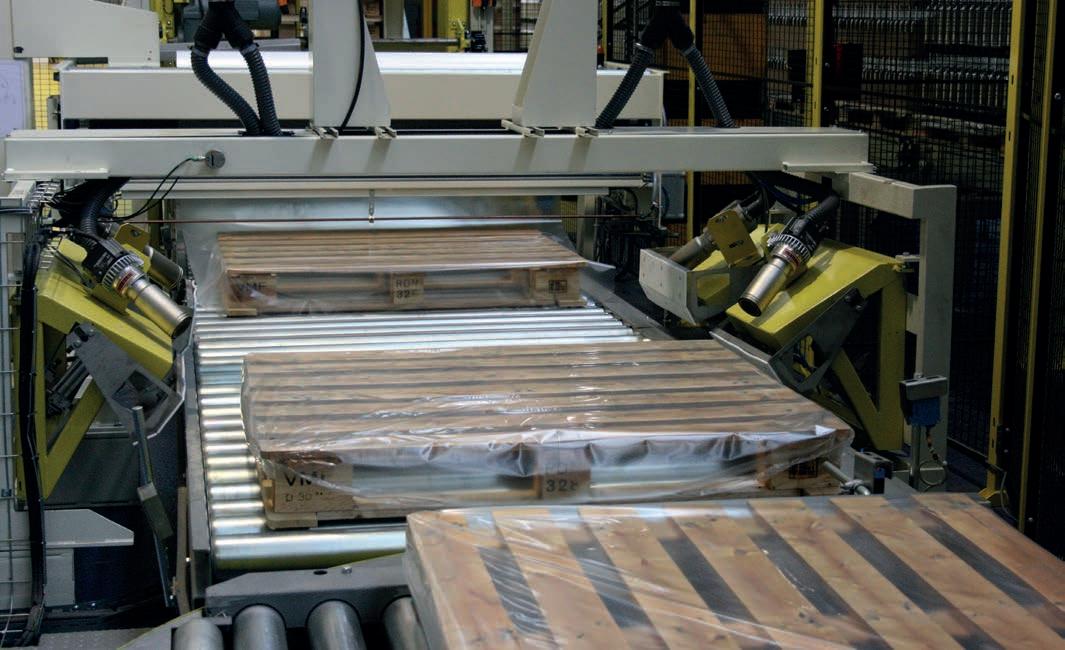
13 minute read
Palletising: Thimon
Fig 1. Pallets are e ippe ith fl oor mats to provide a seal on all six sides.
Taking charge of your entire end line
Thimon* gives an overview of its products for packaging palletised loads and its automated shrink hooding machines developed for the hollow glass market.
Founded in 1968, Thimon is a French manufacturer that designs machines specifi cally to meet customer requirements. We were the fi rst company to create a machine capable of wrapping palletised loads, which made us pioneers in our sector.
Today, the family company is above all a team of 70 people dedicated to creating end-of-line machines specifi cally designed to meet our customers’ needs.
We manufacture every packaging solution existing on the market today. ou may know Thimon for its expertise in packaging palletised loads and designing automated shrink hooding machines.
The latter is developed for and particularly suited to the hollow glass market. But Thimon also manufactures many handling elements for your pallets.
Because we have a multi-market experience, and we are developing our logistics know-how by accompanying our customers on this growing market for Thimon, we design lines that are more and more ergonomic and today offer effi cient and intelligent solutions in general logistics.
We can take advantage of this expertise for the handling of glass products. For example, we can integrate upstream and downstream of your hooding machine.
Empty pallets preparation lines
The empty pallet preparation line is independent and is located upstream of the glass container palletisation.
Its purpose is to place a fl oor mat (plastic fi lm) on an empty pallet and to glue, staple or shrink-wrap it onto the pallet. This line can be equipped with an empty pallet destacker at the infeed and or a pallet restacker with fl oor mat at the outfeed.
