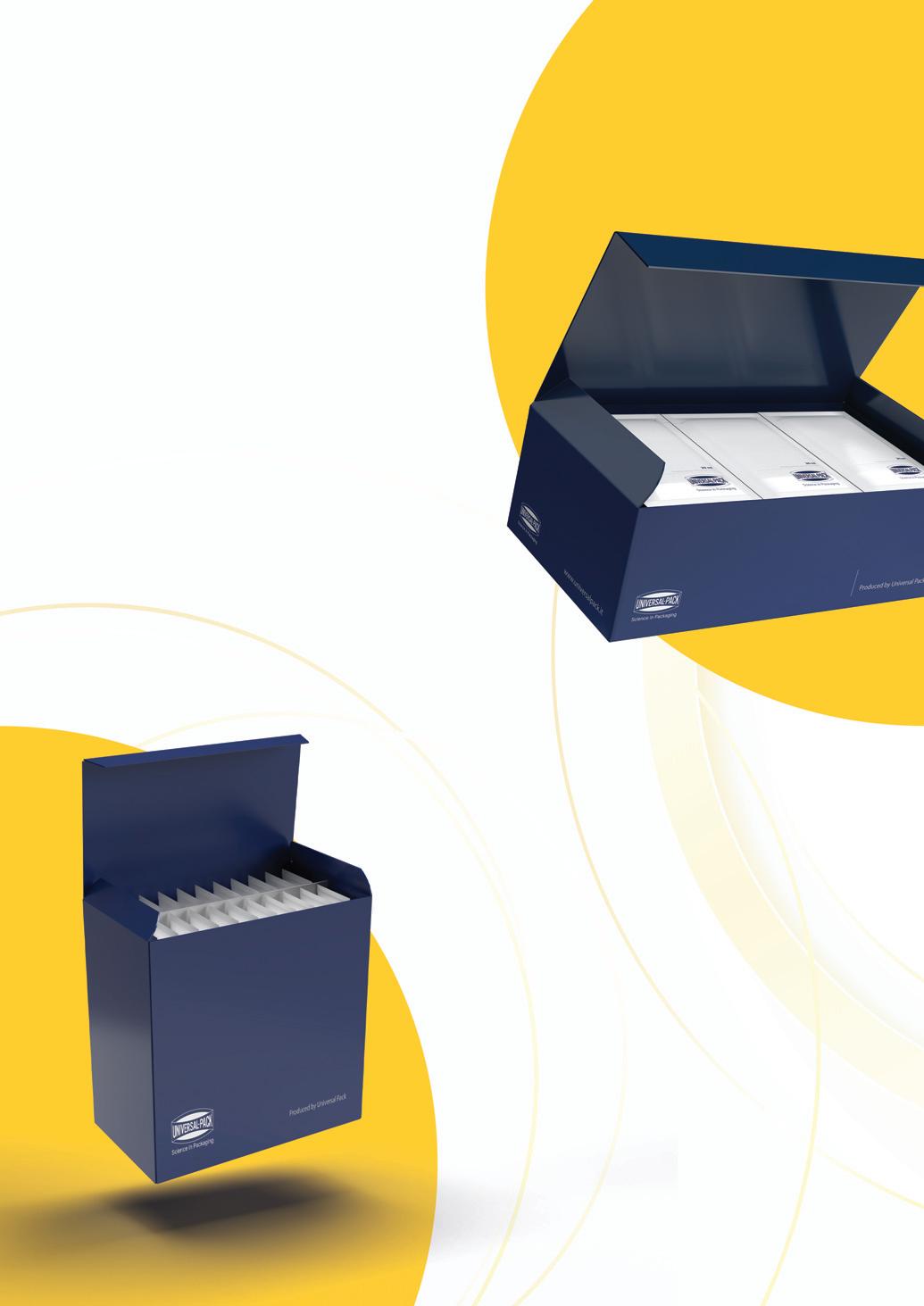
technology. Universal Pack is now installing machine motors that have a lower energy demand. All its machines are also able to operate to very high levels of overall equip ment effectiveness.
With so much innovation and development happening behind the scenes, it is no wonder that Universal Pack is experiencing, on average, an annual turnover increase of 10-15%. In fact, the company has successfully installed more than 8,000 machines across 150 countries, and it has now reached full capacity at its 10,000sqm factory in San Giovanni in Marignano. To solve the issue of space, Universal Pack is now looking to build a brand-new premises.
Building green
The new facility will be designed and built to run as a net zero energy building and will cover all Universal Pack’s current capabilities, while also accounting for any potential future growth.
