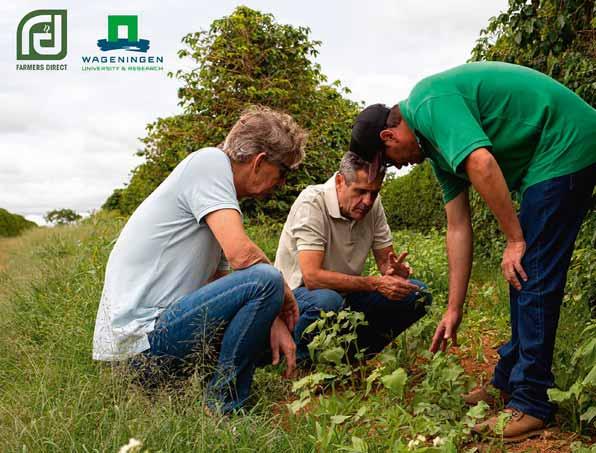
31 minute read
Column
NIEUWE BELGISCHE PET- RECYCLINGFABRIEK
Recycler Morssinkhof-Rymoplast Groep heeft een 9-jarig contract binnengehaald voor de recycling van PET-schaaltjes en -flessen in een nieuwe fabriek in het Belgische Neufchâteau. Morssinkhof-Rymoplast zou naar verluidt € 30 miljoen in het project hebben gepompt. PET-flessen en -schaaltjes worden dan gerecycled tot secundaire grondstoffen om in te zetten voor de productie van nieuwe schaaltjes en flessen. (Bron: Fost Plus)
CAPTAINS OF PROCESSING DINNER
Op 12 mei organiseert Machevo met partners Easyfairs en vakblad Bulk wederom een netwerkdiner. Dit ‘Captains of Processing Dinner’ in de Evenementenhal in Gorinchem is exclusief voor de directie en het management van Machevo-leden. Naast gegeten wordt er ook gediscussieerd onder leiding van een breed samengesteld opiniepanel uit de branche.
KLIMAATREKENTOOL VOOR KOFFIEKETEN
Wageningen University & Research en FarmersDirect Coffee hebben ’s werelds eerste CO2-calculator ontwikkeld die de klimaatafdruk van de koffieketen berekent. De rekentool die in mei af is, combineert de CO2 impact voor elk onderdeel van de keten om vast te stellen hoe duurzaam de koffie geproduceerd is. Het gaat drie jaar duren om alle gegevens van koffieboeren in de productieketen volledig in te voeren met deze methodiek. Streven is de CO2-impact volledig inzichtelijk te hebben voor 2025. Ook het industriële proces wordt erin meegenomen, zoals het vervoer en het branden van de bonen. Via een QR-code op de verpakking is straks onder meer te zien welke route de koffie heeft afgelegd en wat de CO2-voetafdruk van de koffieketen is. Het gaat nadrukkelijk om koffie die via Farmers Direct Coffee is ingekocht. Achter dit initiatief zitten ondernemers die de koffieketen willen innoveren en verduurzamen met een eerlijke prijs voor de boer én voor de markt. Met behulp van data en blockchain helpt FarmersDirect Coffee boeren aan lagere kosten en een betere oogst. In Nederland koopt Boni Supermarkten sinds februari bonen in bij FarmersDirect Coffee voor het eigen koffiemerk. Michiel van Mourik (45) en Daan Mulder (22), oftewel Buurman & Buurman, R&D en test engineers bij Van Beek
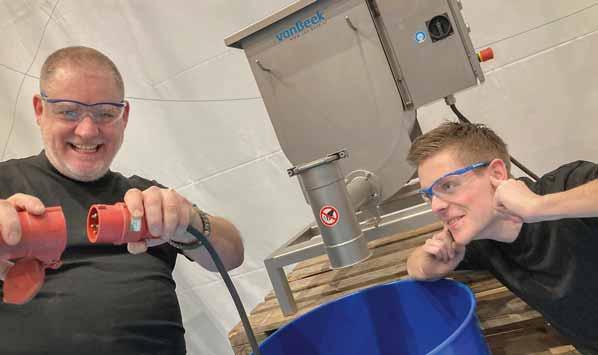
R&D TALK JONG TALENT BELANGRIJK VOOR TOEKOMST VAN BEEK
Door jong talent te mixen met ruime ervaring wordt Van Beek als bedrijf toekomstbestendiger. In het R&D team zorgt de balans tussen jong en oud ervoor dat sparren, kruisbestuiving en persoonlijke ontwikkeling naar een hoger niveau worden getild.
Wie de jeugd heeft, heeft de toekomst. Voor sommigen een clichématige dooddoener, maar voor een toekomstbestendig bedrijf een absolute noodzaak. Wie het aandurft om jong talent binnen de organisatie te mixen met ruime ervaring, krijgt daar het beste van twee werelden voor terug. En toch is dat makkelijker gezegd dan gedaan. Wij mensen hebben er namelijk een handje van om bij het minste geringste vol op de rem te trappen: ‘Hoezo veranderingen doorvoeren, alles verloopt toch prima?’ Nou, nee. Ze zijn zich er veelal niet van bewust, maar oudere werknemers zitten vaak vastgeroest in een patroon. In het ergste geval zijn ze ‘intern gepensioneerd’. Er vindt misschien nog wel innovatie plaats op nieuwe producten, maar niet wat betreft nieuwe productiewijzen.
Jongeren daarentegen zijn onbevangen, komen met frisse ideeën van school. Het zijn enthousiaste energiebommen, ze willen juist vernieuwen en brengen hernieuwde, efficiënte methoden mee. Het is vervolgens aan de door de wol geverfde collega’s binnen het bedrijf om ze te helpen het geleerde in praktijk te brengen. En dat is eigenlijk precies hoe het er bij ons aan toegaat: we vormen als R&D team een twee-eenheid, weten waar de ander goed in is, staan open voor elkaars input en vullen elkaar aan.
Nu draait het bij Research & Development natuurlijk ook om vernieuwing. Ergens tegenaan schoppen en verandering teweegbrengen, is gewoon ons werk. We noemen onszelf ook wel gekscherend de Buurman en Buurman van Van Beek! Natuurlijk kan een leeftijdskloof op de werkvloer ook verstorend werken voor de harmonie en productiviteit, deels aangewakkerd door een heersende bedrijfscultuur of jezelf groter willen maken dan de ander. Daar is bij ons geen sprake van. De balans tussen jong en oud zorgt er bij ons juist voor, dat sparren, kruisbestuiving en persoonlijke ontwikkeling naar een hoger niveau worden getild. En laten we eerlijk zijn: naast dat we elkaar voorzien van een flinke dosis kennis en energie, is het natuurlijk beregezellig!
Michiel van Mourik (45) en Daan Mulder (22) R&D en test engineers, Van Beek
WETGEVING ZIT NIEUWE CIRCULAIRE FABRIEK IN DE WEG
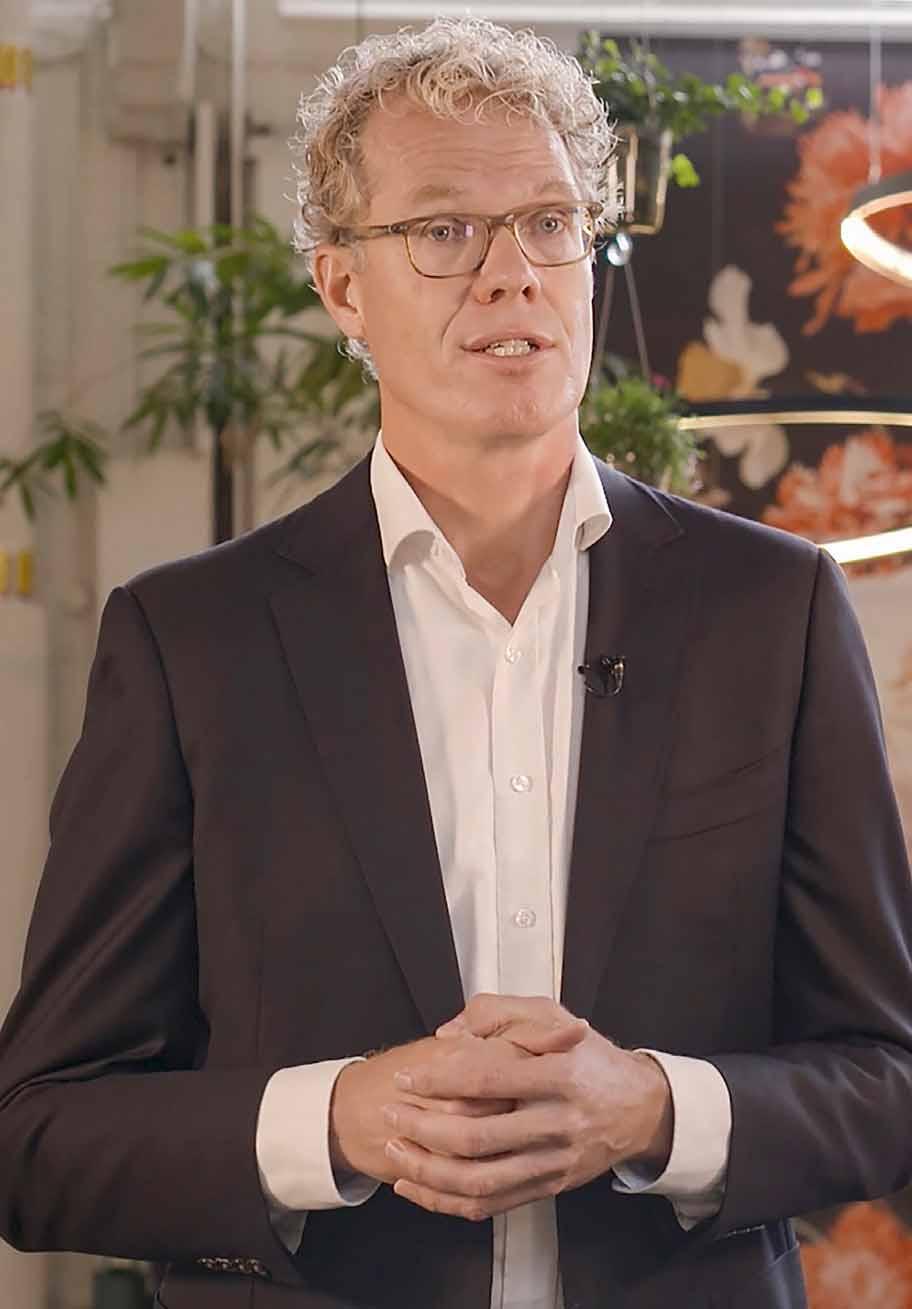
Black Bear Carbon loopt tegen de hindernissen van de circulaire economie aan. De producten van het bedrijf zijn wettelijk gezien afval. De vergunning voor een nieuwe fabriek laat op zich wachten. CEO Victor Vreeken blijft optimistisch.
Op de website van de omgevingsdienst in ZuidLimburg met de koepelvergunning voor de Chemelot site in Geleen staat het mapje voor Recovered Carbon Black Nederland (rCBNL) al klaar. Maar begin januari 2022 is het nog leeg. Het bedrijf, dat getooid is met de marktnaam Black Bear Carbon, heeft zijn deel van de vergunning weliswaar rond, maar het wacht nog op de uitspraak van bezwaarprocedures.
WELWILLEND Intussen had de bouw van een fabriek om carbonblack en olie uit granulaat van autobanden terug te winnen, najaar 2021 al moeten zijn gestart. De provincie als bevoegd gezag staat welwillend tegenover de komst en de Chemelot-organisatie ziet het bedrijf als een aanwinst voor de Europese circulaire hub die het chemiecomplex wil worden.
Het herwonnen carbon-black (rCB) – dat stevigheid geeft aan rubber – is een nuttig ingrediënt voor nieuwe autobanden, uiteenlopende rubbertoepassingen en als pigment in verf en plastic. Eerdere tests bij verf- en bandenproducenten lieten prima resultaten zien. Het pyrolyseproces dat het bedrijf toepast, levert bovendien een kwaliteit olie op die geschikt is als brandstof maar ook in de raffinage van aardolie inzetbaar is. Het bedrijf, dat op Chemelot jaarlijks zo’n 12.000 ton rCB en 14.000 ton pyrolyse-olie wil gaan produceren, is met een groot aantal potentiële klanten in gesprek. De fabriek vergt een totale investering van zo’n 100 miljoen euro. Het bedrijf krijgt al financiele steun van InvestNL en Chemelot Ventures.
