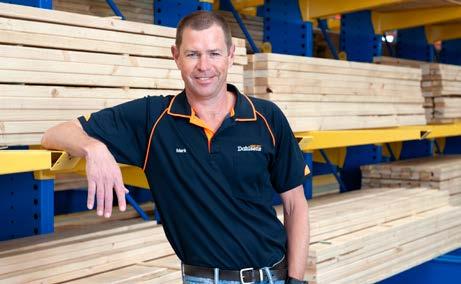
35 minute read
News
•Dahlsens'Mark Cooper
Some turbulent times ahead for building sector
THE pipeline of houses still to be built in Australia is going to be above normal until late next year, according to Industry Edge managing director Tim Woods.
And he expects there will be a sharp downturn, although he says it should not particularly long because long-term demand is "baked in" thanks to population growth.
Mr Woods was speaking at a Forestry Australia webinar on the outlook for Australian forestry and timber products.
Mr Woods said any slump would be short-lived thanks to a fairly aggressive migration program that will hopefully reduce some of the pressures on labour in the Australian economy. "Timber supply is going to continue to be tight, but it is already improving," he said. "However, long term supply will be quite difficult because demand is growing faster than supply now and for all times that we can model into the future. "That doesn't mean imports are a problem," Mr Woods said. "It means they're a potential saviour. But over reliance on imports is a supply chain risk. "And that's why there's an industry focus on increasing local production, not just as sawn wood, but also of those improved utilizations that might come from various forms of engineered products," he said. "And I guess when it comes to prices for sawn timber, well, we do anticipate that they're going to remain high. They’re unlikely to hit bottoms they have previously struck. And that is a good piece of good news for this supply chain."
According to the general manager of the southern business of National tradefocused building material supplier Dahlsens, Mark Cooper, the combination of the global housing boom, low interest rates and the Government’s HomeBuilder grant resulted in huge building industry demands over recent years. We are hearing from many of the builders we partner with that they have 6-12 months of work in the pipeline; however, it is difficult to provide a clear vision after that
Mr Cooper added that the company does not predict that the building industry would experience a sharp downturn.
“We anticipate that interest rates will settle, the industry workforce will build, and skilled workers from overseas will immigrate to Australia. We believe new housing builds and renovations will start to dip; however, we don’t think they’ll drastically disappear,” Mr Cooper said.
He explained the Dahlsens team was working with suppliers to support a continued increase of timber supply.
Mr Cooper said that while pine supply on some lines remained tight, overall stock levels in key timber lines had improved.
“To ensure the survival of the supply chain and the wellbeing of everyone across the industry, we have been working closely with our supply partners to ensure we can continue to support these levels of building.”
Mr Cooper added that Dahlsens remained nervous about the industry relying too heavily on imported products and believes Australia should be investing in growing the footprint of our forestry estate in Australia.
“We are advocating for the Australian Government and various influential industry association bodies to step up investment in renewable plantations, particularly in softwood, to sufficiently meet the future demand.
“We are very clear on our stance that there is a need for more trees to be planted if we are to supply our industry locally,” he said.
“However, we have seen minimal movement on this front in the last 30 years. Meanwhile, there is an increased demand for fibre based renewable products, not just in the building industry, but from other sectors too - for example, paper bags and cardboard as a replacement for single use plastics and packaging.
“Our strategy remains to support more local production so the Australian building industry can access these locally produced products,” said Mr Cooper.
•Industry Edge's Tim Woods
NEWS CLT valued at $2021m by 2027
According to a report by Reports and Data, the global cross-laminated timber (CLT) market was valued at US$786.71 million in 2019 and is expected to reach $2,021.29m by the year 2027, at a CAGR of 12.51%. Source: Digital Journal, Reports and Data
By volume, the market is expected to reach 3,237.61 thousand cubic metres in 2027 from 1,411.55 thousand cubic metres in 2019, growing at a CAGR of 11.23%. Rising awareness regarding sustainable architectural methods, coupled with the rising number of CLT producers and increasing interest for green homes are factors augmenting the market growth.
The move from concretebased development to woodbased development alongside government initiatives to cut down on pollution emanating from construction activities around the globe are factors impacting the market.
In addition to this, the diminishing costs of CLT due to increasing suppliers and shorter total project development time is having a positive impact on the industry. Stringent government regulations regarding the use of timber for building homes, due to the risk of fire, is expected to be a restraint to industry growth.
However, certain unique benefits like the ability to better absorb seismic shocks than concrete structures are also a reason why builders are showing an interest in this material.
A report by the Institute of Civil Engineers (ICE), UK, illustrates that the construction industry is likely to be one of the most dynamic industrial sectors in the next 10 years from 2020 and the same will be witnessed in economies globally.
The report illustrates that the volume for construction output will grow by 85% to over $15.5 trillion globally by 2030, of which the three major countries China, the US and India to account for over 57% of this growth.
