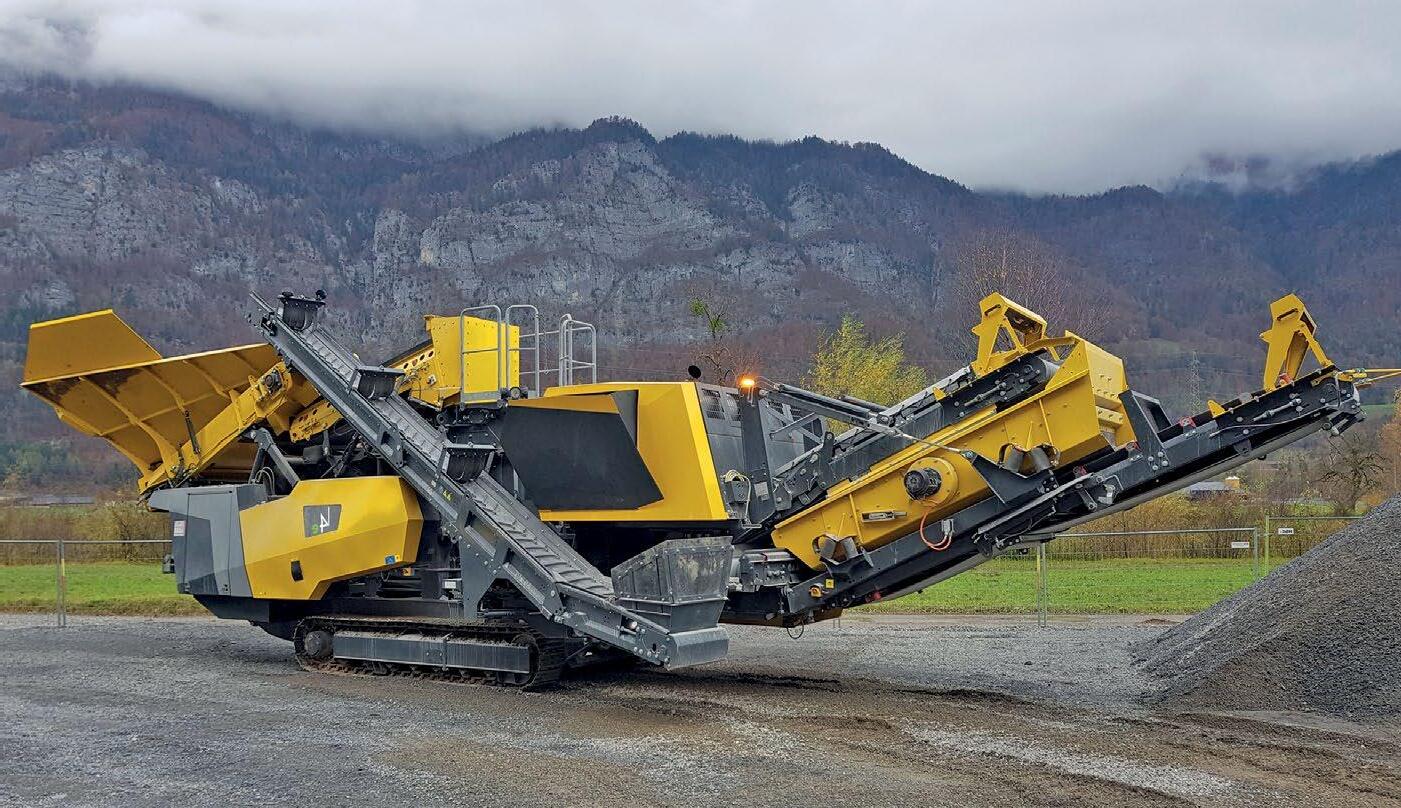
3 minute read
CRUSHER ELECTRIFICATION GATHERING PACE
That electromobility is a notable trend in the mobile crushing industry is no overstatement. Speaking to Quarrying Africa, Marcel Kerkhofs, marketing manager at Keestrack, says all forms of crushers – jaw, cone and impact – big or small, are now available with full electric plug-in. By Munesu Shoko.
As the industry seeks to simultaneously drive efficiencies and reduce its carbon footprint, the move towards electric crushers is in full force. One of the manufacturers at the forefront of the electric revolution is Keestrack, which has already brought to market an extensive range of commercial units.
