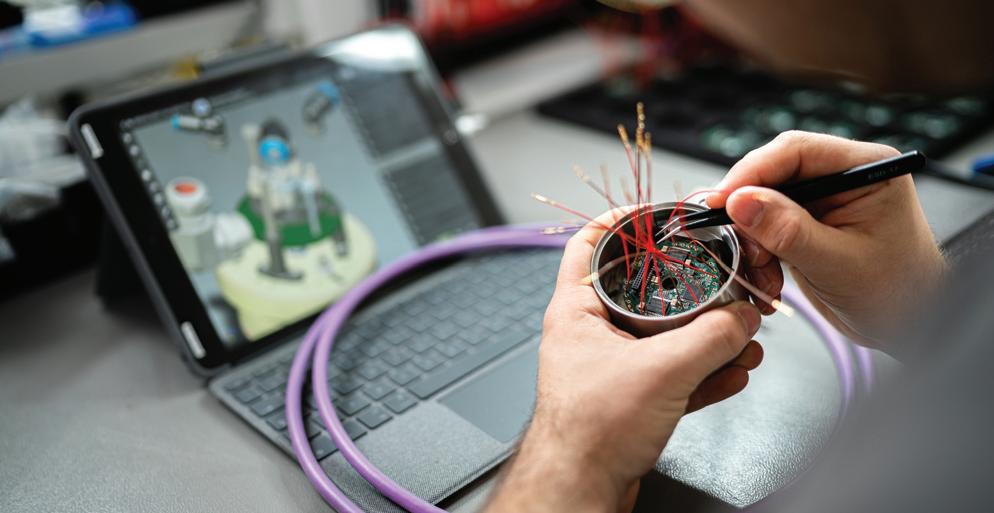

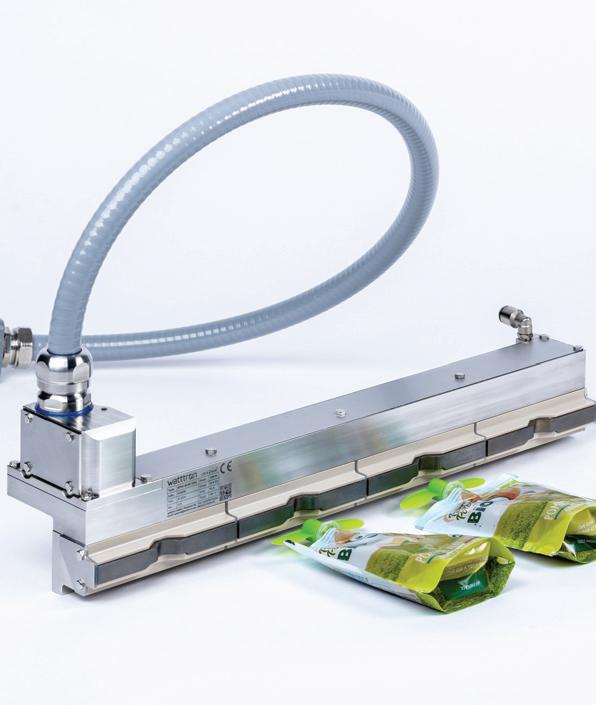
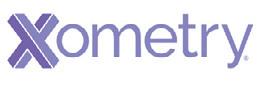
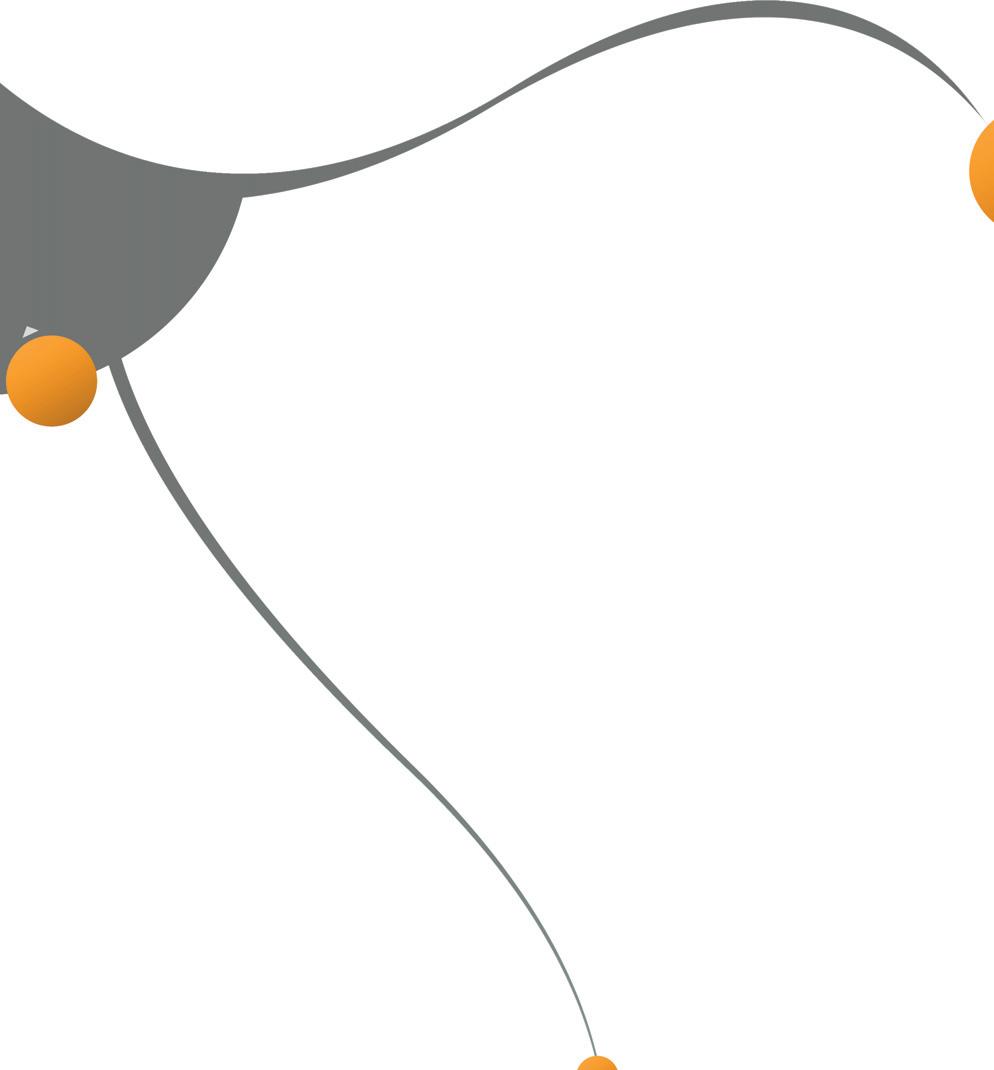
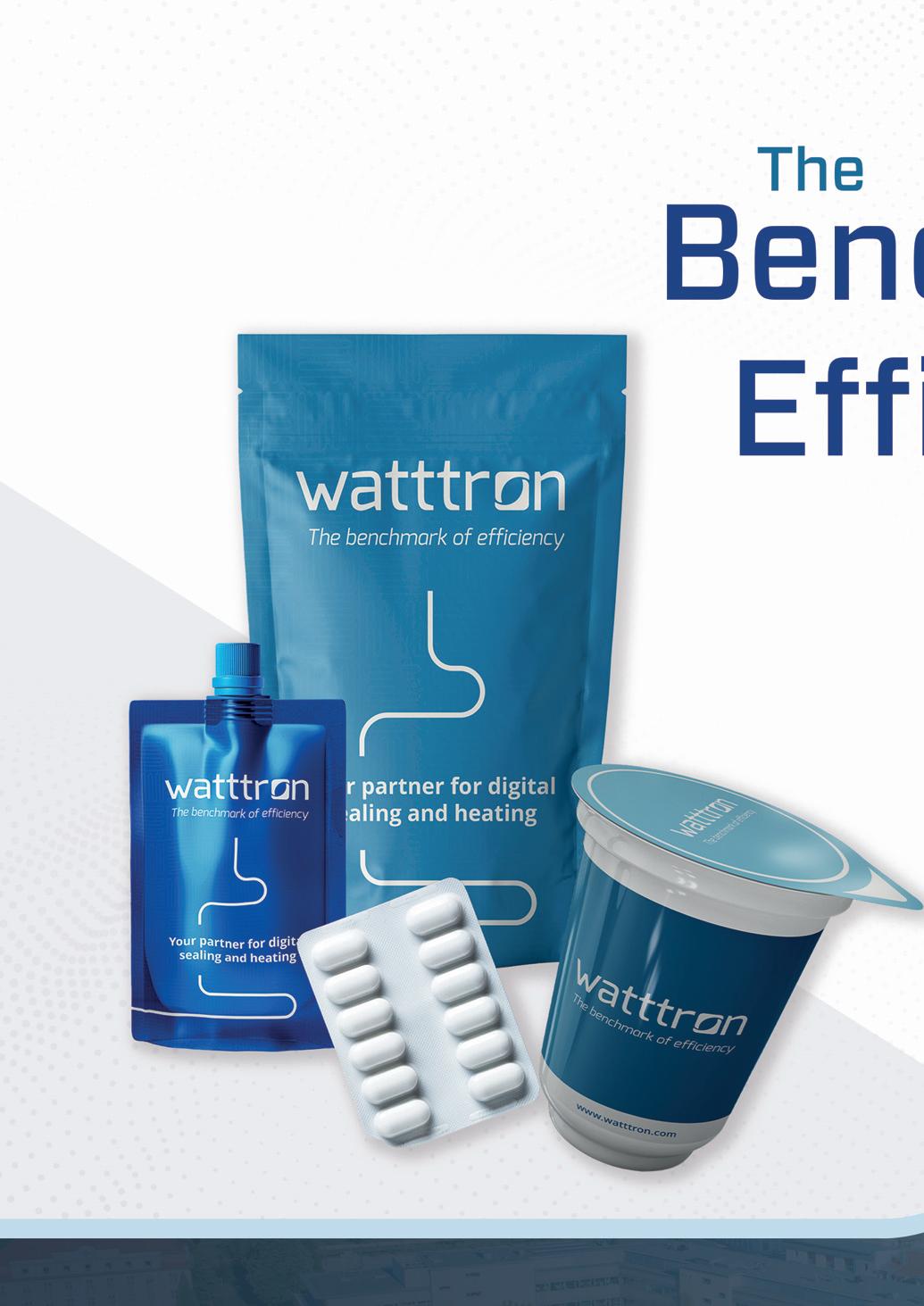

Specialising in intelligent heating systems, watttron gives customers control over their thermal processes, optimising quality and efficiency. CEO Marcus Stein discussed the company’s mission to make packaging machinery sustainable, as well as economical. Report by Antonia Cole.
Founded in 2012, watttron’s goal is to fully transform the packaging industry, CEO Marcus Stein said: “We began with three employees, but this number has now grown to over 70. With a global network ranging from Japan and Italy to the US, UK and more, we have already made a significant impact on the sector.
“We have over 30 machines in production and supply to some of the biggest CPGs