China’s share of the global construction industry will increase marginally as growth slows until 2030. Comparatively, US construction will grow faster than China, growing by an average of over 5% per annum.
The same report illustrates that apart from the top three countries, the growth in the construction industry is witnessed in Indonesia, while Mexico is forecasted to overtake Brazil in the Latin America region.
NOVEMBER 2022
Issue 7 – Volume 32
Incorporating Australian and New Zealand Timberman. Established 1977.
News 3-11
Machinery
12 Forklifts 14 Associations 15-19
FRONT Cover: The Wellington St project in Melbourne will be built from Glulam and CLT..
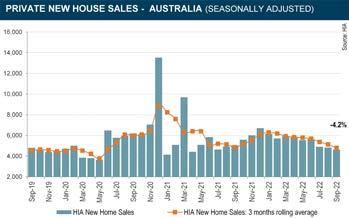
PUBLISHER and Chief Executive: Hartley Higgins
General Manager: Robyn Haworth
Editor: Bruce Mitchell b.mitchell@ryanmediapl.com.au Adelaide Office (08) 8369 9512
Advertising: Gavin de Almeida g.dealmeida@ryanmediapl.com.au Adelaide Office (08) 8369 9517
Creative Services: Tim Coleman
Publication Design: Tim Coleman
Timber classifieds: g.dealmeida@ryanmediapl.com.au Adelaide Office (08) 8369 9517
Subscriptions: subs@forestsandtimber.com.au Adelaide Office (08) 8369 9522
Subcription rates One-year (8 editions) $55 Two-years (16 editions) $95
Accounts: Adelaide Office (08) 8369 9514
Postal Address: 630 Regency Road, Broadview South Australia 5083 Phone: (08) 8369 9555 Fax: (08) 8369 9501
Melbourne Office: Suite 2262, 442 Auburn Rd, Hawthorn VIC 3122 Phone: (03) 9810 3262
Find us on Facebook @AustralasianTimber
Website www.timberbiz.com.au Printed by Lane Print, Adelaide, SA
Conditions
The opinions expressed in Australasian Timber Magazine are not necessarily the opinions of or endorsed by the editor or publisher unless otherwise stated. All articles submitted for publication become the property of the publisher. All material in Australasian Timber Magazine copyright 2022 © Ryan Media. All rights reserved. No part may be reproduced or copied in any form or by any means (graphic, electronic, or mechanical including information and retrieval systems) without written permission of the publisher. While every effort has been made to ensure the accuracy of information, the publisher will not accept responsibility for errors or omissions, or for any consequences arising from reliance on information published.
Interest rates continue to weigh on new home sales
NEW home sales declined by 15.7 per cent in the three months to September, compared to the previous quarter.
The HIA New Home Sales report – a monthly survey of the largest volume home builders in the five largest states – is a leading indicator of future detached home construction.
“This data produced the weakest quarter since June 2020, when the national lockdown drove Australia into its first recession in almost 30 years,” HIA Chief Economist Tim Reardon said.
“New home sales fell in the month of September, for the third consecutive month, by a further 4.2 per cent.
“This reflects the increasing weight that the RBA’s tightening cycle is placing on home buyer borrowing capacity,” he said.
“The RBA increased the cash rate again in October, and this will further accelerate the decline in new home sales.”
The RBA’s most acute tightening cycle in almost 30 years was occurring at the same time as the industry was experiencing the fastest increase in home building costs in almost 50 years.
Mr Reardon said that these compounding forces would see sales continue to slow and that the full impact of the rise in the cash rate was yet to emerge.
“This month’s data shows that home building is past the pandemic peak and is now set to experience a long COVID slow down,” he said.
“Given the longer-than-usual lags in this building cycle, the RBA’s rate hikes to date will similarly take longer than usual to affect the broader economy.
“Much of the impact of the RBA’s tightening cycle will be obscured until the second half of next year.
“These treacherous lags will force the RBA to wait longer to see the easing in price pressures that it desires. This could result in them weighing too heavily on household finances and jeopardising the housing industry’s future soft landing,” Mr Reardon said.
For the three months to September 2022, compared to the previous quarter, most states declined under the weight of interest rates. Victoria led the declines, down by 20.8 per cent, followed by Queensland (-17.0 per cent), New South Wales (-16.3 per cent) and Western Australia (-10.0 per cent). South Australia saw the only increase, up by 6.6 per cent.
•HIA Chief Economist
Tim Reardon
Simple signature could free up Victoria’s timber reserves but Govt won’t do it
THERE is something of a proverbial saying – dating back to the reign of Henry VIII - that says silence equals consent.
The principle is not accepted in modern English law, but it cost Sir Thomas More his head in 1535 when asked at his trial why he was silent on being asked to acknowledge the king’s supremacy over the Church.
Sir Thomas argued that his silence equalled consent, but the court held it equalled denial. The king desperately wanted Sir Thomas’ “approval”.
What’s this history lesson got to do with anything today?
