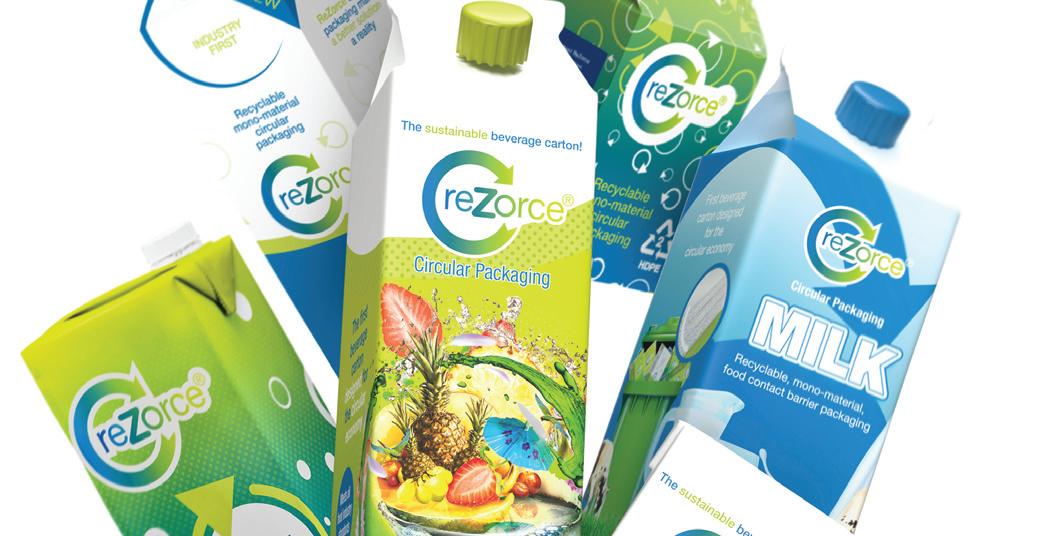
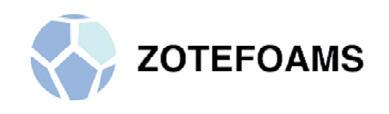


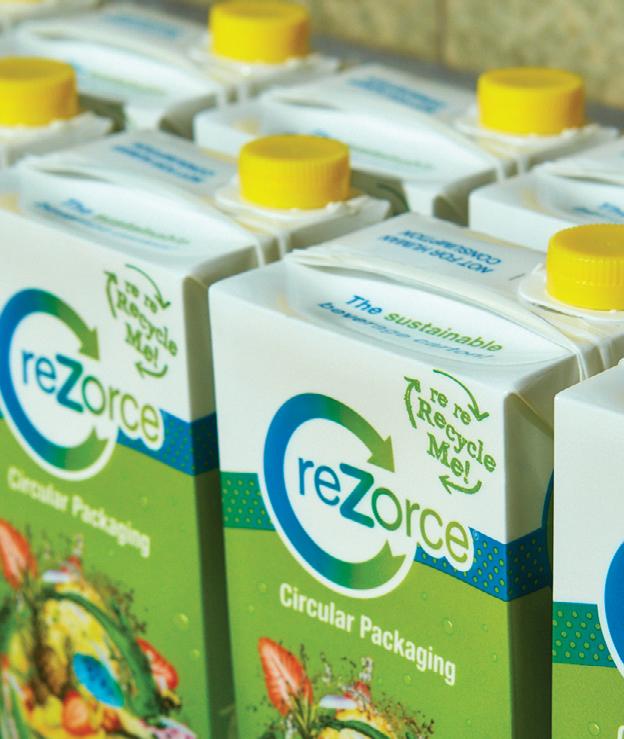
UK-headquartered Zotefoams plc aims to disrupt the 300 billion-p beverage carton market with its ReZorce mono-material barrier p Neil Court-Johnston, President of Zotefoams’ MuCell Extrusion bus outlined this exciting development to Inside Sustainability.