Advertisement
“The main driver behind the electrification trend is sustainability – the need to reduce carbon (CO 2 ) emissions. We all want to contribute to the creation of a better and healthier world without having to compromise on quality and efficiency,” says Kerkhofs.
Leading from the front Keestrack first ventured into the electric game in 2012 with the introduction of its e-drive – an electric plug-in with an onboard gen-set for operating environments which has no mains power available on site.
“The e-drive machines invigorated the mobile crushing sector with a drop-off gen-set which could power several crushers, screens and stackers, in the case of no electric connection being available. This way the total production train is driven by only one engine, resulting in reduced fuel, maintenance and operational costs,” he says.
In recent years, Keestrack has introduced its ZERO-drive machines, a 100% electric
100%
In recent years, Keestrack has introduced its ZERO-drive machines, a 100% electric offering
40%
Compared offering. In this range, electric motors drive most of the equipment and power some necessary hydraulics systems.
A wide range of Keestrack equipment –namely the H6e and H7e cone crushers, all impact crushers, all scalper screens (except the K8), C6e classifier, all stackers, all jaw crushers (except the B3) and the A6 tracked apron feeder – are available in ZERO-drive.
“At this point electric drive systems are the greenest and most cost-effective options on the market, as they are more efficient than conventional hydraulic systems. They enable the end-user to be less dependent on a specific engine supplier. If there is no electric plug-in available, end-users can choose their own gen set or select one of the Keestrack (tracked) engine/gen-set units,” says Kerkhofs. Compared to conventional diesel-hydraulic
KEY TAKEAWAYS
As the industry seeks to simultaneously drive efficiencies and reduce its carbon footprint, the electrification of mobile crushers is gathering pace
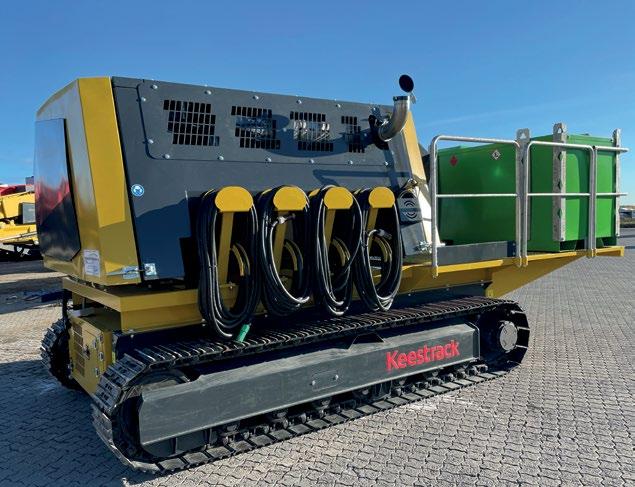
The main driver behind the electrification trend is sustainability – the need to reduce carbon emissions
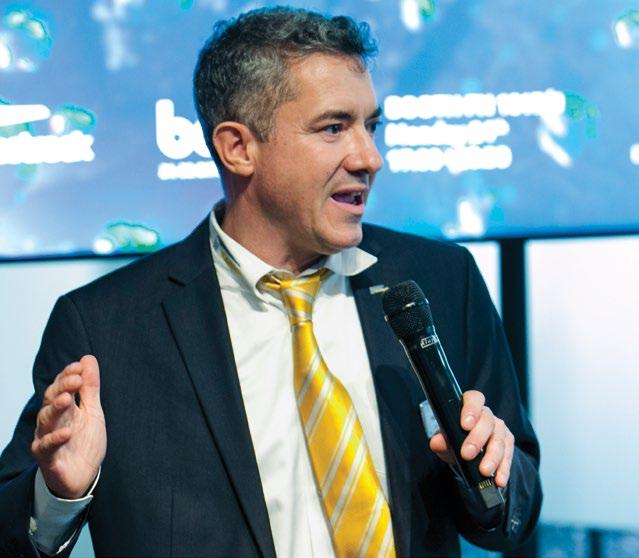
Keestrack first ventured into the electric game in 2012 with the introduction of its e-drive
In recent years, Keestrack has introduced its ZERO-drive machines, a 100% electric offering units, diesel-electric-driven plants directly save up to 40% of fuel. While working in production trains, the attributable fuel consumption may even decrease by 70% when the hybrid screens and stackers are powered directly via the plugout supply of an upstream or downstream electric crusher.
