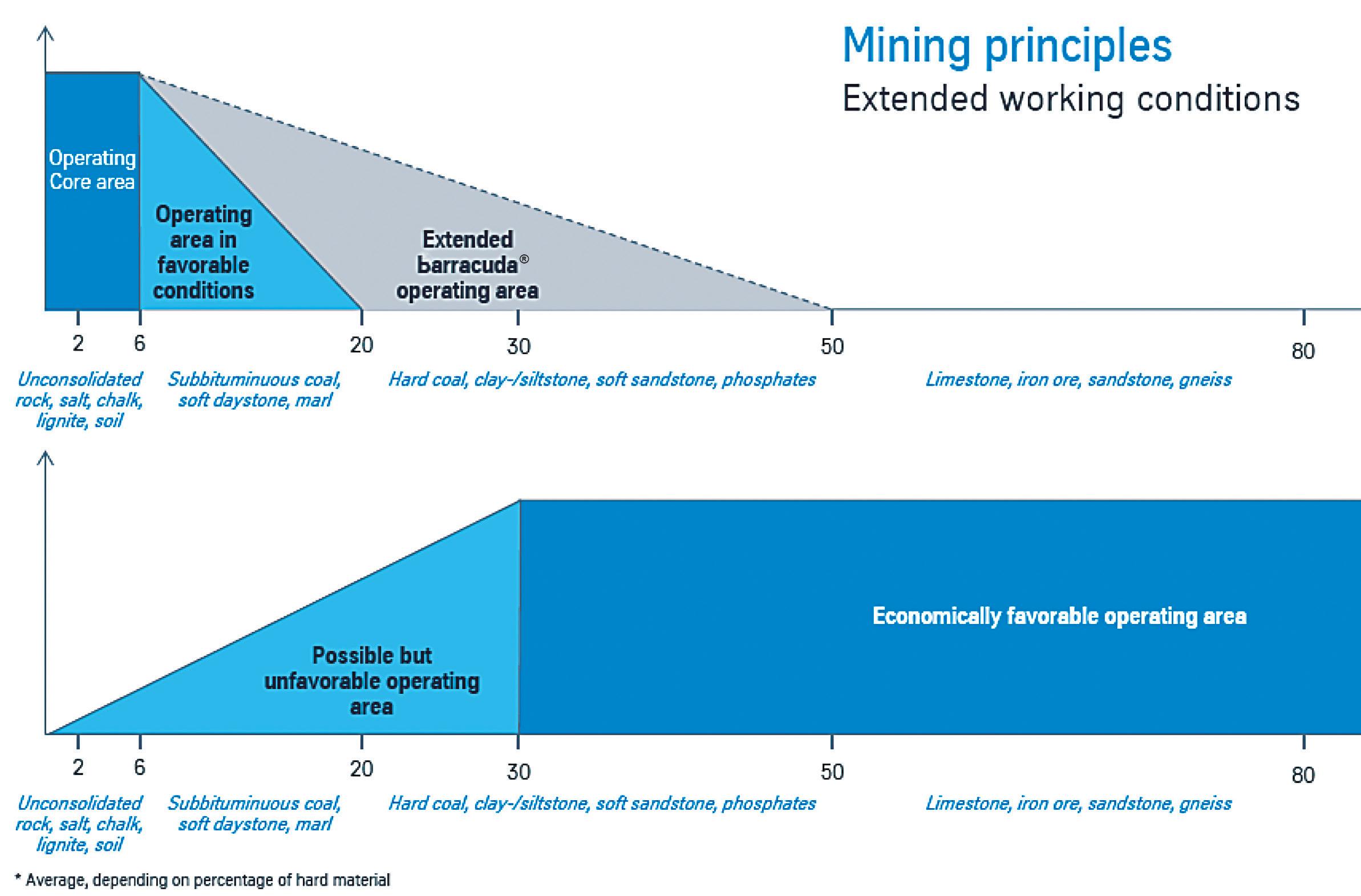
4 minute read
On the Move
There’s a vibrancy about thyssenkrupp’s Mining business unit in South Africa in 2020. With innovative new products on offer, it’s no surprise the team is excited.