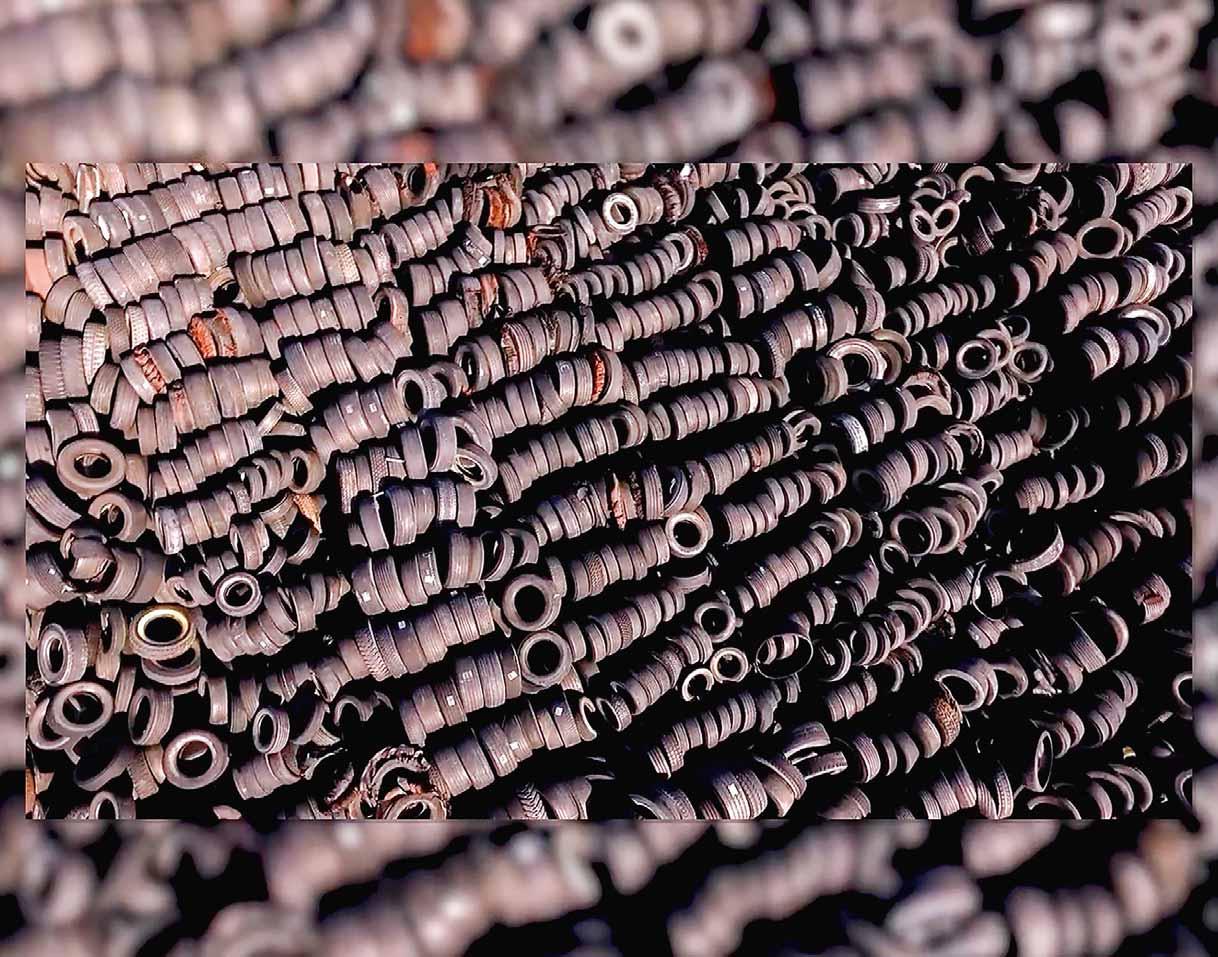
Black Bear Carbon gebruikt pyrolyse om afgedankte vrachtwagenbanden te verwerken tot koolstofgranulaat, olie en gas.
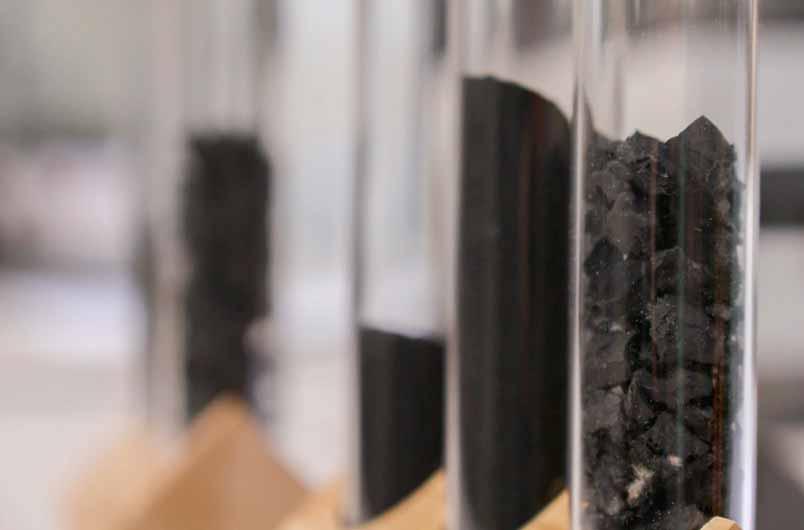
PROTEST Een plaatselijke natuurorganisatie heeft echter – als enige – protest aangetekend tegen de ontwerp-vergunning. Zo zou de fabriek niet veilig bedreven kunnen worden en is er geen functionele binding met de andere Chemelotbedrijven, zoals de koepelvergunning voorschrijft. De plannen van Black Bear Carbon om in Rotterdam een nieuwe fabriek te realiseren, liepen vorig jaar op niets uit, omdat vanwege de onvoldoende stikstofruimte in het gebied de lange weg naar een natuurvergunning nodig was. Externe financiers dreigden in dat geval af te haken. De koepelvergunning van Chemelot biedt deze ruimte wel, maar uitsluitend daarom zou het bedrijf naar Zuid-Limburg willen komen, aldus de zienswijze van de lokale natuurorganisatie. De omgevingsdienst moet hier nu op reageren, waarna het ontwerpbesluit nogmaals zes weken ‘voor beroep’ ligt. Daarna wordt de vergunning pas definitief en onherroepbaar.
IMAGO De maandenlange vertraging zorgt voor flinke teleurstelling bij Black Bear Carbon CEO Victor Vreeken. “Natuurlijk nemen we deze bezwaren serieus, maar ik heb er alle vertrouwen in dat we er op een goede manier uitkomen. Ons doel is een professionele chemische procesinstallatie neer te zetten, die aan alle veiligheidsstandaarden voldoet. Chemelot is een toplocatie in Nederland en hanteert extra strakke regels.” Het bedrijf wil zich nadrukkelijk onttrekken aan het slechte imago dat de brand in een proeffabriek in Nederweert in 2019 met zich meebracht. “De oorzaak van deze calamiteit had volgens onderzoek niets van doen met onze pyrolysetechnologie, maar alles met de middelen die ons destijds ter beschikking stonden en de randvoorwaarden die dat tot gevolg had voor het veiligheidsmanagement. Inadequaat? Nee, zo zou ik het niet willen noemen. Het was wel een belangrijke les. Alle conclusies uit het onderzoeksrapport zijn in de nieuwe fabriek geadresseerd. In Geleen krijgen we een eigen kavel tot onze beschikking, nu nog een leeg grasveld. We kunnen de installatie van nul af aan gaan opbouwen, zodat een veilige bedrijfsvoering is geborgd”, zegt Vreeken.
PROCES Black Bear Carbon timmert al meer dan tien jaar aan de weg met zijn verwerkingstechnologie voor afgedankte auto- en vrachtwagenbanden. Dat proces omvat een aantal stappen. Eerst wordt het staal uit de banden verwijderd. Deze voorbewerkingsstap, die in Nederweert voor veel overlast zorgde, is niet meer nodig. “Er zijn leveranciers genoeg, die daar heel goed in zijn”, vertelt Vreeken. “We verwerken alleen het granulaat.” In het pyrolyseproces wordt het granulaat in een lange reactor zuurstofloos verhit op 500-700˚C. Het rubber valt in de carboniseerstap in kleinere moleculen uiteen, met olie en gas als bijproduct. Het gas wordt verbrand in een gasmotor om elektriciteit voor het proces op te wekken. In banden zitten verschillende gradaties van carbon-black. Deze zwarte koolstof wordt vermalen en ondergaat vervolgens nog een pelletiseer- en droogstap tot een robuuster en beter te handlen eindproduct. “We zijn uiterst selectief in de feedstock die we kiezen. Voorlopig gebruiken we uitsluitend vrachtwagenbanden. Door voor deze stroom te kiezen, kunnen we een hoogwaardige productkwaliteit garanderen”, zegt Vreeken. “Dat maakt het ook niet meteen een goedkope technologie. Dit proces willen we verder opschalen. We zijn geen autobandenrecycler maar een circulair productiebedrijf. Dat geldt ook voor de olie die maken. We willen topproducten leveren van hoge kwaliteit.” ●
Wetgeving grootste obstakel
De verouderde en onduidelijke wetgeving zit Black Bear Carbon danig in de weg. Ondanks de nuttige circulaire bestemmingen kleeft aan recovered carbon-black (rCB) en ook aan de gewonnen pyrolyseolie het wettelijk predicaat afval. Dit hardnekkige euvel is al langer bekend en geldt voor tal van secundaire productstromen. De Europese wetgeving is nog grotendeels gericht op de lineaire economie en houdt weinig rekening met circulaire innovatie. Bepalend is de ‘afvalstatus’ in de Europese Kaderrichtlijn Afvalstoffen, in Nederland geïmplementeerd in de Wet milieubeheer. Wezenlijk voor rCB is dat het product de ‘einde-afvalstatus’ krijgt. Pas dan is het vrij verhandelbaar en zijn klanten bevoegd het product in te nemen als grondstof voor hun processen. Voor Black Bear Carbon is zoiets essentieel, ook naar investeerders toe. Tot 2020 konden bedrijven bij Rijkswaterstaat, de uitvoeringsorganisatie van het ministerie van Infrastructuur en Waterstaat, een ‘Toetsing afval of grondstof’ doen. Rijkswaterstaat oordeelde dan of een verwerkt materiaal de einde-afvalstatus kon krijgen, wat bedrijven rechtszekerheid bood. De overheidsorganisatie neemt echter geen nieuwe aanvragen meer in behandeling vanwege capaciteitsgebrek en verwijst naar de regionale omgevingsdienst. Deze stelt op haar beurt geen uitgaande stromen te mogen beoordelen volgens de richtlijnen van datzelfde Rijkswaterstaat. Vanwege deze onduidelijke en onwerkbare situatie heeft Black Bear Carbon nu voor alle overheidsniveaus zelf een verklaring opgesteld om uit te leggen waarom het product de einde-afvalstatus zou moeten krijgen. Een van de argumenten is dat het rubbergranulaat als erkend product al wordt toegepast in kunstgrasvelden. Daarmee is het geen afval meer. Het ministerie heeft dan wel aangegeven mee te willen denken over een oplossing, maar tot nu toe heeft het nog geen actie ondernomen en zo blijft deze impasse in stand.
