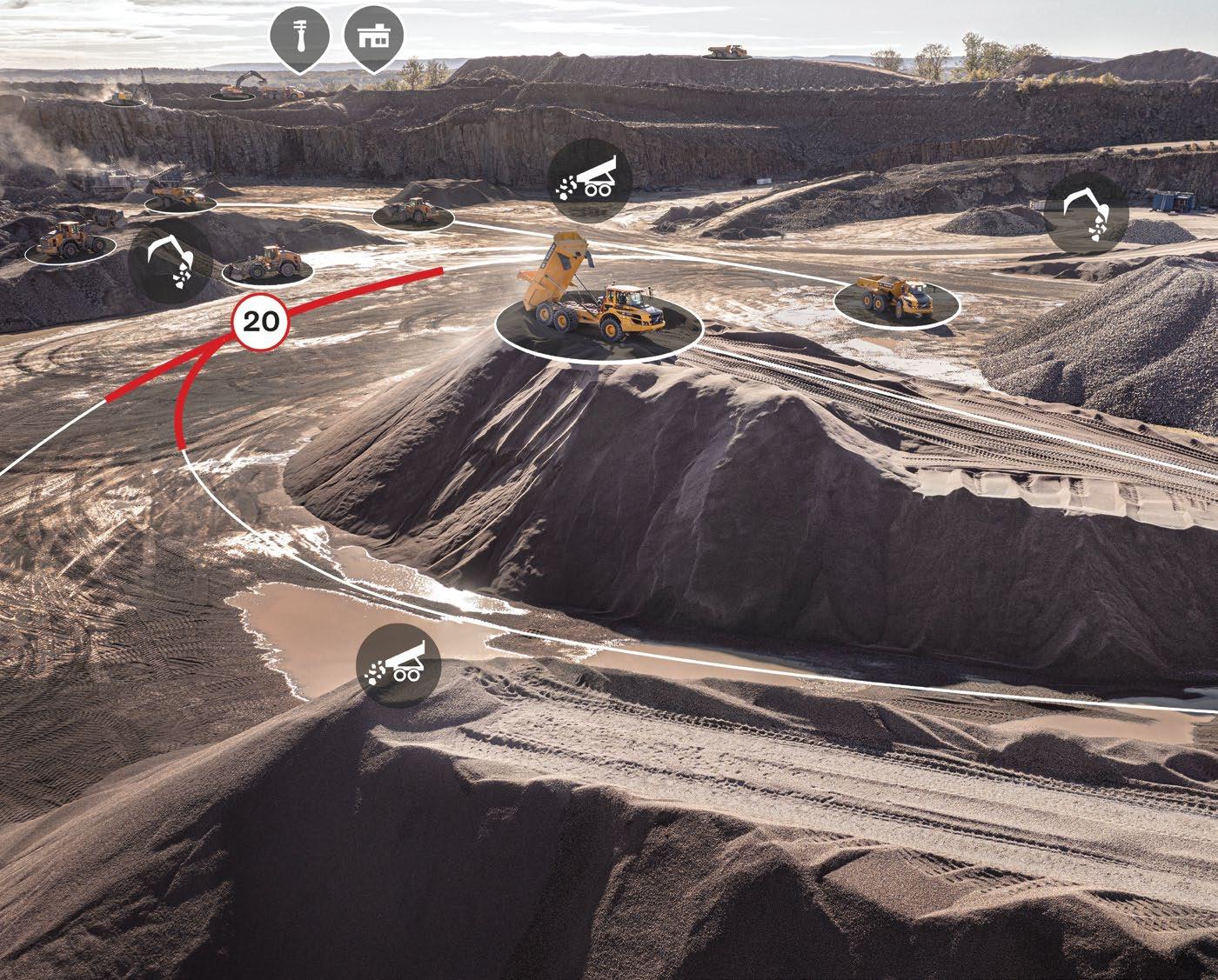
9 minute read
DRIVING EFFICIENCY AND PRODUCTIVITY GAINS
The extractive sector is at a pivotal moment in its history, especially given the incessant changes in technology that could transform the industry. Thus, the importance of adopting a digital transformation strategy cannot be stressed enough, especially in businesses such as quarrying and mining that involve repetitive jobs and moving substantial amounts of materials.
