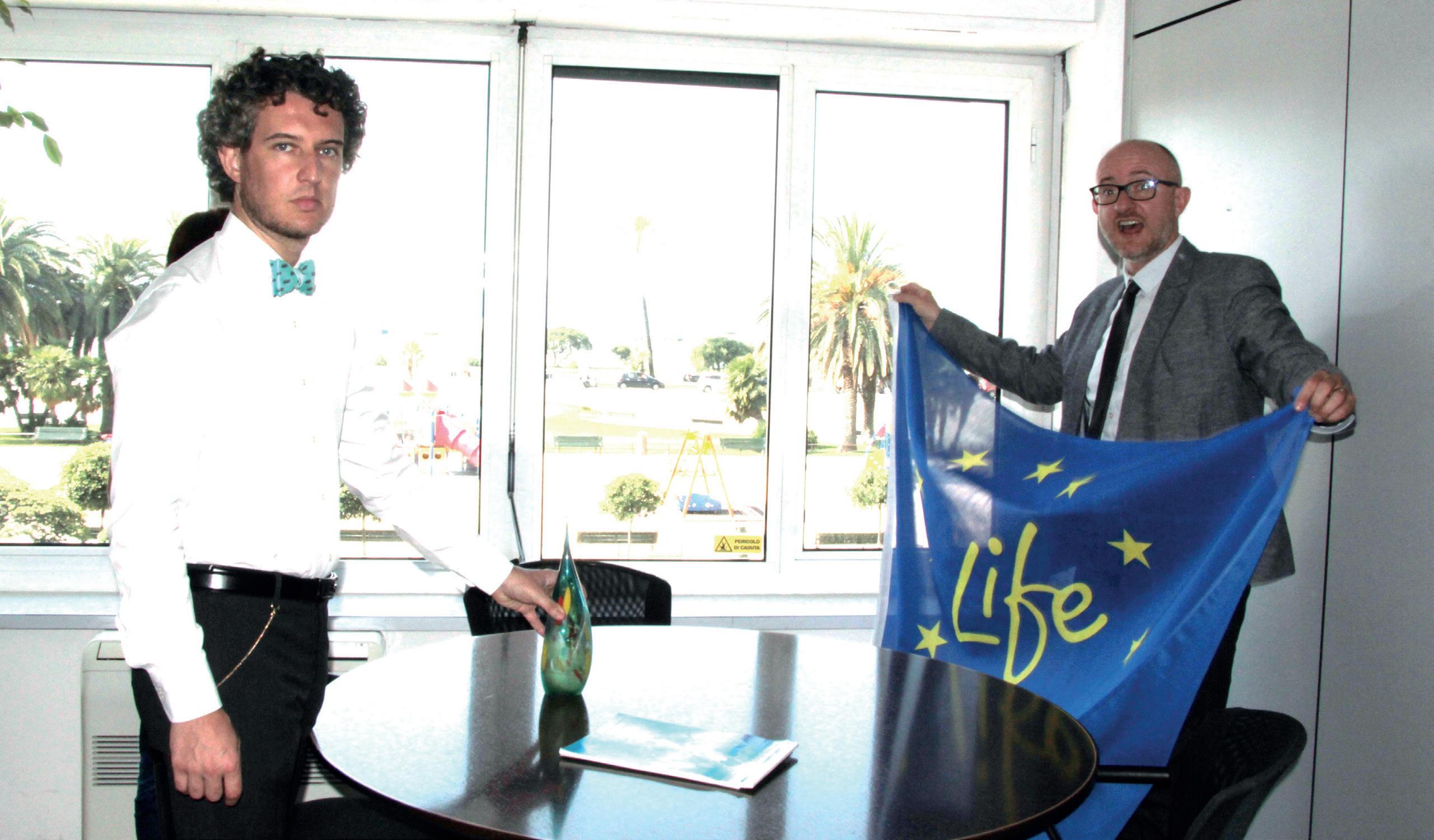
8 minute read
Hydrogen: Stara Glass
Giorgio Minestrini, dissemination manager, and� � Ernesto Cattaneo, coordinator of the LIFE SUGAR project, inside Stara Glass offices.
The idea of a Total Recovery Glass Furnace and the LIFE SUGAR Project
Ernesto Cattaneo* discusses a consortium which aims to launch a glass manufacturing furnace that can decrease energy and NOX emissions of a regenerative furnace.