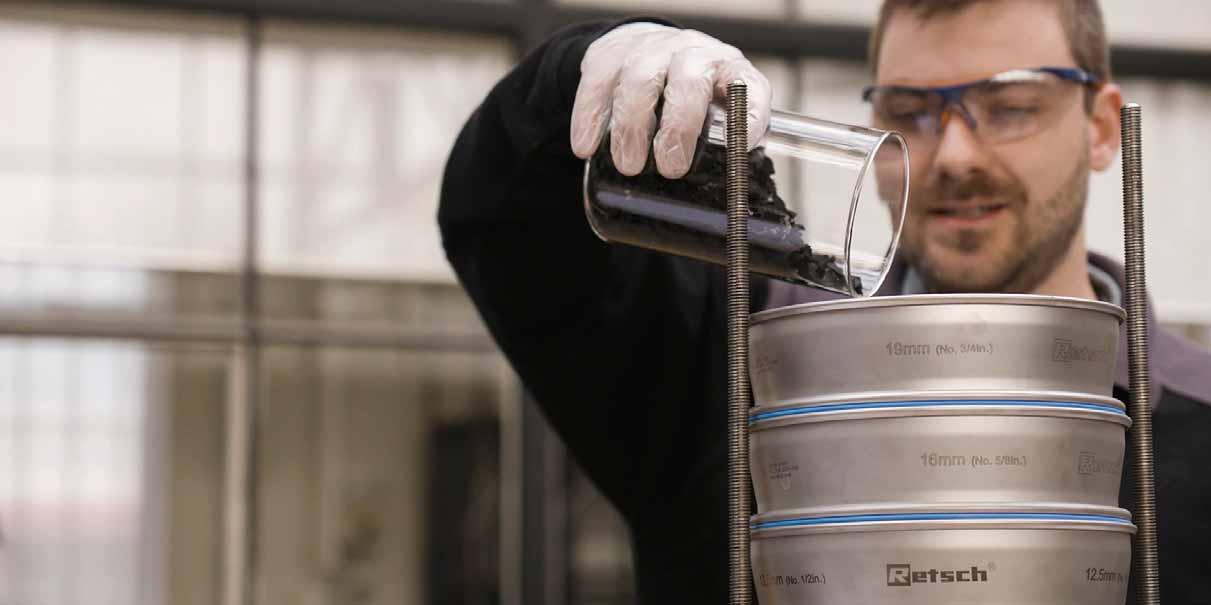
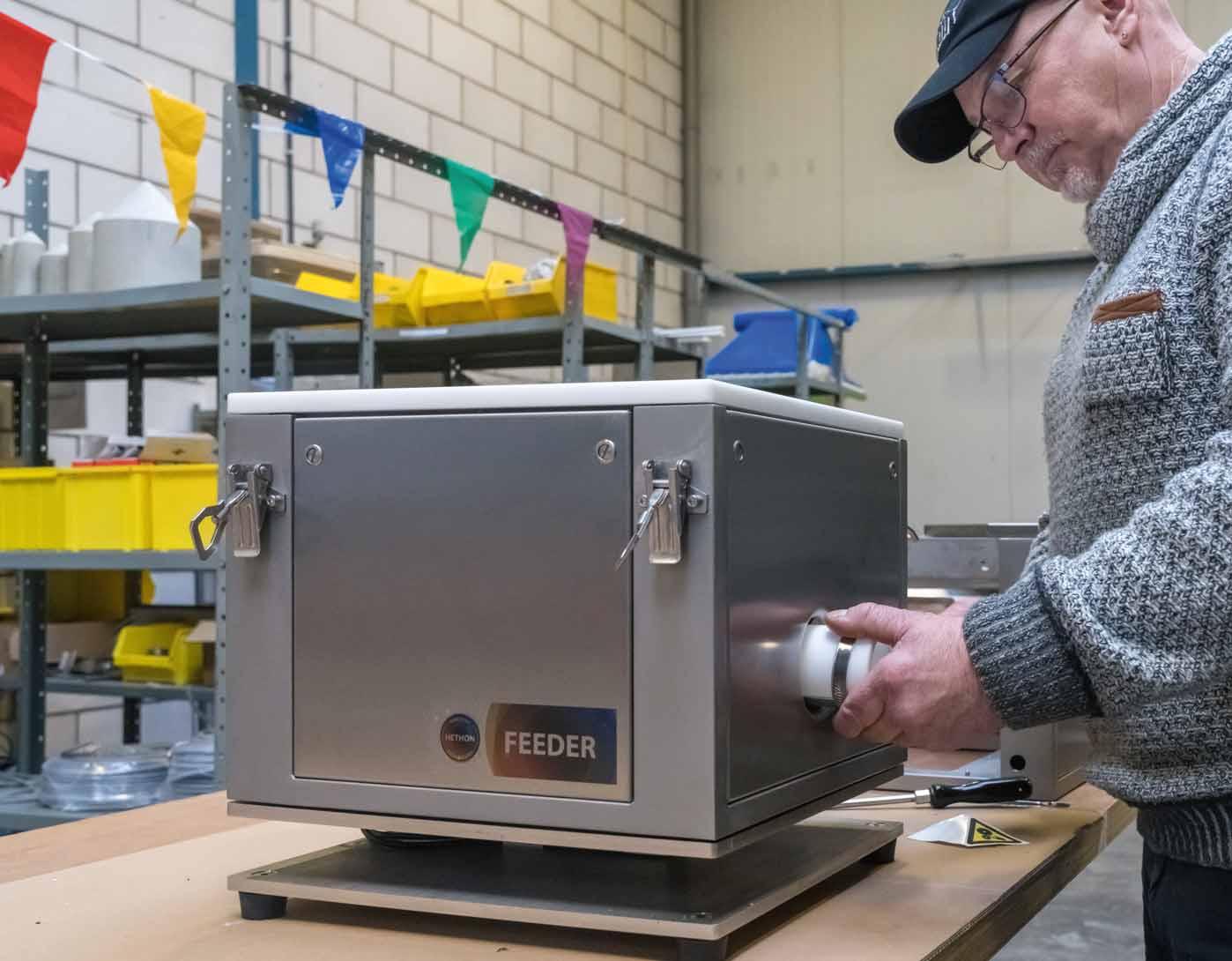
Oplossing voor lastige poeders HOPPER MET FLEXIBELE WAND DOSE
Een hopper met flexibele wand is een betere oplossing voor het doseren van kleverige poeders en mengsels van ingrediënten met een verschillende massa dan een trilgoot of doseertrechter met woelarmen.
Om ‘lastige’ poeders te doseren worden vaak trilgoten ingezet, of feeders met woelarmen die de poeders of granulaten gelijkmatig van de trechter naar de schroef of vijzel moeten transporteren. Dit werkt lang niet altijd goed. Poeders zonder natuurlijke flow kunnen aan de armen blijven vastkleven, bruggen en holtes vormen, compacteren en ontmengen. Het gevolg is dat de toevoer naar de schroef of vijzel hapert. De oplossing voor dit soort problemen is een hopper met flexibele wand. In deze hopper worden lastige poeders met mechanisch beweegbare peddels vanaf de buitenkant van de doseertrechter, die is gemaakt van buigzaam polyurethaan (PU), naar de schroef toe ‘gemasseerd’. Zo wordt het poeder gelijkmatig naar de schroef gevoerd, zonder beschadigd te raken.
LEVENSMIDDELENINDUSTRIE Vanwege onder andere dit type feeders is fabrikant Hethon in Doetinchem al decennia een bekende naam in feeders. De apparaten vinden wereldwijd hun weg naar onder andere spuitgietbedrijven, glasfabrieken, waterzuive-
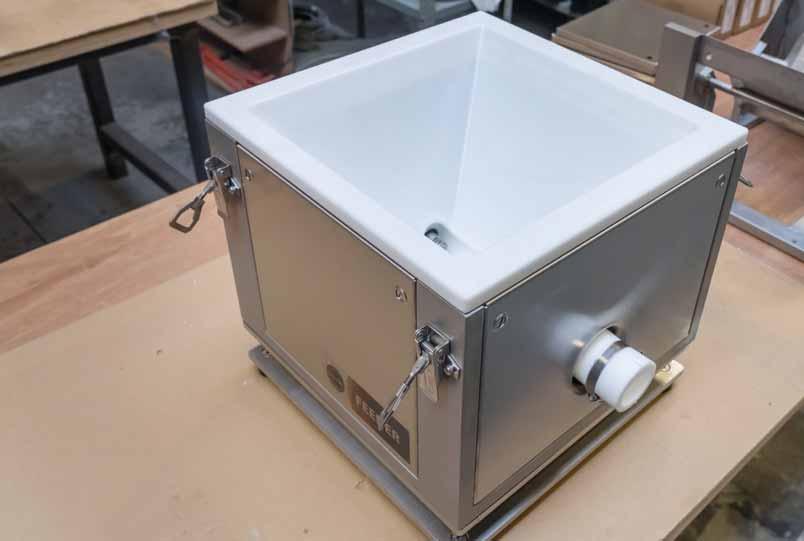
André Danen bouwt een Hethon feeder met flexibele wand, weging en besturing samen in de werkplaats in Doetinchem. Omdat de wand flexibel is, kan hij van buitenaf mechanisch ‘gemasseerd’ worden. Dit voorkomt brugvorming, compactering en ontmenging van het poeder in de feeder.
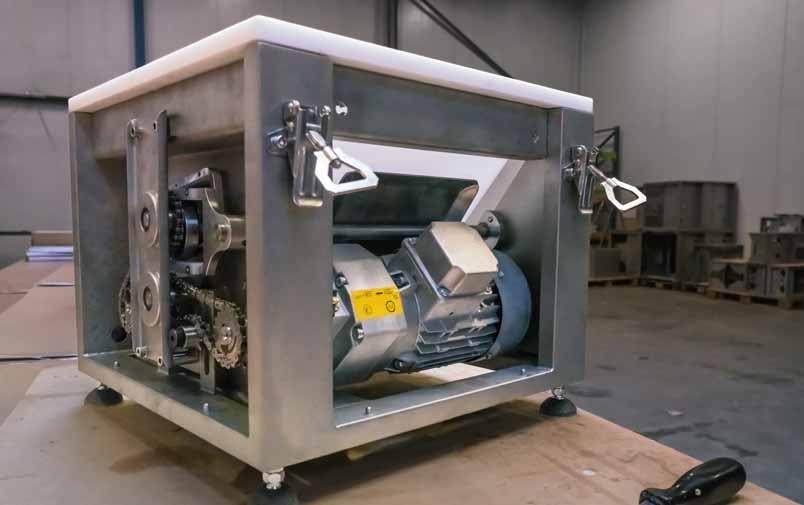
De motor die de mechanische peddels aan de buitenzijde van de wand aanstuurt.
ERT ZONDER HAPEREN
ringsbedrijven en worden zelfs bij crematoria en een fabrikant van vliegtuigmotoren gebruikt. “Maar de meeste klanten”, zegt eigenaar Brenda Kesteloo, “zijn levensmiddelenproducenten die er bijvoorbeeld suiker, zout, dextrose, maïzena en citroenzuur mee doseren. Ook bijzonder is, dat we een ATEX-certificaat voor de hele machine kunnen afgeven.”
NAUWELIJKS STILSTAND Directeur en internationaal verkoopadviseur Gerard van Schoten vertelt dat de feeder zo ontbekende verhouding tussen massa en tijd. Gravimetrie werkt iets verfijnder. De feeders doseren dan recept-gestuurd op gewicht. Voor die functie kan communicatie met toevoersystemen zoals een lopende band of extruder als input dienen.” Bijkomende voordelen van gravimetrische besturing zijn de mogelijkheid van datalogging en het feit dat bij deze geautomatiseerde besturingssystemen een wereldwijde back-up van de klant mogelijk is. ●
worpen is dat wisselen van trechters razendsnel verloopt: “De flexibele binnenbak is snel te wisselen en tussentijds te reinigen. Het is een kwestie van de vergrendeling losmaken en wisselen; er is nauwelijks stilstand.” Het gebruik van verschillende trechters voorkomt smaakoverdracht.
GRAVIMETRISCH “Het systeem is uit te rusten met een volumetrische of een gravimetrische besturing”, legt Van Schoten verder uit. “Volumetrisch betekent dat de dosering plaatsvindt op basis van de vooraf
Optimalisering diervoederproductie MEETTECHNIEK MAAKT OPSLAG EN DROGEN EFFICIËNTER
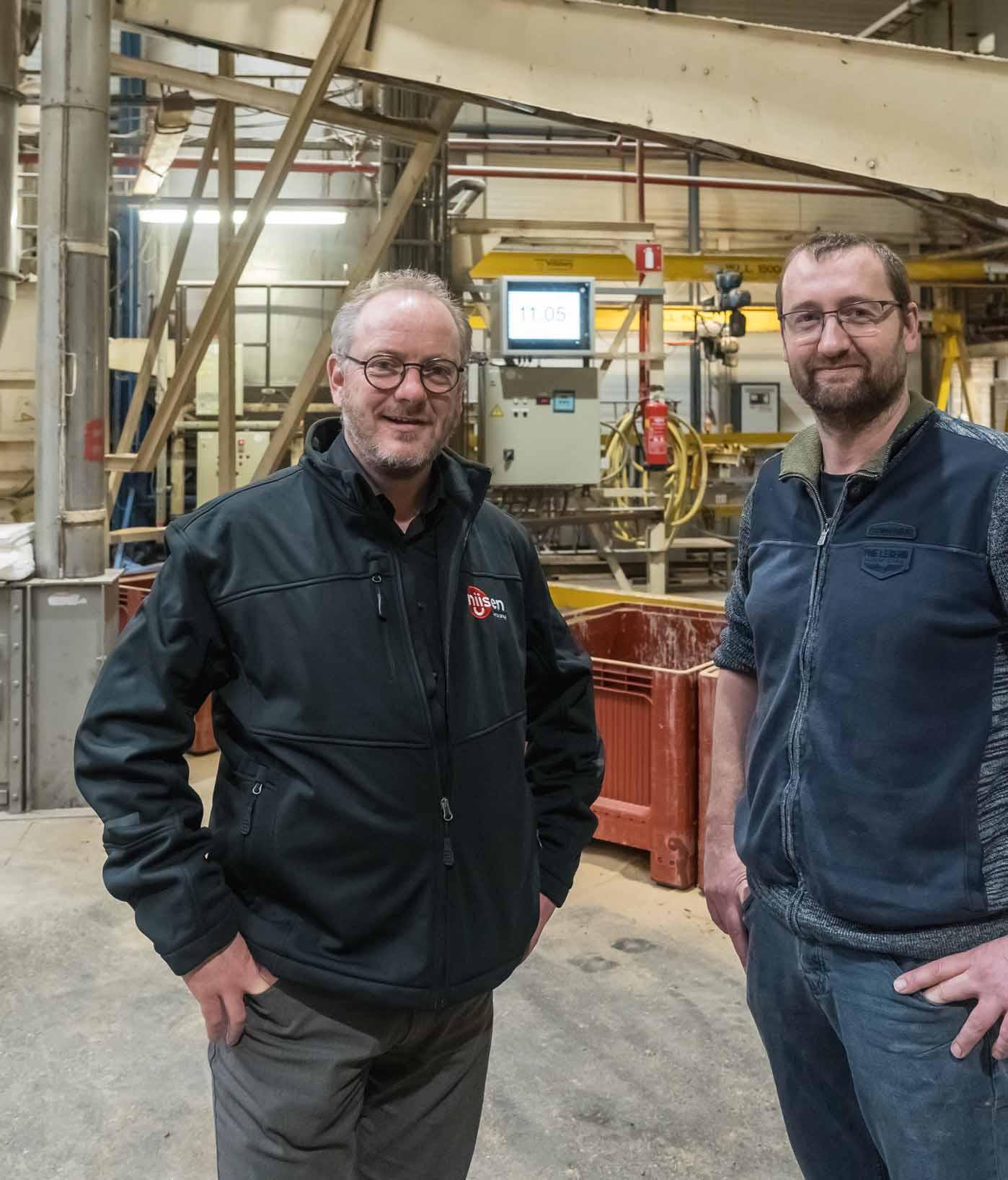
Bij diervoederproducent Nijsen Company optimaliseert een nieuwe valplaatweger het voorraadbeheer van de grondstoffen. Een slimme vochtmeter verbetert de grip op het droogproces.
