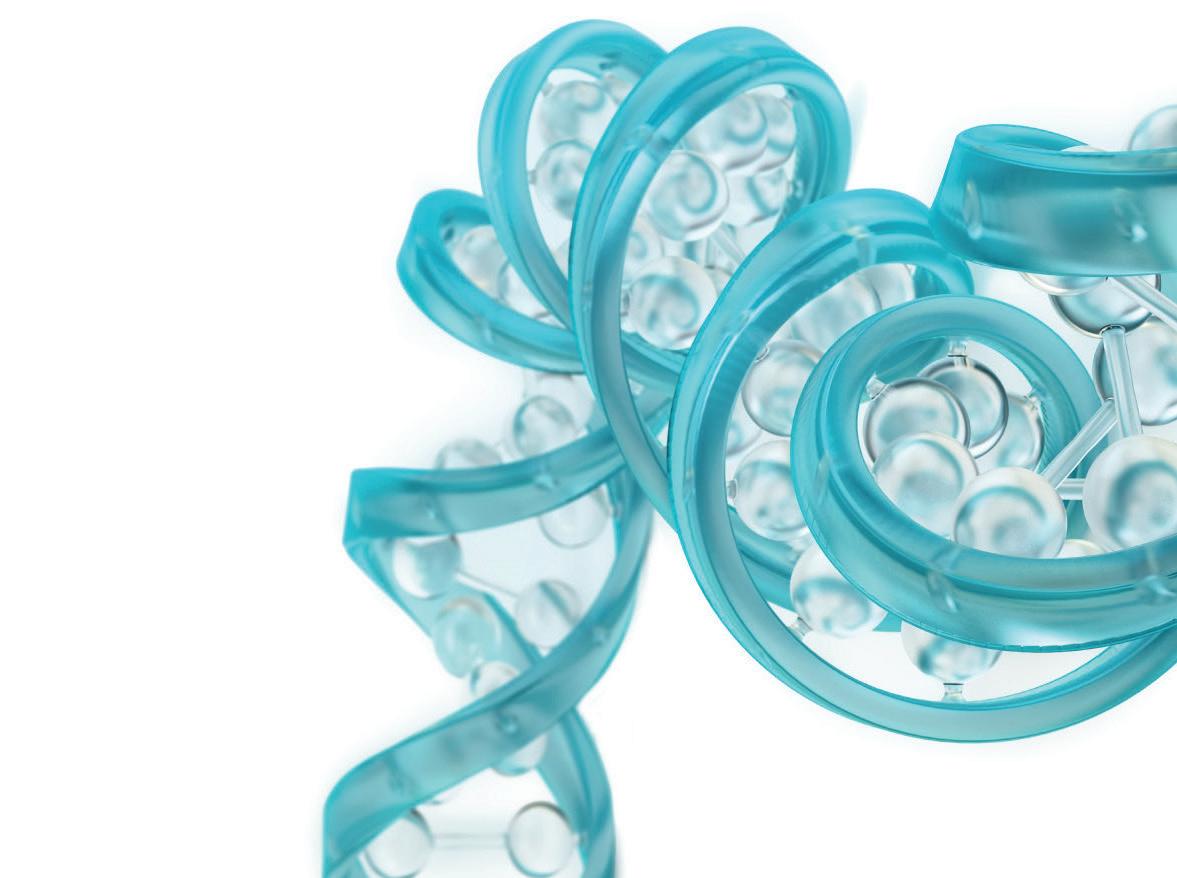
15 minute read
La sostenibilità dei rifiuti plastici in mostra
Promossa dal Comune di Castelfiorentino (Firenze) e dal Progetto Metamorfosi e curata da Maria Vittoria Gozio, dal 13 maggio 2023 all’8 gennaio 2024 la quarta edizione della “Mostra Diffusa”, quest’anno intitolata “Community”, è animata dalle opere di Davide Dall’Osso, artista che, per la sua produzione, non ha scelto il nobile marmo, il possente bronzo o le luminescenze del neon, bensì gli scarti di un materiale comune, sovrabbondante e a forte impatto sull’ambiente: la plastica. Ne è nato un percorso artistico unico che ha portato Dall’Osso a essere uno dei primi a riflettere sul tema della sostenibilità e a fare arte “di recupero” in Italia. Ecco, allora, che la plastica, anzi, detto ancora meglio, i rifiuti plastici si trasformano e trasmettono un messaggio di sostenibilità, rispetto e dialogo in maniera potente, quella tipica delle opere d’arte. Un materiale sintetico, artificiale, impattante trova nuova vita grazie alla lavorazione che l’artista gli conferisce e al contesto scenico e drammatico dove viene collocata. Così gli scarti stimolano la comunità che ospita le opere d’arte che ne sono frutto a prendere coscienza di un problema che la riguarda direttamente, ossia la scarsità di risorse sulla Terra, e la invita a riflettere e ad agire, obiettivo verso il quale l’arte svolge un compito decisivo e, grazie al lavoro di Dall’Osso, si riappropria dello spazio pubblico, entra nella vita pubblica e privata, avvicina e unisce.
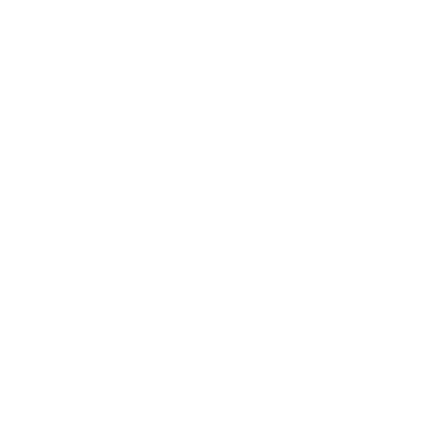
Le materie plastiche, con la particolare tecnica di lavorazione scelta dall’artista, si prestano ad assumere le più svariate forme, permettendo di sprigionare una drammaticità antica che si tramuta in un sentimento contemporaneo. Tra i soggetti prediletti da Dall’Osso vi sono quelli femminili, colti nella loro bellezza e forza, ma anche delicatezza e interiorità, come nelle opere Duende e Ballerine. A fornire molto dello scarto di policarbonato utilizzato per le sculture è l’azienda pratese Isopad che, come spiega Davide Dall’Osso, “ha una grande sensibilità verso l’ambiente: dedicano tempo, dipendenti e, dunque, risorse per sostenere il mio percorso artistico, aiutandomi nella scelta e nella raccolta”.
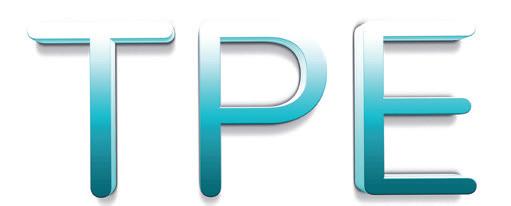

“Questa nuova installazione a Castelfiorentino vuole essere parte di un dialogo interculturale della nostra cittadina. L’arte come medium tra le persone che abitano le vie e i quartieri della nostra comunità”, ha dichiarato Dall’Osso.
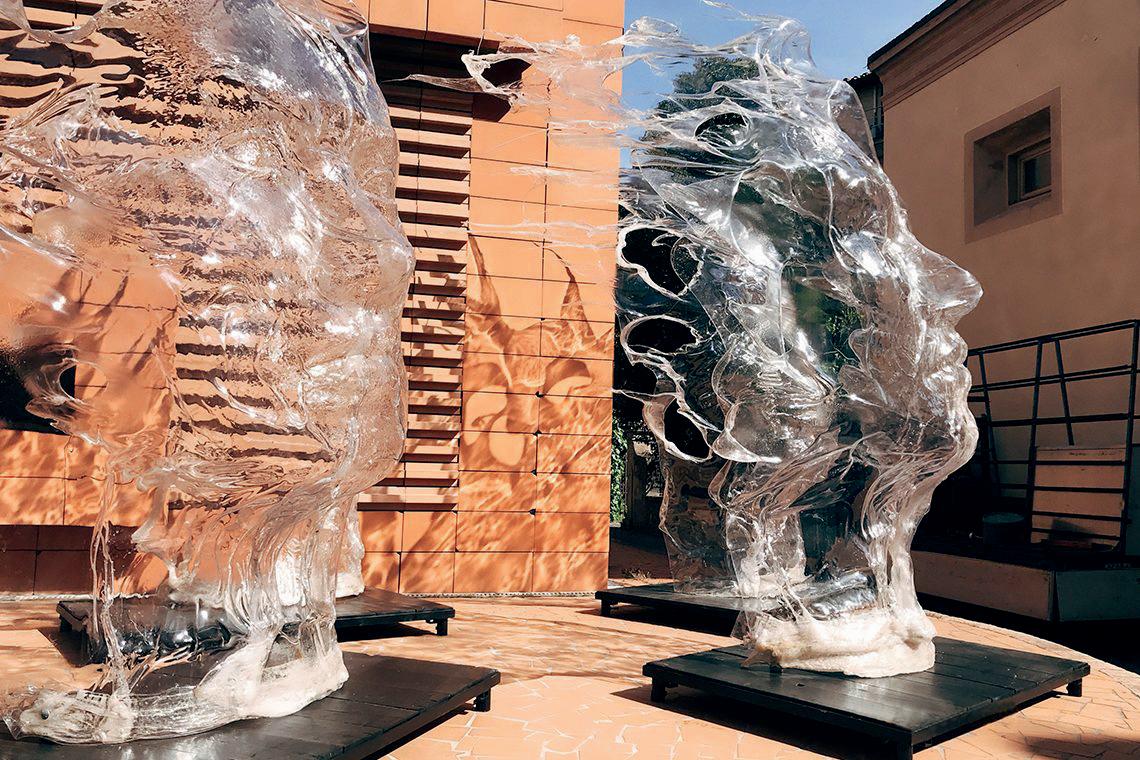
Luci puntate su digitalizzazione pervasiva, leadership applicativa e sostenibilità. Un’analisi in occasione di SPS con il direttore vendite di Gefran Italia ci ha permesso di comprendere i messaggi principali che la multinazionale italiana ha portato in fiera a Parma e che ripropone a Plast.
Viviamo in un mondo iperconnesso dove la tecnologia permette di raggiungere potenziali clienti e collaboratori senza muoversi dalla propria azienda o, addirittura, da casa. Alla luce di queste premesse, la domanda è la seguente: perché investire ancora in una fiera di settore?
È presto detto: il web non permette di incontrare fisicamente i clienti, guardarli dritti negli occhi e stringere loro la mano. Ne abbiamo parlato con Renzo Privitera, direttore vendite Italia di Gefran, durante la fiera SPS Italia (svoltasi a Parma dal 23 al 25 maggio scorsi).
Da oltre dieci anni
Messe Frankfurt Italia organizza a Parma SPS