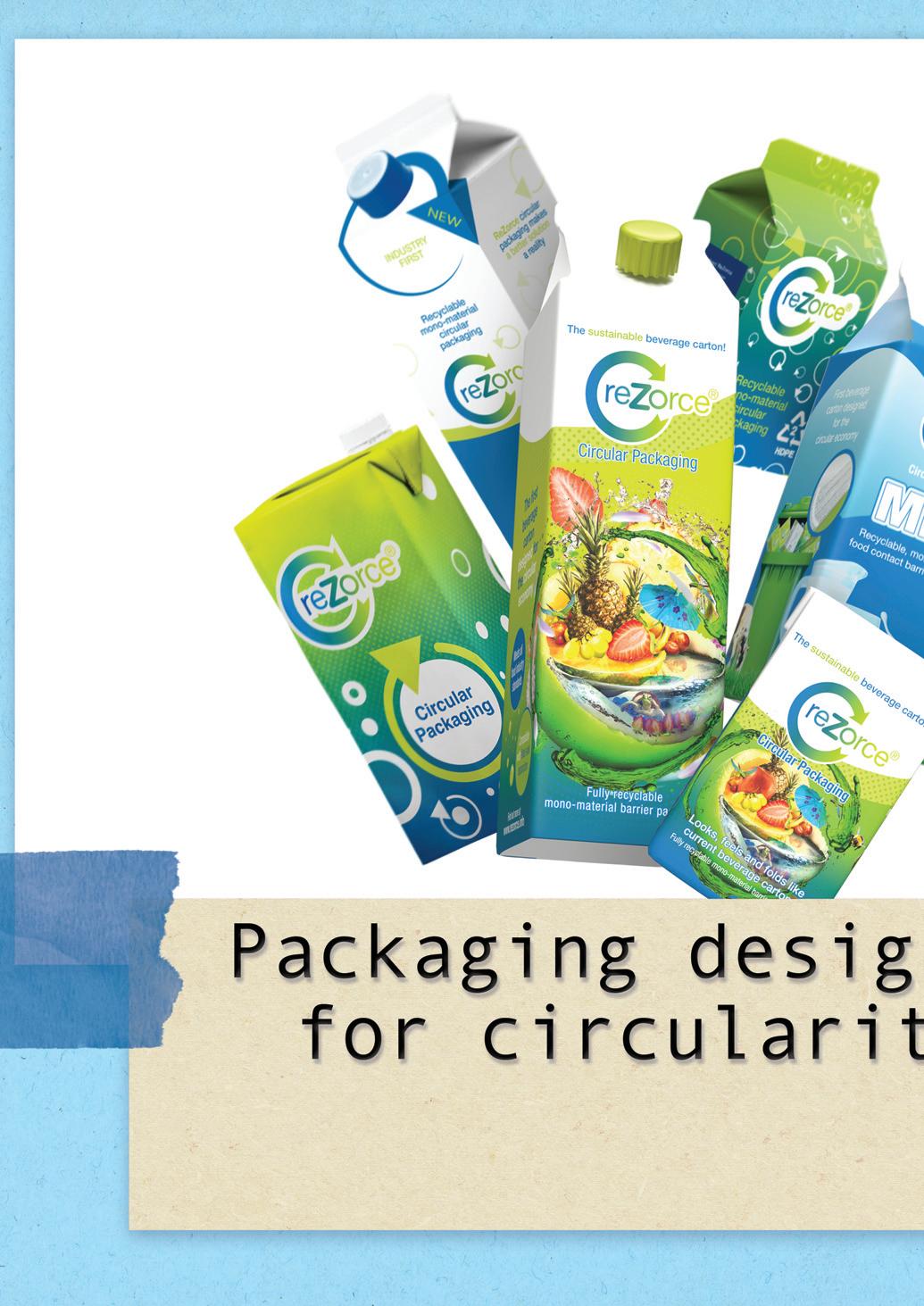
siness unit,
The Zotefoams portfolio of unique technologies produces lightweight foamed polymers used across diverse sectors including space exploration and running shoes, transportation and industrial packaging.
“Our history is rich in material science,” said President Neil Court-Johnston. “Zotefoams’ DNA revolves around developing optimal material solutions for the benefit of society. This is echoed at MuCell Extrusion, our business unit responsible for developing the ReZorce® mono-material barrier packaging.”
ReZorce began in 2011, when Zotefoams acquired Massachusetts-based MuCell Extrusion LLC, specialists in the injection of atmospheric gases (carbon dioxide or nitrogen) into plastic extrusions during the melt phase, reducing the density of finished products.
“During the process, we inject the gases evenly across the web to create an extrusion with a foamed core bounded by solid outer skins,” explained Mr Court-Johnston. “Typically used in consumer packaging, this process allows manufacturers to reduce polymer usage by 15 to 20 per cent without impacting performance.