The Member for Eastern Victoria Melina Bath seems to think it’s got a lot to do with the Victorian Government’s attitude to the timber industry and the industry’s inability to supply hardwood to the nation’s building industry which is cerying out for supply.
During constituency questions, she took the opportunity to raise the issue of what she described as the appalling treatment of Gippsland native timber mill workers, whose livelihoods are being destroyed by a “slack government” which has abandoned its commitment to maintain wood supply at 2019 levels.
“Third-party litigation has seen timber harvesting cease or dwindle, and wood volume is in dire shortage,” she told Parliament.
“Strangling the mills, the Andrews government is ignoring its promise to maintain the industry at 2019 levels.”
“Protections under the greater glider action statement require VicForests to retain 40 per cent in each coupe when conditions are triggered, which it has done for the last four years. The issue sits with the ambiguities and flaws in the timber code of practice. Minister, will you gazette the 40 per cent rule in the timber code of practice so it gains the legislative power for the courts to recognise and stop this third-party litigation?”
Hansard did not record a response from the Minister Lily D’Ambrosio.
So, to put a halt to the roundabout of coupes being opened by VicForests, then closed by litigation time and time again, all the Minister has to do is gazette the 40 per cent rule in the timber code of practice so it gains the legislative power for the courts to recognise and stop this third-party litigation?
It seems so.
Then, it must be asked, does this hesitancy meet the silence is consent maximum? Does this hesitancy mean the Minister is giving silent consent for the third-party litigation to continue?
That, at the end of the day, might be for the voters in Victoria to decide on November 26.
australasian
NEWS TAFE training next generation of house builders
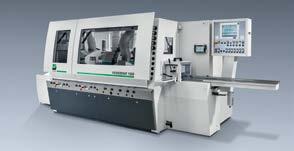
TAFE NSW is training the next generation of tradies, as the nation’s construction industry continues to thrive following a record year of house builds commencing in 2021.
The Housing Industry Association (HIA) is forecasting 125,000 houses are expected to begin construction this year across Australia, following a record 149,000 last year. This is driving hot demand for tradespeople until at least the end of 2023.
HIA’s General Manager Apprentices, Russell Holtham said TAFE NSW plays a critical role in the training of HIA apprentices in residential building trades in NSW.
“Vocational education is a key pathway into the construction industry. TAFE NSW offers students an invaluable combination of theory and practical experience, which combined with HIA’s apprentice offering means graduates are ready to hit the ground running.”
The NSW government last year announced support for 3,000 training places for women in trades with the funding intended to remove the cultural and social barriers keeping women from building sites.
New research reveals women comprise only 2 per cent of workers in construction. TAFE NSW provides women with pathways into a range of construction trades and already boasts a comparatively higher proportion of female enrolments in construction courses at 9 per cent.
TAFE NSW Nowra student Reana Bidois is studying a Certificate III in Carpentry and is an apprentice with BPL Contracting in Nowra and on the South Coast.
Reana is among a growing number of women who are capitalising on the construction boom to gain new skills, qualifications, and a new career in an industry with variety and opportunity for growth.
Since she was a teenager she’s wanted to follow in her father’s footsteps and learn a trade.
“After school I started out in hair dressing and was a nail technician for a while. I Then had a trucking business in Sydney for a while, but I always wanted to be a tradie.
“When I moved back to Nowra a few years ago I decided to become a carpenter. I started out as a laborer and was offered an apprenticeship.
“I would encourage young women coming out of school to consider a trade as their thinking about their future. Girls often talk about nursing, hairdressing, and beauty but I wouldn’t overlook a trade.
“I think as a society we’re really coming around to seeing more equality between men and women, but I think the more we see women taking the step to follow their passion and jumping into a trade, the move we will move this thinking forward.
“Being a woman in this trade isn’t something I give a lot of thought to. The tradesmen I work with don’t treat me any different. I’d say don’t be scared to try a trade, get in touch with TAFE NSW and go for it.”
“The website and the teachers can explain what’s involved and help you understand what to expect. The TAFE NSW teachers are really supportive and have real industry experience to pass on as they have all worked in the construction sector themselves.”
TAFE NSW Nowra Carpentry and Building Head Teacher John Quin, said as NSW’s leading provider of vocational education and training, TAFE NSW was uniquely positioned to arm students with the hands-on, practical skills they need to develop successful careers.
“There are so many opportunities to make a difference in a rewarding trade career, and our skills-based courses allow students to hit the ground running in local industries and stay living and working in regional areas,” Mr Quine said.
“Many of the construction sectors across NSW are experiencing growth in jobs, so there is currently an opportunity to choose from a diverse range of careers.”
Australia’s growing demand for tradies is unlikely to end any time soon, as the ongoing house building and renovation boom keeps skilled tradespeople like electricians, plumbers, carpenters, and builders busier than ever.
