
4 minute read
Rassegna internazionale di scienza e tecnologia
Ventisettesima puntata della rubrica dedicata agli articoli di stampa estera selezionati dal comitato di redazione di Elastica, composta da Fabio Bacchelli, Rino Gilotta e dal team di Cerisie, coordinati da Maurizio Galimberti.
CIRCOLARITÀ DEI RIFIUTI DI GOMMA EPDM ATTRAVERSO
LO SVILUPPO DI UN PROCESSO CONTINUO DI DEVULCANIZZAZIONE TERMOMECCANICO-CHIMICA E ATTIVAZIONE
Testata: Kautschuk Gummi Kunststoffe, 2, 36 (2023)
Titolo originale: Closing the Loop by Developing a continuous thermomechanochemical Devulcanization and Activation Process for EPDM Rubber Waste
Autori: L. Gschwind, C. Jordan
A C URA DI FABIO BACCHELLI
Il concetto di economia sostenibile si è tradotto in innumerevoli sforzi rivolti a trovare soluzioni innovative per il riciclo dei prodotti in gomma. La sfida, in termini di circolarità, risiede nella tecnologia di riconversione del reticolo tridimensionale formato durante la vulcanizzazione, a cui va aggiunta la grande varietà di formulazioni esistenti sul mercato e la complessità strutturale dei prodotti.
La granulazione è il modo più comune per ottenere gomma riciclata sotto forma di polverino (RWP). Le particelle possiedono ancora una buona elasticità e, senza ulteriori modifiche, possono essere incorporate in nastri trasportatori, guarnizioni, superfici stradali, ecc. La quantità dell’RWP che può essere utilizzato per sostituire la materia prima fresca senza intaccare la qualità del prodotto finale è, tuttavia, limitata. Ulteriori modifiche del rifiuto, come l’attivazione superficiale o la devulcanizzazione, rappresentano utili sistemi per migliorare la prestazione e convertire la gomma di scarto in materia prima-seconda.
Il cosiddetto processo di attivazione migliora la compatibilità della gomma riciclata con la gomma fresca, aumentando l’adesione tra le fasi e la reticolazione chimica. In contrasto con l’attivazione, la devulcanizzazione viene invece utilizzata per rompere in modo selettivo i legami zolfo del reticolo di vulca- nizzazione, preservando per quanto possibile i legami carbonio-carbonio. L’obiettivo può essere raggiunto per via termofisica, termomeccanica, termochimica, oppure irraggiamento, ultrasuoni, microonde o metodi biologici. Processi di devulcanizzazione di scarti di gomma EPDM mediante l’aggiunta di disolfuri, sono prevalentemente condotti a temperature variabili tra 180 a 300°C. Le alte temperature utilizzate portano, oltre a un elevato consumo energetico, alla parziale degradazione della catena polimerica con conseguente perdita di proprietà. Ne consegue che, dal lato applicativo, il materiale devulcanizzato deve essere mescolato con gomma vergine per garantire al compound finale il recupero delle proprietà richieste.