These pallets, equipped with their fl oor mats, are then moved to the palletisers (using shuttles). The fl oor mat is necessary because it provides a seal on all six sides of the pallet (Fig 1).
Shuttles
Shuttles (one, two, four pallet places) allow empty or charged pallets to be moved automatically from the empty pallet preparation lines to the palletisers or from the palletisers to the hooding lines (Fig 2). It is also possible to move the pallets after hooding to the storage areas.
Thimon manufactures induction shuttles which main advantages are: � Very low maintenance. � No parts aging due to friction. � No electrical risk as cables are buried and insulated. � No strain on forklift trucks and or operators (no ground or overhead supports).
Load and pallet centring devices
This equipment, which is fully automated and equipped with four mobile panels, is used to centre the products on a pallet to reduce defects linked to palletising or
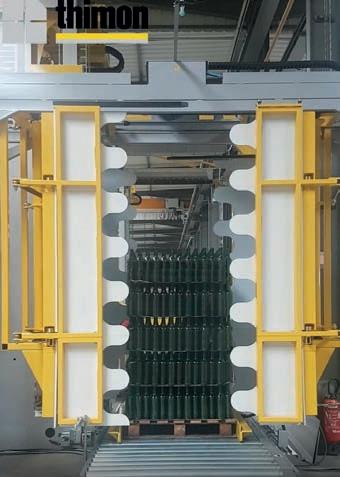

Fig 2. Shuttles allow empty or charged pallets to be moved automatically.
pallet handling (Fig 3).
Used at the entrance of the hooding line, it allows to recentre the layers of glass containers on the pallet before hooding. The operation is done for all four sides at the same time, without any rotation of the pallet.
Top glass shrink top cover dispenser system
This is a device that allows a cover to be placed on the top of the pallet after a fi rst complete hooding and to shrink the same fi lm thanks to a heating frame (Fig 4). The top glass is installed just downstream of the shrink-wrapping machine.
This type of equipment is very often used by glass manufacturers to add extra protection to reinforce the tightness of the packaging and to ensure perfect protection of their products. This process is very effective when stacking and storing pallets outdoors.
Stackers
The role of this element is to lift a pallet after shrink hooding and to automatically stack it on another pallet. Thimon stackers are equipped with fully secured retractable forks and lifting system. The stacking of pallets at the end of the hooding line optimises the fl ow and reduces and facilitates the operations of the forklift drivers in the storage areas.
We also manufacture many handling elements common to all our customers’ markets, such as: � Lifts lowering devices. � Lifting tables.
Fig 3. Thimon’s load and pallet centring device.
� Conveyors. � Turntables. � Orthogonal transfer tables. � Broken glass collection bins under roller conveyors. � Shrinkage compensation options for ambient temperature. � Chain conveyor sidewall covers. � Raised or covered cable trays.
As a reminder, in addition to its automated shrink hooders and the various handling systems presented in this article, Thimon has also developed robot machines, particularly adapted to the glass market. These shrink hooders are an excellent alternative for companies that want to offer themselves a high quality service.
We know how to handle your pallet and the associated data (traceability, SSCC number, origin, etc.) throughout the entire cold end, from the exit of your palletisers to the loading of your products onto the trucks. More than 100 glass industry companies trust us to optimise their whole end of line.
We have mastered all packaging technologies for all markets and offer the benefi t of over 50 years’ experience. It is by accompanying our customers every day and by seeking out the best solution in every situation that we have constantly developed our expertise, with the sole aim of satisfying our customers. �
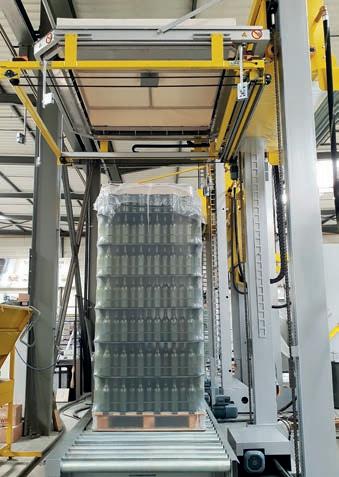
Fig 4. The top glass device is often used by
glass manufacturers to ensure the protection of their products.
