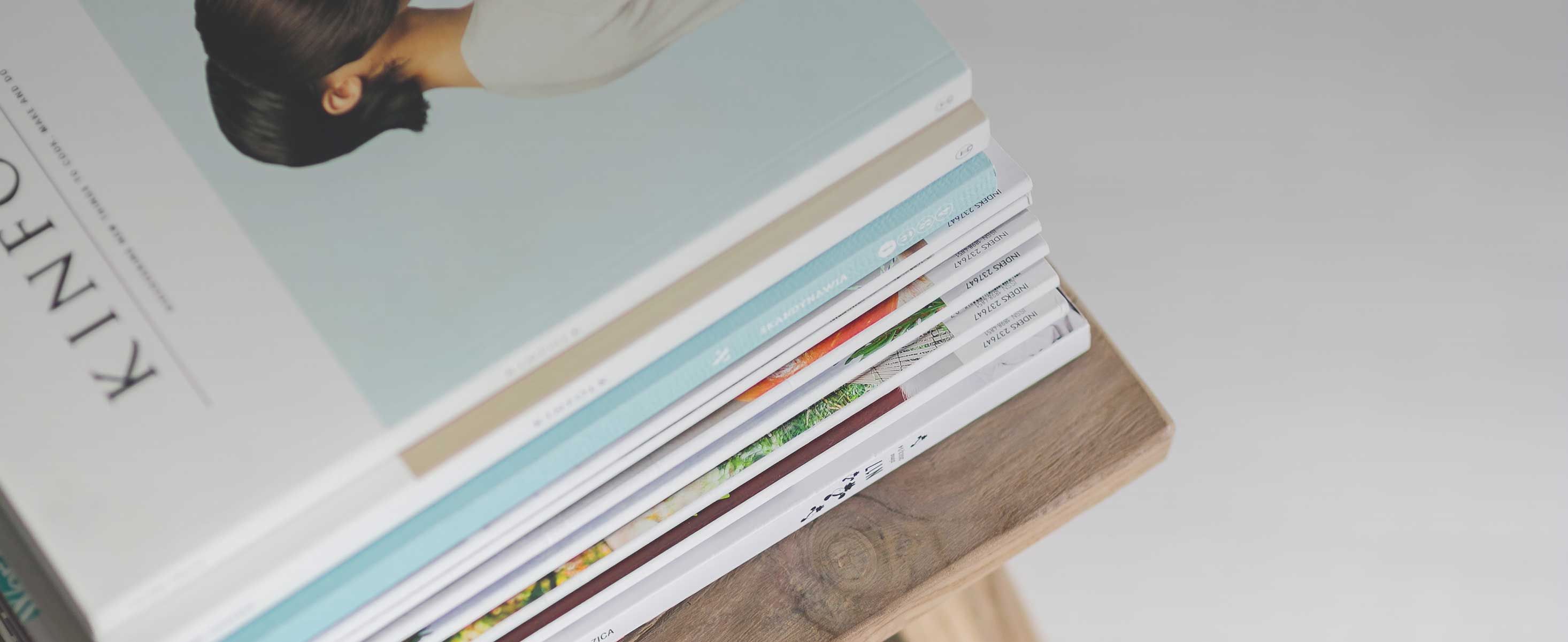
3 minute read
Solar kilns gaining ground in Australia
SOLAR Dryers Australia (SDA) is the designer/ manufacturer of a range of unique Solar/Gas timber kilns and Heat Treatment Units.
SDA kilns have gained wide acceptance in the past 25 years with around 200 units sold in Australia and abroad.
Sizes range from 10m3 to 100m3 with kilns characterized by simplicity of operation and heating costs well under half that of other kilns.
The auxiliary heating system ensures that drying times are the same as any other kiln, regardless of climate. The external arrangement of the auxiliary heating system also ensures no hazardous fumes present safety issues inside the kilns.
Control is via a simple PLC offering manual or automatic schedules.
Small Kilns
The smallest kilns in the range are the SG10 and SG 22, 10m3 and 22m3 respectively. These small kilns are based on 20’ or 40’ refrigerated shipping containers. These are ideal for the purpose as they are portable, well insulated and sealed, with all inside surfaces either stainless steel or aluminium.
Container kilns are loaded using a track and trolley system. The stainless-steel trolley is rolled out onto a fixed track outside the kiln where it is loaded by forklift and then pushed into the kiln.
The kilns are shipped to site with all the components packed inside the container. Re-assembly takes around a day and then the kilns are ready for operation.