By Munesu Shoko.
Advertisement
Digital transformation has the potential to help quarrying and mining companies reduce their costs and improve profits by streamlining their work processes and providing greater data insights with which to drive strategic decisions.
In a one-on-one with Quarrying Africa, Andrey
Komov, Head of Productivity – Sales Region International, Volvo Construction Equipment, warns that failing to adopt a digital transformation strategy can have devastating consequences.
Even small efficiency gains per tonne moved, he says, can add up to significant savings over time, making the business more competitive and improving the bottom line. In complicated quarry environments, traditional methods may struggle to detect these efficiency gain opportunities, highlighting the need for digital technologies.
Steps to implementation
Digitalisation, Komov stresses, is not a cureall solution, but rather a tool that can help increase efficiency. The key is to use it in the right way and for the right purposes.
“At Volvo Site Solutions, we have developed Site Efficiency Programmes that combine various digital services, training and consultancy to help customers achieve their
1-million t
If an operation moves 1-million tonnes per year, one can always find efficiency gains of at least US$0,1 per tonne with Volvo’s Site Solutions
Key Takeaways
Digital transformation has the potential to help quarrying and mining companies reduce their costs and improve profits by streamlining their work processes and providing greater data insights with which to drive strategic decisions
Even small efficiency gains per tonne moved can add up to significant savings over time, making the business more competitive and improving the bottom line
Volvo CE’s approach to digitalisation entails four steps: Insight, Analyse, Improve and Sustain
By automating processes and reducing waste, digitalisation eliminates extra administration, paperwork and routine, allowing workers to focus on more important tasks goals, such as reducing costs, lowering CO 2 emissions, or increasing production,” he says. Volvo CE’s approach to digitalisation entails four steps: Insight, Analyse, Improve and Sustain. In the Insight phase, the company uses digital tools to establish a baseline of current performance and identify areas for improvement. “Once you can measure it, you can improve it,” says Komov.
“In the Analyse phase, we help quarry owners define key problem areas and simulate the outcome of changes to the site layout and fleet using a digital twin of the site. Here, we can also assist in setting new performance targets,” he adds.
The Improve phase involves implementing the proposed changes. For example, the company offers digital tools to help operators perform better and provide site managers with a better understanding of daily performance.
“In the final step, Sustain, we check whether our targets were met. For example, we check if we achieved the reduction in fuel consumption
208
One manager that we thought was possible. We also monitor progress over time, looking for opportunities to improve and ensuring that the circular approach to improvement never stops,” explains Komov.
By following these four steps, Volvo CE customers can achieve sustainable results and improve their operations in the long term.
“At Volvo Site Solutions, we understand that every customer has unique challenges and objectives. That is why our programmes are tailored to fit the specific results our customers are looking for and may differ from one customer to another. In cases where a customer faces a challenge for which we do not have a ready-made solution, we see it as an opportunity to brainstorm and develop a custom solution,” he adds.
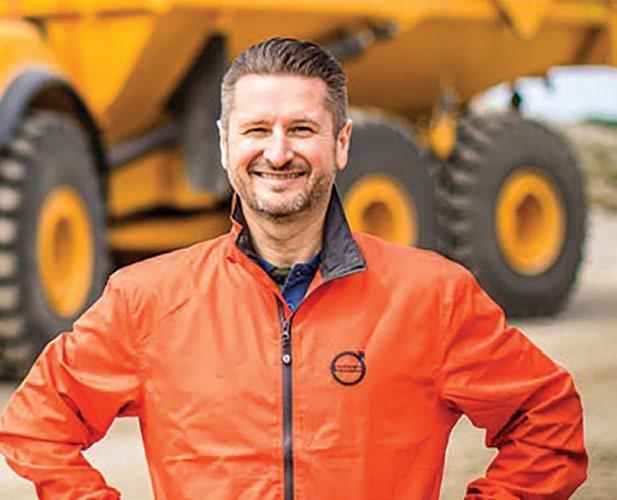
Volvo CE is always eager to learn more about the problems its customers are facing, as this helps the company to develop tools that meet customer-specific needs. “We believe that the key to success is listening to our customers and working together in partnership to find solutions. So, we encourage our customers not to face these challenges alone. Instead, we work together in partnership, as we believe that partnership is the new leadership,” he says.
