
5 minute read
new products and global contracts
Fig 8. Effect of initial steel temperature on treatment time at SSM Fig 9. Effect of initial steel temperature on specific aluminium consumption at SSM

recommended that no Al coil or loose spool be added in the LHF before arcing. Also, it was recommended that the temperature be raised by arcing followed by addition of ferro-alloys and de-oxidisers (trimming additions) based on the previous analysis from the VOR/VAR. The aim was for a despatch temperature to the caster of 1590°C for first heat to the caster then 1580°C for the second heat onwards.
Results and discussion:
The deoxidising power of aluminium[4-6] is well known as it is used for primary deoxidation of steel in both electric arc and BOF steelmaking. Various deoxidation processes and their effects have been described in detail by Pickering et al[7]. An industrial scale study on deoxidation by aluminium carried out by Bettembourg et al[8] showed that ideally about 1.5kg of aluminium is required for primary deoxidation per tonne of cast steel. The best approach to decrease aluminium consumption is to receive the steel from the primary steelmaking furnace with the lowest possible concentration of both iron oxide and dissolved oxygen. Carry-over slag is one of the main variables to decrease the initial oxidation conditions during tapping of the steel.
Plant trials carried out at SMS-I, RSP, employing the recommendations above totalled 142 heats. The average aluminium consumption achieved was 4.2kg/t in the trial as compared to the 2019-20 shop average of 5.35kg/t (Fig 6).
The majority of the trial heats on Al consumption using the modified process method was in the range of 2 – 6 kg/t with the majority of heats towards the lower of these values. In a few heats, consumption was greater than the previous shop average. Any higher Al consumption (say >7kg/t) may be due to reasons such as a returned heat from LHF, excess slag carry over, slag decanting, slag overflow, purging failure, a reladled heat, low temperature and so on.
Initial deoxidation with petroleum coke helped in decreasing the level of dissolved oxygen in the steel. Others have shown that initial deoxidation with petroleum coke followed by other deoxidisers not only help in reducing the dissolved oxygen in steel (and hence lower consumption of primary deoxidisers) but also helps improve the cleanliness of the steel[9, 10]. Initial deoxidation with pet coke also helps in reducing nitrogen pick up[9]. The deoxidation product in the case of coke is gas, no solid or liquid inclusions are generated in the steel and coke also results in less top slag in the ladle.
The tapping temperature at the BOF was increased as illustrated in Figs 8 & 9. The previous lower temperature of the steel on arrival at secondary steelmaking had not only resulted in increased treatment time during secondary steelmaking but also contributed significantly to greater aluminium consumption due to the need for temperature adjustment by chemical heating in the VOR.
Measures to reduce slag carryover from the BOF to the ladle were taken.
The deoxidation practice was designed in such a way that the addition of a small quantity of petroleum coke and Al bar during tapping the steel from the BOF did not fully kill the steel prior to its arrival at the SSM units. Some dissolved oxygen in the steel improves the heating effacing during arcing and hence arcing duration is decreased. The practice of arcing the heats after the addition of large quantities of aluminium in the VAR was changed. This also helped control Al fading during arcing in the VAR. All the suggested measures in the VAR, VOR and LHF resulted in a decrease in average Al consumption to 4.2kg/t, around 30% compared to the 2018-19 value. �
Acknowledgement
The authors thank the management of Rourkela Steel Plant and R & D Centre for Iron and Steel, Steel Authority of India Ltd, Ranchi, for their support.
References
1. Stolte, G. Secondary Metallurgy: Fundamentals, Processes and Applications. Verlag Stahleisen GmbH: Dusseldorf, 2002; 146 pp. 2. Fruehan, R.J. Ladle Metallurgy Principles and Practices; Iron and Steel Society: USA, 1985. 3. A. N. Conejo and D. E. Hernández, “Optimization of Aluminium Deoxidation Practice in the Ladle Furnace”, Materials and Manufacturing Processes, 21: 796–803, 2006 4. A. Ghosh, Principles of Secondary Processing and Casting of Liquid Steel, 1990 5. T Saeki, T Nlsug, K Ishikura, Y Igaki and T. Hiromoto “Development of Oxygen Sensors and Their Application in Steelmaking Operations”, Transactions of the Iron and Steel Institute of Japan, 1978, 18(8), pp.501-509. 6. Pierre GS, Blackburn RD, “The relationship between first-order interactions and oxide solubilities in liquid iron” Trans Met Soc AIME. 1968 Jan;242(1):2-4. 7. Pickering FB, “Production and Application of Clean Steel”, Int. Cont. 1970, Jun:23-6. 8. Bettembourg JP, DieudonnéJ GJ., “Study of deoxidation by aluminum on an industrial scale”, International Conference on Production and Application of Clean Steels. London: The Iron and Steel Institute 1970 (pp. 59-67). 9. Kloppers C, Fedotova T. “Primary deoxidation of Basic Oxygen Furnace steel by means of carbon”, Journal of the Southern African Institute of Mining and Metallurgy. 2001 Oct 1;101 (7):321-8. 10. Kumar S, Keshari KK, Gupta A, Prasad A, Kumar V, Mishra B, Abhishek K. Improvement in Castability of Al-Killed Steel in Billet Casters by Process Optimization. Transactions of the Indian Institute of Metals. 2020 Jan 1;73(1):243-9.