Italia - acronimo di Smart Production Solutions
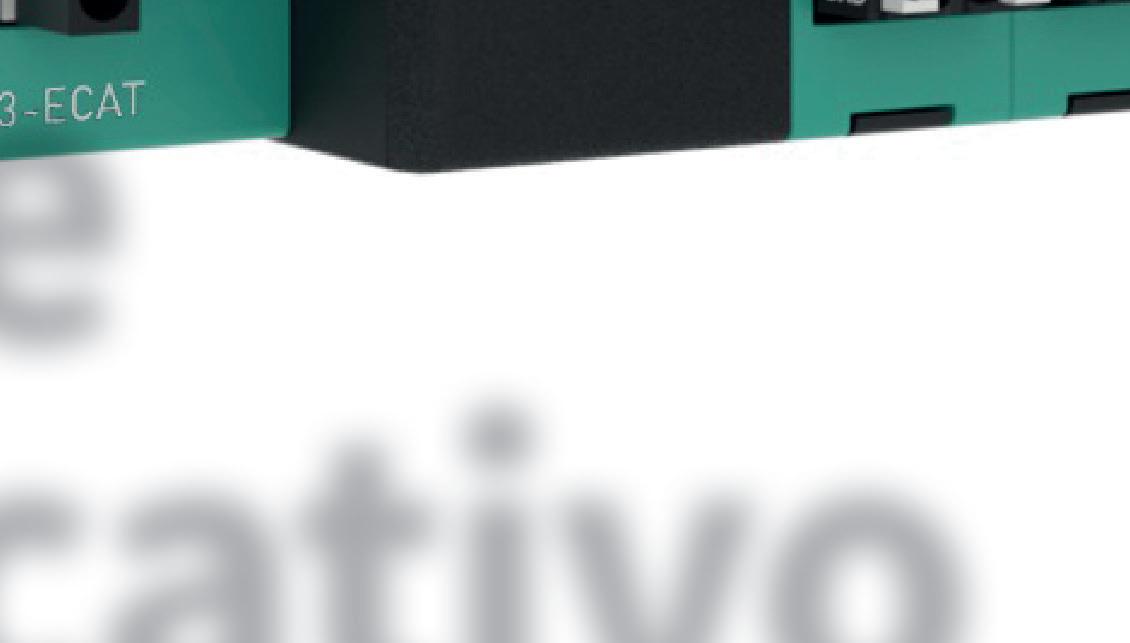
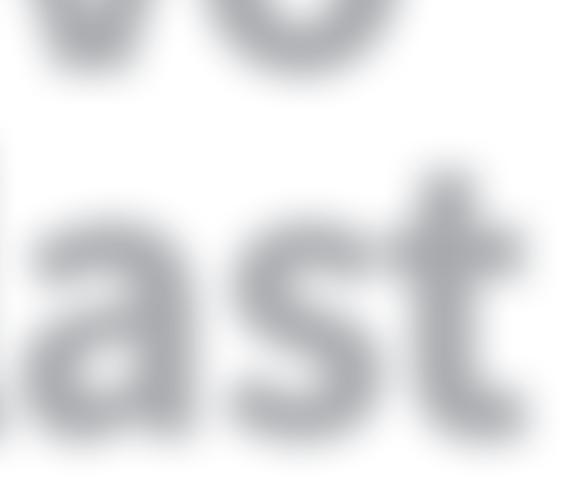
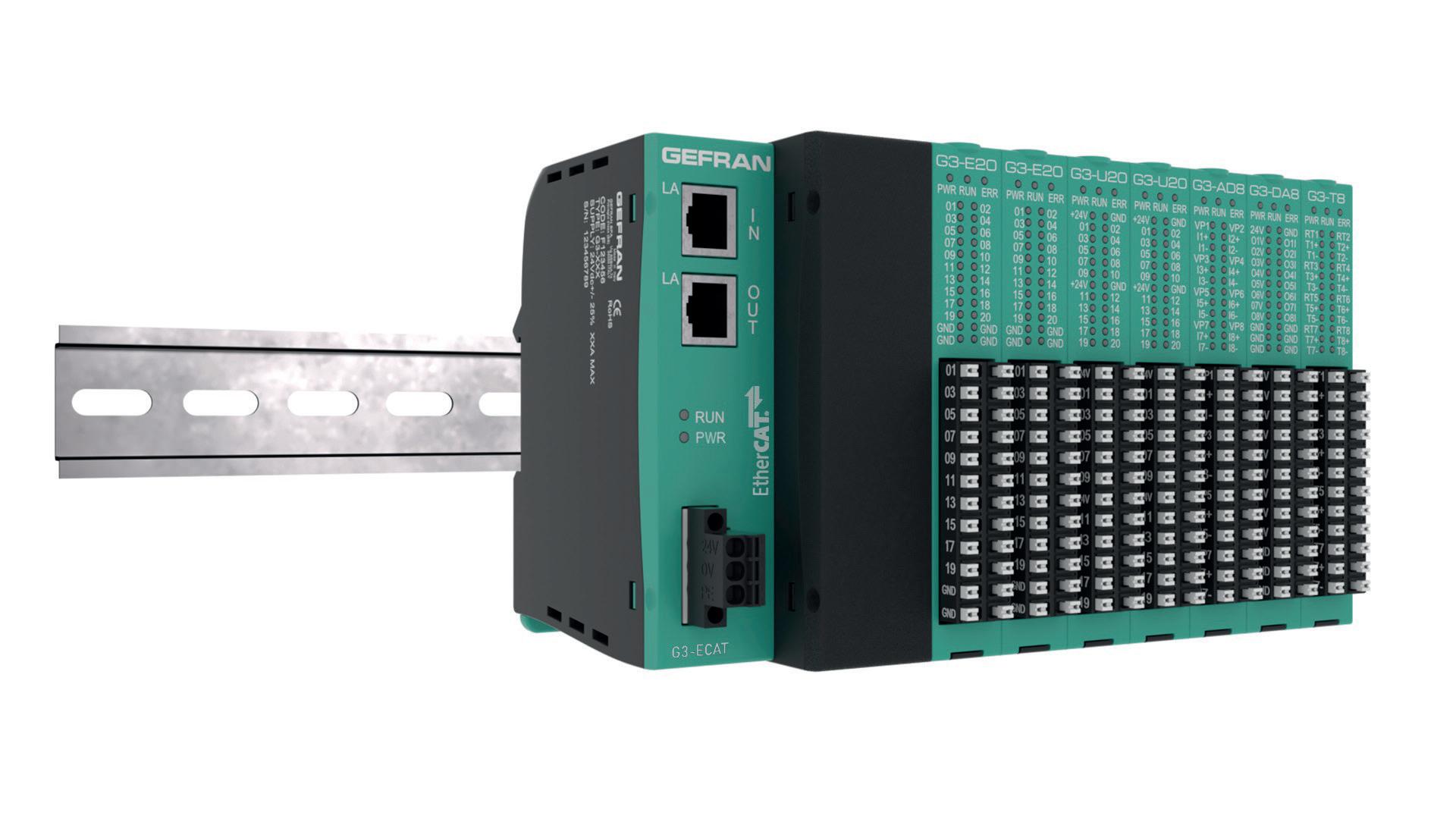
- fiera dedicata ad automazione e digitale per l’industria. In linea con il vostro core business in progettazione e produzione di sensori, strumentazioni per controllo di processi industriali e sistemi per l’automazione, quali proposte avete portato in fiera?
“In linea con la filosofia SPS Italia di rivolgersi a più settori industriali finali, qui a Parma abbiamo scelto di presentare la nuova generazione di trasduttori di pressione industriale serie KM. Progettati per le principali applicazioni di idraulica mobile nell’ambito del sollevamento, della movimentazione terra e di quello agricolo, le sonde KM rappresentano un concentrato di tecnologia, robustezza e versatilità, il tutto racchiuso in formato estremamente compatto.
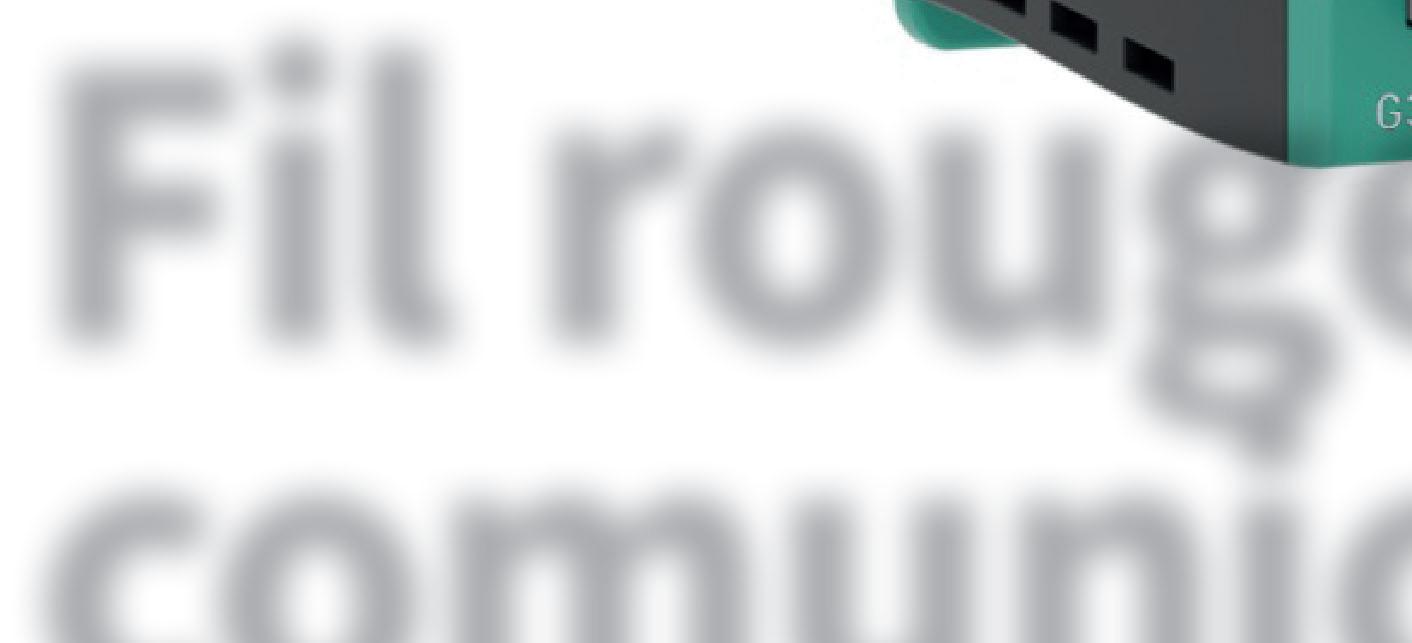
SPS è stata anche l’occasione per promuovere la collaborazione tra Gefran, in quanto membro ANIE, e la OPC UA Foundation, attraverso applicazioni OPC UA field to cloud. Queste ultime dimostrano come dati raccolti sul campo dai sensori e dagli SSR Gefran con tecnologia IOLink, possano essere trasmessi in cloud in modo efficiente e scalabile attraverso protocolli standard come MQTT e OPC UA. G-Mation G3 è invece la nuova serie di sistemi I/O su base EtherCAT per la gestione evoluta dei segnali in campo. La meccanica modulare, alla base del progetto, permette un’installazione efficiente e garantisce una manutenzione semplificata. I G3 completano i pannelli operatore G-Vision nel contesto delle architetture di automazione G-Mation.
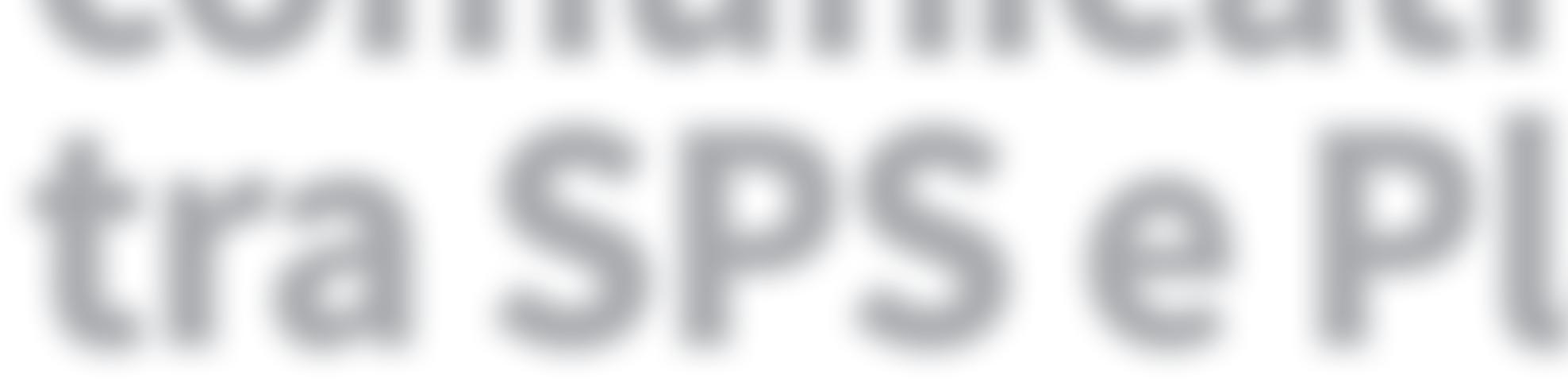
Altra grande novità sono gli SSR serie GRZ per il controllo dei carichi trifase per riscaldamento elettrico. Basati sulla piattaforma GRx, da cui ereditano il formato estremamente compatto, questi relè statici sono scalabili su un range di corrente particolarmente esteso, che va da 10 a 75 A, risultando la soluzione ideale per un vasto numero di applicazioni industriali, inclusa la produzione di materie plastiche. Mi preme infatti ricordare che, sin dalla sua fondazione negli anni Sessanta, il primo settore di sbocco per Gefran fu proprio quello delle materie plastiche. Le nostre origini sono legate alla costruzione di apparecchi elettrici per ausiliari a supporto della trasformazione di materie polimeriche e, sebbene nel tempo ci sia stato un ampliamento delle aree strategiche di attività, ancora oggi gli OEM produttori di macchine e impianti per materie plastiche rappresentano uno dei nostri mercati principali. Non a caso, dal 5 all’8 settembre saremo presenti alla manifestazione fieristica Plast 2023 di Milano”.
In quanto multinazionale attiva in più aree del mondo e in più settori applicativi, compreso quello delle già citate materie plastiche, qual è la vostra interpretazione dell’automazione industriale e dei relativi controlli di processo?
“Viviamo da diversi decenni l’automazione come modalità atta a velocizzare la produzione e aumentarne i volumi. Oggi più che mai la differenza risiede nei dati, non tanto nella capacità di rilevarli in modo preciso e puntuale, che comunque resta fondamentale, quanto nel riuscire a valorizzarli, per esempio in ottica di condition monitoring. Per farlo serve che i dispositivi in prima linea siano digitalizzati, per questo negli ultimi anni abbiamo lavorato molto per estendere la nostra gamma di sensori e SSR in IO-Link. Al tempo stesso serve un forte know-how specifico dell’applicazione. Pensiamo a una pressa a iniezione, da tempo siamo a stretto contatto con gli OEM e sappiamo bene qual è il livello di performance, di affidabilità o di informazione che serve al cliente per la sua applicazione. L’idea, quindi, è di dargli esattamente quello che gli serve”.
Un sondaggio di “economiesuisse” mostra come l’allentamento delle restrizioni imposte durante il Covid abbia aiutato a superare il collo di bottiglia negli approvvigionamenti, ma anche come la guerra in Ucraina abbia acuito di nuovo il problema. In tale contesto, come reagiscono le vostre attività manifatturiere e le vostre efficienze nelle forniture?
“In questo scenario, Gefran ha dimostrato di essere una “mosca bianca”. In questi anni non abbiamo mai fermato le nostre linee produttive e, per quanto ci compete, non abbiamo mai contribuito all’interruzione di quelle dei nostri clienti. Siamo riusciti a farlo grazie principalmente a due fattori: l’elevata integrazione verticale (dalla camera bianca fino all’officina meccanica), anche delle competenze, che ci permette di avere il controllo totale sul processo produttivo e che risulta in una flessibilità che ci distingue dai nostri competitor, e i forti investimenti che stiamo sostenendo nell’automazione della produzione.
Devo ammettere che non è stato semplice, considerando anche il cospicuo aumento dei prezzi subito dai i componenti elettronici, ma la scelta di salvaguardare la continuità delle forniture ai nostri clienti si è rivelata vincente, consentendoci anche di acquisirne di nuovi”.
Gefran conta su circa 660 dipendenti, di cui oltre 400 in Italia, collaborazioni con centri di ricerca e università nazionali e internazionali, otto stabilimenti produttivi, 13 organizzazioni commerciali e oltre 80 distributori nel mondo. In virtù di tale dimensione “globale”, come descrivereste l’andamento della domanda di automazione di fabbrica?
“Oggi più che mai, l’automazione di fabbrica è fondamentale per migliorare i processi produttivi, ridurre gli errori e i costi e aumentare la flessibilità operativa delle aziende. In linea con questo trend, nel periodo 2021-2022 in Gefran abbiamo registrato ottimi fatturati, con aumenti a due cifre e, il primo trimestre del 2023, ha confermato una crescita che, anche se non pari a quella dello scorso anno, è rimasta costante.
Per concludere, credo che l’automazione, accompagnata da una crescente digitalizzazione, sia oggi l’unica via da seguire per garantire sane crescita e competitività alle nostre economie”.
Relè SSR serie GRZ, per il controllo dei carichi trifase per il riscaldamento elettrico, scalabili su un range di corrente da 10 a 75 A.
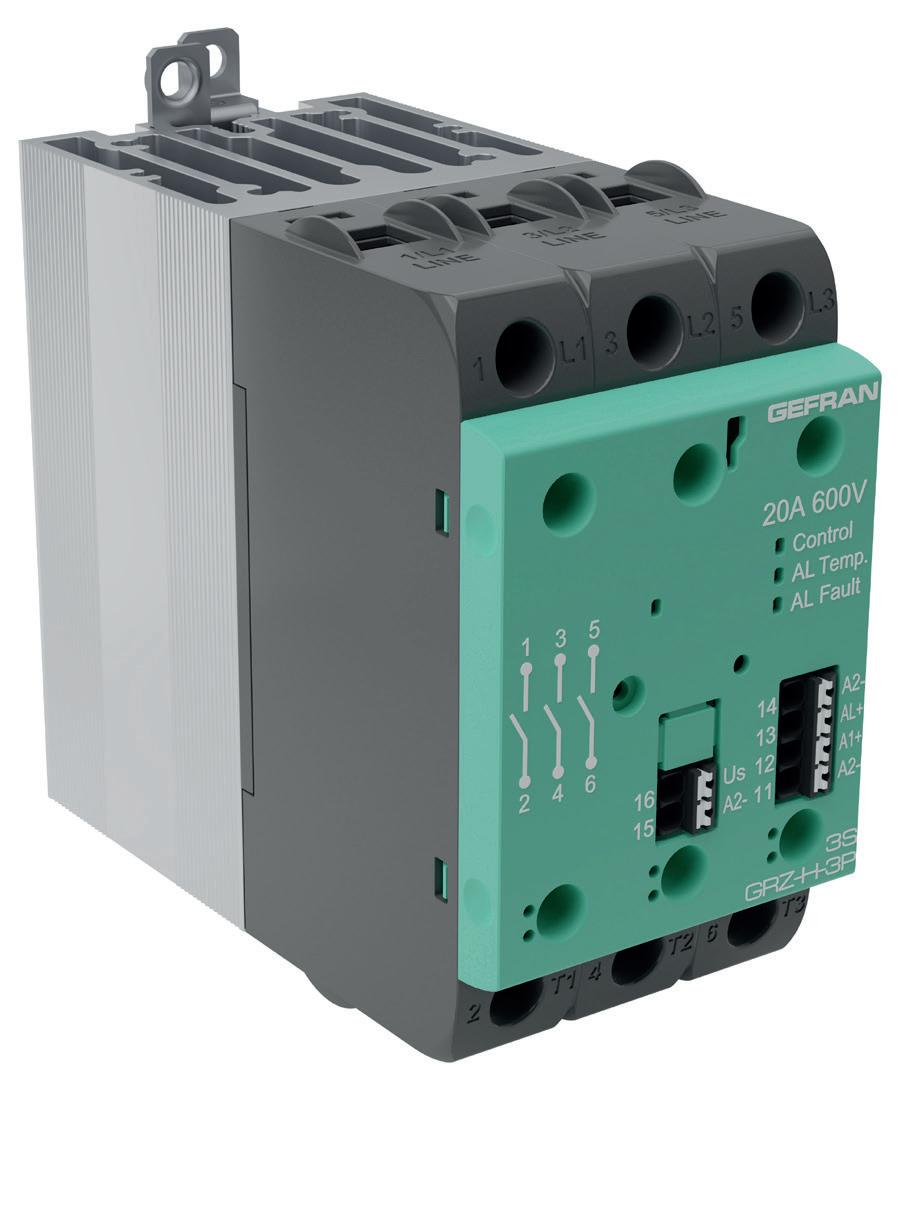
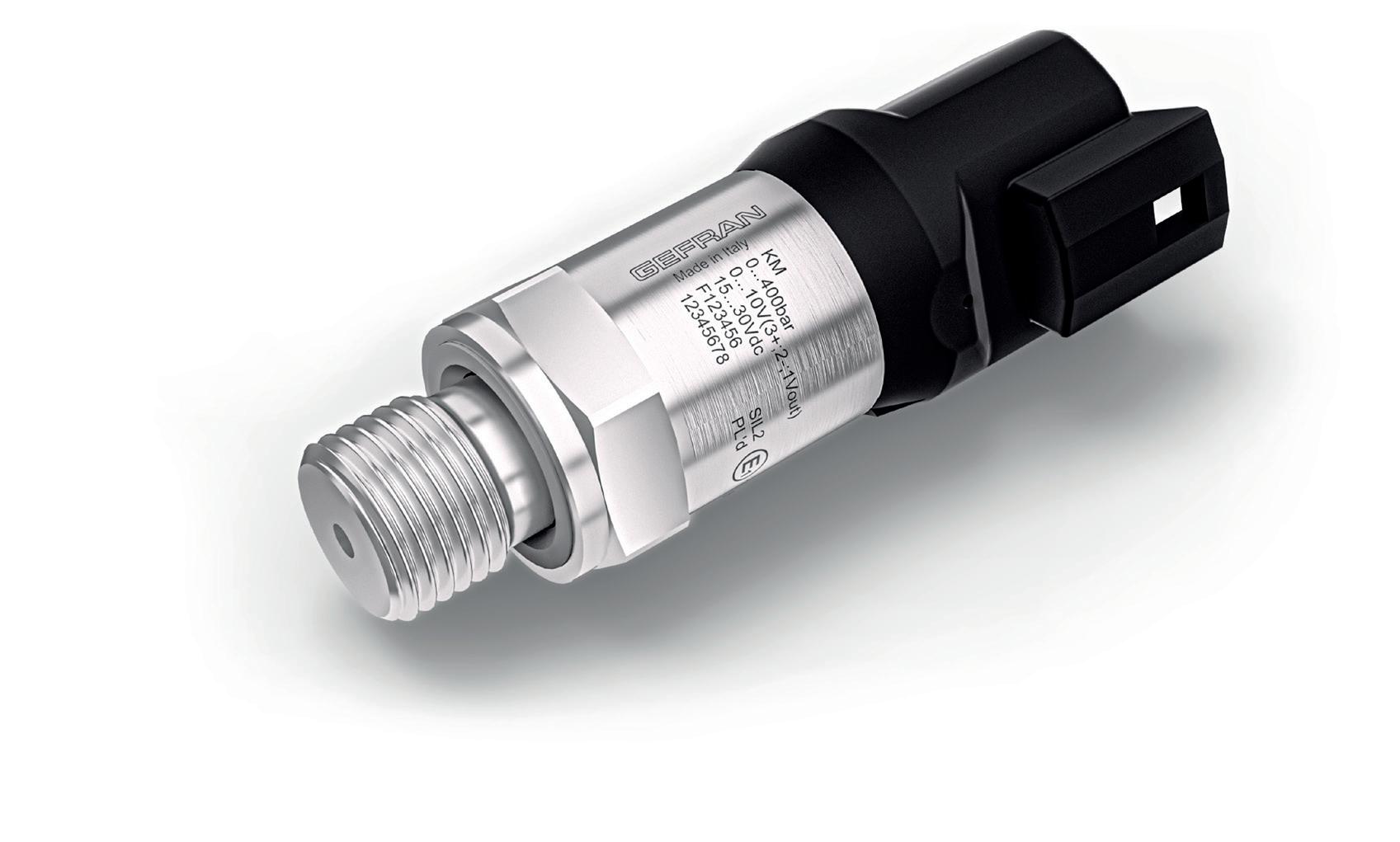
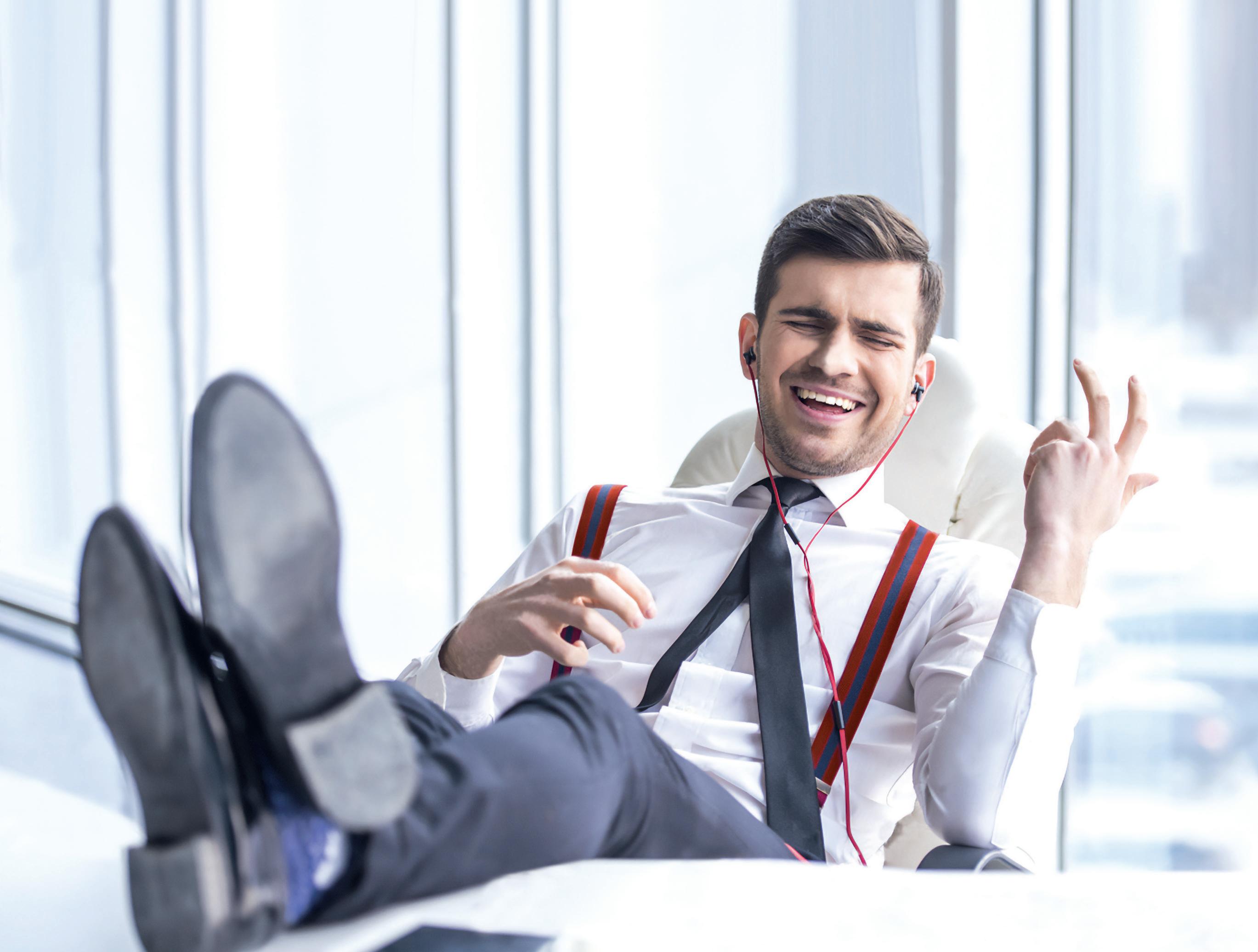
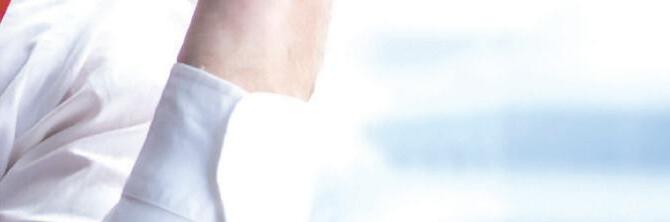
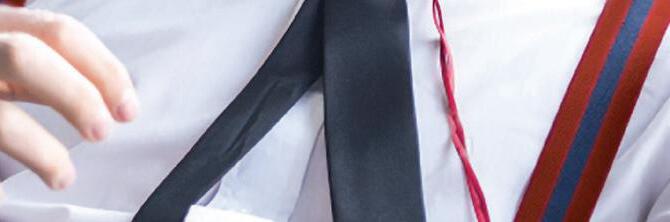
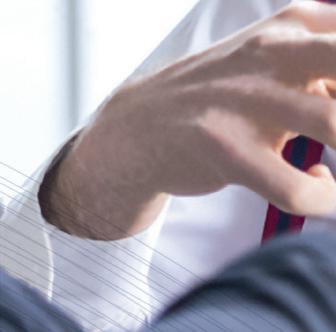