in the world. With recent investments, I expect this success to grow even further.”
The company began at the Institute of Natural Materials Technology at the Technical University of Dresden and Fraunhofer Institute for Process Engineering and Packaging Dresden. The company was established with the mission of creating intelligent heating systems that fully utilise material and energy use.
Working within the plastics processing, packaging, medicine and pharmaceutical technology, and food industries, watttron’s innovations aim to support clients in operating more sustainably. By reducing the energy requirements of products, customers can then achieve flexible and highly efficient operations.
Versatile technologies
Providing digital heating systems, watttron has developed the technology to deliver local and defined heating. The company’s patented cera2heat matrix heating system facilitates very precise, heterogeneous contact heating on surfaces, enabling more efficient processes.
The thermal system utilises small heating pixels that are regularly arranged in large numbers. Each pixel’s temperature is
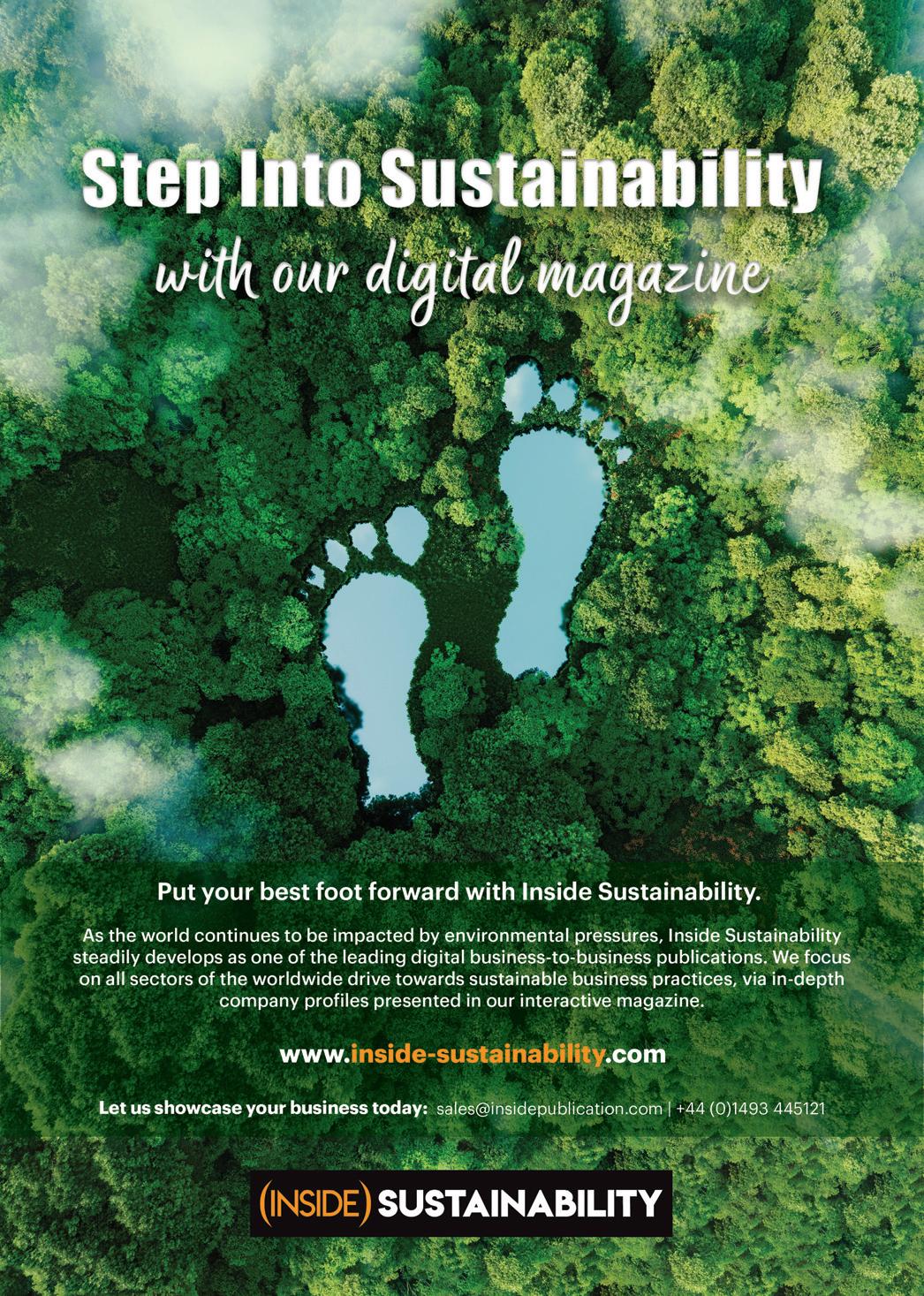
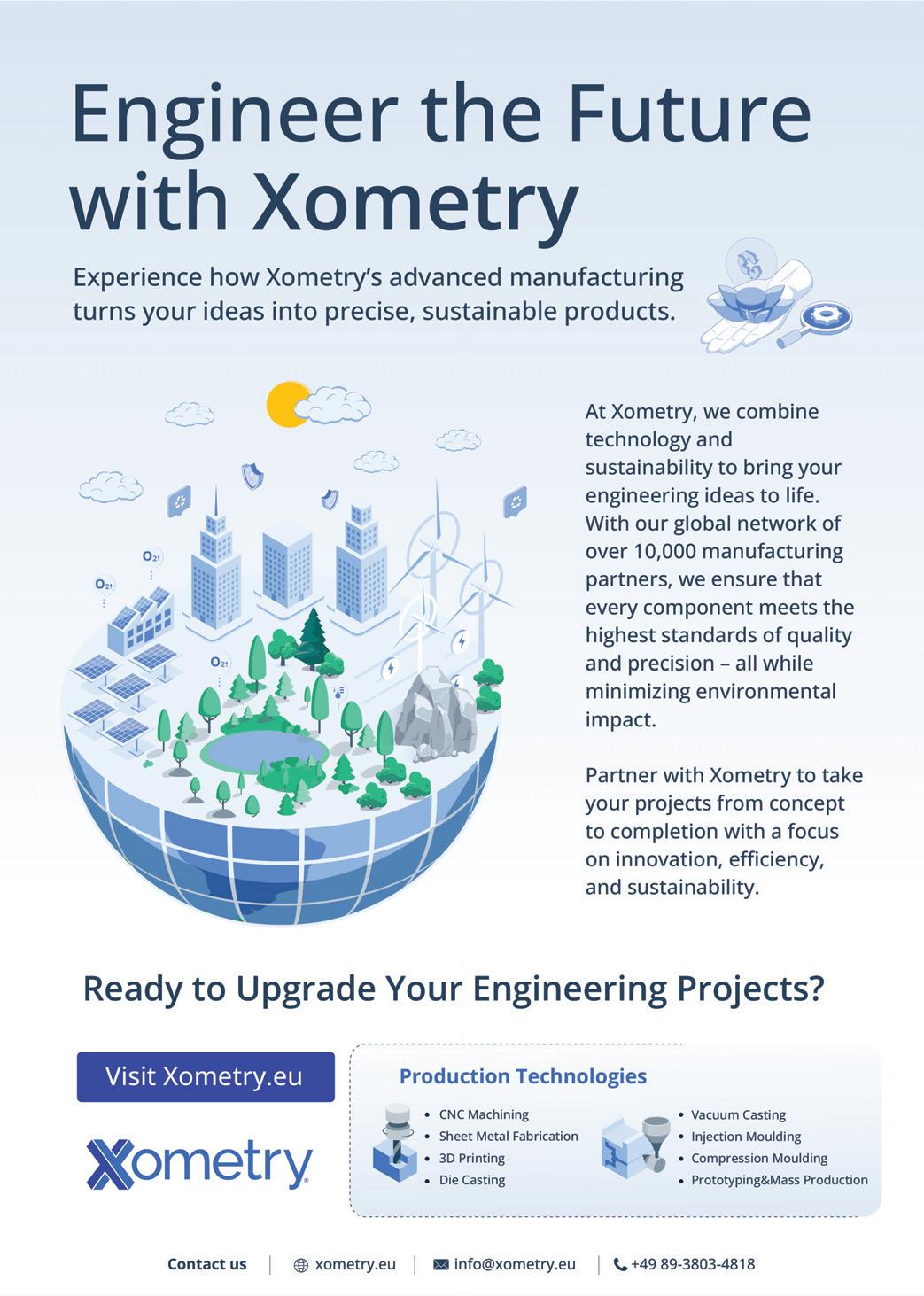
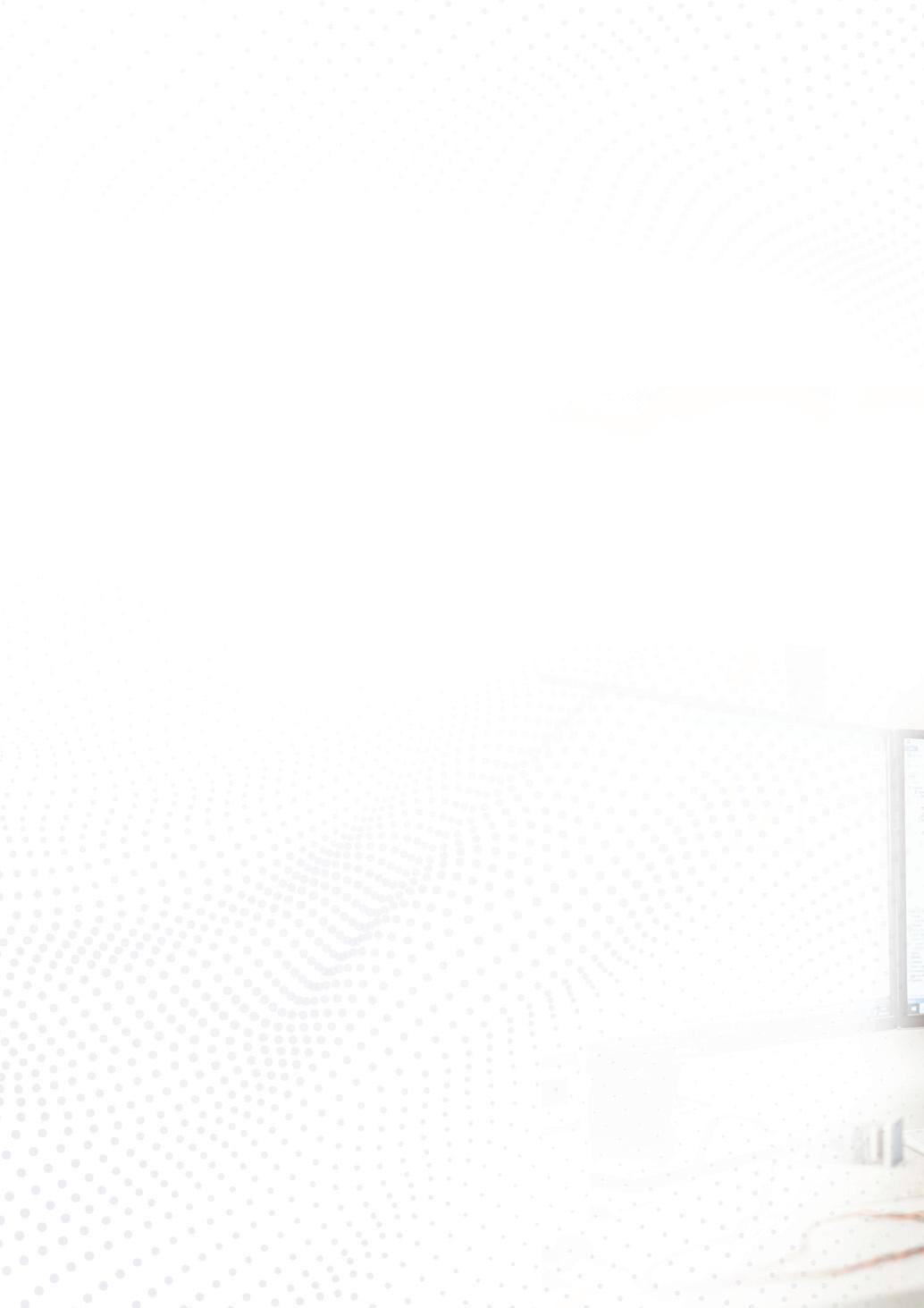
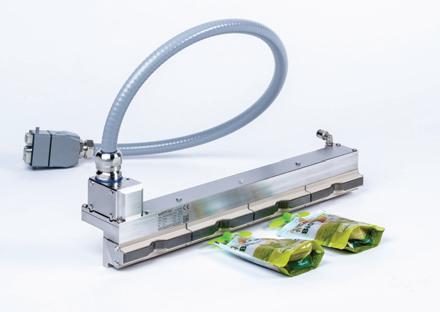
individually controllable and programmable, meaning energy use can be optimised for heating dependent upon specific client requirements, such as for specialised materials.
An analogous to TFT screen makes the heating pixel controls visible as a thermal image. This improves ease of use, facilitating seamless integration into production lines
