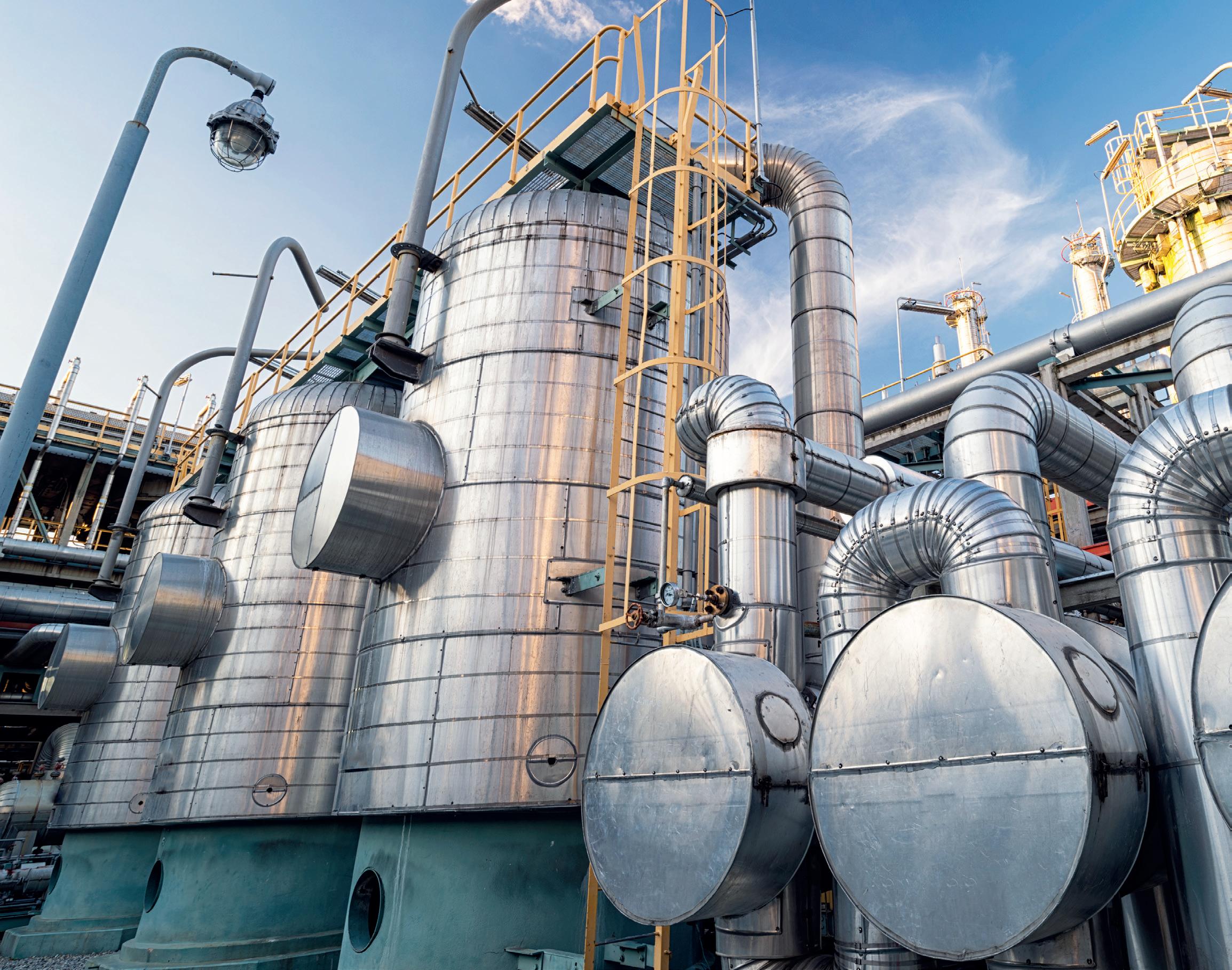
5 minute read
Hydrogen in glassmaking: CelSian Consortium plots industrial stage
Hydrogen consortium plots industrial stage
A consortium which was formed last year to investigate the potential of hydrogen in the glass manufacturing process has continued to make progress despite the challenges of the pandemic. Greg Morris spoke to steering committee member Oscar Verheijen about its aims.
Aproject to investigate the use of hydrogen in the glass manufacturing process has made progress this year and aims to apply for industrial scale funding.
The consortium, headed by Dutch energy group DNV and which includes a number of glass manufacturers and technology suppliers, has continued its pilot phase and even increased its number of participants.
