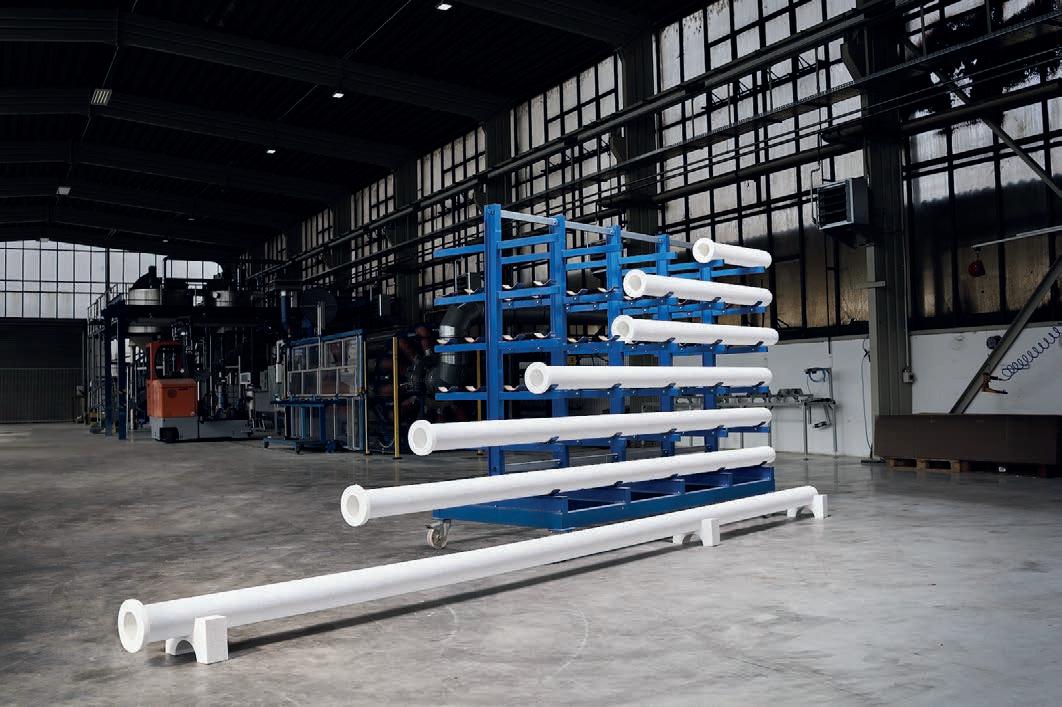
11 minute read
Refractories: Rath
Fig Filtrath filter elements ha e been speciall e elope for se in hot gas filtration p to
rom refractories to hot gas filtration
obert uss er discusses a feeder e pendable series e clusively developed and produced by ath which will be presented at glasstec .
With more than 130 years of experience in refractory technology means Rath is at home wherever heat-resistant materials are essential – and thus also in the glass industry.
The internationally operating Austrian refractories manufacturer offers a range of materials for the entire glass manufacturing process and specialises in hot gas filtration.
It will present a new feeder expendable series at glasstec in September. There is also news from the Rath hot gas filter elements production facility in Meißen: the manufacturing capacities have been doubled by putting a new production line into operation.
Rath owns seven production sites in Europe and the USA and operates in more than 30 countries.
Refractory materials
Including the original Emhart Glass designed feeder systems, Rath offers a range of quality refractory materials for the entire glass manufacturing process. High quality raw materials are used for all of Rath’s refractories, designed to achieve predictable density and resistance to erosion and corrosion.
The organisation delivers refractory and insulating products for regenerator chambers, melting furnaces, distributors, forehearths and the original Emhart designed feeder expendables (including spouts, spout accessories, tubes, plungers, stirrers, rotor segments, orifice rings, etc.). Having the original Emhart technical database and the widest mould park among the expendable suppliers, Rath provides the industry’s widest range of refractory feeder expendable compositions for all kinds of glass qualities. Its refractory spare parts are available in a variety of materials to address each customer’s individual needs. The bonded compositions include alumina silicates, AZS, zirconia, zirconia toughened alumina, fused-silica, calcined clay and clay flux materials.
Glass manufacturing products
Rath’s refractory products are designed for sectors such as container glass, float glass, C-glass, E-glass and tableware. It is also a supplier of glass house crucibles, daily pots, and accessories, such as gathering balls, rings, half rings, stoppers, furnace doors for art glass manufacturers.
The product range includes dense bricks and cast components, as well as refractories, dense low-cement, ultralow cement, non-cement, insulating, gunning and gunite castables, insulating
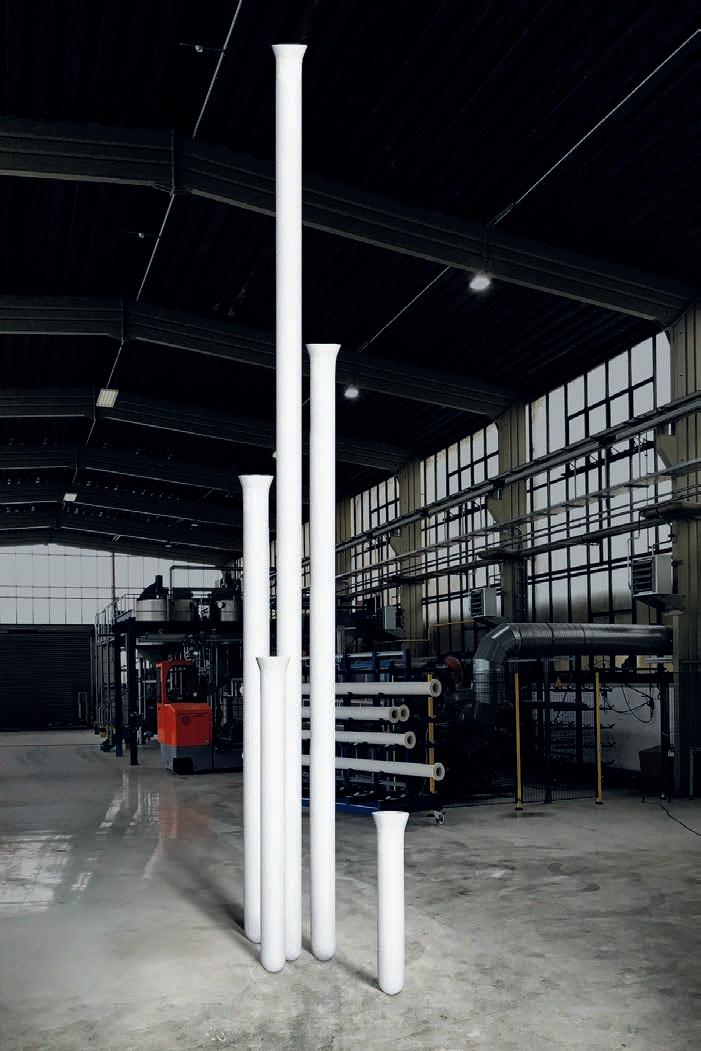
bricks and other insulation materials such as high-temperature insulation wool, vacuum-formed and microporous products.
