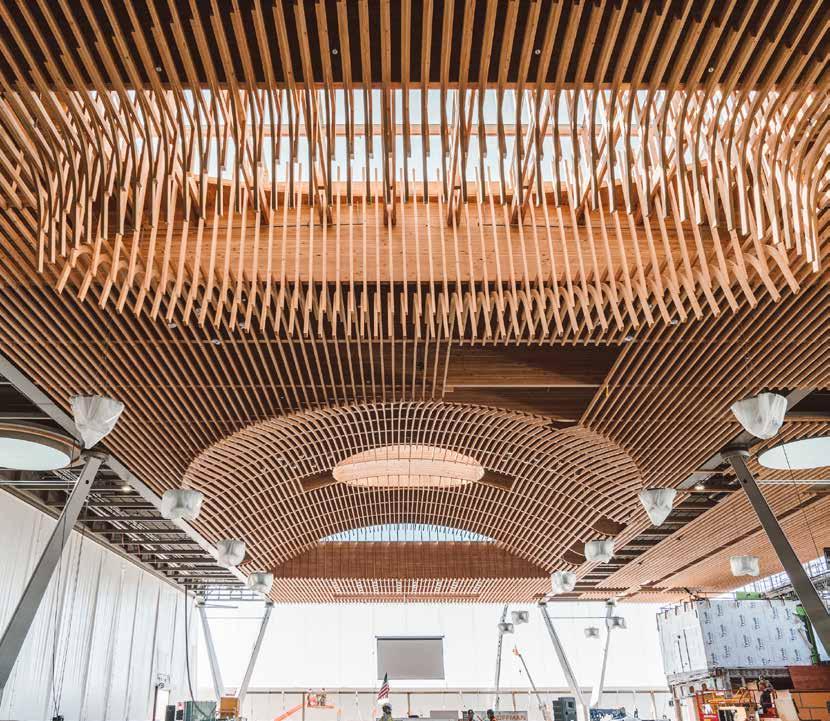
Raising the roof in Portland Qld's timber solution for housing shortage France’s timber lesson for Australia
Raising the roof in Portland Qld's timber solution for housing shortage France’s timber lesson for Australia
The I-Joist line is a high-speed line for the manufacture of I-Joists from LVL billets and OSB sheets. Features are;
• High-speed output, producing beams in excess of 15-20m/min.
• Has the capability of cutting LVL billets into Chords for the I-Joist production but also LVL into sticks for resale.
• Webs are processed from OSB sheets, typically 2.4mx1.2m in size.
• Utilising PUR glue for the bonding (other glues can be used).
• Sensors are installed to monitor the glue flow rate and spread to ensure accurate coverage.
• Printing is available.
• I-joists are accurately cut to length.
• Finished I-Joists are stacked into packs for strapping.
• Relatively small footprint, 85m x 25m maximum. Will be smaller if certain sections not required.
• Australian Made and serviced with all supportห done by MPB Engineering.
Volume 35 – Issue 1
Incorporating Australian and New Zealand Timberman. Established 1977.
Front Cover:
The PDX Airport Main Terminal expansion in Portland stands as the largest mass timber project ever undertaken. The decision to use mass timber for the terminal’s 3.6ha roof was driven by a desire to celebrate the Pacific Northwest’s timber industry.
Story page 8-9
Publisher and Chief Executive: Hartley Higgins
General Manager: Robyn Haworth
Editor: Bruce Mitchell b.mitchell@ryanmediapl.com.au
Advertising: Jamie Richardson j.richardson@winetitles.com.au
Adelaide Office (08) 8369 9514
Production & Creative Services: Robyn Haworth
Timber classifieds: j.richardson@winetitles.com.au
Adelaide Office (08) 8369 9514
Subscriptions: subs@forestsandtimber.com.au
Adelaide Office (08) 8369 9500
Subcription rates Free
Accounts:
Adelaide Office (08) 8369 9500
Postal Address: 630 Regency Road, Broadview South Australia 5083 Phone: (08) 8369 9500
Melbourne Office: Suite 2262, 442 Auburn Rd, Hawthorn VIC 3122 Phone: (03) 9810 3262
Find us on Facebook @AustralasianTimber Website www.timberbiz.com.au
Conditions
The opinions expressed in Australasian Timber Magazine are not necessarily the opinions of or endorsed by the editor or publisher unless otherwise stated.
All articles submitted for publication become the property of the publisher. All material in Australasian Timber Magazine copyright 2022 © Ryan Media. All rights reserved. No part may be reproduced or copied in any form or by any means (graphic, electronic, or mechanical including information and retrieval systems) without written permission of the publisher. While every effort has been made to ensure the accuracy of information, the publisher will not accept responsibility for errors or omissions, or for any consequences arising from reliance on information published.
Portland’s new main airport terminal in Oregon shows what can really be achieved with timber in large –very large – projects.
And it demonstrates bit time that timber is a totally sustainable resource.
The terminal’s swallowed up 3.5 million board feet of wood in the roof, concessions, flooring, and feature walls were sourced from within a 483km radius of the airport.
The decision to use mass timber for the terminal’s 3.6ha roof was driven by considerations of cost, constructability, and a desire to celebrate the Pacific Northwest’s timber industry.
The roof, which includes fortynine skylights of varying shapes and sizes, filters natural light into sixty percent of the terminal.
The structure, constructed from mass plywood panels, glulam beams, and timber lattice, showcases traditional weaving techniques indigenous to the region.
This intricate design not only highlights the craftsmanship involved but also contributes to the terminal’s sustainability by reducing the need for steel and other materials.
It’s a growing trend in Australia as well with more and more architects turning to wood for all the right reasons.
Cross-laminated timber features heavily in the Timber Design Award-winning Kirby Building at Macquarie University.
Apart from the beauty, the use of CLT reduced the building’s carbon footprint.
Slowly, the environmental benefits and sustainability that building with wood delivers is making its mark.
If the 31-storey The Edison - North America’s largest mass timber project – is anything to go by, the sky is indeed the limit.
The rise of increasingly sought after, timber framed lifestyle dwellings is helping to free up housing stock across Australia.
On the Fraser Coast, home to Hyne Timber - one of Australia’s oldest and largest softwood manufacturers, their framing is currently being used for almost 800 new lifestyle dwellings being built by Brighton Homes alone.
These are located across three village developments on behalf of Brighton Homes clients, Ingenia, Stockwell Group and Green Fort Capital.
Typically, over 50’s homeowners sell their home to move into a ‘right size’ lifestyle village without a mortgage –thereby freeing up housing stock for next generations.
According to the 2021 ABS Census, 250,000 Australians reside in retirement communities which is a 23% increase from the 2016 data. This number is
expected to exponentially grow with our aging population and 458 operators of retirement communities across the country.
According to the Retirement Living Council ‘Better Housing for Better Health’ report, the current pipeline of retirement communities will reduce the housing shortage by 18%. Further growth of this pipeline to meet the ongoing demand, could further reduce Australia’s housing shortage by 67% by 2030. (Source: https:// www.propertycouncil.com.au/ submissions/better-housing-forbetter-health)
Brighton Homes Business Development Manager, Patrick Cumner, said their own pipeline for retirement villages will deliver almost 12,000 dwellings across Queensland in the next few years.
“Lifestyle villages have been hugely popular across America for many years and this model is taking off here in Australia.
“These centrally located
villages can have hundreds of low maintenance dwellings along with the popular, shared facilities, services and social programs which make these communities so desirable for healthy and active retirees.
“In the most part, homeowners do not own the village land on which their home sits, and therefore, by law, the home must be relocatable. This type of construction lends itself to timber while also delivering the many user-friendly and environmental benefits our locally grown timber provides.
“Evidence demonstrates that his shift to lifestyle villages can only have a very positive impact on our retirees, the broader community and the Australian economy including housing availability for our next generations.” Mr Cumner said.
James Hyne, Stakeholder Engagement Manager for the Hyne Group said this is a great
step in the right direction for housing availability,
“With the housing and land availability challenges here in Australia, this type of lifestyle model is contributing positively to our communities in many ways.
“Not only are these lifestyle villages in hot demand, but they’re also being largely built using timber for a range of benefits including the ability to relocate them, quieter buildings, locally grown, locally manufactured and locally processed into frames and trusses at companies such as Brett’s Timber and Hardware and CQ Building Supplies.
“From a pine seedling to a new home, thousands of local jobs make up these dwellings, further supporting our regional economy.”
With an estimated 3,500m3 of timber to be used for the three Hervey Bay lifestyle villages, this volume of timber will sequester approximately 2,500 tonnes of carbon from the atmosphere which is the equivalent to 1,270 cars off the road for a year.
This volume of structural
graded, softwood plantation pine will have regrown across the Australian softwood plantation estate in just 10 hours. Construction doesn’t get more renewable than that.
Whites Timber Products Pty Ltd ACN 647 042 751 convicted and fined for private native forestry offences.
Whites Timber Products Pty Ltd ACN 647 042 751 (Whites Timber) was prosecuted by the NSW Environment Protection Authority (EPA) and pleaded guilty to three offences related to contraventions of the Private Native Forestry Code of Practice for Southern NSW (2008) (PNF Code)
Between about 20 September 2021 and 22 November 2021 forestry operations were carried out at a premises in Kybeyan by Whites Timber. As a result of their forestry operations, Whites Timber committed the following offences against section 60ZZA(1) of the Local Land Services Act 2013 (NSW) (LLS Act):
1. Whites Timber failed to retain the minimum number of habitat trees required (being at least 20 habitat trees per 2 hectares), in contravention of clause 4.2(1) of the PNF Code and section 60ZZA(1) of the LLS Act.