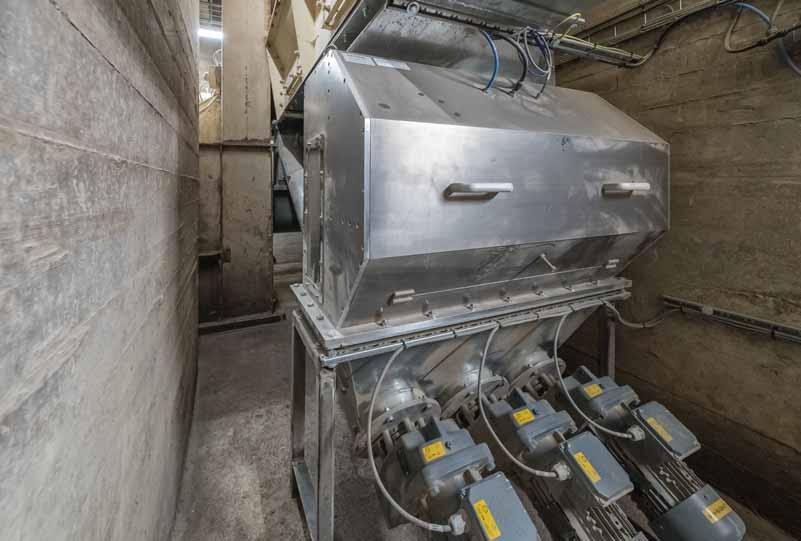
Directeur John Geurts (l) en hoofd technische projecten Paul van den Munckhof van diervoederproducent Nijsen. Om de uiteenlopende grondstofstromen bij Nijsen nauwkeurig inline te kunnen meten, is de Multiflowside-valplaatweger de beste optie.
Nijsen Company beschikt in zijn fabrieken in Veulen onder de rook van Venray over uiteenlopende proceslijnen voor de productie van diervoeders. Naast een traditionele droge diervoederlijn, die grondstoffen als maïs, soja en tarwe verwerkt, ontwikkelde het bedrijf vanaf de jaren negentig een procedé om levensmiddelenstromen uit de voedingsindustrie, zoals brood, koek en snoep, te recyclen.
PELLETS Kleinschalig begonnen vindt de productie inmiddels op industriële schaal plaats. “Op specificatie maken we ook hier basis-ingrediënten voor diervoeder van”, wijst directeur John Geurts op de brede stroom langwerpige zo’n zes millimeter lang korrels die over de band van een van de proceslijnen gaan. “De ingrediënten uit de levensmiddelenindustrie zijn voor ons een grondstof. Het zijn eersteklas voedingsstoffen die voor menselijke consumptie bestemd zijn. Dit is de beste kwaliteit granen, oliën en vetten die je kunt gebruiken.”
GEHEIM “We zijn erin geslaagd al deze uiteenlopende hoogwaardige stromen tot een consistent kwaliteitsproduct te verwerken”, zegt Geurts trots. “Voor de hanteerbaarheid maken we er een pellet van.” Over het productieproces zelf wil Geurts zo min mogelijk kwijt. “Dat is het geheim van de smid. Er zijn heel veel bedrijven die graag willen weten hoe wij dit doen.” De basisprocesinstallaties zijn omgeven door maal- en menglijnen, naast een veertigtal silo’s waarin de grondstoffen worden gebufferd.
VALPLAATWEGER Meten en wegen worden voor het bedrijf steeds belangrijker. De ingebruikname van een nieuw automatiseringssysteem was aanleiding voor Nijsen om in de processen en bij het innamepunt voor de grondstoffen extra meettechnologie in te bouwen. Bij de grondstofinname heeft het bedrijf sinds kort een Multiflowside-valplaatweger (MFS) in gebruik. Trucks rijden af en aan met nieuwe grondstoffen. “We wilden bij het brengstation een goed inzicht krijgen in de exacte tonnages die richting de silo’s gaan”, vertelt hoofd technische projecten Paul van den Munckhof. “Hiervoor hadden we helemaal niets op dit vlak. De enige ruwe data die we hadden, kwamen van de weegbrug waar de vrachtwagens overheen gaan.” Met de MFS wil Nijsen zijn voorraadbeheer optimaliseren. Ook is het bedrijf in staat grondstoffenstromen zo nog beter te traceren. Bij de grondstoffen die Nijsen verwerkt, spelen geen factoren als stofgevoeligheid (ATEX) en risico op aanhechting of brugvorming in leidingen en installaties. Dat laatste zou een negatief effect hebben op een goede valplaatweging.
Paul van den Munckhof, Nijsen
BIJZONDERE EISEN Aan de valplaatweging worden bijzondere eisen gesteld. Er moeten immers telkens andere grondstoffen worden gewogen. “We hadden een apparaat nodig dat nauwelijks gevoelig is voor veranderingen in de dichtheid of korrelgrootte van de grondstof. Een gewone impact-flowweger voldoet niet, want die moet je kalibreren op één product met een bepaalde dichtheid of omvang. Als er dan een grondstof met andere eigenschappen in de buffering komt, dan moet je zo’n meter opnieuw kalibreren. Dat werkt bij ons niet, want we hebben hier zo’n honderd verschillende grondstoffen en er gaan vele tonnen per uur doorheen. Om
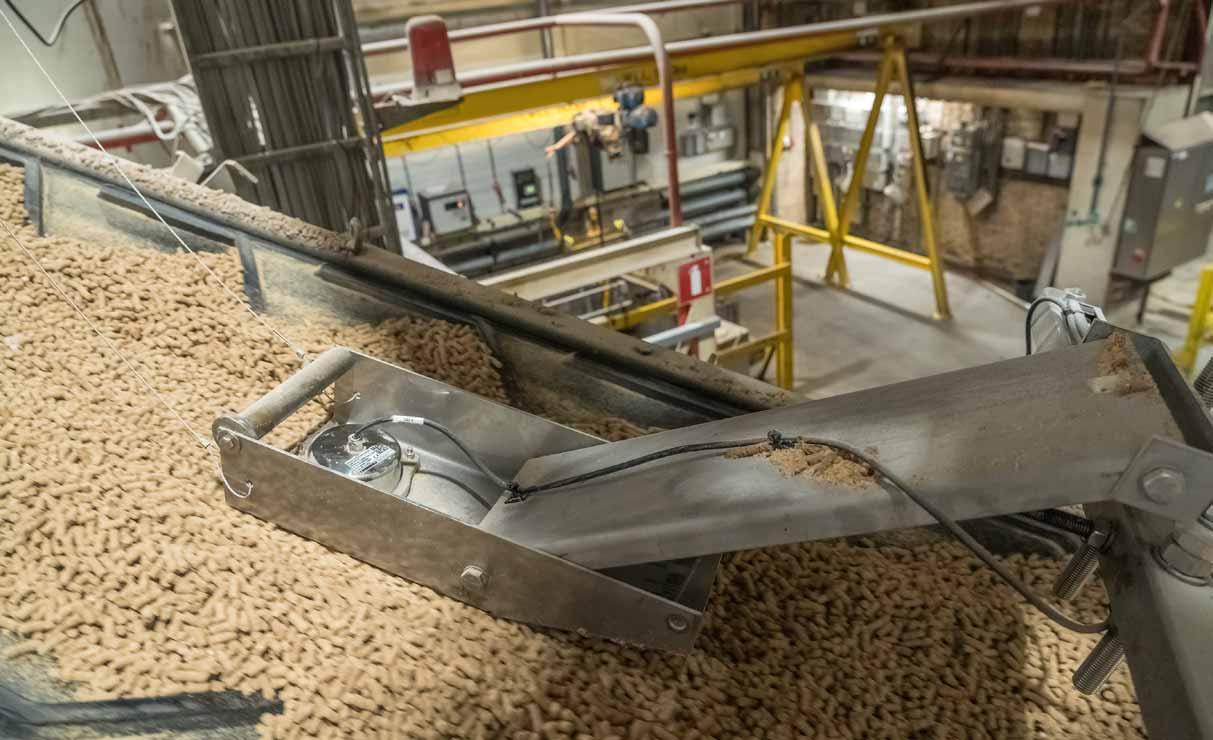
Vlak voor de droogoven gaat de stroom vochtige diervoederpellets onder een stalen bak door voor een vochtmeting.
nauwkeurig inline te kunnen meten, is een valplaatweger de beste optie.”
NAUWKEURIG Met dit type MFS van leverancier Dosco is Nijsen in staat op een constante volumestroom te meten, ook bij steeds wisselende grondstoffenstromen. “De weger meet op enkele tientallen kilo’s af wat er aan grondstof naar de silo gaat en is zo nauwkeurig genoeg voor het doel waarvoor we hem willen gebruiken. Of we nou maïs, bietenpulp of een andere grondstof meten, we zitten altijd goed. De afwijkingen zijn minimaal, ongeacht de grondstof die we bufferen. We zijn weer een stukje slimmer geworden”, zegt Van den Munckhof.
VOCHTMETING Aan het begin van de voedselrecyclinglijn zijn grote machines in bedrijf die de verpakte levensmiddelen efficiënt van hun plastic ‘jasje’ ontdoen.
Multiflowslide mikt puur op massa
Sinds de introductie van de Multiflowslide-valplaatweger (MFS) in 2010 heeft Dosco zo’n honderd apparaten afgezet in de procesindustrie in Nederland. Door de ontwikkeling van nieuwe elektronica is de nauwkeurigheid van de MFS, die direct in de materiaalstroom meet, verder verbeterd. De valplaatweger – ook wel centriputaalweger genoemd – meet de impact van stortgoed over een cirkelvormige weegplaat in het systeem. Op de valplaat wordt het materiaal van richting veranderd. Met een loadcell wordt de middelpuntzoekende kracht gemeten. Deze kracht is recht evenredig met de massa stroom. De impact wordt naar de bijbehorende elektronica omgezet, die de productstroom in kilogrammen per uur plus de gepasseerde hoeveelheid presenteert op het bedieningsdisplay. De Multi flowslide is bij uitstek geschikt voor het meten van vrij stromende, niet klevende materialen, zoals kunststofkorrels, granen en goed lopende poeders. Mocht het product een lichte neiging hebben om zich af te zetten, dan kunnen in de valplaatweger luchtsproeiers worden geïntegreerd. Deze zorgen voor een elektronisch gestuurde, automatische reiniging van het meetpad. Volume is de belangrijkste parameter voor de valplaatweging, niet het gewicht van de stof die er doorheen gaat. De MFS van Dosco kan een bulkdichtheid van 0,03 tot 4,5 kg/l aan in capaciteiten van 0,5 tot 300 m3/uur. De valplaatweger bij Nijsen/Granico heeft een capaciteit van 150 m3/uur. De lijst van droge bulkgoederen die succesvol met de MFS kunnen worden gemeten, is inmiddels indrukwekkend, van koffiebonen tot houtsnippers en PET-granulaat.