European Union aims for carbon neutrality by 2050. This ambitious and well due goal has put the glass industry under an unprecedented negative spotlight. We used to be thought about for the total recyclability of our products, or for their unmatchable chemical inertia. Now the glass industry means a ratio 3.5:1 between glass and CO2 production. In fact, Europe produces 35 Mtonne/ year of glass and 10 Mton/year of CO2 for its melting.
If some glass researchers had had a magic trick in the sleeve to solve the CO2 issue, at this point it would have already come out. But it did not, so it appears we will have to start paving all the hard roads in front of us, and analyse all possible contributions to CO2 containment, one by one: � Electrification: in Italy, the average fuel efficiency of electrical energy production is 45%. Regenerative furnaces, can easily have a 65% fuel efficiency. Therefore, in the countries where energy production is not mostly renewable, glass furnace electrification causes a world increase of CO2, not a decrease. � Alternative fuels: they make sense when all the process is sustainable. Hydrogen is indeed interesting, since is does not contain carbon, but nowadays 95% of the hydrogen in the world is produced by steam reforming, it is therefore grey and very far from carbon neutrality. � Carbon Capture and Storage (CCS): it does not seem to be applicable everywhere, and anyway, as said, we need to deal with 10.000.000.000kg/year of CO2. � Efficiency increase: even if regenerative furnace chambers have a tremendous temperature efficiency, in fact they heat air up to 1300°C with a flow of 1500°C waste gas, still about 30% of the burned fuel is wasted with the 500600°C fumes. This direction for carbon containment is indeed the most virtuous one, because it involves all others as a cascade.
Stara Glass, as a furnace design company, has always aimed at utilising the residual waste gas heat that, depending on the furnace size, might even be 2MW. The idea is to cool down the waste gas up to the coldest level allowed by the filter, which is commonly about 200°C for bag filters, and reintegrate in the process the saved thermal power.
Stara Glass, with its Centauro technology (Fig 1), has already been able
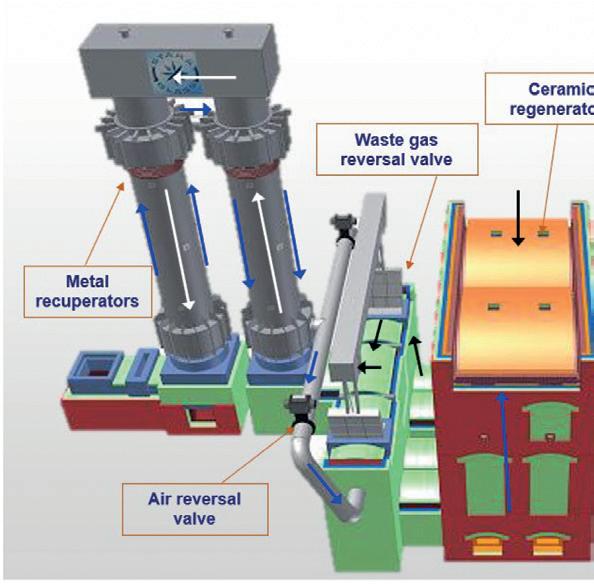
� Fig 1. Stara Glass Centauro. � Fig 2. An example Centauro furnace with its fl ows, its temperatures and its heat recovery system split in.

to extract the residual waste gas heat, in form of hot clean air, but this was used outside the glass production process, for example to produce hot water or to heat the factory during winter time, but, while the factory gas bill decreases, the furnace specifi c consumption (kcal/kg) of a Centauro furnace is the same of an equivalent end-port.
In the simplest words, Centauro is an end-port furnace where the low temperature part of the chambers, about 3-4 m of checkers in height, is substituted by a metal heat recovery system thus: � Solving important layout restrictions. � Allowing the utilisation of the SNCR technology for NOx removal (that is applied in the about 800°C zone between chambers and recuperators). � Allowing the said extra-process heat recovery.
Fig 2 shows an example Centauro furnace with its fl ows, its temperatures and its heat recovery system split in: � Regenerative chambers � Radiating heat exchangers (double shell counterfl ow metal recuperators) � Convective heat exchanger (crossfl ow with large air-fl ow)
Oversizing the fl ow in the metal part allows extracting all extractable heat from waste gas.
You can see that, in front of 11.000 Sm3/h of air needed from the combustion, more than 27.000 are sent to the fi rst exchanger, and 13.000 Sm3/h @ 150°C + 3.400 @ 500°C are extracted to be used in the factory. When all heat is constantly utilised a saving of about 1MW is achieved.