*Thimon, Méry, France https://www.thimon.com/en
TECHGLASS celebrates commissioning of 480tpd furnace
TECHGLASS has been designing and supplying completely equipped furnaces, working ends and forehearths for over 30 years. In July 2022 a 480tpd furnace was commissioned - the Stoelzle Group’s largest and one of the largest end port furnaces in Europe.
Cooperation between TECHGLASS and Stoelzle Czestochowa dates back to the establishment of the Polish branch of this Austrian company, which took place in 2001.
To date, TECHGLASS has delivered there the furnace, working end and forehearths three times, and has completed more than 150 smaller orders.
In 2020, the decision was made to implement a furnace with a pull of 480 tons per day with 5 forehearths, in a hall designed for a furnace with a 40% smaller melting area, the most ambitious option among those considered. The six-month tender process was completed in February 2021 with the victory of TECHGLASS. Forehearths, working end and furnace
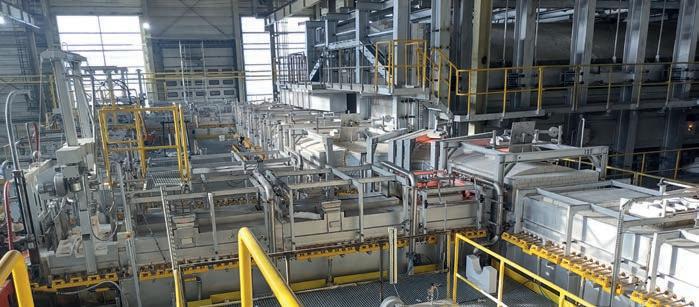
In house business model
The execution of the project took place during the Covid pandemic and the war in Ukraine. Lead times for some components have been extended several times over. It has become common practice for suppliers to provide offers that are not binding in terms of neither prices nor deadlines.
However, the TECHGLASS business model based on designing and manufacturing almost all of the systems in-house has helped address these challenges.
The status of each of thousands of orders Massive regenerator was monitored in real time, allowing a quick response in case of any problems. This would not have been possible if production had been carried out by subcontractors.
Share of electric energy in melting up to 40%
The furnace is designed to melt of up to 192tpd out of 480tpd by electric current.
This allows the melting process to be optimized according to cost and availability of energy sources.
It also offers the potential for dramatically greater reductions in CO2 emissions than standard solutions with electricity at an estimated 20%.
The furnace was equipped with a combustion system with automatic individual burner control.
This makes it easier to operate the system and, most importantly, reduces nitrogen oxide emissions and has a positive impact on energy consumption.
Alternative fuels
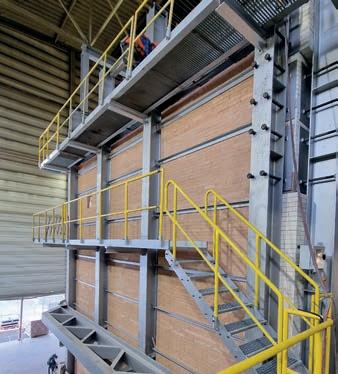
Short glass to glass time
It took only 67 days from the glass drainage from the previous furnace to the start of the heat-up of the new one - three days less than originally anticipated.
It is difficult to interpret this result without knowing the extent of the necessary demolition, construction and installation works.
However, anyone who witnessed the situation before the drainage and then before the heat-up must consider this result to be record-breaking.
The determination and dedication of TECHGLASS employees have been recognised by the management of Stoelzle Czestochowa. The combustion system is designed for easy extension of LPG or oil supply.
The furnace control system ensures the stability of the combustion process, regardless of the amount of each fuel fed, reducing the impact on the production process to a minimum.