The drop-off engine unit, with integrated gen-set, can be placed on the tracked platform, on the chassis of the machine, or just next to the equipment, and can power several electric driven machines in case there is no plug-in connection from the grid available.
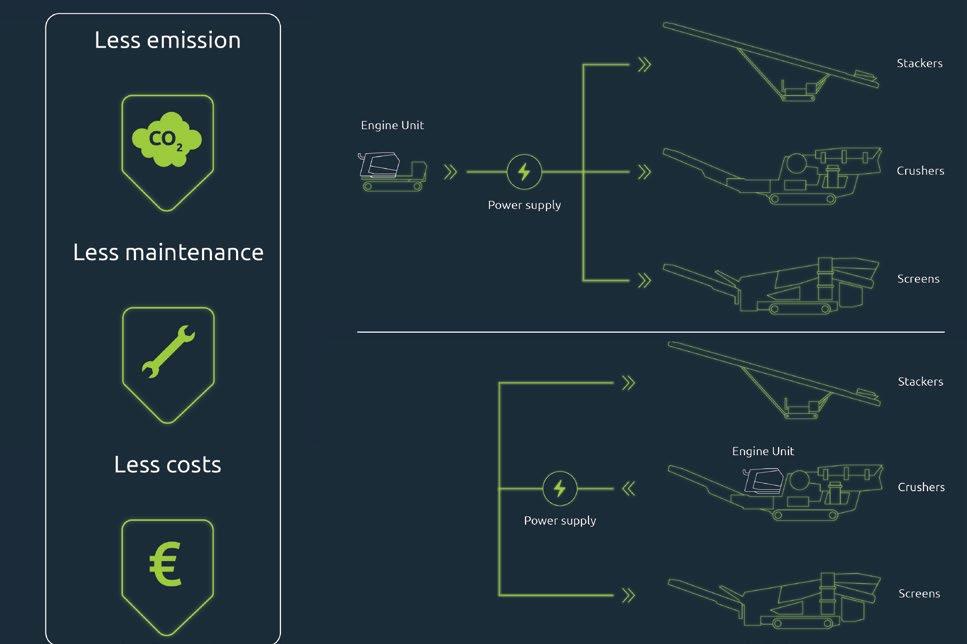
When plugged into the grid, savings are even bigger (depending on the local electricity price), as operational and maintenance costs will decrease drastically.
New concept
A completely new mobile concept from Keestrack is the tracked horizontal reversible impact crusher (RIC), the Keestrack I4e. Due to the innovative RIC technology, the machine can be used in secondary and tertiary crushing of rock, oversized gravel and recycled materials such as asphalt.
The specific design of the reversible horizontal impact crusher with a large variable crushing chamber, powerful rotor (Ø1 100 mm; 4 blow bars) and electronically monitored hydraulic gap adjustment (+80 to -220 mm with new tools) allows feed sizes up to 250 mm and ensures consistently high-quality end products of up to 0/2 mm in closed circuit.
“Secondary and tertiary crushing can be combined in one highly mobile solution, which makes the Keestrack I4e a real alternative to mobile cone crushers or vertical impact crushers, especially with regards to its outstanding production capacities from 100 to 250 t/h,” says Kerkhofs.
According to Keestrack, the system also offers lower wear, better quality of end products (grain shape) and significant energy savings in typical applications (for example, sand production 0/4 mm: approximately -30% compared to cone crushers; -30 to -40% compared to VSI impact crushers). This is largely due to the advanced electric ZERO drive concept, backed up by the dropoff engine/gen-set consisting of a 447-kW diesel engine and 300-kVa generator.
Electric drives for the crusher (160 kW), feeders and conveyor belts as well as the system hydraulics enable particularly cost-efficient and emission-free plug-in network operation. Three specific patents illustrate the innovative potential of the new Keestrack I4e concept.
The compact system, with transport dimensions of 15,27 m x 3 m x 3,31m, weighs in at 42 t and comes with a single deck afterscreen with a return conveyor of oversized material. The closed circuit ensures production of 100% final material with high-quality global standards.
