
3 minute read
El giro verde que nos conviene a todos
from Fluidos nº 459
by Publica SL
DLM presenta sistemas de protección de roscas para los sectores hidráulico, neumático y de automoción.
Riccardo Ampollini Ermanno Pedrotti
La economía circular suele verse como un sector en el que hay mucha teoría y poca sustancia, y su implantación se considera agotadora y poco ventajosa. Un encuentro con Lisa y Mauro Montanari -segunda generación al frente de DLM, una pyme lombarda que fabrica tapones protectores de material reciclado- nos mostró que el escenario es justamente el inverso.
Después de haber fundado DLM en 1987 que, por aquel entonces, fabricaba codos hidráulicos, Antonio Montanari se hizo cargo del negocio de un anciano moldeador de artículos de polímeros plásticos que, al no tener herederos, le transmitió sus conocimientos. Gracias a esa integración de técnicas, el padre de Lisa y Mauro comenzó a fabricar los primeros moldes para tapones de polímero plástico que utilizaba para proteger las roscas de sus curvas hidráulicas.
Retrato robot de una pyme italiana con proyección en el mercado mundial
Hoy DLM solo fabrica caperuzas protectoras, y si el 55% de su producción se va ya de entrada al extranjero, buena parte del resto vendido en Italia también se exporta. Es una tendencia validada por Federtec, que en su informe final 2021 comunicaba que más del 60% de la producción nacional de componentes para fluidos, transmisión de potencia, control y automatización inteligente traspasa las fronteras nacionales, realizando un aporte significativo a la balanza comercial del sector.
“Para responder a las necesidades cada vez más globales de los clientes, contamos con un centro logístico de 3.000 m2 activo las 24 horas del día, los 365 días del año”, explica Lisa. “La misma lógica existe las 24 horas del día para la identificación de las tapas protectoras. Aquí la web es la interfaz con el cliente que accede a ella en tres pasos:
1) visualización de las categorías de productos: tapones, protecciones de bridas, tapones para pintar, etc.;
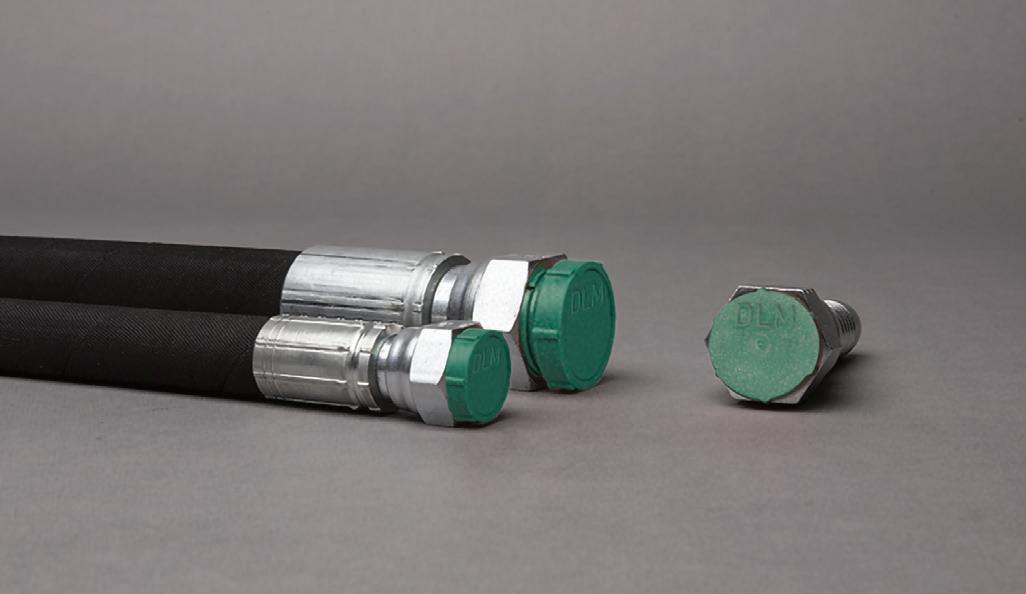
2) accediendo a las fichas técnicas y/o solicitando muestras;

3) enviando a DLM solicitudes de ofertas.
Si luego se necesita un producto a medida, se activa la oficina técnica que, en concierto con el taller de herramientas, crea proyectos y soluciones ad hoc”.
Significado de la certificación
‘Plastic Second Life’ emitida por IPPR
Fundado en Milán en 2004 como una entidad independiente para dar visibilidad a los fabricantes y distribuidores de plásticos reciclados, el IPPR (Instituto para la Promoción de Plásticos Reciclados) ha otorgado a DLM la marca “Plastic Second Life” (PSV) a través del Certificado No. 2140/2022 para la línea de capuchones Green Line que se expondrá en la feria de Hannover en Alemania del 17 al 21 de abril de este año.