2. Whites Timber reduced the stand basal area (in the southern harvesting area) to a mean below the minimum limit of 12m2/ha in Table A, in contravention of clause 3.1(1) of the PNF Code (read together with clause 3.1(2)) and section 60ZZA(1) of the LLS Act.
3. Whites Timber reduced the stand basal area (in the southern harvesting area) to a mean below the minimum limit of 16 m2/ha in Table A, in contravention of clause 3.1(1) of the PNF Code (read together with clause 3.1(2)) and section 60ZZA(1) of the LLS Act.
On 12 December 2024, the Land and Environment Court of New South Wales convicted Whites Timber for the three offences against section 60ZZA(1) of the LLS Act and made the following orders:
1. Whites Timber Products is convicted of the offence against section 60ZZA(1) of the Local Land Services Act 2013 (NSW) as charged and is to pay a fine of $100,000.
2. Whites Timber Products is convicted of the offence against section 60ZZA(1) of the Local Land Services Act 2013 (NSW) as charged and is to pay a fine of $200,000.
3. Whites Timber Products is convicted of the offence against section 60ZZA(1) of the Local Land Services Act 2013 (NSW) as charged and is to pay a fine of $300,000.
4. Pursuant to section 122 of the Fines Act 1996 (NSW), a moiety of 50 percent of any fine determined by the Court, be paid to the prosecutor.
5. Pursuant to section 257B of the Criminal Procedure Act 1986 (NSW), Whites Timber Products is to pay the Environment Protection Authority’s legal costs as agreed or as may be determined under section 257G of the Criminal Procedure Act 1986 (NSW).
The Court’s judgement may be accessed at https://www.austlii.edu.au/cgi-bin/viewdoc/au/cases/nsw/ NSWLEC/2024/135.html#_Toc184901110
WoodSolutions has stepped in as a sponsor the Master Builders National Excellence in Building and Construction Awards, an event that celebrates Australia’s best builders and their contributions to the construction industry.
This prestigious event highlights achievements across residential, commercial, and infrastructure projects.
The WoodSolutions program is resourced by Forest & Wood Products Australia (FWPA), a not-for-profit organisation committed to driving demand for and enhancing the value of wood products. Through its free resources, expert guidance, and practical solutions, WoodSolutions helps professionals across the building and design sectors embrace timber as a sustainable and innovative choice across the built environment.
As part of its commitment to sustainability in the built environment, WoodSolutions supports three award categories: the Sustainable Residential Building Award, the Sustainable Commercial Building Award, and the National Contract Home Award ($750,000 to $1 million). These categories spotlight innovative practices in sustainable design, material use, and construction processes that are transforming the built environment. By sponsoring these awards, WoodSolutions aligns its mission of increasing demand for innovative, sustainable, and competitive timber products with its dedication to environmental stewardship and industry advancement.
The Awards provide a
platform for professionals to exchange ideas and showcase excellence, fostering education and innovation—values that WoodSolutions champions through its extensive free resources, including technical guides, webinars, and the WoodSolutions Campus for selfpaced learning.
Attending this event also allowed the WoodSolutions Timber Framing Campaign Manager, Chris Briggs, to engage directly with the design and construction community, helping builders and designers discover the versatile and sustainable potential of timber.
“This collaboration strengthens the industry’s commitment to creating structures that are not only functional but environmentally responsible,” said Briggs.
“The use of timber in these winning projects is apparent and the ways the builders are incorporating it into the structures and the aesthetic design details is growing,” Briggs continued.
“I think these projects really celebrate the value of choosing wood in our frames and recognising how good it makes us feel to occupy the spaces where wood surrounds us.”
The WoodSolutions National Sustainability Residential Building Award went to Davies Construction in TasmaniaExternal link. This sustainability conscious project incorporates a compact design and energy-efficient construction that minimises heating requirements. Davies Construction applied Passivhaus principles for the first time, demonstrating a commitment to planet-focused building
methods. Utilising Trombe walls and materials with high thermal mass, it effectively generates and retains heat. The studio operates as a net-positive energy system, producing its own power and feeding surplus electricity back to the grid. Materials, finishes, and systems were carefully chosen for their durability, low maintenance needs, and environmental sustainability. Water efficiency is addressed through innovative storage solutions and resourcesaving fittings.
This project not only exemplifies sustainability but also acts as an educational platform, reflecting the company’s dedication to advancing sustainable construction practices.
The WoodSolutions National Contract Home ($750,000 to $1 million) winner was Scott Salisbury Homes from South Australia.External link This
exquisite design by Scott Salisbury Homes showcases a remarkable blend of innovative design, superior craftsmanship, and impeccable quality. The residence’s striking curved façade invites you into a meticulously designed interior where every element is thoughtfully executed with wood floors and accents throughout.
Curved architectural elements merge functionality with aesthetic appeal. Designed to harmonise the outside and inside living spaces, this project epitomises sophistication.
advanced the sustainability of the River’s Edge project at the University of Tasmania Inveresk Campus, achieving an impressive 32% reduction in embodied carbon compared to conventional construction methods.
WoodSolutions extends congratulations to Davies Construction, Scott Salisbury Homes, and Fairbrother Construction for their remarkable achievements at the Master Builders National Excellence in Building and Construction Awards. These award-winning projects exemplify the integration of innovative design, sustainable materials, and outstanding craftsmanship, setting a high standard for the industry.
Finally, the WoodSolutions National Sustainability in a Commercial Building Award was given to Fairbrother Construction for another big win out of TasmaniaExternal link. Through innovative collaboration and early contractor involvement, Fairbrother has significantly
WM_Advert_Australasian Timber Magazine_185X1230_AUS_Jan25_PRC.pdf 1 2025/01/20 20:52
This achievement is attributed to a comprehensive range of strategies, including the recycling of steel gas pipes for driven piles, minimising the use of applied finishes, and prioritising locally sourced materials. Key materials such as carbon-neutral bricks, responsibly sourced timber, and other environmentally sustainable products have been integral to the project’s success. The scale and quality of these initiatives position the River’s Edge project as a pioneering example of sustainable building practices, setting a new benchmark for reducing environmental impact in the construction industry.
As a proud sponsor of these awards, WoodSolutions is honoured to celebrate the creativity and dedication demonstrated by these companies. Their exceptional work not only elevates industry practices but also inspires the broader design and construction community to embrace sustainable building solutions.
The numbers attached to Portland’s new main airport terminal in Oregon are truly staggering.
The terminal’s 3.6 hectare used 3.5 million board feet of wood used in the roof, concessions, flooring, and feature walls were sourced from within a 483km radius of the airport. The wood includes contributions from small family-owned forests, non-profits, and tribal nations. This sustainable approach by the architects at ZGF both supports local economies and highlights Oregon’s tradition of forest product innovation.
The roof features 24.3 metre long, single-span glue lam beams, with 277 such beams and 500,000 lineal feet of lattice. The project required modular construction to avoid airport disruptions, using 20 modules and seismic isolators. The roof’s design included 35,000 supply panels and 1,200 pieces.
The project showcased the potential of mass timber in the US, emphasizing speed, precision, and sustainability.
The PDX Airport Main Terminal expansion in Portland simply stands as the largest mass timber project ever undertaken.
The decision to use mass timber for the terminal’s 3.6ha roof was driven by considerations of cost, constructability, and a desire to celebrate the Pacific Northwest’s timber industry. The roof, which includes forty-nine skylights of varying shapes and sizes, filters natural light into sixty percent of the terminal. The structure, constructed from mass plywood panels, glulam beams, and timber lattice, showcases traditional weaving techniques indigenous to the region. This intricate design not only highlights the craftsmanship involved but also contributes to the terminal’s sustainability by reducing the need for steel and other materials.
Instead of constructing an entirely new terminal, the Port of Portland and ZGF opted for a phased renovation and expansion. This approach
allowed the airport to remain fully operational throughout the five-year construction period. The prefabricated wood roof, which spans the expanded lobby, check-in, and security areas, played a crucial role in minimizing disruptions. This strategy not only saved time and costs but also reduced the carbon footprint of the project.
To avoid disruption to the traveling public, the new roof was being built 800 metres away from the existing airport roof, then disassembled in 100x300 modules and assembled above the existing roof in segments over a one-year period.
Timberlab (formerly known as Swinerton Mass Timber) came onto the project in 2019 in a design-assist role to ensure the design of the mass timber roof structure could be manufactured and procured from regional timber manufacturers – sustainably and cost-effectively.
Timberlab’s director of manufacturing Jared Revay told
last year’s Timber Construct 2024 conference sourcing on the product was important to the airport.
“They said, ‘We don’t want you to just create this amazing roof that’s got all these organic shapes. We want you to take our investment and invest it into the local economy, into local forests that are indigenous cultures and also small family forests, restoration forests and forests,” Mr Revay told the conference.
He said this was the first time Timberlab had seen a specification like this.
“It was really working with an architect that was flexible to developing a specification that allowed us to help them tell a story of where the wood came from and why it was significant for this project.
“Some of the families and tribes that this wood came from in the Northwest just wanted to share that a little bit,” he said.