For more information about the range of construction industry courses available at TAFE NSW or via TAFE Digital, visit www.tafensw.edu. au or phone 131 601. • TAFE NSW Nowra student Reana Bidois
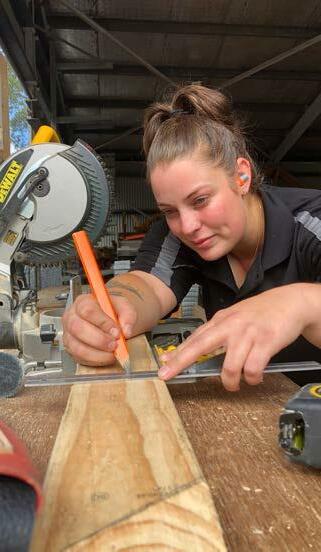
WEINIG Powermat 1500
Timber towers turning turbines
Wood has gained mainstream appeal as mass timber in the construction industry in recent years, but unexpectedly, the material has also become a viable alternative to traditional materials like steel and concrete in other industries.
For one, plywood is used to make what is reportedly the first wooden satellite called WISA Woodsat, launched in 2021.
And now, wind turbine towers are also being constructed using engineered wood, specifically laminated veneer lumber.
The company behind this turbine tower innovation is Modvion, founded by David Olivegren and co-founded by Otto Lundman and Joakim Örneblad.
According to Lundman, who is also the CEO of Modvion, Olivegren had first seen wooden wind power towers in Germany. But equipped with experience in building boats and working with architecture, he had a better idea on how to construct better wooden towers — hence Modvion.
The first project the company had embarked on was a 30m-tall prototype tower on the island of Björkö, Sweden, just outside of Gothenburg.
“That tower made people believe in our vision and made the idea real,” said Lundman.
“It also attracted the attention of one of the world’s largest wind turbine manufacturers, namely Vestas, who have since become shareholders of Modvion. Björkö will always be important for us.”
Currently, it is building its first commercial building, which will be ready in 2023. The turbine tower will be 100m tall, reaching a total height of 150m when including the turbine and the blades.
“This will be the first tower from our new production line, which will then proceed to build an even taller tower to support a larger turbine of around 6mW, which is where we will sell larger volumes. That tower will be for turbines around 250m tall,” Lundman said.
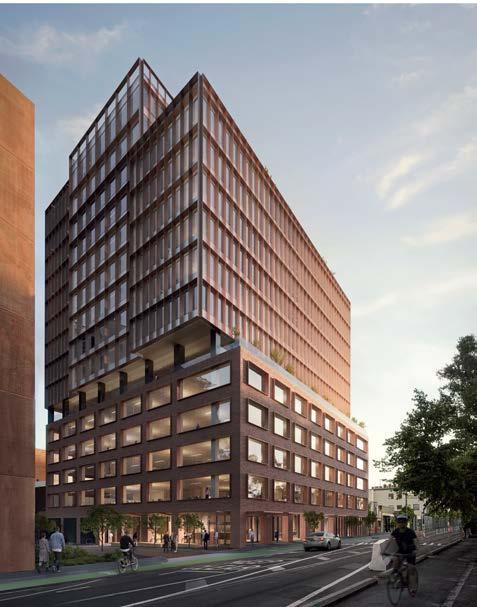
Timber mix for big build in Melbourne
PHILIP HOPKINS
THE developer Hines had formed the concept and design for its big new timber building in Melbourne, but no final decisions had been made about the type of timber. Sustainability was the key theme of the proposed building at 36 Wellington Street in Collingwood.
“Then we saw Bendigo,” said Hines construction manager, Jo Lees. Bendigo - that’s the new Government Hub being built that marks a new level in the use of mass engineered timber in a major building in Victoria.
“We loved the timber; we saw what they were doing,” Ms Lees said. “It was easy for us to tell a story on what the concept meant for us in terms of timber, the value that brings, and that lends itself to 6-Star, Green Star (environmental rating).”
All the timber in the Wellington St building comes from Victoria – Glulam (GLT) from Australian Sustainable Hardwoods (ASH) in Heyfield and CLT from X-Lam Australia in Wodonga.
The resulting 15-level, 18,500 square-metre commercial building has two levels of basement, six levels of concrete podium and nine levels of timber structure, which makes it the tallest timber structure in Australia – a mixture of certified CLT and GLT.
Hines, a US real estate investment, development and management company, has 26 timber buildings in the US at all stages from concept to completion. A total of 13 are completed. All are part of the company’s 3T Portfolio – timber, talent and technology.
Ms Lees said when the timber concept was first mooted, Hines assumed it would use European spruce. However, the Bendigo builder ICON suggested they consider ASH. “We were not sure of ASH’s capacity, but over the next six to nine months, as we got our building permits, they ramped up,” she said. “They got to the point where they could supply Bendigo and our job. We got together with ICON to formulate why we should use ASH.”
Ms Lees said several reasons showed that Australian timber was a viable option. “Cost – that always comes into it. The saving on shipping was a fairly high percentage of dollars,” she said.
