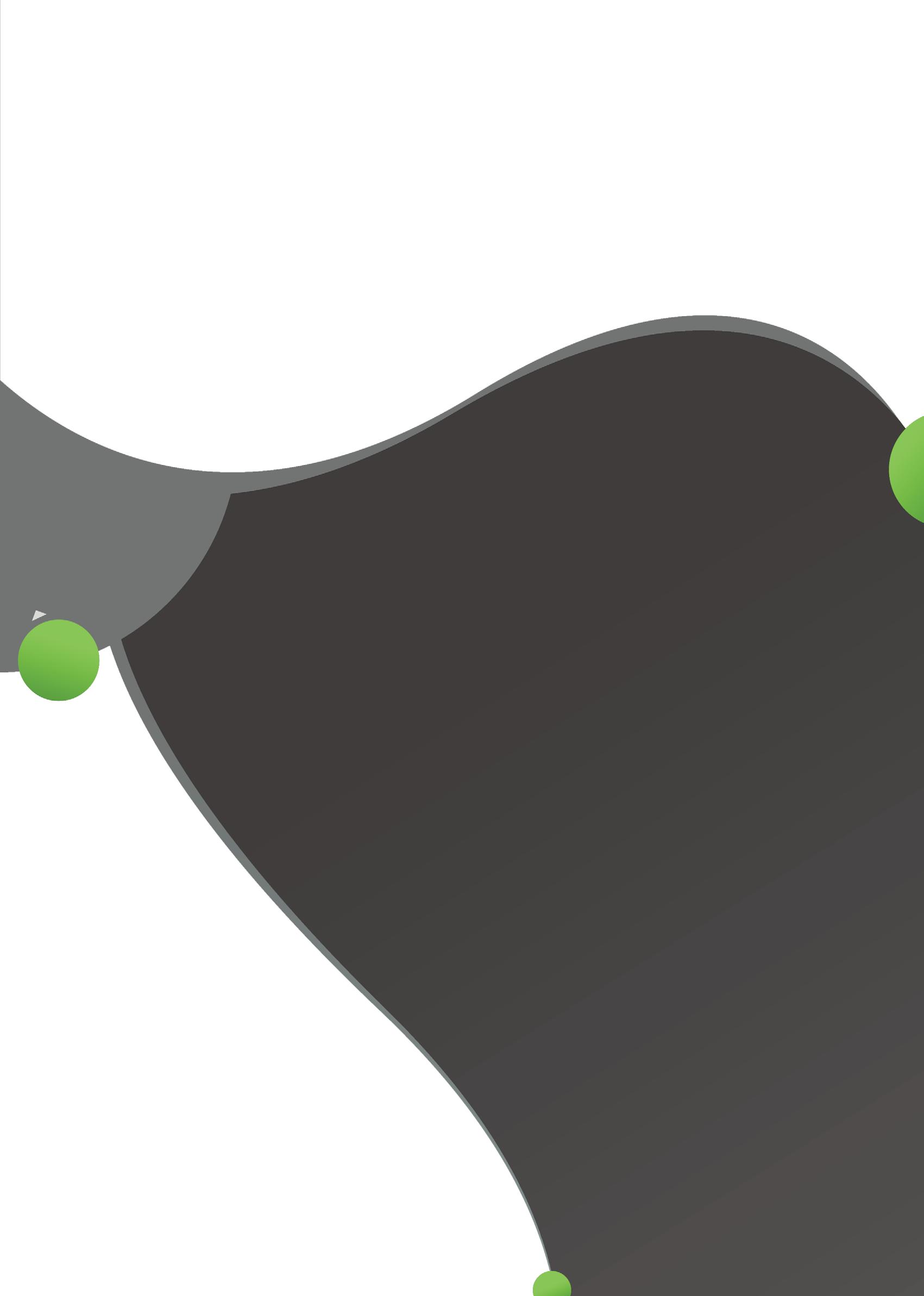
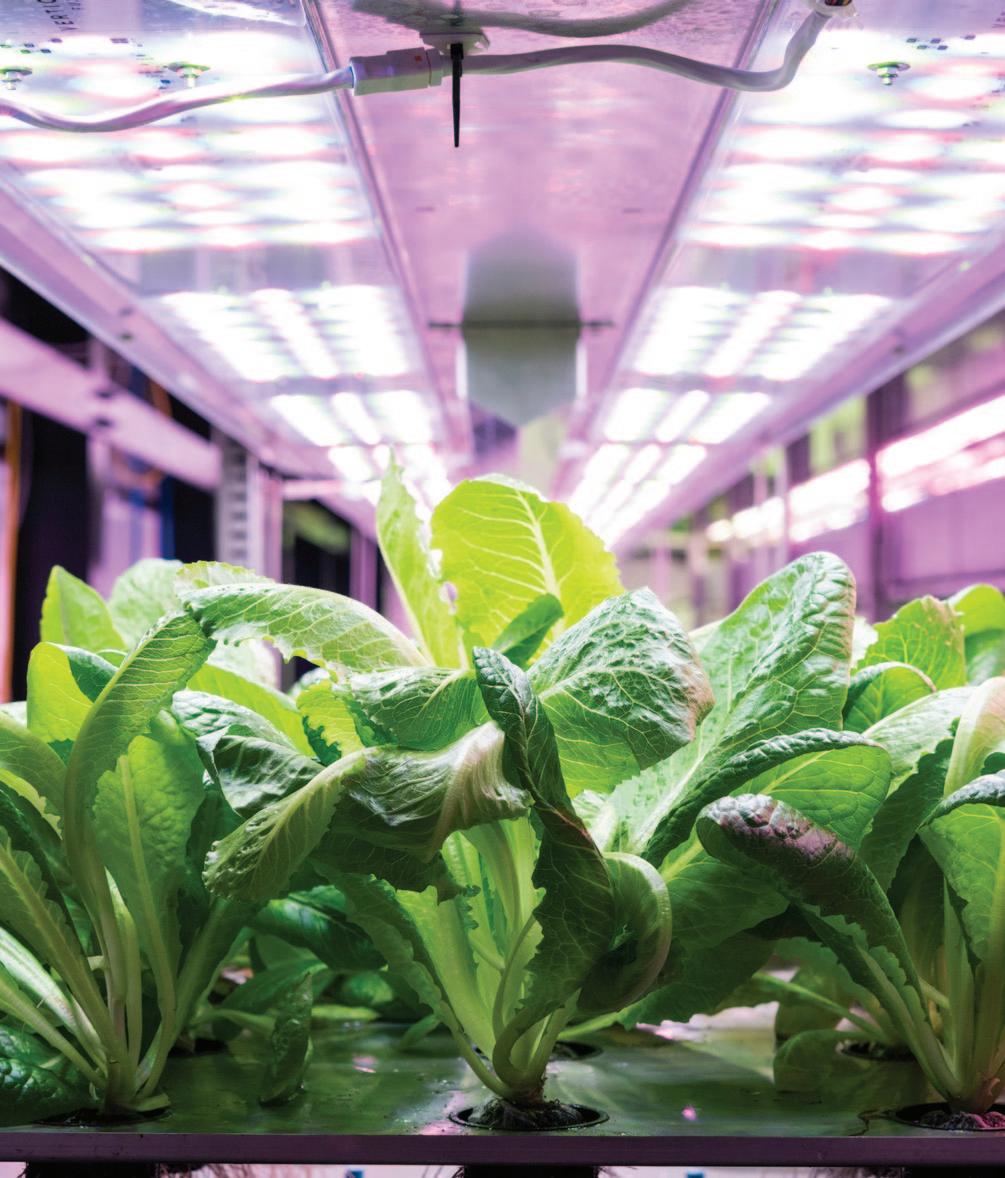

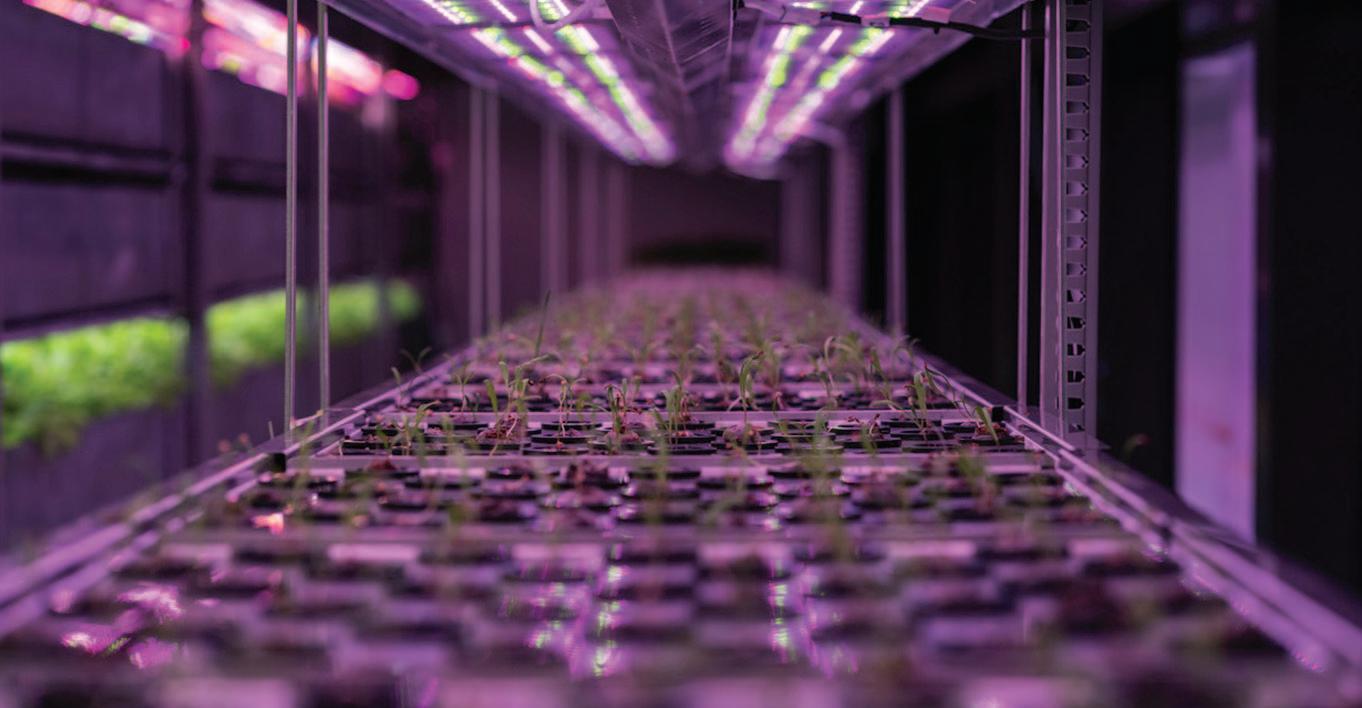
Vertical Future is a revolutionary and unique agricultural technology company, who over the last six years, has focused its efforts on inventing and implementing advanced vertical farming technology for its clients. Chief Commercial Officer, Gustav Holst