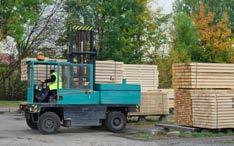
3 minute read
Forklifts
FORKLIFTS Keeping it all safe
MOST forklifts drive around in conventional warehouses where pallet racking is up to 4 metres high.
In those applications, warehouse managers prefer to use short trucks that can be used in narrower aisles, as this optimum use of space helps to improve storage capacity.
If there is space above, they like to extend the racking and utilise trucks with higher masts. However, there are still boundaries for the movement space required by a counterbalance truck. When the height of a warehouse really needs to be utilised, other materials handling equipment will be deployed.
VNA trucks or rail-guided cranes are specialised and highly efficient solutions, but are primarily to be used within the aisle. More flexibility is provided by the reach truck, which can often put pallets away at well above 10 metres, but can also be deployed for transporting pallets over distances.
Whilst being extremely stable, putting pallets away using a reach truck causes visibility challenges by default. Naturally, to work safely, these machines should be manned by your best trained drivers and obviously your load carriers must be faultless. Nothing is more dangerous than working with damaged or inferior pallets. Sure, pallet beams in fluorescent colours will help to put the pallet away, but real advantages are found within the reach truck itself.
HOW CAN YOU MAKE SURE PALLETS ARE LOADED IN THE SAFEST WAY? HERE ARE 3 FACTORS THAT CAN MAKE ALL THE DIFFERENCE.
1. DESIGN
First of all, only use reach trucks with a design that maximises the operator’s view of high loads. Overhead guards should be designed in such a way that they not only protect against falling goods, but also offer an excellent view through the bars on the fork tips. Pay attention to the design of the mast itself or the fork carriage. Are they slender enough for the operator to see through and have good visibility of the load?
KEY POINTS
■Explore whether you can utilise the warehouse space better by switching to reach trucks. Have a walk through the warehouse with your expert forklift dealer. Find your nearest dealer here. ■Review retrofit options to enhance productivity. ■Check whether you can improve operations by only switching the masts and opt for versions with sway control or dampened ‘no knock’ transitions between mast stages. 2. SMART FEATURES
Choose a reach truck with well-thought-out features that help put the pallet away safely. In some cases, these may also be available as a retrofit. Ideally, use a reach truck equipped with a camera/monitor combination and a pre-set height selector. Such a selector will help the mast stop at exactly the right height and often the steps will be aligned with the height of the beams in the pallet racks. Automatic centring of the fork tilt and side shifting in advance will also improve the safety and reduce cycle times. There is no such thing as too much effort when it comes to minimising risks. 3. SWAY
When lifting heavier pallets above 10 metres, gravity and lateral forces come into play. When stopping, a mast might rock back and forth for a moment, meaning the operator has to wait for the movement to cease before they can put the pallet away. In materials handling this is called ‘sway’. Some reach trucks offer features that reduce these mast movements. For example, reach trucks can be equipped with passive sway control, where the chassis moves slightly to compensate for elevated load motion to dampen it. Active sway control is delivered by software which pro-actively delivers the correct adjustment to counteract the mast’s sway.
Safety Storage Efficiency Safety Storage Efficiency Enhance the Safety, Storage and Efficiency of your Timber Storage
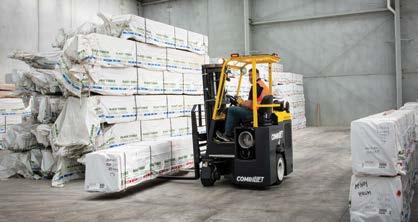
Combilift is the perfect fit for the Timber industry. Our multidirectional forklifts and pedestrian reach trucks will allow you to maximise the storage, efficiency and safety of your warehouse & storage facility.
combilift.comContact Us Today
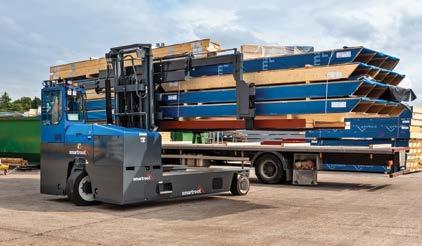
To find out how Combilift can help you safely and efficiently load containers