“Time – having it local, three hours away, was a saving. All that ties into risk; it was a less risky proposition going local – there is better control over shipping, more quality control. Culture – they know the industry in Australia, the installers, the contractors, even things down to delivery.”
Ms Lees said ASH’s managed regrowth hardwood was a different colour, darker than European spruce. “We needed to get the architects on board. The structural properties are different as well; Vic Ash is stiffer than spruce, requiring some rework in the engineering but that worked in our favour; the stiffer timber beams and columns could be a bit more slender, using less wood for the same structural result. That was one of the many considerations,” she said.
The Wellington St building has 970 cubic metres of hardwood GLT as beams and columns, and 2350 m3 in CLT made from radiata pine. About 30 per cent of the GLT volume is columns and 70 per cent beams. “The beams and columns are all exposed. We are excited about that as it will be a great feature,” Ms Lees said.
Some CLT is exposed, but fire checks meant fire plasterboard had to be adhered to the underside of the ceilings. “We can’t have exposed CLT there. That’s a shame, it’s a lovely aesthetic.”
The podium has a brick façade with an orange, ochre that to make sure it was cost efficient, manufactured in time and looks good. That is a lot of the work – about five months collaborative with architects and engineers.”
Mr Wright said the 1000m3 of their managed regrowth hardwood amounted to about 350,000 kilograms of stored carbon. “We regrow that volume in the forest in less than five minutes,” he said.
ASH had more input into the beams and columns on the Wellington project. “We learnt lessons from previous jobs. The structural strength in our hardwood is incredible; its strength-to-weight ratio compared to its price is internationally incredible. processors cut and mould the timber to meet the requirements of the connections.
“We create a 3D model, the structure we devised with the architect and engineer – the full building is in virtual reality. Every member, every screw in that model is millimetre perfect. From that we take a shop drawing with every individual piece. I can look at the beam, for example, with its screws and brackets, and rotate it on the computer; we can see where everything is, which helps determine improvements before being manufactured,” Mr Wright said.
“That shop drawing feeds through to our robots. The robots have their own program that actually determine the best tools to use – drills, saws, milling units, chain saws. There are 160 tools on this machine. It will choose the best tool to make the cut, or the drill and our technician can override that. Technology has caught up now – you build it in the boardroom and then the robots go and make it for you.”
The building is zoned commercial and has a cafe and restaurant on ground floor. The bike and changing room are on the ground floor and not in the basement. Ms Lees said Hines management was quite surprised at the number of lockers and showers. “It’s about active transport – riding or walking to work,” she said.
These factors will contribute to the new ‘Well’ rating for buildings, a measurement that has come out of the US. “Lend Lease were the first to go for accreditation at Barangaroo. There are levels of accreditation - silver, gold, platinum – a whole range of the scorecard,” Ms Lees said.
“The pathway is similar to Green Star in terms of air quality, health and wellbeing for staff and managers – anyone who comes into contact with the building. It also includes things like amenities – yoga classes, employee support services for building management staff. A lot of Green Star feeds into it – mechanical system requirements, such as cleaner air and air quality. That’s part of the story we want to tell.”
Mr Wright said the team approach with the architect, engineer, the builder, the client and X-Lam had been a smooth process. “This is the blueprint on how to do these builds, the team has been really good; the building will come together really well,” he said. “This is the future.”
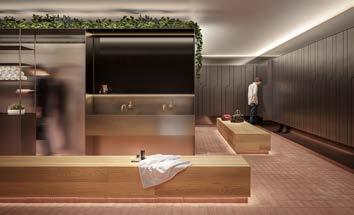
and brown colour scheme to tie into the timber. In the lobby, there is the same brickwork and some timber elements - furniture, joiners and small stairways.
ASH’s national business development manager, Daniel Wright, said unlike at Bendigo, his company took a pretty involved role this time in design and detailing. “The connections and the design from the architectural intent were the guidelines - grid spacings, floor-to-ceiling, the distance between the columns, the visual intent. They were all by the architect,” he said.
“How the joints and connections work - we helped with We have lots of data with fire testing; we understand how the wood performs in fire and how safe it is,” he said.
“We were able to start pushing cost efficiencies. The column sizes are 380 millimetres by 380mm, the beams about 700mm to 900mm deep by 380mm as well. It’s an improved efficiency of about 15 per cent compared with Bendigo, even though it has similar loads. Fire and structural knowledge help with that.”
The Wellington project will take ASH about four months to produce. It starts with CNC - ‘computer numerical control’; big robotic timber
“This is the blueprint on how to do these builds, the team has been really good; the building will come together really well... This is the future.” Stora Enzo goes pre-fab
TO meet the demand for sustainable and innovative construction solutions, Stora Enso has launched Sylva which is a massive wood building kit of pre-manufactured, custom-made applications delivered just-intime to the building site.
The solution enables faster construction, reduced costs, more efficient use of raw material and fewer emissions than concrete or steel.
