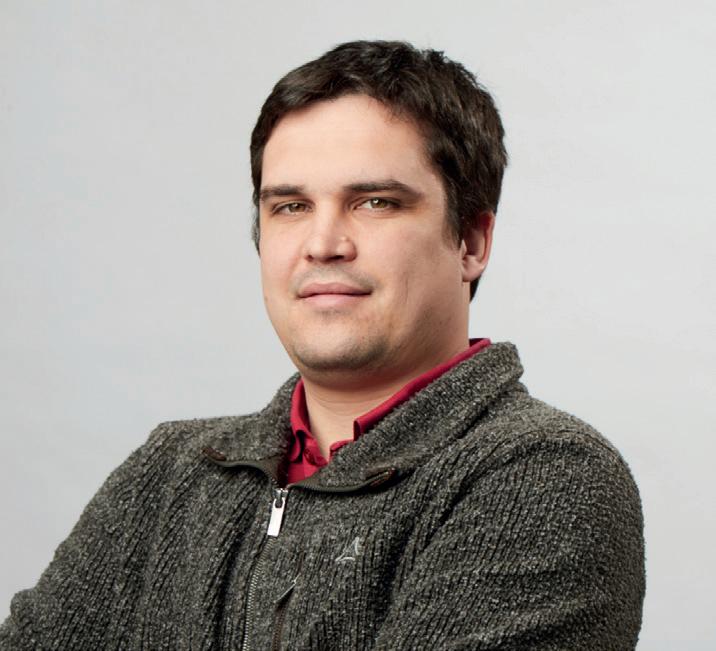
7 minute read
Crazy steel facts – worth
pitting and stress corrosion in the worst case. To prevent restrictions or even failure of the equipment, only exclusive materials are approved by oil and gas companies. Good resistance to pitting and stress corrosion is frequently required in this respect, combined with a strength that allows users a certain amount of freedom in terms of component design.
The steadily increasing requirements on the material properties lead to ongoing research and development of materials in order to counter corrosion in particular. The focus often lies on coatings or modified alloy compositions. For instance, the rotors already mentioned are tungsten carbide or hard chrome-plated in order to improve wear and corrosion resistance. Coatings can totally change the properties of a component though sometimes well adapted to its requirements. As described above, alloy development is always subject to certain limits with regard to the desired combination of different properties. While coating processes, such as hard chromeplating, often generate considerable additional costs, alloy development represents a more cost-effective alternative. Another feasible alternative is the application-oriented qualification of materials. Here, the conditions encountered during use are analysed and transferred to appropriate laboratory tests. If a steel passes the tests required for the qualification process, it can be approved for certain applications or customers. This was also carried out at Deutsche Edelstahlwerke (DEW) for the special steel, Corrodur 4418 Mod, which has to comply with requirements from the industry standards NORSOK M-650 and NACE MR0175.
Controlled heat treatment
Deutsche Edelstahlwerke, part of the SCHMOLZ + BICKENBACH Group, offer a wide portfolio of steel qualities for the oil and gas exploration sector. These include low and high-alloyed structural steels, ferritic, martensitic, high-alloyed austenitic and duplex stainless steels as well as non-magnetic steels. Corrodur 4418 Mod (also known as Super 13Cr) DEW is now qualified as a stainless steel and is widely used in completion tools in the oil and gas exploration industry. This involves a material solution that exceeds conventional chrome steels in terms of performance. The required properties are specifically set by means of a controlled heat treatment. The result
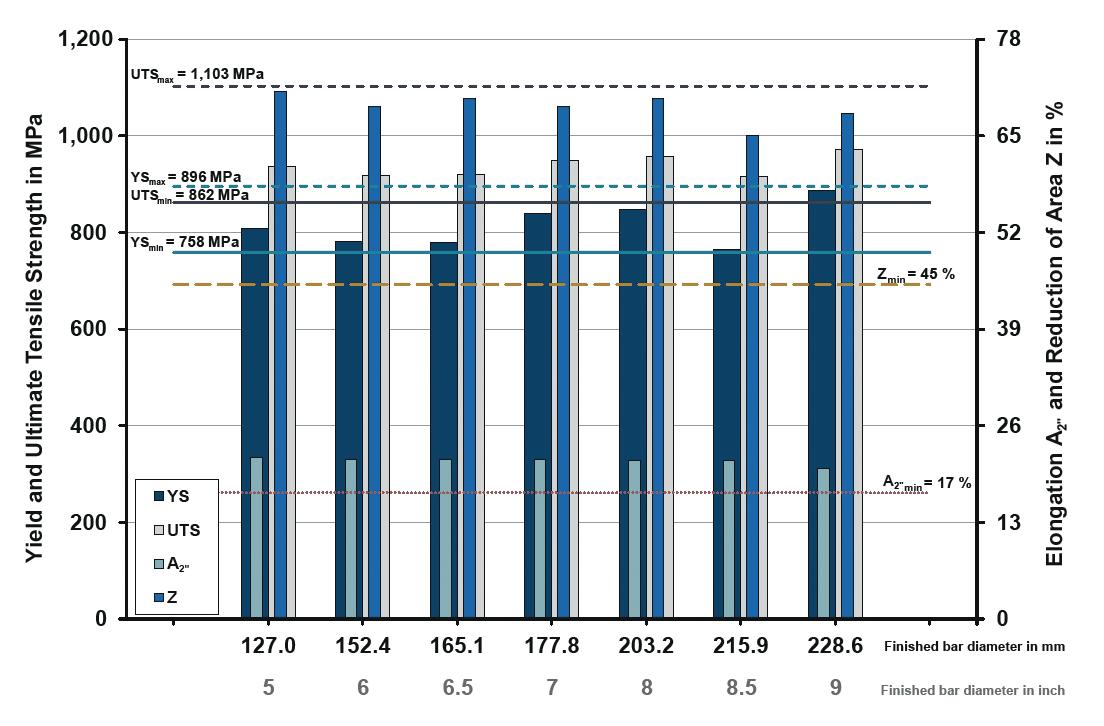
Mechanical properties of Corrodur 4418 Mod measured in the tensile test depending on finished diameter. Source: Deutsche Edelstahlwerke
