
5 minute read
Una Opinión de Hoy
Avances tecnológicos en procesos industriales cerámicos
La sostenibilidad, la reducción del impacto ambiental y la minimización de los costes energéticos son en estos momentos tres prioridades para la industria azulejera. Dentro de esta coyuntura, alimentada por las exigencias derivadas de la Agenda 2030 de la Unión Europea, buena parte de los esfuerzos del sector se centran en desarrollar nuevos avances tecnológicos alineados con estos objetivos.
Dr. Juan Miguel Tíscar, responsable de la Unidad de Simulación y Modelización de Procesos en el Instituto de Tecnología Cerámica - ITC
Dentro de esta tendencia, actualmente me encuentro inmerso en el desarrollo de un horno eléctrico para la cocción de baldosas cerámicas. Hasta la fecha, la mayoría de los hornos eléctricos existentes en el sector cerámico corresponden a hornos de laboratorio y pequeños prototipos semicontinuos, que no suelen utilizarse para la fabricación de baldosas cerámicas a gran escala.
El coste de la electricidad con respecto el coste del gas ha retrasado el desarrollo de estos equipos durante años, aunque ahora, la presión de Europa con respecto a las emisiones de CO2 y el incremento del coste del gas natural está impulsando el desarrollo de hornos industriales eléctricos para la cocción de baldosas.
Dentro del Instituto de Tecnología Cerámica me encargo del desarrollo de modelos matemáticos y, en este ámbito, implementamos en C++ un modelo para predecir la respuesta térmica de las baldosas expuestas a un flujo de calor radiante proveniente de resistencias eléctricas. Nuestro propósito es determinar la mejor disposición de las resistencias para maximizar la transferencia de calor a las baldosas, minimizando pérdidas. Para
ello también hemos desarrollado un optimizador multiparamétrico que se encarga de darnos las mejores soluciones y así determinar: la potencia de las resistencias, la distancia entre ellas y la altura de éstas con respecto las baldosas.
Todo este trabajo se podría realizar, evidentemente, mediante experimentación y diseño de experimentos. Sin embargo, desde ITC-AICE sostenemos que, gracias a la simulación, se consigue reducir de forma significativa la cantidad de ensayos experimentales para el diseño de equipos, además de incrementarse las posibilidades de éxito de los proyectos en los que trabajamos.
En la imagen de la derecha se observa una baldosa sometida a un ciclo térmico. En un instante puntual, se visualiza la distribución de temperaturas en la superficie de la baldosa debido al efecto de la resistencia que tiene encima (barra negra), la cual está ligeramente desplazada a la izquierda. Nuestro objetivo es posicionar correctamente todas las resistencias para que la baldosa sea sometida al ciclo térmico adecuado minimizando el coste energético requerido.
❖ Simulador de material en polvo
Las propiedades de las baldosas cerámicas vienen determinadas por la microestructura del material que, a su vez, depende de la naturaleza de las materias primas empleadas, así como de las distintas etapas que integran su proceso de fabricación. A través de estas etapas interconectadas, la mezcla inicial de materias primas experimenta una serie de transformaciones fisicoquímicas de forma progresiva, generándose diversos productos intermedios para, finalmente, dar lugar al producto final.
Esta mezcla de materias primas se somete a operaciones de molturación para garantizar una mezcla homogénea de sus componentes, con una distribución de tamaños de partícula adecuada, y debidamente acondicionada para el moldeo de la pieza. La molturación puede realizarse por vía seca o húmeda, siendo necesario en este último caso secar la suspensión resultante mediante atomización. Este es un proceso continuo y automático que permite obtener una serie de gránulos de material (polvo atomizado), con un contenido en humedad determinado y una forma y tamaño idóneos para que fluyan en la siguiente etapa del proceso cerámico: el conformado.
Durante el conformado, el polvo atomizado se vierte en un molde mediante un sistema de transporte para, seguidamente compactarlo y obtener la forma de la baldosa. En el moldeo de piezas planas, debido a su geometría sencilla y a la pequeña relación espesor/superficie, se realiza un prensado unidireccional en seco empleando, generalmente, prensas hidráulicas. De esta forma, se obtienen las baldosas en crudo que son trasladadas a un horno en el que tendrá lugar la etapa de cocción a alta temperatura. A pesar de los importantes avances en los sistemas de prensado y en la tecnología de los hornos, curiosamente, la primera etapa de llenado del molde no ha experimentado apenas avances en las últimas décadas.
En la actualidad, la precisión de esta etapa sigue dependiendo de la experiencia e intuición del operario, siendo esto especialmente relevante cuando se trata de fabricar baldosas de gran formato (mayores de 120×120 cm). Independientemente del mayor o menor grado de destreza del operario, este es un procedimiento que sigue siendo muy propenso a generar defectos en las baldosas debido a una ineficaz distribución del polvo en el molde. Así, según mi criterio, sigue faltando un enfoque científico y sistemático para mejorar esta etapa.
El método de los elementos discretos (DEM) simula numéricamente el comportamiento reológico de un medio formado por un conjunto de partículas, las cuales interaccionan entre sí a través de sus puntos de contacto. Por consiguiente, representa una metodología adecuada para el estudio de materiales granulares y discontinuos. Esta metodología se ha utilizado en el análisis del flujo de polvos durante la descarga de silos, la simulación de ensayos de compresión o en la mezcla y el transporte de polvos, entre otros.
Con esto, las simulaciones DEM suponen un enfoque computacional para comprender y optimizar el proceso de llenado de moldes que se emplean actualmente en la fabricación de las baldosas cerámicas. De esta manera es posible analizar cómo se generan los defectos durante el conformado de baldosas cerámicas, así como proponer estrategias para su prevención.
Con esta premisa se desarrolló, con la empresa Macer, un software de simulación de materiales granulares mediante el DEM, especialmente diseñado para resolver la problemática asociada al proceso de llenado de moldes en la fabricación de baldosas cerámicas. El éxito del software impulsó el desarrollo de una herramienta de simulación de polvo más generalista, denominada ScaleDEM, y desarrollada por ITCAICE junto con la Universidad de Gante. Se trata de un software modular de simulación de materiales granulares en entornos industriales, que proporciona una mejor comprensión de los equipos de manipulación de polvo, así como la creación de prototipos virtuales. ◆
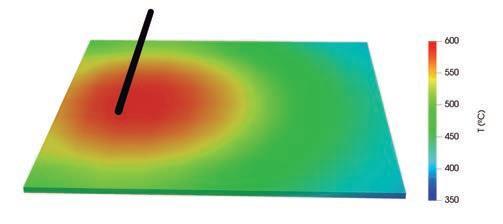