“One of the major reasons why the construction industry’s carbon emissions have reached its highest level is its constant over-reliance on carbon-intensive materials such as steel and concrete,” says Lars Völkel, EVP and Head of the Wood Products division at Stora Enso.
Sylva uses cross-laminated timber (CLT), laminated veneer lumber (LVL) and glued laminated timber (GLT). The Sylva kit includes everything needed to create a modern, sustainable wooden structure for low-carbon buildings. The custom-made walls, floors, roofs, stairs, beams and columns optimise the use of massive wood to suit buildings of all types and scales.
Stora Enso’s automated coating line, being built in Austria, will further enhance the value and quality of the Sylva components by offering high-quality waterbased coatings, protecting them against moisture, sunlight, insects and fire. This will result in shorter construction times, decrease costs for construction companies, and provide added value and improved product quality.
“By delivering prefabricated, easy-to-install components to the construction sites, we respond to the increasing trend of off-site construction while offering a solution to the industry’s labour shortage. Sylva by Stora Enso is a game-changer for making this happen, replacing concrete and steel with renewable wood to enable a circular, low-carbon construction process,” said Mathieu Robert, Head of Building Solutions at Stora Enso.
NEWS Atlassian build gets under way
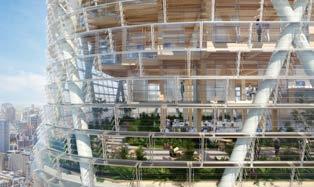
CONSTRUCTION firms from Japan and Australia have started work on a 182-meter-high skyscraper in central Sydney in what is planned to be the world’s tallest hybrid-timber building using an eco-friendly wood product.
Tokyo-based Obayashi and Sydney-based Built plan to complete construction on the 39-story Atlassian Central in 2026. The building will be used for offices, accommodation and retail outlets, the companies said in recent press releases.
The companies aim to cut carbon dioxide emissions during construction by 50% or more compared to a conventional building project and operate the tower entirely with renewable energy, they said.
The seventh floor upwards will feature a hybrid-timber structure that consists of a combination of steel frames and cross-laminated timber — or a wood panel product made from glued layers of sawed lumber.
The product is said to emit less carbon dioxide in production and is lighter than concrete. It can also be recycled for other uses, according to the Japanese construction firm.
Reinforced concrete will be used below the seventh floor, including the basement, the two builders said.
“Nothing about this project is typical,” said Built CEO and managing director Brett Mason in a company press release.
“It has been designed and developed to be a proof of concept for what the future of buildings should look like that are low impact on the environment in both construction and operation.”
Obayashi has been emphasizing in its home market the construction of low-emission wood buildings and increasing the use of the eco-friendly lumber product.
Top architect on Tassie tour
CLAIRE BENNETT
JAMES Fitzpatrick at fitzpatrick+partners Architects continues to use crosslaminated timber on many of his projects.
In fact, his firm has invested significantly in the research of CLT and other engineered timbers in buildings, with an aim to help lessen the built environment’s impact on the planet.
James’ search for an innovative timber manufacturer led him recently, along with his client and engineer, to Cusp’s manufacturing facility in Wynyard, Tasmania.
His visit and comments attest to the quality of Cusp’s products.
“It was great to catch up with Michael Lee and the Cusp Team and see the final commercial grade CLT and glulam products in full production,” he said.
“The Eucalyptus Nitens produces a face quality beyond expectations and combining this with the structural properties of a hardwood will see us using these products in many of our projects moving forward.”
“Congratulations to all on an exemplary process – from idea to reality.”
James founded fitzpatrick+ partners in 2000. Fast forward two decades later and the Sydneybased design studio employs some 60 architects working on projects • Cusp General Manager Michael Lee with leading Sydney architect James Fitzpatrick
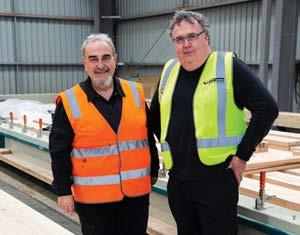
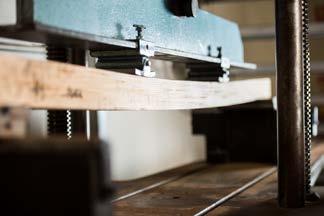
across Australia. They’ve won multiple awards for their sustainable, leading-edge approach to residential, interior and commercial building designs.
Fitzpatrick+partners is currently working on Australia’s first seven-story timber healthcare building – which is due for completion in early 2023. They’re also pioneers in sustainable architecture, delivering the first 6-star Green Star as-built office building in NSW, and have recently developed a carbon measuring tool for architects.
“In the spirit that working together is the only way we can address our climate emergency, we have released this product to the Australian market at no cost,” James said.
Cusp General Manager Michael Lee said he first met James and introduced the Cusp product to him when he toured the state as part of the Tasmanian Visiting Architects Program several years ago.
James’ visit to the Cusp facility was the first time he’d laid eyes on the product.
“You’ve got one of the leading architects and designers in the country saying really positive remarks about our product,” he said.
