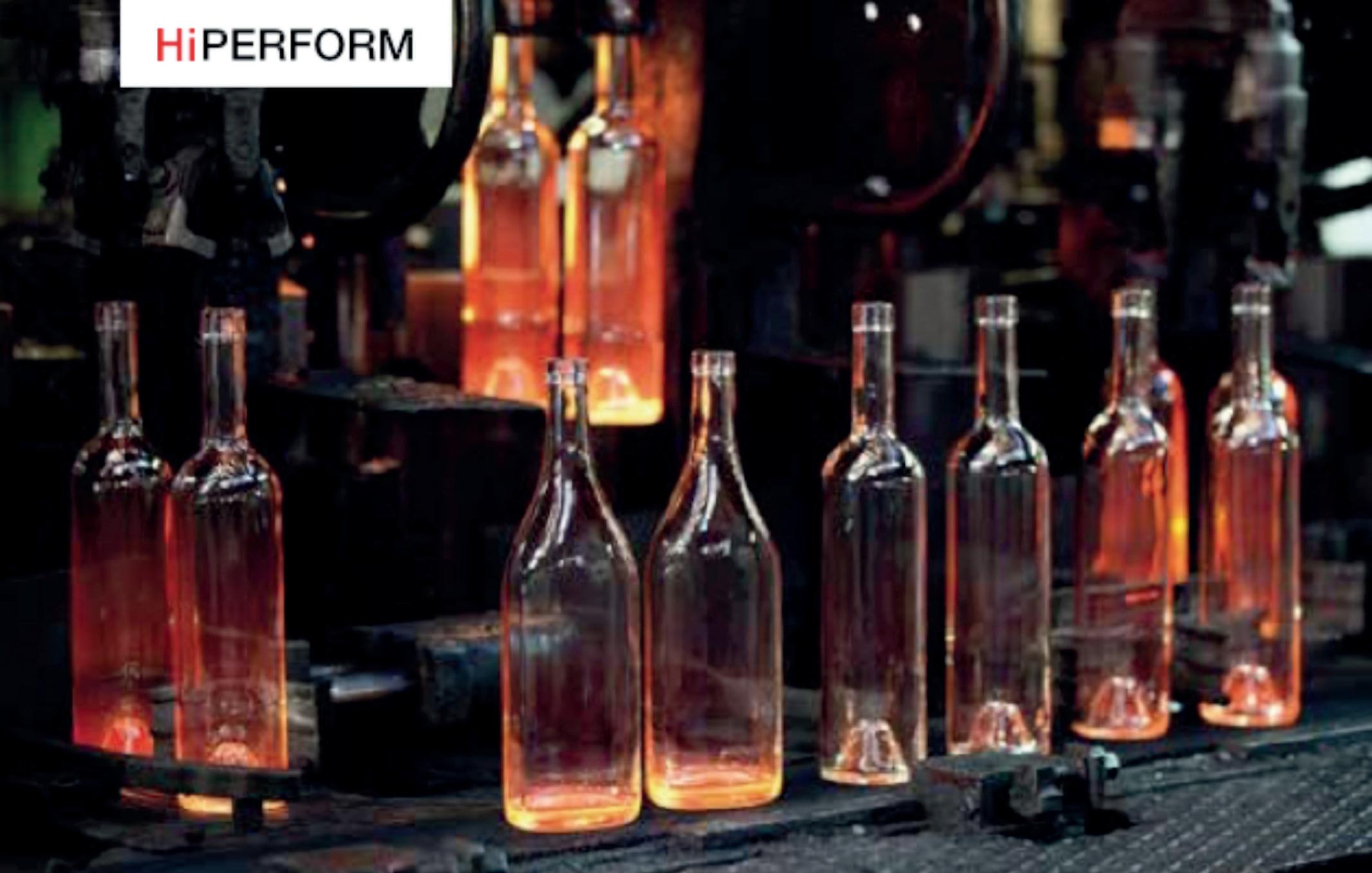
9 minute read
Future of Forming:Heye/Glass Futures
In search of a container forming revolution
Peter Firth* highlights the evolution of container glass forming and asks if there will be any further revolutionary changes in the forming process or of the machines that implement it.