is an extremely high-performance steel characterized by high strength, outstanding toughness and good resistance to pitting and stress corrosion. With a tensile strength of at least 125 ksi (862 MPa), a yield strength of at least 110 ksi (758 MPa) and a toughness of at least 60 ft-lbs (81 J) at 14 °F (-10 °C), Corrodur 4418 Mod is far superior to conventional 13% chrome steels.
Performance advantage
These properties were determined by extensive laboratory tests. The steel was austenitized between 1778 and 1886 °F (970 - 1030 °C) and then quenched in water. Tempering was subsequently carried out at 1022 to 1202 °F (550 - 650 °C). The best compromise between strength and ductility was achieved in the temperature range between 1076 and 1106 °F (580 - 630 °C). This temperature range was confirmed in real life during the heat treatment of bars, proving that the required properties are also met by industrial heat treatment in continuous furnaces.
The test results for Corrodur 4418 Mod were impressive in terms of its corrosion properties. Extensive tests found no signs of inter-crystalline corrosion according to ASTM A 262 Prac. A and Prac. E, as was expected. In addition, tests performed according to NACE TM0177 and NACE TM0316 regarding sulphide-induced stress cracking (SSC) and stress corrosion cracking (SCC) using application-oriented media were passed successfully. This enabled the steel to be qualified by Equinor ASA (formerly Statoil ASA) as well as a growing number of other end-consumers.
At the beginning of 2020, DEW presented its new special steel at the Corrosion Conference & Expo, the world’s biggest trade fair for solutions to prevent corrosion. More than 6,000 corrosion experts from 60 countries visited the exhibition in Nashville/Tennessee, USA, including scientists, engineers and technicians, but also purchasers, meaning the new steel and its qualification could be presented at all levels of the supply chain. �
For further information, log on to www.dew-stahl.com
Merlin Seifert
Trade Union banners depict UK steelworks
The Cleveland Industrial Archaeology Society has published a book of 11 paintings depicting UK steelworks of the 1920s. Painted by artist Herbert Finn, seven of these were painted in large format onto silk to create Trade Union banners. By Dr. Tim Smith*
TO commemorate this portrayal of steelmaking 100 years ago, the Newcomen Society has posted fi ve of the illustrations on its web site, along with short descriptions of the technologies.