In questo studio, viene presentato lo sviluppo di una tecnologia di riciclo della gomma EPDM basata sulla combinazione di tre fasi: devulcanizzazione chimica, attivazione con un polimero liquido e aggiunta del sistema di vulcanizzazione per la produzione di una materia prima secondaria di alta qualità. L’uso di dibenzammido-difenil-disolfuro (DBD) come agente devulcanizzante per l’EPDM è documentato in letteratura. Per l’attivazione è stato utilizzato un polimero a basso peso molecolare (LP) Trilene 67, intensivamente studiato per l’attivazione di gomma riciclata con buoni risultati. Il sistema vulcanizzante viene aggiunto direttamente dopo la devulcanizzazione e l’attivazione. Non sono necessarie fasi successive e la materia prima secondaria può essere lavorata mediante stampaggio a iniezione per produrre, ad esempio, sistemi di tenuta. I materiali ottenuti con questo procedimento, una volta vulcanizzati nuovamente, sono stati testati misurando compression set, durezza e proprietà tensili. La polvere di gomma ricilcata (RWP) è prodotta da M.D.S. Mayer. Il materiale di riferimento contenente comma fresca e sistema vulcanizzante si basa sulla composizione dell’RWP ed è costituito principalmente da 100 phr di EPDM (Keltan 9650Q), 120 phr di nerofumo N550 e 100 phr di olio paraffinico. Gli additivi utilizzati per la produzione del materiale sperimentale sono l’agente di devulcanizzazione (DBD, Struktol 424 di Schill-Seilacher) e il polimero liquido (LP, Trilene 67 di Lion Elastomers). Il pacchetto