Ihave often asked myself, and many others, about whether we are going to ever see a fundamentally different automatic glass container forming process. When I say a different process, I mean totally unrecognisable from any of the current two-stage process; whether that be Blow-Blow, Press-Blow, or NarrowNeck-Press-Blow (BB, PB, NNPB).
Within these original forming approaches, we have seen some radical mechanisation changes over the years that span about a century now. This was started with the BB process where it was made both by hand and semi-automatically by people effectively making one bottle at a time, aided by moulds and mouth-blown or using compressed air.
They used the power in their arms to open and close the moulds as well as collect the glass. Often requiring two people for each single forming station, if I remember correctly, from seeing the old film footages (I am not that old!).
After this original manual two-stage, semi-automatic mechanisation of the forming process, there came the full automation of the process via the rotary machine where the whole machine was rotated around an axis. Maybe his is where the original 360-degree timing came from, even before the 360-degree drum-driven I.S. Machines?
This development of the first automatic machine is attributed to Michael J. Owens from the Libbey Glass Company in Toledo, Ohio, USA. Although the machine was a breakthrough at the time, it was effective in the forming process but suffered from productivity issues as the whole machine would have to be stopped to attend to breakdowns or equipment parts changes.
� Glass Futures site.
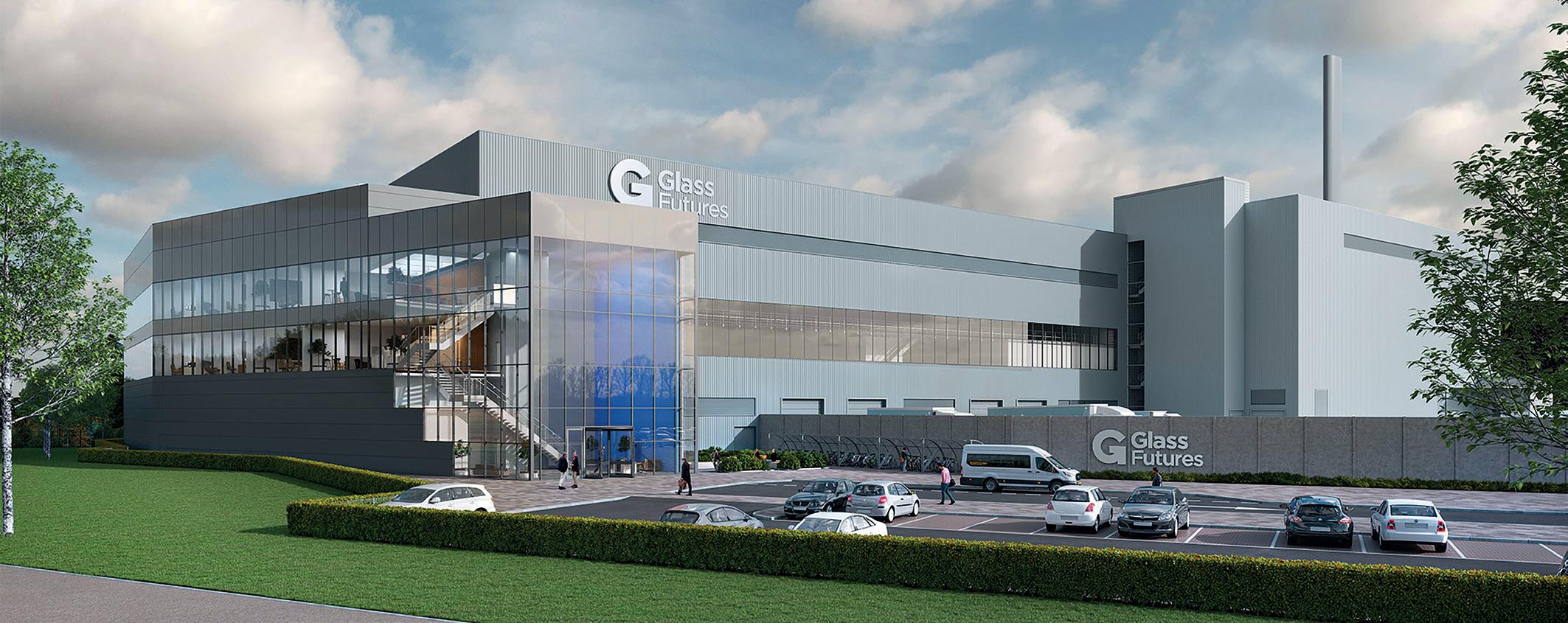
Even though still the same essential process, the next revolution was the change from the rotary machine to what we now know as the I.S. Machine. The letters I.S. is believed to have stood for either the description of the machine as the Individual Section Machine or because of the inventors being named Ingle and Smith. The original patent application being by Henry W. Ingle and Charles Goodwin Smith of the then Hartford-Empire company (now known as Emhart Glass). Maybe it was a bit of both, and both are worthy descriptions.
This revolutionary new forming machine was made, marketed and distributed widely under patent protection. As the intellectual property protection expired, competitors using virtually the same mechanisms arrived on the scene to assist in proliferating the provision of such machines all over the world. I can’t even expect myself to name all the different suppliers of such machinery nowadays, although these now differ in many details to the original mechanism by Emhart.
There are currently many manufacturers of IS Machines, but to the casual observer, these will still exhibit the fundamentally same characteristics as each other. Decisions on which supplier of a forming machine to choose from often comes down to matters of company standards and price, as well as maybe supply capabilities depending on the specific forming controls required.