One of those illustrated here, ‘Ironworks with two blast furnaces’ shows molten iron being tapped into pig beds. Remarkably, these are in the open air, which must have led to some excitement after rain! The furnaces have mechanical charging for ore, coke and limestone by inclined hoist and
The book ‘The Banner of the Steel Workers Union’, compiled by the late Jake Almond, contains all 11 illustrations and is available, for £10 including post and packing, by emailing info@cias-teesside.uk.
Five pictures have been selected for the Newcomen web site and can be viewed at www.newcomen.com/ steelmaking-technology-trade-unionbanner/ The commentary is written by Jonathan Aylen, former president of the Newcomen Society, and a past regular contributor to Steel Times International.


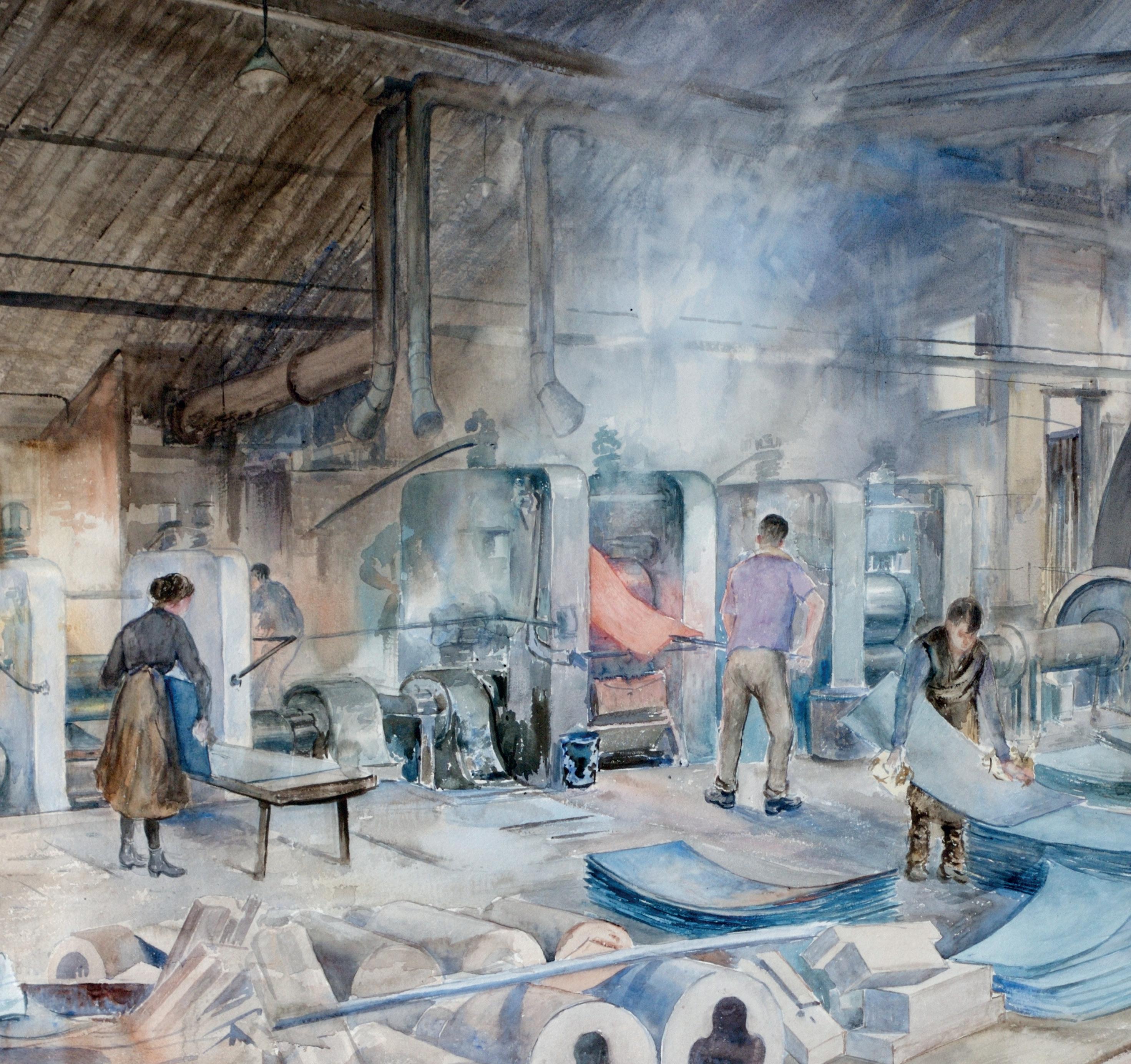
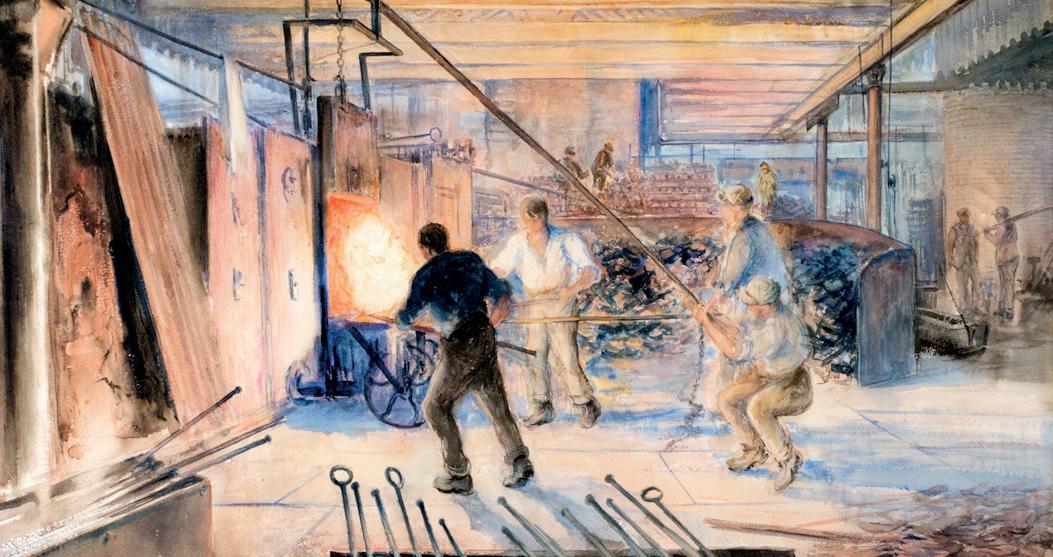
Above: Pack mill rolling plate for tinning Right: Two blast furnaces with pig iron casting bed Left: Puddling iron in a reverberatory furnace
a ‘merry go round’ method for returning the empty hoppers. It is not apparent what type of system is used to distribute the charge into the furnace. The nearest furnace has single chamber cowper hot blast stoves. Similar furnaces were present at DK Roheisen und Recycling in Duisburg, Germany, although using a pig casting machine by this time.
Also illustrated is the rolling of plate for tinplate in a steam-driven cross-country pack mill. The presence of a woman ‘opener’ in the picture reflects their role in separating the sheets of iron after rolling. Hot metal was passed through the mill, progressing into packs as reduction proceeded. This was achieved by folding over the ever-lengthening