Key to successful digitalisation
Digitalisation, adds Komov, is a journey that drives change and new ways of working in a company. Therefore, the entire team should be on board and fully committed. Success in digital transformation cannot be delegated to just one person or group. It requires the involvement and dedication of the whole team.
Connectivity on site is crucial for successful digitalisation. To measure parameters in realtime, it is essential to have strong connectivity using machine telematics or tablet solutions. Unfortunately, stresses Komov, there are no shortcuts to achieving this. Volvo CE machines can be equipped with satellite telematics in areas without mobile network coverage, but this option is more expensive due to the cost of satellite connectivity.
Starting small is a better approach to digitalisation, he adds. It is better to start and make adjustments ‘on the go’ rather than trying to make the perfect plan for digitalisation and never taking action. By implementing small, simple changes with immediate gains to the bottom line, a company can achieve quick wins.
“At Volvo, we offer solutions that are brandagnostic and affordable, which means customers can use them regardless of whether they have a Volvo machine in their fleet. We have also developed tablet versions of our digital tools that allow customers to ‘plug and play’ with any machine, providing wider functionality when integrated into a Volvo machine via Co-Pilot. We are continuously learning together with our customers, and our list of solutions will continue to grow over time,” says Komov.
Available solutions
Digitalisation is often perceived as expensive. However, Komov believes this is a misconception. “At Site Solutions and Productivity Services, we challenge and change this paradigm. Our solutions are subscriptionbased, allowing quarries to start with any budget without the need for huge upfront investments. Our customer success managers ensure that customers receive a premium support level and an excellent experience with our solutions,” he says.
For instance, he adds, if an operation moves 1-million tonnes per year, one can always find efficiency gains of at least US$0,1 per tonne with Volvo’s Site Solutions. This translates to a saving of US$100 000 per year, giving the operation more budget to invest in improving efficiency.
Volvo CE offers a range of digital tools and solutions that can help quarries optimise their site management, increase safety and improve efficiency.
Performance Indicator is a tool that provides live information about production volumes from each machine (measured using the onboard weighing system on Volvo CE machines), payload utilisation (underloading, overloading, carry-back), fuel efficiency (tonnes per litre), and more. Customers can set target volume and see deviations in real-time, allowing them to take immediate corrective measures. Data can be sent straight into the management system in digital format, eliminating paperwork. This tool works best together with Connected Map.

Connected Map gives both machine operators and site managers visibility of the site. Operators can see each other’s position on the Co-Pilot screen inside their Volvo CE machine or on a tablet screen in non-Volvo machines. This increases safety, especially on sites with curved or narrow roads. Operators can also see each loading unit and choose to reduce speed or go to an alternative loading unit with fewer or no queues.
Site management has a full picture of the site on their PC or tablet and can manually despatch machines if there is a need due to congestion or deviations from target production volumes in certain areas. The tool is brand-agnostic and can work on any machine.
“In the 21 st century, air traffic is primarily controlled by humans using digital tools from airport control towers. Similarly, Connected Map serves as a digital tool that provides quarry managers with real-time visibility and control of their operation. While some mining operations have implemented costly automated despatching solutions, these solutions are not always effective without human input,” says Komov.
Connected Map, on the other hand, offers an affordable and reliable solution that allows for human intervention to ensure maximum efficiency. Additionally, Site Management features, such as restricted areas and speed limits, can be set up to improve site safety and overall productivity. Just like the radar screen in an air traffic control tower, Connected Map provides a critical tool for managers to optimise their quarry operations.
Task Manager is a Volvo CE tool that is mostly used in infrastructure projects and connects people, machines and projects, giving real-time status updates. It can also serve the needs in quarrying if there are no Volvo CE machines on site with integrated on-board weighing systems. The tool allows for manual tracking of production volumes and can generate loading receipts for operators. Site managers can get the full picture on their PC or laptop.