Stuge spoke in-depth about the company’s current scope and its innovatively sustainable processes, in conversation with Imogen Ward.
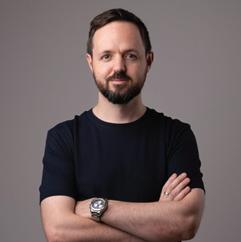
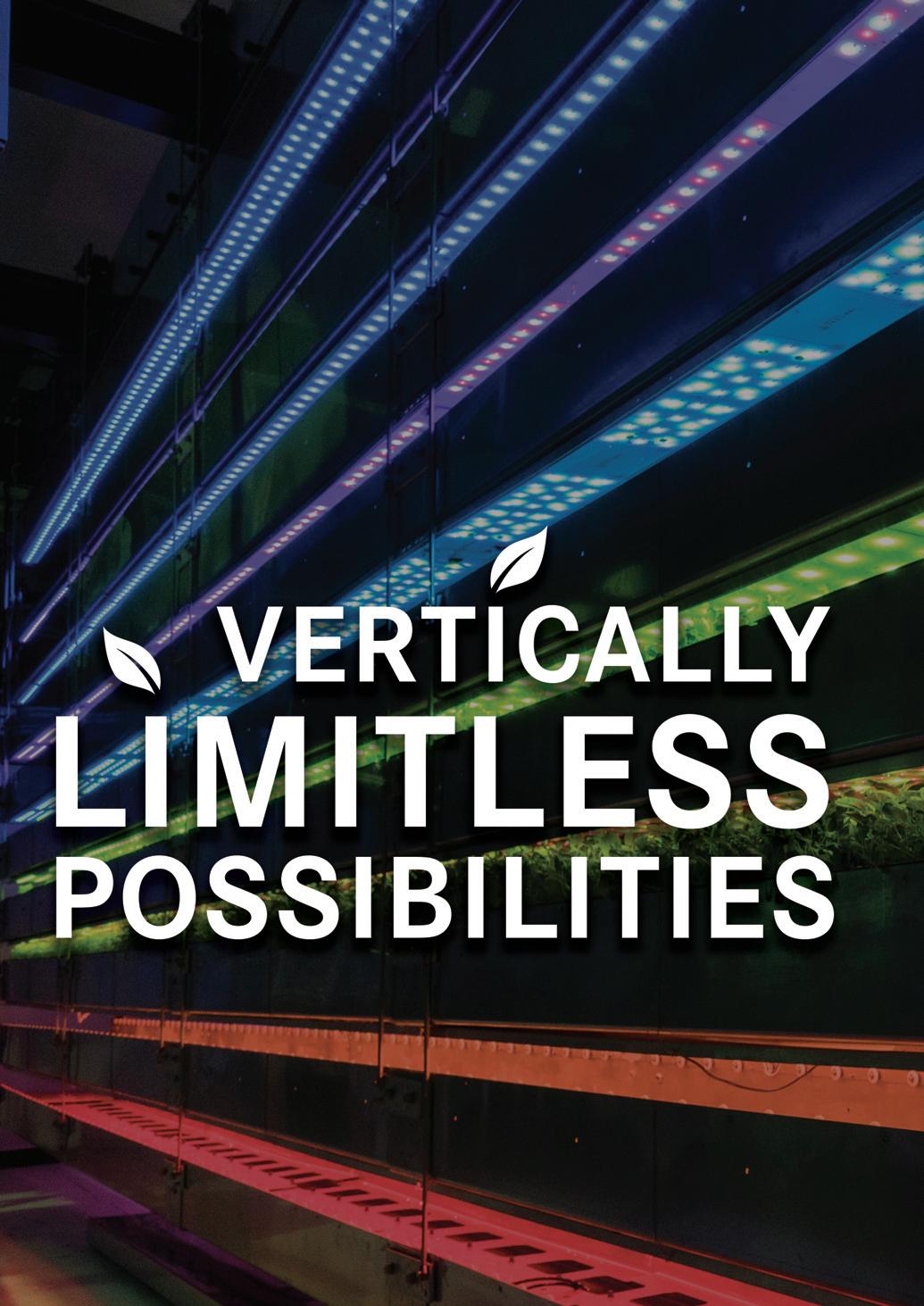
Originally starting as growers in 2016, Jamie and Marie Burrows, owners and founders of Vertical Future, noticed a gap in the vertical farming market for technology. After realising just how limiting the existing vertical farming technology solutions were, in terms of scalability and manual dedication, Vertical Future decided to diversify and develop its own systems –ultimately pivoting from an operator to a technology company.
Now designing, building, and selling its turnkey farms, the company has developed highly advanced and sophisticated software, reinventing what it means to vertically farm.
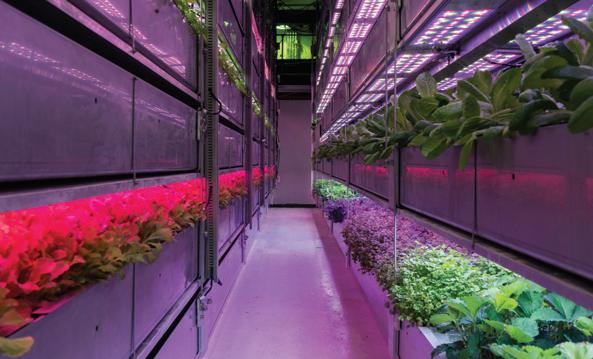
With nine farms currently operating in London, Vertical Future has well and truly mastered the confined limitations of the Urban world. Featuring a lab in London focused on every element of the company’s sophisticated software, Vertical Future is fully prepared for any eventuality.