Paul van den Munckhof, Nijsen
De nutriëntenrijke stromen ondergaan een uitgebreid proces van malen, zeven en persen tot er een vochtig deeggranulaat ontstaat. Aan het eind van dit proces worden de pellets gedroogd. Vlak voor de stroom pellets de droogoven ingaat, vindt voortaan een vochtmeting plaats. De stroom vochtige pellets gaat vlak onder een stalen bak door waarin hightech sensoren van het Litronic-FMS-meetsysteem van Liebherr zijn verwerkt, eveneens geleverd door Dosco. Deze sensor meet tot centimeters diep in de laag pellets continu het exacte vochtpercentage. “Ons product is door het verwerkingsproces al vrij homogeen van samenstelling, maar het vochtgehalte wisselt”, legt Van den Munckhof uit. “We willen het droogproces beter kunnen sturen en beheersen. Hoe nauwkeuriger we het vochtgehalte kunnen vaststellen, des te beter we de droger in kunnen stellen. We kunnen het vochtgehalte nu realtime meten, terwijl de productstroom doorloopt, zodat de droger optimaal zijn werk kan doen. Zo kunnen we ons productieproces verder verfijnen en preciezer afstellen.” ●
‘MET ONZE CONTINUMETING WETEN DE NORM VOLDOEN’
Met continue laserdiffractiemetingen kunnen bedrijven met een milieuvergunning voor het uitstoten van deeltjes zelf nauwkeurige metingen uitvoeren. Omdat de resultaten vrijwel realtime beschikbaar zijn, hoeven ze geen extra marges in te bouwen en weten ze zeker dat ze aan de steeds strengere uitstootnormen voldoen, legt Yves Willems van deeltjesmetingspecialist Optyl uit.
Om te checken of een bedrijf voldoet aan de uitstootnormen, wordt de concentratie deeltjes in de lucht gemeten. Bij deeltjes kan het om van alles gaan, bijvoorbeeld graanstof, PFAS, roet of metaaldeeltjes. “Deeltjes worden altijd gemeten in milligram per normaal kubieke meter ”, opent eigenaar Yves Willems van Optyl in het Belgische Lummen, specialist in deeltjesmeting. Het woord ‘normaal’ slaat daarbij op ‘genormaliseerde omstandigheden’. Dat zijn de standaard uitgangswaarden voor de isokinetische parameters processnelheid, temperatuur, druk en vochtigheidsgraad. De daadwerkelijke metingen worden altijd teruggerekend naar deze genormaliseerde omstandigheden.
AD HOC “Deeltjesmetingen worden gewoonlijk uitgevoerd achter de filters die de uitstoot van stof moeten tegenhouden of in schoorstenen van waaruit de uitstoot plaatsvindt”, zegt Willems. “Het gaat vaak nog om ad hoc-opdrachten aan gespecialiseerde milieubureaus om metingen uit te voeren, maar vanuit de industrie is er steeds meer behoefte aan vaste opstellingen voor deeltjesmetingen die ze zelf continu kunnen uitvoeren.”
DRIE MEETPRINCIPES In de basis zijn er drie meetprincipes die voor deeltjesmetingen kunnen worden toegepast: de elektrodynamische meting, een optische meting en laserdiffractie. Bij de elektrodynamische meting creëert een actieve sensor een elektromagnetisch veld. De veranderingen in dit veld zijn een maat voor stof/deeltjes. De optische methode werkt met een zender en een ontvanger, waarbij het lichtverlies tussen zender en ontvanger de hoeveelheid deeltjes weergeeft. Laserdiffractie werkt ook ongeveer zo, maar dan nauwkeuriger. Daar waar een uitgezonden laserstraal wordt onderbroken door een stofdeeltje, kan deze niet worden opgevangen. Op grond daarvan kan de hoeveelheid deeltjes worden berekend. Het woord ‘berekend’ is daarbij belangrijk: voor alle meetprincipes geldt, dat goede sensoren moeten samengaan met goed overdachte algoritmes om tot gekalibreerde metingen te kunnen komen. Daarvoor moeten de voorbereiding en het meetproces namelijk
Optyl Meet Koffer (OMK)
Willems: “Voor ons toestel, de Optyl Meet Koffer (OMK) die geheel in eigen beheer is ontworpen, ontwikkeld, gebouwd en getest, combineren we isokinetische staalname met laserdiffractie. Het toestel is zelfkalibrerend. De instructies voor gebruik zijn verder zodanig, dat de uitkomst altijd een geldige, bruikbare meting oplevert. Omdat het om een meting gaat die zich elke 15 seconden instelt, is de meting op elk punt in de tijd veel betrouwbaarder omdat de stofconcentratie en alle parameters continu worden gemeten, verwerkt en opgeslagen. Bij de maximaal 1 à 2% afwijking komt niemand in de wereld in de buurt.”
Het woord ‘koffer’ is trouwens niet altijd van toepassing, want Optyl kan de methodiek binnenkort ook als vaste meetopstelling leveren. Er zijn vier klantgroepen: filterfabrikanten die hun filters willen testen, universiteiten en onderzoeksinstellingen die zo betrouwbaar mogelijk willen meten, industriebedrijven die hun uitstoot zorgvuldig willen monitoren en milieudienstverleners die de industrie bedienen. volgens nauwkeurig omschreven voorschriften verlopen. Het filter in het meetsysteem wordt voor de meting gedroogd en gewogen en na de meting nogmaals gedroogd en gewogen.
ONNAUWKEURIG EN LANGZAAM “Het probleem is”, zegt Willems, “dat de relevante parameters bij de kalibratiemetingen door milieulaboratoria maar op twee punten in de tijd worden gemeten, namelijk voor en na de meting. Omdat die parameters continu iets wijzigen, moet er rekening worden gehouden met 30% onnauwkeurig-
BEDRIJVEN ZEKER DAT ZE AAN
Yves Willems, directeur van Optyl, specialist in deeltjesmeting.
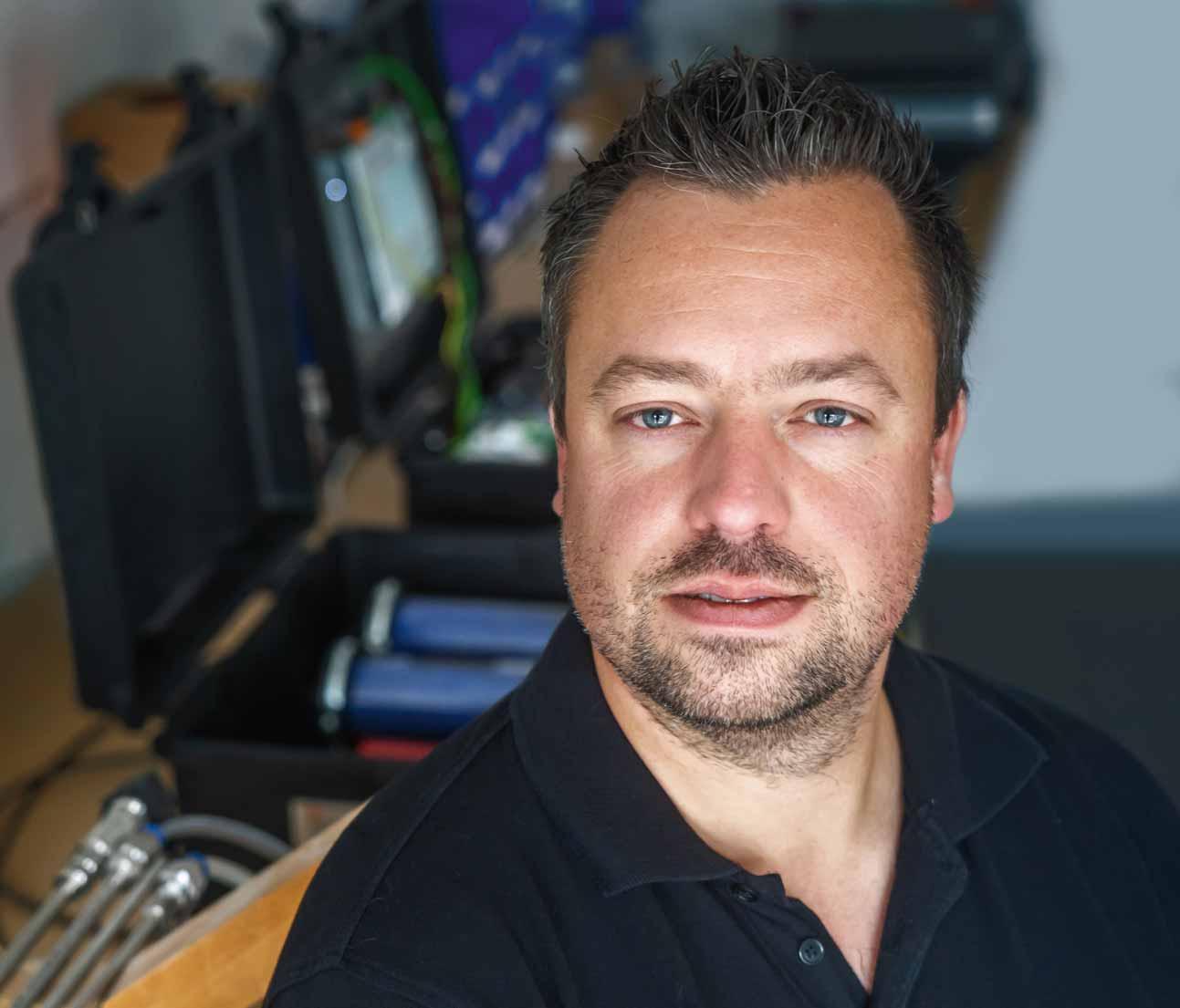
heid in dergelijke metingen. Daar komt nog bij dat de resultaten van eenmalige metingen vaak twee tot drie weken op zich laten wachten.”
SNEL EN BETROUWBAAR “Bij een continumeting die naast de deeltjesmeting tegelijk ook de isokinetische parameters constant terugrekent naar de normaalwaarden, is dat de onnauwkeurigheid maar 1 tot 2%”, legt Willems uit. “Dat resultaat is niet alleen betrouwbaar, maar ook met slechts twee seconden vertraging beschikbaar.” Voor bedrijven maken betrouwbaarheid en snelheid in de meetresultaten nogal een verschil. Willems: “Nu de uitstootnormen zo streng zijn geworden, bijvoorbeeld van 50 mg/m3 voorheen naar 5 mg/m3 nu, is elke extra milligram beperking heel moeilijk te bereiken – en dus kostbaar. Met een afwijking van 30%, uit kalibratiemetingen die slechts met grote tussenpozen beschikbaar komen, moet voor de zekerheid nog een flinke marge worden aangehouden om de norm niet te overschrijden. In de praktijk zullen bedrijven die volgens de regels 5 mg mogen uitstoten, daarom 4 mg moeten aanhouden. Maar met de veel betrouwbaarder continumeting weten ze zeker dat ze binnen de normen blijven.” ●
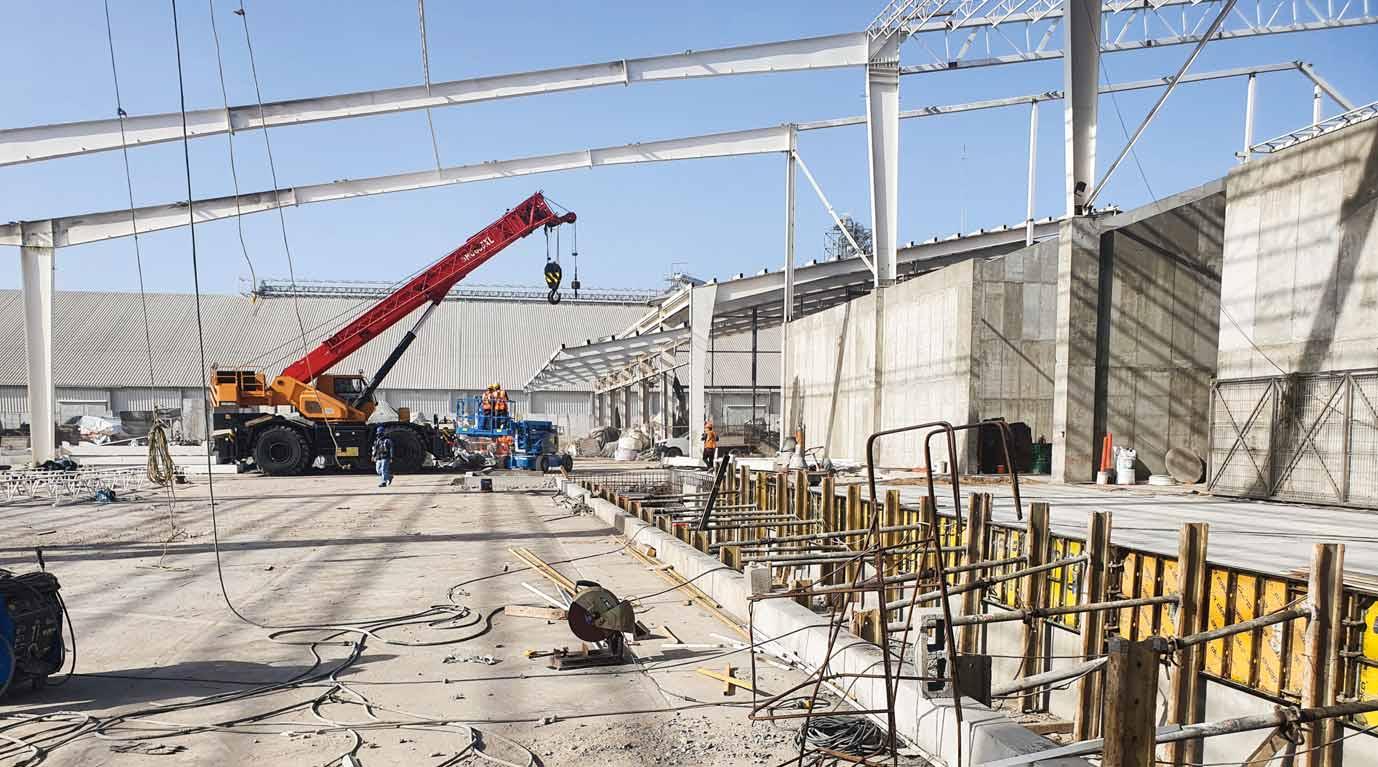
Bouw van de ISAOSA fabriek, met de put waarin later de machines van EMT geïnstalleerd worden.