But then came the manufacturing issues.
“This was where the real challenge came because how do you get 277 of these beams made and on a production style basis, where they all have to be perfect, literally perfect, often some tolerance, but most more within an eighth tolerance throughout the entire beam,” Mr Revay said.
“And then also pushing the limits with the certification bodies developing beams that were ninefoot 3d and 80 feet long.
“And what this looked like was developing a way that we could build these beams confidently.
“We even went as far as getting steel templates that were laser cut to be precise to help lay out the cold form jigs to ensure that the shape was going to be perfect.”
“And we did a mock up install, and we went as far as scanning it and to ensure that it could fit back into the building perfectly.”
Mr Revay said that once everything was in place things happened very quickly.
“Once we got the teams out there and the instruction booklets, the materials labelled, there’s nothing like watching a project go up, because that’s where the true testament of a speed infrastructure, and watching how the circle on that skylight came together, and how beautiful it looked and how perfect it was.”
He said the general contractor was “mind blown” after we put this together.
“He got ready to be up there with saws and jigsaws trying to cut that circle perfectly, but it came together like a dream,” he said.
It defies the image of a cold, academic building designed only for learning by using timber generously.
In doing so, the Michael Kirby Building at Macquarie University stands as a testament to sustainable design and architectural innovation.
And its transformation from a 1980s concrete structure into a modern, timber-framed edifice won its architects Hassell Studio the 2024 Timber Design Award for Excellence In Timber Design.
It has been noted in the TDA magazine that the use of crosslaminated timber not only reduced the building’s carbon footprint but also created an inviting atmosphere conducive to learning and collaboration.
The Law School Project involved the redevelopment of the existing C5C building, including all services, amenities, and infrastructure. This included the demolition of levels 2 and 3 and the partial demolition of ground floor and level 1, and the retention of the existing first floor slab and column structural elements as well as two existing in-ground theatres.
● Structural Engineer: Taylor Thompson Whitting (TTW)
● Builder: FDC Construction (NSW)
● Fabricators: Rubner Holzbau, KLH Massivholz
● Photographer: Nicole England
● Location: Macquarie Park, Sydney, New South Wale
The TDA magazine says the resulting structure is a four-storey building incorporating mass timber on top of and around the retained first floor slab structures, as well as two new concrete cores. The large open central atrium, which contains a scenic lift, architectural helical staircase and cantilevered CLT meeting rooms, is a key design feature. The redeveloped building has an increased
height up to 4 storeys and an approximate gross floor area of 8,610 square metres
Major project supplier WAbased Mortlock Timbers says the space has an extensive amount of timber and the material palette considers both the comfort and the well-being of students and faculty in the building.
The company says architects such as Hassell look to
subconsciously link nature and biophilic considerations in designs such as these to improve the wellbeing of an individual.
“Our Proplank click-in batten system can be found along the ground floor of the building. The 30x20mm batten ceiling features near 11,000 lineal meters of our American oak, pre-finished in Enviro Clear,” Mortock says.
“This finishing product is a
smooth, film-forming coating that is used exclusively for internal timber installations. This is primarily because it allows for easy maintenance when specified for high-traffic areas.”
Hassell says the upcycled Michael Kirby Building brings a new, revitalised energy to the heart of Macquarie University’s Wallumattagal Campus and creates an enduring legacy with flexibility to cater to future changes.
“The adaptive reuse of an existing ground and firstfloor concrete structure has transformed the 1985-built administration centre into a more expansive and flexible fourstorey building featuring a lighter, timber-framed structural system and glazed façade,” the company says.
“Formerly an under-utilised external courtyard, the building’s new naturally ventilated toplit atrium creates a sense of openness and interconnectivity, promotes a sense of wellbeing and houses various indoor and outdoor gathering spaces that encourage interaction and the exchange of ideas.
“Our expansive, transparent design fosters a culture of collaboration and innovation among staff, students, alums, researchers, and industry partners. Internal spaces are designed at various scales for adaptable use over time, addressing the University’s evolving needs.”
TTW, which supplied Structural, Civil, Façade, and Construction Engineering expertise to the project says the Michael Kirby Building combines exemplar state-of-theart mass timber engineering and construction with adaptive re-use.
“The utilisation of lightweight and quick-to-construct mass timber was pivotal to project’s success,” TTW says.
A key constraint for the site, and its potential redevelopment, was the Epping to Chatswood rail corridor that runs directly below the building’s footprint. The impact on the rail corridor and the approval pathway with TfNSW was considered throughout all design stages of the project.
“We provided design input to assist studies into use, cost, and programme feasibility for complete demolition and re-build versus partial retention and addition for the building,” TTW says.
“From the studies, it was determined that the most feasible pathway forward would be an adaptive re-use methodology for the site. The existing concrete was retained to the first floor, with three levels of mass timber being constructed in its place, adding an extra storey on to the building and enclosing the central courtyard to form a new atrium.
“The lightweight nature of mass timber limited the strengthening extent required to the existing concrete structure, and a careful load-balancing exercise was undertaken to demonstrate that the larger building would not impact the existing rail corridor, therefore streamlining the approvals process.
“Our engineering design services spanned all phases of the project, from initial feasibility, and conceptualisation to construction. TTW’s specialist timber engineering team provided valuable input through full design and detailing of the timber structure to ensure that the showpiece of the building was efficient, quick to install, and met the architects’ and clients’ vision for a beautiful mass timber experience for the occupants.” ATM
Australia’s bushfire seasons have steadily worsened in recent years, a trend that has become increasingly concerning as climate change intensifies conditions.
Bushfires have long been a natural occurrence, but their scale, frequency, and unpredictability have grown, particularly during the summer months.
January remains a time when bushfire risk is at its peak, placing construction sites in bushfire-prone areas under immense pressure. These sites face the immediate risk of fire damage, alongside disruptions and delays caused by rapidly changing conditions.
The New South Wales Rural Fire Service (RFS) has struggled to meet its hazard reduction targets in recent years.
Due to above-average rainfall, only 40% of planned hazard reduction burns were completed ahead of the 2024 season, leaving many areas vulnerable. Research from CSIRO reinforces the urgency, showing that expanding communities are increasingly encroaching into bushfire-risk zones.
“With construction growing in high-risk areas, fire safety measures are more important than ever,” Leon Ward, Regional Lead
for PlanRadar Australia + New Zealand, said.
“Builders and developers must prioritise strategies to reduce fire risks, protect workers, and keep the public safe, minimising hazards during this critical time.”
Construction sites in bushfireprone zones face unique risks, exacerbated by fluctuating weather conditions, high winds, and extreme temperatures. These sites are particularly vulnerable because of:
• Unfinished or temporary structures increase the likelihood of fire damage.
• Tight project schedules can deprioritise fire prevention planning.
• The dynamic nature of bushfire risks requires quick and adaptive safety measures.
Embedding fire safety protocols at every stage—from planning to execution—is critical. Regular fire safety audits, compliance checks, and ongoing reviews of safety measures are non-negotiable for mitigating risks during this volatile season.
As bushfire risks escalate, digital tools are playing a critical role in improving fire safety management on construction sites.
“Partnerships between technology providers, like PlanRadar and the Fire Protection Association Australia (FPAA), can play a key role in improving fire safety on construction sites,” Mr Ward said.
“It’s a proactive approach to mitigating the escalating threats posed by bushfires, ensuring that fire safety is not an afterthought but an integral part of the project management lifecycle.”
• Real-time communication tools provide immediate updates on fire risks and safety protocols to all stakeholders.
• Compliance management features streamline fire safety audits and regulatory reporting, ensuring teams meet Australian standards.
• Remote site monitoring reduces the need for on-site personnel during high-risk periods, keeping teams informed while minimising exposure.
• Centralised documentation ensures critical fire safety records are always accessible for audits, risk assessments, and insurance purposes.
By embedding fire safety measures into every stage of a construction project, companies can:
• Protect workers and assets by reducing the risk of firerelated incidents.
• Minimise costly disruptions, delays, and damages caused by bushfires.
• Ensure compliance with bushfire safety regulations using efficient digital tracking tools.
Investing in fire safety early reduces long-term costs, lowers insurance liabilities, and improves site resilience against bushfire impacts/
As Australia faces longer and more intense bushfire seasons, the construction industry must take proactive measures to improve safety. By integrating technology such as fire safety management software, construction teams can stay prepared, protect their sites, and minimise project downtime.
“Construction companies need to adopt these strategies and technologies now to stay ahead of the growing climate threat,” Mr Ward said. “By taking action, they can protect their workforce, projects, and bottom line.”
Allam Property Group have always believed the foundation of a great home begins with the right materials. That’s why Allam have built with timber framing for over 30 years.
Since 1991 Allam Property Group have helped thousands of families across New South Wales and now Victoria build their dream home. Building in sought-after locations, using high quality building materials and providing inclusions and options to suit a wide range of lifestyles, Allam Property Group ensures a reliable and secure experience for their customers.
“Buying a new home can be life changing. It must be a positive, easy, and, above all, secure experience,” founder and Managing Director, Barney Allam OAM says.
“We’ve built Allam’s success on the solid foundations of open communication, reliability, and skill. We take our reputation seriously, so we need to ensure the materials we use reflect this. That’s why we build with Hyne Timber. We build with the good stuff.”