But it would be much more interesting to bring that thermal power inside the process. How? It is possible to produce electrical energy, but Carnot points out we would waste more than 2/3 of it. Heat is not a noble source of energy like mechanical or electrical power, heat is convenient to be used to heat up, not to create motion. So, what can we heat? � Air: end-port and Centauro furnaces have already heat recovery systems dimensioned to their upper limit. � Glass batch or cullet: it is possible, and some glass producers do it, but it involves potential carry-over and dioxins issues, and it is technically unfeasible to transfer to this fl ow all the heat we intend to recover. � Fuel: natural gas has such a lower volume, compared to waste gas, that it cannot physically store all the thermal power we want to recover. But methane can be made react, in a very endothermic chemical reaction, to convert be converted into a fuel of a much higher calorifi c value: hydrogen.
The LIFE SUGAR Project
SUstainable Glass: Architecture of a furnace heat recovery system including a steam Reformer
The idea of the LIFE SUGAR project is utilising the waste gas heat to convert the natural gas methane into hydrogen by a steam reforming reaction.
CH4 + H2O 3H2 + CO
This reaction is strongly endothermic and our theoretical evaluation is that the reforming of about 1/3 of the fuel, which will be reintroduced in the furnace as syngas, is enough to saturate the process and allow an about 15% energy and therefore CO2 saving.
Since the reaction happens at temperatures higher than a regular end-port waste gas, we will utilise the particular structure of the Centauro system heat recovery and extract the waste gas between the metal and ceramic parts of the heat recovery system, as shown in Fig 3.
Hydrogen combustion will raise the NOx levels but the effective SCNR system included in Centauro furnaces will contain the issue under NOx emission law limits.
The LIFE SUGAR project has been fi nanced by the LIFE instrument of European Community and it involves several specialised companies: � SG - Stara Glass: project leader specialised in glass furnace design and innovation, based in Genova, Italy. � PRO - SGRPRO: a start-up dedicated to measure, computing and research, controlled by Stara Glass. � JM - Johnson Matthey: a global science and chemicals company, and a sustainable technologies specialist including catalysts and processes for steam reforming, based in Reading, England. � KT - Kinetics Technology, an international technology licensor and EPC contractor with a track record in steam reforming. Based in Roma, Italy. � SSV - Stazione Sperimentale del Vetro is a research centre and analytical laboratory specialised in glass science and technology, with a strong experience in on-site process and emissions measurements. Based in Murano, Italy. � UNIGE - Università degli Studi di Genova- the reference research centre for modelling and testing glass production industrial solutions.
The project features the following activities: 1. Design, construction and installation in the UNIGE facilities of a mock-up component to test the catalyst. 2. Recruitment of a glass producer to test the solution on the fi eld; this activity is already concluded; the prototype will
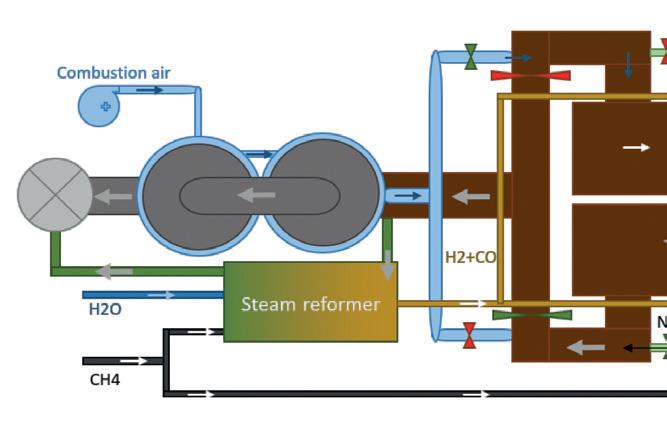
� Fig 3. Centauro + SUGAR technology.
� Fig 4. the locations of the LIFE SUGAR project.