Furthermore, Rath produces special shaped products for the glass industry in its facilities in the USA and EU, such as burner blocks, peephole blocks, camera blocks, doghouse protection arches, lip blocks, restrictor tiles, tweels, mandrels, and fused-silica suspended and crown repair bricks. In addition, Rath provides refractory concepts for distributor and forehearth channels, including roof and burner courses, forehearth channels from different bonded high alumina and AZSbased refractory materials.
glasstec 2022
The further development of refractory compositions is a challenge that Rath is taking on. Robert Nusszer, Managing Director of the Sales Unit Glass, said: “We are constantly modernising the technology and our refractory compositions. The development of the new feeder expendable product family is a very important step ahead for all of us in the Rath Group.”
After a five-year research and development process, the new Fourath 4xx feeder expendable series is ready for introduction at glasstec in Düsseldorf. Mr Nusszer continued: “We are pleased to present the next generation of our previous feeder series: a new product line based on a formulation which has been exclusively developed and produced by Rath.
“The product has been put through its paces in our laboratories and has successfully passed the first glass factory trials in the last 1.5 to 2 years.”
Fourath 4xx
The Fourath 4xx feeder expendable series improves crack and thermal shock resistance, has extremely low impurities level, longer service life, higher glass quality and gob homogeneity.
While the previous 3xx mixes – like the well-known 333, 315, 301, 338, 345 –were produced using the slipcasting technique, the Fourath 4xx mixes are produced using hybrid technology. Rath uses the same mould park, but casting is no longer done via slipcasting; instead, a special vibrocasting technology is used.