EMT INSTALLEERT KUNSTMESTMENGLIJN IN MEXICO
EMT heeft een ultramoderne kunstmest-mengfabriek geïnstalleerd voor ISAOSA in Topolobampo, Mexico. Een foto-impressie van het project.
EMT, een van de grootste producenten van kunstmestmeng- en afzakapparatuur ter wereld, heeft een enorme kunstmestmenglijn geleverd in Mexico. De installatie werd in Nederland gebouwd en vervolgens met 25 containers van 40 voet lang verscheept. De twee parallelle productielijnen die in de meer dan 200 m lange fabriek geïnstalleerd zijn, produceren samen een mengsel van 300 ton kunstmest per uur. Onderdeel van de lijn is een directe ureum-coat en -mengbehandeling. Boven een directe mengschroef met een vloeistofi njectiepunt is een kluitenbreker geplaatst. Zowel de kluitenbreker als de injecteur worden continu gemonitord en de materiaalstromen aangepast om te zorgen dat het eindproduct precies aan de eisen voldoet. centrale transportband waarna er met weeghoppers andere stoffen bovenop gedoseerd worden. Per lijn zijn er in totaal 12 doseerbunkers en 6 vloeistofdoseerunits ingebouwd. Een andere mengschroef zorgt ervoor dat alle producten goed gemengd worden. Daarna wordt het mengsel over een grove zeef geleid. Optioneel kan met een fijne zeef ook nog het stof uit het mengsel worden gezeefd.
VULSTATION Het eindproduct gaat op een transportband naar een van de vijf rvs bulkhoppers met elk een capaciteit van 30 ton, of rechtstreeks naar het treinvulstation. De band kan over het buitenste hek van de fabriek gehangen worden om treinwagons te vullen die op het spoor direct daarnaast staan. Als de trein vol is, wordt de transportband weer ingetrokken. De complete menglijn is computergestuurd en kan eenvoudig worden bediend met één operator vanuit het centrale kantoor. Met deze proceslijn kan ISAOSA haar jaarlijkse productie verdrievoudigen tot 300.000 ton per jaar.
TWEEDE MENGINSTALLATIE Naast de menglijn voor korrelmeststoffen installeerde EMT ook een tweede menginstallatie, speciaal ontworpen om verschillende in water oplosbare meststoffen te mengen. Deze machinelijn bestaat uit 11 weegbunkers die gevuld kunnen worden uit bigbags, bulk of small bags. Ook hier worden grote klonten uit het product gezeefd en kan vloeistof in de mengschroef worden toegevoegd. Via een transportband wordt het materiaal in vijf verschillende afzakstations gelost, waar het in diverse maten zakken verpakt wordt. ●
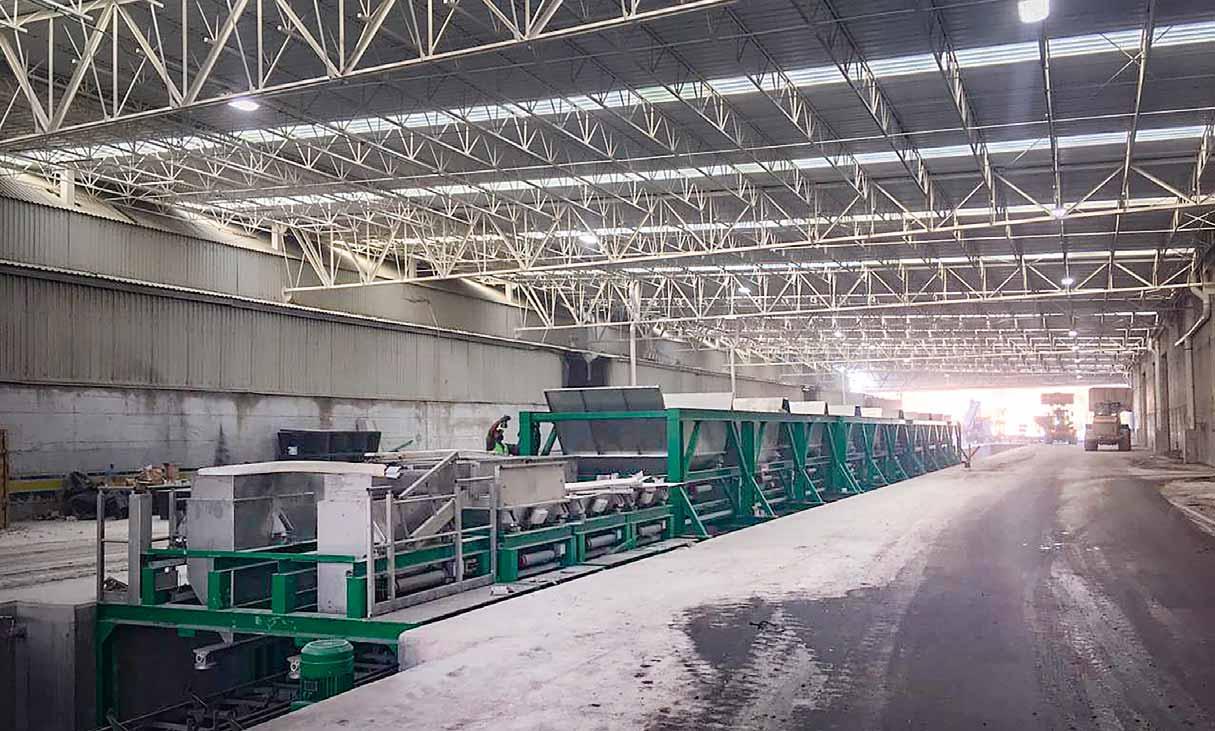
Opbouw van de productielijn in de put.
Kluitenbreker en machinelijn met centrale transportband nadat ze in de put geplaatst zijn.
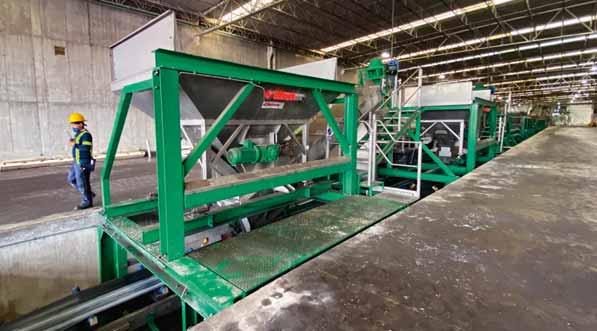
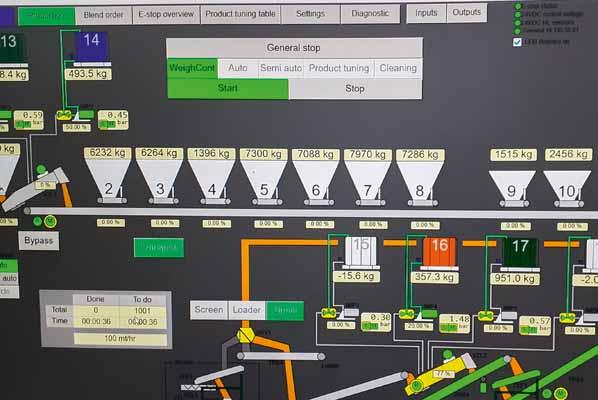
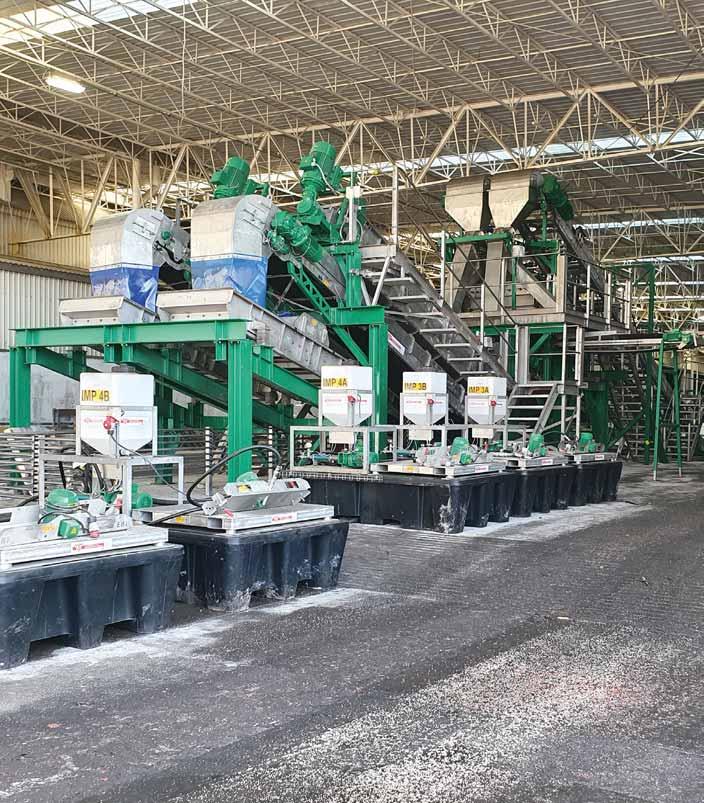
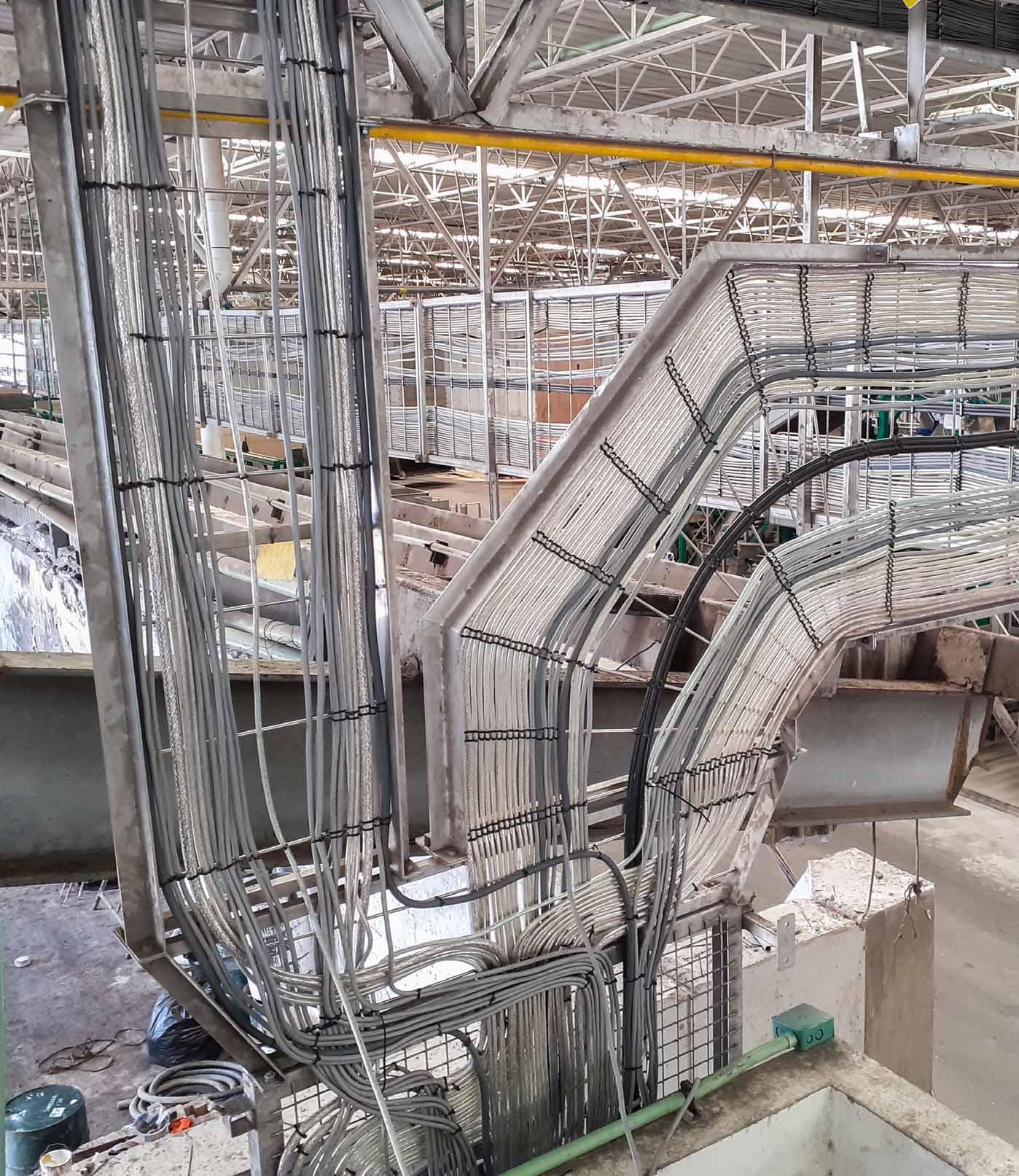
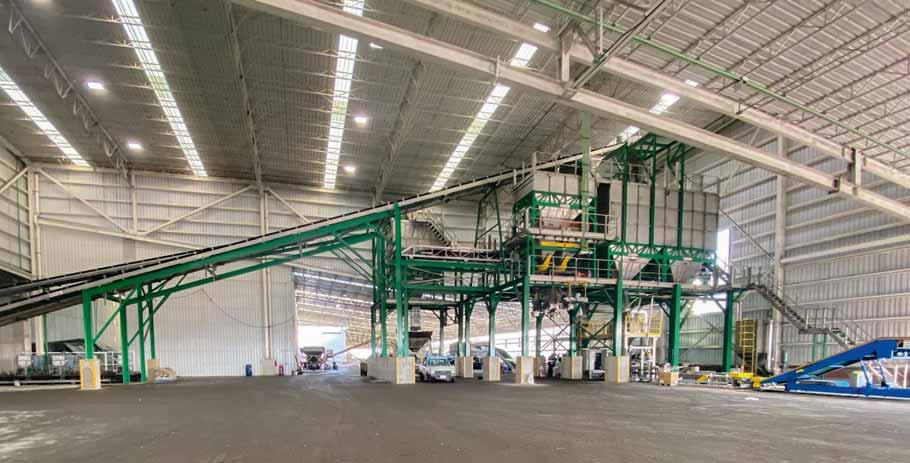
Silotoren voor bulkverlading en het vullen van treinwagons.