“We also discovered that the foamed inner layers delivered excellent barrier properties – essential in many food packaging applications to maintain the freshness of products by protecting against the ingress of moisture and oxygen.”
Three years ago, in collaboration with Smithers (the global technology consultants), Zotefoams comprehensively reviewed the per-annum packaging.
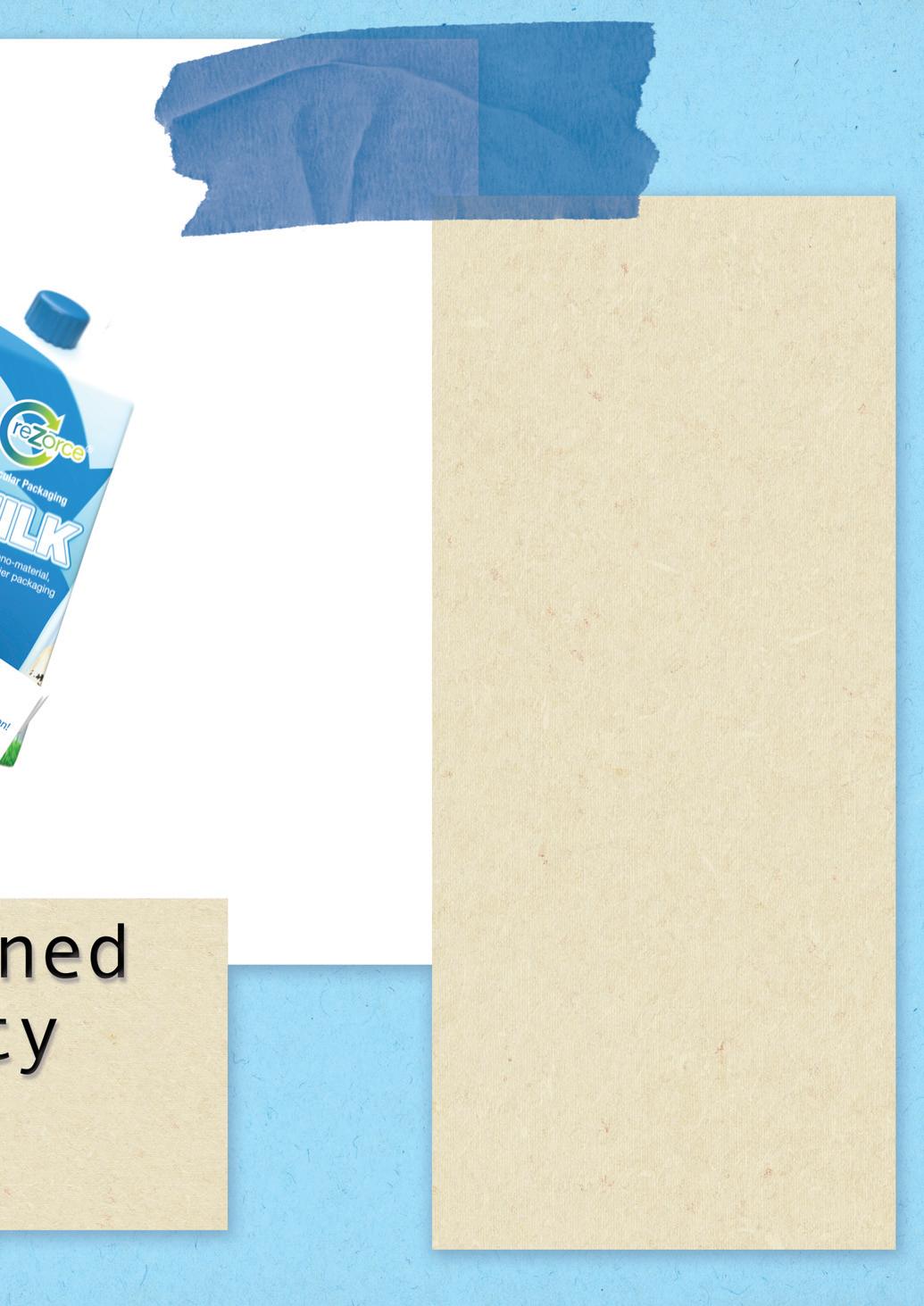