However, notwithstanding the details, the customer glass plant will still be getting what they could have also obtained from another machine supplier. At least the customers of the glass containers will not be able to recognise any difference in the chosen forming machine.
When NNPB was developed by Heye Glass in the 1970s, it was seen as revolutionary, and so it was. Although still within the bounds of the recognisable two-stage forming process, the change they introduced was to press the parison of a narrow neck container rather than use compressed air to form it. This was revolutionary in that the ‘finish’ (ring or top) of the container was formed last in the blank-side process, rather than first as in the BB process. Nothing fundamentally different to the widemouth PB production process, however, but nonetheless this was revolutionary in narrow-neck container forming thinking at the time.
NNPB became a worldwide glass container forming gamechanger. This new container forming process enabled lighter containers to be manufactured for the same capacity than could be achieved with BB.
Only many years later are we seeing enhancements in the details in the BB forming process challenge the performance of the NNPB process. Application of blank-side vacuum and attention to forming details and equipment has given rise to containers made with BB which compete with those made from NNPB. But we still have the same three fundamental forming processes.
Even if there have been changes in the basic container forming approach since, those approaches have not found the traction and support that means they can compete with the original processes. By competing I mean in terms of productivity and quality.
In the combination of these two factors, the I.S. Machine remains the workhorse of the industry. With a few bespoke customisations for making speciality items maybe, but still pretty much based on the original forming processes already mentioned.
I am aware of one other fundamental departure from the traditional container forming machine. Again, this was from the team at Heye Glass, which made a container machine known as the H1-2 Machine. This was still in operation at Oberkirchen on C Furnace when I was employed as Technical Director (UK - Glass) within the Ardagh Group. (Heye Glass became part of Ardagh, although the technical and machinery division, Heye International, still stands as a separate company under the Ardagh Group).
However, the lack of significant overall benefits of the H1-2 over the IS Machine, and its restriction to wide-mouth production, led to it being shut down about 13 years ago, along with C Furnace itself.