sheets and was necessary to achieve the thin gauges required in such mills that had no back-up rolls to reduce roll deflection. Most such mills were two-high with the hot sheet fed into the roll bite by the ‘rollerman’ and returned to him by the ‘behinder’ who grabbed it with tongs and passed it back over the top of the mill stand. At each pass the roll gap was reduced until the sheet was long enough to be folded across its width at the half way point by the ‘doubler’ who then squeezed the fold flat in the ‘squeezer’ ready to pass through the mill again. During a series of passes and reheats, this doubling was carried out three times to give a pack of eight sheets, which were trimmed along all four edges and separated by the ‘Opener’ prior to pickling in acid and cleaning ready for hot dip tinning.
Another picture is of crucible steelmaking, a method developed by Huntsman in Sheffield in 1740 to produce a more homogenous steel from cemented bar. Cementation was a method of reintroducing carbon into refined low carbon flat bar by packing the bars in sealed chests along with carbon bearing materials and heating these for several days to enable carbon to diffuse into the metal to produce steel, but with a strong carbon gradient. Huntsman melted this steel in clay pots, which was then poured into moulds to form ingots of more homogenous steel. This led to Sheffield becoming pre-eminent in the cutlery industry – the word ‘cutlery’ including any cutting instrument. Examples of both types of furnace have been preserved in Sheffield today.
Another illustration shows puddling of cast iron pigs to wrought iron and illustrates the arduous and strenuous working conditions of the time.