Allam Property Group have always believed the foundation of a great home begins with the right materials. That’s why Allam have built with timber framing from the very beginning. Mr Allam says, “Not only do our trades love working with timber, but our team can be confident a timber frame means a low maintenance home for their customers.”
Building with timber framing ensures all Allam homes are completed to a high standard due to the material’s ease of use and
preference among tradies.
“Timber’s lightweight and manageable nature make it easy to work with, allowing for straightforward drilling, notching, and shaping for builders and chippies,” says Mr Allam.
“Timber framing allows ease and precision when installing services so sparkies and plumbers are not only trained and familiar with timber framing but love to work with it.”
Handing over a home that’s low maintenance for their customers is paramount to the Allam team and providing homes built with a timber frame exceeds this. Timber is a naturally strong and robust material due to its stiffness and density withstanding some of the most extreme weather conditions. Plus, it won’t creak, squeak, ping or pop and it won’t rust or corrode over time.
Allam Property Group have seen firsthand how timber framing stands the test of time. Using timber framing as their material of choice since the beginning Allam know that timber faming offers a tried-and-true performance that their customers can trust.
When it comes to timber framing products, choosing Hyne’s T2 Blue treated pine framing is a no-brainer for the Allam team. The termite-resistant benefits, locally sourced quality pine, combined with a 25-year product guarantee, make it an obvious choice.
Knowing exactly where their building materials come from is crucial for the Allam team.
The best assurance Allam can get is knowing Hyne Timber
products are Australian grown and made, with a history spanning over 140 years. Using timber grown in our backyard means our team know it will handle Australia’s harsh climate, stay straight, and perform on the job.”
The CodeMark Australia treatment certification for T2 Blue provides an additional layer of confidence for their team and customers. “This independent, third-party check ensures the quality and reliability of our framing products.”
Supporting Australian made products is more than just a business choice for Allam; it’s a commitment to the thriving communities they build in. As a property group, Allam recognise their responsibility to uplift and support the local economies where they build. This means prioritising Australian made
products and partnering with local suppliers. By doing so, they are not only ensuring the quality and authenticity of materials they build with but also bolstering the businesses, families, and communities that form the backbone of those regions.
Knowing Hyne Timber have the kangaroo to go with every product further aligns with the Allam Property Group values.
All Allam homes have quality and comfort at the forefront of every decision made with the goal to provide consistency and quality time and time again, having a strong house frame made from Hyne timber sets the foundation for this.
To find out more about Allam Property Group and their 30 years of success in the Australian building industry visit allam.com.au
PHILIP HOPKINS
ON the first anniversary of the Victorian government’s closure of Gippsland’s native forest industry, France’s rebuilt historic Notre-Dame Cathedral has been completed in all its glory – and French native forest timber was at the heart of this historic project.
The oak hardwood timber used came from trees in French forests between 80-150 years old, with some more than 200 years old. The rebuilding of Notre-Dame received PEFC certification, the world’s largest forest certification standard, which certified the sustainability of the solid oak used to rebuild the cathedral’s roof structure. Oak is regarded as the queen of the French forest. PEFC, founded in 1999, is present in 56 countries.
Victoria’s hardwood native forest industry, and the native forest industry in Tasmania, New South Wales and Queensland, are certified to PEFC standard through Responsible Wood and the Australian Forestry Standard.
However, France’s achievement stands in contrast to Victoria, where the state government closed the native forest industry. The government claimed native forest harvesting was unsustainable, but critics point to other factors – poor native forest management, environmental hysteria, intellectual ignorance and naivete, and political malice.
The medieval frames of Notre Dame’s nave and choir, built in the 13th Century, and those of the spire designed by French architect Viollet-le-Duc, and both arms of the transept, dating from the 19th Century, were destroyed in the fire on April 15, 2019. They were restored identically, using the same techniques and materials as the original, solid oak.
The contracting authority for
the restoration project, ‘Rebatir Notre-Dame de Paris’, noted in a statement that by rebuilding NotreDame de Paris’ roof structure in wood, part of which - the great roof - is also known as “the forest”, the shared history of the cathedral and French forests would continue to be written for centuries to come.
“Like Notre-Dame de Paris, France’s forests are living symbols of our tangible and intangible cultural heritage, so it’s important to preserve them to ensure their longevity for future generations,” said the authority’s president, Philippe Jost.
The certification from PEFC and the FCBA Institute of Technology (Forêt Cellulose Bois-construction Ameublement) confirms the sustainable origin of the solid oak wood materials used, and the responsible nature of the work carried out by the contracting authority, chief architects of historic monuments and project managers.
The mission of the FCBA, founded in 1952, is to promote technical progress and contribute
to improving efficiency and quality assurance in industry. The institute’s scope covers the entire forestrywood and furniture sector: forestry, pulp and paper, logging, sawmills, carpentry, joinery, structures, woodbased panels, furniture, packaging and miscellaneous products.
The entire French forestry and timber industry mobilised to supply the wood needed to meet the specifications of the project. Actors from state-owned forests, community forests, forestry cooperatives, forestry experts, private owners and processing companies were all involved in ensuring that each stage of the reconstruction of the frameworks was carried out using a sustainable forest management approach, which is maintaining the balance between the economic, social and environmental dimensions of the forest.
This systemic approach enables the renewal of the forests from which the timber was sourced, thereby maintaining their multifunctionality, while preserving
diversity, vitality, productivity, and regeneration capacity.
According to PEFC, sustainably managed forest is a forest where biodiversity, soil health, water courses and wetlands are preserved. “It is healthy and able to renew itself, whilst providing a range of benefits including timber and timber products, carbon sequestration and opportunities for leisure activities.”
PEFC project certification stipulates that at least 70 per cent of the total volume of wood used is PEFC-certified. This ensures that PEFC’s forest certification requirements, which define and control a set of forest management rules applicable to all forest stakeholders (forest owners, forest managers, forest operators, forestry contractors), have been implemented.
Additionally, the implementation of PEFC chain of custody in project certification certifies that all parties involved in a construction or renovation project, whether certified companies or subcontractors,
have applied the control principles defined by PEFC, making it possible to track the flow of certified wood at every stage of the supply chain.
The Notre-Dame project involved 35 PEFC-certified sawmills, 175 PEFC-certified forests, and the use of over 80% PEFC-certified logs. PEFC’s rules for sustainable forest management and chain of custody enabled PEFC certification for the entire Notre-Dame de Paris timber reconstruction project.
The tree selection process began in early 2021. The chief architects from historic monuments aimed to find the straightest trees possible. This enabled restorers to work on logs measuring 7-20 metres, with diameters ranging from 50-110cm, while still having the strength required to support several hundred tonnes. The trees had to be between 80-150 years old, with some more than 200 years old.
The final trees were selected, but they had to be harvested in a way that respected the existing
area. For example, PEFC said the trees cut for Notre Dame had reached maturity and had already seeded the surrounding soil, enabling a new generation of trees to replace those harvested. Most of the selected oak trees came from either state-owned, communal or privately owned PEFC-certified forests.
The first trees were felled on 5 March 2021 and the final oak on 8 February 2023. Once harvested, the logs, each weighing 10-15 tonnes, were transported to their destination – sawmill, warehouse or processing site.
Sawmilling into structural sections took place between September 2021 and June 2022. In all, more than 2000 oak trees, the equivalent of 4000 cubic metres of logs, were needed to rebuild the spire and the framework of the choir and nave.
According to PEFC, these 2000 harvested trees made up less than 0.2% of the oak trees harvested annually in France. FCBA calculations show that France’s oak forests regenerate 1500 cubic metres of wood per hour.
The first phase of the project
began with the reconstruction of the spire and two transept arms designed by Viollet-le-Duc, using 19th Century techniques. The second phase of the choir and the nave involved rebuilding the medieval frameworks. This required mastery of traditional, medieval carpentry skills, including squaring – a technique for cutting beams with an axe, which follows the direction of the wood fibres and makes each piece unique.
On 11 July 2023, the first trusses – large, wooden triangular load-bearing beams 14m wide and 12m high and weighing more than seven tonnes and essential for the structure of the building - for the transepts were transported on an 80m-long barge along the Seine river to the foot of the construction site.
They were then lifted by crane high above the cathedral’s vaults to their final positions at the top of the cathedral. Reconstruction of all the roof structures was completed on 8 March 2024. More than 100 trusses make up the structure of the great roof – nave, choir and transept. All structural rebuilding work ended on 8 April 2024.
Christine de Neuville, President of PEFC France, said certification recognises the commitment of not only the client, Rebâtir Notre-Dame de Paris, but also of the entire forestry and timber industry to the long-term survival of the French forest.
Mr Jost said certification recognised the strong support of all the players in the forestry and timber industry: the ONF, France Bois Forêt and its members, the mayors of forest communities, private owners and their representatives, and sawmillers all over France, who donated trees and processed the timber.
“I extend my warmest thanks to them, as well as to the hewers, squarers and carpenters who have placed their expertise at the service of the cathedral’s rebirth, as part of an exemplary restoration project”, he said.
Official figures show that 3.8 million ha of the 17 million ha of French forest – 22% of the surface area - are oak. The total volume of standing oak is estimated at 615 million cubic metres, or 1.2 billion trees.
Ashley Young, the owner of Fortruss Frame & Truss, a leading timber prefabrication company in SE Queensland, recently made a strategic decision to enhance his production line by investing in Multinail’s PieceGiver Automated Timber feed system.