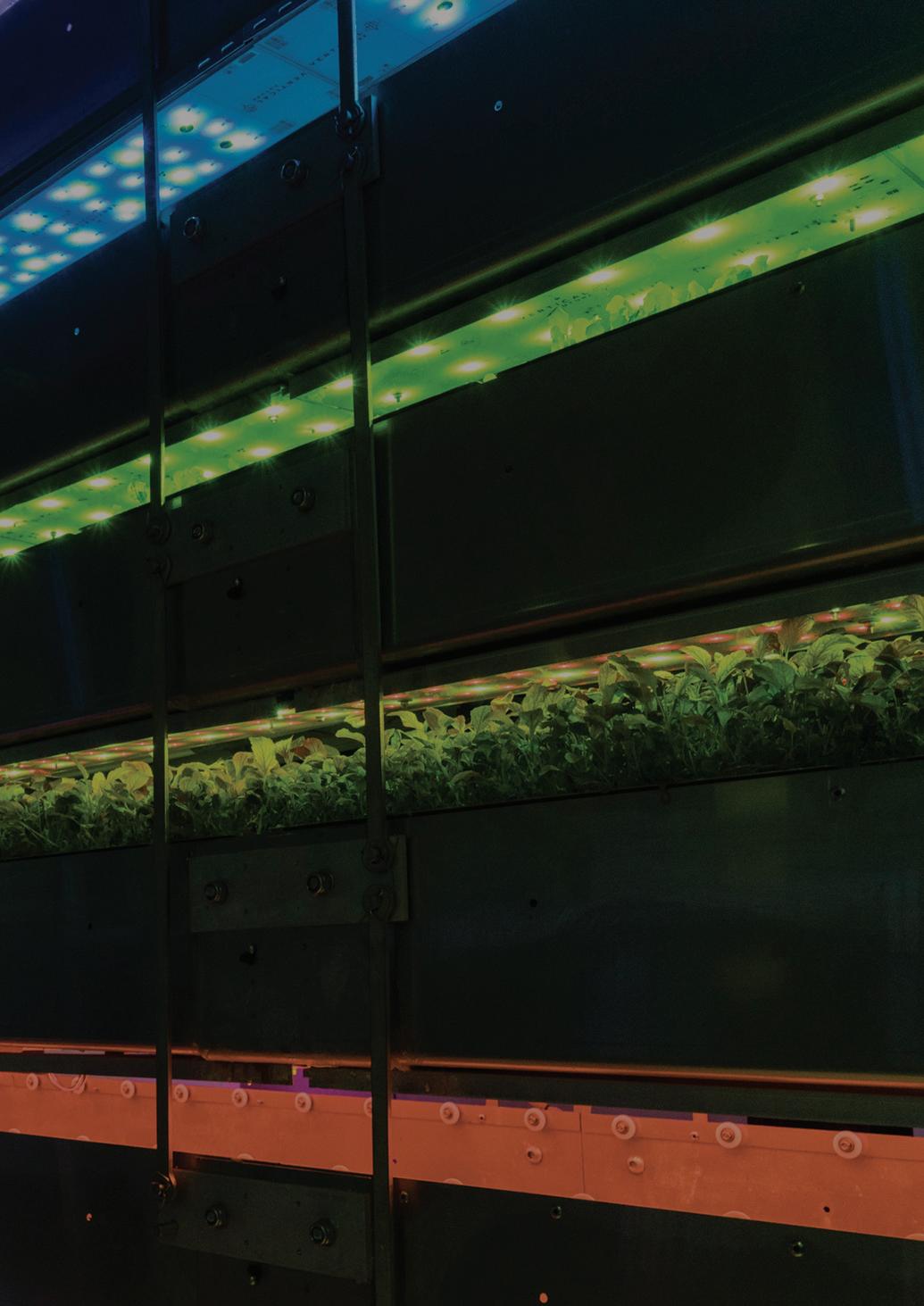
Dedicated DIANA Sustaining a strong relationship with its buyers through the implementation of its software system DIANA, Vertical Future maintains all of its farms remotely. Dedicating the last few years to redevel oping the system, the company now designs all aspects of the system – right down to every LED and robot.
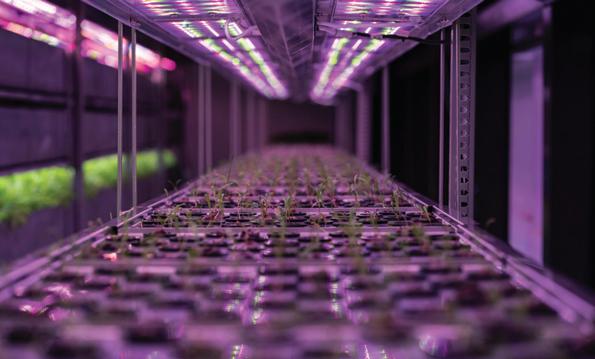
This high-specification system is divided into two parts. The operational side ensures that the farm knows when to water its plants, the correct lighting to provide, and informs the robots where to move crops and how often. Sensors are implemented on every part of the farm, enabling the system to pick up on any faults or errors. “For example, if there is a light that is about to go out, we can predict it and replace it without any dis ruption to the farm” CCO Gustav Holst Stuge said, “the sensor will register an unusual flow of current – the system will pick up on that, telling us exactly what we need to address within the system.”
On the flip side, research and develop ment is completed in a lab in London by 11 specialists who all have PhDs in plant sci ence. These professionals test every element of the farm, to decipher growth recipes and algorithms that are needed for optimal price and product quality.