The cera2heat can also be installed or retrofitted into almost any existing machine, minimising resource use and waste.
“This technology creates new opportunities for customers,” explained Mr Stein. “Each pixel can work differently to create a specialised solution that gives optimal results. For example, if a client makes a pouch where thickness varies along the item, then we can program the pixels to heat each area separately. Instead of having to heat the entire pouch, our customers can direct heat to specific areas, improving energy efficiency.”
Additionally, watttron offers a cera2seal heating system that is designed for sealing and welding processes. With a freely selectable arrangement of individual heating circuits, this technology
enables the production of complicated packaging geometries, including irregular shapes, plus sealing bars and rings of different widths and sizes. Temperature sensors provide the customer precise control of thermal distribution, giving effective results.
“A big milestone for us was when we had our first systems running with a large food producer,” added Mr Stein. “It was really rewarding to see our work put into action and really making a positive difference to our customer’s operation. The large food producer was able to easily integrate recyclable materials into its production lines, whilst also limiting its carbon footprint. Since then, we’ve worked with many more clients and have had very positive feedback.”
Thermal solutions
The company wants to prove to the industry that sustainability and productivity are simultaneously achievable. With less energy, watttron’s systems are still able to run at the same speed, or even faster than many existing machines, and can use recyclable materials. Not only is it an ecological approach, but it also offers an economical benefit for the customer.
“It’s important that we change people’s attitudes towards sustainable solutions,” commented Mr Stein. “This is a challenging task, but our systems are proving that it doesn’t have to cost more to be environmentally friendly. We want to encourage more people to embrace this shift to sustainable operations.”


As watttron’s technology can be integrated into existing machines, this offers customers a more carbon- and cost-friendly approach. By upgrading a client’s existing machine, watttron limits waste from old machines and emissions from new machine production. Also, this process is quicker and easier for the customer, resulting in a solution that enhances operations and protects the planet.