This case study explores the transformative impact of this innovative machinery on Fortruss’ operations, efficiency, and overall business competitiveness.
Driving Factors Behind the Investment
Ashley’s primary motivation for selecting the PieceGiver was to address inefficiencies in the production process. “I needed a way to keep the PieceMaker working more efficiently,” Ashley explained. “Our staff weren’t feeding it enough timber. The PieceGiver also reduced the number of staff needed in the cutting shed.”
Since integrating the PieceGiver, Fortruss has seen a remarkable improvement in production efficiency. “The cutting output has doubled,” Ashley noted. “Although I’m not a figures man, it has doubled the output we
had before. We’ve halved the staff numbers, and now the pressing shed can’t keep up with the saws. Currently, we can run the saws for four days a week and still keep up with the pressing shed.”
The PieceGiver has streamlined Fortruss’ workflow significantly. “With fewer staff, we are seeing about 20% more production,” Ashley said. “The machine doesn’t call in sick, reducing staffing issues. I love
that it’s always ready to work and doesn’t complain.”
The introduction of the bow flipper and stacking device has been particularly beneficial. “While it hasn’t necessarily increased production, the quality has improved,” Ashley remarked. These features have eliminated heavy manual processes, enhancing the work-life balance
for the team by reducing physical strain at the end of shifts.
Ashley couldn’t be more enthusiastic about PieceGiver. “The whole machine is bloody incredible! It’s all valuable, and I love it! Strong suction, double timber pickup, and lower staff requirements make it indispensable.”
Safety is the top priority at Fortruss Frame & Truss, and the PieceGiver has played a significant role in this area. “Although we didn’t have injuries from the old manual method, the risks were always there. Handling and manually feeding long pieces of timber is one reason the PieceMaker was slow without the PieceGiver; the operator was getting tired and slowing down during a shift. The PieceGiver reduces the OH&S risks and speeds up the PieceMaker,” explained Ashley.
While Ashley admits he isn’t a numbers man, the cost savings
are evident. “I don’t have any staffing issues in the cutting shed. There’s one wage saved on the saw, so that’s noticeable, and the results show that it’s fast and cheaper to run. I’m getting excited about the next evolution of the PieceGiver that has one PieceGiver feeding two PieceMaker’s because that’ll mean I have one man where there had been four in the past.”
The PieceGiver and PieceMaker have shifted the production bottleneck from the cutting shed to the pressing shed, enhancing Fortruss’ ability to meet deadlines and customer demands.
“This shift has significantly improved our planning and production capabilities.”
Support from Multinail Ashley couldn’t praise Multinail’s support enough: “Level 10! The support is everything I expect from Multinail. You can’t
hope for better. It sounds like I’m overegging the pudding, but my experience with the service of the MN machinery team has always been exceptional.”
Interestingly, Fortruss has encountered no significant challenges with the PieceGiver.
“It sounds strange, but there haven’t been any challenges with the PieceGiver at all. It’s been
an amazing experience.,” Ashley confirmed.
Overall, the PieceGiver has made Fortruss Frame & Truss more competitive by lowering costs, improving planning, and simplifying staff management.
“With fewer staff and less intensive work, we’re better able to plan because sawing is always available for the pressing teams.”
Fortruss’ experience with Multinail’s PieceGiver highlights the profound impact of advanced machinery on production efficiency, workplace safety, and business competitiveness in the timber prefabrication industry. This case study shows how innovative solutions can drive significant operational improvements and business growth.
ecoCORK insulation acoustic underlay is an innovative underlay material that offers a high-performance, eco-friendly alternative to rubber underlays. Made in Portugal. ecoCORK is THE environmentally sustainable choice. Biodegradable, renewable, and recyclable.
ecoCORK is more than just an underlay –it combines superior thermal and acoustic performance with numerous benefits that meet the diverse needs of residential and commercial projects:
Natural acoustic and thermal insulator
Extremely light for easy installation
Resistant to fire and termites
Excellent sound-absorbing qualities
Non toxic
Can be floated over sub-floors or adhered directly
This two-room cabin demonstrates the building potential of local timbers.
With parts constructed from four cypress species, eucalyptus flooring, poplar plywood ceiling linings and Douglas-fir roof framing, the Specialty Wood Species Cabin might look like a collection of disparate timbers, but it’s that way for a reason.
The cabin showcases what can be done with alternative timbers and without using chemicals. It came about following the seven year Specialty Wood Products Research Partnership (SWP).
The SWP investigated new wood products derived from specialty species. It aimed to increase the productivity and profitability of specialty species and develop a high value specialty wood products industry.
It focussed on the three New Zealand-grown, leading alternatives to radiata pine – Douglas-fir, cypresses and eucalypts.
The government and industryfunded SWP research project ran from 2015 to 2022 and included representatives from Forest Growers Research, Te Uru Rākau – New Zealand Forest Service, the Ministry for Primary Industries, Scion, New Zealand Farm Forestry Association, NZ Dryland Forests Innovation and University of Canterbury. Scion was a key research provider.
Vaughan Kearns of Ruapehu Sawmills had been heavily involved in the SWP project and when it finished, he wanted to find a way to showcase the thermally modified cypress created during the project.
The cabin itself aims to
challenge the durability of thermally modified cypress in a real-world environment rather than just the research environment where durability testing is ongoing.
“It was an opportunity to showcase the other products that came out of the SWP such as the eucalyptus laminated veneer lumber (LVL) and eucalyptus engineered flooring. On the back of that there was the opportunity to showcase the timbers that Ruapehu Sawmills produces such as some cypresses,” Kearns says.
The building was roughly half funded by Ruapehu Sawmills with contributions from SWP partners and the Industry Transformation Plan.
The cabin, roughly 5m by 3.5m is currently housed on Scion’s Rotorua campus for the public to view. Along with strategically
placed double-glazed windows, it is designed to be oriented to make the most of the sun’s natural light and heat.
The timbers used in construction were supplied from trees grown in New Zealand and the only treated timber used in the build is the skids in contact with the ground. The rest of the wood is either naturally durable or thermally modified (baked at high temperatures to remove sugars and increase durability and stability) showing you can build without added chemicals and still meet building code requirements.
Wood used in the build includes Grand fir, Douglasfir, Western red cedar, poplar plywood, Eucalyptus fastigata and Eucalyptus obliqua and four cypress species of macrocarpa, lusitanica, Cupressus x Nootkatensis and Chamaecyparis
lawsoniana (Lawson cypress).
Some of the cypress used was from a cypress hybrid trial established by Scion in 1997, meaning Scion has been able to track the trees from cuttings, through to finished products.
Scion’s work researching naturally durable or thermally modified wood is longstanding with recent research focussing on thermally modifying tōtara to enhance its durability enough for exterior building uses.
Senior technologist Rosie Sargent says it is great for people to be able to see the types of products that can be made from these species, and the cabin provides an opportunity to learn how these products perform in real life situations.
Trees to High Value Wood Products interim portfolio leader Elizabeth Dunningham says the cabin will provide useful data about product performance
as Scion staff make ongoing assessments.
The cabin is made up of a range of wood and wood products including Eucalyptus obliqua flooring and a thermally modified cypress feature wall.
“A wide range of collaborators contributed years of hard work and key technical know-how into the SWP, so it’s great the cabin is at Scion to showcase some of the products from that important collaboration.”
Marco Lausberg, Forest Growers Research’s SWP programme manager, says the cabin was a talking point when on display at last year’s FGR annual conference and there could be a growing market for these products.
“There’s a different consumer that is happy to pay more for less of an environmental impact. There is interest and demand for nontreated products.”
The SWP had a $14 million budget made of annual contributions of $710,000 from industry, $710,000 from MBIE and also had annual aligned funding of $550,000 from Scion.
It was driven by reducing sectoral risk, creating products for new markets and spurring regional development.
As a key research provider for the SWP partnership, Scion led the research into many of the products featured in the cabin. In some cases, research is ongoing, and the cabin will provide data about product performance in service over time as Scion staff make assessments of the cabin’s different components.
New data shows imported timber volumes increasing at the cost of Australian jobs and an urgent need for ‘country of origin’ timber labelling
It highlights the need for Australians to be better informed about where the timber they buy, comes from, according to Chief Executive Officer of the Australian Forest Products Association, Diana Hallam.
“Australians need and love their hardwood products and this new data shows that Aussies are increasingly getting them from overseas following the state based native forestry closures,” Ms Hallam said.
The Australian Bureau of Statistics (ABS) data shows the value of hardwood imports from Indonesia increased from around $35.5 million in 2015 to a peak of $218 million in 2020 at the height of the housing boom and still at $137 million in 2024, despite the housing slump, while imported value from Malaysia increased by two and a half times over the same period.
“Australians are still getting hardwood products, but they’re getting more from overseas and from places that don’t enforce the stringent environmental practices and regulations our industry operates to in Australia, highlighting the need for ‘country of origin’ labelling reform to inform consumers,” Ms Hallam said.
“This ABS data is further evidence that instead of supporting local and environmentally conscious industry that fights climate change and is the economic lifeblood of many regional areas, governments have chosen to replace our hardwood timber needs with imports that could be more environmentally damaging – and that many Australians aren’t properly informed about,” Ms Hallam said.
Atechnical challenge presented by New Zealand’s premium glulam manufacturer, Techlam, has led to an exciting partnership with Scion, fostering a unique international collaboration.