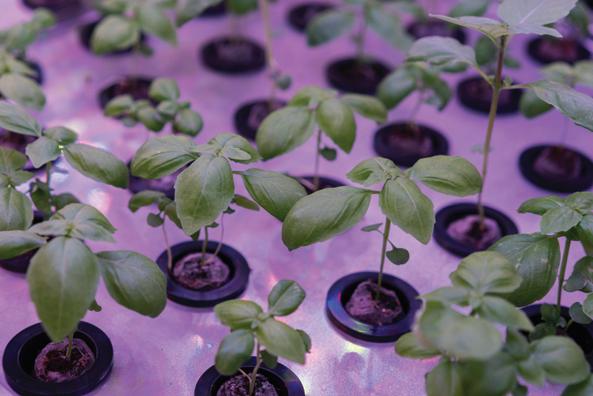
“Our specialists come up with the per fect amount of water, nutrients or different types of light,” said Mr Holst Stuge. “Once they have this data, it gets codified into algo rithms and becomes a sort of rule within the software. This information is then deployed into the farms.”
With a user-friendly interface, the farms are effortless to control. Updates can be downloaded by the touch of a button. The vertical farms only need one operator to produce as much as a conventional farm 100 times the size.
The successful software lives up to its reputation, having just received an award in Brussels for basil yield. “Vertical Future
increased the yield of basil by six times,” Mr Holst Stuge said. “We did this by finding a rare species of basil and deciphering how to grow that in a vertical farm. This infor mation was then uploaded to DIANA. So, for our customers who are growing basil, their yield has immediately increased six times.”
Sowing sustainability
The company is not only focused on increased food production, but is also incredibly environmentally conscious. Ensuring that its farms are as sustainable as possible, Vertical Future has several green processes implemented.

Comparatively, the space required for a Vertical Future Farm is around 1-3% the size of that required for conventional farms producing the same number of crops.
By implementing aeroponics, the com pany also uses a fraction of the water that a conventional farm consumes. Misting the plants for ten minutes every hour, the com pany created a very precise watering system. The plants are also suspended in air, rather than in water-soaked soil. By doing this, Vertical Future removes any disease risk