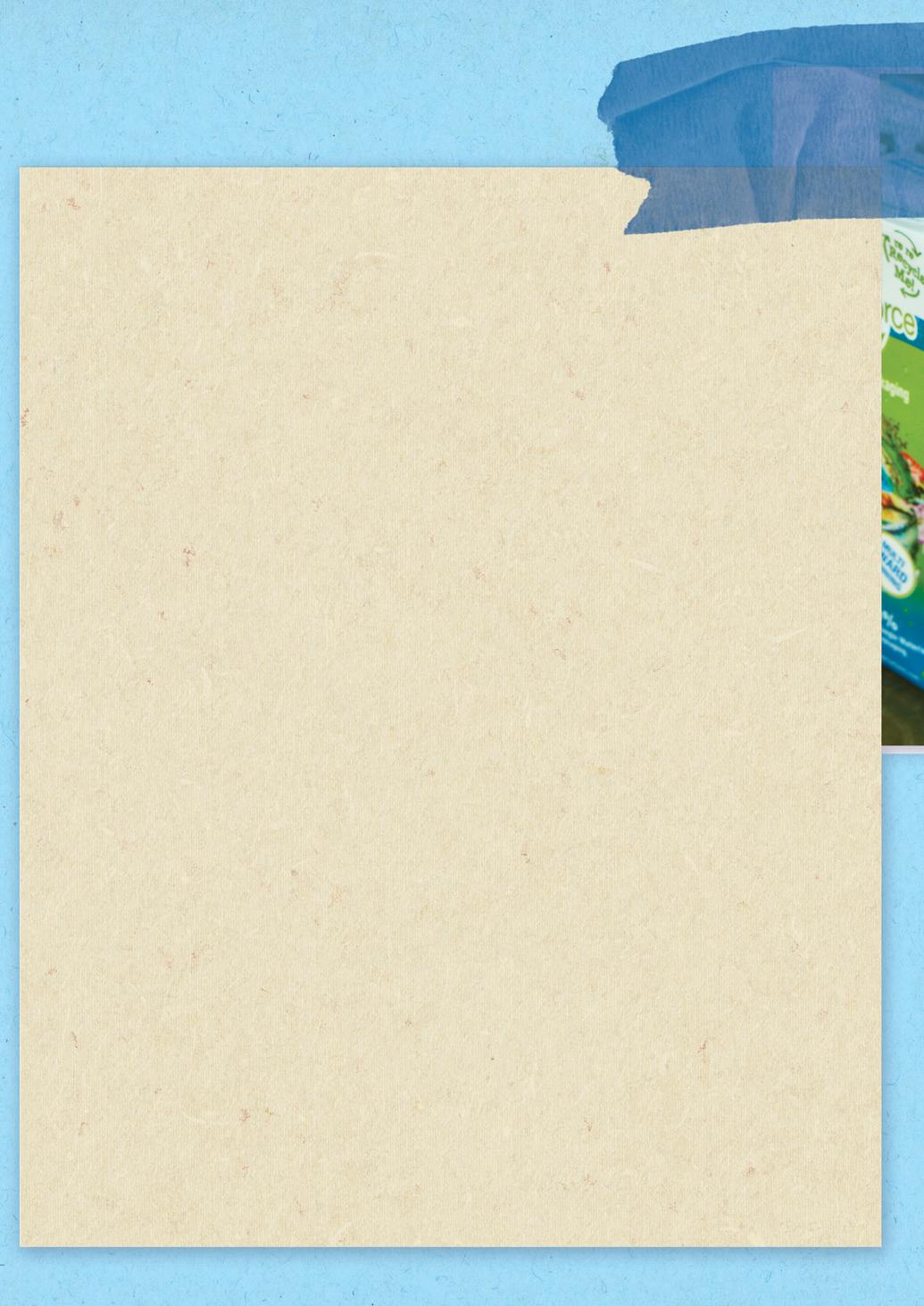
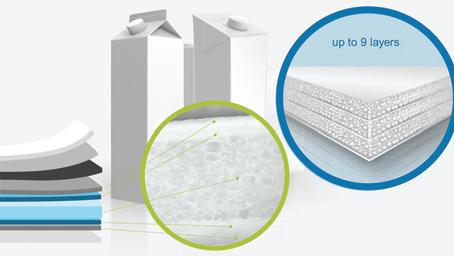
barrier packaging market. The study revealed aseptic beverage packaging as an area in desperate need of more sustainable solutions. Typical barrier packaging in this market consists of layers of different materials – wood fibre, plastic and sometimes foil – bonded together as a composite structure.