Effective against aggressive media
One of the most important things needed when developing new oil and gas fields are tools which work reliably in great depths under the sea. The problem is that these tools are subjected to rock formations of varying hardness and aggressive media, necessitating special high strength steels which also exhibit a high corrosion resistance. This combination of properties proves to be a challenging proposition, says
Merlin Seifert*
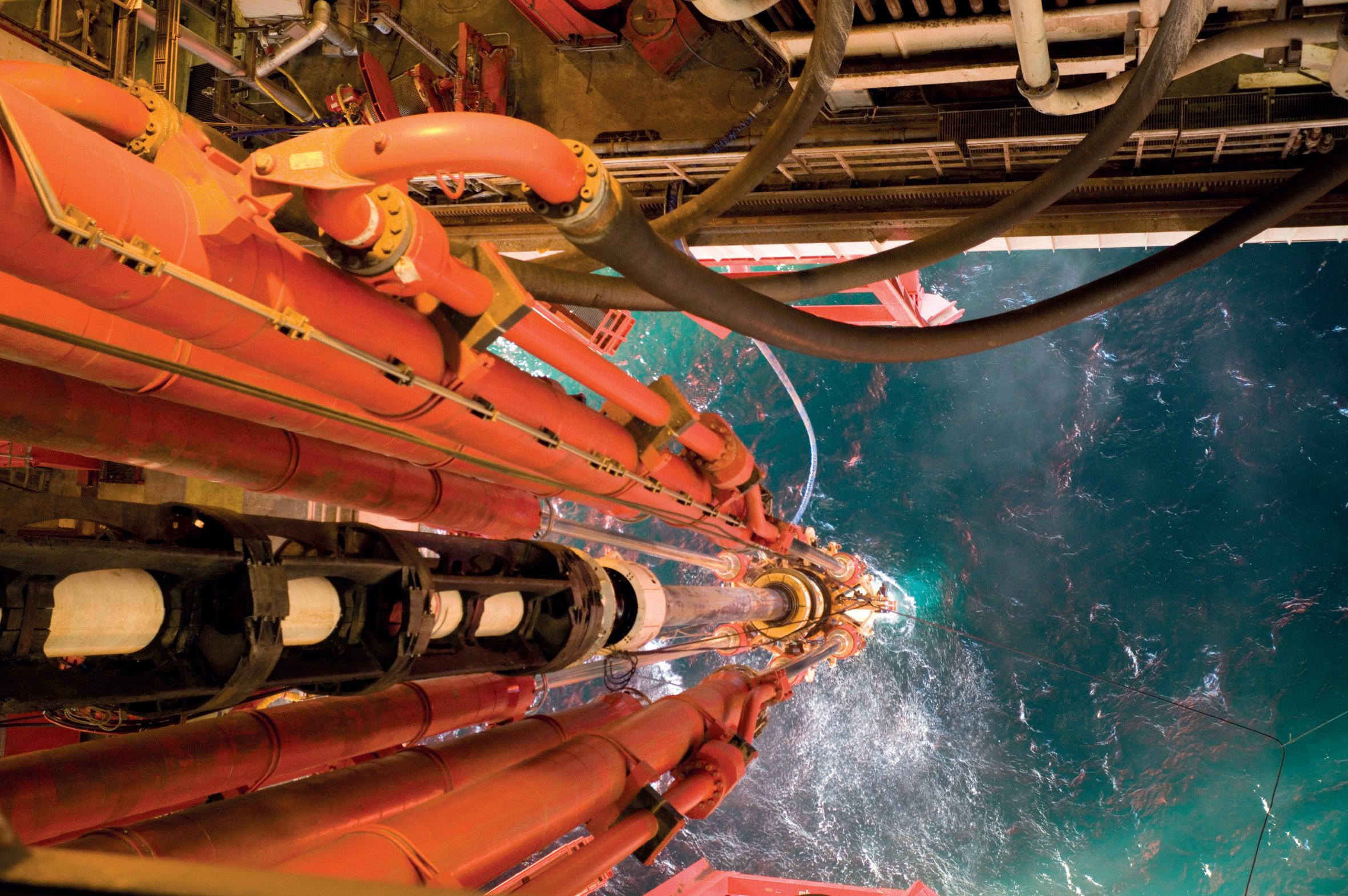
Deutsche Edelstahlwerke has developed a stainless steel that increases process reliability in the oil and gas extraction field and that steel is Corrodur 4418 Mod.
WHETHER for enhancing effectiveness in a car’s powertrain, extracting oil and gas safely and reliably or increasing the durability of components in the aerospace sector, the use of special long steel is indispensable in many industries. Finished machined mandrel bars, for example, made from hot work tool steel and in lengths of up to 26m, are used in mills that manufacture seamless tubes and pipes for the oil and gas industry. Other applications for long steel products in the field of oil and gas extraction are drill collars and rotors in the drive unit and power section of subsea drill strings.
Special long steel generally allows a high product differentiation, yet requires extensive expertise – especially in the highly sensitive area of oil and gas exploration. The drilling fluids used here often contain sour gas and chlorides. These aggressive media constantly attack the extraction equipment, particularly at increased temperatures. The reaction with the steel in use can lead to