This functionality becomes of vital importance in the current situation of uncertain natural gas availability and unpredictability of its price.
Machine Learning
It has been repeatedly confirmed that good learning algorithms achieve better results than experts. TECHGLASS is implementing a programme to introduce Machine Learning modules into control systems.
In the first stage, ML is planned to be used to minimize glass level disturbance after changing the combustion side. TECHGLASS engineers are also working on applications of ML in other areas, such as optimising forehearths operation during assortment changes.
Obtaining even a small amount of energy savings from these measures is worth the effort put into them.
TECHGLASS offers solutions for production of all types of glass
Recently a TECHGLASS furnace of pull of over 300tpd for melting sodium silicate has been commissioned.
The furnace is part of a project executed for CIECH Vitrosilicon S.A. which also covered engineering and supply of batch house and three modern production lines
CIECH Vitrosilicon is the biggest supplier of sodium silicates in Europe. It has two production plants in Poland. The company belongs to CIECH Group – an international, expanding group operating in chemical industry with strong global presence.
TECHGLASS’ innovation
The standard is to transfer solutions for soda-lime glass, mainly container glass, to sodium silicate production. The innovative TECHGLASS furnace was designed from the ground up for melting this glass.
This allowed the production of high-quality sodium silicate with energy efficiency unattainable with standard approaches and with very low NOX emission. The furnace can be operated without investing in and maintaining any secondary methods of reducing nitrogen oxides.
Low energy demand
The furnace supplied by TECHGLASS has exceptionally low energy demand, which is especially important with today’s rising gas prices and carbon dioxide emission costs.
To meet the customer’s very stringent requirements in this area, TECHGLASS has made a number of improvements.
A very efficient transfer of energy to the melt from the furnace’s combustion space was achieved by equipping the furnace with two “extra wide” dog houses and four oscillatory batch chargers for excellent batch distribution.
The furnace combustion system for CIECH Vitrosilicon was equipped, as in the case of Stoelzle Czestochowa, with automatic individual burner control. It is also designed for easy extension with LPG or oil supply.
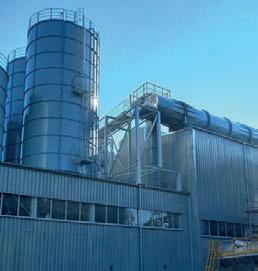
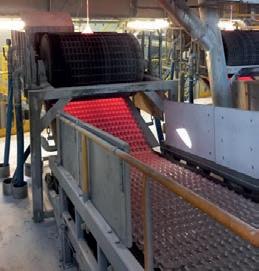
Left: Production hall. Right: Glass cubes production From left to right: Andrzej Skowiniak - President of TECHGLASS, Robert Janeczko - Chairman of the Board, CIECH Vitrosilicon. Hubert Domaradzki - Member of the Board, CIECH Vitrosilicon

Reduced module
An important feature of the furnace design is to reduce the time between the production of products with different specifications, the so-called module. As a result, the amount of unwanted transient product is significantly reduced, which translates into savings and reduced environmental impact.
Scope of supply
As part of the project, TECHGLASS also designed and supplied a batch house and three complete lines for producing frit in the shape of almost any size of cubes.
Each of the three frit production lines is equipped with forming machines, conveyors, a cooling water system, all auxiliary systems, and a control system integrated with the furnace control system.
The execution of the project was such a success, that soon after its completion CIECH Vitrosilicon ordered a rebuild of the existing furnace with TECHGLASS. The rebuild was based on a significant modification of the furnace’s design.