“Experts in the sector focus on carbon footprint reduction, which is positive,” Mr Court-Johnston continued. “However, the issue of circularity is not addressed, because the bonded material makeup of the carton is extremely difficult to recycle. So, 90 per cent of the 300 billion beverage cartons consumed every year are incinerated or sent to landfill. This has a huge impact on the environment.”
Introducing ReZorce
Keen to solve this problem, MuCell Extrusion developed a new packaging solution using its patented technology.
“ReZorce is a fully recyclable, monomaterial packaging featuring a food contact barrier,” said Mr Court-Johnston. “By recyclable, we mean circular. Lots of packaging is recyclable by design, but there is a difference between designing
packaging so that it can be recycled, and giving the consumer recycled packaging that is a mono-material.”
The term mono-material means that 95% or more of the packaging is formed using a single material, in this case high-density polyethylene (HDPE), making it easy to recycle across the UK.
To ensure the sustainability of ReZorce, MuCell has utilised its extrusion technology to create a honeycomb structure within the inner layers, which are injected with carbon dioxide. This uses 15-20% less plastic, creating a lightweight and environmentally friendly product.
“This is an industry first,” Mr Court-Johnston explained. “By replacing the plastic polymer with gas, we increase the circularity of the product. A regular plastic carton can go through four or five recycling loops before it becomes too brittle to safely carry produce.
“What we are doing is different. The foamed layer or layers within the core of ReZorce create a natural barrier for oxygen and moisture, due to the tortuous path through the honeycomb structure. We add an additional industry-standard barrier material within the layers to create outstanding barrier performance comparable to aluminium.”
Environmental impact
Through this technology, ReZorce can contain up to 70% recycled material within the inner layers, while using virgin polymer for the food contact outer layer, as mandated by food safety legislation.