vulcanizzante è costituito a zolfo, acido stearico, zinco ossido, N-cicloesil-2-benzotiazolo-sulfenammide e zinco bis-dibenzilditiocarbammato. Per studiare la combinazione di attivazione e devulcanizzazione, sono state preparate formulazioni con LP variabile tra 0 e 10%. Il processo di attivazione dell’RWP con LP è stato eseguito in un mescolatore interno di laboratorio a 90°C. È stato poi aggiunto il 2% in peso di DBD. Il composito è stato quindi alimentato a un estrusore bivite con profilo di temperatura tra 120 e 80°C. L’aggiunta del sistema di vulcanizzazione è stata condotta in un mescolatore interno o direttamente nell’ultima apertura dell’estrusore. La vulcanizzazione del prodotto finale è stata studiata via MDR. Il materiale ottenuto è stato utilizzato per la produzione di sistemi di tenuta tramite stampaggio a iniezione e confrontato con un materiale di riferimento di durezza pari a 50-60 Shore A.
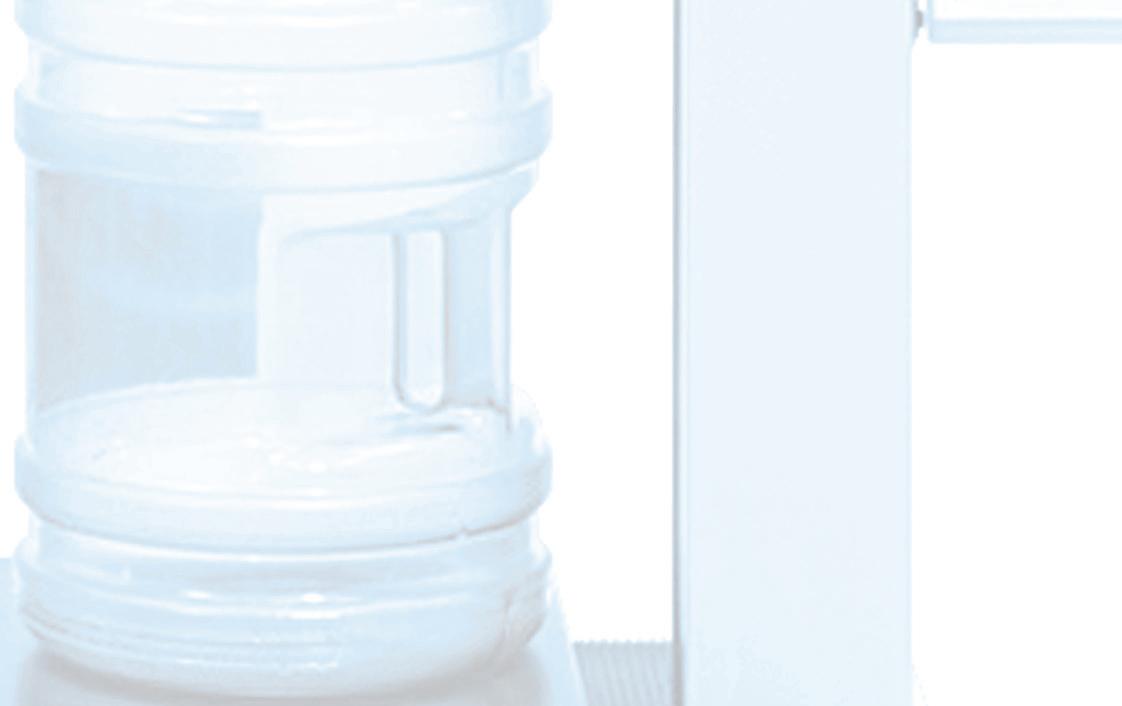

Aumentando la quantità degli agenti vulcanizzanti, la durezza del prodotto originale può essere ripristinata in modo da soddisfare i requisiti della norma DIN EN 681-1:2006 per i sistemi di tenuta a durezza 60 Shore A. Da un punto di vista della sostenibilità, una minore quantità di agenti di curing è auspicabile ed è quindi consigliabile porsi come obiettivo una tenuta di durezza pari a 50 Shore A. Il compression set può essere migliorato solamente aumentando il tempo di vulcanizzazione. Un buon compromesso tra carico e allungamento a rottura può essere raggiunto