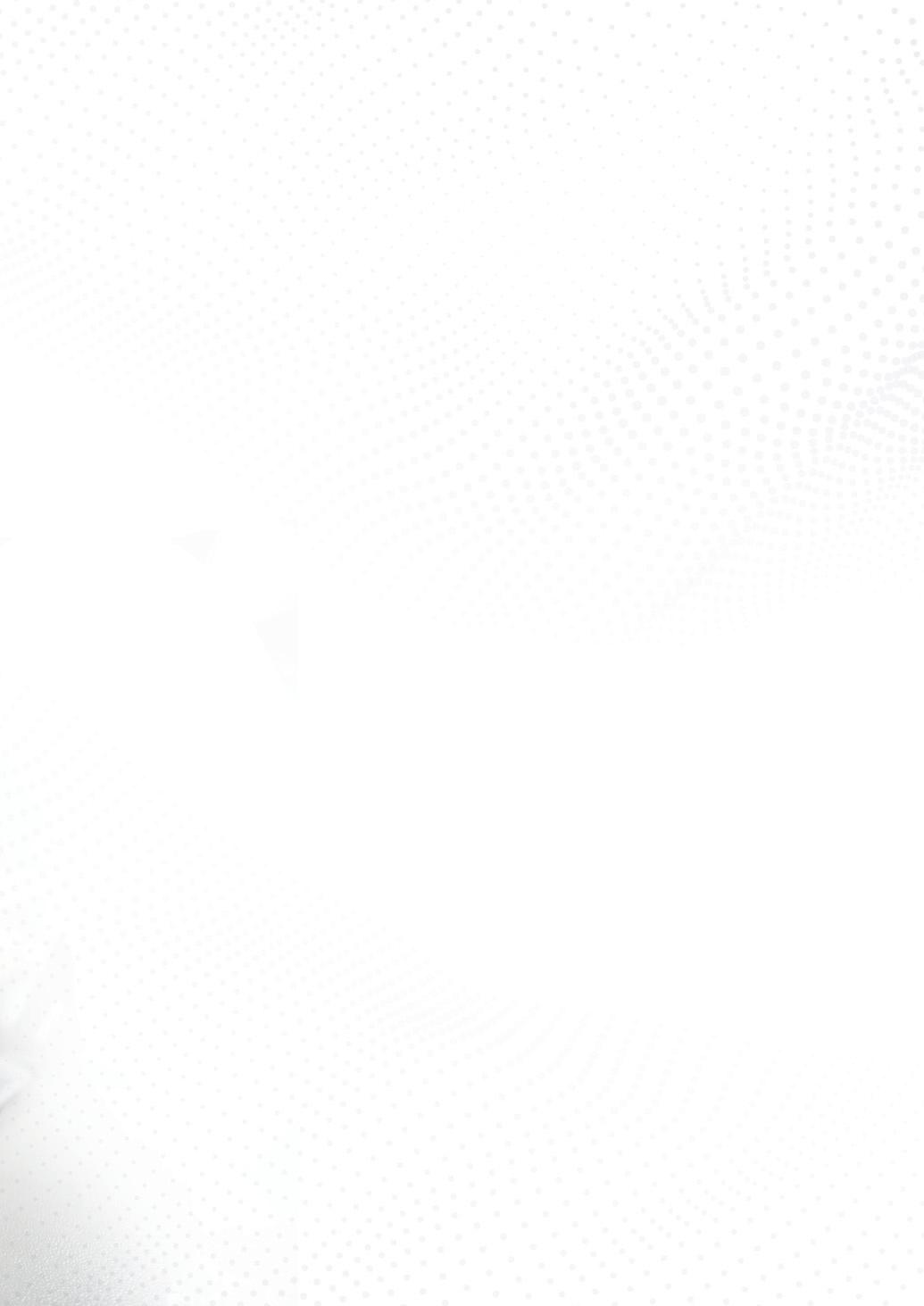
“There are three key benefits of our systems when put into practice,” continued Mr Stein. “Customers can use less material, use recyclable materials and lower energy consumption. We help clients change to mono-materials, as well as improving wall thickness distribution. Overall, our technology uses up to 80 per cent less energy than a typical machine, offering substantial cost-and energy-efficiency.”
In April 2024, watttron announced that it had received €12 million in investment to further develop innovations. Now, that funding has been extended to €15 million. This will not only allow watttron to increase capacity, but it will also enable the company to research and improve existing technology.
Industry partnerships
R.A Jones makes some of the world's fastest production machines, finishing up to 800 pouches a minute. One of its customers wanted to switch to using mono-materials, so R.A Jones partnered with watttron to retrofit the machines. The customer uses 40,000km of film every year, which with watttron’s technology is now all recyclable material.
“We have been able to build up a relationship with R.A Jones through this, as we can offer a solution to its clients,” said Mr Stein. “This is really important as we strive to transform the impact of mass production. We are able to reach more people, have a larger sustainable contribution and progress our vision to make recyclable packaging the standard.”
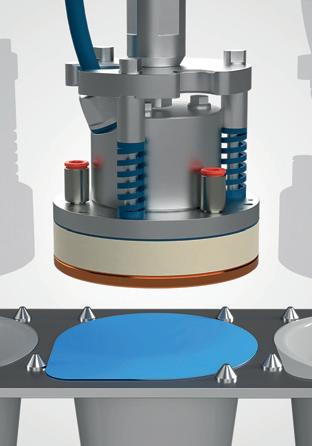
Over the years, watttron has built up many long-term relationships with suppliers and partners across the industry. Many of the company’s partners have worked with watttron since its inception, building up trust. Strong partnerships allow watttron to grow and integrate its technology into the industry, making it more sustainable.