A life cycle assessment comparing the environmental impact of a ReZorce carton with a traditional LPB carton of the same size and for the same application demonstrated that the ReZorce carton uses 53% less energy, 51% less water and has a carbon footprint less than half that of the LPB carton.
Zotefoams has also worked closely with R-Cycle, the creators of digital product passports for plastics. All ReZorce cartons feature R-Cycle’s QR codes, ensuring full traceability of the product.
“In a world where greenwashing is prevalent, we are completely transparent,”
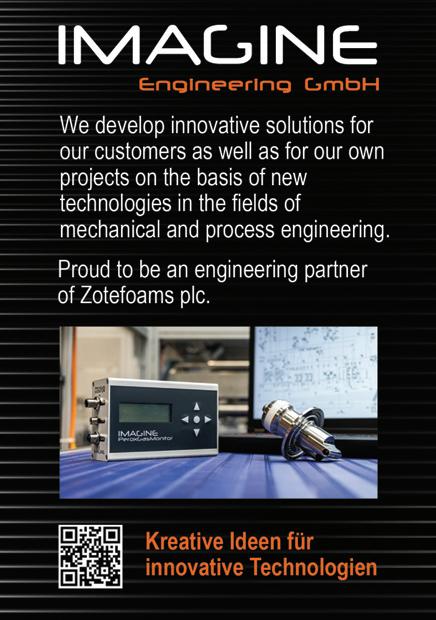
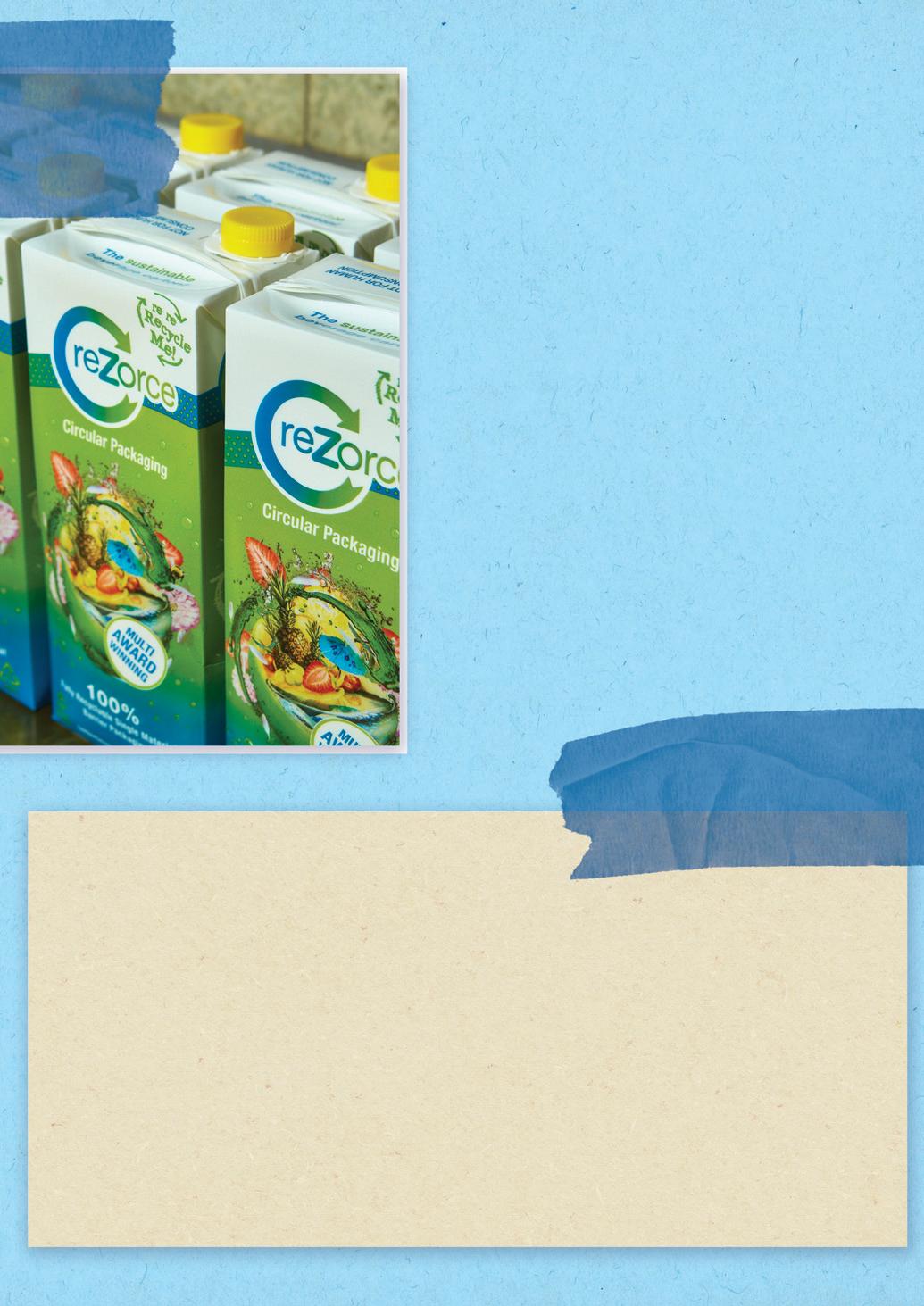
said Mr Court-Johnston. “We want people to hold us accountable for our claims.
R-Cycle’s product passports will be the key differentiator for that.”
The cartons will also feature a digital watermark, making it simple for companies like Biffa (the UK’s number one recycler) to identify the materials used in the cartons. This allows sorting of ReZorce into dedicated fractions rather than mixed plastics, to enable production of the high-quality
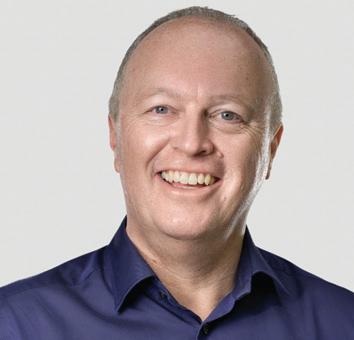

recyclate necessary for the circular economy. Zotefoams has partnered with Biffa to validate the closed loop and recycled nature of ReZorce.
“During development, we worked closely with the recycling industry testing lots of different technologies,” Mr Court-Johnston continued. “The main challenge was making ReZorce’s journey accessible, and R-Cycle was the most user-friendly route possible.”
What next?
In July 2023, Zotefoams partnered with Refresco, the world’s largest independent packer of beverages for retailers and A-brands, to further develop ReZorce and conduct market trials with a major European retailer.
“We have agreed a desired outcome with Refresco, so that following the trial, we will roll out and scale up production,” said Mr Court-Johnston. “We already have a pipeline of a billion apple and orange juice cartons, in both large and small por -