Puddling used coal as the fuel in a reverberatory furnace, so separating the charge from the fuel to prevent contamination, and replaced the use of more costly charcoal hearths. The most widely adopted processing was that developed by Henry Cort in 1783 and improved by him the following year.
The fifth illustration is again a cross country mill but this time, as evidenced by the switchgear on the gantry above, driven by an electric motor, a pioneering power source for a mill in 1920 replacing steam power. A DC cumulative compound motor would be used to deliver high starting torque and variable speed control. �
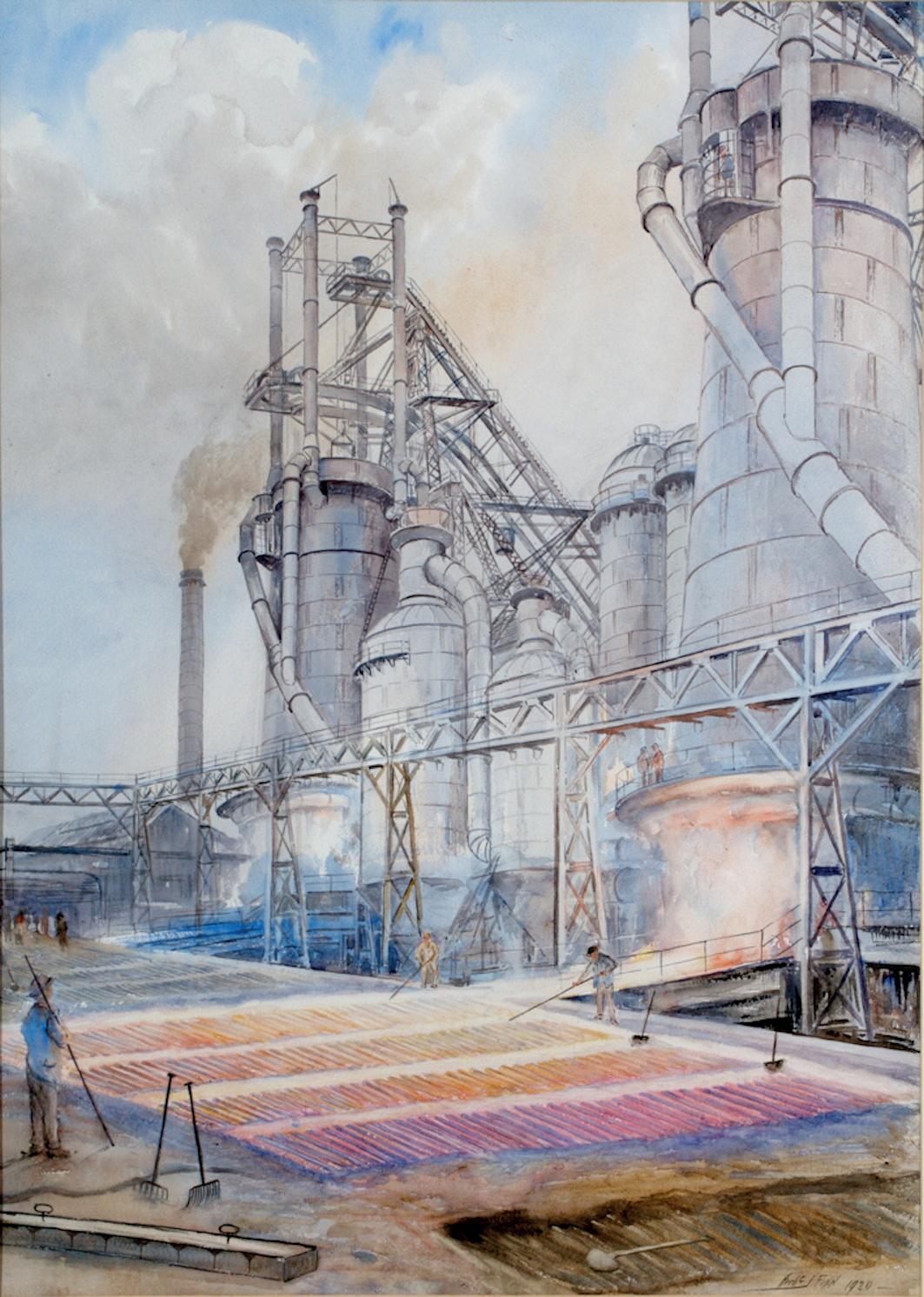