“This brings advantages for our customers. For example, the new feeder series convinces with improved product quality – due to a more compact mix and better surface quality,” said Mr Nusszer.
“We selected the highest quality raw materials to keep the impurity level to a minimum. Furthermore, with the new manufacturing technology – thanks to the much better dimensional tolerances we can keep – we can avoid the additional grinding, for example of the tube’s outer surface.”
Thus, Rath can increase the service life. “The thermal shock resistance has also improved and the risk of cracking is lower than ever. The product remains in perfect condition until the end.”
The new product is out now. Rath customers can easily switch to the Fourath 4xx feeder series. There are no additional costs for the moulds – the same part numbers are used as before, only the last three digits will change. The pricing of the new mixes is more or less the same; a price increase due to the improved quality is not envisioned.
The following products will be shown at glasstec: the already well tested and released 420 (a complementary mix of 333, 315) – tubes, plungers, orifice rings and stirrers as well as the new 473 zirconiainserted spouts; for the latter, Rath is still looking for candidates for operational
Fig Filtrath filter elements ha e been speciall
e elope for se in hot gas filtration p to
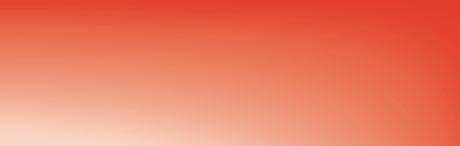
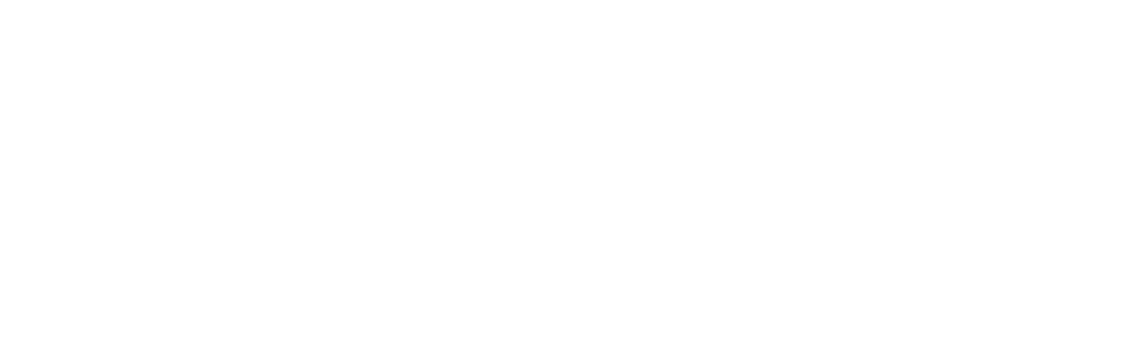
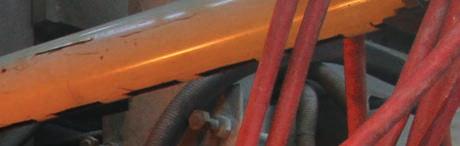
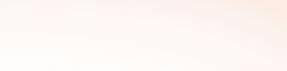
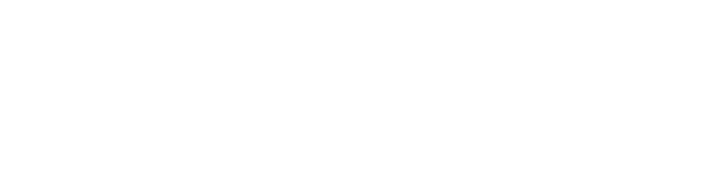
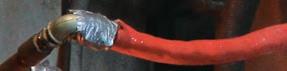


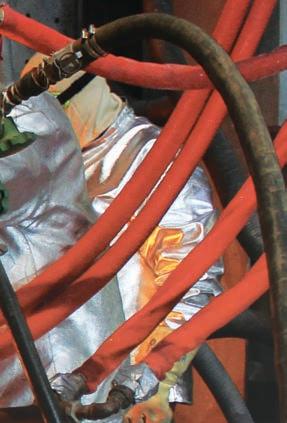
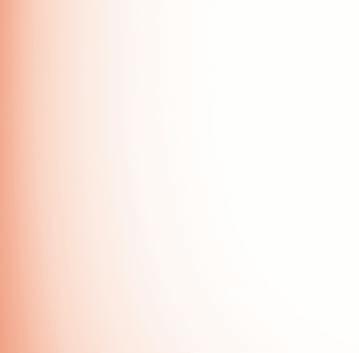
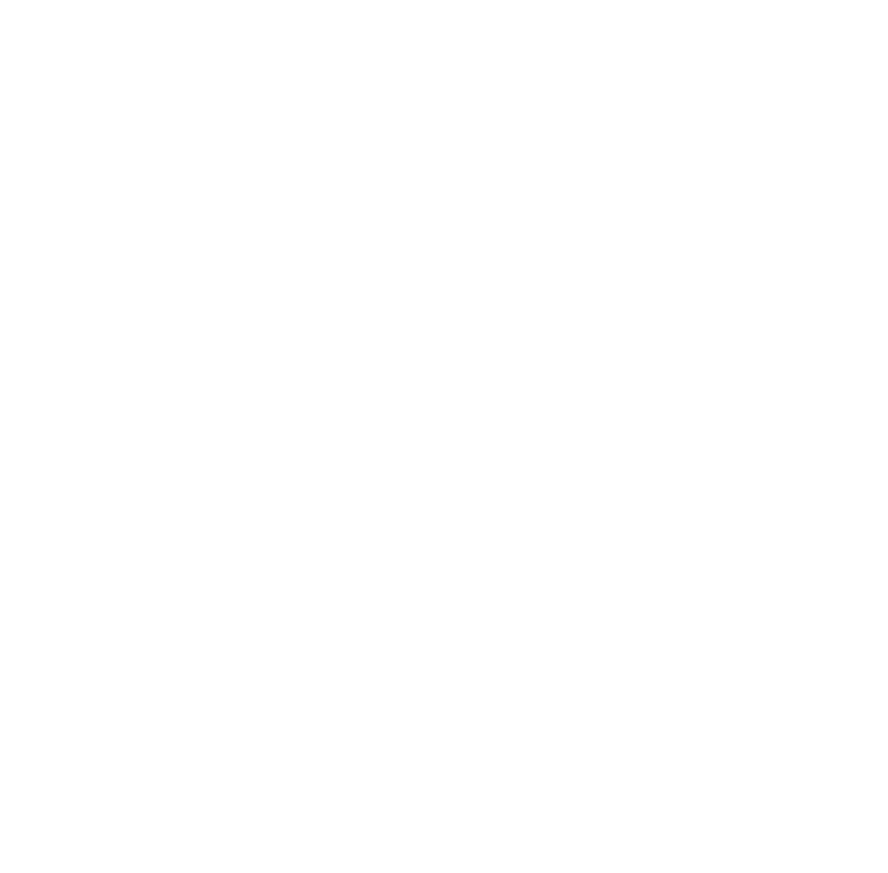
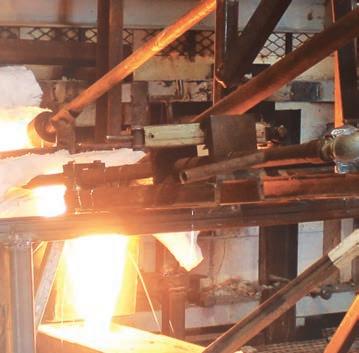
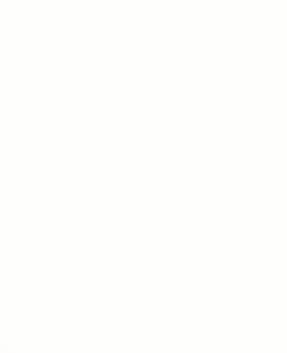
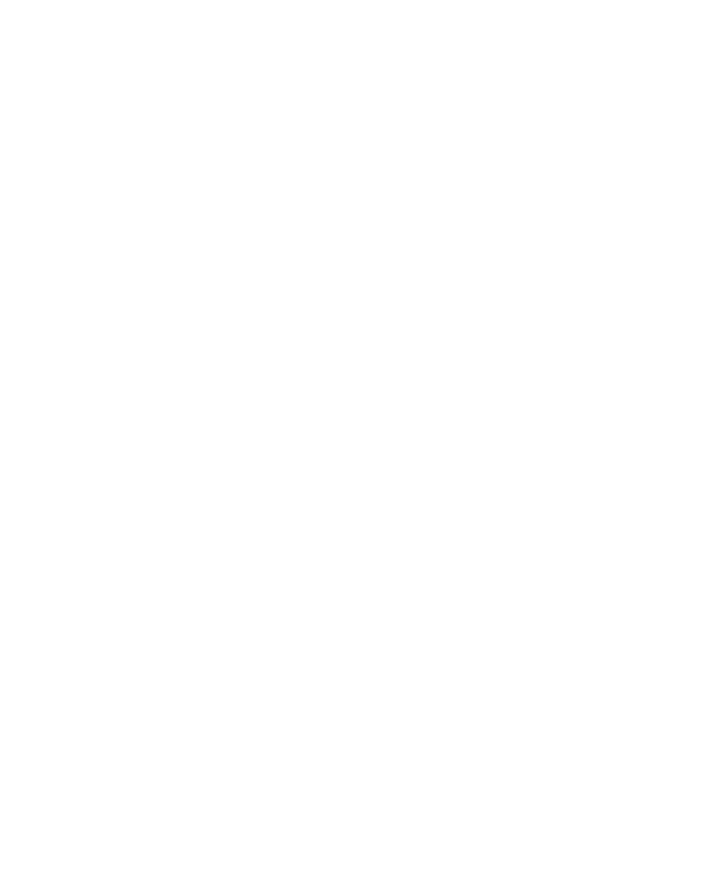
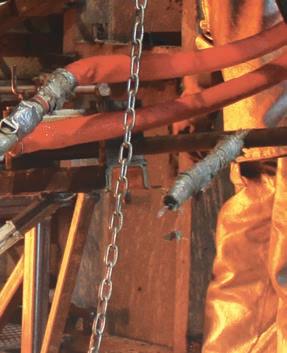