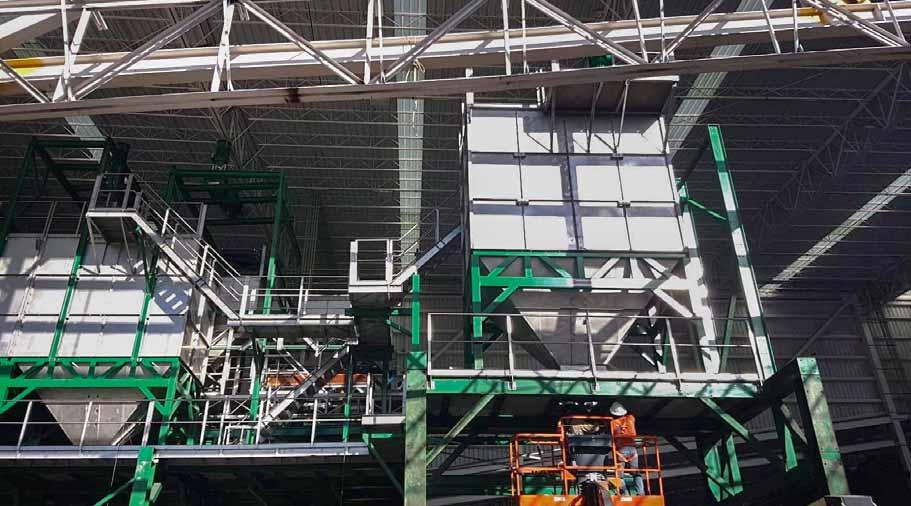
Het installeren van de 5 silo’s, met elk een capaciteit van 30 ton.
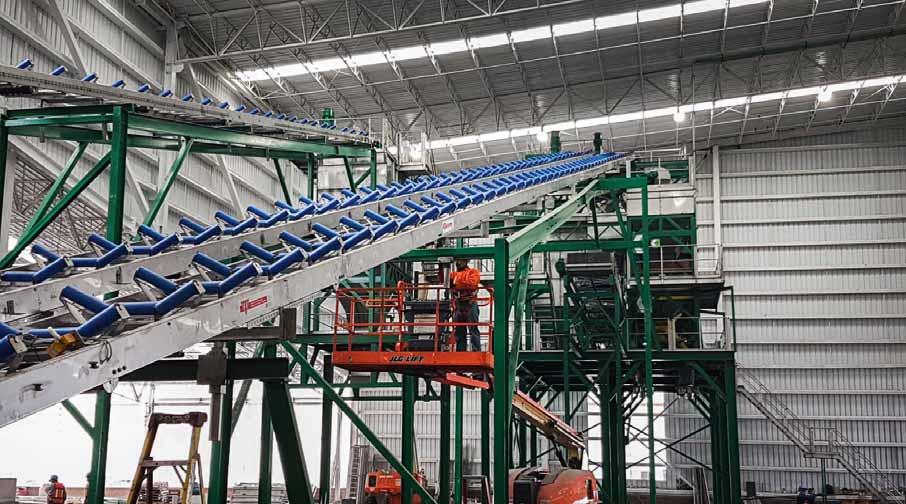
Met online configurator Sisca KLANT KAN NU ZELF SCHROEFTRANS
Voor eindgebruikers en system-integrators ontwikkelde Van Beek een online tool om zelf een schroeftransporteur te configureren voor eenvoudige toepassingen. Doel: een snelle productie van machines met een scherp prijskaartje.
‘Hallo, ik ben Sisca, uw online engineer’. Deze welkomstgroet staat op de website van Van Beek Schroeftransportsystemen. Prominent in beeld is het hoofd van een vrouwelijke engineer met een vriendelijke en deskundige blik. Wat volgt is een doorwrocht keuzemenu om de precieze specificaties van de gewenste schroeftransporteur in te vullen, van het model (koker, trog of omega), de uitvoering (keuze uit drie soorten materiaal), de lengte, de werkhoek en de doseercapaciteit tot de temperatuur en eigenschappen van het te transporteren product (viscositeit, stortgewicht, ATEX, enzovoorts). krijgen, om de machine nog eens van alle kanten te bekijken.
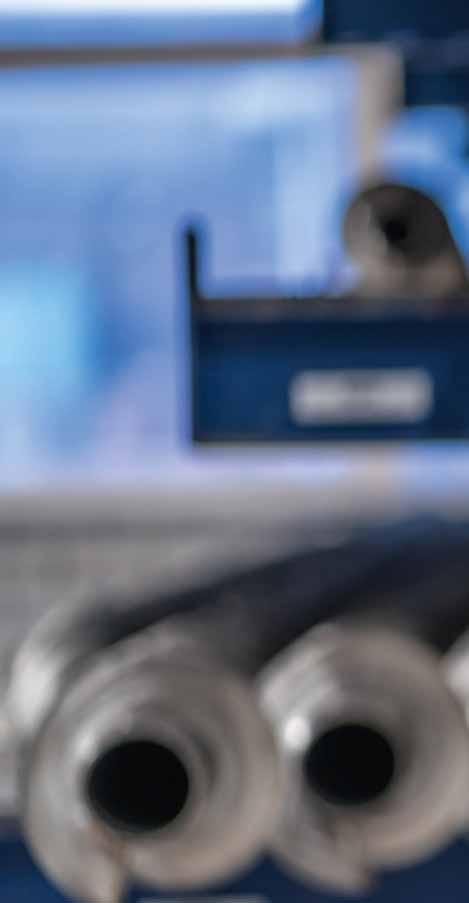
EENVOUDIGE OPLOSSINGEN “Klanten komen vaak bij ons langs voor schroeftransporteurs voor uiteenlopende toepassingen”, licht directeur Perry Verberne van Van Beek de ontwikkeling van Sisca toe. “We bouwen op maat gemaakte, doorgaans complexe machines, geen standaard transporteurs. Onze sales-engineers kijken samen met de klant naar de oplossing die nodig is. In veel gevallen is dat ook de beste aanpak bij een klant die net iets speciaals wil. Daar-
PROJECTDOSSIER Het systeem selecteert zelf de diameter en het aandrijfvermogen van de transporteur. Ook is het mogelijk de machine nog een RAL-kleur mee te geven in de huisstijl van het bedrijf. Linksonder verschijnt intussen doorlopend de voor al deze specificaties geldende totaalprijs van de schroeftransporteur en de levertijd in beeld. Een minieme wijziging doet de prijs stijgen of dalen. De omega-uitvoering, van boven te openen dus makkelijker te reinigen, valt bijvoorbeeld duurder uit. Als deze exercitie is voltooid, heeft Sisca een projectdossier aangemaakt van de geconfigureerde transporteur. Tot slot is het mogelijk binnen één uur een offerte en een gerenderde 3D-tekening van het prototype in de mailbox te
naast hebben we ook klanten die een eenvoudige oplossing nodig hebben. Daar zitten weinig toeters en bellen aan: een bepaald type product moet van A naar B en dan horizontaal of via een bepaalde hoek. Het behandelen van dit soort vragen hebben we met Sisca gedeeltelijk geautomatiseerd.”
MAATWERK “Ook deze groep klanten willen we een echte maatwerkoplossing bieden”, vervolgt Verberne.
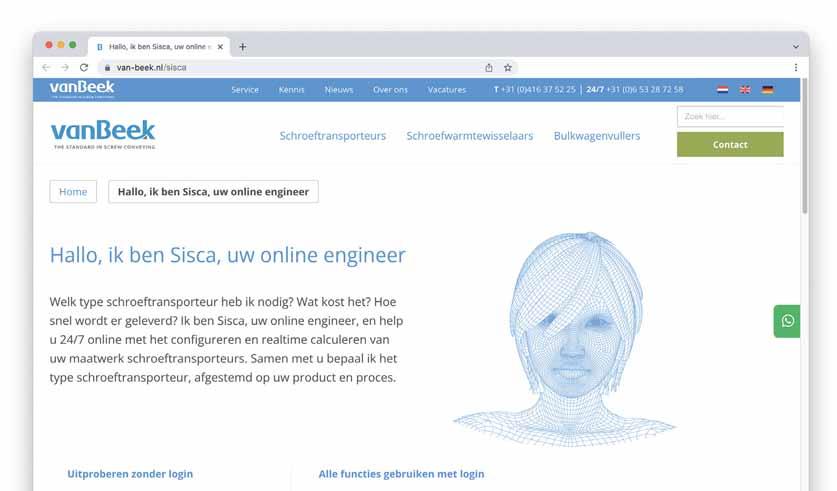
“Zo’n online-geconfigureerde transporteur wordt eveneens tot op de millimeter nauwkeurig gemaakt. We willen deze groep klanten graag aan ons binden, want het is een behoorlijk groot marktsegment. Voor onszelf betekent het dat we met Sisca de minder complexe projecten af kunnen vangen en een flink stuk engineering kunnen uitsparen”, verduidelijkt Verberne.