James doesn’t talk about sustainability, he lives it. He’s a timber fanatic. His designs are impeccable. His own dwelling, the Seed House, is a monument to timber and a moment to mass timber builds, with CLT incorporated in it. I can’t speak highly enough of his work.”
NEWS MBA forecasts a bumpy ride ahead
MASTER Builders Australia is predicting a bumpy ride for residential building but a more favourable medium- term outlook for non-residential and civil construction in its update to its forecasts for the building and construction industry out to 2026.
In the post-pandemic economic environment of interest rate rises, surging inflation, and unemployment at a 50-year low, the latest forecasts indicate that activity is still likely to expand modestly over the medium term despite the effect of short-term challenges. However, there will be considerable variation in the pattern of growth by subsector.
Even though about 200,000 new homes need to be built each year to accommodate long-term population growth, we are likely to fall significantly short of this until 2026. Activity on the medium-high density side of the market is likely to be particularly slow.
“While pandemic conditions brought forward some residential building demand, the current economic conditions of interest rates hikes, inflation increases, and continued shortage of workers and materials, are significantly contributing to the decline,” Master Builders Australia Chief Executive Denita Wawn said.
Long-term supply constraints continue to hamper residential building, with Master Builders Australia supporting the decision by the Federal Government to establish the Housing Supply Council in conjunction with State and Territory Governments.
“Our members continue to be frustrated with lengthy delays in approvals for land title, building applications, and occupation certificates. Shortage of land in the right places, high developer charges, and inflexible planning laws also restrict opportunities to meet the housing needs of our future. These long-term supply challenges are the responsibility of State and Territory Governments,” she said.
The outlook for non-residential building activity (social, cultural, retail, commercial and warehousing) is reasonable with a small decline in 2023 but steady increase from 2024 to 2026.
“Master Builders remains concerned about the potential impact of unfavourable changes to the industrial relations framework for non-residential activity. Changes already made and intended are likely to mean higher costs and lengthier rollout times. Were it not for these changes, the forecast growth rates would be more substantial,” Mrs Wawn said.
Civil and engineering construction is likely to show the strongest performance of the three sectors of the industry and while a small decline is forecast for 2023, growth is forecast for 2024-26. However, the industrial relations changes currently under implementation will prevent growth here from reaching its full potential over our forecast horizon and beyond.
Staying ahead of the curve Keeping pace with increased order volume made difficult
GREG GILL, REGIONAL DIRECTOR OF SALES ACROSS APAC AT ECI SOFTWARE SOLUTIONS.
THE Australian timber industry continues to face challenges, with supply chain issues, skill shortages and increases in material costs all impacting growth. Now, many are realising that to stay ahead of the curve and ensure profitability, an innovative solution must be deployed to help with the daily running of businesses and bring in new opportunities.
A CHANGING INDUSTRY
Despite the many challenges, the construction industry is experiencing a post-pandemic boom as home and building renovations continue alongside major infrastructure projects fuelled by government investment. However, for many merchant businesses, keeping pace with increased order volume is made difficult by a lack of skilled workers. According to Arcadis’ 2022 International Construction Costs Index report, there has been an 80 per cent increase in unfilled roles within construction since 2019 and have predicted by 2023 there will be over 100,000 vacancies.
It further stated that this is the ‘challenge of the decade’ due to skill shortages and now many businesses are focusing on ways to invest in reliable digital methods to help mitigate these issues and improve outcomes.
IMPROVE EFFICIENCY ACROSS THE BUSINESS
For merchant businesses considering new technology, deploying integrated business management software can streamline processes and improve operational efficiency. Interestingly, Architecture and Design reported that the industry was named the least digitised sector in 2016, with under 40 per cent of companies looking to adopt a digital transformation roadmap.
Faced with labour shortages, we expect to see businesses of all sizes reconsidering this decision, owing to the significant efficiency savings.
For example, using an ERP system that integrates document management reduces the administrative burden associated with running a busy merchant business. Not only does this free up your team’s time to focus on more value-add activities, it can also allow you to easily scale or open a new branch. With all key documents stored on the cloud, including handwritten and faxed documents, all employees can gain instant access to customer order history, inventory and invoices - removing the need for long telephone conversations or email chains.
Similarly, cloud-based solutions remove the need for employees to spend hours filing or documenting paperwork. Not only does this save time, it also prevents the chance of customer data being lost or misplaced - something that could potentially result in a poor customer experience.
BETTER VISIBILITY
With the supply chain and labour shortages crisis ongoing, making good business decisions is essential. With all key information stored on a central system, each department can view the necessary data, metrics and order status’ quickly and easily. Should last minute situations arise, such as an unforeseen order delay or a customer placing a large order, having these comprehensive reports to hand and real-time data available will facilitate smarter decision making.
Similarly, with full visibility of metrics, it’s easier to analyse sales and measure profitability, without teams having to lose time sifting through multiple spreadsheets and paper trails.