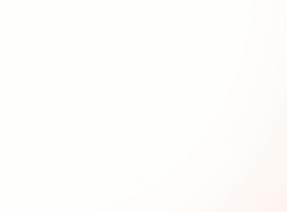

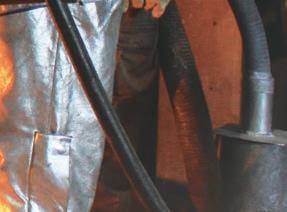
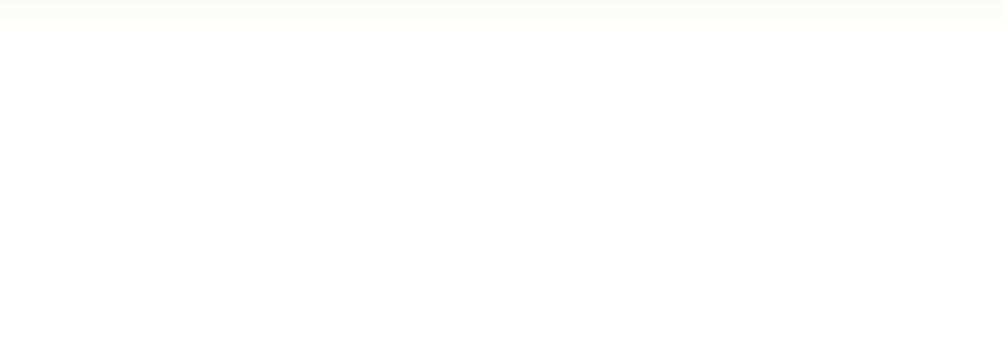
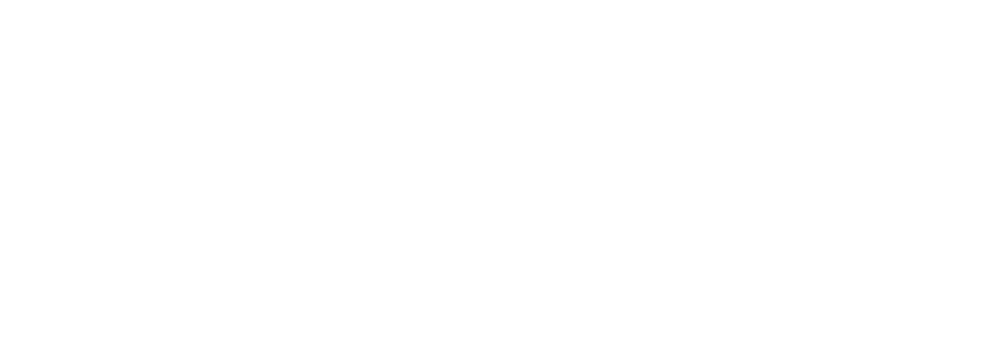

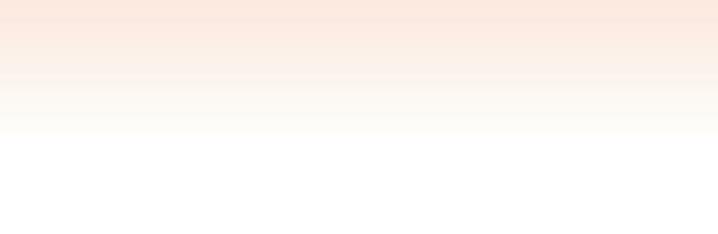
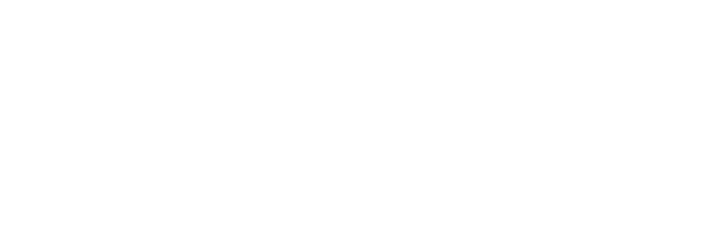
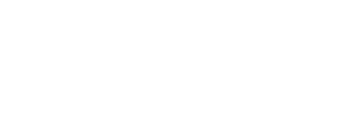
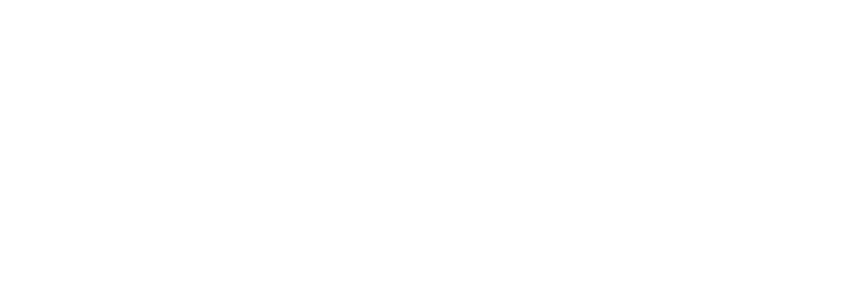
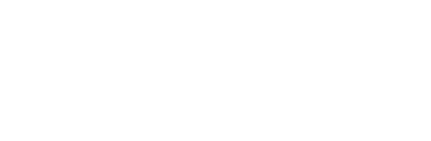
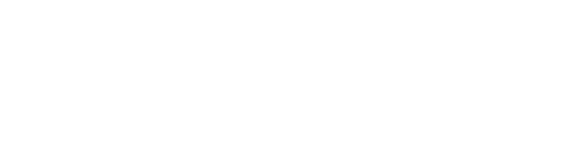
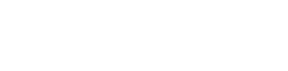
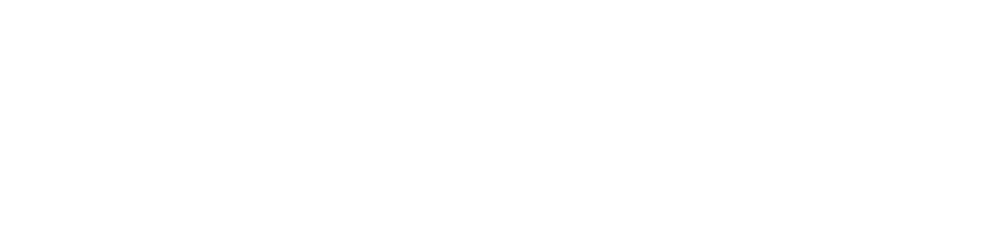
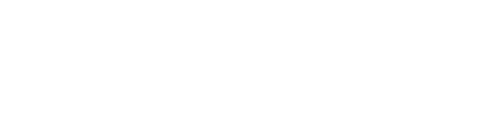
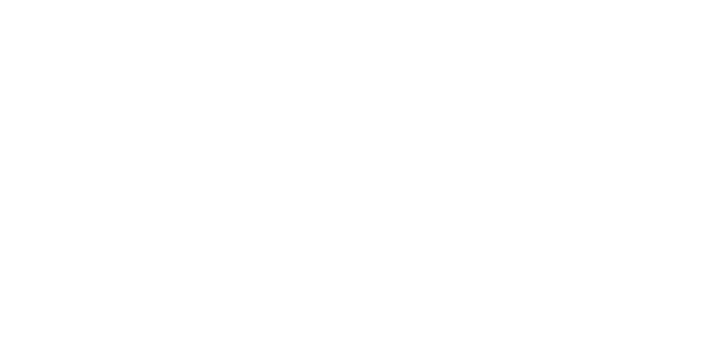
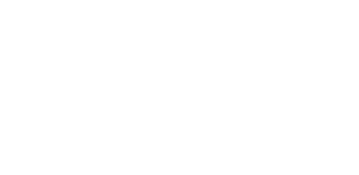
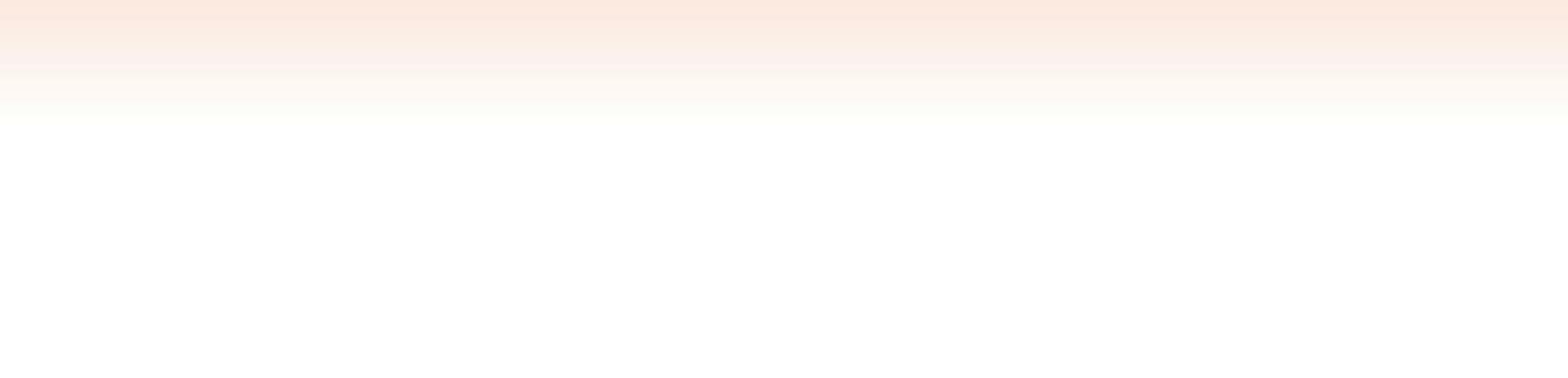
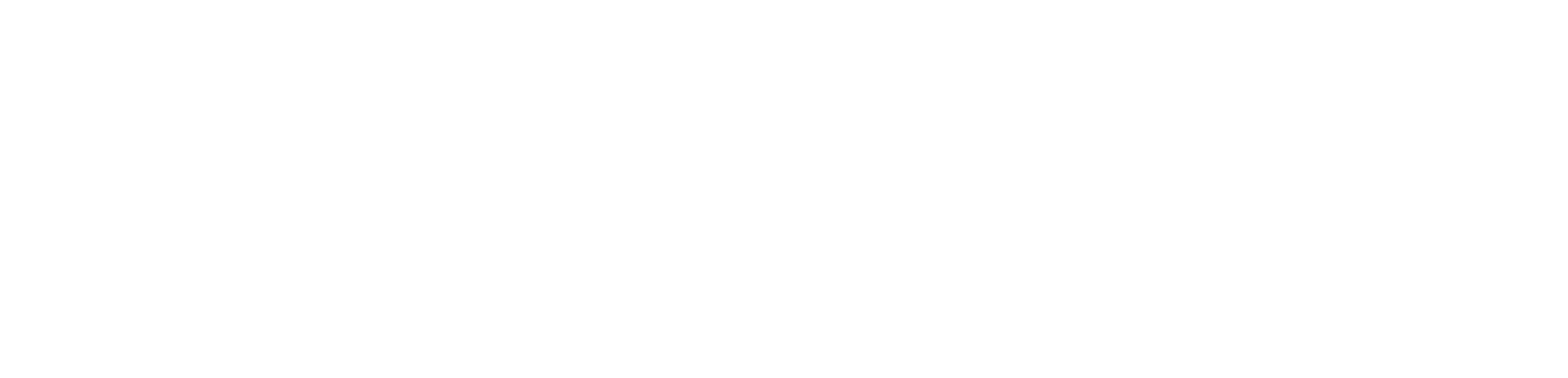
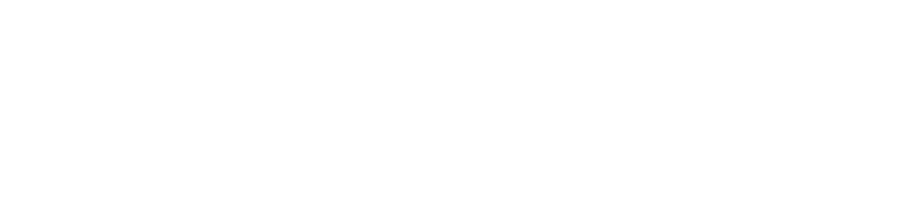



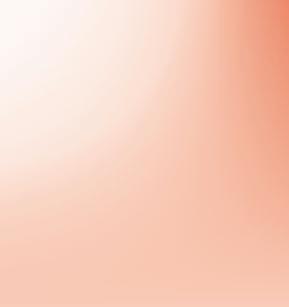
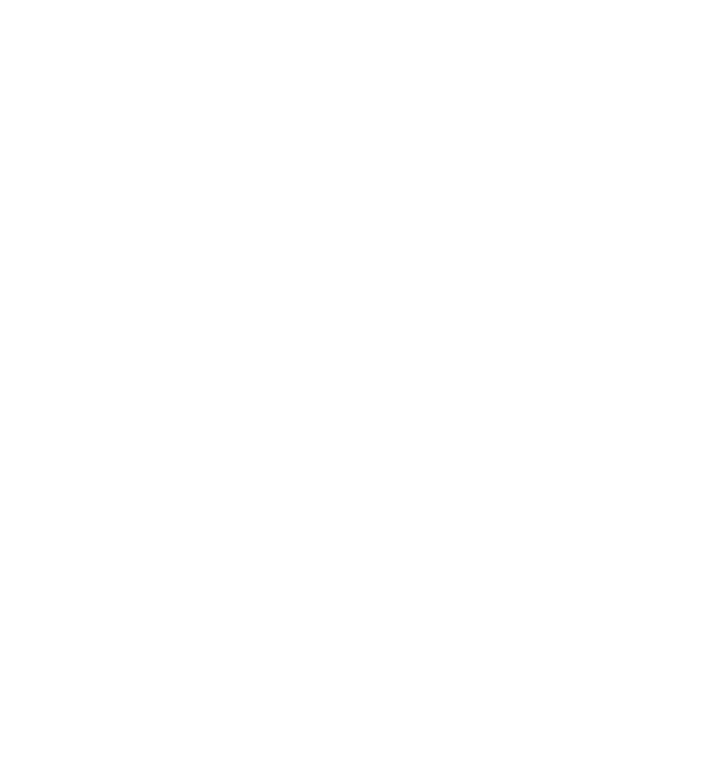
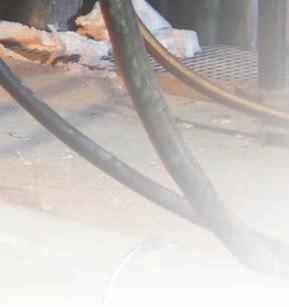
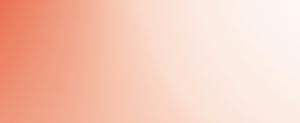
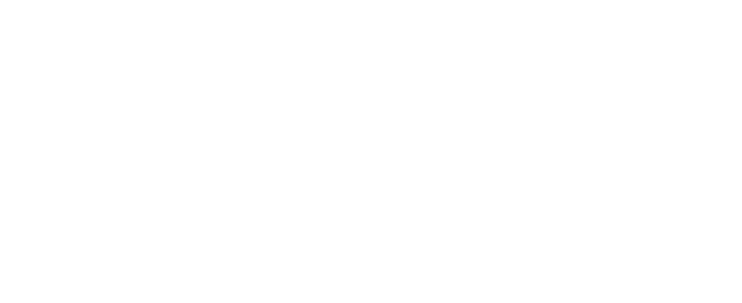