agendo, anche in questo caso, sula quantità degli agenti vulcanizzanti. In conclusione, i test di confronto con i materiali di riferimento mostrano che la materia prima-seconda composta soltanto da RWP (88%), DBD, LP e agenti vulcanizzanti può essere processata direttamente, durante l’operazione di stampaggio a iniezione, senza passaggi aggiuntivi e che le proprietà finali dei manufatti dipendono soltanto dalla geometria della guarnizione e dalla durezza del composito, ma non dalla tipologia della formulazione, cioè dal fatto che siano stati realizzati interamen te con materiale riciclato.
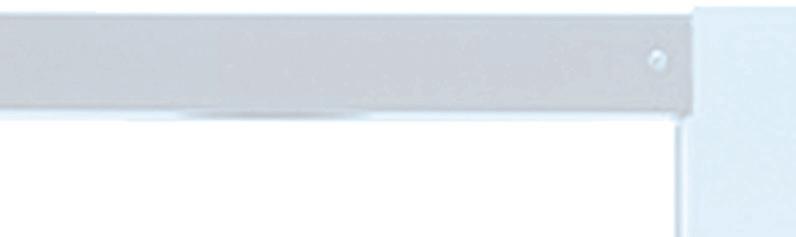
DGTS Srl, nell’intento di soddisfare sempre al meglio le esigenze dei suoi clienti, è in grado di offrire un supporto tecnico competente e completo tramite i suoi servizi:
Vendita e Installazione di apparecchiature e strumenti per il Laboratorio Controllo Qualità e Ricerca e Sviluppo per la determinazione delle caratteristiche fisico meccaniche delle materie prime e dei prodotti finiti Corsi di Formazione ed Aggiornamento del personale sull’utilizzo degli strumenti e dei relativi software ed accessori


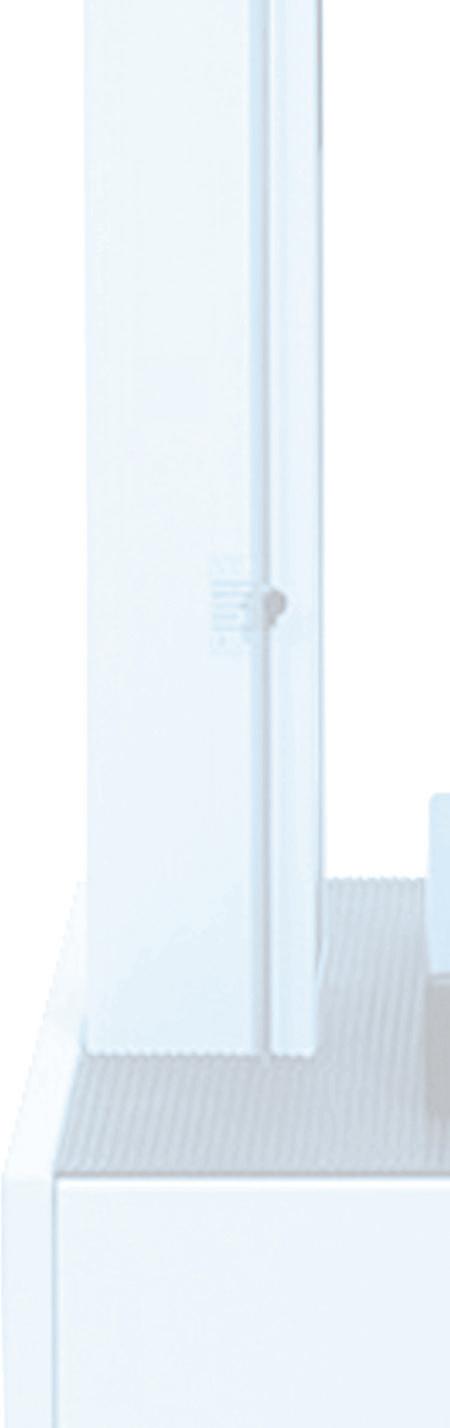

Presentazione degli strumenti anche presso la sede del cliente, con la possibilità di eseguire prove dimostrative su campioni forniti dal cliente stesso
Assistenza Tecnica post-vendita
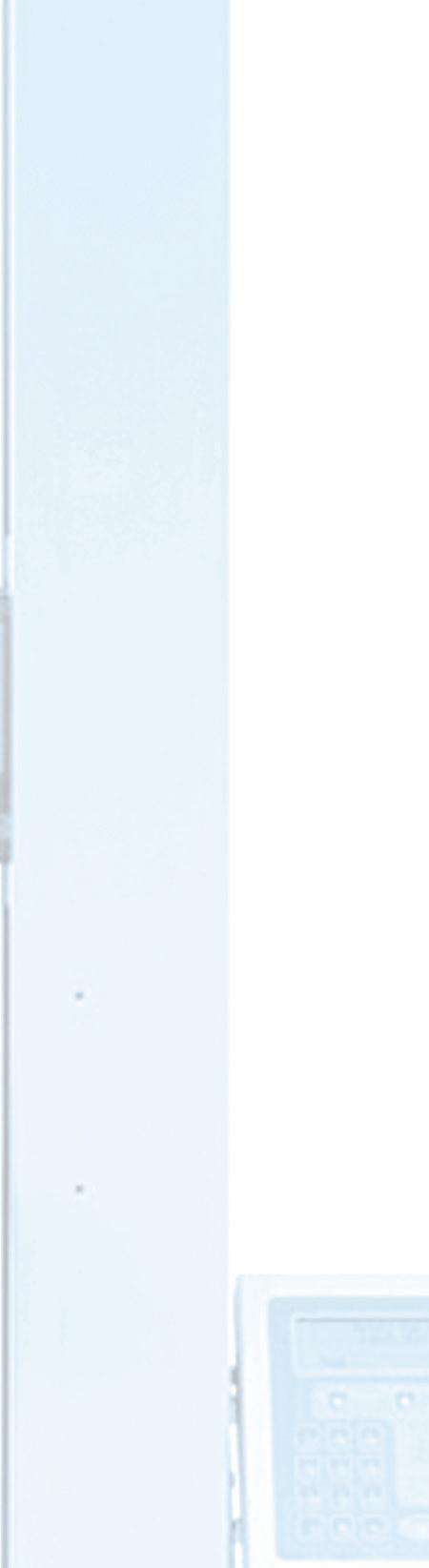
Servizio di Taratura e Calibrazione
Servizio di Manutenzione
Servizio di Riparazione
Regolamento (CE) 2023/2006