In response to Techlam’s request for expertise, Scion proposed an innovative solution: inviting Jean Margerie, a student from France’s prestigious engineering school École nationale supérieure d’Arts et Métiers (ENSAM), to join the project on a six-month joint internship.
Henri Baillères, Scion’s General Manager of Forests to Timber Products, explains that while Scion has long collaborated with the Levin-based company, this new partnership bridges industry and research, combining expertise and knowledge.
“When Techlam approached us for support, we saw an opportunity to meet their challenge with an innovative, mutually beneficial solution,” he says.
“For Techlam, it provided access to advanced equipment and research expertise that allowed them to expand their project scope and gain valuable insights into their processes. For Scion, this collaboration offered a direct link to industry, enabling us to apply our research in real-world settings and gain practical feedback to drive product innovation.”
After travelling over 20,000 km to New Zealand, Jean joined Scion in February 2024 to support Techlam’s efforts in improving quality control for glulam beams. He split his time between research at Scion and hands-on work at Techlam.
“Partnerships like this are central to Scion’s mandate and
strategic approach, fostering crosssector collaborations to advance forestry research, drive innovation, and promote sustainable forestry practices,” says Henri.
Since its establishment 30 years ago, Techlam has grown from a small operation to a 50+ person company, supplying radiata pine glulam beams across New Zealand, South Pacific, and globally.
Managing Director Brett Hamilton describes the partnership with Scion and ENSAM as “transformative.”
“Jean tackled our most pressing challenges and contributed to research and development, driving improvements in both product quality and innovation in glulam manufacturing,” he explains.
Brett highlights ENSAM’s status as a prestigious engineering institution known for producing high-calibre students. “The advanced, industry-focused training at ENSAM emphasises practical problem-solving and project leadership, not just theoretical knowledge. This approach has allowed Jean to apply his expertise directly to our
processes, achieving impressive results,” he says.
For Jean, the internship was the final piece in completing his studies in engineering.
He says his first impressions were overwhelming, but the support from Scion, Techlam, and ENSAM was the key to his success.
The internship had three distinct phases. First, a new testing device was implemented on the production line to measure a beam’s stiffness without damaging it, enhancing quality control. The second phase involved two months in Techlam’s factory focused on improving product consistency. Finally, back at Scion, research explored creating hybrid beams with exotic and carbon fibres, aiming for innovative beams compatible with Techlam’s existing processes. Although only a proof of concept was developed, it set the stage for future advancements.
Reflecting on the experience, Jean says it was a unique way to do an internship and a great way to shape his career.
“Working in both industry and research has been invaluable,
giving me insight into the challenges and opportunities in each field. This experience has shaped my perspective and strengthened my career path in engineering.”
Jean is not the first engineering student from ENSAM to intern at Scion, following in the footsteps of Scion Wood Process Engineer, Romain Meot. Joining Scion in 2023, Romain played a pivotal role in establishing this successful partnership, serving as Jean’s
mentor and a vital link between Scion and Techlam.
“The main advantage for students here is access to experts in many fields. They can reach out to specialists to solve technical problems, giving them wellrounded support.”
Techlam Quality Control Manager, Dave Hollows, who mentored Jean during his time with the company, notes the significant impact of Jean’s fresh perspective.
“Jean collaborated closely
with Techlam and Scion to drive the development of innovative, sustainable building materials, and his insights have brought immense value to our team. On a personal level, Jean reminded me to approach challenges thoughtfully, to question assumptions, and to look at problems through a more analytical lens.”
He says this shift in mindset has fundamentally changed the way we approach problem-solving across our operations.
“Having someone from the outside, like Jean, allowed us to step back and reconsider practices we’ve grown accustomed to. His questions often prompted us to think differently about things we’d taken for granted.
“In many ways, he mentored us by encouraging a broader view of situations we hadn’t fully examined before.”
While Jean’s internship concluded in August, he continued his work at Techlam as an employee for three additional months and is looking towards a new position starting next year, working alongside both Scion and Techlam.
This collaboration is a model Scion plans to replicate with other companies, furthering industry innovation and strengthening global connections. Henri notes the growing interest from highly skilled students at prestigious institutions in New Zealand and worldwide who are eager to join Scion for internships, bringing specialised expertise in engineering and problem-solving.
“For these students to make a real impact, we need more organisations to step forward and collaborate,” Henri said.
“Companies gain fresh solutions, elevate their projects, and benefit from these dynamic, solution-driven minds, ultimately helping to lift the industry standard.”
orest & Wood Products Australia has announced the signing of a new Statutory Funding Agreement with the Department of Agriculture, Fisheries and Forestry (DAFF) that will be in effect from 1 January 2025 to 2034.
As a Rural Research and Development Corporation (RDC), the FWPA’s Statutory Funding Agreement (SFA) represents the renewal of a 10-year contract between the Australian Government and FWPA.
The new contract is in response to changes in the levies legislation passed by Parliament.
The levy system represents a long-standing collaboration between the Australian Government and industry. It is designed to bolster productivity and competitiveness in international markets by imposing statutory levies on producers, processors, and exporters. These levies are collected with industry input and are crucial for funding initiatives that benefit the agricultural sector.
Australia’s rural R&D levy system is often regarded as a global benchmark for government and industry partnerships in agricultural innovation. It balances efficiency, inclusivity, and shared responsibility, driving improvements in productivity and sustainability while addressing industry-specific challenges.
This new agreement and modernisation of the levies will empower FWPA to further enhance the services it can deliver to its members and other levy payers, providing substantial benefits to our members and the wider industry.
“On behalf of FWPA, I would like to express our sincere gratitude to the Department of Agriculture, Fisheries and Forestry for their support and partnership, demonstrated by the renewal of our SFA,” FWPA Board Chair Craig Taylor said.
DAVID MCELVENNY
In the last article (NovemberDecember edition) I talked about the principles of writing in-house training and assessment materials, which raised the thorny problem of workplace literacy.
But before we move on to the topic of LLN (language, literacy and numeracy) difficulties and look at some of the strategies that trainers can use to reduce its negative impacts on learning, I’d like to take a big picture view of the problem and ask:
When did this age-old barrier to learning morph from just another challenge for workplace trainers into a ‘crisis’ that has since attracted billions of dollars in government funding, and turned the whole LLN juggernaut into a sub-industry in its own right?
The fact is that trainers, employers, and of course the workers themselves, have been dealing with this issue forever, long before government policy makers rode into town to fix it. And they’ll still be dealing with it, face-to-face and day-to-day, long after the cavalry ride off again, to the next big problem that needs
their attention.
So in this article, I’d like to explore the nature of the problem itself and try to put the whole issue back into perspective for trainers, whose job it is to deal with the full gamut of hurdles that are placed in front of them when they commence a training program with a new group of learners. Then in the next article we’ll look at some of the simple, well-proven techniques that trainers can use to overcome or work around the LLN difficulties that their students may have.
The more things change …
A good place to start with this journey is the 1991 policy paper written by John Dawkins (then education and training minister) called Australia’s Language: The Australian Language and Literacy Policy. He said in the Foreword:
‘About 1 million people in all, or up to 10% of the Australian population, do not possess effective English literacy skills, and this includes many who speak it as their first language. The literacy difficulties encountered by so many Australians have
not received sufficient public attention.’ (p.iii)
In the same year, the Workplace English Language and Literacy (WELL) Program was launched. In my opinion, this funding body did a lot of good work, and I was involved in various WELL-funded projects as an industry trainer and literacy specialist from the mid 1990s right up until it was disbanded in 2014.
Fast forward 20 years from the 1991 federal LLN policy to a report commissioned by the Industry Skills Councils in 2011 called: No more excuses: an industry response to the language, literacy and numeracy challenge. The executive summary said:
‘Literally millions of Australians have insufficient LLN skills to benefit fully from training or to participate effectively at work. The situation looks as if it could be getting worse, not better: the LLN performance of Australian students has, over the past decade, worsened in comparison to other OECD countries.’ (p.1).
The problem started to be
referred to as a ‘crisis’ by unions and agencies, and there was a renewed push to provide LLN funding for a wide range of industry programs. Training Packages were also redesigned, and the Industry Skills Councils started to build ‘Foundation Skills’ into units of competency. The purpose of identifying foundation skills was to explicitly address the underpinning abilities needed to learn effectively and work productively. They included LLN, plus digital skills (often abbreviated to LLND) and a range of general employability skills.
Fast forward another 12 years to 2023, when the results of the latest OECD Programme for International Student Assessment (PISA) were released in Australia. PISA assessments are carried out every three years with 15 year old school students in 81 different countries, and the results date back to when the program began in 2000.
The most recent assessment found that between 2000 and 2022, Australian students’ performance in literacy had fallen by 30 points, equivalent to a year and a half of schooling. In maths, Australian students’ performance fell by 37 points, equivalent to almost two years of schooling (PISA 2022: Reporting Australia’s results, Volume 1, Student performance and equity in education, 2023, Commonwealth of Australia).
Step forward one more year to October 2024, when AI Group published an industry survey titled: Counting the cost: Addressing the impact of low levels of literacy and numeracy in the workplace. The researchers found that:
‘… low levels of literacy and numeracy continue to have an
impact on both employees and employers in 2024, with 88% of companies affected by low levels of literacy and numeracy. Low levels of literacy and numeracy are having a more pronounced effect on productivity in the workplace than reported in the Centre’s survey in 2022.’ (p.3).