This year, watttron will be returning to FACHPACH alongside FormerFab, specialists in paper-based forming shoulders. Both companies will have a booth to exhibit and discuss innovations. The collaboration between both companies shows customers how the technologies can combine and be applied in different scenarios.
“FACHPACH is a great place not only to meet potential clients, but to keep in contact with our existing partners,” explained Mr Stein, in conclusion. “We can build upon our existing relationships, whilst also discovering new industry developments. I love being able to meet people from all over the world to discuss sustainability. At watttron, we are working on a global issue, so collaborating across the packaging sector is key.” n
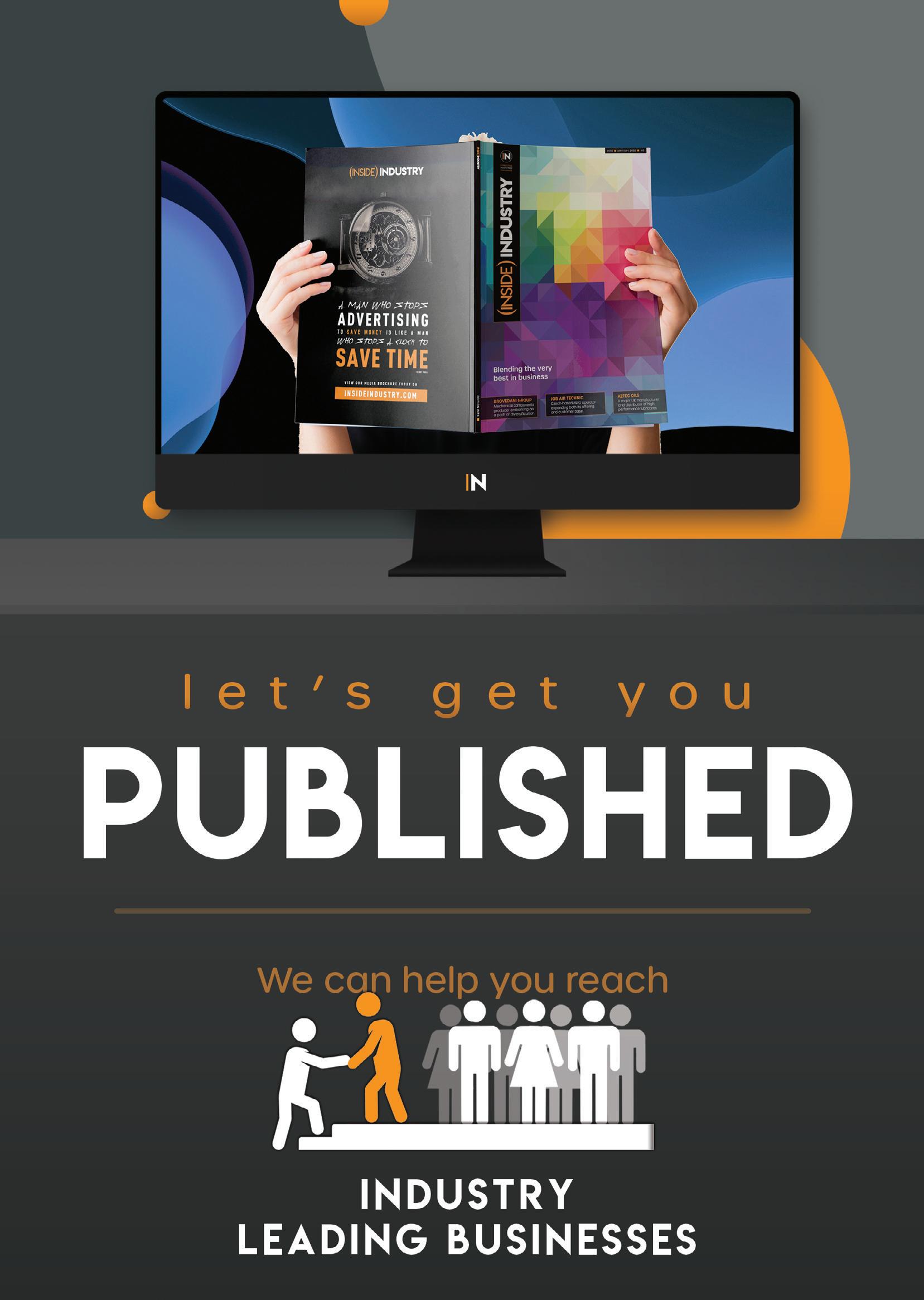