The "Bulk Handling Today" team met with Henry Swart, business development manager for materials handling & mining systems, to find out the source of their enthusiasm and why the barracuda ® bucket wheel excavator is such a game changer.
Advertisement
Under one roof
thyssenkrupp has had a long presence in the region. Initially operating through an agent in South Africa, the German powerhouse cemented its African foothold in 1959 by establishing Krupp South Africa (Pty) Ltd. in Johannesburg. An illustrious history saw numerous mergers and name changes as the company widened its footprint, stepping across South Africa’s borders into the entire continent. Showcasing its steadfast commitment to customers along their operational journey through service and after-sales excellence, the company opened a Service Centre in Chloorkop in March 2009, which encompasses an own training academy and is regarded as one of the most sophisticated service centres on the continent. This technologically advanced facility specialises in the complex engineering and refurbishment of OEM parts and components, spare parts management, field services, plant upgrades and redesigns, life-cycle services, operation and/or maintenance contracts as well as machine audits.
A great heritage, but there’s more
“We are fortunate to have access to a wide range of technologies from mineral processing to mining systems and materials handling. Our company’s success is based on a blend of factors: Highly skilled employees; energy efficient superior quality equipment, technology and solutions; our customer centric focus and our concentrated efforts to expanding our African footprint.” Through its Minerals Processing unit, thyssenkrupp offers customers a wide range of crushing and grinding technology. To meet Africa’s growing demand for energy, a dedicated Power & Energy division delivers efficient innovations such as turnkey biomass fired plant solutions, from boiler supply to building the complete plant around the boiler. The Materials Handling unit delivers exceptional pit-to-port solutions for efficient bulk handling solutions with equipment such as drum reclaimers, stackers, travel cars, ash spreaders, conveyors and ship loaders. “We are deeply rooted in Africa with a large installed base on the continent. Our newest in-pit crushing
and conveying system for example has just now been erected in Mozambique where we have combined a mineral processing front end with mining system conveyors," Henry says. “Furthermore, we will continue designing and suppying dry tailings storage facilities, as we have done for the past 40 years.” These tailings, waste or discard systems are operated autonomously and are typically found in the power industry and mines where continuous operator involvement is kept to an absolute minimum and production load losses cannot be tolerated. “We have almost 100% market share in South Africa when it comes to these heavy duty ramp, extendable and shiftable conveyor installations combined with rail or crawler mounted spreaders. Our latest developments in shiftable and extendable conveyor design will reduce customer risk when exposed to plant down time during conveyor shifts and extensions,” Henry adds.
A cost saving, safer game changer
"But the innovation we want to talk about today is the barracuda ® . thyssenkrupp has developed a cost saving solution for open cast mining where the material properties allow the possible elimination of drilling, pre-blasting and primary crushing. “Our barracuda ® compact bucket wheel excavator is certainly such a game changer,” Henry says. The barracuda ® was developed with a cutting action as opposed to the more common digging action which facilitates the excavation of harder materials with compressive strengths up to 50 MPa. It

therefore vastly extends the application range of bucket wheel excavators. In other words, the barracuda ® is a genuine alternative to the conventional drilling and blasting methods used in mining coal, phosphate, ore and potash or the corresponding overburden and waste removal. To meet the demands of harder materials, the teeth arrangement has been adapted to the usual bucket wheel configurations. Buckets and pre-cutters are positioned much closer together and there are more teeth on the bucket. This very narrow teeth arrangement gouges into the material while digging. The result is a reduction in the size of the section or the lump size that has to be dug out per tooth, which in turn means less loosening force is required. The welcome side effect is that the material in question is cut into easily conveyable pieces of less than 200mm. When the barracuda ® has completed its work, the primary crushing stage is finished too – without the need for drilling, blasting or a surface miner. The barracuda ® technology can lower production costs and boost efficiency. And there’s a reduction in environmental emissions which means lower carbon tax. "This step change in OPEX is what the mining industry desperately needs,” Henry concludes.