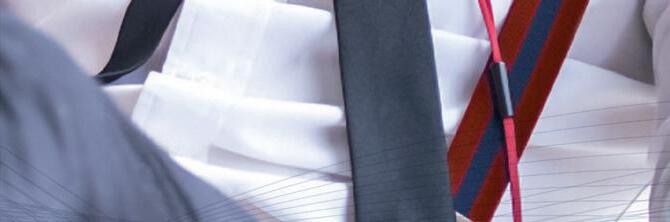
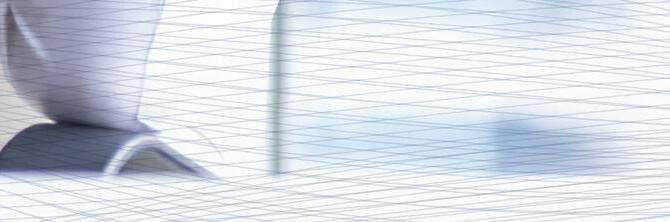
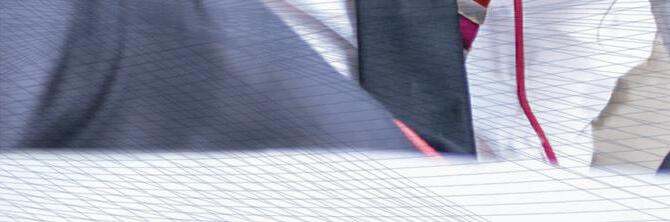
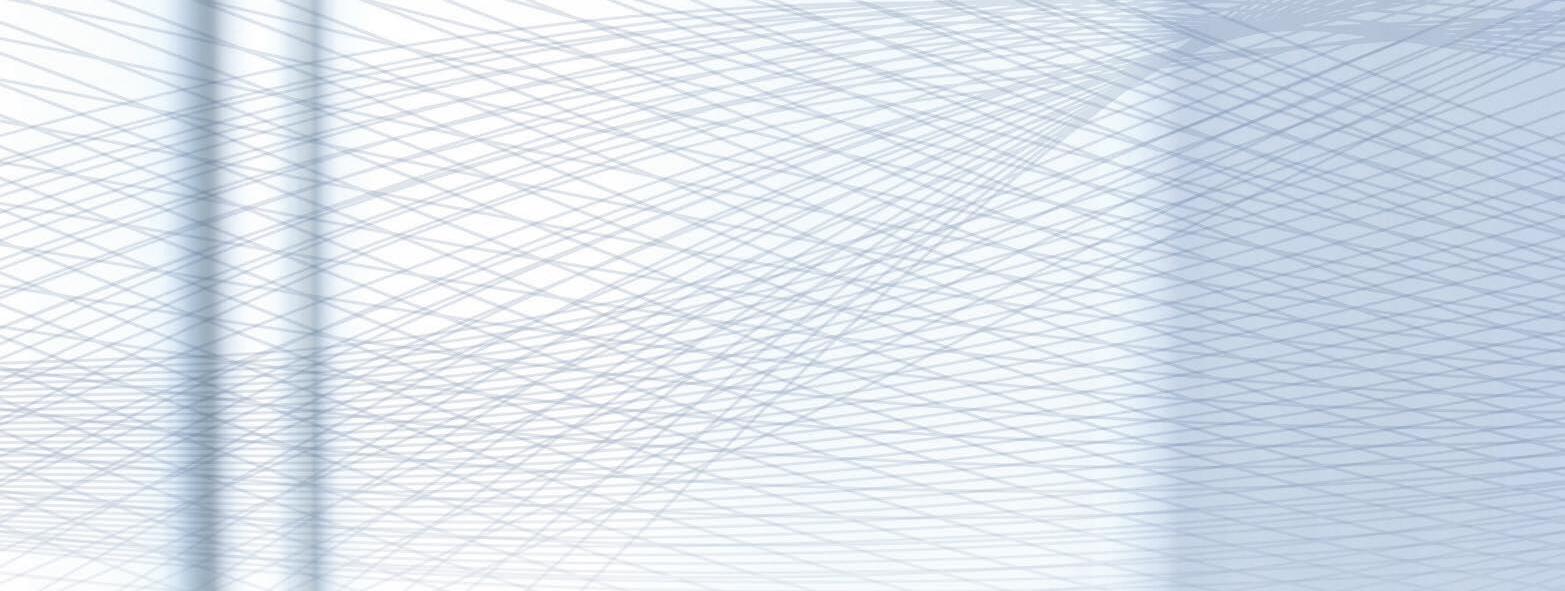

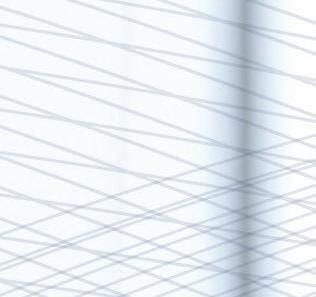
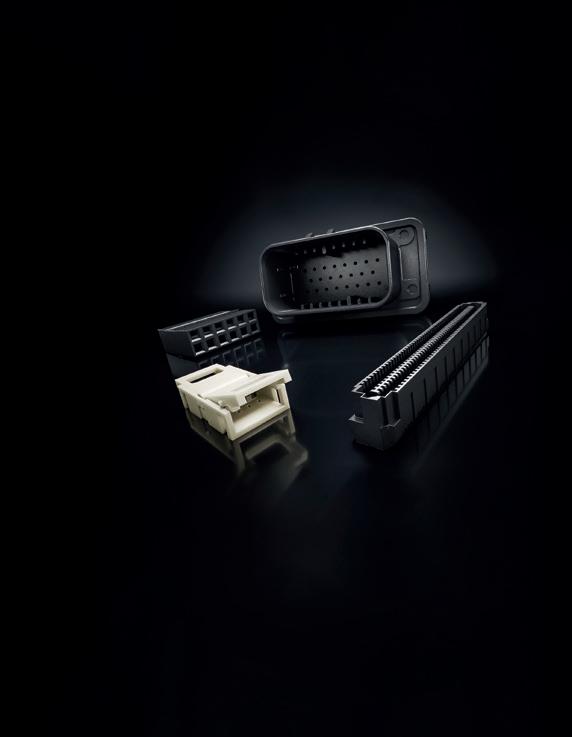


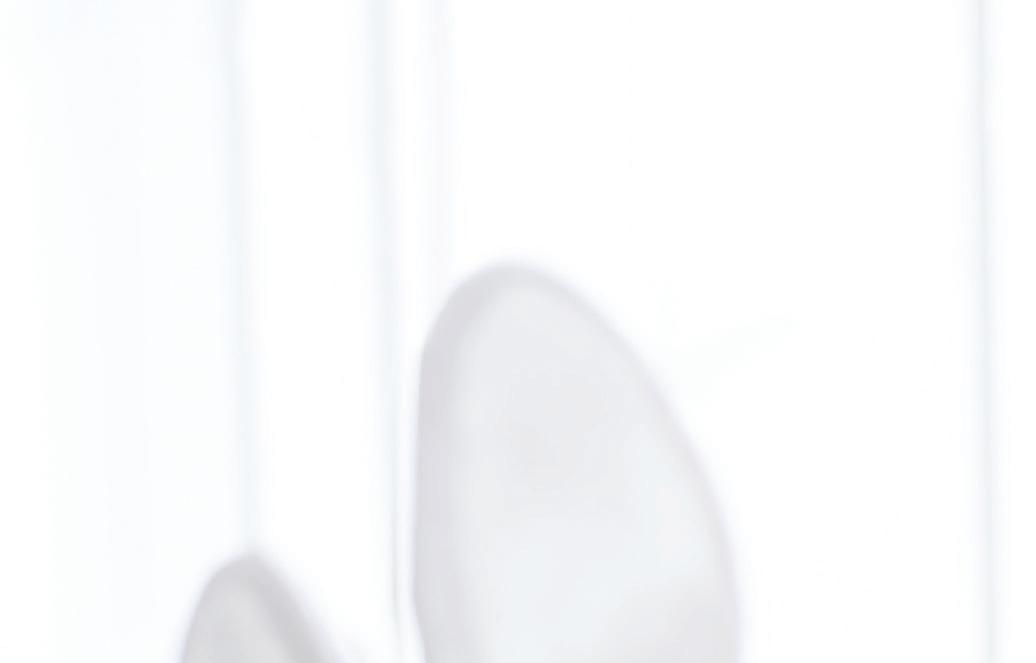
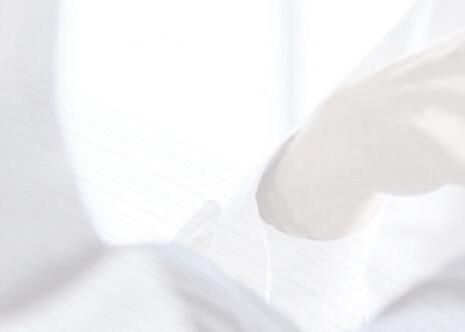
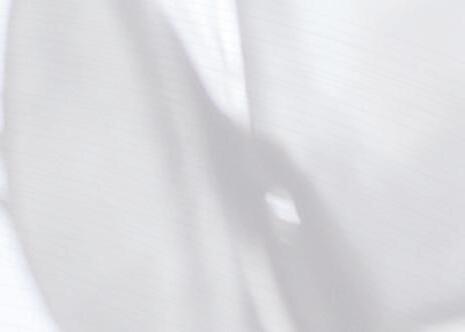
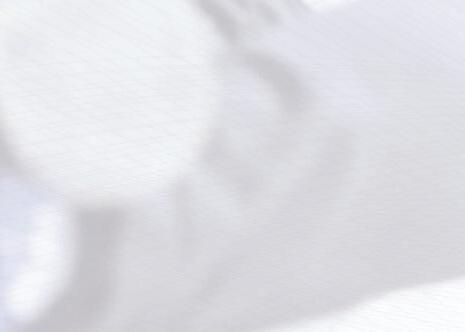

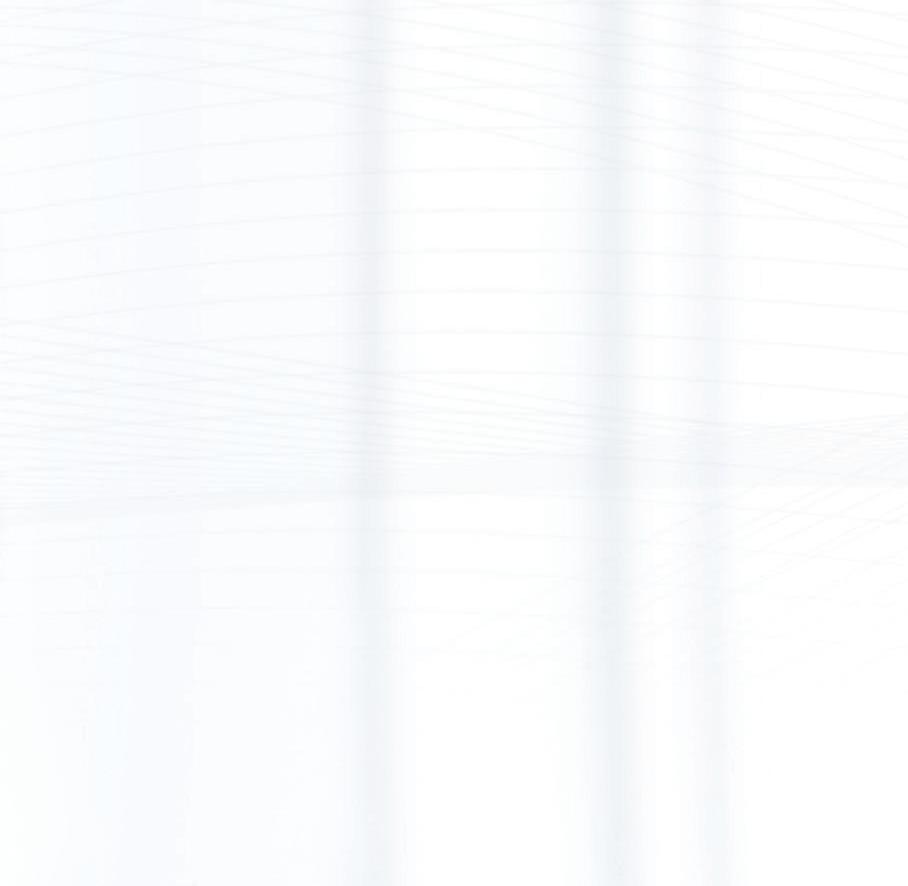
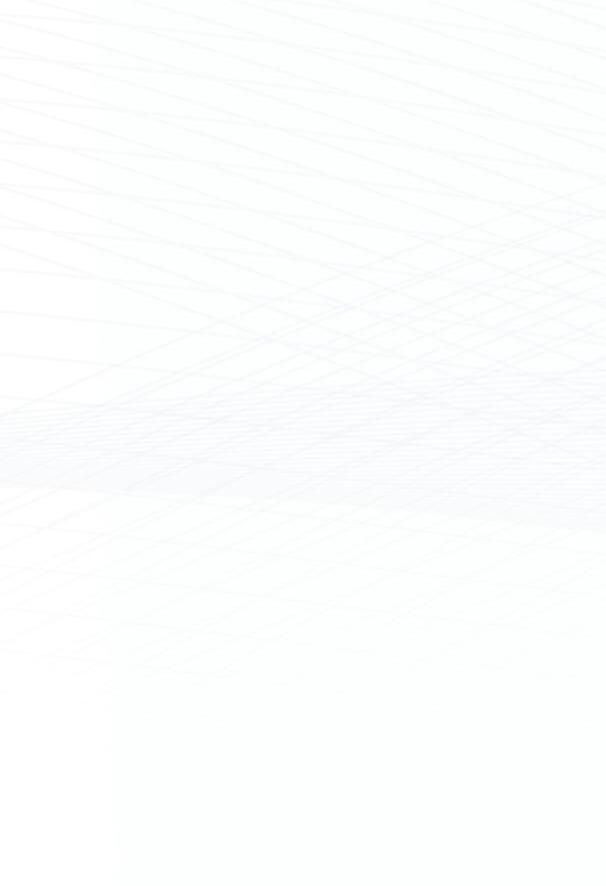
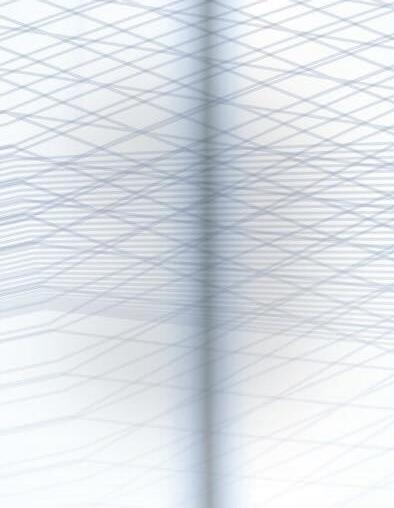
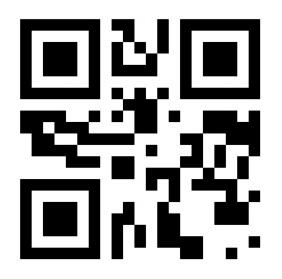