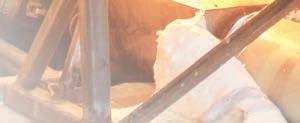

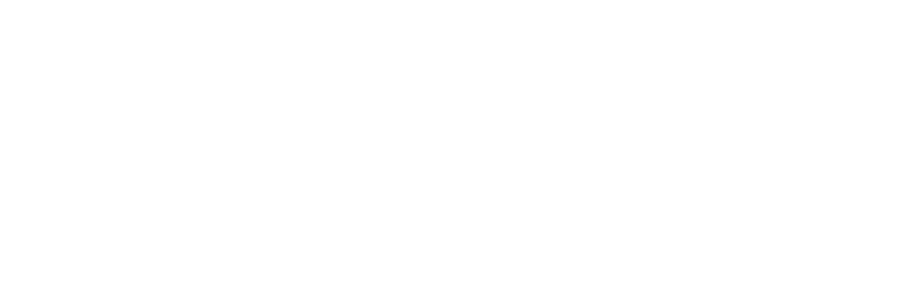
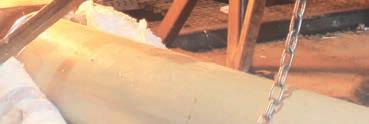
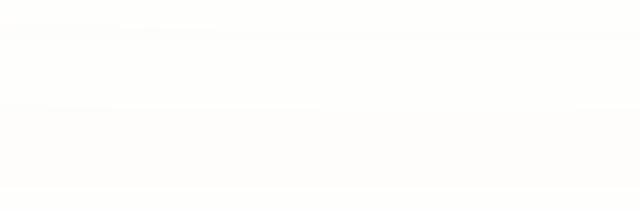
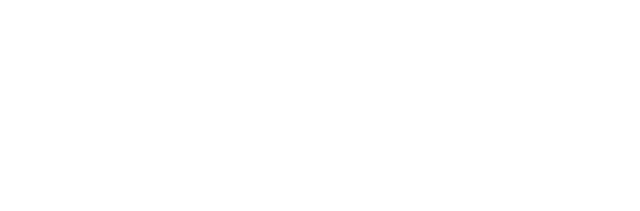
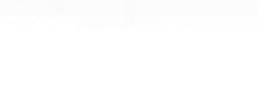
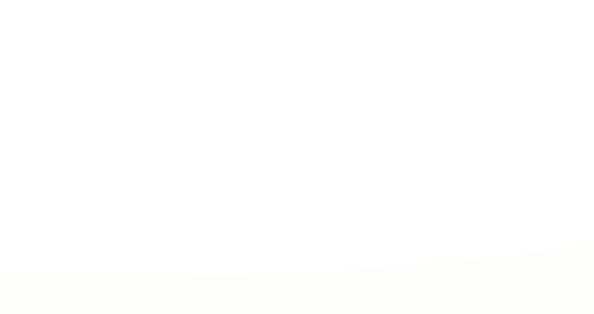

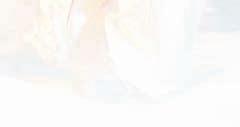



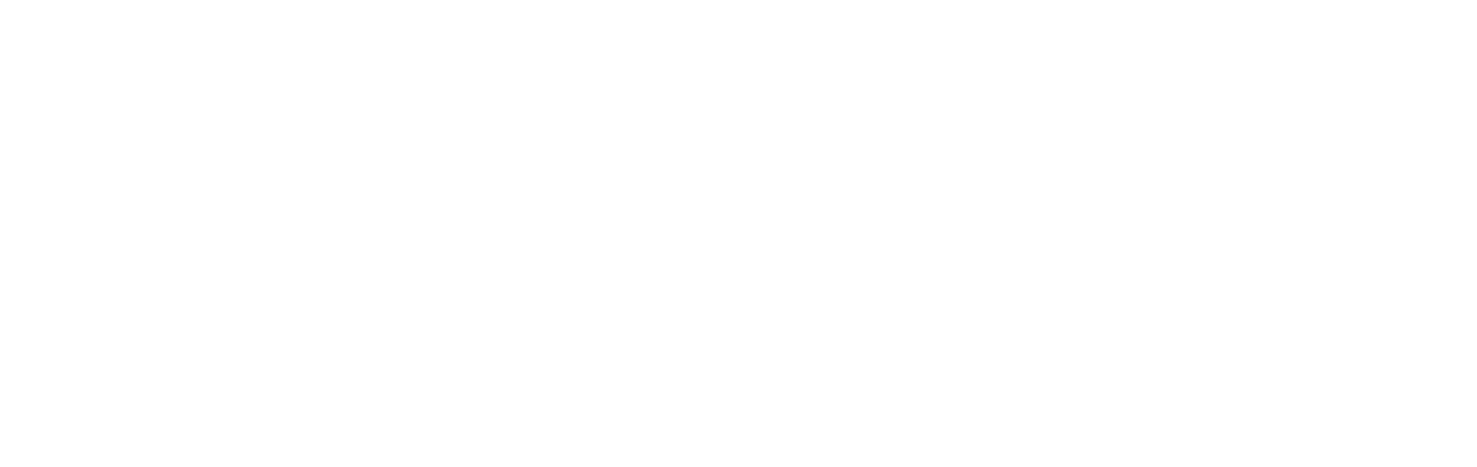
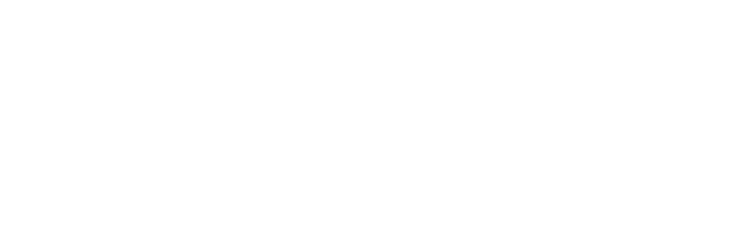




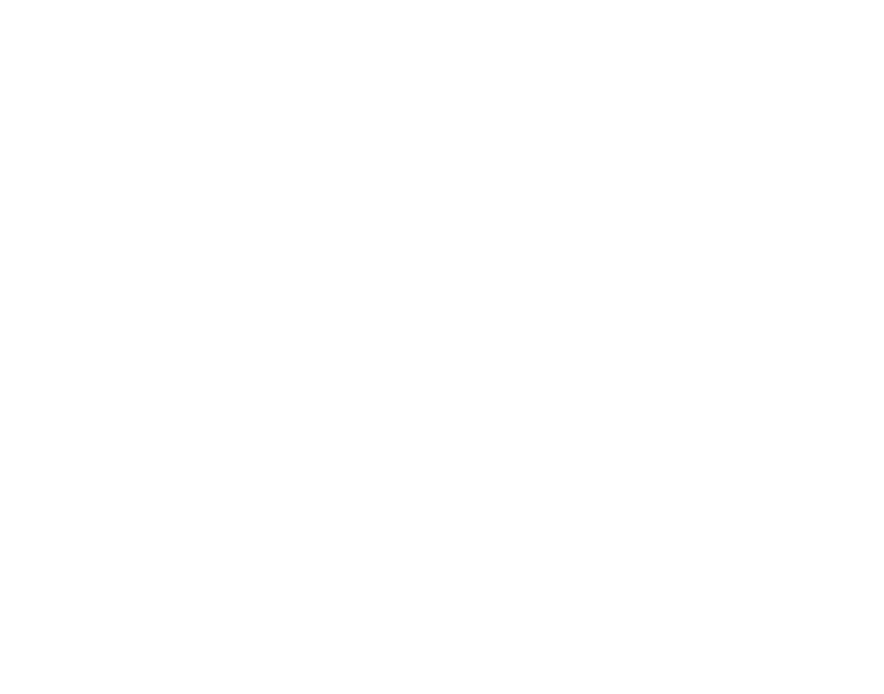
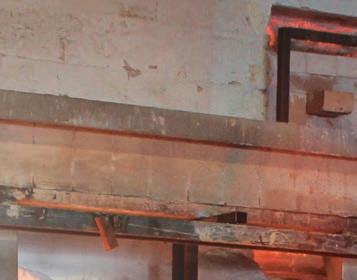

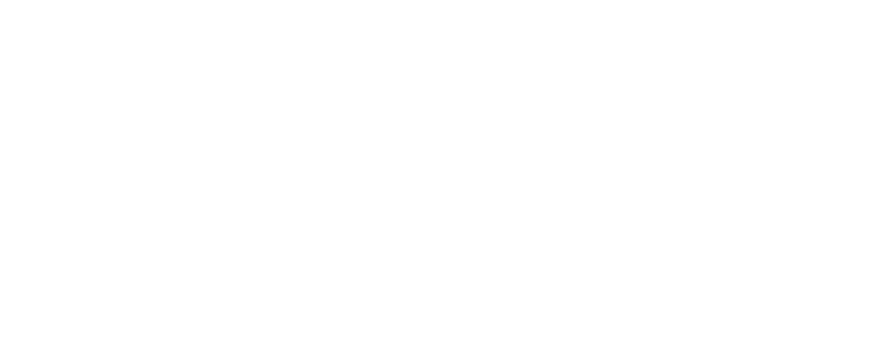
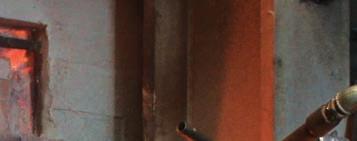

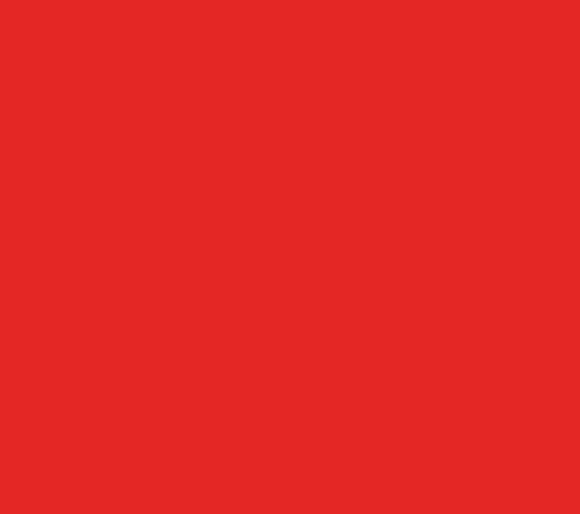
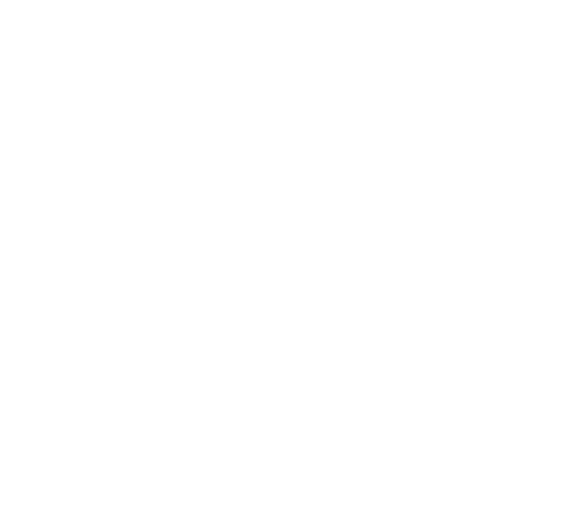
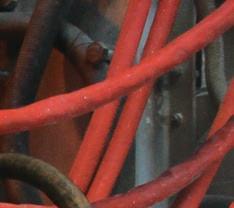

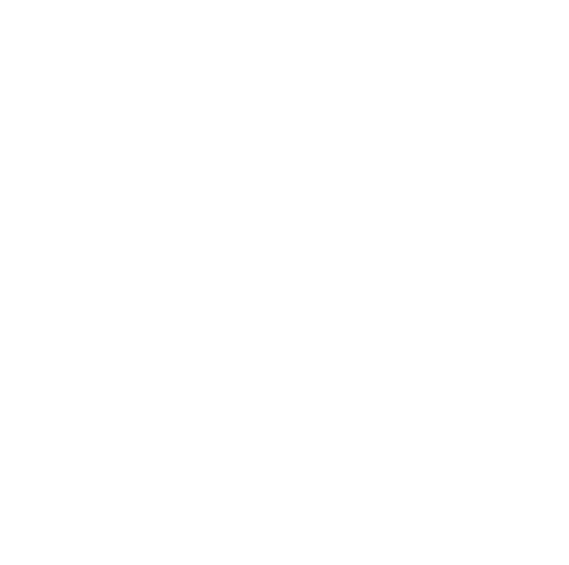
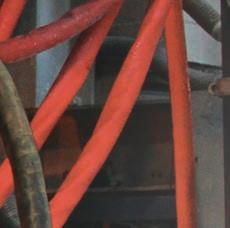
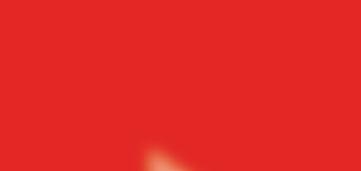
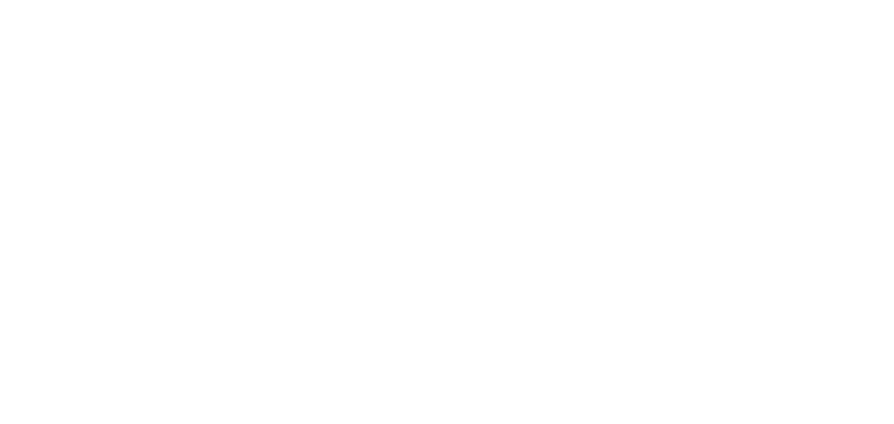
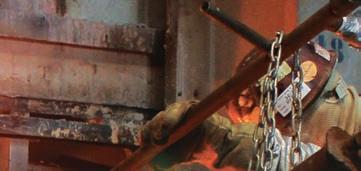
testing in glass factories.