The future
Looking ahead, Kerkhofs expects the industry to continue searching for the most costeffective and sustainable drive systems. Several options are already being evaluated, including hydrogen, fuel cells or battery packs.
“Furthermore, I expect the mobile crushing product range to grow in both ways –smaller equipment for city centre-based applications, and bigger mobile crushers for quarrying, mining and recycling,” concludes Kerkhofs. a
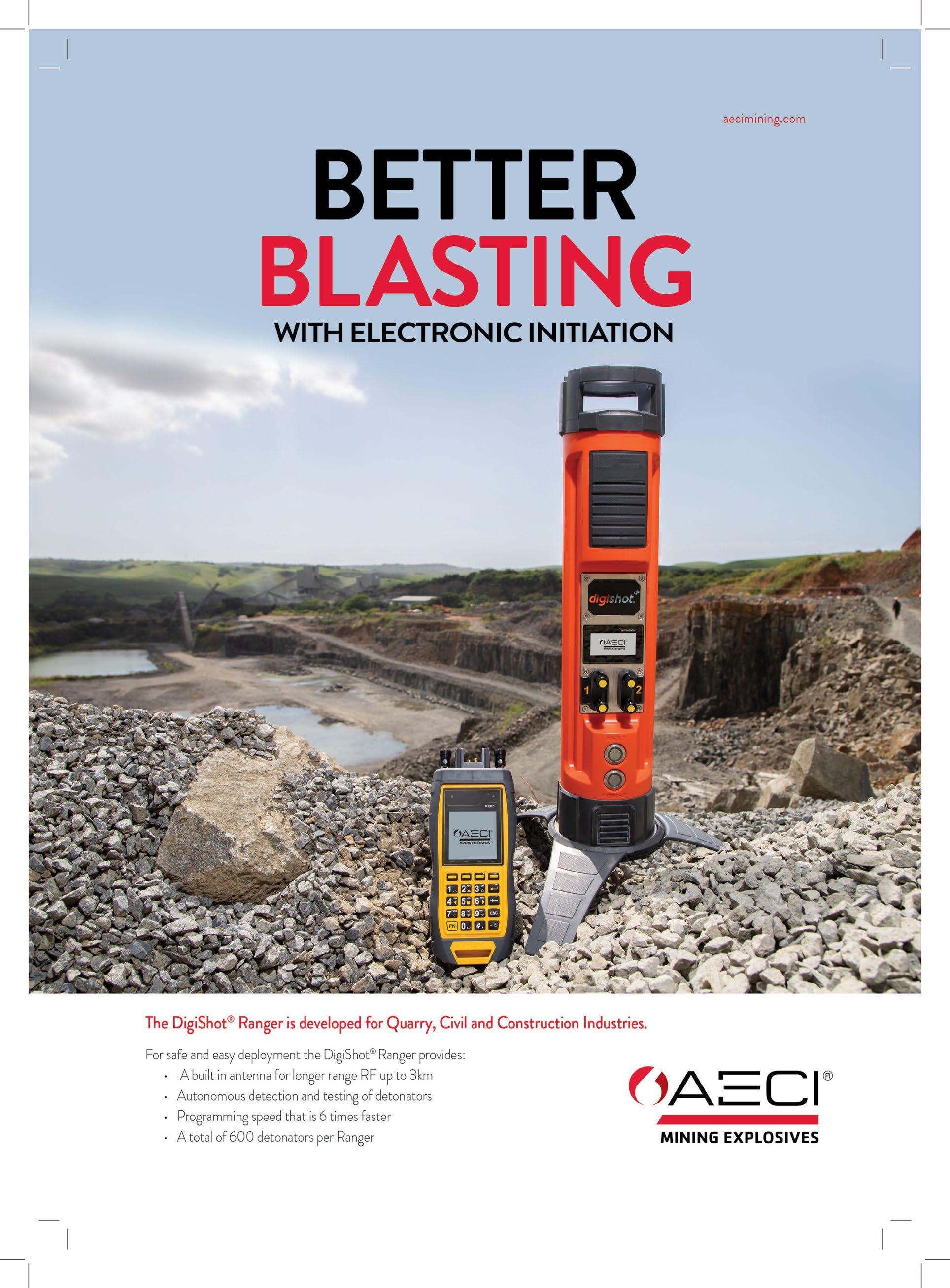