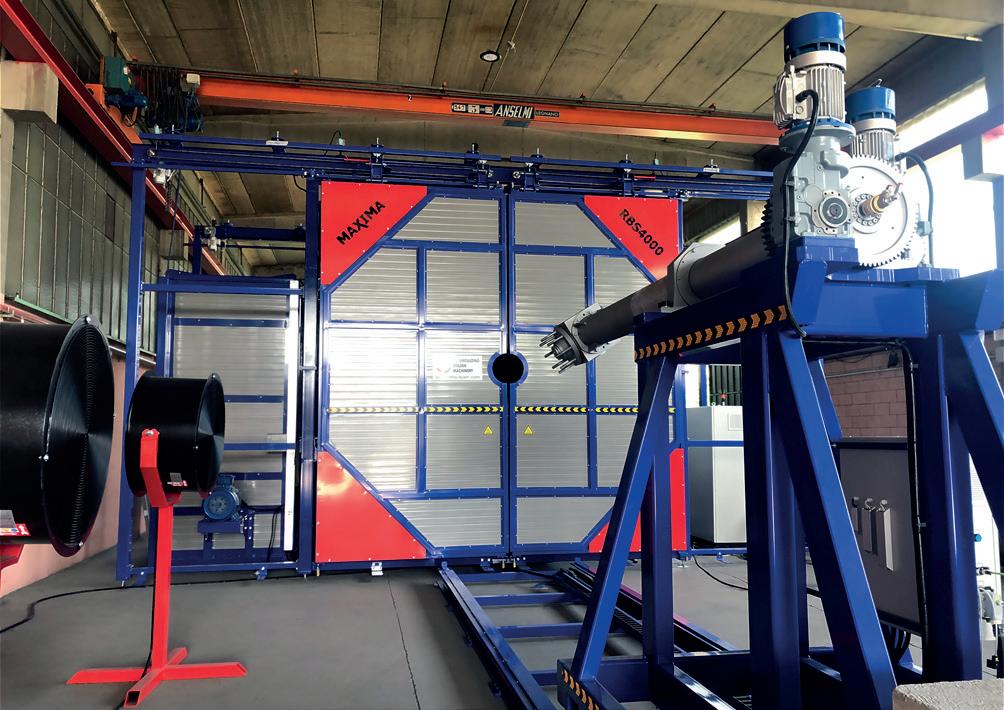
2 minute read
di materiali molto contaminati Permanenza ridotta del fuso nel filtro e rapida dispersione dei contaminanti
Tra le soluzioni integrate per la lavorazione dei polimeri nel processo di riciclo che Maag presenta a Plast 2023, spicca, in particolare, il filtro del fuso ECO 500 di Ettlinger. Si tratta di un filtro del fuso ad alte prestazioni per il trattamento di materiali fortemente contaminati, ideale per il riciclo chimico di polimeri a bassa viscosità. Il filtro è di tipo autopulente con tamburo rotante forato, attraverso il quale scorre un flusso continuo di fuso dall’esterno verso l’interno. Un raschiatore rimuove i contaminanti trattenuti sulla superficie e li alimenta al sistema di scarico. Ciò consente di utilizzare il filtro in modo automatico ininterrottamente per lunghi periodi senza dover sostituire il vaglio. Ne derivano filtrazione affidabile della massa fusa, curva di pressione costante con perdite di massa fusa estremamente basse, rapida dispersione della contaminazione e breve tempo di permanenza della massa fusa nel filtro. Maag propone anche il sistema di granulazione in acqua Pearlo 350 EAC, appositamente progettato per produzioni elevate fino a circa 18.000 kg all’ora di polimero vergine. L’esclusivo design della lama di taglio e le condizioni ottimali di flusso dell’acqua e del materiale all’interno della camera di taglio si traducono non solo in un raffreddamento ideale e omogeneo, ma anche un’eccellente qualità dei granuli. Innovativo anche il sistema di avanzamento della lama di taglio, che ne permette un movimento preciso e la riaffilatura durante la produzione. Ciò consente una maggiore disponibilità delle apparecchiature, cicli di produzione più lunghi e costi minori.
EBG, invece, è un sistema di granulazione a trefoli per compound altamente caricati, idroscopici e sensibili all’acqua. Il dispositivo si distingue per l’elevato grado di automazione, la delicata lavorazione dei materiali e l’eccellente qualità del prodotto. Tra le sue caratteristiche principali si ricordano l’alimentazione automatica in caso di rotture dei trefoli, rimozione dei residui di fusione sulla trafila mediante lama ad aria calda brevettata e sincronizzazione tra nastro trasportatore e granulatore dei trefoli, solo per citarne alcuni.
Impianto di Rima Team in Galles Stampaggio rotazionale su misura
Il costruttore di impianti per lo stampaggio rotazionale Rima Team ha recentemente fornito una macchina Maxima a carosello (una di quelle che verranno proposte dal costruttore a Plast 2023), con diametro sferico di 4.000 mm e due carrelli (con due bracci diritti e uno a squadra in aggiunta), a un trasformatore gallese per la produzione di serbatoi carburante.
A fronte della ridotta altezza del reparto di produzione la camera termica è stata ribassata di 500 mm, abbassando di conseguenza anche i tubi di riparo fiamma con lo sdoppiamento dei condotti di aspirazione. Data la riduzione di tali dimensioni, l’installazione di un bruciatore da 1.000 kW rischiava di surriscaldare e deformare le protezioni e, di conseguenza, la camera è stata rivestita in acciaio inossidabile resistente alle alte temperature. Con questo sistema il calore è stato concentrato nel forno migliorando i tempi di riscaldamento che, in aggiunta al doppio sistema di aspirazione per mantenere costanti i flussi dell’aria con collettori telescopici, permette di ottenere un significativo risparmio energetico. A seguito del posizionamento ribassato del bruciatore è stato creato un ballatoio intermedio per potervi accedere, così come accessibile è stato reso il tetto del forno e il camino estrazione fumi. Inoltre, a causa del pavimento del reparto produttivo non perfettamente planare, con un discostamento di oltre 10 cm da un lato all’altro, è stato necessario realizzare delle piastre di livellamento regolabili supplementari per fare in modo che la macchina sia in bolla.
Tutte le modifiche apportate a questa versione speciale si aggiungono alle caratteristiche standard delle macchine del costruttore, come le porte scorrevoli del forno, utilizzate per macchine dai 4.000 mm in su, più robuste per evitare deformazioni, la struttura robusta della camera di stampaggio realizzata in acciaio da costruzione che ne limita la deformazione al calore e i pannelli termoisolanti ad alta efficienza trattati con vernici speciali che incrementano la conservazione del calore all’interno della camera. I flussi d’aria ben direzionati direttamente sullo stampo, unitamente al bruciatore di ultima generazione, con emissioni quasi vicine allo zero, permettono il raggiungimento delle temperature di esercizio in tempi limitati, con un netto miglioramento dei tempi di cottura.