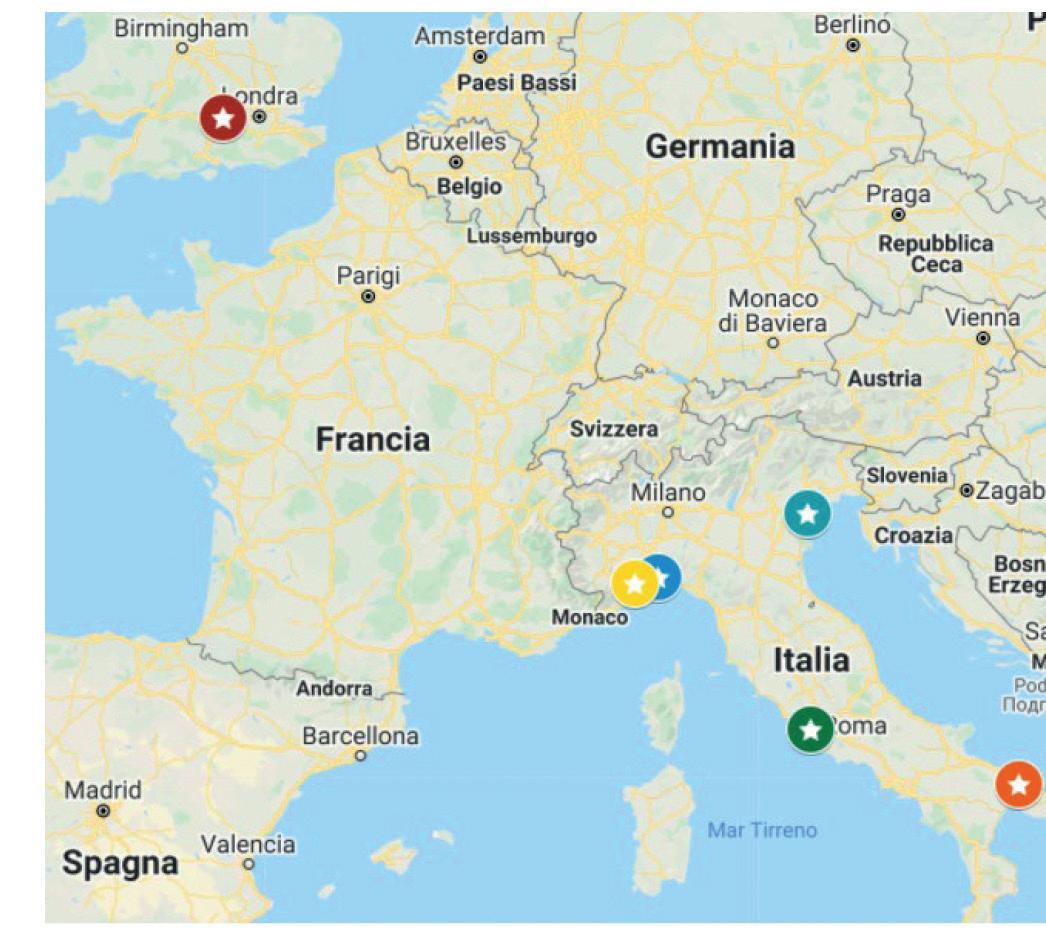
be installed in the new Centauro furnace of the Castellana Grotte (Bari – Italy) Vetrerie Meridionali O-I plant. 3. Design and construction of a SUGAR prototype module, about 1:5 scaled (foreseen energy saving: 2-5%). 4. Test, tuning and fi eld demonstration of the technology. 5. Design of the fi nal full-scaled product. 6. Business development, dissemination.
The fi nal goal of the project is to launch on the glass market what we call a total recovery furnace, that can decrease the energy consumption (and NOx production as well) of regenerative furnaces in a very signifi cant way – target 15% – and, with it, CO2 emission and glass production cost, to match the increasing demand of production sustainability.
While this idea is not applicable to regenerative furnaces, it is to other types like unit melter or oxy-gas furnaces, with different levels of effi ciency. Once the externally heated steam reformer unit and process for glass furnaces are developed, we will work for an even wider application of this technology. �
*LIFE SUGAR project coordinator, Stara Glass head of innovation projects, Stara Glass, Genoa, Italy www.staraglass.it/
Air Products is blazing a new trail for oxy-fuel burner technology . . .
Boost your performance and productivity for better glass with the Cleanfire® HRx ™ burner!
Upgrading your oxy-fuel burners, adding burners to boost production, or converting your air-fuel furnace to oxy-fuel? The patent pending Cleanfire HRx burner offers you expanded functionality and flexibility with unmatched performance. It can deliver: • Increased flame radiation for high fuel efficiency • Ultra-low NOxemissions • Foam reduction capability for higher-quality glass • Enhanced productivity • Optional remote performance monitoring feature This burner is the latest innovation in the long line of industry-leading Cleanfire® burners for the glass industry. To learn more or to schedule a demonstration in our state-of-the-art lab, call 800-654-4567 (code 10867) or visit airproducts.com/HRx.

To make glass better, put Air Products in the mix.
© Air Products and Chemicals, Inc., 2018 (41791)
tell me more
airproducts.com/HRx