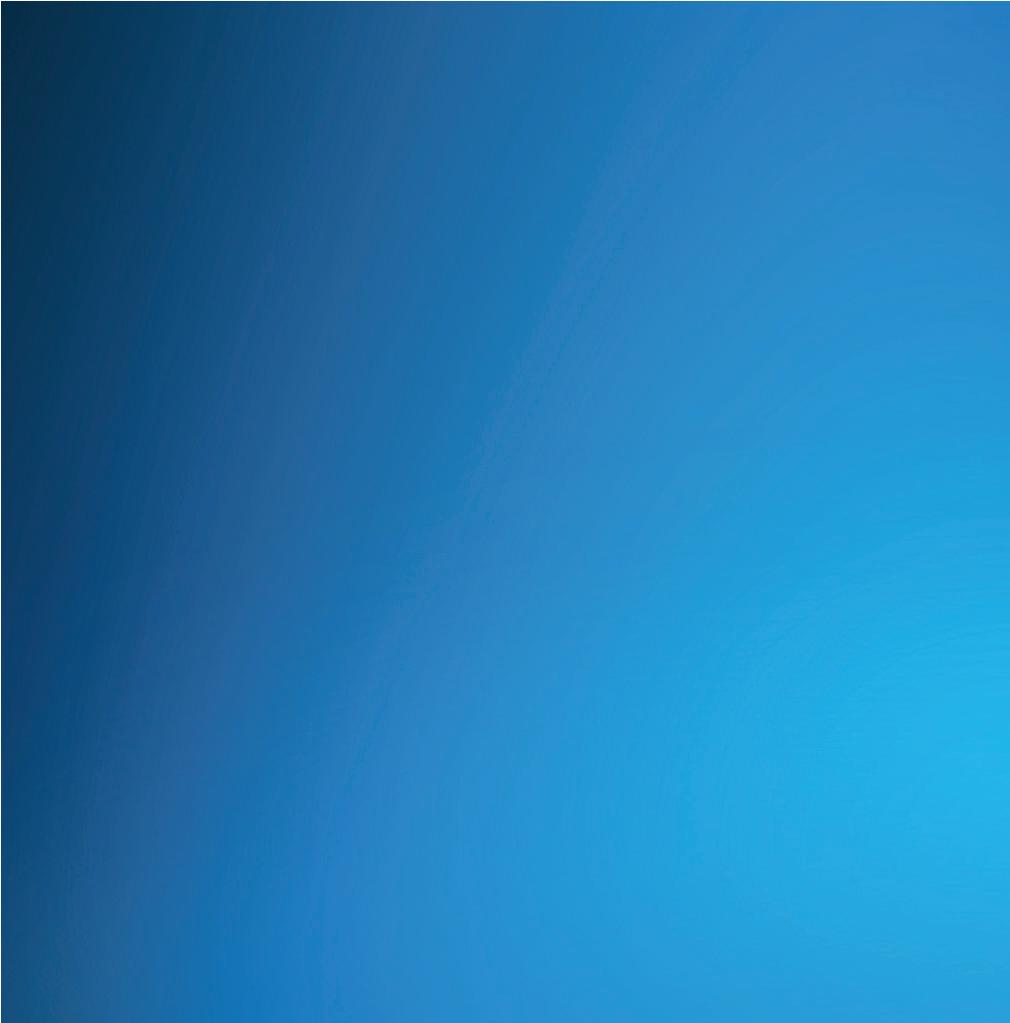
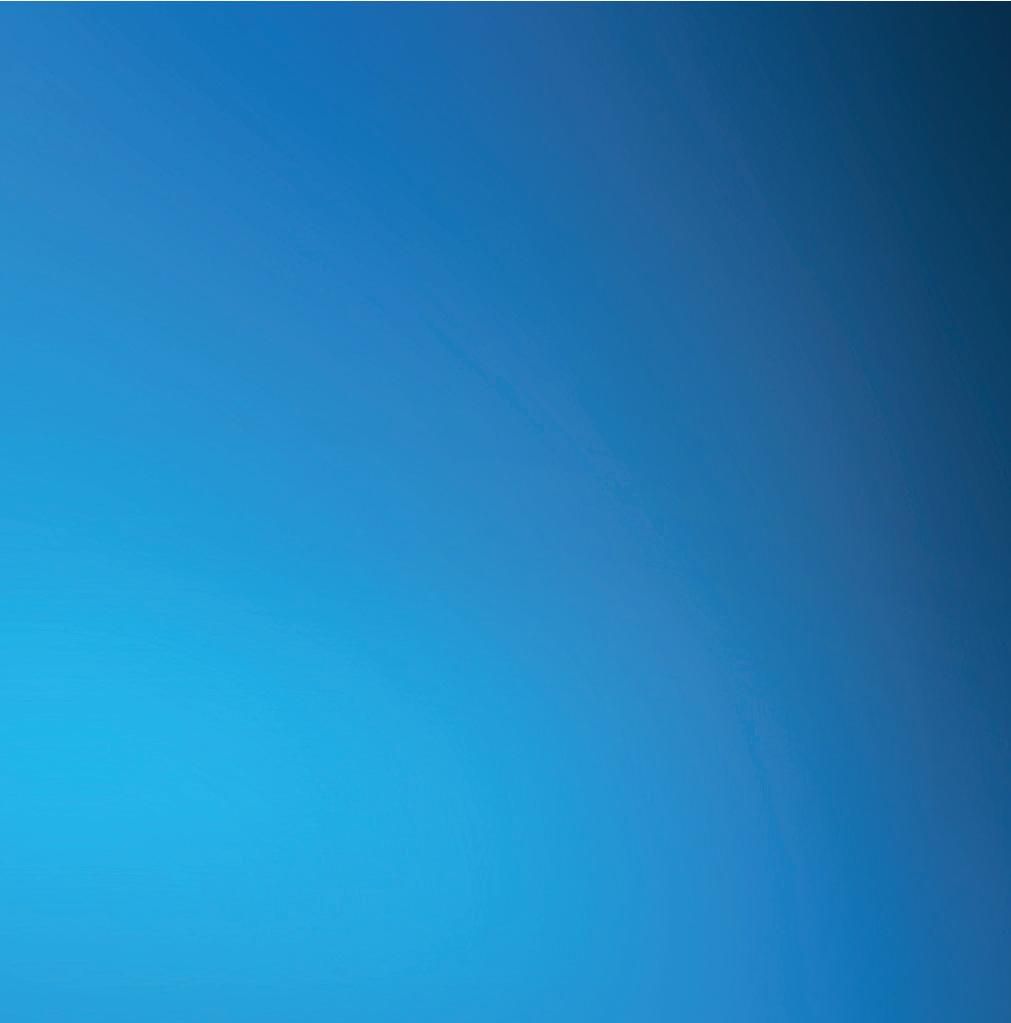

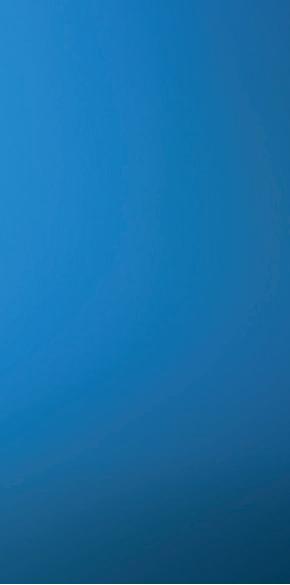

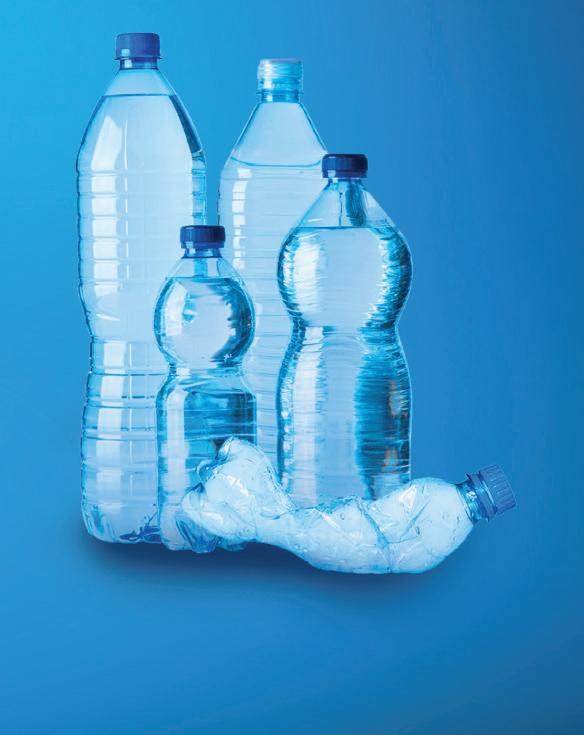
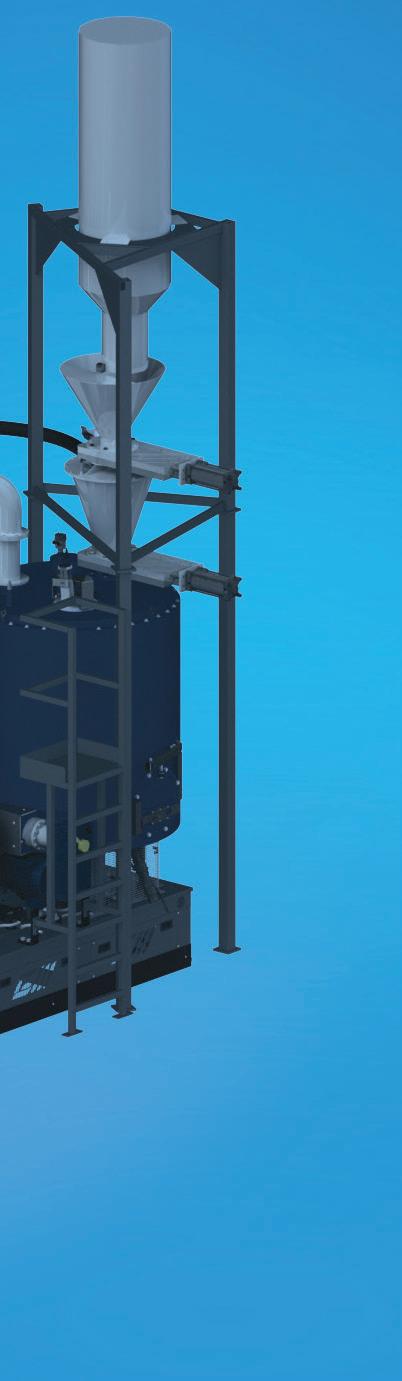
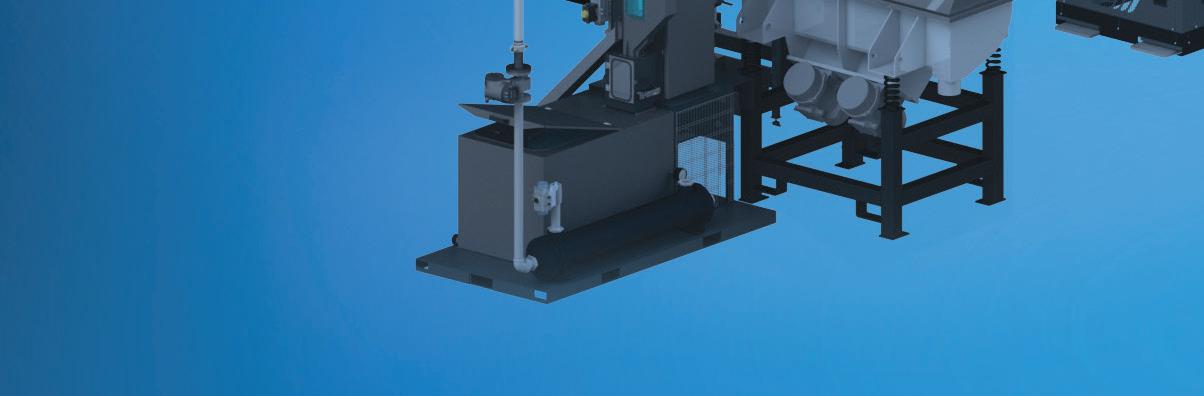