thyssenkrupp Industrial Solutions South Africa Henry Swart Email: henry.swart@thyssenkrupp.com www.thyssenkrupp-industrial-solutions.com
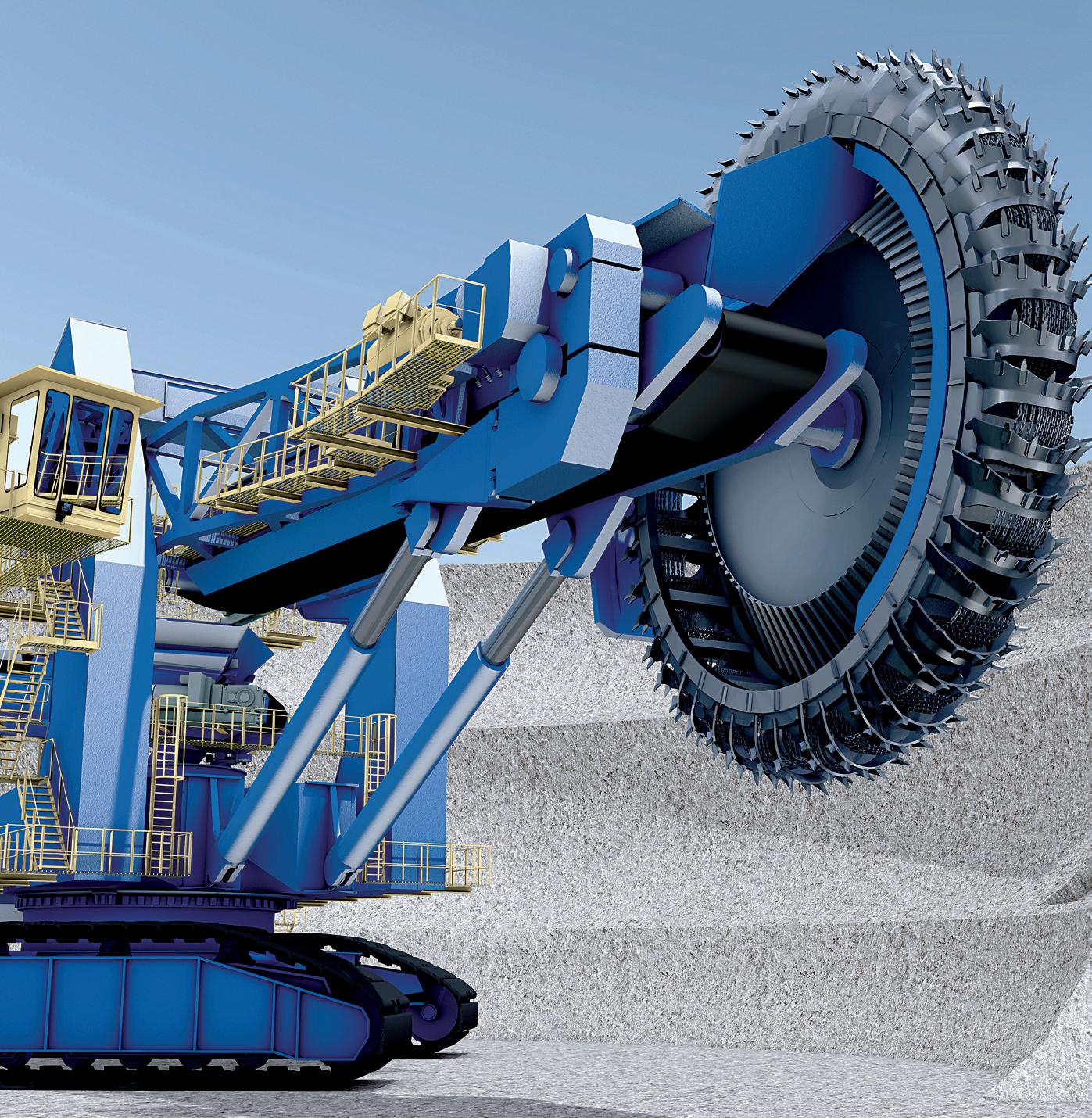