Oscar Verheijen, Project Manager from CelSian and a member of the consortium’s Steering Committee, said there were now 34 members of the hydrogen group, with the majority from the glass industry but other members from other sectors such as steel.
“It is an interesting consortium made up of companies from different geographies as well as diverse industries, such as steel and energy.”
The aim of the pilot phase has been to test the performance of different air- and oxy-fuel burner types combusting mixtures of CH4 and H¬2, and consider the implications of switching to hydrogen by for example determining the changes in the radiative heat transfer and NOx emission. It is hoped to develop a burner type that will allow the gradual transition from natural gas to hydrogen.
He added: “The results so far have been encouraging. At this stage we’re still gathering more knowledge, developing NOx mitigating strategies, testing the burners and control systems which is ongoing. At the same time we have had more participants join, despite the fact we have already been running for a year.
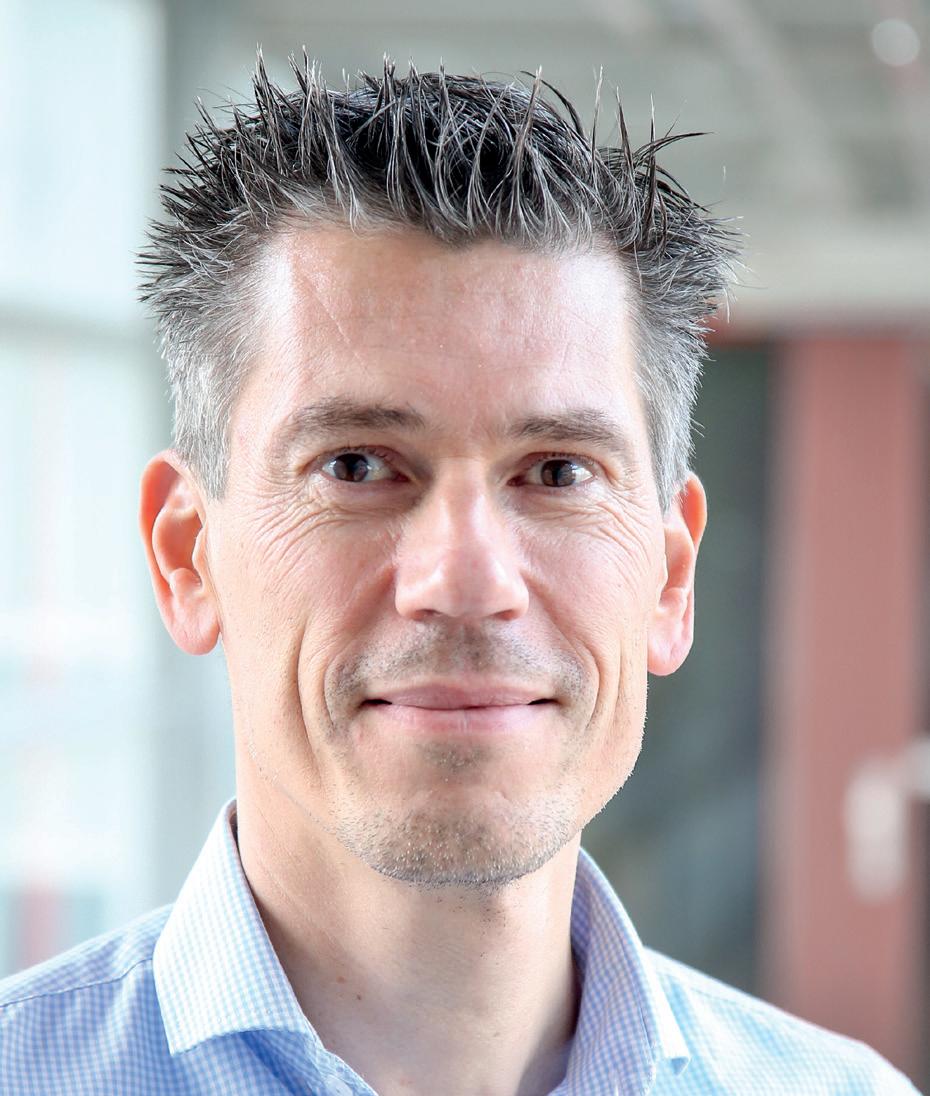
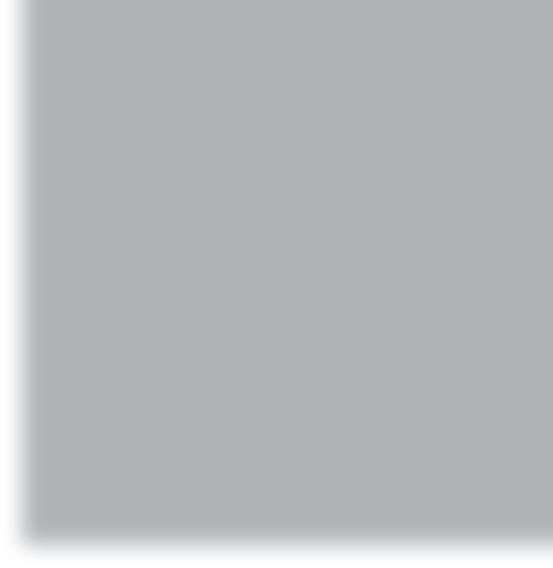
� Oscar Verheijen.