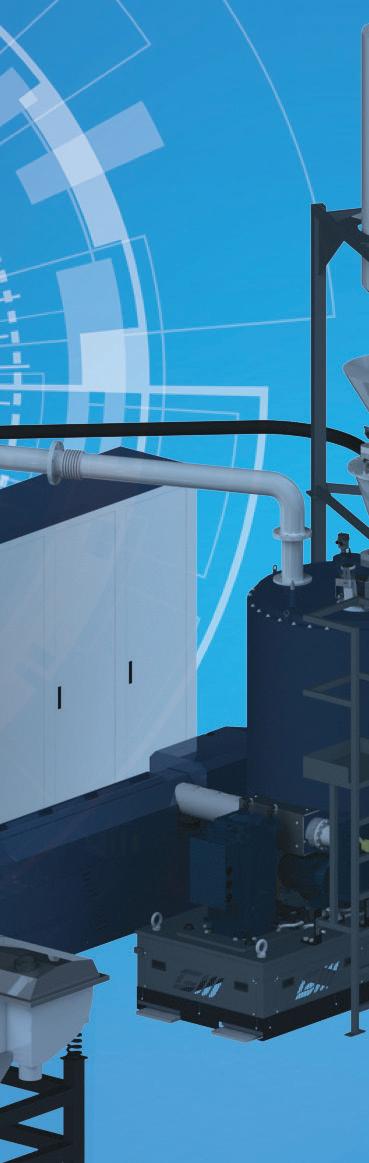

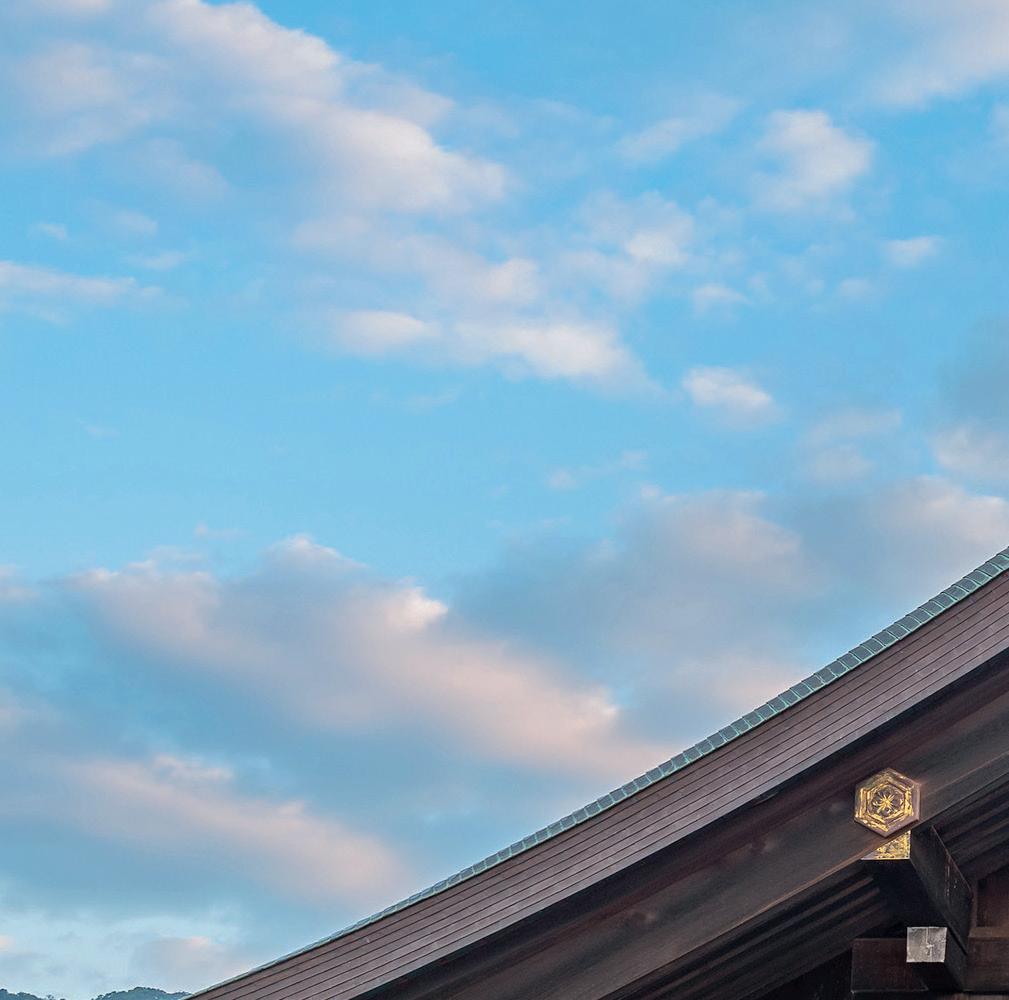


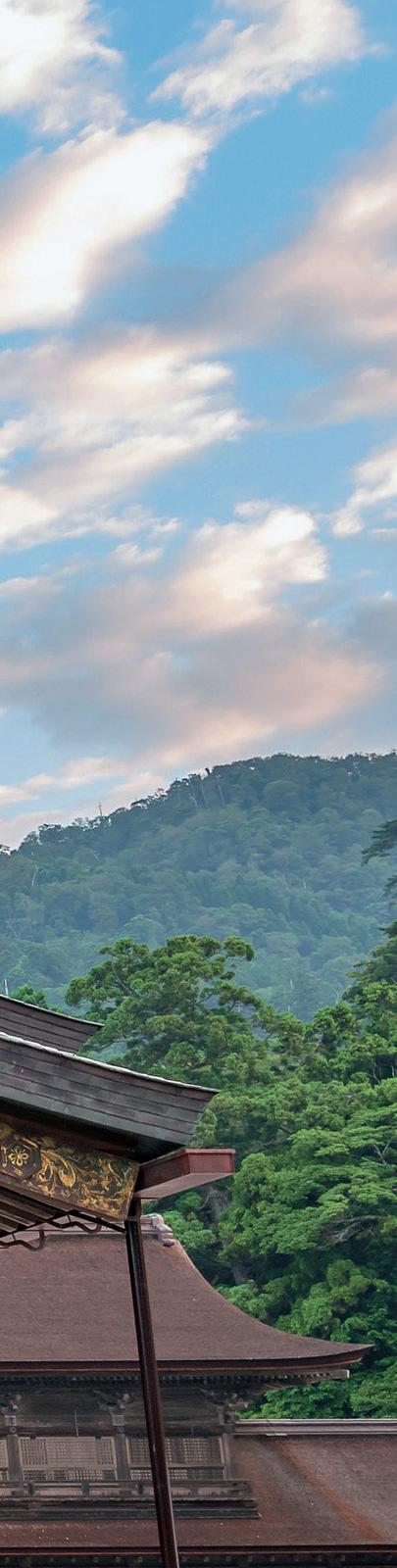
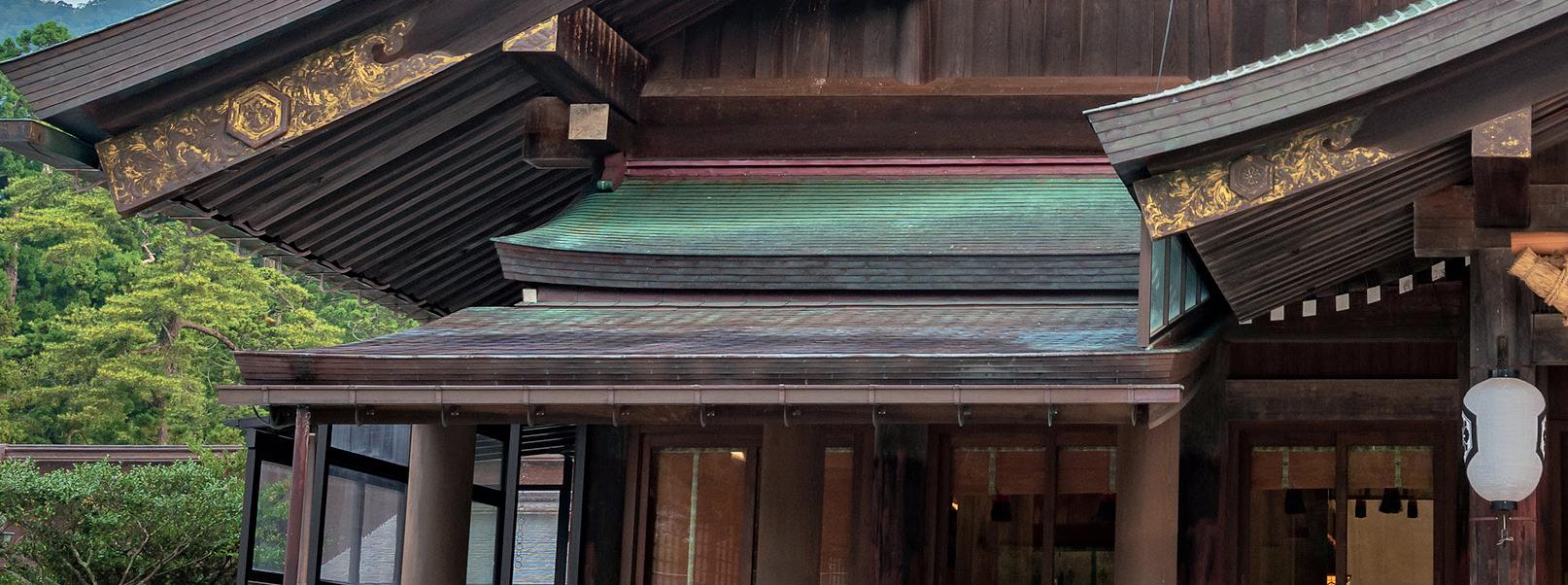
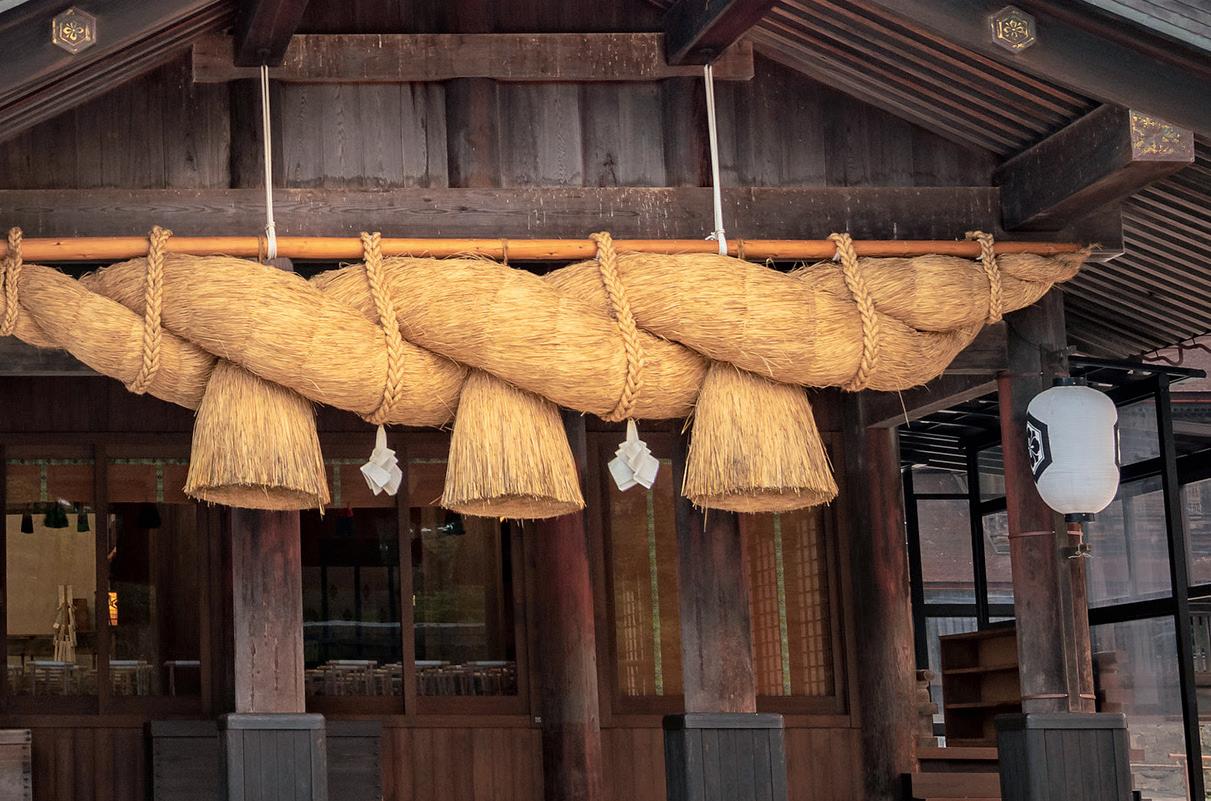
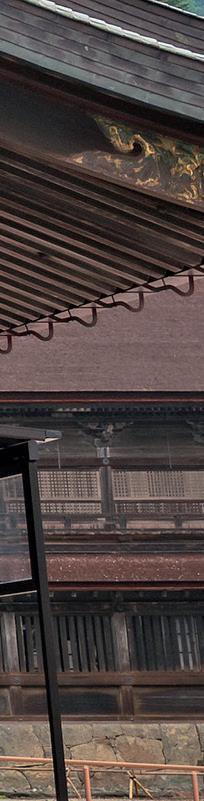

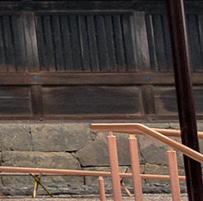
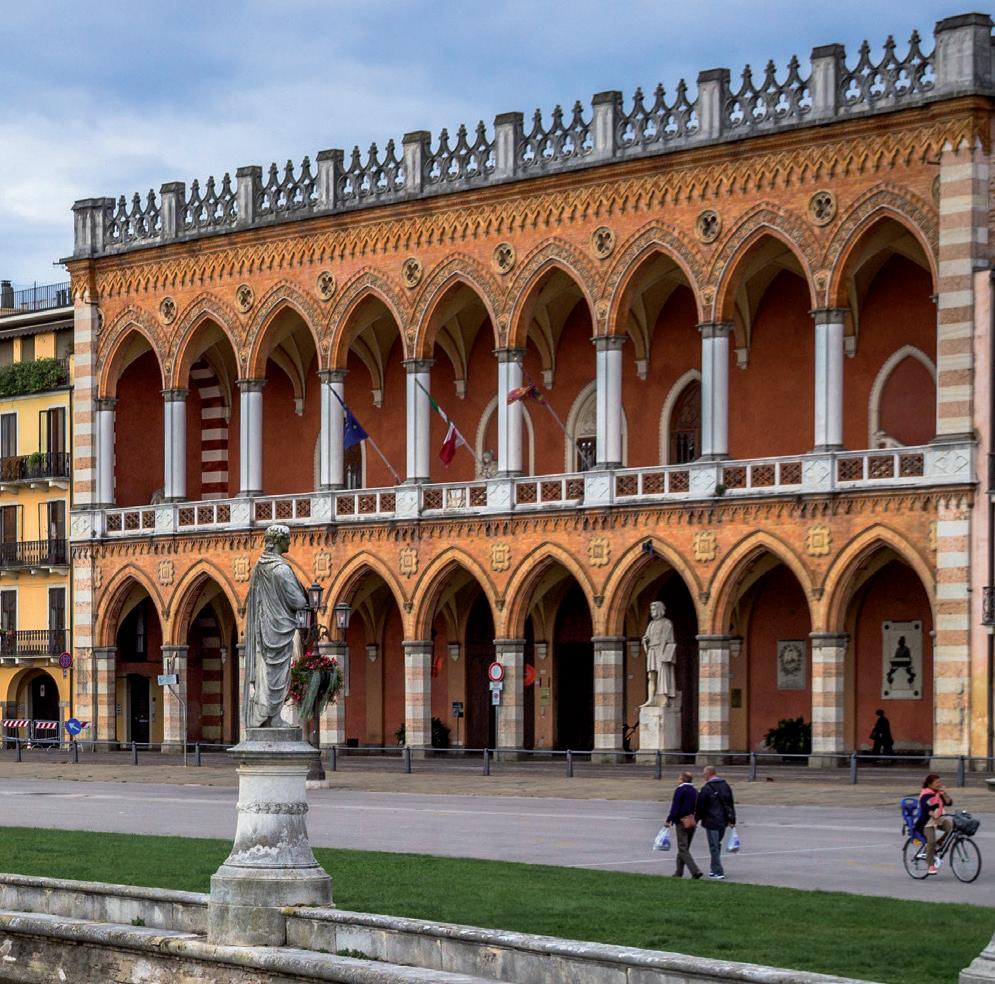
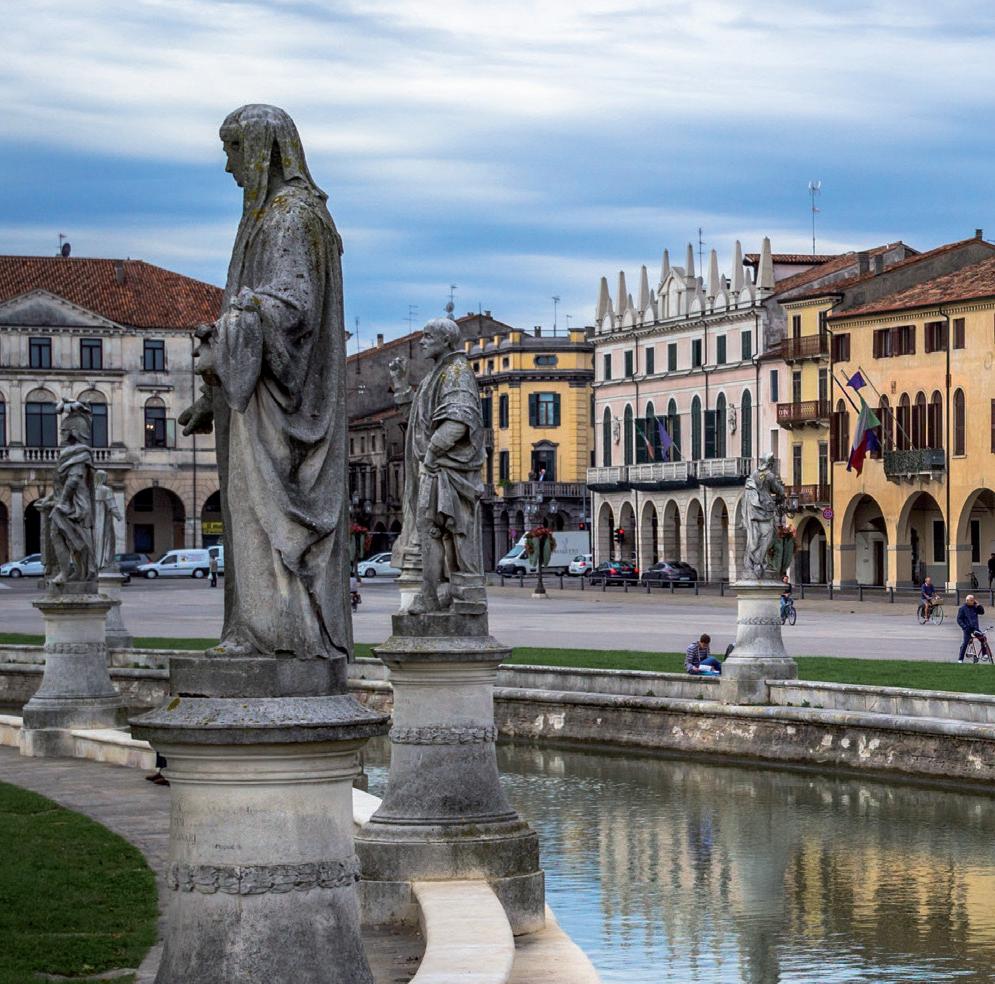