Hot gas fi ltration
Whether fi ne dust, sulphur dioxide emissions or nitrogen emissions caused by high melting temperatures, all cause poor air quality. As a result, the glass industry – like many other industries – faces a big challenge: to fi lter and remove dust from fl ue gases and pollutants as effi ciently as possible and to reduce emissions.
Rath is rising to this challenge. As a company with extensive experience in refractory technology, it’s only logical that Rath also specialises in hot gas fi ltration. For many years, the company has been developing ceramic hot gas fi lter elements that make it possible to fi lter particle-laden industrial fl ue gases at temperatures up to 1000°C and reduce emissions of nitrogen oxides.
Since 2016, all resources, capabilities and expertise in hot gas fi ltration have been pooled in Meißen, Germany. This research and production site of the company is now home to cutting-edge facilities for the manufacture of Rath’s Filtrath non-catalytic and Filtrath CAT catalytic fi lter elements (Figs 1 & 2). The latter were developed for pollutant emission control.
These rigid yet highly porous and catalytically coated ceramic fi lter elements are used for multiple pollutant control of (fi ne) dust, acid gases, dioxins and nitrogen oxides in hot gas fl ows (at temperatures between 250° and 420°C) and can easily replace conventional textile fi lters.
Rath also offers tailor-made solutions in terms of hot gas fi lter cartridge length. Using a specially developed ‘screw & glue’ connection, fi lter cartridges up to a length of six metres can be produced from several segments. The segments are assembled into a long fi lter element when the fi lter cartridges are installed on site.
As of June 2022, Rath has doubled its manufacturing capacities when it put a new production line into operation at its Mei en plant. The fi ltration business line has seen a signifi cant growth. “It has great potential since the glass industry has to drastically reduce its footprint on environmental pollution and the greenhouse effect. Rath is committed to advancing environmental protection and helping its customers in the glass industry achieve their ambitious environmental goals. Thus, Rath continuously develops and invest in this technology”, Mr Nusszer said.
Glass know-how
To meet the customers’ requirements in the best possible way, Rath has established a dedicated glass unit; all the resources and know-how in the fi eld of glass are bundled in one global division. Rath’s engineers and technicians for industrial glass applications have an outstanding expertise, allowing them to develop powerful refractory materials that are tailored to the client’s individual requirements.
Rath also offers expert consulting services – from planning and installation to the maintenance and care of furnaces – and is a full-range supplier in the production of all required refractory materials for all layers in furnace construction. �
*Managing Director of the Sales Unit Glass, Rath, Krummnußbaum, Austria www.rath-group.com/glass
(Learn more about the new product line by visiting Rath’s glasstec booth D15 in Hall 13.)
A GLASS OF ITS OWN
Refractories and Hot Gas Filtration for High Demands
JOIN US! glasstec Düsseldorf Sept. 20 – 23
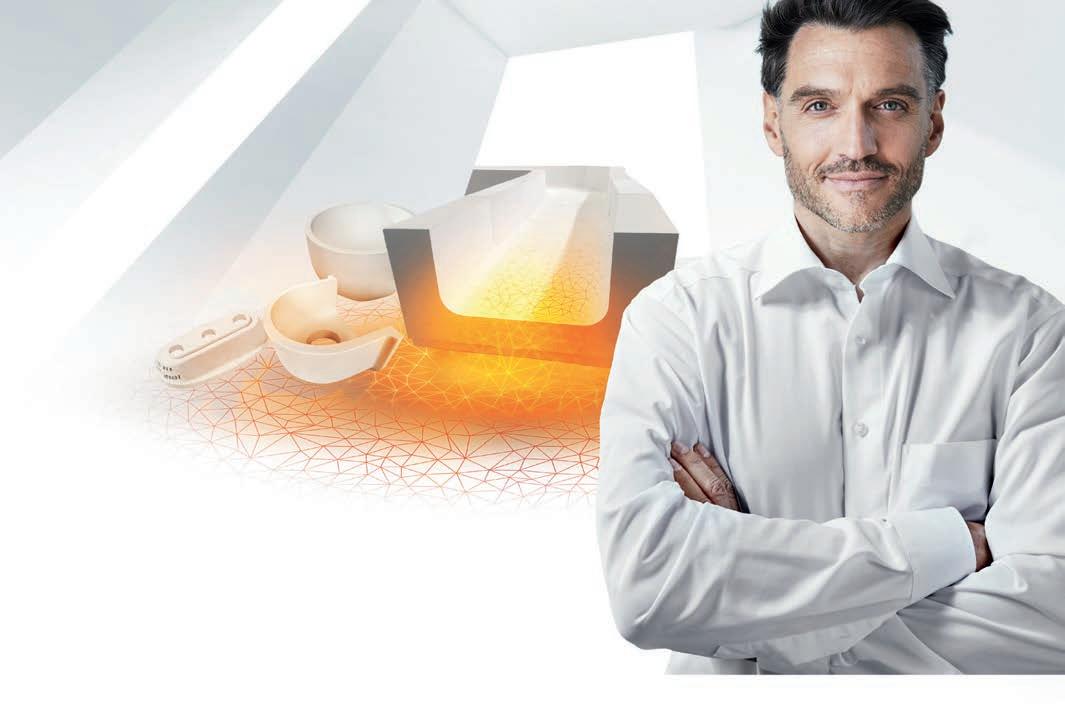
Visit us at glasstec Düsseldorf! Convince yourself live of the quality of our products. We’ll be on hand to showcase outstanding innovations from the following elds: • Refractories for the entire production chain • Crucibles for Art Glass • Hot Gas Filtration to ensure clean air