The report was timely, because in July 2024 the federal government launched the latest iteration of its Skills for Education and Employment program, with a budget of $436 million over the next four years.
What is going on, and why are industry trainers so ho-hum about it?
There is no doubt that LLND skills are becoming increasingly important in the timber industry as automated equipment and work processes continue to evolve. But the fact remains that our industry has always been characterised by a large cohort of workers who tend to have lower-than-average literacy skills, and there is no reason to believe that this will change in future. Despite the technological advancements, there are still many jobs where physical stamina and hands-on skills are more highly valued than generalised LLN abilities – so it’s natural that people who fit this profile will gravitate towards these jobs.
In my experience, employers have generally coped with their workers’ LLN limitations by adopting practical strategies that reduce the workers’ reliance on those attributes. The industry is full of expert operators who have excellent hand skills and mechanical aptitude, but relatively poor literacy skills. There are also many examples of supervisors, managers and sometimes even business owners who have come from the same cohort of workers who didn’t do particularly well at school and joined the workforce with lower-level LLN skills.
mail that’s just
It’s interesting to note that even among researchers there is no universal agreement on the extent to which lower-level literacy skills are actually a problem in the workplace. For example, at the height of the LLN ‘crisis’, following the release of the No more excuses report (referenced above), another study was undertaken called: Investigating the crisis: production workers’ literacy and numeracy practices (published in 2013 by the National Vocational Education and Training Research Program). Instead of administering diagnostic LLN tests to employees or looking at the issues statistically, the researchers took a different tack and asked the workers, supervisors and on-site trainers for their own opinions on what the underlying problems were. Viewed from this angle, the researchers said:
‘The real literacy and numeracy problems in manufacturing companies were seen not to reside with the workers, but in the way documentation was produced and
presented to the workers. (One) trainer noted that much of the workplace documentation could be simplified visually, making it easier for everyone. Job sheets, for example, were often complex and very poorly presented and unreadable, even to the trainer.’ (p.24)
Another case study found that when they looked more closely into the root cause of production mistakes in a company, 80% of the errors had originated in the sales department, and not on the factory floor. Ironically, when the LLN levels of the sales staff were assessed in a standardised test, their scores were found to be too high to qualify for remedial LLN training.
The report went on to lay much of the blame for the LLN crisis with the management and admin staff who were writing the documents that workers were having so much trouble understanding. Although this particular study was restricted to certain companies in the manufacturing industry, the same issues can be seen everywhere.
My own view is the creeping spread of ‘bureaucratise’ as an acceptable form of language, and the advent of copy-and-paste as a technique for creating new documents, are major contributing factors. Just look up any unit of competency to see what sort of mutant monster you get when you mix those two ingredients together in equal parts.
But let’s return to the workers and their immediate training needs, because that’s where trainers do have a direct influence over the way LLN difficulties are handled when workers are learning new skills. In the next article, I’ll look at the different types of LLN deficits and why they tend to occur, and then discuss some of the strategies that trainers have used for many years to work around these barriers and get the best possible outcomes for their students.
- David McElvenny is the CEO of Building Learning (www. buildinglearning.com. au) and Workspace Training (www. workspacetraining. com.au).
US real estate development company Neutral has secured $US133.3 million in construction financing for its development project, North America’s largest mass timber project The Edison, a 31-story mass timber, luxury apartment project in Milwaukee, Wisconsin.
Bank OZK provided senior financing, and Pearlmark delivered the mezzanine financing, with JLL Capital Markets working on behalf of Neutral to facilitate the transaction.
The Edison, located at 1005 North Edison Street in Milwaukee, WI., will total 308,913 residential rentable square feet and 378 residential market-rate units (studio, one-, two- and three-bedroom) as well as approximately 7,200 square feet of complementary retail space.
The project will feature bestin-class amenities focused on residents’ wellness, including a cafe, fitness center, spa, pool, sauna, demo kitchen, dog park, movie room, community garden, entertainment deck with kitchens,
and a top-floor sky lounge.
The Edison represents Neutral’s commitment to redefining conventional development with innovation in sustainability and well-being: At 31 stories, The Edison is on track to be the tallest mass timber building in North America and one of the tallest mass timber structures globally. The Edison blends exposed mass timber with abundant natural materials and state-of-the-art ventilation systems, creating an environment that nurtures both resident well-being and environmental sustainability.
The building’s materials are estimated to reduce embodied carbon footprint by 17% (without accounting for biogenic carbon) and 54% (with biogenic carbon), as well as reduce the operation carbon footprint and energy consumption by 45% compared to conventional buildings of the same typology and use. Edison will pursue Passive House certification from PHIUS 2021 Core Standard, one of the leading and strictest certifications for energy-efficient
buildings. The Edison will also pursue Living Building Challenge 4.0. Core Certification, focused on regenerative buildings and overall resident well-being.
The Neutral development team is led by CEO Nate Helbach, CPO Daniel Glaessl and CTO Matt Frazer.
“We’re grateful to partner with Bank OZK and Pearlmark and for JLL Capital Markets’ leadership in facilitating this milestone financing. Successfully securing funding in today’s challenging financial market environment underscores the strength of the project’s fundamentals and our exceptional project team,” said Helbach.
“With The Edison, we’re demonstrating that innovation in sustainable high-rise construction is both technologically and financially feasible. Edison will pursue some of the strictest sustainability standards, like passive house certification, by PHIUS 2021. We are also implementing design guidelines of LBC 4.0 Core Certification that focuses on the overall well-being
and happiness of the people who will live and work in The Edison,” said Glaessl.
The Pearlmark team was led by Managing Director Mark Witt.
“We are excited to be involved in the financing of this project with Neutral, a repeat sponsor of the firm. This project has a great location on the Milwaukee River and steps away from the Deer District, with its numerous entertainment and food options,” said Witt.
The JLL Capital Markets team representing the borrower was led by Director Mike Brady, Associate Tara Hagerty and Analyst Merrick Evans.
“We are thrilled to be a part of this team to not only add a unique luxury living option to Milwaukee but also advance mass timber developments. We believe this project will set a new standard for elevated living.” said Brady.
Project construction is expected to start in the first quarter of 2025 and is expected to be complete in the second quarter of 2027, Neutral officials said.
The debate on the “right” materials to use when building homes in bushfireprone areas often sparks fierce opinions and misguided claims.
While some advocate for alternative materials, timber framing remains a viable, safe, reliable and effective option when designed and built in accordance with modern practices. It’s time to set the record straight and address some of the myths that have driven unnecessary fear about building with timber.
One common misconception is that timber frames ignite easily and pose a higher risk of destruction in bushfires compared to steel. However, this oversimplified view ignores the science. Timber-framed houses built in bushfire-prone areas must be designed and constructed in accordance with the Australian Standard AS 3959 Construction of buildings in bushfire-prone areas. AS 3959 provides solutions for timber-framed houses from lower bushfire threats through to an extreme threat referred to as Flame Zone. AS 3959 makes no distinction between using a timber-framed or steel-framed building!
However, from a basic material science perspective, timber, unlike steel, does not lose its structural integrity at lower temperatures. Steel, on the other hand, begins to lose strength and can melt or buckle well before reaching the extreme heat generated by a bushfire. This was seen during the 2009 Black Saturday fires in Victoria and countless other events—steel was no more invincible than timber, and many steel homes suffered the same fate in the face of ferocious flames.
KERSTEN GENTLE Executive Officer FTMA Australia
Another important factor is the role of the surrounding environment. Studies and expert analysis repeatedly confirm that the fuel load around a property— the dry vegetation, debris, and landscape management—is a significant determinant of whether a home survives a bushfire. Building materials alone do not dictate safety. A home surrounded by cleared defensible space and properly managed vegetation is far more likely to survive than a steel-framed house that is overgrown with combustible plants. It’s time we stopped stigmatising timber and started focusing on smarter overall designs and landscape strategies.
What’s more, guidelines for building in bushfire-prone areas— such as using ember guards, managed building sites, and strategic design methodologies— are applicable to all construction types. Timber homes, when constructed to meet the AS 3959 Bushfire Attack Level (BAL) requirements, are every bit as capable as steel or other materials at resisting a bushfire. Claims to the contrary often originate from industries with vested interests, perpetuating myths for commercial gain.
The growing intensity and frequency of fires globally can no longer be ignored, and climate change is a significant driving factor behind this alarming trend. By continuing to rely heavily on
materials like steel and concrete, which are produced through energy-intensive processes that emit vast amounts of carbon dioxide, we are exacerbating the very crisis that fuels these catastrophic bushfires.
Conversely, timber offers a sustainable alternative that actively combats climate change by storing carbon throughout its lifecycle. Utilising timber for construction not only reduces our carbon footprint but also aligns with long-term climate action goals. By choosing timber, we are not just building safer, smarter homes in bushfire-prone areas— we are investing in a solution that mitigates the climate crisis and the rising severity of bushfire events it continues to create.
The reality is that no building material, steel included, can stand up to the full force of a catastrophic bushfire fuelled by high winds, extreme temperatures, and towering flames. The Santa Ana winds in California or the blazing infernos wrought by Australia’s Black Summer are clear demonstrations that environmental factors outweigh material choice in the scale of destruction. It is building design, adherence to bushfire construction standards, and proactive land management that provide real solutions—not uninformed material bias.