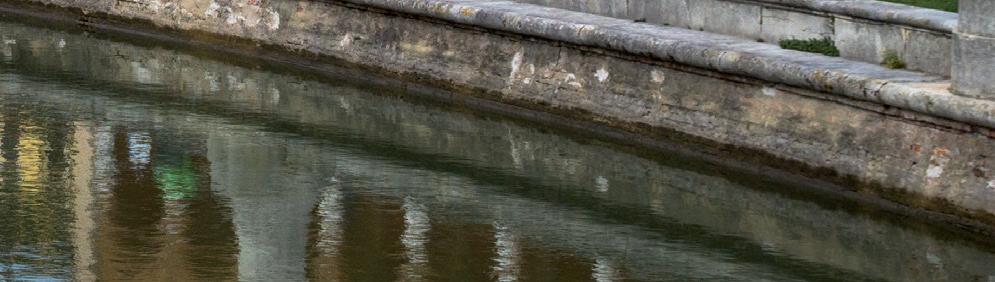

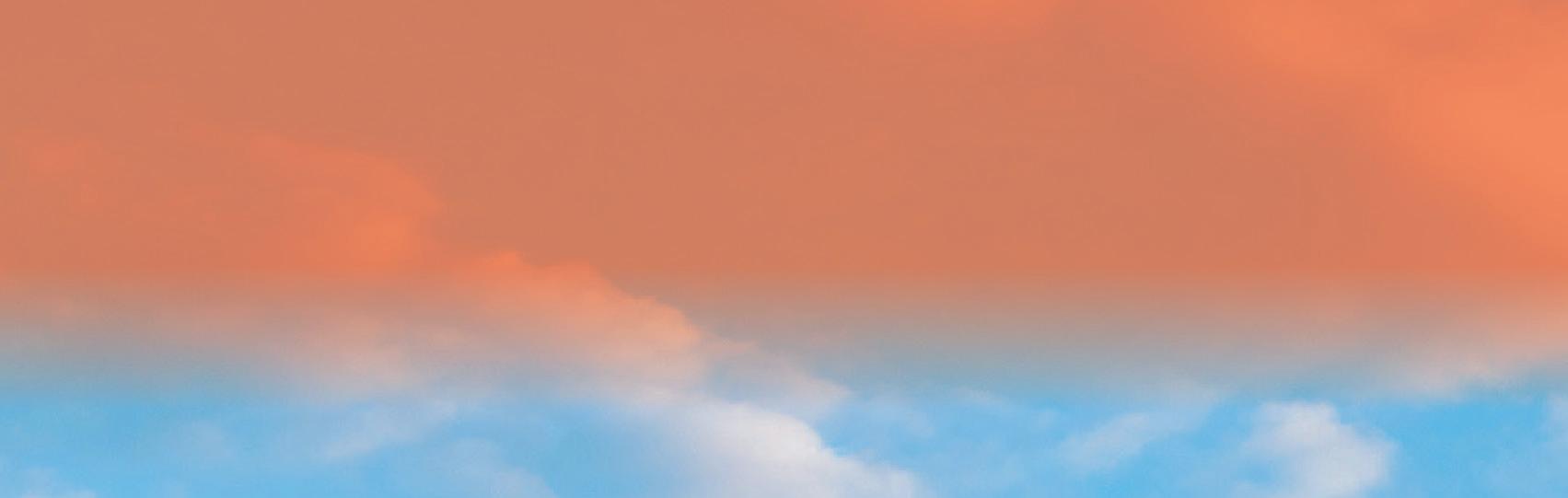
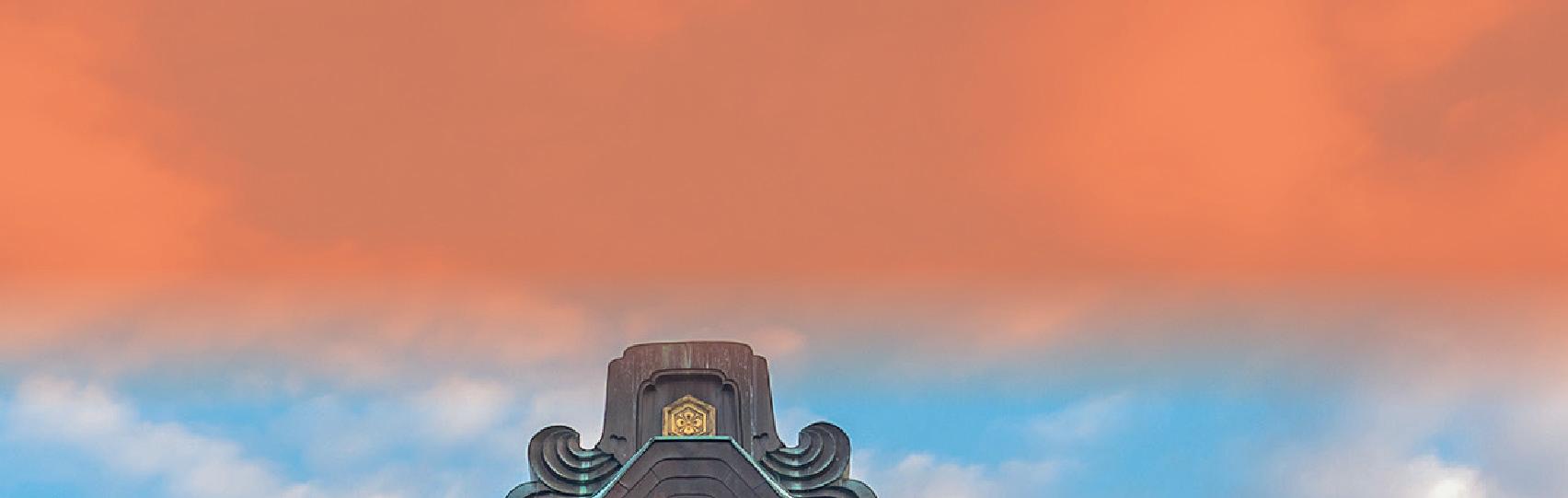
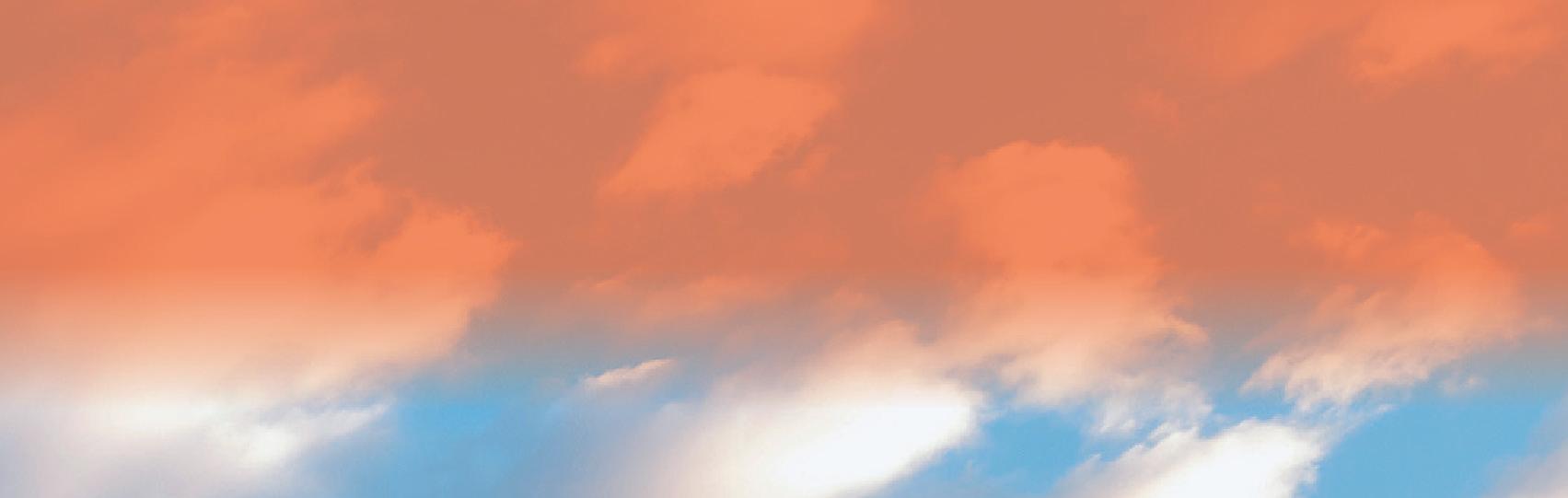
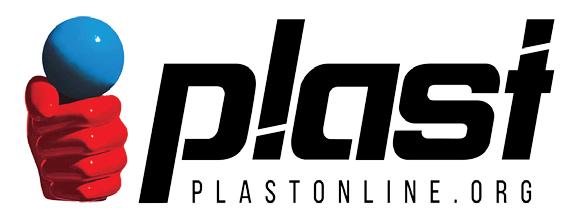
L’azienda bresciana continua a investire in sostenibilità: oltre a presentare la prima pressa completamente elettrica per il mondo della gomma (REM 300), pubblica il primo rapporto di sostenibilità e si sottopone alla certificazione CFP (Carbon Foot Print) di prodotto.
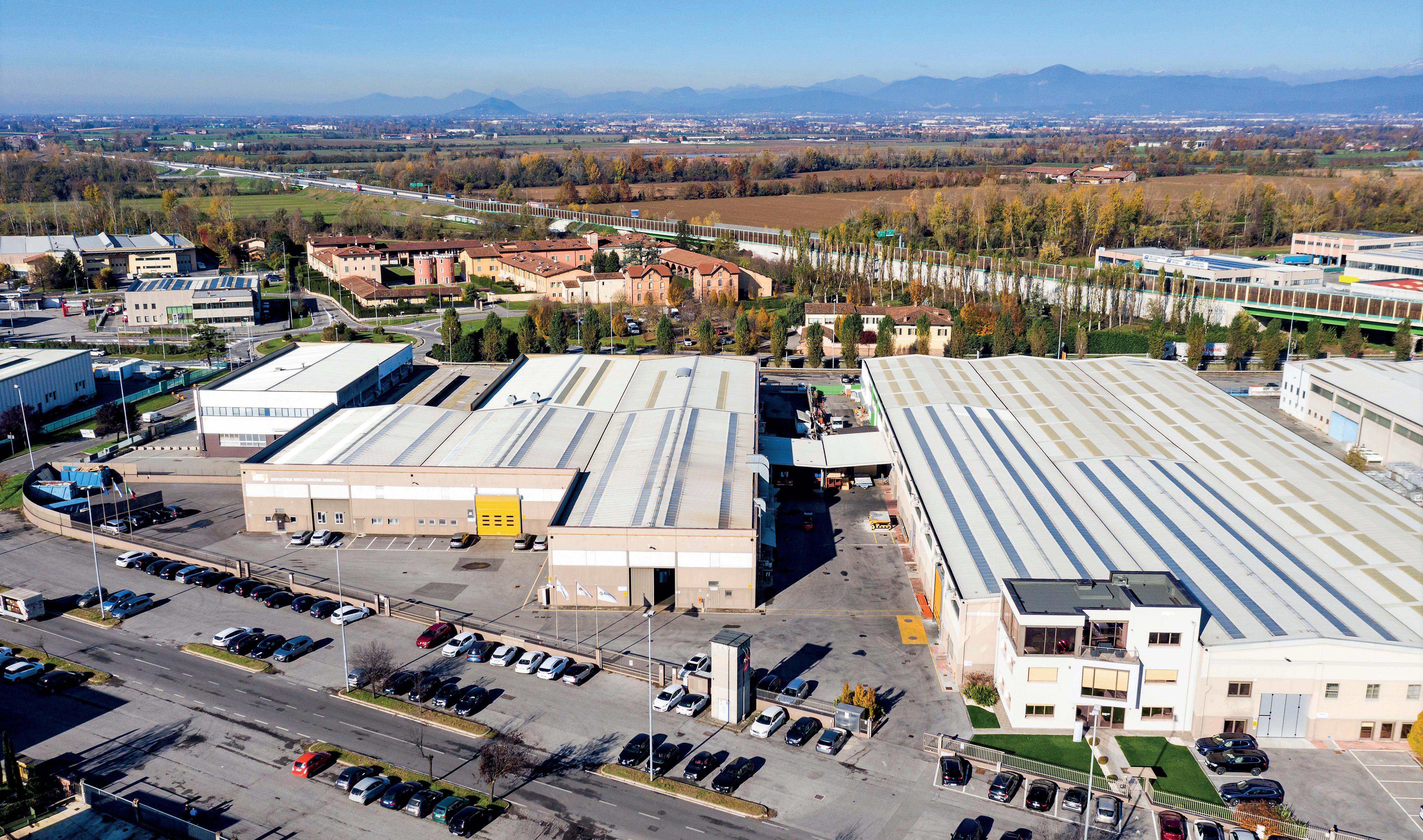
Tra i principali costruttori di presse per lo stampaggio a iniezione di elastomeri e termoindurenti in Italia, IMG prosegue nel suo cammino di sostenibilità. Dopo aver presentato con grande ritorno di interesse il modello REM 300, che viene esposto a Plast 2023, la prima pressa completamente elettrica per il mondo della gomma, nel 2023 pubblica il suo primo rapporto di sostenibilità per presentare gli impegni e le prestazioni dell’azienda nell’ambito dello sviluppo sostenibile, anche in vista della modifica statutaria che porterà IMG a diventare società Benefit.
Una sensibilità condivisa
Tra gli aspetti più rilevanti, quello ambientale è certamente prioritario per IMG, basti pensare alla recente installazione in azienda del nuovo impianto fotovoltaico che rende la produzione completamente autonoma, così come la gestione respon- sabile dei rifiuti aziendali e, quando possibile, la ricerca di fornitori a chilometro zero o, in alternativa, nel territorio di pertinenza.
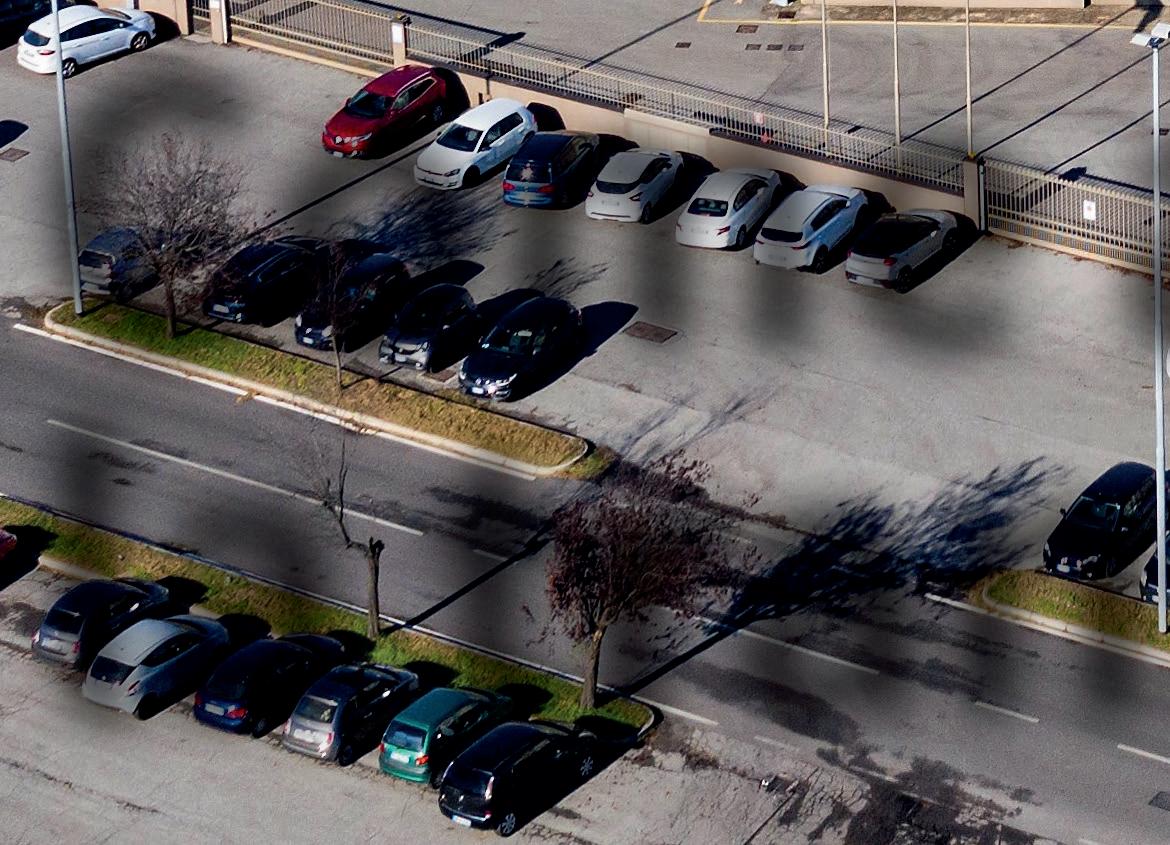
“Un cambio di passo che in IMG è diventato prassi”, ha dichiarato Barbara Ulcelli, amministratore delegato di IMG. “Una sensibilità che in azienda è condivisa a tutti i livelli, come dimostra la nostra indagine interna fatta a gennaio con Nomesis, che ha rimarcato il clima positivo e collaborativo in tutti i reparti, in cui la fiducia verso la capacità di IMG di affrontare le sfide future è alta: il 73% dei collaboratori ha dato un punteggio tra il 7 e il 10 su una scala da 1 a 10”.
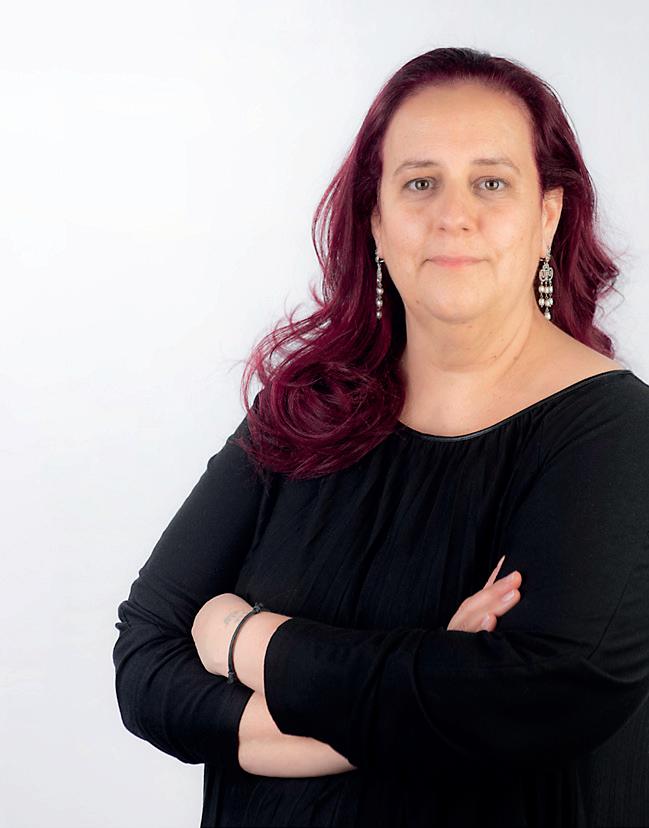
Per dare concretezza all’impegno ambientale, IMG ha svolto uno studio in relazione al modello GUM orizzontale Hydroblock 300 Ton 620 cc, con vite punzonante per calcolare la Carbon Foot Print (CFP): l’obiettivo di questa elaborata analisi consiste nella valutazione dei potenziali impatti ambientali connessi alle emissioni di gas a effetto serra, così come descritta dalla norma UNI EN ISO 14067:2018, associati al ciclo di vita della pressa stessa. Per la raccolta dei dati è stato preso come riferimento il periodo tra gennaio e dicembre 2019. Lo stesso studio è stato applicato al nuovo modello REM 300 completamente elettrico, un macchinario innovativo dal punto di vista tecnologico. La valutazione dei potenziali impatti della pressa risulta importante anche in un’ottica di eco-design e per questo motivo si è scelto di studiarne il ciclo di vita.
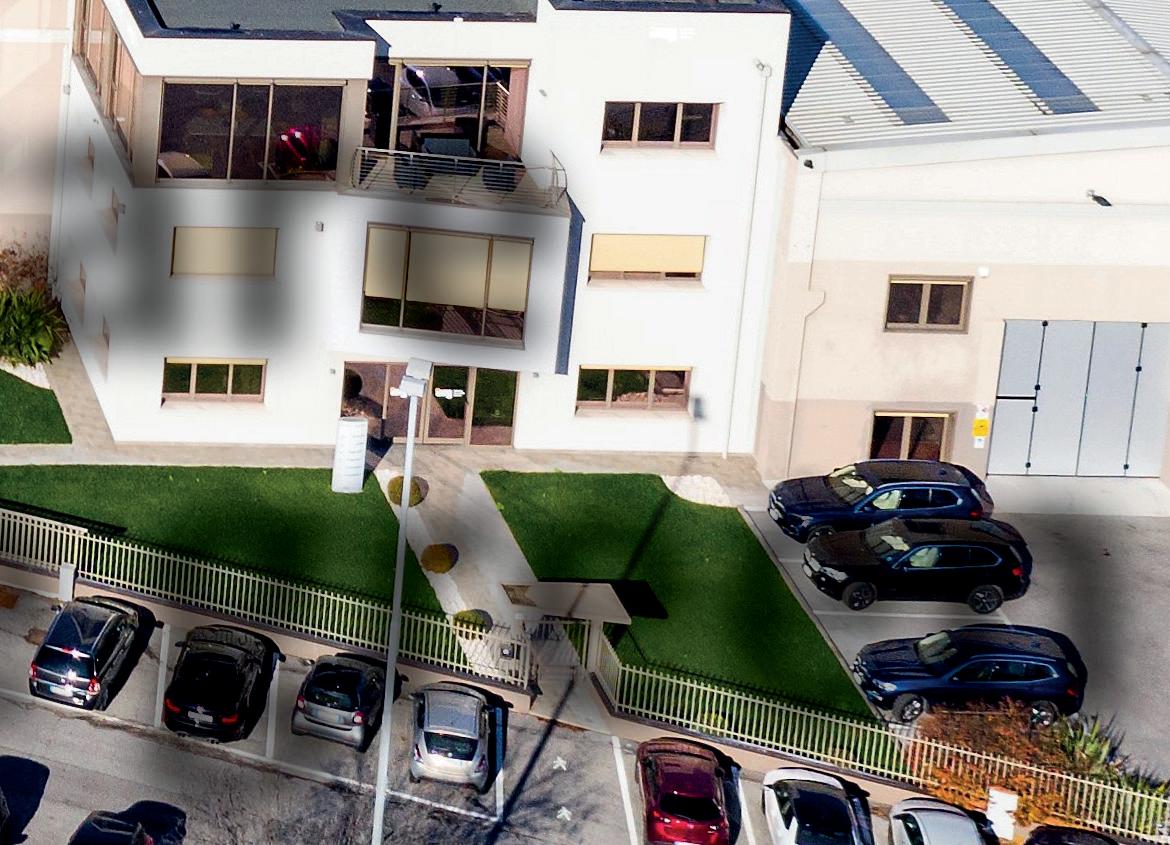
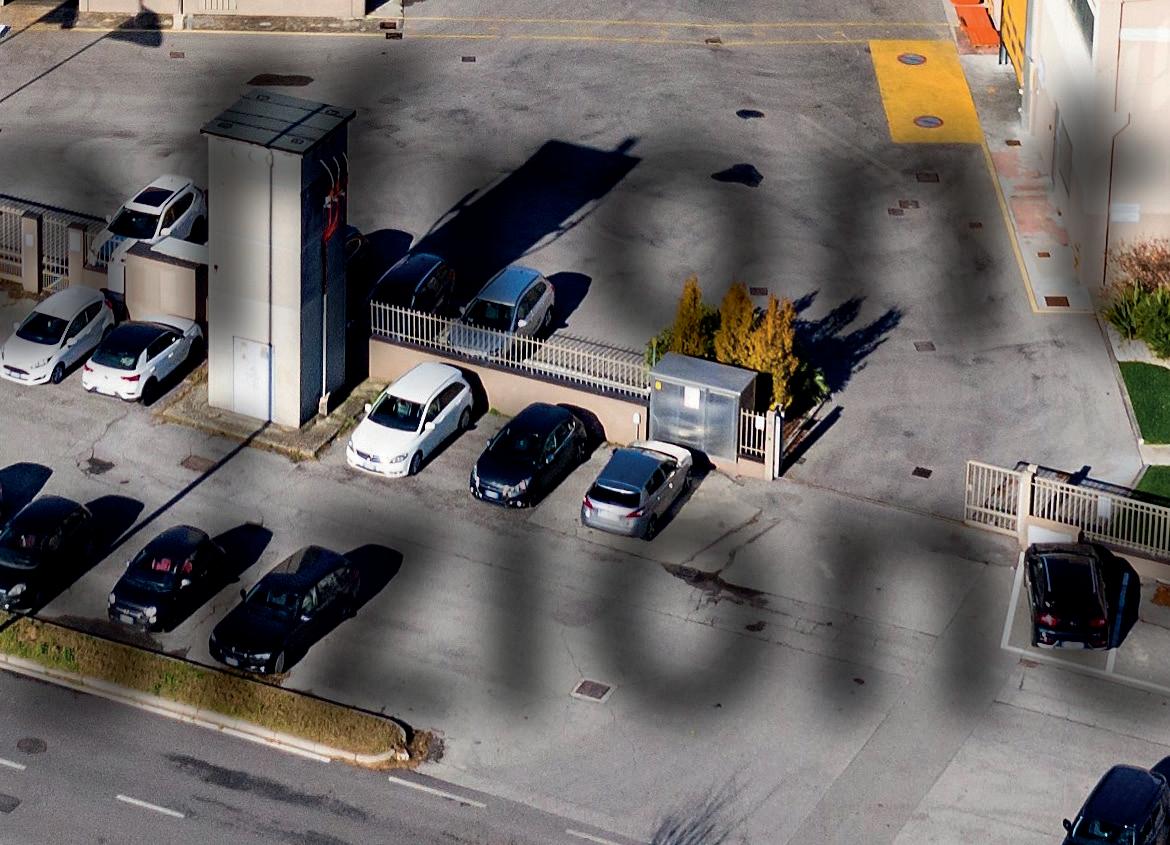
Come ulteriore passo in avanti, nella direzione di un continuo monitoraggio delle proprie strutture per una sempre maggiore efficienza energetica, IMG ha accettato la proposta di Amaplast di sottoporsi al calcolo della CFP di processo dell’intera organizzazione. Lo studio (limitato allo “Scope 2”), attraverso l’analisi delle emissioni dirette e indirette, permetterà la determinazione di un valore di emissione di CO2 per l’anno 2022.
Anche la transizione all’Industria 4.0 si sta compiendo, da un lato con il Light Machine Learning, dall’altro con la realizzazione a più ampio respiro di presse auto-adattive e la modellizzazione del processo di stampaggio della gomma. IMG si sta impegnando anche con continui investimenti in ricerca e sviluppo sulle applicazioni dell’intelligenza artificiale dedicata alle presse a integrazione dei programmi Machine Learning IoT.
Un’ottica orientata al futuro
Gli studi per realizzare prodotti sempre più performanti vanno tutti nella direzione di un efficientamento delle risorse. In un’ottica orientata al futuro, in cui l’attenzione alle ricadute che la produzione industriale genera, IMG è riuscita a portare sul mercato un prodotto inedito ad alto tasso di innovazione, con consumi abbattuti del 20% rispetto a una normale pressa idraulica.
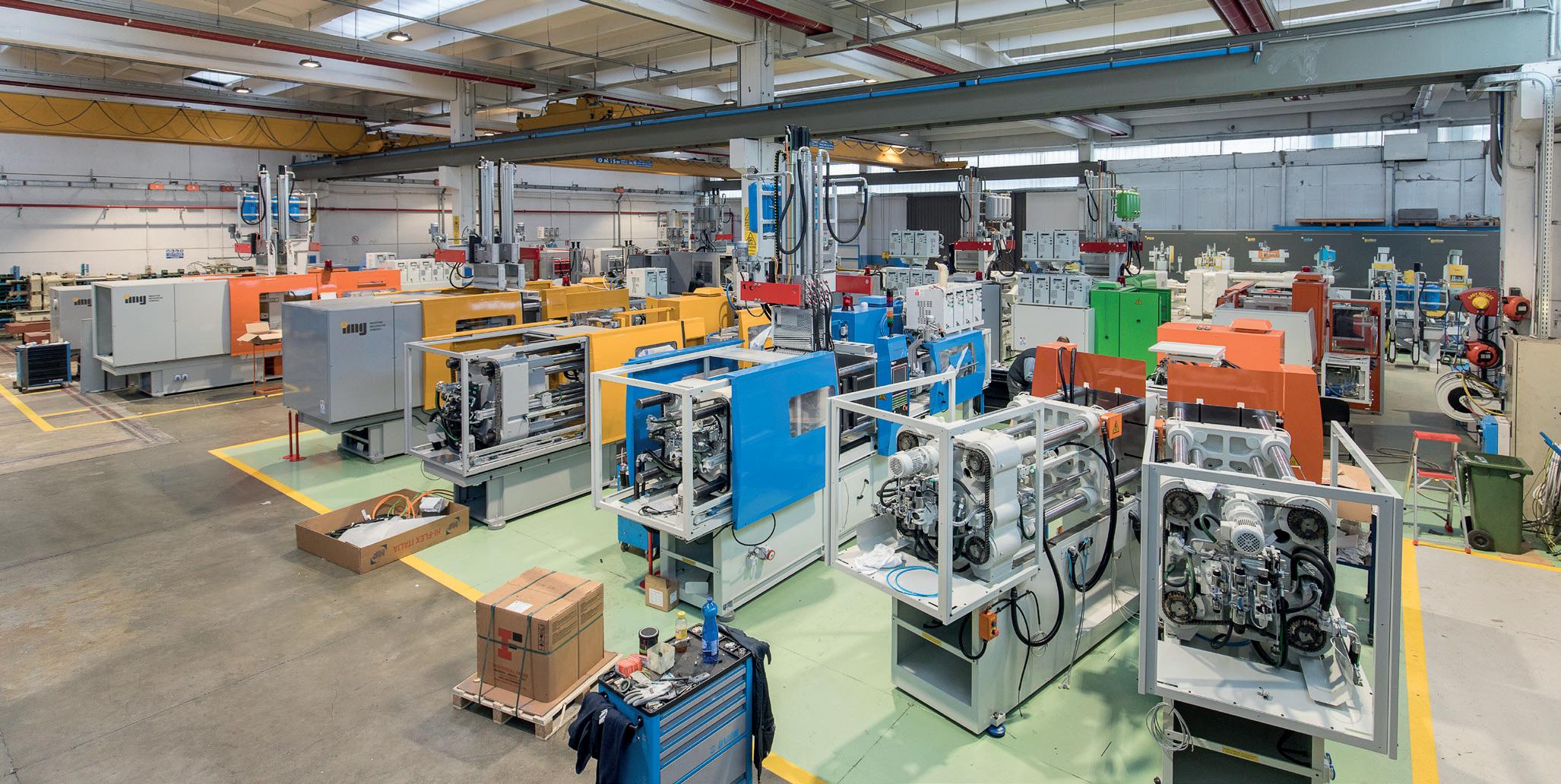