At Volvo Site Solutions, they understand that every customer has unique challenges and objectives. That is why their programmes are tailored to fit the specific results customers are looking for and may differ from one customer to another.
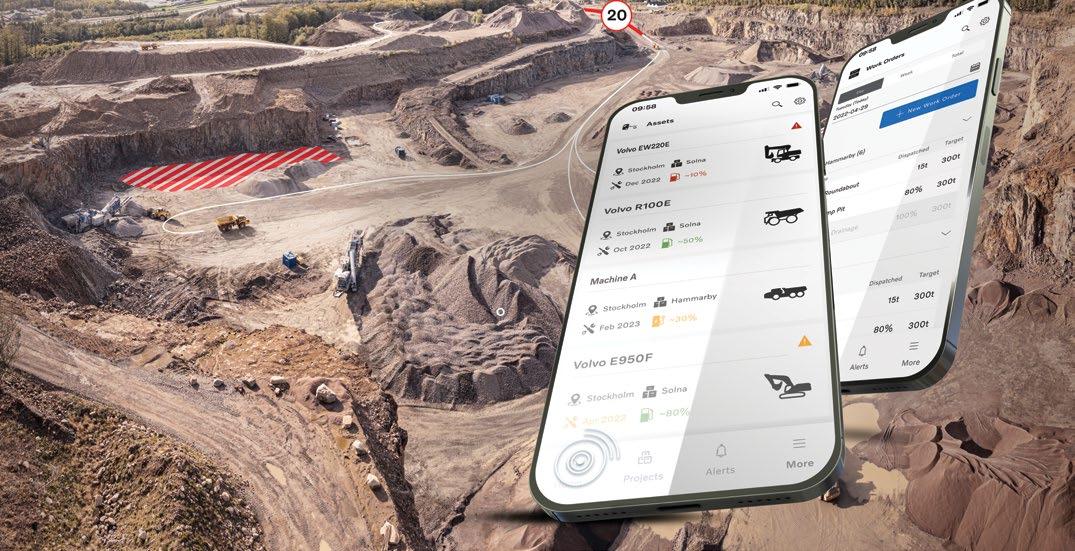
Connected Load Out is a solution that simplifies the load-out process by digitising orders and load tickets and connecting loader operators, site offices and incoming trucks. The real-time overview leads to more efficient choices and control of the process, saving both time and money.
Site Simulation is used for site optimisation by creating accurate scenarios of different site layouts, fleet set-ups, ground conditions and more. Customers can immediately see potential improvement gains on a cost-per-tonne level.
EcoOperator is a training programme that uses Volvo simulators, which allow for significant speedup of operator competency development without burning diesel or damaging machines.
“Recently, we made it possible to deliver this training to anywhere in the world by putting simulators into mobile containers with climate control. We have found that operator experience can influence productivity by around 20%, so this programme is a crucial part of increasing efficiency,” says Komov.
Poor operating behaviour, he adds, can also lead to machine downtime, which is why operators are such an important part of the equation and why improvements through digitalisation can be significantly lower if operators are left out of scope. Volvo CE has therefore built in operator coaching functions into Volvo Co-Pilot Operator Coaching, which provides feedback to operators on their behaviour and areas for improvement.
ActiveCare is a machine monitoring service that uses telematics to check the health of Volvo CE machines, analyse error codes and diagnose issues using artificial intelligence. This helps prevent breakdowns and increase uptime. The service is free for five years for Volvo heavy machines working in quarry and mining segments.
Volvo CE has built in operator coaching functions into Volvo CoPilot Operator Coaching, which provides feedback to operators on their behaviour and areas for improvement.