Suppliers are now incrementally improving their I.S. Machines with reduced dependency on compressed air as the main motive force. Although compressed air is still exclusively used as the forming air for the containers and as a means of cooling for the plungers. Most of the basic standard sizes of the machine still remain as well, such as the 21” width of the section boxes and the centre distances between the moulds on the machine, typically being 4.25”, 5.0”, 5.5” and 6.25”, as well as many other different more recent centre distances for triple and quad gob production.
Unsurprisingly, general industrial technology developments have been the recent driver for the changes in the I.S. Machine. Although this is more of a continuous improvement route, rather than a radical departure from an established forming process or machine concept. The more common such applications being the servomechanisation of section mechanisms, which followed the earlier servo developments in the ancillary drives and mechanisms such as the feeder, shears, scoop, ware pushers, conveyor drives, ware transfer and lehr-stacker.
We are now also seeing many thirdparty suppliers that specialise in certain aspects of the forming process and who look to interface with the forming machine; whether that is directly by connection and control, or indirectly through the provision of information to the Machine operator.
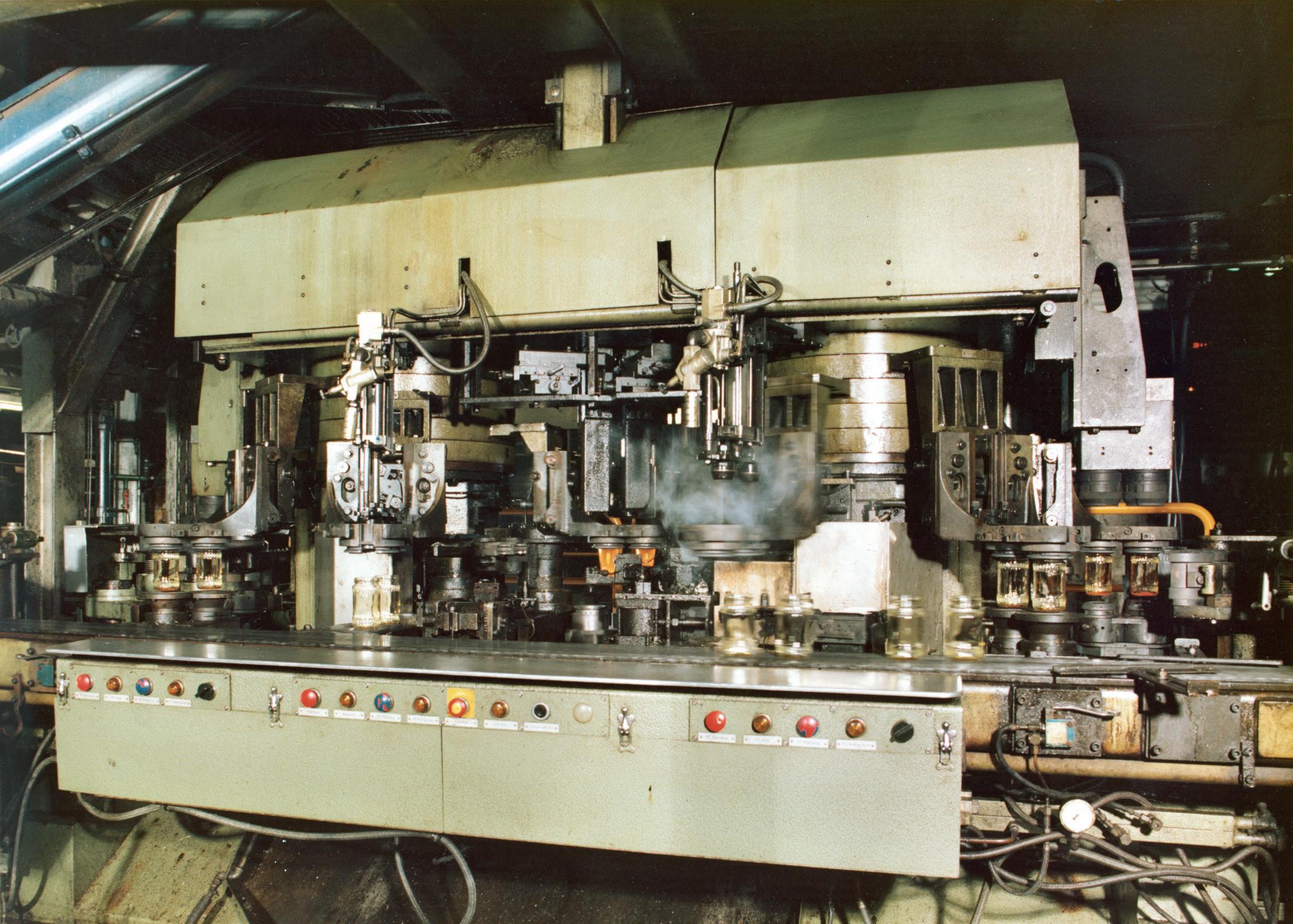
Typical examples here being infrared vision or sensing systems to detect the heat in the glass or from the mould gear, or simply vision to visually assess the position of motions including the gob delivery to the blank-side. Further, priordeveloped robotic technology is now being deployed in the forming process to replace previous human operator machine interventions.
The point being here that nothing is fundamentally changing anymore, and back to my question about whether we will see any further revolutionary changes in the forming process or the machines that implement it.
I, for one, would be happy to hear of some new changes that can revolutionise the way we make glass containers, even though I cannot currently conceive of what that might be myself.
Maybe the last major spark of mechanical and forming genius from the inventors Ingle and Smith is what mankind is left with for the basics of the glass-container forming process for time to come? Or maybe the next generation of Ingle and Smith is reading this article or even working away on it secretly ready to surprise us all. Only time will tell.