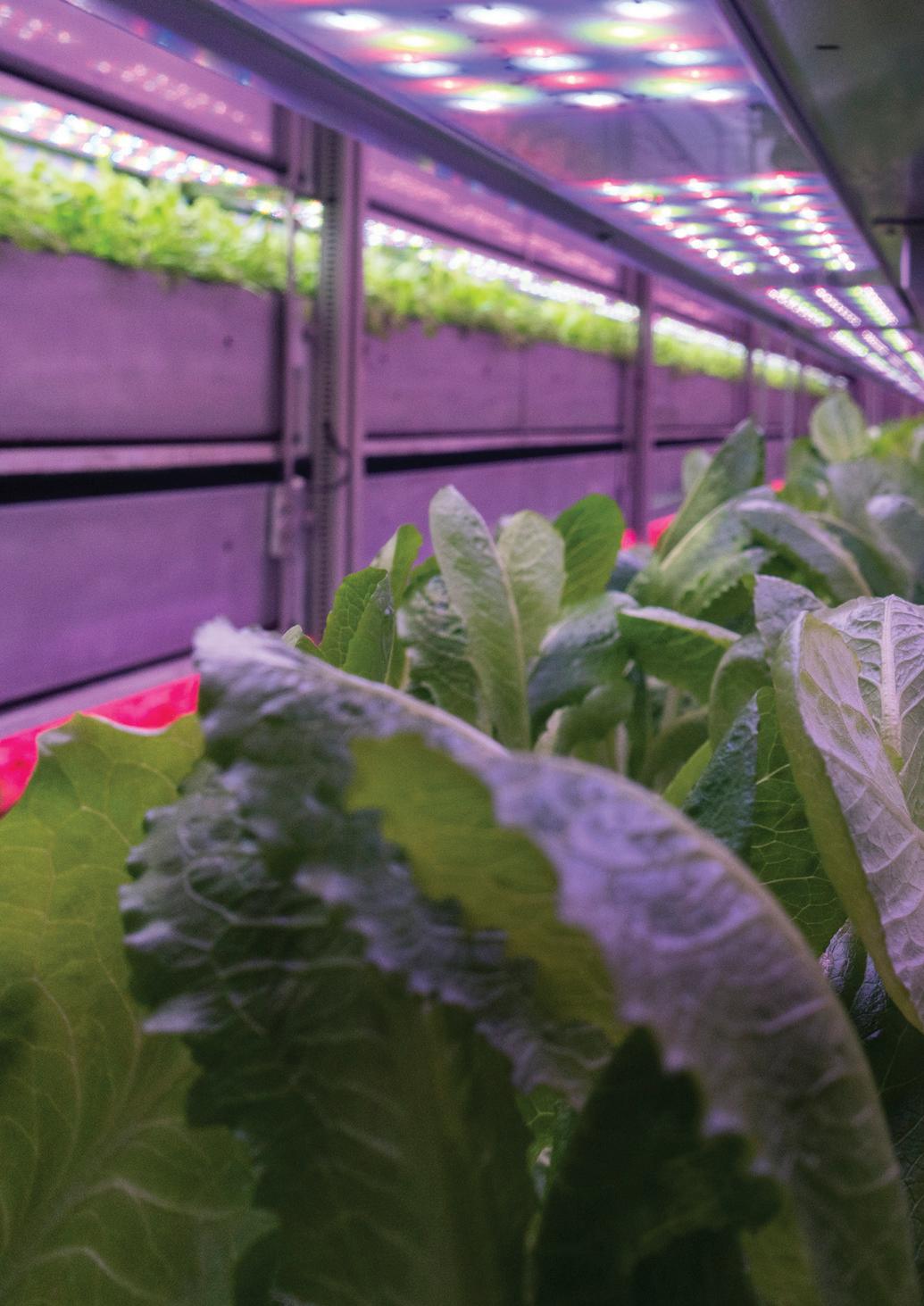
from a shared water system. This means that if a disease were to occur, the affected plant is removed without any consequence to other crops, essentially reducing food wastage too.
The flexibility of the system also means that if a plant were to struggle, the water or nutrient exposure will automatically adjust for that specific crop, ensuring its likelihood of surviving.
Because Vertical Future promotes the use of aeroponics, tilling is not needed. By removing ploughing from the process, the company is reducing the amount of carbon that would have been released into the atmosphere.
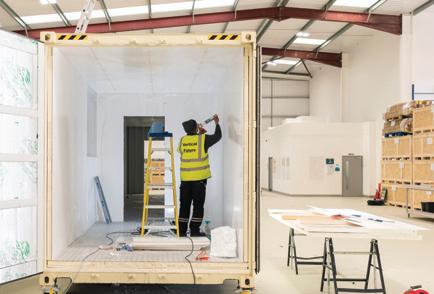
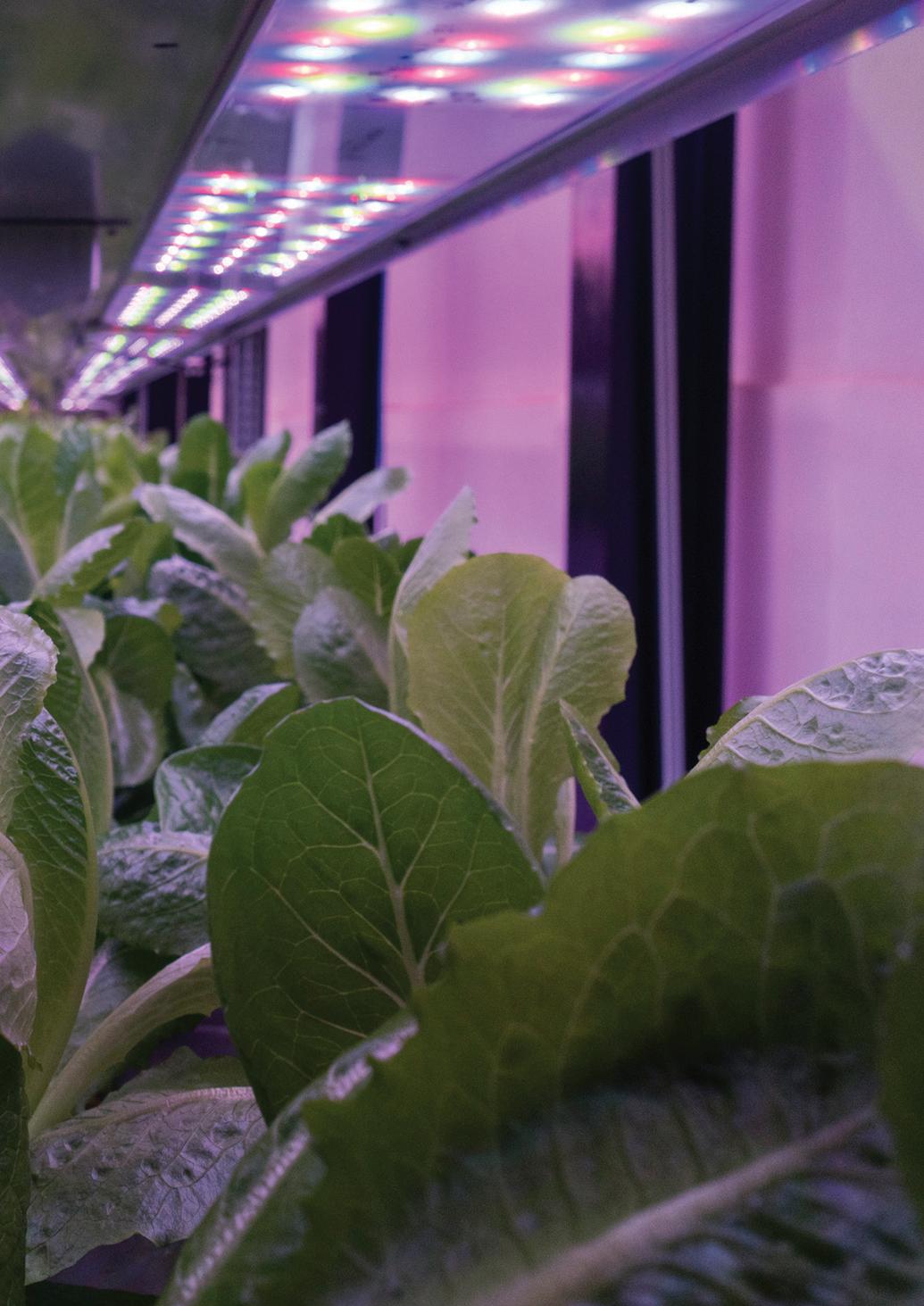
Vertical Future is also completely against the use of any kind of pesticide, herbicide, or fungicide. “When they get sprayed onto your crops,” Mr Holst Stuge said, “people are then ingesting these incredibly toxic substances. We do not use it at all, there is no need, we have no pests in our farms because we don’t use soil. Every time these chemicals are sprayed, they destroy the UK’s rich biodi versity, as seen in the critical decline in bee populations.
“These insects are important vectors that allow our biodiversity to grow. Not only are we making healthier food for our cus
tomers, but we are also taking the stress off the planet, whilst still producing the food we need.”
Cropping up worldwide