TECH G LA SS - G LA SS IN D U STRY SO LU TIO N S www.techglass.pl office@techglass.pl
ACM O N SYSTEM S
As a manufacturing solution provider for batch plants in glass industry 4.0
roviding state of the art batch oriented solutions to a vast range of industries like chemicals minerals construction and glass cmon s stems has gained a signi cant cross functional e pertise. his enables us to provide manufacturing solutions . from conceptual design up to nal deliver and from operations to information business la ers.
he strategic partnerships with contractors like alorni ech have been providing us the opportunity to bid among best-inclass solution providers in the sector and to gain a signi cant market share, having already delivered successful projects on either brown or green eld basis to multinational glass manufacturers.
pro ect milestone sealing the aforementioned partnership with the talian ngineering ontractor is the one at ulf lass actor in atar. high end mi ing plant for container glass production of tonnes per da . alorni tech is the contractor of the whole pro ect while cmon s stems is the one ensures the optimal batch and cullet distribution for two furnaces.
cmon s stems is responsible for the entire process engineering of the batch plant which includes but is not limited to batch house, cullet returns both internal and external, mixers, silos for raw material storage building architectural la out and metallic sca old stud e uipment detail engineering manufacturing erection and installation supervision commissioning and pro ect hand over. he pro ect will be delivered full automated securing of trouble free operation et with direct connection to s stems and business intelligence la ers. ost sales services like training spare parts for two and ve ears operation are also including to cmon s scope of suppl .
eorge oshakis ommercial irector of cmon roup said ver the last ve ears our main focus and commitment was to glass industrial sector a niche vertical which despite from initial challenges turns out to be the sector with the greater eturn on nvestment ratio throughout the entire organisation. he glass sector and more speci c batch plants and cullet return solutions is considered to be the industrial eld we will continue to invest in the ears to come.
cmon roup is a world class enterprise providing industrial solutions on a turn ke basis in elds of material handling automation and process engineering robotics and conve ing s stems in real time connectivit with business la ers through industr . so ware pla orms. he s nergies created from three independent entities creates a uni ue blend of e pertise considered to be the one stop source for a wide range of industr verticals.
pecialising in process technolog of powders particles and granules cmon s stems a member of cmon roup has been delivering customised and innovative solutions for raw materials automation.
delivering added value to our customers we support a sustainable industrial suppl chain and a smooth transformation to the digital factor of the future.
Best in class batch house and cullet return solutions.
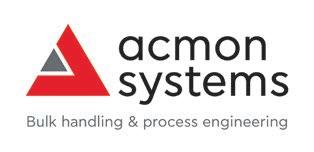
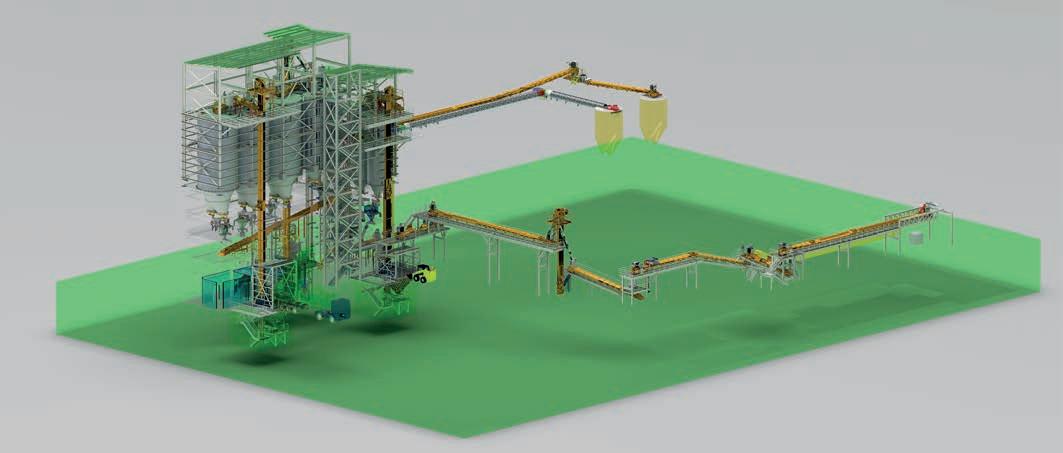