By way of encouragement and assistance for supporting the future possible developments, whether incremental or revolutionary, I have been pleased to be working as part of the design team for the Glass Futures St Helens project. This is a glass Research & Development (R&D) plant for all kinds of glass production, but starting with a forming focus on glass containers.
Very soon in the plant design process, we will be looking at the specification of a small R&D I.S. Machine, which will be made available for experimentation and development work. Maybe this might help support the future of glass container forming and eventually lead to a revolution. It could even be a gamechanger such as we have seen in the past, or maybe that is just wishful thinking?
No matter what, there will at least be one facility in the world that is absolutely open to any ideas and happy to put those ideas under glass as soon as possible. By working on this project, I am currently proposing that we consider a 6-Section Machine Bed, with just four installed sections. In this way, we will have two vacant section stations able to be tailored to customer R&D requirements.
This would therefore allow those two additional stations to be loaded with glass and also to feed onto the machine conveyor, together with any other production at the time from the installed sections.
The width of any proposed development section would not be a restriction as there is a 2 x 21” (42”) in space to work with. The remaining space to the side of the outer potential ‘test section’ location would enable relatively easy access to the internals of any new sectional development work.
If, however, it was a totally different machine concept that needed to be put under glass, there is a space for a future as yet unknown forming machine from an additional future foreheath we are allowing for in the design of the facility.
If you, your company, or your employer have an interest using such test facilities for taking the forming process to the next level, please get in touch with us to discuss.
You also still have a chance to influence the proposed R&D plant layout (which I covered in brief in an article in April 2021 in Glass International).
Do this simply by making contact and presenting your suggestions. We are open to any constructive input during this design phase of the St Helens R&D Glass Plant.�
*Private Consultant (Glass Container Production), working with Glass Futures on the GFL St Helens Project Contact: Via LinkedIn Profile (search ‘Peter J Firth’) or email peterjfirth@gmail.com
Glass Futures, https://www.glass-futures.org/ Heye International, www.heye-international.com