Un’assoluta novità nel settore dello stampaggio di prodotti in gomma, che vanta una forza di chiusura di 3.000 kN e numerosi elementi migliorativi. Dopo decenni di utilizzo di presse oleodinamiche (dagli anni Cinquanta a oggi), la ricerca e sviluppo di IMG ha voluto puntare sulle migliori tecnologie oggi disponibili per predisporre una macchina in grado di ridurre concretamente l’impatto ambientale delle attività industriali di stampaggio degli elastomeri.
La REM 300 funziona senza olio idraulico, sostanza che, solitamente, nelle presse va cambiata ogni 5.000 ore. Un importante costo in meno in termini di approvvigionamento e di smaltimento, visto che con la REM 300 non è più necessario smaltire un rifiuto considerato speciale. Un grande passo avanti anche per quanto riguarda le prestazioni: l’elettronica gestionale di questa innovativa pressa consente un monitoraggio estremamente più preciso di tutte le funzioni e, pertanto, un livello di performance decisamente superiore nella qualità della stampata, nella movimentazione dei corpi interni e nella misurazione e impostazione dei tempi di lavoro. Il setup è facile e intuitivo e l’attuazione elettrica consente maggior velocità, precisione, minor scarto di produzione e ripetibilità delle azioni per evitare difformità.
La REM 300 è dotata di nuovi dispositivi IoT (Internet of Things) come sensori vibrazionali, trasduttori in IO-Link e driver con librerie di diagnostica predittiva per la rilevazione e il controllo delle prestazioni, anche da remoto. La pressa garantisce poi una diminuzione dei consumi energetici grazie al “plug and play”, che permette l’utilizzo della corrente solo negli effettivi momenti di necessità. Tutto ciò si traduce in una importante riduzione dei costi di produzione.
“Una nuova tecnologia che esiste nel mondo della plastica, ma non in quello della gomma, frutto di ingenti investimenti in ricerca e sviluppo dell’azienda”, ha spiegato Barbara Ulcelli. “Impatto ambientale, controllo dei costi e sicurezza sono oggi i tre elementi sui quali il mercato è divenuto estremamente sensibile e che pertanto aprono spazi importanti di crescita. Un cambio di paradigma che IMG sta maturando nei confronti della sostenibilità: una visione green che trova concretezza in un prodotto con caratteristiche rivoluzionarie. Una novità altamente differenziante nel settore delle presse per elastomeri che, ancora una volta, dimostra l’attenzione di IMG verso una continua innovazione tecnologica a supporto della propria clientela”.
Da ultimo, ma non meno importante, l’aspetto della silenziosità: in un contesto lavorativo in cui il rumore è un fattore disturbante, la REM 300 è a minor impatto per quanto riguarda le emissioni acustiche, altro elemento di attenzione nei confronti dell’operatore. Ma lo sviluppo va oltre il prodotto: IMG, infatti, garantisce un servizio di assistenza continuativo per ogni evenienza.
Grazie al suo alto tasso di innovazione REM 300 risulta fra i vincitori del bando Tech Fast della Regione Lombardia.
Come è possibile risparmiare tempo e costi con l’integrazione di funzionalità diverse? Lo dimostra Arburg a Plast 2023 attraverso partner e applicazioni come i connettori Luer, utilizzati come chiusure nell’industria farmaceutica, tappati e svitati direttamente nello stampo. Questa soluzione innovativa elimina la necessità di un secondo stampo e di una linea di assemblaggio aggiuntiva, riducendo significativamente i costi e aumentando l’efficienza. In mostra anche gli articoli stampati in bicomponente su una Allrounder More 1600, assistita da un robot a sei assi.

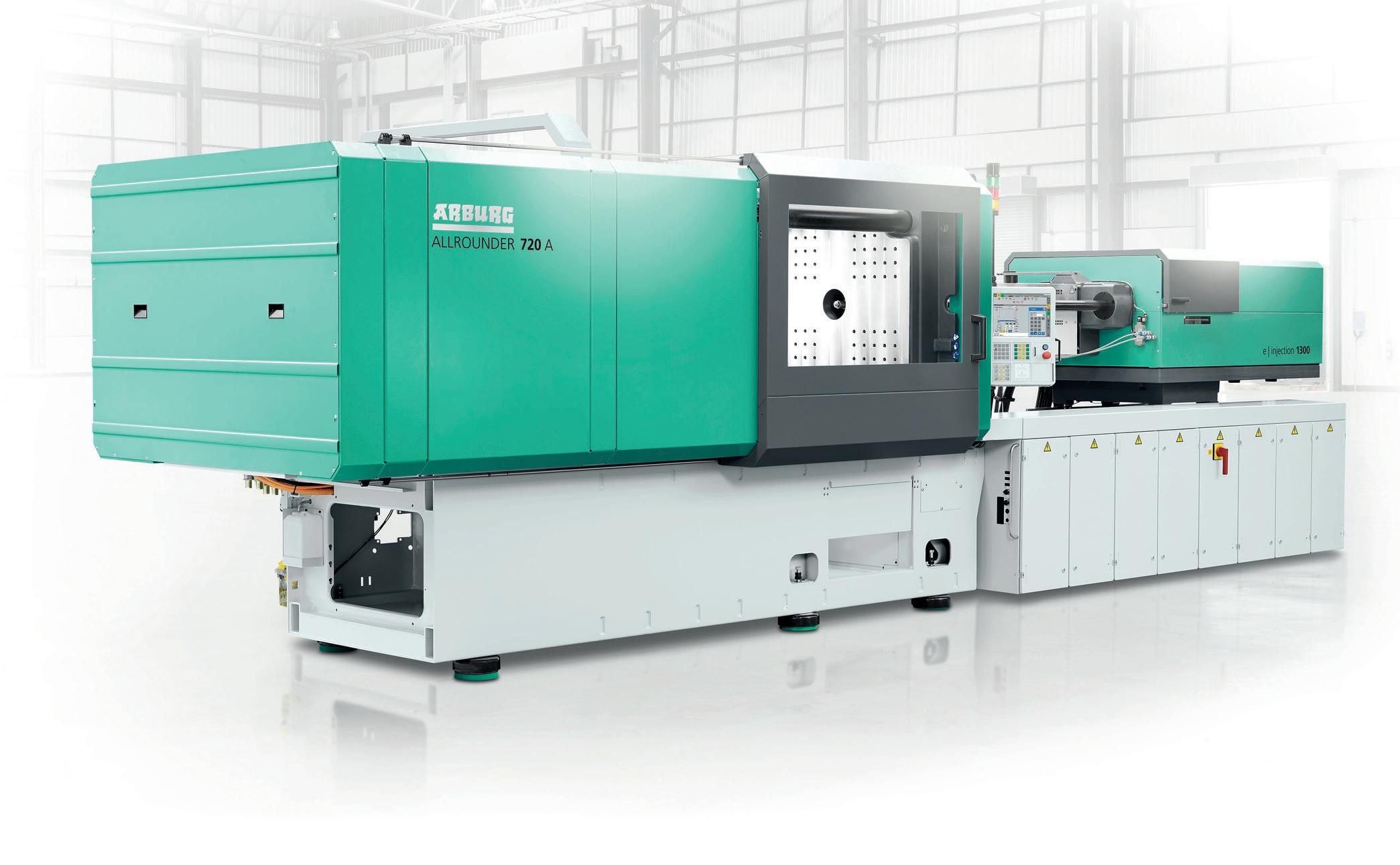
Precisione negli spazi minimi
In un tempo ciclo di soli dieci secondi vengono prodotti quattro connettori Luer. Durante lo stampaggio a iniezione è richiesta precisione e accuratezza: il peso della stampa dei componenti in PP è di soli 0,2 g, mentre i componenti in TPE pesano soltanto 0,05 g. in questo caso il materiale viene realizzato attraverso materie prime rinnovabili e riciclate chimicamente (ISCC Mass Balance). Lo stampo 4+4 cavità dispone della tecnologia RotaricE2 di Braunform dove i quattro assi servoelettrici della consociata di Arburg AMKmotion, monitorati dal sistema di controllo Gestica, controllano le procedure interne dello stampo per core-back, il sollevamento del coperchio, la tappatura delle chiusure e lo svitamento della filettatura Luer.
Produttività preprogrammabile e robot
Tramite la funzione di assistenza aXw Control CycleAssist l’unità di comando Gestica conosce il ciclo programmato e rappresenta graficamente i tempi effettivi di ciascuna fase in base ai valori di riferimento precedentemente definiti, ripartiti in modo dettagliato per tempi di avvio, tempi di ritardo e durata di funzionamento. In questo modo è possibile visualizzare i tempi di non funzionamento e, di conseguenza, preprogrammare un aumento della produttività.
Inoltre, in Gestica è integrata la tecnica di comando del robot a sei assi Yaskawa che, proprio come nel caso dei sistemi robot Multilift lineari, può essere programmata in maniera semplice e rapida direttamente nell’unità di comando della pressa. Il robot industriale “powered by Arburg” viene presentato a Plast 2023 con un programma di automazione già ampliato nella primavera 2023 che permette di prelevare pezzi finiti con una mano di presa a 4 dita dallo stampo e, prima di depositarli, li porta singolarmente al controllo mediante telecamera, ordinati per cavità negli appositi contenitori.
Sempre più Allrounder
Le Allrounder More, concepite per applicazioni multicomponente, possono essere adattate in maniera versatile ai singoli requisiti dei clienti e del mercato. Inoltre, offrono un maggior spazio per gli stampi più grandi, una migliore corsa utile degli estrattori e una più adeguata modularità dal punto di vista strutturale. Le presse dispongono di un gruppo di chiusura a ginocchiera elettrico altamente dinamico con servomotori raffreddati a liquido altamente efficienti dal punto di vista energetico, due unità di iniezione e forza di chiusura 1.600 o 2.000 kN.
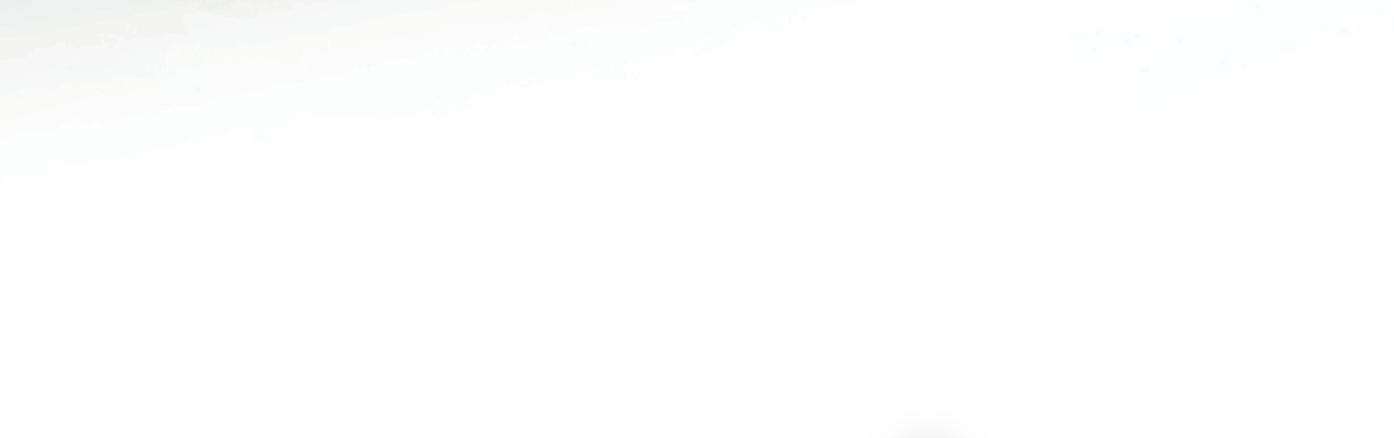