Timber-framed homes have a place in bushfire-prone areas, and their use should not automatically raise alarm bells. What matters is how we design and build them, as well as how we manage surrounding vegetation and community preparedness. Blanket statements dismissing timber are both scientifically inaccurate and counterproductive. The focus
must be on promoting practical, evidence-based strategies instead of politicised fearmongering about building materials.
The way forward for communities in bushfire-prone areas should be based on thoughtful planning, sustainable practices, and respect for firesmart guidelines. Timber is not the enemy; mismanagement, reckless land practices, and misinformation are. It’s time to embrace timber as part of the solution to combat climate change—not unfairly condemn it as part of the problem.
If an employee is a regular no-show at work, you need to address the issue. What’s the best way to handle chronic takers of sick leave?
Let’s make it clear at the outset – sick leave is not there to be used whenever someone feels like a day off. It is available when employees are unfit to attend work because of illness or injury.
Yet many employees believe it’s their right and that they can take this time off at any stage during the course of their employment, much like annual leave.
WHAT YOUR EMPLOYEES SIGNED UP FOR
Underpinning every employee relationship you have is a commitment, written or verbal, given by an employee to attend work as agreed and to perform duties to the best of their ability and in the best interest of you, their employer.
WHAT INFORMATION DO YOU NEED FROM A SICK EMPLOYEE?
As an employer or manager, you need to ensure you manage your business efficiently. At the same time, you need to be able to discharge your legal and safety obligations effectively. To do this you must have full and correct
Brian Beecroft CEO, TTIA
information about an employee’s illness and limitations for work. You will get this information in a medical certificate. Your employees should provide you with a medical certificate as evidence of illness of more than two consecutive days.
A medical certificate is documentary proof of illness from a registered medical practitioner stating that the employee will be/ was unfit for work. It is generally regarded as proof an employee was legitimately absent from work because of the stated illness or injury.
(Note that without a certificate, an employee is not entitled to personal leave or compassionate leave.)
Sections 97 and 107 of The Fair Work Act 2009 provide that
if an employer requires it, an employee must provide evidence that would satisfy a reasonable person that sick leave is taken because the employee is not fit for work because of a personal illness or a personal injury.
An employee’s entitlement to take sick leave is contingent on them complying with the evidence requirements (vii). What constitutes “reasonable evidence” depends on the circumstances, however, a medical certificate or a statutory declaration should be accepted as appropriate evidence.
• Ask questions. Do all that is reasonably practicable to ask and inform yourself about an employee’s absence to ensure that there are no work, health and safety issues. Be aware not to cross any discrimination laws when doing this e.g. Section 30 of Disability Discrimination Act 1992 (Cth).
• Engage with the ill or injured person early and regularly, without them considering you are harassing them.
• Discourage someone from coming to work if they have a transmittable virus such as COVID-19 or the flu.
• Discuss their fitness and
what work they can safely do. This may involve liaising with their doctor or occupational therapist.
• Discuss what you can do, or provide them with, in the way of resources or counselling to help them to return to a safe workplace. You are aiming for their timely, functional, and safe return to the workplace.
• Ensure that employees know and understand your workplace policy on absence.
• Consider implementing a wellness program to combat sickness.
• Identify and monitor unsupported absences, particularly where there is a trend and develop and have procedures in place for unacceptable absences.
• Equip the workplace with a range of hygiene products that can be used to prevent transmission of COVID-19, cold and flu. These include tissues, soap, paper towels and disinfectant gels and wipes.
TTIA can help you to manage and put systems in place regarding absenteeism. Contact our National Industry Hotline on (02) 9264 0011 or email ttia@ttia. asn.au
The 2024 year was a busy one, starting at Oberon, NSW where members got to peek behind the curtain, seeing how MDF is produced at Australian Panels. It was great to see the efforts made to repurpose and recycle offcuts and waste material, a highly educational tour to start the year.
Moving on to Adelaide midyear, local members hosted an assembly of industry knowhow, delving into the ever-changing coating industry which is a close cousin of timber veneer, being the final piece in the puzzle for consumers of our fantastic product.
In mid-November 2024 the Timber Veneer Association of Australia travelled to Western Australia for the first time in more than a decade, to visit long term member World Wide Timber Traders. Over a dozen members made the journey west, combining the Association’s AGM with a site visit.
PETER LLEWELLYN Technical representative, Timber Veneer Association of Australia
Various topics were discussed at the AGM, covering subjects that challenge our members and businesses alike day to day. The battle against staining of Eucalyptus species appears to be coming to a head with research into the issue performed by UTAS. A collaboration with members across various industries offers some insight into the problem on a chemical level and, more importantly, through best practice disciplines.
TVAA is now one step closer to solving this long-standing issue, leading the veneer industry through research and working with fellow TVAA members in the coating space to assist with solutions on a
commercial scale.
Our gracious hosts in Western Australia, World Wide Timber Traders, took the opportunity to showcase their manufacturing abilities to the TVAA visitors, from veneer cutting and joining to panel pressing. Members who may not have appreciated the scale of the business gained insights and manufacturing tips, all with the goal of keeping timber veneer front of mind and produced to the highest standards. We thank World Wide Timber Traders for their time and hospitality.
The past year has been an interesting time for the veneer industry with a “changing of the guard” occurring in the membership. With businesses being sold and powerhouses of the veneer industry in Briggs Veneer and Timberwood Panels changing hands, a new wave of members eager to get involved has been welcomed by the TVAA.
We recognise loyal supporters such as Juel Briggs and Gray Parsonson for their unwavering commitment to the industry and involvement in the Association over the years.
A special thanks to Frank Luiz of Briggs Veneers for his commitment to the TVAA, his insight and attention to detail in the TVAA’s Treasurer’s position.
With the formalities of the AGM completed for another year we welcome our new committee, poised to advocate for our beautiful natural resource in timber veneer and ready to face the challenges that business brings in this day and age.
2022
Norske Skog Australasia managing director Andrew Leighton has been appointed Forest and Wood Products Australia’s new Chief Executive Officer.
He replaces Ric Sinclair who retired as managing director late last year after 13 years in the role.
Mr Leighton has spent seven years as managing director of Norske Skog Australasia, time as Vice-Chair of the Australian Forest Products Association and a diversity of other positions that relate to the many areas in which FWPA is active.
2019
The first sod has been turned ahead of construction of Hyne Timber’s new Glue Laminated Timber (GLT) production plant. Hyne Timber’s CEO Jon Kleinschmidt said the new building would be constructed using the company’s own products,
“The new building will be constructed using our own GLT, manufactured at our existing plant in Maryborough to further showcase capability and over 40 years of GLT manufacturing experience,” he said.
“Further, Hyne Timber remains committed to using Queensland products and services throughout delivery of this construction project with a priority on Fraser Coast businesses where possible,” said Mr Kleinschmidt.
Australian Paper has released its 2012 Sustainability Report documenting its environmental, economic and social performance across its six domestic business units.
In 2012, Australian Paper saw reduced domestic sales volumes as a result of a weak economy, a strong Australian dollar and an influx of competition from imports which negatively impacted sales revenues and profits.
“Foreseeing these market conditions, Australian Paper continued to improve its sustainability to ensure that we are here for the long term. We have turned challenges into opportunities and are proudly taking bold business initiatives so that we can adapt and find better ways to operate in the face of difficult market conditions,” said Chief Executive Jim Henneberry.
Australian door manufacture Specialty Doors has launched two new product-based businesses Specialty Commercial and Specialty Acoustics. Specialty Commercial is focused on timber profiling and custom componentry, while Specialty Acoustics offers a range of acoustic products.
Director Marcus Bastiaan said the new product businesses were an answer to sustained enquiry and a chance to expand The Specialty Groups product range.
“The new companies give us the chance to broaden our existing product range. We have found a growing demand from existing customers for
quality timber componentry and a renewed focus on acoustic performance from the Australian and New Zealand building industries,” Mr Bastiaan said.
Specialty Commercial is focused on production and supply to primarily the Queensland and New South Wales market. The company is currently operating from Brisbane and supplies resellers to order. Mr Bastiaan said the company would embark on an instore range of timber componentry products in the New Year.
“This is the first time we have offered resellers stock lines. First to market will be a range of entry door handles made from recycled
Australian Hardwoods,” he said.
The company’s focus on sustainable sourced and recycled timber has been an opportunity to showcase Australia’s world class forestry standards.
Mr Bastiaan believes the construction industry should be championing native forestry products, and that it’s up to manufacturers like Specialty Commercial to offer products that compete with imported species.
“We have the best hardwood in our backyard, and we intend to showcase more of it. Too often when it comes to componentry the building industry gets pigeonholed into using imported species like Pine, Beech and
American Oak. Our new range is price competitive and made from Australian timbers like Blackbutt, Tasmanian Oak and Spotted Gum,” he said.
Specialty Acoustics has an entirely different mission. The company is focused on providing quality acoustic products to meet growing demand in the construction industry. Through a technical and installation partnership with Acoustic Doors Australia the companies provide specification, manufacturer and installation services.
Mr Bastiaan said the business will give builders the technical and onsite support they need.
“Acoustic products are highly engineered and require careful installation. The new company’s product and service offering gives site managers peace of mind and offers accountability to commercial construction companies,” he said.
Specialty Commercial and Specialty Acoustics officially launched on Australia Day 2025. Alongside Specialty Doors, the three businesses sit within The Specialty Group.