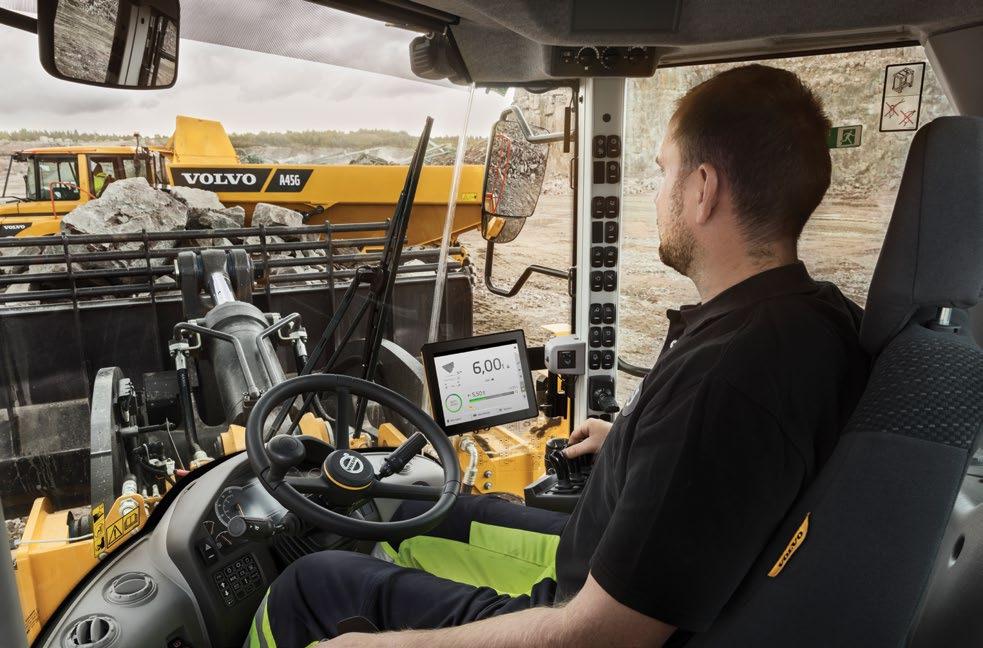
Key benefits
Digital transformation brings numerous benefits to quarries, including guaranteed efficiency gains that lead to savings and increased profitability, says Komov. By automating processes and reducing waste, digitalisation eliminates extra administration, paperwork and routine, allowing workers to focus on more important tasks. Moreover, digitalisation helps reduce the quarry’s carbon footprint and make the business more sustainable.
“One of the most significant benefits of digital transformation is the live picture it provides of the production process and volumes. This realtime monitoring allows quarry managers to see deviations immediately and act accordingly, optimising production and reducing downtime,” says Komov.
In addition to extra efficiency gains, digitalisation makes the quarry a better place to work and helps attract top talent on the competitive labour market.
“Another important benefit of digital transformation is increased site safety. With tools such as Connected Map and Task Manager, quarry managers can monitor the site in real-time, track machine and operator behaviour and create no-go zones to prevent accidents. By using data to identify safety risks, quarries can proactively implement safety measures and avoid accidents before they happen,” he adds.
Case studies
Over the years, Volvo CE has successfully partnered with numerous quarrying businesses to help them transform their operations through the implementation of its digital technologies. The joint efforts with customers have yielded positive feedback, which has been a major source of motivation for the company in its digital journey.
“One of our customers who adopted our Performance Indicator and Connected Map technologies reported saving four hours per week on reduced administration time. This translates into 208 hours per year, or 26 working days for a top manager,” he says.
Several customers who have implemented Volvo’s Connected Map technology have reported increased operator awareness of vehicle traffic flow. Operators can now slow down when they see a line forming to be loaded by an excavator, instead of rushing to the spot and waiting. This, combined with speed zone implementation has led to a positive effect on fuel consumption.
By conducting site optimisation work, Volvo CE can analyse cycle data from a customers’ operation and help them identify improvement potential. In one instance, Volvo noted a long waiting time for truck loading and dumping. Further investigations revealed that the wheel loader operator was not working efficiently, causing loading to take an excessive amount of time.
“By creating a digital twin of the site, Volvo CE was able to analyse the impact of process changes and concluded that they could reduce cost per tonne by 18% with minor changes in their cycle time. Operator training from Volvo CE was recommended as one of the next steps,” concludes Komov. a

Ctrack has a long history of managing movable assets and its locally built hardware, along with a variety of bespoke software solutions, has proven to be ideal for harsh mining conditions.