Vertically integrated, the company produces all its components in-house. By solely building and maintaining the systems, Vertical Future has overcome supply issues and reduced risk of delays. Another challenge that the company has conquered is the surge in energy prices. To counteract this, Vertical Future has begun connecting its farms to renewable power micro grids, focusing mainly on solar panels. Not only does this help control power prices, but it also creates opportunities for off-grid food production. With off the grid power and
water, vertical farms can be built anywhere in the world. This has the potential to signifi cantly impact global hunger, which is a problem of proximity to food production.
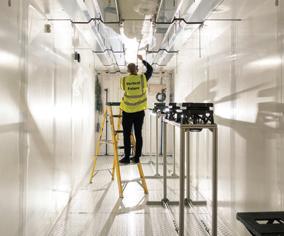
“Having the opportunity to work with technology that can have a real impact is quite unique,” said Mr Holst Stuge. “We’re at the point where food security, power consumption and supply chain issues are all coming together to drive the need for sustainable food. It’s really an issue on everyone’s mind. Having tech nology that can address that is amazing and really fun to work with. We say proudly that our tech nology can solve this problem not in the future, but today.”
For now, however, Vertical Future is focused on spreading its technology across the globe. “What we are building is quite unique,” Mr Holst Stuge concluded. “We are one of the few companies that has really proven that we can produce food at a sus tainable price with our technology. We are very focused on bringing down our cost of production, and going global, so we can address some of the food production issues worldwide. We are not wanting to produce the most expensive salads in the world. We want to produce food for everyone, everywhere, without having to compro mise on quality or sustainability.” n
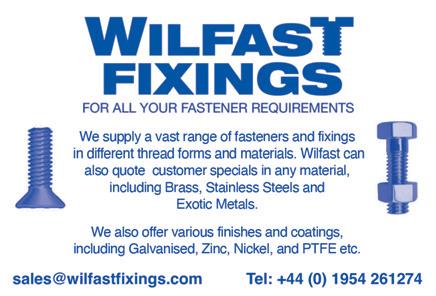