We are very pleased with the increased engagement from the glass industry.”
Some of CelSian’s work within the project includes working with laser sensor to monitor the convection process, look at how the fl ame shape is developing and the combustion process. A simulation is then carried out to quantify and describe the heat transfer, which might be critical for any future furnace and process design based on hydrogen.
While the pandemic did halt some of the operational parts of the project, such as ensuring everything ran at a scheduled time, the technical and management side continued unabated.
The pilot phase of the project is due to come to an end on 2022 but there are already plans to extend it to an industrial phase. This will depend on receiving appropriate economic support from the funding authorities.
Mr Verheijen hopes that the project will eventually be able to demonstrate there are no technical hurdles to implement hydrogen combustion in the glass industry. This could either be the use of 100% hydrogen or the use of blends such as natural gas.
Mr Verheijen said: “If you can use blends and can easily control the combustion process based on the mixture and do not see impact on glass quality then it opens the way for the introduction of hydrogen combustion, whether it is full scale, or 50% or 30%.”
Mr Verheijen is hopeful that some glass manufacturers would consider introducing hydrogen on a small scale in order to reduce their CO2 emissions rather than waiting for a full furnace rebuild, which could be several years for some glass producers.
“They do not have to wait until the moment they do a rebuild before completely switching over to hydrogen, and that creates a fl exibility for the availability of hydrogen. Although we have to acknowledge there will be local challenges based on the necessary infrastructure of hydrogen.”
Members
The number of participant companies within the consortium has increased to 34 in the past year, and approximately 40% of participants are from the glass sector.
These include container manufacturers O-I, Ardagh Glass, Bormioli Rocco, and Verallia, fl at glass makers AGC, Cardinal, Saint-Gobain and Vitro Architectural Glass, specialist glass manufacturers Corning, Schott, and Nippon Electric Glass, fi ber glass producer Owens Corning, pharmaceutical manufacturer SGD Pharma, tableware specialist Arc International, as well as furnace supplier Tecoglass and technology supplier Stara Glass.
Mr Verheijen said: “A lot of companies see they will have to do something in the future and use this project to get knowledge and to defi ne their roadmap. It’s diffi cult to defi ne whether it will be electric fi ring or a hydrogen hybrid, it is about collecting know how at this stage.”
He added: “One of the biggest challenges is always to fi nd a good consortium of companies who work well together. We do have a good group and it has snowballed. Other companies look towards it and say they should be part of that otherwise they might miss some information. So the size of the group automatically increases.”
The subject of sustainability and of the environment has become a hot topic within the glass industry in recent years. Mr Verheijen has been impressed by how rapidly manufacturers have investigated new technologies that could reduce glass production emissions.
The GlassTrend organisation, of which Mr Verheijen is chairman, has seen increased interest in the subject in recent meetings, not just from European and Asian companies but from North America as well.
“The US re-signing up to the Paris climate agreement will further support the development of sustainable technologies from which hydrogen might be a solution for the future. Therefore, USbased companies are keen to participate in this project.
“They are aware of investing in glass resources and even looking at carbon capture followed by storage and/or utilisation, which I would not have expected to have happened two years ago. So there is more traction in the market on this topic.”
A unique aspect about the project is that a specifi c facility has been constructed at DNV’s site near Groningen, The Netherlands where the testing has taken place. DNV has a strong background in the development and testing of combustion technologies within their R&D facilities. The facility includes a furnace with a water cooled bottom, which extracts heat from the furnace.
The consortium aims to deliver the proposal for the next phase of the project next year with the intention to start work on the second phase in early 2023.
For this follow-up phase it is envisioned to include batch melting in the pilot facility to assess also the impact of H2rich combustion on glass quality. �