“Este certificado nos autoriza a colocar la marca PSV/MixEco no. 5631 vigente hasta el 5 de septiembre de 2025”, dice Mauro recordando que el giro verde nació en conjunto con el relevo generacional que involucró no solo acciones y/o roles, sino también know-how y valores corporativos hasta la revisión verde de los sistemas y el catálogo de la firma.
Mientras tanto, la ‘revisión de la planta’ se ha concretado en la puesta en marcha de 25 nuevas prensas de inyección híbridas que, en su conjunto, han permitido a DLM un ahorro del 30% en el consumo de kWh por kg de material/producto procesado. Luego se reemplazaron los refrigeradores y compresores por equipos de última generación y, por último pero no menos importante, se instalaron paneles solares de 300 kWp que, hoy, contribuyen al 35% de las necesidades de energía de la compañía.
“Antes de estas intervenciones, el consumo eléctrico anual era de 3,17 kWh/kg, mientras que estamos por los 1,99 kWh/kg”, precisó el copropietario de la empresa lombarda.
La ‘revisión del catálogo’ sancionó la transición de los materiales vírgenes a los de ‘segunda vida’, con nada menos que 18 meses de pruebas que llevaron a los tecnólogos de DLM tanto a entender cómo y dónde hacer el mejor uso de los nuevos recursos como a establecer que ni los biodegradables ni los bioplásticos cumplían plenamente con las expectativas, ya que:
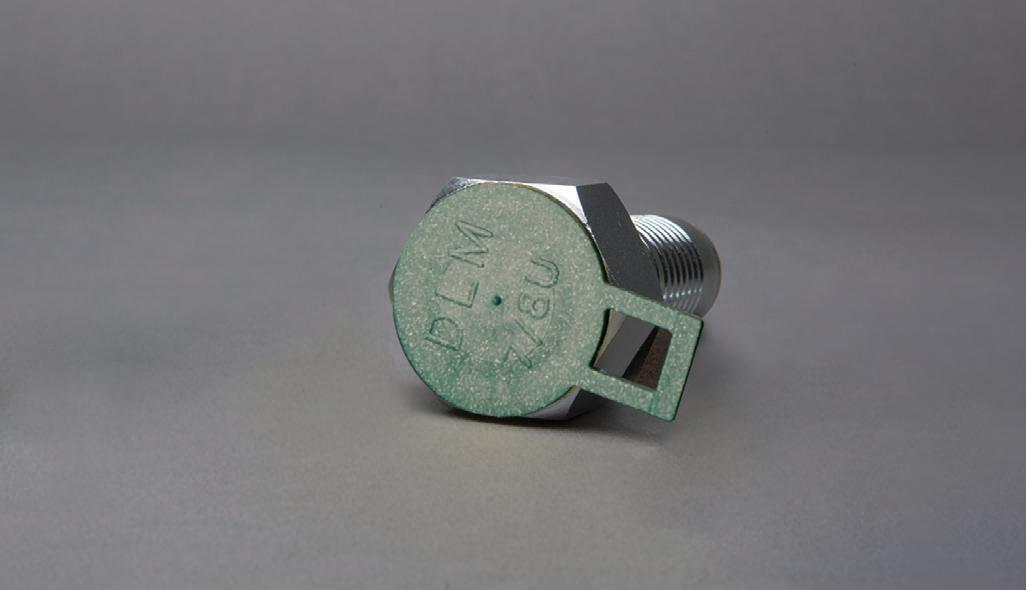
• al final de su vida, los materiales biodegradables requieren trasladarlos a plantas de compostaje o vertederos, interrumpiendo el virtuosismo de la circularidad;
• los bioplásticos no están disponibles en grandes cantidades.
Y la guinda del pastel...
DLM lleva tiempo trabajando en un proyecto de economía de cuatro años (2021-2024): “Es un plan centrado tanto en los moldes de inyección de colada caliente para no generar mazarotas, como en los mezcladores capaces de dar color a las piezas en planta”, concluye Mauro Montanari. Hasta la fecha, los moldes representan un ahorro anual de desperdicio de 12.170 kg y una reducción de emisiones de CO2 de 18.680 kg, y las mezcladoras reducen los residuos de preparación de material en 4.500 kg, con una reducción de CO2 de 6.920 kg”.
“En todos los niveles de la organización existe la conciencia de que reducir el impacto ambiental es un compromiso con las familias, los niños y las generaciones futuras”, comenta el fundador, sin ocultar cómo sus compañeros más comprometidos con los objetivos de la empresa son el verdadero motor de esta fantástica transición.
www.dlmtappi.com