“In recent years, our business has expanded a lot,” said Mr Fabbri. “And with that growth comes a need to extend our physical presence as well. We don’t have any more space in our current facility, and it isn’t as green as we would like it to be. For these reasons, we plan to build a net zero energy facility, which will feature more advanced technologies, have a higher performance and will run on renewable energy from its own photovoltaic installation.”
Although the estimated size and completion date are still under wraps, Mr Fabbri expects more information to be released soon. Until then, the company will continue to grow and innovate within the world of packaging.
“All our machines are custom built,” said Mr Fabbri, in conclusion. “Each new project is different to the ones that came before, and we never turn down a request. That’s part of what makes us so successful.
“I personally love the flexibility of this company: each time we start a new project, we get to research, experiment, build prototypes and innovate, which is really enticing. It’s also crucial for our company, as we intend to revolutionise the packaging industry. The possibilities are truly endless.” n
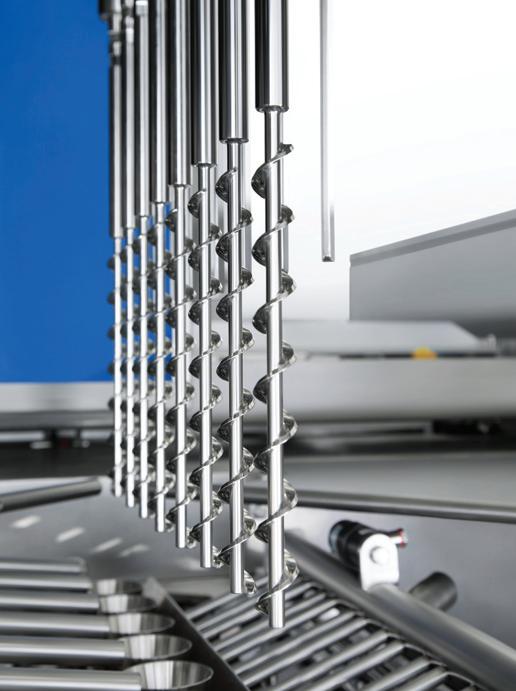
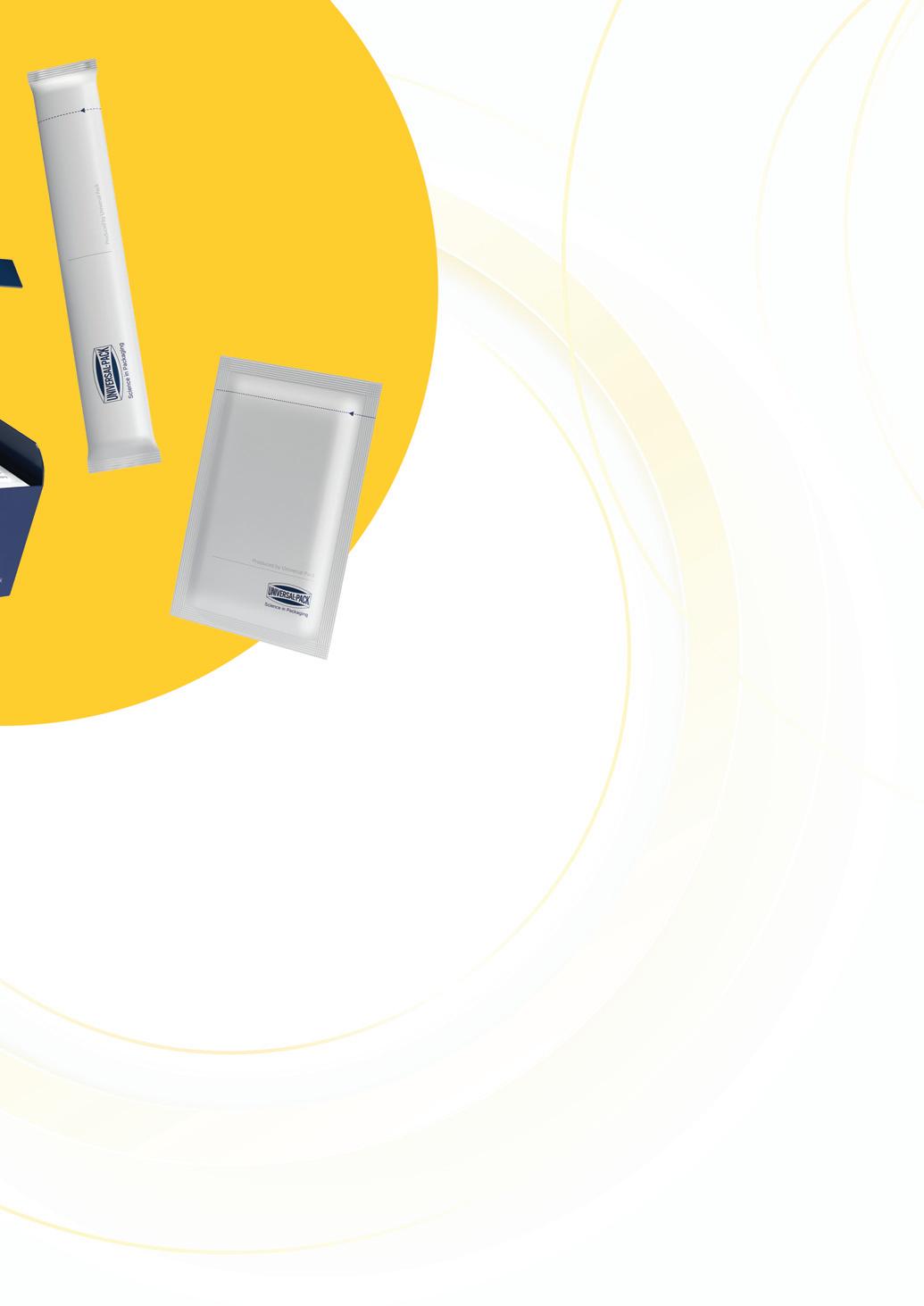
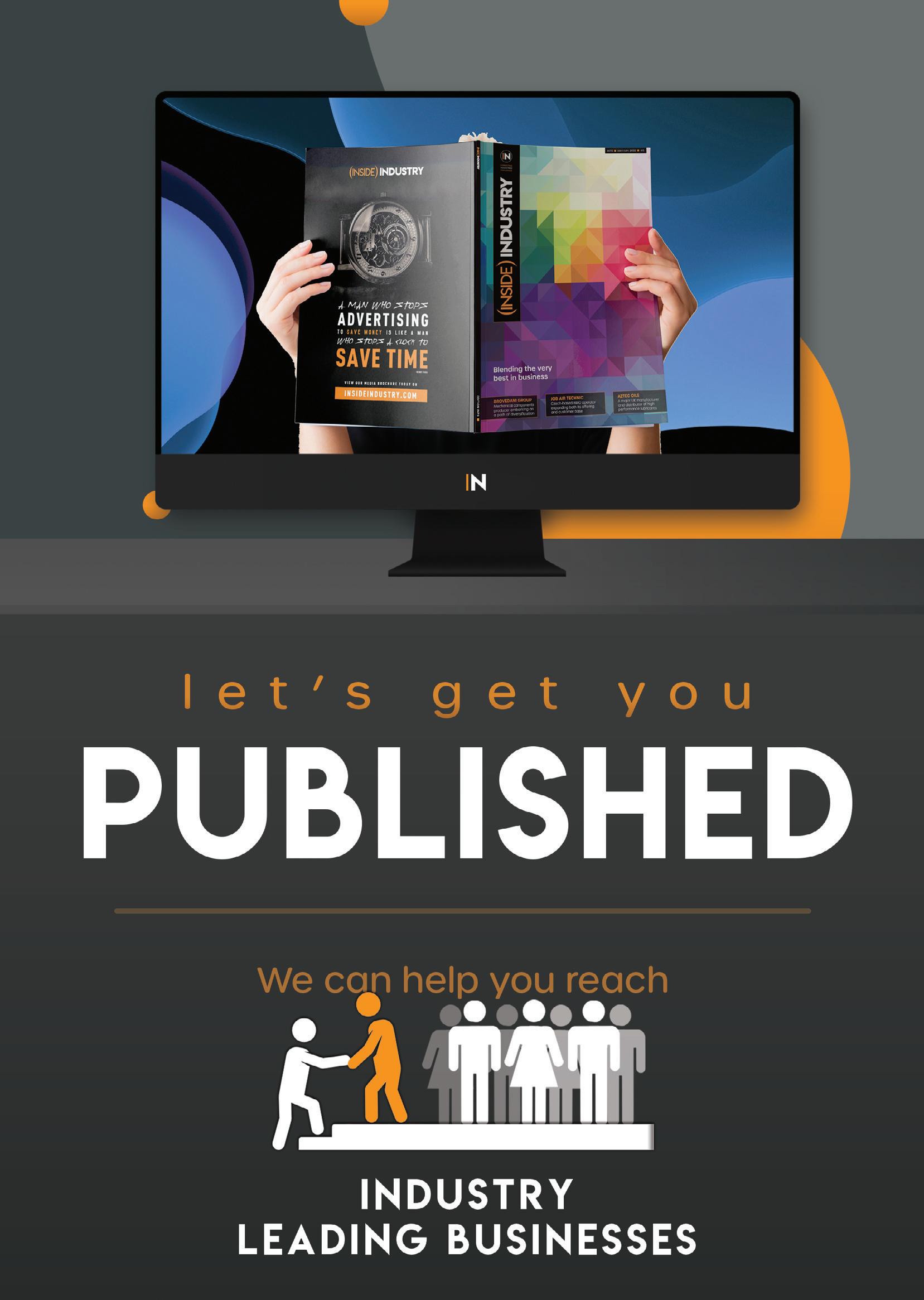
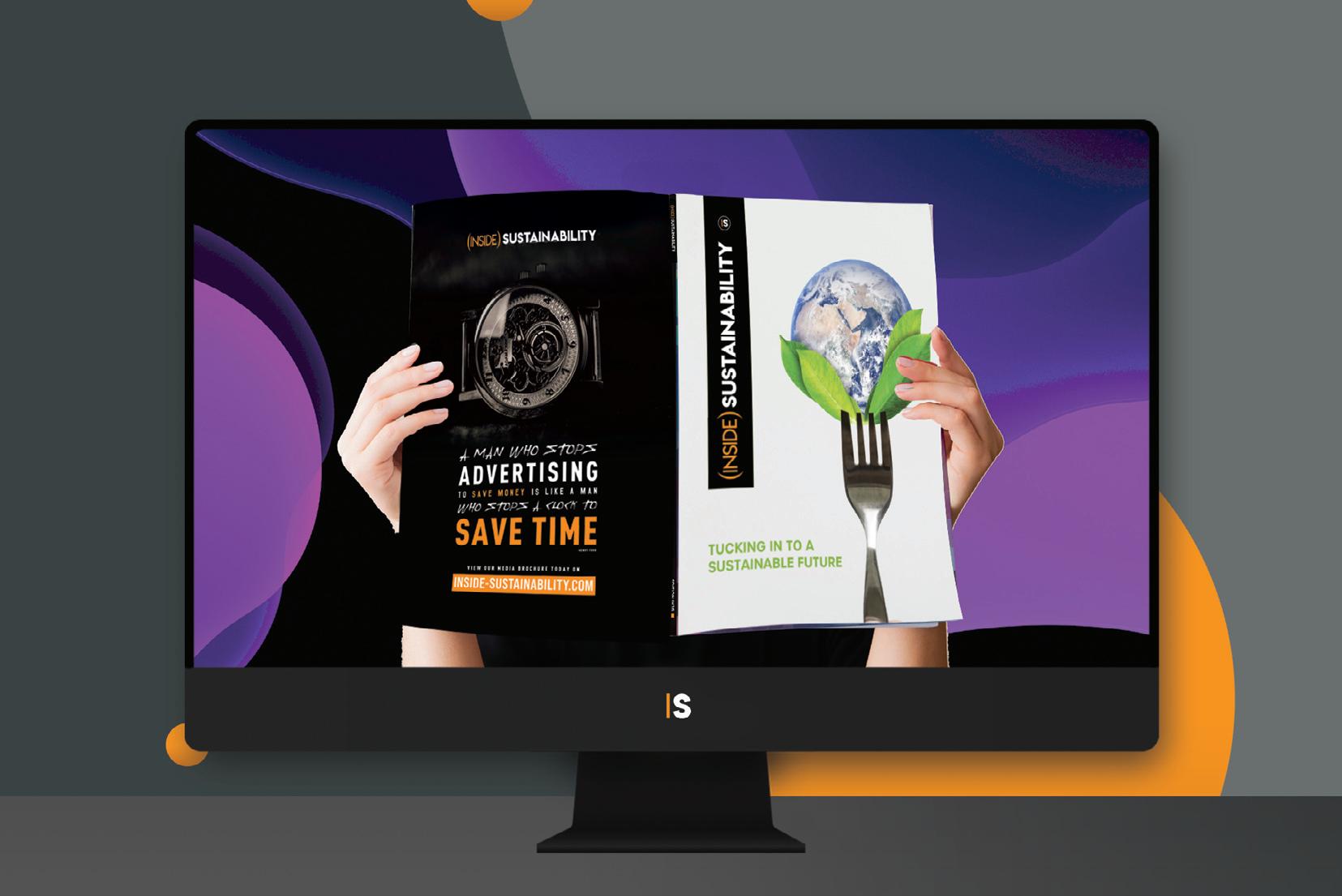