CAD-MODEL Op de achtergrond wordt tijdens het invullen van de configurator een volledig 3D CAD-model van de betreffende schroeftransporteur gegenereerd en eenmaal in Sisca geconfigureerd kan de transporteur zo de productie in. Voor de klant is het interessant want de machine kan snel geleverd worden. “Een uitgebreide prijslijst zou te statisch zijn en levert geen winstvoordeel op. Al onze
PORTEUR CONFIGUREREN
Perry Verberne, directeur van Van Beek schroeftransport: “Sisca kan de minder complexe projecten afvangen en een stuk engineering uitsparen.” (Foto: Marco Vellinga)
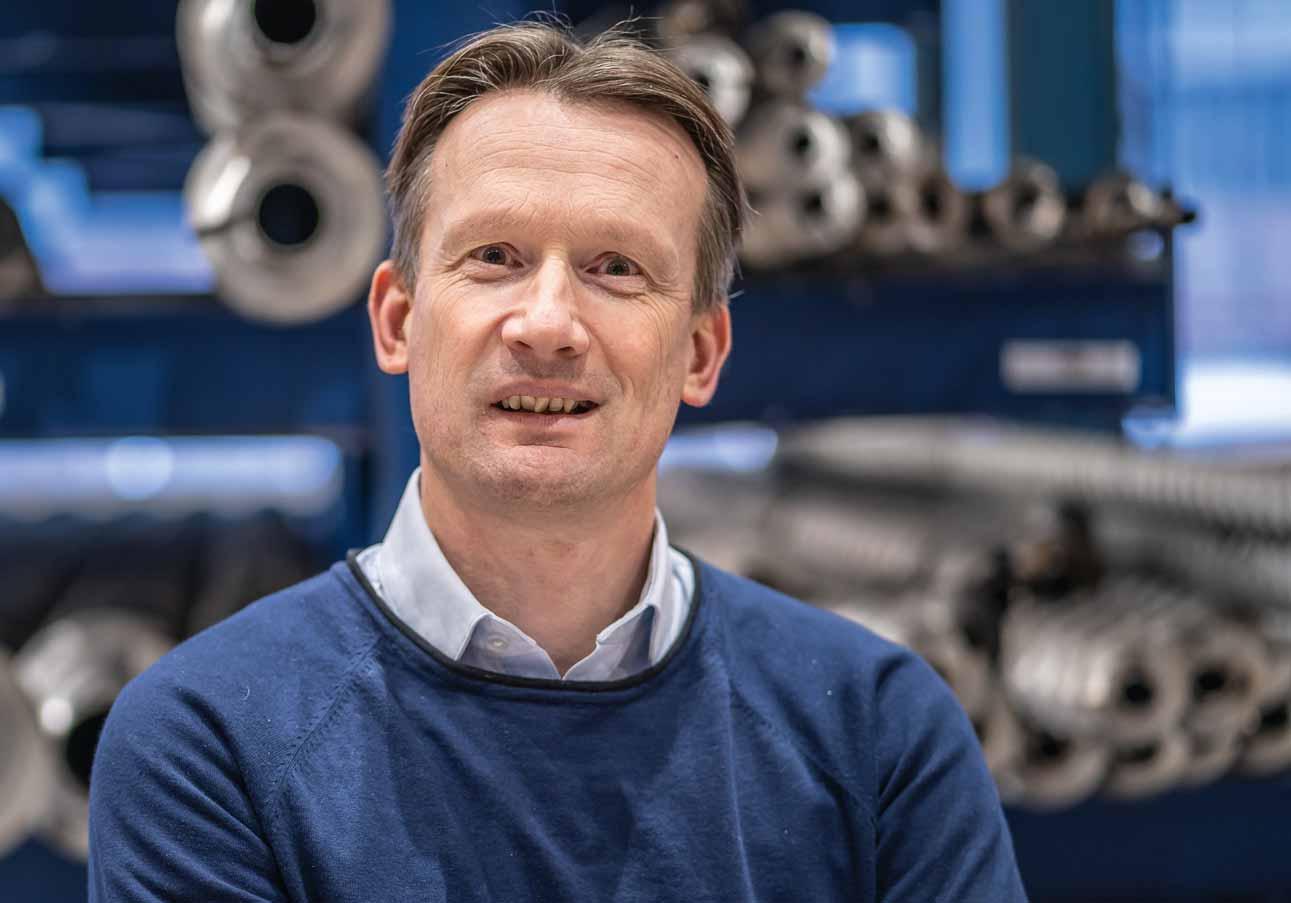
kennis zit in dit systeem.” De naam is willekeurig gekozen, legt Verberne nog uit. “Sisca is gewoon een leuke naam en je kunt er het woord ‘configurator’ in zien.”
PROEFGEDRAAID Begin 2022 is Sisca live gegaan, beschikbaar in drie talen (Nederlands, Engels en Duits). De afgelopen maanden is met de bèta-versie van de machineconfigurator proefgedraaid door een aantal bestaande klanten, voornamelijk systemintegrators, om voor hun eigen klanten calculaties te maken en offertes aan te vragen. “Het systeem is flink aan de tand gevoeld, maar werkt prima en is bijzonder klantvriendelijk”, vertelt Verberne.
GLOBALE INSCHATTING “Onze klanten hebben nu een eigen portal waarin ze naar hartenlust en 24/7 configuraties kunnen maken, of ze nou in de VS, Australië of in het Verre Oosten zitten”, zegt Verberne. “Het verschil in tijdzone maakt niet meer uit. Klanten kunnen zo snel geholpen worden. Ze kunnen makkelijk een transporteur configureren en krijgen meteen een prijs en een levertijd. Veel klanten hebben in deze fase van een project niet meer nodig dan een globale inschatting van de kosten. Ze weten even voldoende. Ook kunnen ze meerdere files aanmaken, mochten ze voor hun project verschillende schroeftransporteurs nodig hebben. Natuurlijk blijven we altijd stand-by. Als gebruikers tijdens het configureren nog vragen hebben, kunnen we telefonisch meekijken.”
EERSTE INGANG Verberne verwacht niet dat hij met Sisca meteen een heel regiment schroeftransporteurs gaat verkopen. “Sisca vormt de eerste ingang voor mogelijke kopers, maar biedt in onze ogen wel een belangrijke meerwaarde. Ik kan me ook voorstellen dat klanten die straks een tijdje met Sisca hebben gewerkt, wèl bestellingen gaan plaatsen. Maar dat moet nog blijken. Het zou echter wel eens snel kunnen gaan.” ●

Peter Keizer (l) en Geert Grinwis van GP Stainless.
OVERNAME MAAKT DE LIJNTJES HEEL KORT
Met de overname van Wissekerke tekende machinebouwer GP Stainless voor groeimogelijkheden en stelde tegelijk de toekomst van de aandrijfspecialist zeker. Een win-win situatie waarvoor de eerste kiem werd gelegd bij een samen werking in 2017. “Toen hebben we elkaars kwaliteiten en manier van zakendoen goed kunnen ervaren”, aldus Peter Keizer en Geert Grinwis van GP Stainless.
“Je kunt wel zeggen dat we in maart 2020 op een heel natuurlijke manier om de tafel gingen zitten”, herinnert Peter Keizer zich. Keizer en Grinwis zijn mede-directeur-eigenaren van GP Stainless, een bedrijf dat roestvaststalen machines bouwt voor vooral de farmaceutische en de voedingsindustrie en maatoplossingen biedt. Doordat GP Stainless een aantal jaren daarvoor al eens tot grote tevredenheid met Wissekerke Techniek uit Stellendam had samengewerkt in een project, wisten ze precies wat de specialisten in pneumatiek en hydrauliek te bieden hadden. Vandaar dat toen de 62-jarige René Wissekerke terloops het woord ‘overname’ op tafel legde, Grinwis en Keizer daar niet vreemd van opkeken en met enthousiasme de onderhandelingen aangingen. REMZAND “Via een project in 2017 van Wissekerke met het GVB Amsterdam hebben we elkaars kwaliteiten en manier van zakendoen voor het eerst goed kunnen ervaren”, zegt Keizer. “Wissekerke leverde vanuit hun specialisme het dichte-fase pneumatisch transportsysteem van een remzandvulsysteem voor de Amsterdamse trams. Zij
hadden de kennis in huis over dat zandtransport. Wij konden de buitenopstelling – compressoren, tanks, leidingen – ontwerpen en produceren in de uiteindelijke uitvoering van overdekte abri’s.” Doordat deze samenwerking een groot succes was, kwam Wissekerke op het idee van de overname.
VERTROUWEN Het jonge bedrijf van Grinwis en Keizer – GP Stainless werd pas 8 jaar geleden opgericht – nam voor de begeleiding van het overnameproces wel een extern adviesbureau in de arm. Grinwis: “Mede daardoor konden we onze overeenkomende kernwaarden ‘openheid’ en ‘eerlijkheid’ tijdens het stapsgewijze traject wederzijds goed staande houden. Het onderlinge vertrouwen bleef onveranderd groot.” Dat vertrouwen werd nog verder gevoed door de respons van Wissekerke toen GP Stainless een klant naar het bedrijf doorstuurde. “Deze afnemer was een goeie klant van ons. Hij had het er min of meer terloops over dat zijn compressoren zo’n drama waren. Ik heb dat toen meteen doorgespeeld naar Wissekerke, die dit heel vlot oppakte. Kort samengevat: de installatie werd neergezet en wij konden mooi benadrukken dat we ons aan de afspraken houden.”
BEDRIJFSPAND Naarmate de overname vorderde, bleek het ook interessant voor beide bedrijven om, behalve naar de aandelen, te kijken naar het bedrijfspand van Wissekerke. Keizer: “Ons eigen pand in Ouddorp was al te klein. We doorlopen meteen vanaf de oprichting al een flinke groeifase. Wissekerke had een grote ruimte, met een hele ruime werkplaats. Daarom kozen we ervoor om ook hun hele pand erbij over te nemen.” Door de overname van het pand is de samenvoeging van de bedrijven ook voor de werknemers erg prettig, ze profiteren letterlijk van de extra ruimte. “De monteurs van Wissekerke Techniek kunnen nu gemakkelijk een stel collega’s van GP op een klus inschakelen. De lijntjes zijn heel kort. Mede daardoor hebben we zelfs 2 monteurs binnen de onderneming kunnen vasthouden, in deze krappe tijden toch mooi meegenomen.” ●
Hier begon het mee: remzand vulsysteem voor het GVB
Voor de Amsterdamse trams bouwde GP Stainless en Wissekerke samen een remzand-vulsysteem in overdekte abri’s. Wissekerke leverde het dichte-fase pneumatisch transportsysteem. Het bedrijf had de kennis in huis over het zandtransport. GP Stainless ontwierp en bouwde de buitenopstellingen – compressoren, tanks, leidingen – die in overdekte abri’s op het perron werden geplaatst. De goede samenwerking van de bedrijven bij dit project en het opgebouwde vertrouwen legden de kiem voor de overname in 2021.
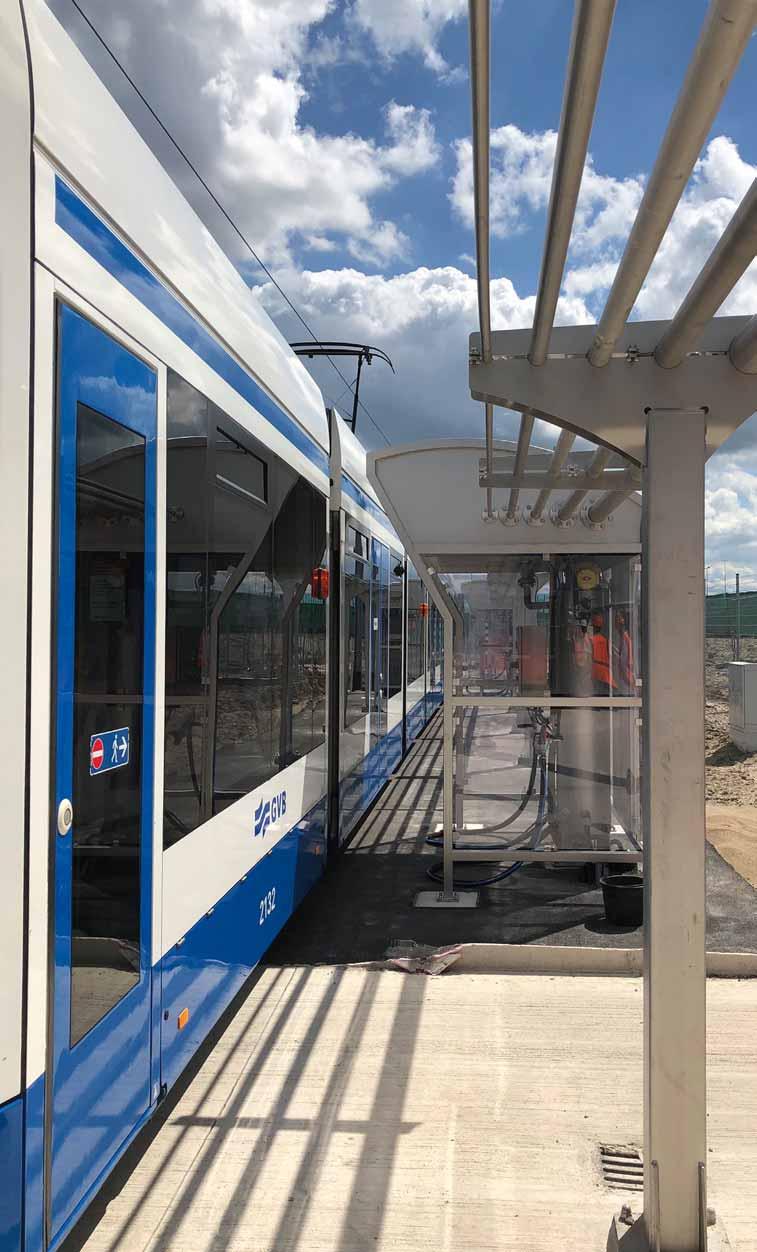