Kilns can easily be moved to a different location later if necessary.
Large Kilns
SDA’s larger kilns range from 50 to 100 m3. These kilns are designed to client requirements and manufactured in Bellingen, NSW, Australia. They are then shipped to site where assembly takes about two weeks.
The large kilns are sometimes combined in multiple units.
AST-Hurford at Kempsey, NSW, Australia, has 13 kilns of 50 to 75m3. Parkside Timbers in Queensland, Australia, runs nine kilns, each of around 100m3 capacity and is the largest solar timber drying operation in the world.
The heating system is the same in all models, but the number of solar panels varies according to kiln capacity. The array of solar hot water panels is mounted on the roof of the kiln or on an adjacent building. Water is pumped in a closed circuit between the panels and the heat exchanger inside the kiln. Heat is extracted from the water, which then returns to the panel array for re-heating. An instantaneous gas water heater in the circuit heats the water if no solar is available.
Once a kiln temperature is selected at the control box the system automatically maintains this temperature using either solar or gas or a combination of both.
At Bellingen, Australia, Rose Gum Timbers operates two 50m3 solar/gas kilns drying mostly Blackbutt and Spotted Gum.
Initial heat up to 55˚C is usually overnight on gas and uses approximately 140 litres (LPG). Carefully monitored venting then allows temperature to be largely maintained by solar during the day, with 30 – 40 litres used to maintain temperature overnight.
So for a charge of 25mm air dried hardwood, subsequent kiln drying to 12% MC takes about 10 days with a gas total of around 500 litres or $440 for 40 m3.
This equates to $11 per m3 or about 25% of the cost of conventionally heated kilns.
Heat Treatment Units
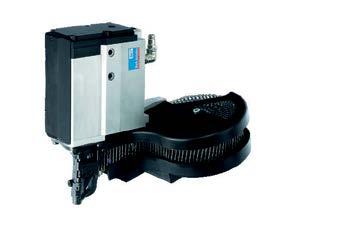
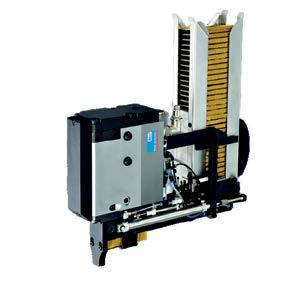
SDA also repurposes refrigerated shipping containers to build Heat Treatment Units for ISPM 15 treatment of export packaging. These 20’ & 40’ units can be operational on the day of arrival (HTU 20/ HTU 40).
Larger units are built to order, and are similar in design to our larger timber kilns.
All HTU’s features a simple automatic controller which enables documentation to be printed or stored.
This satisfies the ISPM 15 requirements, and with most accreditation bodies familiar with SDA units.
Automate for speed and efficiency to eliminate labour shortage problems.
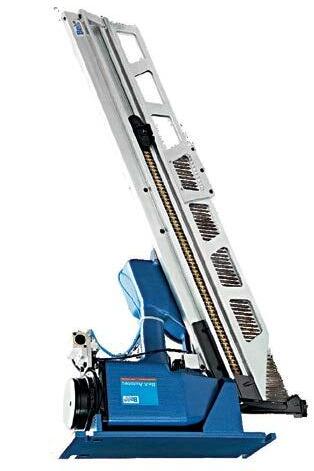
The manufacturing world we live in now post COVID-19 has seen international setbacks and problems with delays in importing and increases across the board in prices of goods. Australia has also seen a growing problem with shortages in labour, causing further delays in local manufacturing. This poses great challenges for the economy as a whole, but also for individual businesses. Producing economically while maintaining quality standards is becoming a real challenge for many businesses. One solution to this problem is to expand the automation of individual work processes or entire production lines.
The BeA Group, headquartered in Germany, with APAC headquarter in Sydney and warehouse in Brisbane, Sydney and Melbourne, offers excellent automation solutions. BeA partners with local and world leading automation specialists in timber construction and wood processing, to provide tailored automation solutions across the entire production line in industries such as furniture, production of pallets, house frame and truss, and windows and doors and like manufacturing. With its „Autotec“ division, the BeA Group is one of the world‘s leading manufacturers of equipment for automated production. In this field, BeA cooperates with the world market leaders for wood processing equipment and is a reliable partner with over 100 years of competence and know-how in this field. Autotec equipment is available in a wide variety of versions and for almost any application. Should a very special solution be required, BeA can also offer special solutions with its internal engineering department.
Phone: 1300 232 287 or +61 438 841 708
Email: apac@bea-group.com www.bea-group.com