BOOST CUSTOMER SERVICE
Meeting customer demand can put a lot of pressure on employees, especially given the high number of vacancies many businesses are currently facing. With a fully integrated business management solution, staff can easily manage different options for ordering and delivery - not only saving them time but also ensuring a positive customer experience. Similarly, the system can remember customers’ previous purchases, making order planning far easier from an operational point of view.
Sometimes delayed delivery can happen, but ensuring there is no miscommunication between the customer and the business improves customer satisfaction. Quickly answering customer queries and using the dashboard to provide updates on the latest changes to their order status will help to resolve any potential issues faster.
With the increased vacancies continuing to rise, building an efficient team that can meet those tight deadlines can be tricky. Taking the time to incorporate a digital solution will support the business to manage high workloads whilst boosting productivity and future sales.
To find out more about how ECI can help your business please visit our website: https://www.ecisolutions. com/en-gb/builders-merchants-software/spruce/
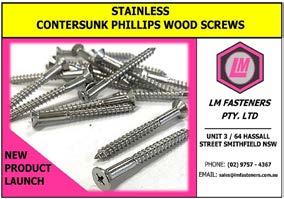
Pulp is not making it to Opal
PHILIP HOPKINS

THE Victorian Government has only supplied 15-20 per cent of its promised wood pulp commitment to Opal Australian Paper over the past 13 years, the Government has admitted.
The figures were tabled in State Parliament by the Minister for Agriculture, Gayle Tierney, in response to a series of questions from the Independent Member for Morwell, Russell Northe.
The Government’s 1996 agreement requires it to supply a minimum of 350,000 cubic metres of pulpwood each year between 2010-11 and 202930 to the Maryvale pulp and paper mill.
Australian Paper’s 2018 Sustainability Report shows that the Maryvale mill bought 1.65 million tonnes of pulp wood for its operations; 68 per cent was supplied by Hancock Victorian Plantations and 26 per cent from VicForests, with hardwood residues from sawmills making up the remaining 6 per cent.
Ms Tierney told Parliament that after the 2009 bushfires, the government reduced the annual supply of ‘mountain forest’ pulpwood (mountain ash or alpine ash) to 265,000 cubic metres.
“The government continues to supply approximately 50,000 cubic metres of mixed species pulpwood under the agreement,” she said.
In June 2020, the agreement was varied to allow silvertop ash to be substituted for mountain forest pulp log. Silvertop ash is classified as ‘mixed species’ timber.
Ms Tierney said the variation provided for a proportion of up to 40,000 cubic metres of mountain forest pulpwood to be substituted with silvertop ash for the period 2019-21 to 2023-24 inclusive.
“A number of other clauses in the agreement allow for variations,” she said. VicForests manages the supply of pulpwood to the Maryvale mill on behalf of the Victorian Government.
Mr Northe pressed for information on which forest areas supplied the timber, but Ms Tierney said the specific details of VicForests’ supply to the mill, including volumes and prices for supply from different forest management areas, were “commercial-inconfidence”.
Queried on the impact a shortfall in supply would have on Maryvale, Ms Tierney said Opal was continuing to liaise closely with many of its suppliers, including VicForests and Hancock Victorian Plantations, “to successfully maintain its operations”.
Mr Northe pushed for information on the impact of third-party litigation on native timber harvesting over multiple decades.
“Third parties have taken legal action under the Code of Practice for Timber Production 2014 as well as earlier versions of the code,” Ms Tierney said.
“In 2021 and 2022, the government • Loading logs at Opal Australian paper
varied the code and the Conservation, Forests and Lands Act 1987 to create greater certainty regarding the implementation of the code. Further public consultation has taken place on additional amendments to the code that will come into effect in 2022.”
Queried on what impact the litigation was having on direct and indirect jobs for forest contractors, Ms Tierney said contractors experiencing difficulties with stand-downs due to litigation “are encouraged to contact VicForests regarding the temporary support that is available for their businesses and their workers”.
Ms Tierney acknowledged that VicForests successfully appealed against the Federal Court’s May 2020 decision in favour of the Friends of the Leadbeater’s Possum action against VicForests.
“As other matters are currently before the Courts with judgement reserved, I will not make any further comment,” she said.
Mr Northe asked what the Government was doing to ensure supply in the face of unsuccessful litigation. Ms Tierney said it was difficult to quantify the impact of unsuccessful legal actions, which typically involve temporary injunctions that are subsequently lifted.
“VicForests updates its harvesting methods and locations regularly in response to new research findings, bushfires and other events. Legal cases also consider changes in the harvesting environment,” she said.
“As such, it is difficult to recreate the baseline scenario in which third-party litigation did not occur and coupes were harvested in a substantially different order over an extended period of time.
VicForests has worked closely with contractors to minimise employment impacts.”
Forest contractors in Gippsland have currently no work and two mills in East Gippsland are running out of timber due to legal action by environmentalists and decisions by the Supreme Court.
SIMPLY BETTER