A Plast 2023 una Allrounder More con forza di chiusura di 1.600 kN realizza connettori Luer in PP e TPE. Le presse per stampaggio multicomponente possono essere automatizzate in maniera versatile con robot lineari e multiasse.
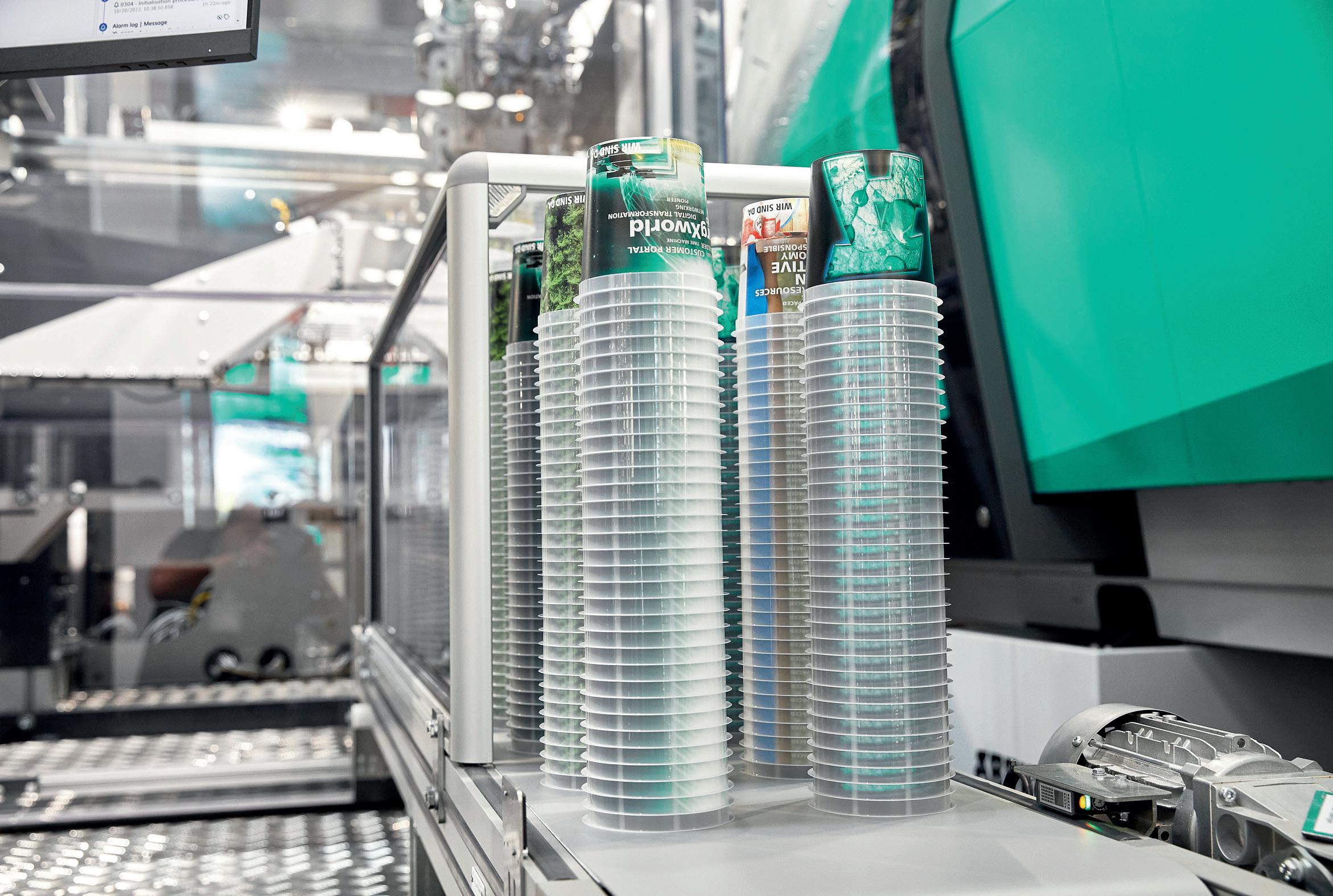
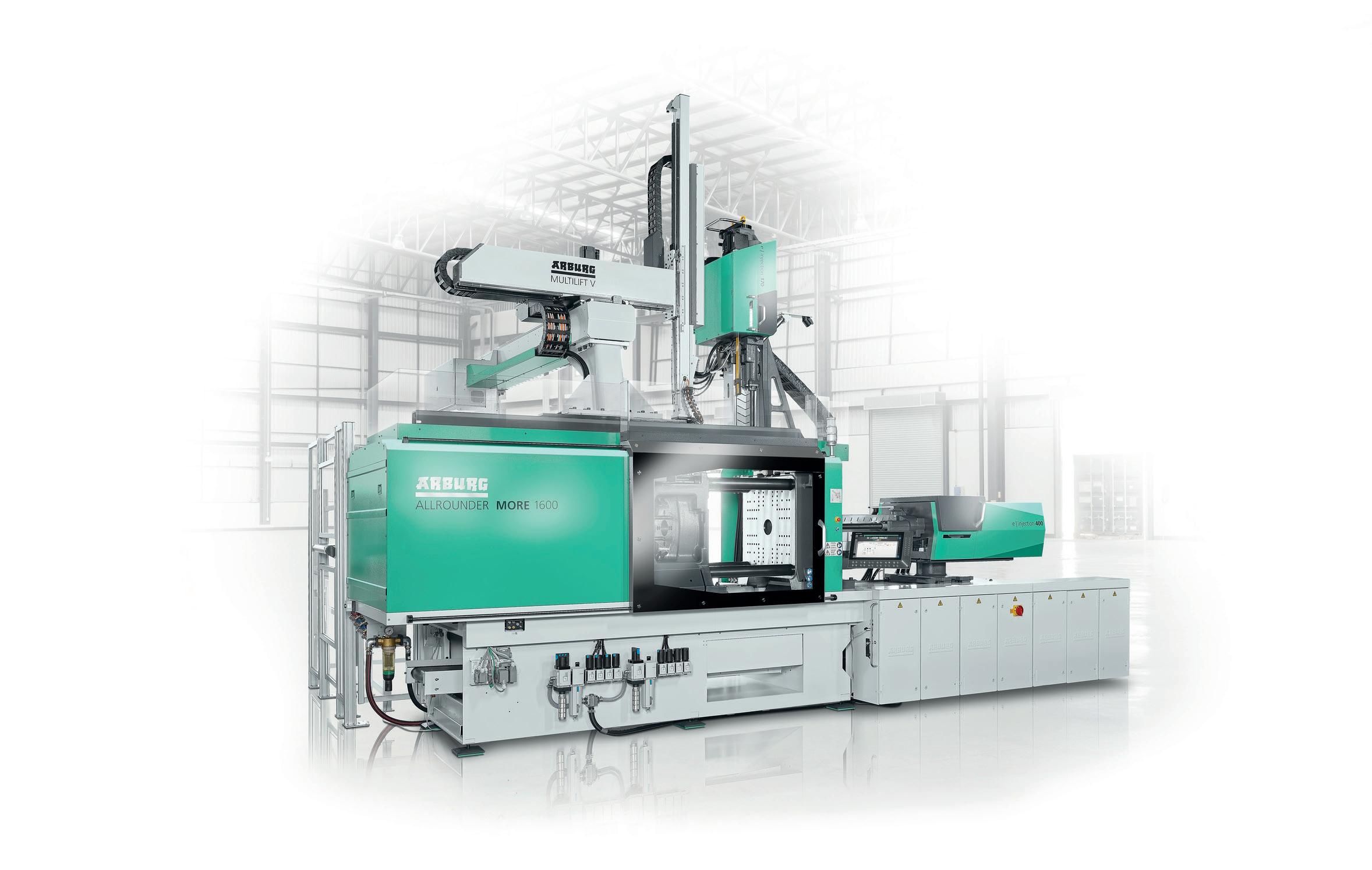
A Plast 2023 una Allrounder More con forza di chiusura 1.600 kN realizza connettori Luer in PP e TPE per i quali è richiesta una particolare precisione poichè il peso dei componenti in TPE è solo di 0,05 g.

Presso la fiera italiana vengono presentate anche tre Allrounder dedicate all‘imballaggio; come alternativa alla termoformatura, una Allrounder 720 A elettrica con la nuova unità di iniezione 1300 produce bicchieri IML a parete sottile, utilizzando il processo di stampaggio a inietto-compressione, mentre altre due applicazioni innovative sono visibili negli stand dei partner Trexel e Plasmatreat dove vengono realizzati bicchieri riutilizzabili, particolarmente leggeri, in materiale espanso, nonché bicchieri stampati separabili, in base alla tipologia, e riciclati dopo l‘uso grazie al cosiddetto passaporto digitale del prodotto.
Arburg dimostra che lo stampaggio a iniezione di alta qualità può essere un’alternativa alla termoformatura con una pressa Allrounder 720 A elettrica nella nuova variazione potenza “Ultimate”, con forza di chiusura di 2.900 kN e una unità di iniezione di grandezza 1300. Grazie anche ai servomotori di alta precisione della consociata AMK, la pressa ad alte prestazioni raggiunge portate volumetriche di iniezione molto elevate e velocità fino a 400 mm al secondo, distinguendosi grazie a una potenza particolarmente elevata.
Oltre alla variante “Ultimate” per processi complessi ad alta velocità, la multinazionale tedesca offre ora due ulteriori livelli di potenza per la serie Alldrive: le varianti Premium e Comfort con velocità di iniezione rispettivamente di 260 e 200 mm al secondo. Mentre la variante Comfort è progettata in modo simile alle presse standard idrauliche in termini di potenza, quella Premium presenta una dotazione più ampia per processi speciali e tempi di funzionamento a vuoto ridotti fino al 15%.
La pressa esposta a Plast 2023 utilizza uno stampo a 4 cavità di Brink per produrre bicchieri rotondi IML a parete sottile da materiale monomero PP con il processo di stampaggio a inietto-compressione. Per il monitoraggio del processo, lo stampo è dotato di quattro sensori della corsa di inietto-compressione. Quattro pezzi stampati, ciascuno del peso di 12 g e con spessore della parete di soli 0,37 mm, vengono prodotti in un tempo ciclo di 3,95 secondi, mentre nell’unità di produzione è integrato anche il robot side-entry di Brink, che inserisce le etichette, rimuove i bicchieri finiti e li impila su un nastro trasportatore.
Innovazione per tre processi
In occasione della fiera milanese è possibile osservare una particolare soluzione per gli imballaggi proposta da Trexel. Su una pressa Allrounder 520 A elettrica con unità di comando Gestica e pacchetto MuCell si producono bicchieri termici riutilizzabili personalizzati ed economici, che non solo sono molto leggeri e perfettamente isolanti, ma possono essere riciclati facilmente anche dopo più utilizzi, risultando più leggeri rispetto alle comuni alternative monouso in carta, pur utilizzando molto meno materiale. Questa applicazione pionieristica è stata sviluppata da Arburg con la collaborazione dei partner Bockatech, Borealis, Trexel, Roboplas e MCC Verstraete. Un bicchiere di 14 g e capacità di 430 ml viene prodotto in circa 5,5 secondi e il PP viene arricchito sia chimicamente con l’agente espandente sia fisicamente con l‘azoto attraverso il processo MuCell. Questa soluzione omogenea viene iniettata tramite un canale caldo con ugello ad ago otturatore e, successivamente, lo stampo a una cavità si apre e il componente si espande. La struttura rivestimento-espanso-rivestimento che ne deriva, con celle di schiuma a struttura fine, è decisiva per il peso ridotto, l‘elevata resistenza e l’isolamento termico.
Ma non è tutto, questa soluzione offre anche un enorme potenziale per l’economia circolare, infatti, nell’ambito dell’iniziativa R-Cycle, vengono prodotti bicchieri stampati che possono essere rifiniti in linea e separati per tipologia grazie a un passaporto digitale del prodotto.
Bicchieri a sezione rotonda e parete sottile in PP stampati a inietto-compressione con IML su una Allrounder 720 A elettrica con stampo a 4 cavità.
Per lo stampaggio a iniezione dei connettori Luer con una Allrounder More 1600 sono richiesti precisione e accuratezza: il peso della stampa dei componenti morbidi in TPE è di solo 0,05 g.
Green Soul
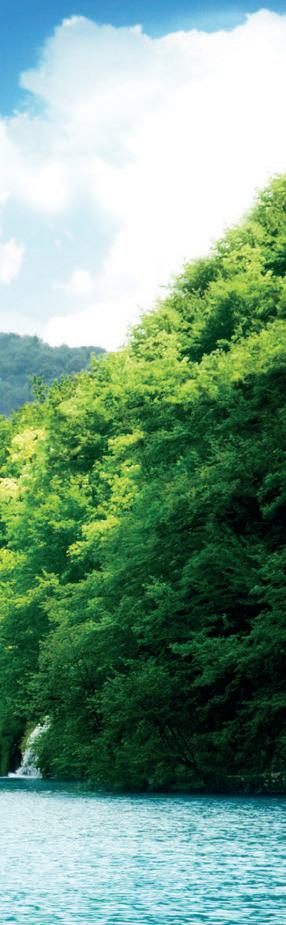
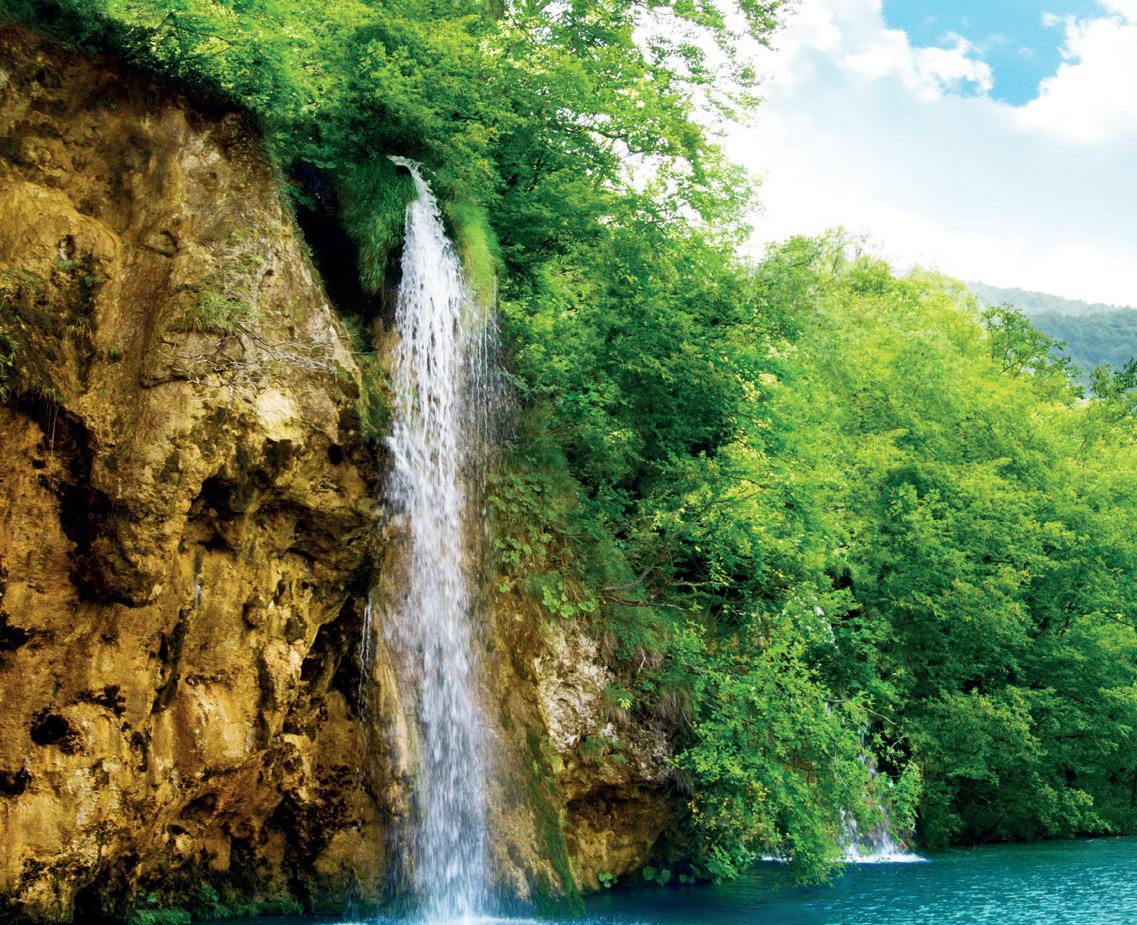
Technological Attitude
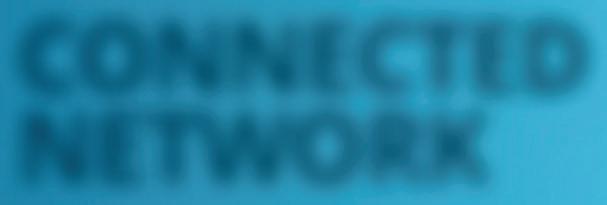
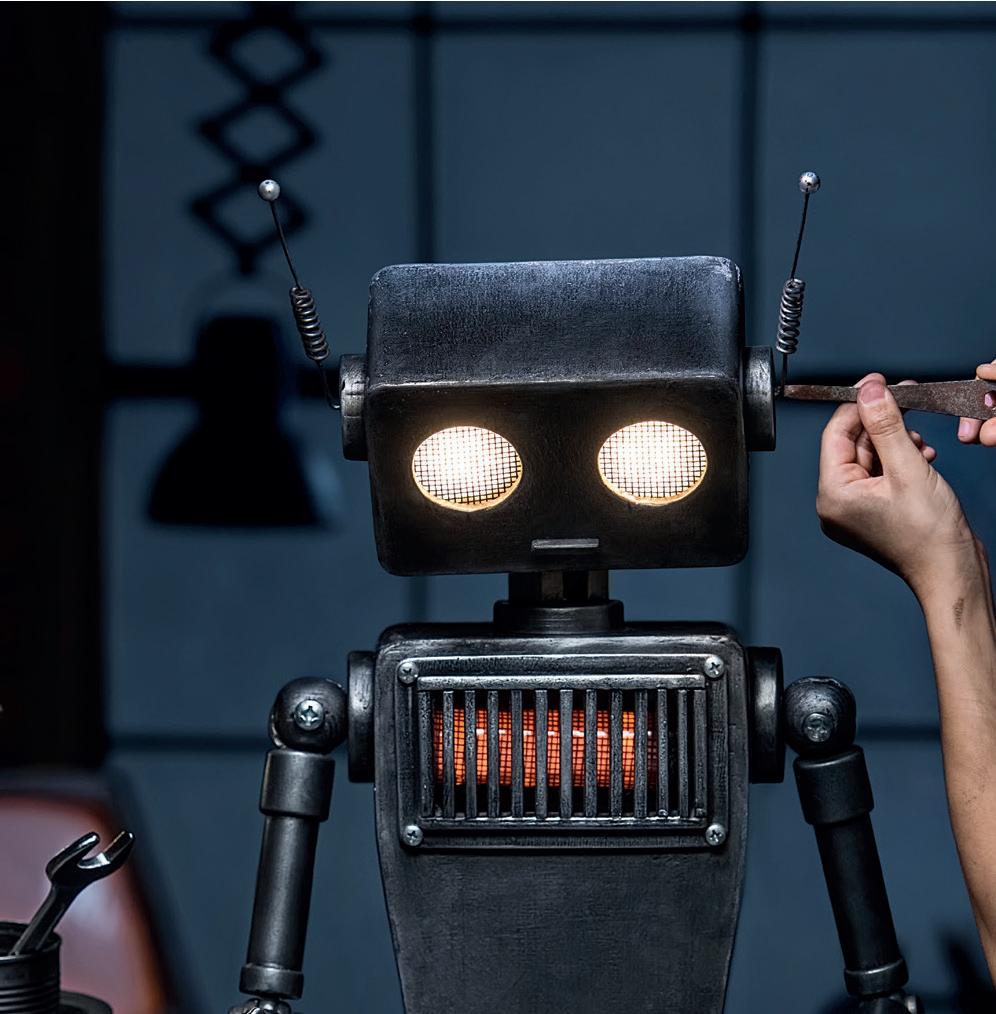